이 소개 자료는 "[Journal of Magnesium and Alloys]"에 게재된 "[Progress and prospects in Mg-alloy super-sized high pressure die casting for automotive structural components]" 논문을 기반으로 작성되었습니다.
![Fig. 1. Mg-alloy super-sized die casting produced by Chongqing University, Millison Inc. and Boao Magnesium Aluminium Manufacturing Company Ltd. The geometry of the Mg-alloy super-sized castings has been withheld due to commercial confidentiality [5].](https://castman.co.kr/wp-content/uploads/image-2011-png.webp)
1. 개요:
- 논문 제목: Progress and prospects in Mg-alloy super-sized high pressure die casting for automotive structural components (마그네슘 합금 초대형 고압 다이캐스팅 자동차 구조 부품의 진전과 전망)
- 저자: Tian Li, Jiangfeng Song, Ang Zhang, Guoqiang You, Yan Yang, Bin Jiang, XianYue Qin, Cheng Xu, Fushen Pan
- 발행 연도: 2023
- 게재 학술지/학회: Journal of Magnesium and Alloys
- 키워드: Mg 합금(Mg alloy); 기가 캐스팅(Giga-casting); 고압 다이캐스팅(HPDC); 초대형(Super-sized).
2. 초록:
Tesla의 기가 캐스팅(Giga-Casting) 공정 도입 이후, 자동차 산업에서는 전기차 및 내연기관 차량의 경량화를 향상시킬 수 있는 상당한 잠재력 때문에 초대형 구조 부품 개념이 널리 받아들여졌습니다. 이러한 초대형 부품은 알루미늄 합금 밀도의 3분의 2, 강철 밀도의 4분의 1에 불과한 뛰어난 경량 특성을 가진 Mg 합금을 사용하여 더욱 경량화될 수 있습니다. 이 탁월한 속성은 구조적 무결성을 손상시키지 않으면서 상당한 중량 감소를 달성할 수 있는 매력적인 전망을 제공합니다. 본 리뷰는 Mg 합금 고압 다이캐스팅(HPDC) 공정에 대한 연구를 검토하여, Mg 합금을 초대형 자동차 HPDC 부품에 통합하는 미래 전망에 대한 통찰력을 제공합니다.
3. 서론:
기후 변화와 온실가스 배출에 대한 우려가 커지면서 자동차 산업은 특히 전기차(EV) 보급에 중점을 두고 있습니다. 그러나 EV는 주로 배터리 무게 때문에 동급 내연기관(ICE) 차량보다 무거워 차량 경량화가 중요해졌습니다. Tesla의 기가 캐스팅(Giga-Casting) 기술은 첨단 고압 다이캐스팅(HPDC) 공정으로, 초대형 단일 부품 구조재 생산을 가능하게 합니다. 이를 통해 Tesla는 171개의 부품을 단 2개의 차체 하부 주조품으로 통합하여 중량을 30%, 비용을 40% 절감했습니다[1]. 이러한 성공은 업계 전반에 걸쳐 초대형 부품 채택을 촉발했습니다. 동시에, 현재 사용되는 알루미늄 합금보다 더 가벼운 소재, 특히 지구상에서 가장 가벼운 구조용 금속인 마그네슘(Mg) 합금(밀도: Al의 약 2/3, 강철의 약 1/4)에 대한 관심이 증가하고 있습니다. Mg 합금은 구조적 무결성을 유지하면서 상당한 중량 감소 가능성을 제공합니다. 최근 충칭대학교, Millison Inc., Boao Magnesium Aluminium Manufacturing Company Ltd의 공동 연구를 통해 세계 최대 Mg 합금 자동차 다이캐스팅 부품(그림 1)을 성공적으로 시험 생산했으며, 이는 Al 합금 주물 대비 32%의 중량 감소를 보여주었습니다[5]. 본 리뷰는 대형 박육 자동차 부품용 Mg 합금 HPDC 공정을 검토하여 초대형 응용 분야에서의 잠재력과 과제를 탐구합니다.
4. 연구 요약:
연구 주제 배경:
자동차 산업은 특히 무거운 EV의 등장으로 효율성 및 환경 성능 개선을 위해 차량 중량 감소 압력에 직면해 있습니다. Tesla의 기가 캐스팅(Giga-Casting)으로 대표되는 초대형 구조 부품은 Al 합금을 사용하여 부품 통합, 비용 절감 및 경량화를 위한 길을 제시합니다. Mg 합금과 같은 더 가벼운 재료를 탐색함으로써 추가적인 중량 감소가 가능합니다.
