이 소개 자료는 "[Journal/academic society of publication]"에서 출판된 "[A forced convection stirring process for Rheo-HPDC aluminum and magnesium alloys]" 논문을 기반으로 합니다.
1. 개요:
- 논문 제목: A forced convection stirring process for Rheo-HPDC aluminum and magnesium alloys (레오-HPDC 알루미늄 및 마그네슘 합금을 위한 강제 대류 교반 공정)
- 저자: Mingfan Qi, Yonglin Kang, Bing Zhou, Wanneng Liao, Guoming Zhu, Yangde Li, Weirong Li
- 발행 연도: 2016
- 발행 학술지/학회: Journal of Materials Processing Technology
- 키워드: forced convection stirring (FCS), Rheo-HPDC, semisolid slurries, Al alloys, Mg alloys, microstructure, mechanical properties, macrosegregation (초록 내용에서 파생된 키워드, 원문에 명시적으로 나열되지 않음)
2. 초록:
Al 및 Mg 합금의 네 가지 다른 반용융 슬러리를 제조하기 위해 강제 대류 교반(forced convection stirring, FCS)이라는 단순화된 공정이 제안되었습니다. FCS 장치를 HPDC 기계와 결합하여 간단한 레올로지 고압 다이캐스팅(Rheo-HPDC) 공정이 개발되었습니다. FCS 공정 중 용탕의 온도 및 조성장이 시뮬레이션되었습니다. FCS Rheo-HPDC로 형성된 합금의 미세구조 및 기계적 특성을 연구하고, HPDC 및 다른 Rheo-HPDC 공정으로 형성된 합금과 비교했습니다. 결과는 FCS 공정이 미세하고 구형이며 매트릭스에 균일하게 분포된 초정 입자를 가진 슬러리를 제조할 수 있으며, 이 공정이 거시편석(macrosegregation)을 효과적으로 억제할 수 있음을 보여주었습니다. 강한 대류는 용탕의 온도 및 조성 균일성을 빠르게 촉진합니다. HPDC 및 다른 Rheo-HPDC 합금과 비교할 때, FCS Rheo-HPDC로 형성된 합금은 미세구조의 미세화 및 기공률 감소로 인해 향상된 극한 인장 강도, 항복 강도, 연신율 및 경도를 가집니다. 열처리를 활용하여 FCS Rheo-HPDC 합금의 기계적 특성을 더욱 향상시킬 수 있습니다.
3. 서론:
지난 몇 년간 환경 및 에너지 문제에 대한 해결책을 제공하기 위해, 특히 3C(컴퓨터, 통신 및 소비자 전자제품) 및 자동차 분야(Sui et al., 2015)에서 경량 금속으로서 Al 및 Mg 합금의 중요성이 널리 인식되었습니다. 오늘날 고압 다이캐스팅(HPDC)은 저비용과 고효율성으로 인해 대부분의 Al 및 Mg 합금 응용 제품 제조에 주로 사용되는 공정입니다. 그러나 Jin et al. (2015)은 고속 금형 충전 중 가스 혼입으로 인해 발생하는 많은 기공이 HPDC 부품에 존재함을 입증했습니다. Cáceres and Selling (1996)은 기공이 국부적인 변형 집중점으로 작용하여 기계적 성능을 심각하게 저하시킬 수 있음을 보여주었습니다. 기공은 또한 열처리 중에 문제를 일으키는데, 열이 기공 내 공기의 팽창을 유발하여 HPDC 부품에 버블링을 생성합니다.
따라서 고품질 및 향상된 성능의 부품을 형성하기 위한 HPDC 공정의 개선은 매우 가치가 있습니다. Flemings (1991)는 Rheo-HPDC 기술이 고품질 부품을 준비하는 데 사용될 수 있음을 입증했습니다. 기존 HPDC와 비교하여 Rheo-HPDC는 낮은 기공률, 열처리성 및 고성능과 같은 많은 이점을 제공합니다. Rheo-HPDC 공정에서는 액체 금속이 초기에 반용융 슬러리로 변환된 다음, 슬러리가 HPDC 기계를 사용하여 직접 성형됩니다. 반용융 슬러리를 준비하기 위해 다양한 준비 공정이 개발되었습니다. 트윈 스크류 교반 공정은 Fan et al. (2005)에 의해 연구되었고, 가스 유도 반용융(GISS) 공정은 Wannasin et al. (2006)에 의해 보고되었으며, 서펜타인 채널 주입(SCP) 공정은 Liu et al. (2015)에 의해 사용되었습니다. 이러한 준비 기술은 실험실에서 널리 연구되고 사용되었으며, 등축 미세구조를 가진 반용융 슬러리를 준비할 수 있습니다. 그러나 장치 청소의 어려움과 장치의 복잡한 분해 및 설치와 같은 많은 단점이 여전히 존재하여 산업 응용 분야에서의 광범위한 사용을 제한합니다.
