This introduction paper is based on the paper "Understanding Residual Stress Effects and Corrective Action for Die Casting Tools – Part 2" published by "DIE CASTING ENGINEER".
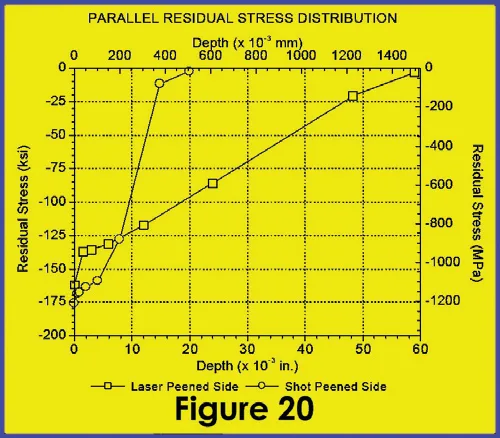
1. Overview:
- Title: Understanding Residual Stress Effects and Corrective Action for Die Casting Tools – Part 2
- Author: Jerald V. Skoff
- Year of publication: 2008
- Journal/academic society of publication: DIE CASTING ENGINEER
- Keywords: (Not specified in the paper)
2. Abstract:
This paper (Part 2) continues the discussion on managing residual stresses in die casting tools, focusing on advanced shot peening techniques and process controls. It details the proprietary Metallife® process, including dual and intensity peening, methods for overcoming line-of-sight restrictions, and critical controls for media, intensity, and coverage (verified using PEENSCAN®). The paper also introduces laser peening as an emerging technology offering deeper compressive layers and discusses residual stress modeling. A case study illustrates the significant tool life extension and cost savings achievable through controlled shot peening.
3. Introduction:
Following Part 1 which covered the fundamentals of mechanically induced compressive stress, this paper delves deeper into specialized controls and technologies for stress relief in die casting dies, primarily focusing on shot peening. While heat stress tempering is one method mentioned in the NADCA User's Guide for Relieving Stresses in Die Casting Dies, proper shot peening techniques are often less understood. This part discusses the special controls used to maximize the benefits of the Metallife® compressive stress and surface modification process, explores new technologies like laser peening, and presents case studies validating the effectiveness of these corrective actions.
4. Summary of the study:
Background of the research topic:
Residual stresses and manufacturing effects significantly shorten the life and performance of die casting dies. Corrective actions like heat stress tempering and shot peening aim to mitigate these issues. However, the specifics and controls required for optimal shot peening are not widely known or practiced effectively in the industry.
Status of previous research:
Part 1 of this series established the basics of mechanically induced compressive stress, including its history, definition, stress curves, depth considerations, and detrimental manufacturing effects. NADCA has published guidelines covering stress relief methods. While heat stress tempering is documented, detailed understanding and application of advanced, controlled shot peening techniques require further elaboration.
Purpose of the study:
The purpose of this paper is to elaborate on the specialized process controls necessary for maximizing the benefits of shot peening (specifically the Metallife® process), introduce advanced techniques like dual/intensity peening and internal peening, discuss methods for process verification (like PEENSCAN®), introduce laser peening as a next-generation technology, and provide case study evidence of the effectiveness of these methods in extending die life and reducing costs.
Core study:
The core of this study focuses on the practical application and control of advanced shot peening processes for die casting tools. Key areas covered include:
- Dual and Intensity Peening: Proprietary multiple peening processes (Metallife®) to significantly enhance fatigue life (300-500%+) by improving the surface compressive stress layer and finish.
- Line of Sight Solutions: Techniques using internal lances and shot deflectors (ISD) to peen internal features like blind bores, shot sleeves, and internal cores (Figure 10).
- Process Controls: Detailed explanation of critical controls for ensuring repeatable and effective peening:
- Media: Requirements for shape (round, Fig 12), uniformity (size, Fig 14), and removal of broken media (Fig 13, Fig 15).
- Intensity: Measurement using Almen strips (Fig 16) to quantify shot stream energy and ensure consistent compressive stress impartation.
- Saturation: Verification process to determine the minimum exposure time needed to achieve full intensity.
- Coverage: Ensuring complete (typically >100%, often 200%+) surface obliteration by peening dimples (Fig 17, 17a), verified using PEENSCAN® (Fig 18) especially for hard tool steels.
- Residual Stress Modeling: Utilizing software (PeenstressSM) to predict and optimize peening parameters based on material, hardness, geometry, and shot characteristics.
- Laser Technology: Introduction to laser peening (Laserlife) as a high-cost, high-benefit alternative offering much deeper compressive layers (Fig 19, Fig 20) with less cold work, studied in collaboration with universities and labs.
- Case Study: Presentation of a historical case study demonstrating significant cost savings ($76,000) and tool life extension by using repeated shot peening applications (Figure 21, Figure 22, Figure 22a).
5. Research Methodology
Research Design:
The paper employs a descriptive and explanatory approach based on extensive industry experience (Badger Metal Tech Inc.), proprietary process knowledge (Metallife®, PEENSCAN®, PeenstressSM), and collaborative research findings (e.g., with Case Western University on laser peening). It outlines specific techniques, control methodologies, technological advancements, and practical results rather than presenting a single controlled experiment.
