본 소개 자료는 [MDPI]에서 발행한 ["Manufacturing of Aluminum Alloy Parts from Recycled Feedstock by PIG Die-Casting and Hot Stamping"] 논문의 연구 내용입니다.
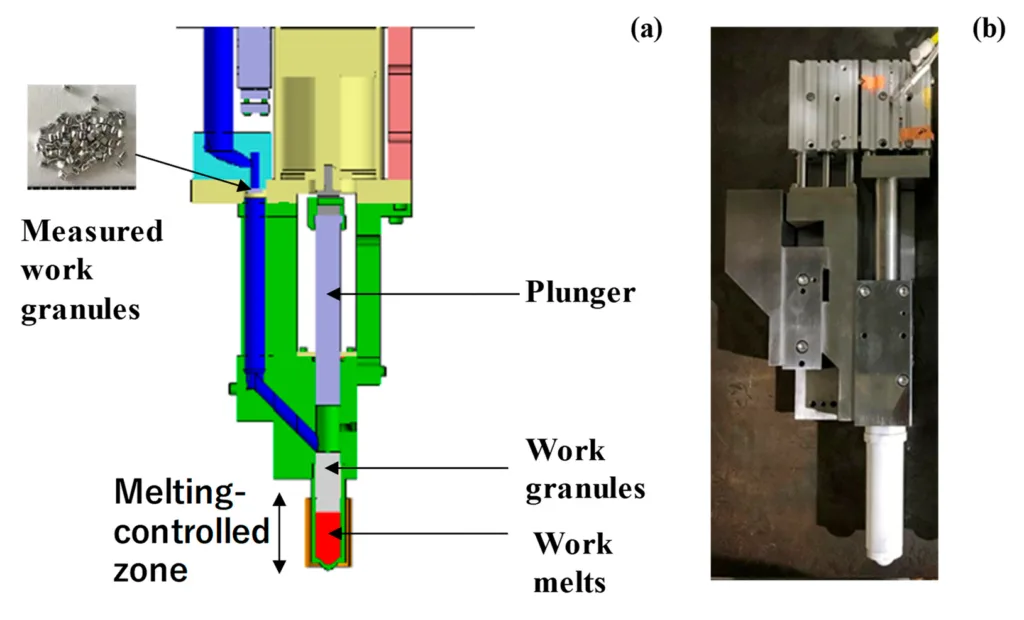
1. 개요:
- 제목: Manufacturing of Aluminum Alloy Parts from Recycled Feedstock by PIG Die-Casting and Hot Stamping (재활용 원료를 PIG 다이캐스팅 및 핫 스탬핑으로 가공하여 알루미늄 합금 부품 제조)
- 저자: Tatsuhiko Aizawa, Takeshi Kurihara and Hiroki Sakayori
- 출판 연도: 2022
- 게재 저널/학회: Lubricants
- 키워드: upward recycling(상향 재활용); aluminum and aluminum alloys(알루미늄 및 알루미늄 합금); pin injection gate(핀 인젝션 게이트); die casting(다이캐스팅); hot stamping(핫 스탬핑); mechanical parts(기계 부품); heatsink(히트싱크); nitrogen supersaturation(질소 과포화); TiAlN coating(TiAlN 코팅)
2. 초록
PIG (Pin-Injection-Gate) 다이캐스팅 및 핫 스탬핑은 재활용 원료로부터 소형 및 박벽 알루미늄 합금 부품을 제조하기 위해 개발되었습니다. 순수 알루미늄 및 알루미늄 합금 과립이 재활용 재료의 공급 원료 모델로 활용되었습니다. 제품의 3D-CAD (Computer Aided Design)에서 추정된 중량으로 측정된 과립 질량은 사출 전에 PIG 노즐에 부어졌습니다. PIG 노즐 장치 내부에서 유도 가열에 의해 빠르게 용융된 후, 알루미늄 용융물은 PIG 노즐을 통해 다이 캐비티에 주입되었습니다. 기존 다이캐스팅 시스템과 달리 용융 알루미늄 스톡을 보관하기 위한 용광로와 도가니가 필요하지 않았습니다. 거대한 로딩 머신을 사용한 클램핑 메커니즘도 필요하지 않아 주조 시 에너지 소비를 크게 줄였습니다. 이러한 공정에서는 폐기물이 훨씬 적게 발생했습니다. 제품 대 폐기물 비율, 즉 재료 효율은 거의 100%였습니다. 질소 과포화 및 TiAlN 코팅은 알루미늄 용융물로부터의 심각한 부착으로부터 PIG 노즐 및 스탬핑 다이 표면을 보호하는 데 사용되었습니다. 순수 알루미늄 기어와 박벽 휴대폰 케이스가 이 공정으로 제작되었습니다. X선 단층 촬영을 통해 두 제품 모두 내부에 공동, 기공 및 수축이 없는 것으로 나타났습니다. 핫 스탬핑 장치를 사용하여 마이크로 필라형 순수 알루미늄 히트싱크를 제작하여 마이크로 필라 높이 대 너비의 종횡비에 대한 유지 온도 효과를 조사했습니다.