슬러리 준비에 존재하는 문제를 해결하기 위해, Zhou et al., 2014a, Zhou et al., 2014b에 의해 반용융 슬러리 준비를 위한 자체 개발 강제 대류 교반(FCS) 장치가 설계되었습니다. 이는 간단한 작동 과정과 저비용을 갖춘 환경 친화적인 장치이며, 청소 없이 연속적으로 작동할 수 있습니다. FCS 장치를 HPDC 기계와 결합하여 Rheo-HPDC 공정을 개발하는 것이 편리하며, 이러한 절차를 FCS Rheo-HPDC라고 합니다.
본 연구에서는 A356, A380 및 7075 Al 합금과 AZ91D Mg 합금의 반용융 슬러리를 FCS 공정으로 준비한 다음, HPDC 기계로 네 가지 다른 부품으로 성형하거나 물로 급랭하여 잉곳으로 만들었습니다. FCS 공정이 잉곳의 미세구조 및 거시편석에 미치는 영향을 연구했습니다. FCS Rheo-HPDC 합금의 미세구조, 기공률 및 기계적 특성을 연구하고 HPDC 및 다른 Rheo-HPDC 공정으로 형성된 것들과 비교했습니다. 열 전달 및 유체 역학을 기반으로, 회전 속도가 온도, 조성 및 고상 분율에 미치는 영향을 상용 전산 유체 역학 소프트웨어 Flow-3D로 시뮬레이션했습니다.
4. 연구 요약:
연구 주제의 배경:
Al 및 Mg 합금은 환경 및 에너지 솔루션을 위한 중요한 경량 소재이며, 특히 3C 및 자동차 부문에서 중요합니다. 고압 다이캐스팅(HPDC)은 이러한 합금의 일반적인 제조 공정이지만, 가스 혼입으로 인한 기공 문제로 기계적 특성이 저하되고 열처리가 방해받습니다.
이전 연구 현황:
레오-HPDC 공정은 반용융 슬러리를 성형하여 부품 품질(낮은 기공률, 열처리성, 고성능)을 향상시킵니다. 트윈 스크류 교반, 가스 유도 반용융(GISS), 서펜타인 채널 주입(SCP)과 같은 기존 슬러리 제조 방법은 적합한 미세구조를 생성할 수 있지만, 장치 청소의 어려움과 복잡한 작동과 같은 문제에 직면하여 산업적 사용이 제한됩니다.
연구 목적:
A356, A380, 7075 Al 합금 및 AZ91D Mg 합금의 반용융 슬러리 제조를 위한 단순화된 자체 개발 강제 대류 교반(FCS) 공정을 소개하고 평가합니다. 결합된 FCS Rheo-HPDC 공정을 개발하고 연구합니다. FCS 공정이 미세구조, 거시편석, 기공률 및 기계적 특성에 미치는 영향을 조사하고, 이를 기존 HPDC 및 다른 레오-HPDC 방법과 비교합니다. FCS 공정 중 온도 및 조성장 시뮬레이션을 수행합니다.
핵심 연구:
핵심 연구는 네 가지 다른 Al 및 Mg 합금에 대한 반용융 슬러리를 생성하기 위한 FCS 공정의 개발 및 적용을 포함합니다. FCS 장치를 HPDC 기계와 결합합니다(FCS Rheo-HPDC). 연구에는 Flow-3D 소프트웨어를 사용하여 FCS 장치 내 용탕의 온도 및 조성장 시뮬레이션이 포함됩니다. 실험 작업은 결과 합금의 미세구조(입자 형상, 크기, 분포, 거시편석) 및 기계적 특성(인장 강도, 항복 강도, 연신율, 경도)을 특성화하고, 기공률을 평가하며, 이러한 특성을 표준 HPDC 및 다른 Rheo-HPDC 기술로 생산된 합금과 비교하는 데 중점을 둡니다. 열처리를 통한 특성 향상 가능성도 탐구합니다.
5. 연구 방법론
연구 설계:
본 연구는 계산 시뮬레이션과 결합된 실험적 접근 방식을 사용했습니다. 새로운 강제 대류 교반(FCS) 장치가 개발되어 고압 다이캐스팅(HPDC) 기계와 통합되어 Rheo-HPDC 공정을 만들었습니다. 네 가지 다른 합금(A356, A380, 7075 Al; AZ91D Mg)이 이 방법을 사용하여 처리되었습니다. 결과는 기존 HPDC 및 기타 확립된 Rheo-HPDC 공정과 비교되었습니다.
데이터 수집 및 분석 방법:
반용융 슬러리는 FCS 공정을 사용하여 준비되었고, 이후 HPDC를 통해 부품으로 성형되거나 잉곳으로 급랭되었습니다. 초정 입자 형태 및 분포, 거시편석을 조사하기 위해 미세구조 분석이 수행되었습니다. 극한 인장 강도, 항복 강도, 연신율 및 경도를 포함한 기계적 특성이 측정되었습니다. 기공률 수준이 평가되었습니다. 전산 유체 역학(CFD) 소프트웨어(Flow-3D)를 사용하여 FCS 공정 중 용탕 내 온도 및 조성장을 시뮬레이션했습니다. 기계적 특성에 대한 열처리의 영향도 조사되었습니다.