Data Collection and Analysis Methods:
The paper synthesizes information derived from:
- Established shot peening principles and standards (e.g., Almen strip testing, saturation curves).
- Proprietary process development and internal data (Metallife® procedures, PeenstressSM modeling, PEENSCAN® verification).
- Collaborative testing results (e.g., laser peening depth measurements by Case Western University, Figure 20).
- Field data and customer case studies (e.g., Canadian die caster tool life and cost analysis, Figure 21).
Analysis involves explaining the correlation between process parameters, control methods, and resulting material properties (compressive stress, fatigue life, surface characteristics) and performance outcomes (tool life, cost savings).
Research Topics and Scope:
The research focuses specifically on corrective actions for residual stress in die casting tools using advanced shot peening and emerging laser peening technologies. The scope includes:
- Detailed discussion of process control parameters (media, intensity, saturation, coverage).
- Advanced peening techniques (dual/tri-peening, internal peening).
- Process verification methods (Almen strips, PEENSCAN®).
- Predictive modeling of residual stress profiles.
- Introduction and comparison of laser peening technology.
- Practical applications, benefits beyond stress relief, and economic impact via case study.
- Limitations such as line-of-sight restrictions for standard peening.
6. Key Results:
Key Results:
- Proprietary dual or tri-peening processes can enhance fatigue life by 300%, 500%, or more compared to normal shot peening by further enhancing surface compressive stress.
- Strict process control is paramount for repeatable results: media must be round, uniform, and free of broken particles; intensity must be measured and controlled using Almen strips and saturation curves; coverage must be complete (minimum 100%, often 200%+) and can be verified using PEENSCAN®, especially on hard tool steels.
- Specialized equipment (internal lances, ISD) enables peening of internal features previously limited by line-of-sight restrictions.
- Laser peening can induce compressive stress layers up to four times deeper (e.g., 0.060" on H-13 steel) than conventional shot peening, with less cold work, offering potential advantages against thermal fatigue but at a higher cost.
- Software modeling (PeenstressSM) can aid in selecting optimal peening parameters and predicting stress profiles.
- A case study demonstrated a 25% cost saving ($76,000) by extending the life of a single die to 300,000 shots through repeated peening applications, versus requiring two separate tools.
- Controlled shot peening offers additional benefits: reduced cavitation/breakout, hidden surface defects/reduced heat checking, improved metal flow, reduced porosity, better paint adhesion, lower temperature gradients, increased lube retention, and lower friction.

Figure Name List:
- Figure 10: Lance Peening and Internal Shot Deflector Peening
- Figure 11: SEM Photo of Single Peen Surface Finish
- Figure 11a: SEM Photo of Dual Peen Surface Finish
- Fig 12: Media Shapes
- Figure 13: Surface from Proper Media / Damaged Surface from Broken Media
- Figure 14: High Quality Shot Peening Media / Poor Quality Shot Peening Media
- Figure 15: Spiral Separation System for Shot Media Classification
- Figure 16: Almen Strip System
- Figure 17: Complete Shot Peening Coverage
- Figure 17a: Incomplete Shot Peening Coverage
- Figure 18: PEENSCAN® Coating Prior to Peening / Partial Removal Indicating Incomplete Coverage / Complete Removal Indicating Complete Coverage
- Figure 19: waffle overlap from fired laser
- Figure 20: PARALLEL RESIDUAL STRESS DISTRIBUTION (Laser Peened Side vs Shot Peened Side)
- Figure 21: $76,000 SAVINGS (Case Study Cost Comparison)
- Figure 22: Not Treated After 72,000 shots
- Figure 22a: Processed NEW & at 50K After 120,000 shots
7. Conclusion:
Controlled induction of compressive stress, a practice dating back centuries, is crucial for correcting detrimental manufacturing effects in modern metal parts, particularly die casting tools. The proprietary Metallife® ambient applied technology, developed since 1983, relies on strict adherence to controlling parameters (media, intensity, coverage, etc.) to achieve desired, repeatable results. Beyond countering residual stress, this surface enhancement provides numerous benefits including reduced cavitation, improved resistance to thermal fatigue and soldering, better metal flow, and enhanced coating adhesion. Optimal results are typically achieved by applying the process when the tool is new and reapplying at designated intervals (e.g., half-life). While not a universal solution for all tool failures, controlled shot peening significantly extends tool life and improves casting quality at a lower overall cost. Emerging technologies like laser peening offer potentially greater benefits (4-6 times deeper stress) but are currently limited by cost primarily to aerospace, military, and medical applications.
8. References:
- http://www.badgermetal.com
- http://www.knightsedge.com
- http://www.metalfinishing.com
- http://www.aws.org
- http://www.protoxrd.org
- http://www.shotpeener.com
- http://www.curtisswright.com
- http://www.drgears.com
- http://www.shotpeening.org
9. Copyright:
- This material is a paper by "Jerald V. Skoff". Based on "Understanding Residual Stress Effects and Corrective Action for Die Casting Tools – Part 2".
- Source of the paper: DIE CASTING ENGINEER, January 2008, available via www.diecasting.org/dce (Note: A specific DOI was not provided in the paper).
This material is summarized based on the above paper, and unauthorized use for commercial purposes is prohibited.
Copyright © 2025 CASTMAN. All rights reserved.