3. 연구 배경:
연구 주제 배경:
탄소 중립적인 지속 가능한 사회에서 친환경 제조는 점점 더 중요해지고 있습니다[1]. 고체 상태 재활용은 재용해 없이 사용된 알루미늄 합금을 재처리하는 방법을 제공합니다[2].
선행 연구 현황:
이전 연구에는 알루미늄 합금 파편의 웜 및 핫 압출과 같은 고체 상태 재활용 방법이 포함됩니다[3]. 기존 다이캐스팅[4]은 네트 쉐이핑에 효과적이지만 에너지 집약적입니다. 기존 PIG 다이캐스팅 시스템은 특히 소형 및 박벽 부품에 대한 기존 다이캐스팅의 몇 가지 한계를 해결합니다[5-7].
연구 필요성:
기존 다이캐스팅은 대형 용광로와 상당한 클램핑력이 필요하여 높은 에너지 소비와 재료 낭비로 이어집니다. 특히 알루미늄 재활용을 위해서는 보다 효율적인 공정이 필요합니다.
4. 연구 목적 및 연구 질문:
연구 목적:
재활용 공급 원료로부터 알루미늄 합금 부품을 효율적으로 생산하기 위해 핫 스탬핑과 통합된 고급 PIG 다이캐스팅 시스템을 개발합니다.
핵심 연구:
폐기물을 최소화하고 재료 효율성을 높여 소형, 박벽 및 미세 텍스처 알루미늄 부품을 생산하는 통합 PIG 다이캐스팅 및 핫 스탬핑 시스템의 기능을 입증합니다.
5. 연구 방법
본 연구에서는 PIG 다이캐스팅과 핫 스탬핑 시스템을 결합하여 사용했습니다.
-연구 설계: PIG 다이캐스팅과 핫 스탬핑을 결합한 실험적 연구.
-데이터 수집:
- 공급 원료의 무게 측정.
- 유도 가열 중 온도 모니터링.
- 자유 사출의 고속 비디오 녹화.
- 흐름 분석을 위한 쇼트 샷 실험.
- 결함 분석을 위한 X선 단층 촬영.
- 표면 텍스처 측정을 위한 레이저 현미경 및 프로파일로미터.
- 원소 조성을 분석을 위한 SEM-EDX.
- 마이크로 비커스 경도 시험.
-분석: - 흐름 패턴의 시각적 분석.
- 사출 속도의 정량적 분석.
- 주조 및 스탬핑된 부품의 치수 분석.
- X선 단층 촬영을 통한 결함 분석.
- 질화 표면의 마찰 특성 분석.
-재료: - 순수 알루미늄(99.7% 순도) 과립.
- AA5052 알루미늄 합금 입자.
- PIG 노즐 및 주조 다이용 AISI420J2.
- 웜/핫 스탬핑 다이용 AISI316.
-표면 처리: - 저온 플라즈마 질화.
- TiAlN 코팅.
- 미세 텍스처링을 위한 플라즈마 프린팅.
-범위: 순수 알루미늄 기어, AA5052 휴대폰 케이스, 마이크로 필라형 순수 알루미늄 히트싱크 제작.