연구 주제 및 범위:
연구는 다음에 중점을 두었습니다:
- 반용융 슬러리 준비를 위한 강제 대류 교반(FCS) 공정의 개발 및 검증.
- A356, A380, 7075 Al 합금 및 AZ91D Mg 합금에 대한 FCS 적용.
- FCS와 HPDC의 통합(FCS Rheo-HPDC).
- FCS 중 열 전달 및 유체 흐름(온도 및 조성장) 시뮬레이션.
- 미세구조 특성화(초정 입자 형태, 분포, 수지상정 억제, 거시편석).
- 기계적 특성 평가(인장 강도, 항복 강도, 연신율, 경도).
- 기존 HPDC 대비 기공률 감소 평가.
- FCS Rheo-HPDC 성능을 표준 HPDC 및 다른 Rheo-HPDC 방법과 비교.
- FCS Rheo-HPDC 합금에 대한 열처리의 영향 조사.
6. 주요 결과:
주요 결과:
- 강제 대류 교반(FCS) 공정은 액상 매트릭스에 균일하게 분포된 미세하고 구형인 초정 입자를 가진 반용융 슬러리를 성공적으로 제조합니다.
- FCS 공정은 거시편석(macrosegregation)을 효과적으로 억제합니다.
- FCS 공정 중 생성된 강한 대류는 용탕의 온도와 조성을 빠르게 균질화하여 수지상정 형성 환경을 파괴하고 초정 입자의 양과 형태를 개선합니다.
- FCS Rheo-HPDC 공정으로 생산된 합금은 기존 HPDC 및 다른 Rheo-HPDC 공정으로 만들어진 합금에 비해 향상된 극한 인장 강도, 항복 강도, 연신율 및 경도를 나타냅니다.