기존 연구 현황:
Al 합금을 사용한 기가 캐스팅은 자동차 산업에서 점차 확립되고 있습니다[1, 2, 3, 4]. 자동차 응용 분야를 위한 Mg 합금 연구는 대형 구조 부품에 적합한 비열처리(NHT) 형태를 포함하여 주조성 및 연성과 같은 바람직한 특성을 가진 적합한 합금 시스템(예: AM, AZ, AJ, AE 시리즈)을 확인했습니다[6-11]. 합금 원소(Al, Si, Zn, Sr, Ca, RE)가 Mg 특성에 미치는 영향에 대한 연구가 수행되었습니다[12-40]. 용탕 처리 기술(탈가스, 플럭스 정련, 전자기/초음파/부유/여과와 같은 비플럭스 정련)은 Mg 합금 주조 품질에 중요한 것으로 알려져 있습니다[41-78]. Mg HPDC에서 흔히 발생하는 결함, 예를 들어 다이 솔더링(Al보다는 덜 심각함), 산화물 개재물/바이필름, 고온 균열 등이 연구되었습니다[79-132]. 주조 무결성을 개선하기 위해 진공 HPDC(VADC/SVDC) 및 VACURAL과 같은 고급 주조 기술이 사용됩니다[135-146]. 대형 Mg 합금 주물의 성공적인 시험 생산이 보고되었습니다[5, 그림 8].
연구 목적:
본 리뷰는 대형 박육 자동차 구조 부품을 위한 Mg 합금 고압 다이캐스팅(HPDC) 공정에 대한 기존 연구를 검토하는 것을 목표로 합니다. Mg 합금을 초대형 자동차 HPDC 부품에 통합하는 것의 실현 가능성, 이점, 과제 및 미래 전망에 대한 통찰력을 제공하고자 합니다.
핵심 연구 내용:
본 논문은 Mg 합금 초대형 HPDC와 관련된 몇 가지 주요 영역을 검토합니다:
- 적합한 Mg 합금: 대형 박육 NHT 구조 부품과 관련된 특성(주조성, 유동성, 연성, 내크리프성 등)에 초점을 맞춰 다양한 Mg 합금 시스템(Mg-Al-Si, Mg-Al-Zn, Mg-Al-Sr, Ca 함유, Mg-Al-RE)을 논의합니다[12-40].
- 용탕 처리: 탈가스 기술(불활성 가스 스파징, 활성 가스, 진공) 및 개재물 제거 방법(플럭스 정련, 전자기/초음파/기포 부상/여과와 같은 비플럭스 정련)을 포함하여 주조 전 Mg 합금 용탕 처리에 대한 필요성과 방법을 다룹니다[41-78].
- 주요 결함: Mg 합금 HPDC에서 발생하는 일반적인 결함, 즉 다이 솔더링(Al 합금과의 비교), Mg의 반응성 및 주조 난류로 인한 산화물 개재물 및 바이필름 형성, 고온 균열 현상(합금 조성 및 주조 조건의 영향)을 분석합니다[79-132].
- 주조 장비/기술: 대형 Mg 부품용 HPDC 기계 요구 사항(Al 대비 낮은 형체력 가능성 포함) 및 주조 품질 향상을 목표로 하는 진공/초진공 HPDC(VADC/SVDC) 및 VACURAL 기술과 같은 고급 공정을 검토합니다[2, 133-146].
- 현재 응용 및 잠재력: 기존 Mg 합금 HPDC 자동차 부품의 예시와 초대형 Mg 주물(예: 차체 하부 및 배터리 인클로저)의 최근 개발 동향을 제시하여 입증된 잠재력을 강조합니다[5, 17, 40, 133, 136, 147-152].
5. 연구 방법론
연구 설계:
본 연구는 포괄적인 문헌 검토입니다. 과학 논문, 기술 보고서 및 산업 간행물에서 얻은 기존 지식을 종합하고 평가합니다.
데이터 수집 및 분석 방법:
저자들은 Journal of Magnesium and Alloys, Materials Science and Engineering A, Metallurgical and Materials Transactions와 같은 동료 검토 저널, 학회 발표 자료, SAE 기술 논문과 같은 기술 문서, 특허 및 핸드북을 포함한 광범위한 출판 자료로부터 정보를 수집했습니다. 분석에는 주요 결과 요약, 경향 및 상관관계 식별(예: 합금 조성 대 특성/결함), 다양한 공정 및 재료 비교, 과제 강조, 수집된 증거를 기반으로 한 기술의 전반적인 진전 및 미래 잠재력 평가가 포함되었습니다.
연구 주제 및 범위:
본 연구는 초대형 자동차 구조 부품 생산을 위한 마그네슘(Mg) 합금에 고압 다이캐스팅(HPDC) 기술을 적용하는 데 구체적으로 초점을 맞춥니다. 범위는 다음과 같습니다:
- 적합한 Mg 합금의 선택 기준 및 특성 (NHT, 주조성, 연성).