6. 주요 연구 결과:
주요 연구 결과 및 제시된 데이터 분석:
- 효율적인 재료 사용: PIG 다이캐스팅 공정은 거의 100%의 재료 효율을 달성했습니다.
- 자유 사출: 자유 사출 실험에서 평균 사출 속도는 0.8 m/s로 나타났습니다(그림 10).
- 알루미늄 흐름: 쇼트 샷 실험은 플라스틱 금형 사출과 유사한 흐름 패턴을 보여주었습니다(그림 11).
- 결함 없는 제품: X선 단층 촬영을 통해 주조 부품에 공동, 기공 및 수축이 없음이 확인되었습니다(그림 12, 그림 13).
- 미세 텍스처링: 핫 스탬핑은 순수 알루미늄 히트싱크에 마이크로 필라를 성공적으로 생성했습니다(그림 14, 그림 15). 유지 온도는 마이크로 필라의 종횡비에 큰 영향을 미쳤습니다.
- 마찰 특성: 질소 과포화 공정은 PIG 노즐과 다이 표면을 알루미늄 용탕 부착으로부터 보호했습니다. 질화된 PIG 노즐에 TiAlN을 코팅하면, 연속적인 PIG 다이캐스팅 공정 후에도 알루미늄 용탕이 심하게 부착되지 않도록 했습니다.

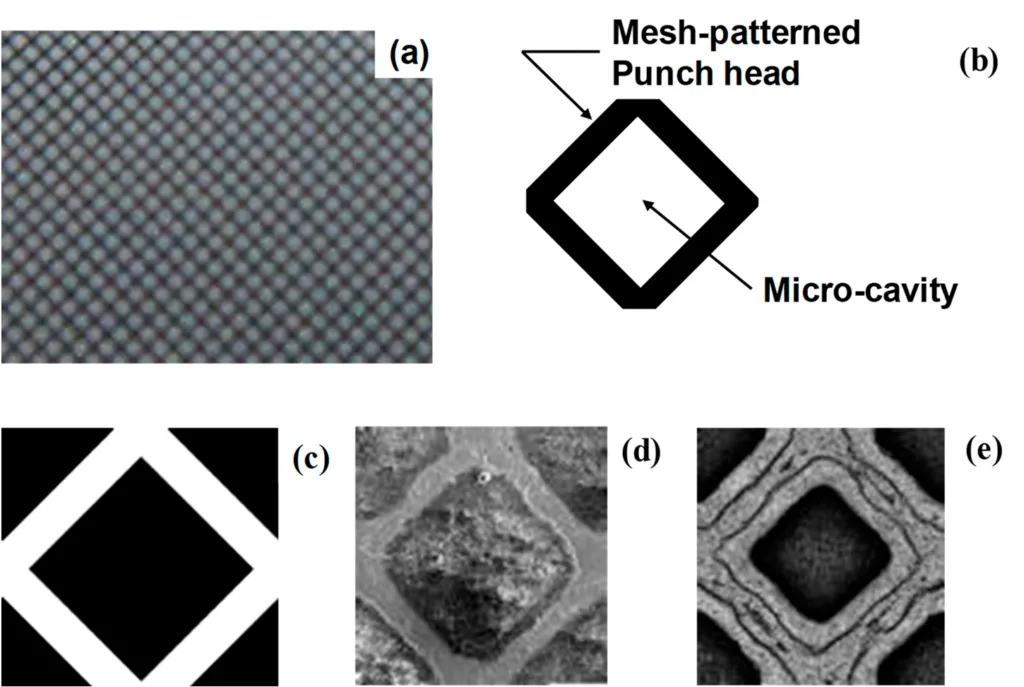