- 기계적 특성 향상은 FCS Rheo-HPDC 공정을 통해 달성된 미세화된 미세구조와 감소된 기공률에 기인합니다.
- 열처리는 FCS Rheo-HPDC로 생산된 합금의 기계적 특성을 더욱 향상시키는 데 효과적으로 사용될 수 있습니다.
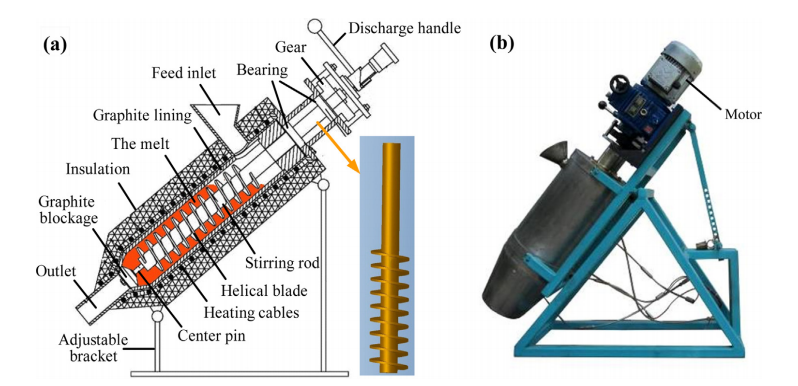
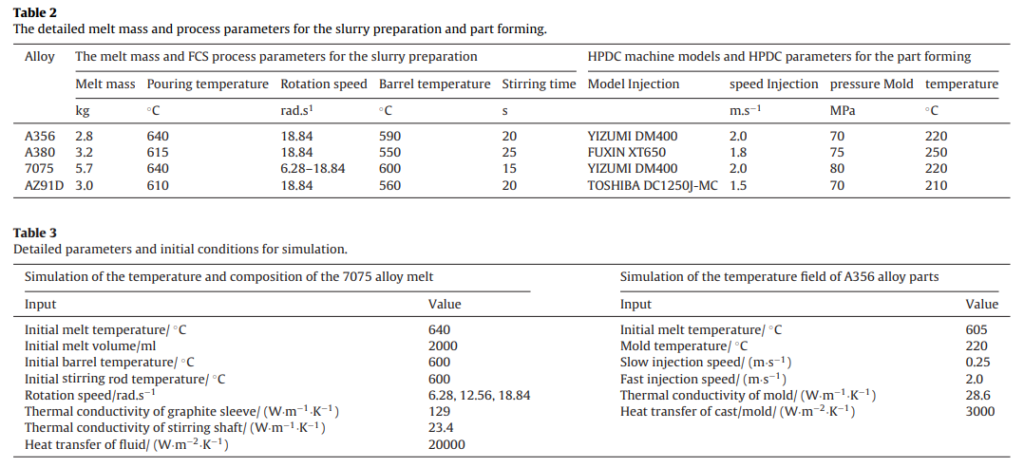
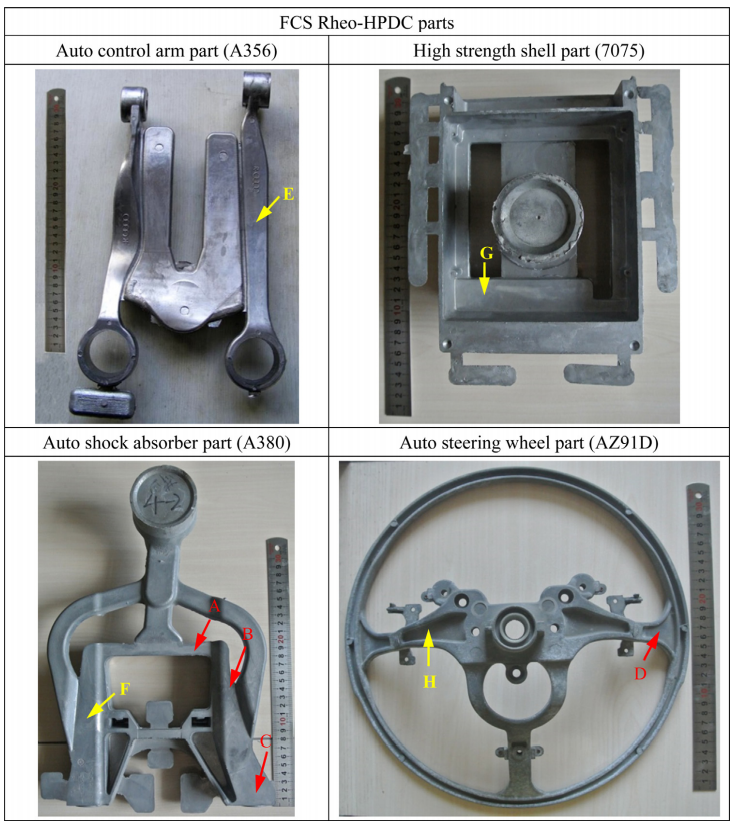
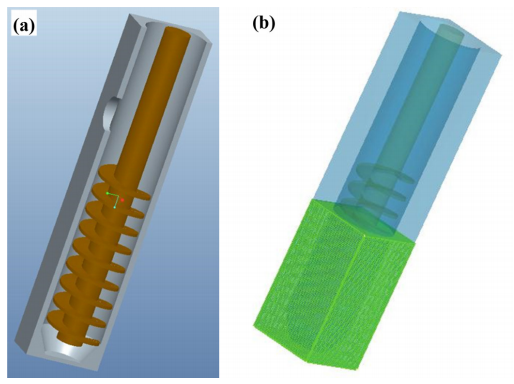
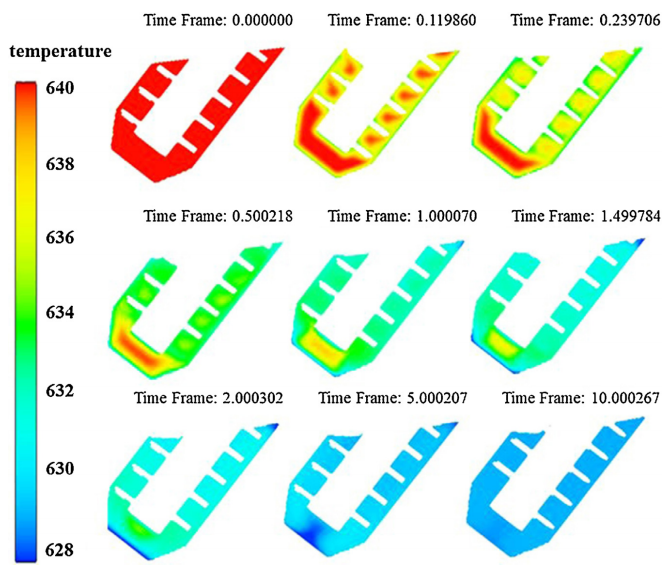