- Mg 합금에 중요한 용탕 준비 기술 (탈가스, 정련).
- Mg HPDC와 관련된 주요 주조 결함 분석 (다이 솔더링, 산화물/바이필름, 고온 균열) 및 완화 방안.
- 주조 장비 및 고급 HPDC 공정 변형 평가 (대형 프레스, 진공 보조, VACURAL).
- 자동차 구조물, 특히 대규모 구조물에서 Mg 합금 HPDC의 현재 및 새로운 응용 분야 검토.
6. 주요 결과:
주요 결과:
- Mg 합금은 훨씬 낮은 밀도 덕분에 Al 합금에 비해 초대형 자동차 부품의 상당한 경량화 잠재력을 제공합니다 (예: 32% 감소 보고됨 [5]).
- Mg 합금은 HPDC에서 우수한 금형 충전 능력을 보여, 얇은 벽(최소 1.8mm)과 긴 충전 거리(최대 1.2m)를 가진 매우 큰 부품의 생산을 가능하게 합니다 [그림 8, 150].
- AE44와 같은 합금은 유동성, 강도 및 연성의 좋은 균형으로 구조 부품에 유망함을 보여줍니다 [39, 150, 그림 7]. 비열처리(NHT) 합금은 대형 구조 부품에 선호됩니다.
- Mg의 높은 반응성과 수소 흡수 민감성 때문에 고품질 Mg 주물을 생산하기 위해서는 효과적인 용탕 처리(탈가스 및 개재물 제거)가 필수적입니다 [41-78].
- Mg 합금은 HPDC에서 Al 합금에 비해 다이 솔더링에 대한 민감성이 현저히 낮아, 더 넓은 공정 창을 허용하고 더 얇은 단면의 주조를 용이하게 합니다 [88, 89].
- Mg의 높은 반응성은 HPDC의 난류 충전 중에 용탕을 산화 및 바이필름 결함 형성에 취약하게 만듭니다. 진공 HPDC(VADC/SVDC) 또는 VACURAL과 같은 특수 기술은 이를 완화할 수 있지만 초대형 부품에 대한 확장성 문제에 직면합니다 [90-105, 135-146].
- 고온 균열은 합금 조성(응고 범위, 공정상) 및 주조 조건(금형 온도, 냉각 속도, 개재물, 결정립 구조)에 의해 영향을 받는 잠재적 결함입니다. AZ91과 같은 일부 합금은 상대적으로 낮은 민감성을 보입니다 [표 2, 106-132].
- 낮은 밀도 때문에 동일 부피의 Mg 부품을 주조하는 데 Al 부품보다 낮은 형체력의 HPDC 기계가 필요할 수 있어 잠재적으로 장비 비용을 절감할 수 있습니다 [섹션 5.1].
- 여러 사례는 차체 하부 및 배터리 인클로저와 같은 초대형 부품에 대한 최근 시험을 포함하여 다양한 자동차 부품에 대한 Mg 합금 HPDC의 성공적인 적용을 보여줍니다 [그림 1, 그림 8, 40, 133, 147-152].
![Fig. 2. Microstructure of AZ91D with and without degassing under different casting conditions [41].](https://castman.co.kr/wp-content/uploads/image-2012-png.webp)
![Fig. 3. the die soldering issue occurred during a 1.6 mm ultra-thin-walled HPDC test [86].](https://castman.co.kr/wp-content/uploads/image-2013-png.webp)
![Fig. 4. Sketch of a surface-film entrainment event in a light alloy casting [44,99].](https://castman.co.kr/wp-content/uploads/image-2014-png.webp)
![Fig. 5. Sketch of VACURAL Technology [145].](https://castman.co.kr/wp-content/uploads/image-2015-png.webp)
![Fig. 6. Sketch of the casting technique used by Gibbs Die Casting to cast Mg alloys [144].](https://castman.co.kr/wp-content/uploads/image-2016-png.webp)
![Fig. 7. A shock tower cast using AE44 alloy, dimensions 571 mm × 210 mm × 352 mm. (a) Appearance of the shock tower, with numbers denoting test bar sampling locations. (b) Tensile properties of the shock tower cast at different switchover positions of 560 mm, 580 mm, 600 mm [150].](https://castman.co.kr/wp-content/uploads/image-2017-png.webp)
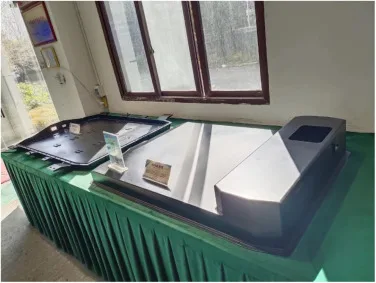
그림 및 표 목록:
- 그림 1. 충칭대학교, Millison Inc., Boao Magnesium Aluminium Manufacturing Company Ltd가 생산한 Mg 합금 초대형 다이캐스팅. Mg 합금 초대형 주물의 형상은 상업적 기밀 유지로 인해 공개되지 않았습니다 [5].