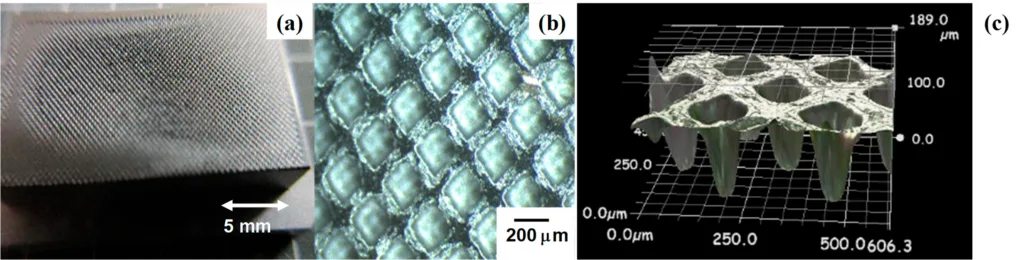

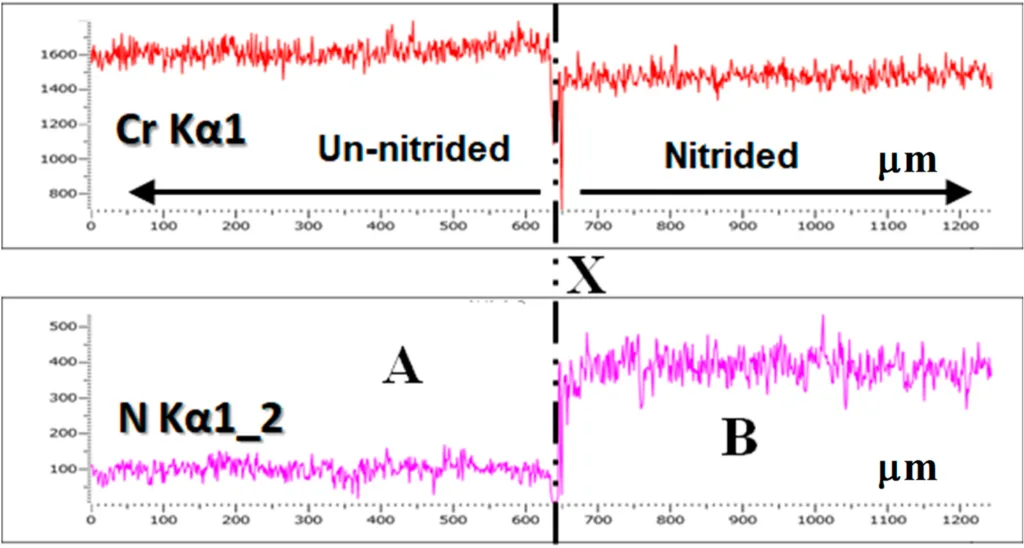
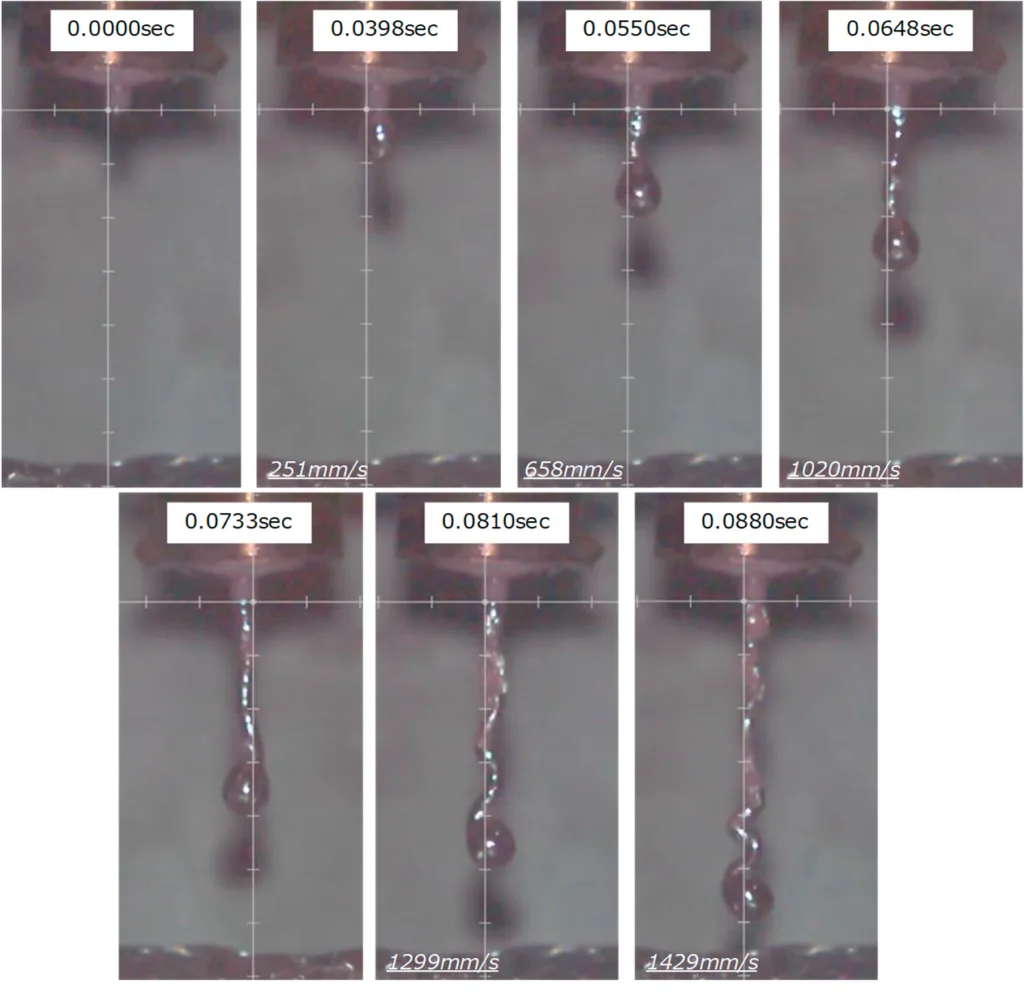

그림 이름 목록:
- 그림 1. 알루미늄 제품을 생산하는 두 가지 절차.
- 그림 2. PIG 다이캐스팅 및 핫 스탬핑 장치를 포함하는 제조 시스템.
- 그림 3. 중량 측정 섹션, 플런저, 가압 도구 및 가열 섹션을 포함하는 PIG 노즐 장치.
- 그림 4. 저온 플라즈마 질화 시스템.
- 그림 5. 저온 플라즈마 질화를 이용한 플라즈마 프린팅 절차.
- 그림 6. 플라즈마 프린팅으로 제작된 메쉬 텍스처 AISI316 펀치.
- 그림 7. PIG 노즐 및 다이용 질화 AISI20J2 재료의 질소 용질 함량 및 경도 깊이 프로파일.
- 그림 8. 비질화 및 질화 AISI420J2 표면 사이의 부식 및 침식 인성 비교.
- 그림 9. "A"에서 "B"까지 "X"를 가로지르는 침지된 AISI420J2 표면의 크롬 및 질소 함량 분포.