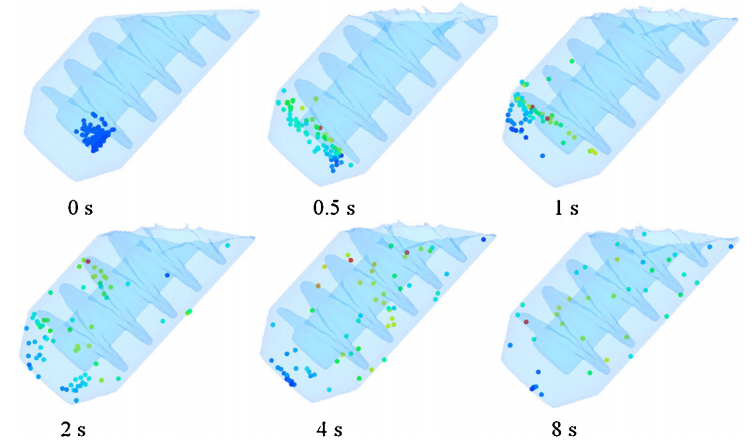
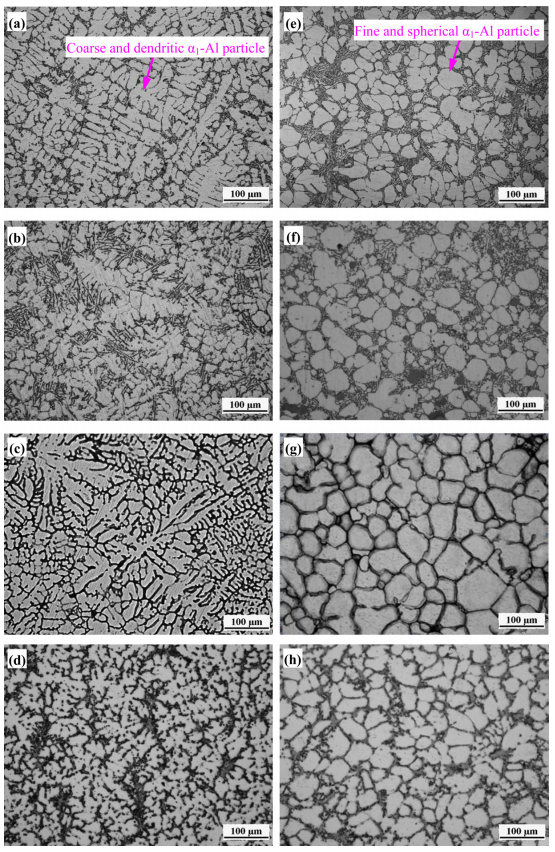
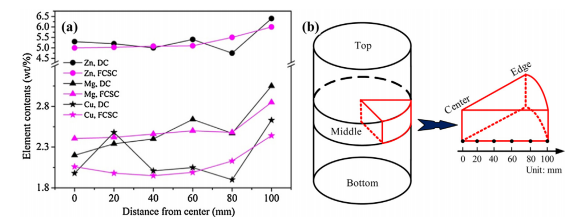
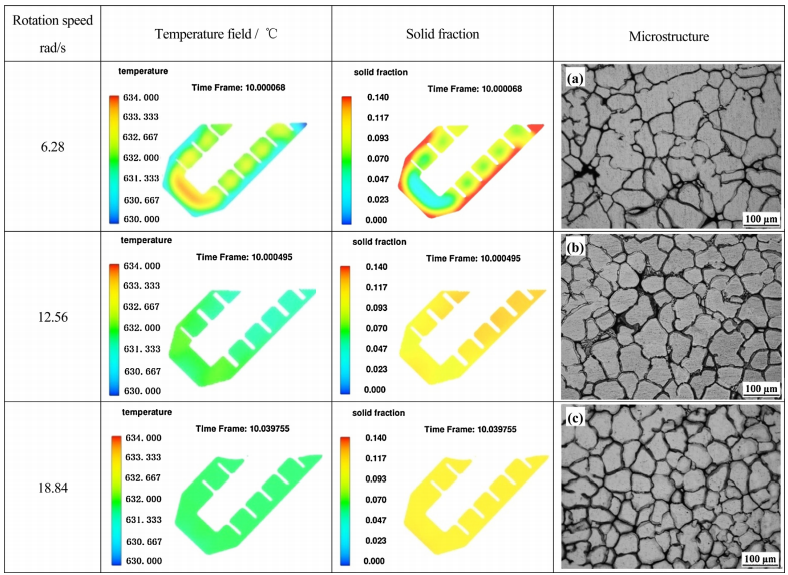
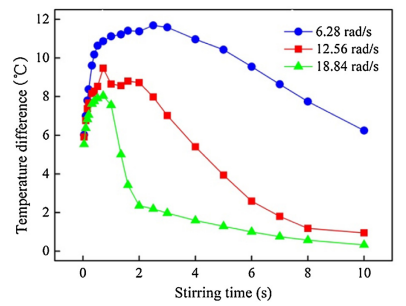
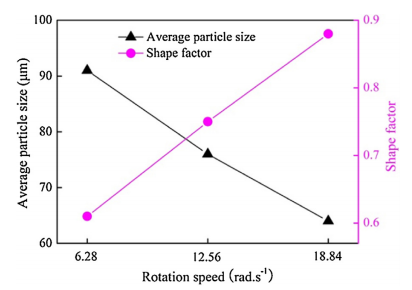
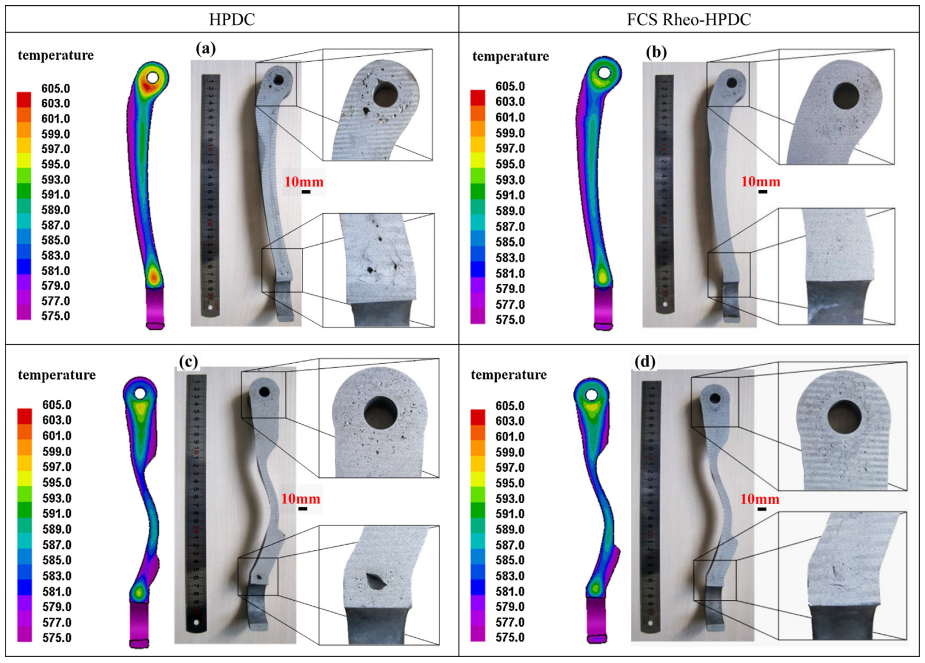
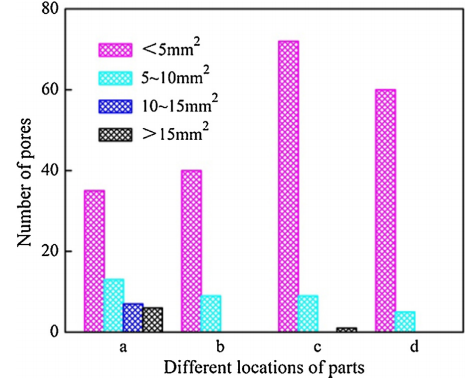
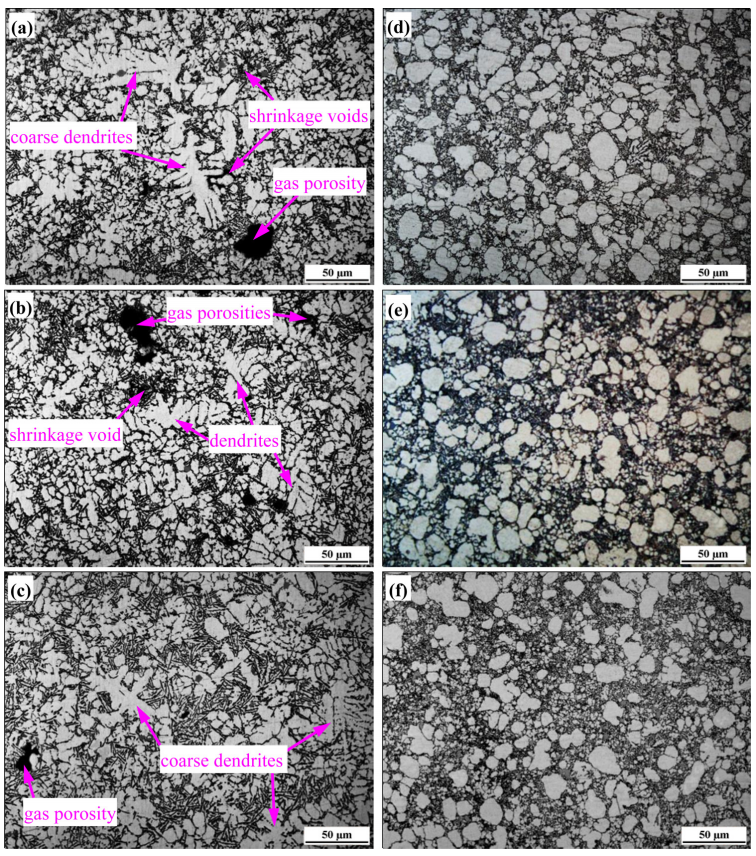