- 그림 2. 다양한 주조 조건에서 탈가스 처리 유무에 따른 AZ91D의 미세 구조 [41].
- 표 1. 다양한 온도에서의 마그네슘 증기압 [49].
- 그림 3. 1.6mm 초박벽 HPDC 시험 중 발생한 다이 솔더링 문제 [86].
- 그림 4. 경합금 주조에서의 표면 필름 혼입 현상 스케치 [44, 99].
- 표 2. 다양한 상용 Mg 합금의 고온 균열 등급. 등급이 높을수록 HTS(고온 균열 민감성)가 높음을 나타냅니다 [114].
- 그림 5. VACURAL 기술 스케치 [145].
- 그림 6. Gibbs Die Casting에서 Mg 합금 주조에 사용된 주조 기술 스케치 [144].
- 그림 7. AE44 합금을 사용하여 주조된 쇼크 타워, 치수 571mm x 210mm x 352mm. (a) 쇼크 타워 외관, 숫자는 시험편 샘플링 위치를 나타냄. (b) 560mm, 580mm, 600mm의 다른 전환 위치에서 주조된 쇼크 타워의 인장 특성 [150].
- 그림 8. Chongqing Qianhe Magnesium Tech Co.에서 주조한 Mg 합금 배터리 인클로저 부품, 두께 1.8mm, 크기 1.2m * 0.8m.
7. 결론:
차량 경량화에 대한 요구가 증가함에 따라 Mg 합금은 자동차 산업, 특히 HPDC로 생산되는 초대형 구조 부품의 새로운 트렌드에서 매우 매력적인 소재로 부상하고 있습니다. 본 리뷰는 이러한 맥락에서 Mg 합금 활용의 중요한 측면들을 강조했습니다. Mg 합금은 뛰어난 금형 충전 능력을 가지고 있어 긴 충전 거리(예: 1.2m)에 걸쳐 얇은 벽(예: 1.8mm)을 가진 매우 큰 부품의 주조를 가능하게 합니다. 그러나 이러한 초대형 부품의 일관된 품질을 보장하기 위해서는 잠재적 결함(산화물, 바이필름, 고온 균열 등)과 미세 구조 특징에 대한 효과적인 제어가 필요하며, 이는 용탕 처리 및 주조 공정 변수의 신중한 관리를 요구합니다. 전반적으로 Mg 합금은 초대형 자동차 부품 생산에 상당한 잠재력을 보여주며 상당한 경량화 이점을 제공하지만, 이 잠재력을 완전히 실현하고 관련 과제를 해결하기 위해서는 추가적인 연구 개발이 필요합니다.
8. 참고문헌:
- [1] E. Musk, Tesla 2020 Annual Meeting of Stockholders and Battery Day, 2020.
- [2] T.A. Baser, E. Umay, V. Akıncı, in: International Conference on Technology, Engineering and Science, 2022, pp. 79-87.
- [3] H. Nakajima, Toyota Technical Workshop, Toyota Motor Corporation, Toyota City, Japan, 2023.
- [4] I. Dnistran, Toyota Showcases its Own Giga Casting in a Bid to Lower EV Costs, 2023 [cited 2023 3rd Aug] Available from: https://insideevs.com/news/671943/toyota-giga-casting/.
- [5] Z. Tong, South China Morning Post, South China Morning Post, Singapore, 2023.
- [6] Das, S.K., H.W. Hayden, and G.B. Barthold, Development of Non-Heat-Treatable Automotive Aluminum Sheet Alloys. 2000. p. 913-919.
- [7] A.W. Shah, et al., Int. J. Metalcast. (2023).
- [8] X.Z. Zhu, et al., J. Mater. Sci. 56 (18) (2021) 11083-11097.
- [9] RHEINFELDEN-ALLOYSHandbook Die Casting Aluminium Alloys, 2023 Alloys for Pressure Die Casting 2016 [citedAug 14]; Available from: https://rheinfelden-alloys.eu/wp-content/uploads/2017/01/Handbook-Die-Casting-Aluminium-Alloys_RHEINFELDEN-ALLOYS_2016_EN.pdf.
- [10] AlcoaAlcoa Specialty Alloys: C611 EZCastTM, 2022 [cited 2023 Aug 14]; Available from: https://www.alcoa.com/global/en/what-we-do/aluminum/cast-products/pdfs/ALC-C611-EzCast-SellSheet.pdf .