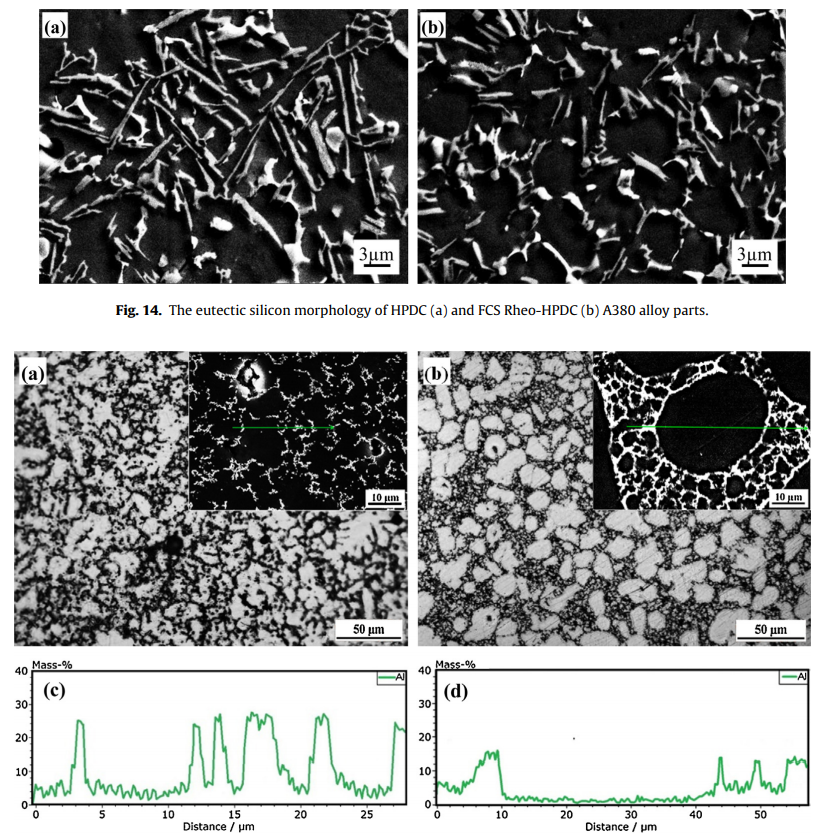
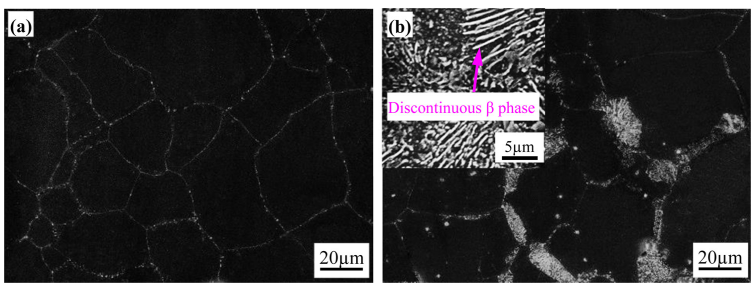
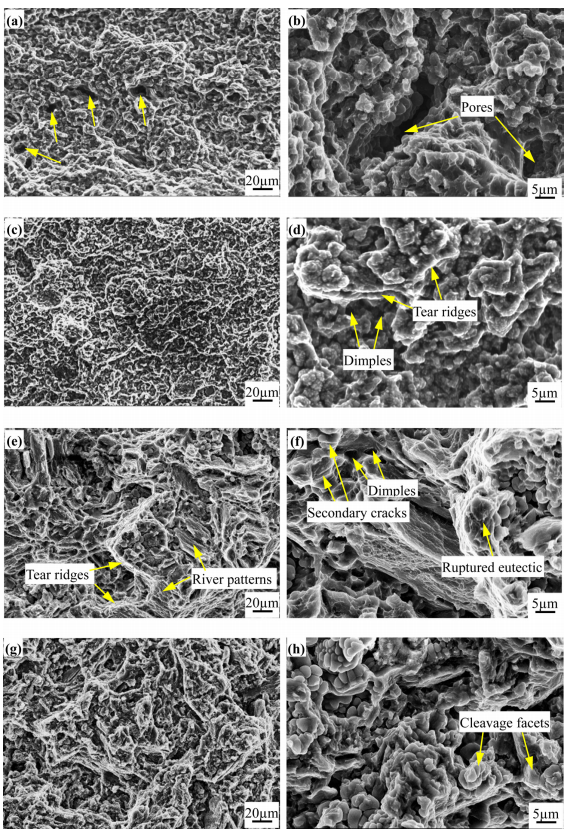
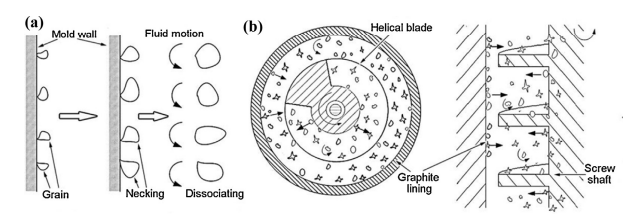
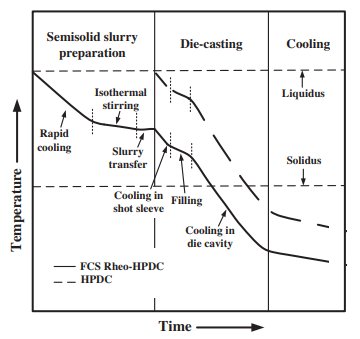
그림 이름 목록:
- Fig. 1 (FCS 장치)
- Fig. 4 (FCS 장치 내 용탕의 온도장)
- Fig. 5 (조성장 - 본문 참조에서 추론)
- Fig. 6 (FCS 주조(FCSC) 및 NC로 준비된 A356, A380, 7075 및 AZ91D 합금 잉곳의 미세구조)
- ...