- [11] AlcoaAlcoa Specialty Alloys: C891F EZCastPlusTM, 2022 [cited 2023 Aug 14]; Available from: https://www.alcoa.com/global/en/what-we-do/aluminum/cast-products/pdfs/ALC-C891F-EzCastPlus-SellSheet.pdf.
- [12] A.L. Bowles, Q. Han, J.A. Horton, TMS (2005) 99-104.
- [13] Y.-Z. Lü, Q.-D. Wang, X.-Q. Zeng, W.-J. Ding, Y.-P. Zhu, Mater. Sci. Technol 17 (2) (2013) 207-214.
- [14] M. Pekguleryuz, M. Celikin, Int. Mater. Rev. 55 (4) (2013) 197-217.
- [15] S. Candan, E. Candan, Trans. Nonferrous Metals Soc. China 27 (8) (2017) 1725-1734.
- [16] A. LUO, M.O. Pekguleryuz, J. Mater. Sci. 29 (1994) 5259-5271.
- [17] J.P. Weiler, J. Magnes. Alloys 9 (1) (2021) 102-111.
- [18] Q.C. Jiang, et al., Mater. Sci. Eng.: A 392 (1-2) (2005) 130-135.
- [19] L.Y. Wei, G.L. Dunlop, H. Westengen, Mater. Sci. Technol. 12 (9) (1996) 741-750.
- [20] M. Easton, et al., Mater. Sci. Forum 828-829 (2015) 3-8.
- [21] M.O. Pekguleryuz, M.M. Avedesian, Inst. Magnes. Technol. 42 (12) (1992) 679-686.
- [22] V.E. Bazhenov, et al., J. Magnes. Alloys 9 (5) (2021) 1567-1577.
- [23] V.E. Bazhenov, et al., J. Magnes. Alloys 8 (1) (2020) 184-191.
- [24] G. Chen, et al., Trans. Nonferrous Metals Soc. China 21 (4) (2011) 725-731.
- [25] K. Hirai, et al., Mater. Sci. Eng.: A 403 (1-2) (2005) 276-280.
- [26] C. Jingyang, et al., Spec. Cast. Nonferrous Alloys 8 (2005) 454.
- [27] H.L. Zhao, S.K. Guan, F.Y. Zheng, J. Mater. Res. 22 (9) (2011) 2423-2428.
- [28] Y. Turen, Mater. Des. 49 (2013) 1009-1015.
- [29] E. Baril, P. Labelle, M.O. Pekguleryuz, Res. Summary 55 (2003) 34-39.
- [30] M.H. Kim, et al., Mater. Sci. Forum 419-422 (2003) 575-580.
- [31] S.-Y. Chang, J.-C. Choi, Met. Mater. 4 (2) (1998) 165-171.
- [32] C.D. Yim, et al., J. Mater. Sci. (8) (2006) 41.
- [33] Y. Nakaura, A. Watanabe, K. Ohori, Mater. Trans. 47 (4) (2006) 1031-1039.
- [34] Y. Fu, et al., J. Rare Earths 35 (5) (2017) 503-509.
- [35] Y. Cui, et al., Materials 13 (16) (2020).
- [36] Y. Lu, et al., Mater. Sci. Eng. A 278 (2000) 66-76.
- [37] W.Q. dong, et al., Trans. Nonferrous Metals Soc. China 02 (2000) 235-239.
- [38] Q. Hua, et al., Mater. Sci. Eng.: A 444 (1-2) (2007) 69-74.
- [39] T. Rzychoń, et al., Mater. Charact. 60 (10) (2009) 1107-1113.
- [40] B. Liu, et al., J. Magnes. Alloys 11 (1) (2023) 15-47.
- [41] E. Zhang, G.J. Wang, Z.C. Hu, Mater. Sci. Technol. 26 (10) (2010) 1253-1258.
- [42] Z.C. Hu, E.L. Zhang, S.Y. Zeng, Mater. Sci. Technol. 24 (11) (2008) 1304-1308.
- [43] A. Elsayed, et al., Trans. Am. Foundry Soc. 120 (2012) 423-429, Vol 120.
- [44] T. Li, J.M.T. Davies, D. Luo, Metall. Mater. Trans. B-Process Metall. Mater. Process. Sci. 52 (5) (2021) 3093-3106.
- [45] S.E. Housh, V. Petrovich, SAE Technical Paper, 920071, SAE international, Warrendale, Pa, USA, 1992.
- [46] S.E. Housh, V. Petrovich, Magnesium Refining: A Fluxless Alternative, 1992 SAE Technical Paper.
- [47] J. Thomson, et al., Transactions of the American Foundry Society and the One Hundred Eighth Annual Metalcasting Congress, 2004.
- [48] E.F. Emley, Metals Technol. 3 (1) (1976) 118-127.
- [49] S. Bell, et al., the Minerals and Metals Sector of Natural Resources Canada, 2006.
- [50] Y. Luo, Appl. Math. Model. 37 (9) (2013) 6177-6182.
- [51] T. Watanabe, et al., J. Jpn. Inst. Light Metals 26 (6) (1976) 266-272.
- [52] H.X. Cao, et al., J. Magnes. Alloys 7 (3) (2019) 370-380.
- [53] L.F. Zhang, T. Dupont, State of the Art in the Refining and Recycling of Magnesium, 2007 p. 25-+.
- [54] F. Pan, et al., J. Magnes. Alloys 4 (1) (2016) 8–14.
- [55] J. Wu, et al., Mater. Res. Express 9 (3) (2022) 032001.
- [56] Moon, B.G., B.S. You, and Koh. Kiho, in Magnesium Technology 2013, N. Hort, et al., Editors. 2013, John Wiley & Sons: New Jersey.
- [57] S.M. Patel, M.M. Patel, V.J. Rao, Mater. Res. Express 8 (11) (2021).
- [58] S.M. Patel, M.M. Patel, V.J. Rao, Mater. Res. Express 8 (11) (2021) 116503.
- [59] F.S. Pan, et al., J. Magnes. Alloys 4 (1) (2016) 8-14.
- [60] G.-h. Wu, et al., Trans. Nonferrous Metals Soc. China 20 (11) (2010) 2037-2045.
- [61] N. El-Kaddah, A.D. Patel, T.T. Natarajan, JOM 47 (5) (1995) 46-49.
- [62] N. Balasubramani, et al., J. Magnes. Alloys 9 (3) (2021) 829-839.
- [63] A. Kumar, P.M. Pandey, J. Magnes. Alloys 9 (6) (2021) 1989-2008.
- [64] Y. Chen, et al., J. Magnes. Alloys 10 (3) (2022) 614-626.
- [65] P. Emadi, B. Andilab, C. Ravindran, J. Magnes. Alloys 10 (12) (2022) 3397-3405.
- [66] H. Peng, et al., J. Magnes. Alloys 8 (2) (2020) 552-563.
- [67] A.R. Eivani, et al., J. Magnes. Alloys 9 (4) (2021) 1304-1328.
- [68] X. Ding, et al., J. Magnes. Alloys 11 (3) (2023) 903-915.
- [69] J.Y. Zhang, et al., J. Magnes. Alloys 9 (4) (2021) 1187-1200.
- [70] G.I. Eskin, Ultrason. Sonochem. 8 (3) (2001) 319-325.
- [71] Y.J. Chen, W.N. Hsu, J.R. Shih, Mater. Trans. 50 (2) (2009) 401-408.
- [72] Z.W. Shao, et al., Met. Mater. Int. 18 (2) (2012) 209-215.
- [73] Z.-W. Shao, et al., Trans. Nonferrous Metals Soc. China 20 (2010) s382-s387.
- [74] M. Khosro Aghayani, B. Niroumand, J. Alloys Compd. 509 (1) (2011) 114-122.
- [75] V. PETROVICH, W. MERCER E., W. GREEN, Patentscope, Espacenet, E.P. Office, Editor, U.S, 1993.
- [76] J. Zha, et al., in: Manufacturing Science and Technology, Pts 1-3, Р.С. Wang, 2011, pp. 2151-2154. Editors.
- [77] J. Wang, et al., Trans. Nonferrous Metals Soc. China 20 (7) (2010) 1235-1239.
- [78] J.L. Zha, et al., Adv. Mat. Res. 295-297 (2011) 2151-2154.
- [79] H. Huang, et al., Int. J. Cast Met. Res. 26 (4) (2013) 213-219.
- [80] Y.L. Li, et al., J. Mater. Sci. Technol. 33 (6) (2017) 558-566.
- [81] A. Juriani, Casting Defects Analysis in Foundry and Their Remedial Measures with Industrial Case Studies, 2015.
- [82] Akhyar, et al., Metalurgija 61 (2) (2022) 309-312.
- [83] Q.Y. Han, China Foundry 12 (2) (2015) 136-143.
- [84] S. Shankar, D. Apelian, Metall. Mater. Trans. B-Process Metall. Mater. Process. Sci. 33 (3) (2002) 465-476.
- [85] Z.W. Chen, Mater. Sci. Eng. a-Struct. Mater. Properties Microstruct. Process. 397 (1-2) (2005) 356-369.