7. 결론:
(1) 반용융 슬러리 제조를 위해 강제 대류 교반(FCS)이라는 단순화된 공정이 개발되었습니다. FCS 공정은 초정 입자가 미세하고 구형이며 액상 매트릭스에 균일하게 분산된 슬러리를 제조할 수 있습니다.
(2) 강한 대류는 용탕의 온도 및 조성 균일성을 빠르게 촉진하여 수지상정 형성 환경을 파괴하고 초정 입자의 양과 형태를 개선합니다.
(3) FCS 장치와 HPDC 기계를 결합하여 간단한 Rheo-HPDC 공정이 개발되었습니다. FCS Rheo-HPDC 부품의 다른 영역에서의 미세구조는 모두 미세한 구형 입자와 낮은 기공률(0.3-0.5%)로 구성됩니다. A356 합금 컨트롤 암의 경우, FCS Rheo-HPDC 부품의 총 기공 면적은 HPDC 부품에 비해 3배 감소했습니다.
(4) FCS Rheo-HPDC 부품은 HPDC 및 다른 Rheo-HPDC 기술로 형성된 부품보다 향상된 기계적 특성을 보이며, 극한 인장 강도(UTS), 항복 강도(YS) 및 연신율의 증가율은 HPDC 대비 10% 이상입니다.
8. 참고 문헌:
- C.H. Cáceres et al.Casting defects and the tensile properties of an A1-Si-mg alloyMater. Sci. Eng. A(1996)
- C.H. Cáceres et al.Effects of solidification rate and ageing on the microstructure and mechanical properties of AZ91 alloyMater. Sci. Eng. A(2002)
- Z.Z. Chen et al.Mechanical properties and microstructures of Al alloy tensile samples produced by serpentine channel pouring rheo-diecasting processNonferrous Met. Soc. China(2011)
- J.B. ClarkAge hardening in a Mg-9 wt% Al alloyActa Metall.(1968)
- D. Duly et al.On the competition between continuous and discontinuous precipitations in binary Mg-al alloysActa metal. Mater.(1995)
- M. Esmaily et al.Microstructural characterization of the Mg-al alloy AM50 produced by a newly developed rheo-casting processMater. Charact.(2014)
- Z. Fan et al.Microstructure and mechanical properties of rheo-diecast (RDC) aluminum alloysMater. Sci. Eng. A(2005)
- J.L. Fu et al.Modelling and simulation of die casting process for A356 semi-solid alloyProced. Eng.(2014)
- H.M. Guo et al.Pressurized solidification of semi-solid aluminum die casting alloy A356J. Alloys Compd.(2009)
- H.M. Guo et al.Formation of grain refined and non-dendritic microstructure of an aluminum alloy under angular oscillationJ. Alloys. Compd.(2009)
- J.F. Jiang et al.Microstructure and mechanical properties of the semisolid slurries and rheoformed component of nano-sized SiC/7075 aluminum matrix composite prepared by ultrasonic-assisted semisolid stirringMater. Sci. Eng. A(2015)
- C.K. Jin et al.Die design method for thin plates by indirect rheo-casting process and effect of die cavity friction and punch speed on microstructures and mechanical propertiesJ. Mater. Process. Technol.(2015)
- C. Lin et al.Microstructure and mechanical properties of rheo-diecast hypereutectic Al-si alloy with 2%Fe assisted with ultrasonic vibration processJ. Alloy. Comp.(2013)
- Z.Y. Liu et al.Preparation of semi-solid A380 aluminum alloy slurry by serpentine channelTrans. Nonferrous Met. Soc. China(2015)
- Y.D. Sui et al.Effect of solidification sequence on the microstructure and mechanical properties of die-cast Al-11Si-2Cu-fe alloyJ. Alloys Compd.(2015)
- J. Wannasin et al.Grain refinement of an aluminum alloy by introducing gas bubbles during solidificationScripta Mater.(2006)
- S.S. Wu et al.Microstructure and property of rheocasting aluminum alloy made with indirect ultrasonic vibration processMater. Lett.(2012)
- Y.F. Zhang et al.Mechanical properties of thixomolded AZ91D magnesium alloyJ. Mater. Process. Tech.(2009)
- J. Aguilar et al.Rheo-container-process (RCP): new semisolid forming method for light metal alloys
9. 저작권:
- 이 자료는 "Mingfan Qi, Yonglin Kang, Bing Zhou, Wanneng Liao, Guoming Zhu, Yangde Li, Weirong Li"의 논문입니다. "A forced convection stirring process for Rheo-HPDC aluminum and magnesium alloys" 논문을 기반으로 합니다.
- 논문 출처: https://doi.org/10.1016/j.jmatprotec.2016.04.003
이 자료는 위 논문을 바탕으로 요약되었으며, 상업적 목적의 무단 사용을 금지합니다.
Copyright © 2025 CASTMAN. All rights reserved.