- [86] Z.C. Niu, et al., J. Mater. Process. Technol. (2022) 303.
- [87] D. Schwam, A. Miller, Thin-Wall and High-Strength Die Casting Alloys, Defence Technical Information Center, 2017.
- [88] A.L. Bowles, Q. Han, J.A. Horton, et al., in: S.N. Mathaudhu, et al. (Eds.), Essential Readings in Magnesium Technology, Springer International Publishing, Cham, 2016, pp. 187-192. Editors.
- [89] C. Tang, M.Z. Jahedi, M. Brandt, the 6th International Tooling Conference, Karlstad Univ, Karlstad, Sweden, 2002.
- [90] M.M. Jalilvand, et al., J. Magnes. Alloys 8 (1) (2020) 219-230.
- [91] C.L. Cheng, et al., J. Magnes. Alloys 8 (4) (2020) 1281-1295.
- [92] S. Ma, et al., J. Magnes. Alloys 8 (3) (2020) 819-831.
- [93] M.M. Jalilvand, et al., J. Magnes. Alloys 10 (6) (2022) 1704-1717.
- [94] W.D. Griffiths, N.W. Lai, Metall. Mater. Trans. a-Phys. Metall. Mater. Sci. 38A (1) (2007) 190-196.
- [95] T. Li, W.D. Griffiths, J. Chen, Metall. Mater. Trans. a-Phys. Metall. Mater. Sci. 48A (11) (2017) 5516-5528.
- [96] T. Li, J.M.T. Davies, X. Zhu, J. Mater. Sci. 56 (29) (2021) 16671-16685.
- [97] T. Li, J.M.T. Davies, X.Z. Zhu, J. Magnes. Alloys 10 (1) (2022) 129-145.
- [98] C. Cingi, Mold-metal Reactions in Magnesium Investment Castings, Helsinki University of Technology, 2006.
- [99] J. Campbell, Castings, Butterworth-Heinemann, Oxford, 2004.
- [100] A.R. Mirak, et al., Int. J. Cast Met. Res. 20 (4) (2007) 215-220.
- [101] T. Li, J.M.T. Davies, Metall. Mater. Trans. A 51 (10) (2020) 5389-5400.
- [102] D. Dispinar, J. Campbell, Int. J. Cast Met. Res. 19 (1) (2006) 5–17.
- [103] I.H. Kalkan, et al., Shape Casting, Springer International Publishing, Cham, 2019.
- [104] J. Olofsson, A. Bjurenstedt, S. Seifeddine, Shape Casting, Springer International Publishing, Cham, 2019.
- [105] X. Li, S.M. Xiong, Z. Guo, J. Mater. Process. Technol. 231 (2016) 1-7.
- [106] G. Cao, I. Haygood, S. Kou, Metall. Mater. Trans. a-Phys. Metall. Mater. Sci. 41A (8) (2010) 2139-2150.
- [107] G. Cao, et al., Metall. Mater. Trans. a-Phys. Metall. Mater. Sci. 41A (3) (2010) 706-716.
- [108] Z.S. Zhen, et al., Int. J. Cast Met. Res. 22 (1-4) (2009) 331-334.
- [109] X.D. Du, et al., J. Magnes. Alloys 11 (2) (2023) 694-705.
- [110] Y. Zhou, et al., J. Magnes. Alloys 8 (4) (2020) 1176-1185.
- [111] G.J. Zhang, et al., J. Magnes. Alloys 7 (2) (2019) 272-282.
- [112] Z.Z. Yang, et al., J. Magnes. Alloys 6 (1) (2018) 44-51.
- [113] Q.S. Yang, et al., J. Magnes. Alloys 2 (1) (2014) 8-12.
- [114] J.F. Song, et al., J. Magnes. Alloys 4 (3) (2016) 151-172.
- [115] K. Strobel, et al., Int. J. Cast Met. Res. 23 (2) (2010) 81-91.
- [116] X. Su, et al., Int. J. Metalcast. 15 (2) (2021) 576-586.
- [117] G. Cao, S. Kou, Mater. Sci. Eng. a-Struct. Mater. Properties Microstruct. Process. 417 (1-2) (2006) 230-238.
- [118] Z.S. Zhen, et al., Light Metals Technol. 618-619 (2009) 533-540.
- [119] L. Zhou, et al., Int. J. Cast Met. Res. 24 (3-4) (2011) 170-176.
- [120] L. Zhou, et al., Magnes. Technol. 2011 (2011) 125-130.
- [121] J.F. Song, et al., Metall. Mater. Trans. a-Phys. Metall. Mater. Sci. 46A (12) (2015) 6003-6017.
- [122] A. Srinivasan, et al., Trans. Indian Inst. Met. 65 (6) (2012) 701-706.
- [123] M.A. Easton, et al., Metall. Mater. Trans. a-Phys. Metall. Mater. Sci. 45A (8) (2014) 3586-3595.
- [124] Z. Wang, et al., Metall. Mater. Trans. a-Phys. Metall. Mater. Sci. 46A (5) (2015) 2108-2118.
- [125] G. Cao, S. Kou, Metall. Mater. Trans. a-Phys. Metall. Mater. Sci. 37A (12) (2006) 3647-3663.
- [126] G. Zhang, et al., Materwiss Werksttech 50 (12) (2019) 1471-1483.
- [127] S.K. Rathi, A. Sharma, M. Di Sabatino, Eng. Fail. Anal. 79 (2017) 592-605.
- [128] L. Bichler, et al., Int. J. Metalcast. 2 (1) (2008) 43-56.
- [129] Z. Wang, et al., J. Mater. Sci. 49 (1) (2014) 353-362.
- [130] S. Li, D. Apelian, Int. J. Metalcast. 5 (1) (2011) 23-40.
- [131] J.M. Middleton, H.T. Protheroe, J. Iron Steel Institute 168 (4) (1951) 384-398.
- [132] G.H. Wu, et al., Acta Metall. Sinica 58 (4) (2022) 385-399.
- [133] Sophia, F., et al., in Magnesium Alloys, T. Tomasz Arkadiusz, C.-A. Katarzyna, and J. Ewa, Editors. 2023, IntechOpen: Rijeka. p. Ch. 2.
- [134] HPMMACHINERYHPM North America to Build 4500 Ton Die Cast Machine [cited 2023 Nov 19th]; Available from:, 2015. https://www.yizumi-hpm.com/hpm-north-america-to-build-4500-ton-die-cast-machine/.
- [135] H. Cao, et al., Vacuum 146 (2017) 278-281.
- [136] A.A. Luo, A.K. Sachdev, D. Apelian, J. Mater. Process. Technol. (2022) 306.
- [137] Cosma-International. Aluminum high pressure die casting. [cited 2023 18 Aug]; Available from: https://www.magna.com/docs/default-source/default-document-library/cosma_casting_brochure_english.pdf?sfvrsn=0.
- [138] T. Le, et al., Mater. Res. Express 7 (11) (2020) 116513.
- [139] X. Liu, et al., J. Mater. Res. Technol. 23 (2023) 4293-4306.
- [140] C. Ma, et al., J. Magnes. Alloys 11 (2) (2023) 753-761.
- [141] Z.-q. Wang, et al., Trans. Nonferrous Metals Soc. China 24 (12) (2014) 3762-3768.
- [142] X. Dong, X. Zhu, S. Ji, J. Mater. Process. Technol. 266 (2019) 105-113.
- [143] V. Nandakumar, Process and Tool Design for the High Integrity Die Casting of Aluminum and Magnesium Alloys, The Ohio State University, 2014.
- [144] A.A. Luo, J. Magnes. Alloys 1 (1) (2013) 2-22.
- [145] FRECH, Vacural Technol. (2023) [cited 2023 18th Aug]; Available from: https://www.frechusa.com/vacural-technology.
- [146] Foundry-Lexicon, Vacural Process (2023) [cited 2023 18 Aug]; Available from: https://www.giessereilexikon.com/en/foundry-lexicon/Encyclopedia/show/vacural-process-4629/?cHash=fa70abc99c24ba84803fb708ad2266a7.
- [147] J.P. Weiler, J. Magnes. Alloys 7 (2) (2019) 297-304.
- [148] M. Abate, M. Willman, Use of Cast Magnesium Back frames in Automotive Seating, 2005 SAE Technical Paper.
- [149] J.P. Weiler, Contemporary Magnesium Die-Casting Research and Technology: A Canadian Viewpoint, Springer International Publishing, Cham, 2021.
- [150] W. Xueyang, et al., Spec. Cast. Nonferrous Alloys 42 (04) (2022) 467-472.
- [151] X. Chen, et al., Cast Magnesium Subframe Development-Bolt Load Retention, 2021 SAE Technical Paper.
- [152] J. Aragones, et al., Development of the 2006 Corvette z06 Structural Cast Magnesium Crossmember, 2005 SAE Technical Paper.
9. 저작권:
- 이 자료는 "Tian Li 외"의 논문입니다. "[Progress and prospects in Mg-alloy super-sized high pressure die casting for automotive structural components]"를 기반으로 합니다.
- 논문 출처: https://doi.org/10.1016/j.jma.2023.11.003
이 자료는 상기 논문을 바탕으로 요약된 것으로, 상업적 목적의 무단 사용을 금합니다.
Copyright © 2025 CASTMAN. All rights reserved.