- 그림 10. PIG 노즐 출구 게이트에서 알루미늄 용융물의 자유 사출 시 동적 거동.
- 그림 11. PIG 다이캐스팅을 위해 이중 PIG 노즐 장치를 사용한 쇼트 쇼트 실험.
- 그림 12. 단일 PIG 노즐 장치를 사용하여 PIG 다이캐스팅된 소형 기어 블록.
- 그림 13. 이중 PIG 노즐 장치를 사용하여 PIG 다이캐스팅된 박벽 AA5052 휴대폰 케이스.
- 그림 14. 표면 미세 텍스처링을 위한 순수 알루미늄 응고 프리폼의 웜 스탬핑.
- 그림 15. 미세 텍스처 형성에 대한 핫 스탬핑 중 유지 온도의 영향.
7. 결론:
주요 결과 요약:
통합 PIG 다이캐스팅 및 핫 스탬핑 시스템은 재활용 원료로부터 소형, 박벽 및 미세 텍스처 알루미늄 부품을 높은 재료 효율과 최소한의 결함으로 성공적으로 제작했습니다. 질소 과포화 및 TiAlN 코팅은 공구를 부착 마모로부터 효과적으로 보호했습니다. 핫 스탬핑의 유지 온도는 미세 기둥 종횡비에 큰 영향을 미쳤습니다.
- 학술적 의의: 이 연구는 PIG 다이캐스팅과 핫 스탬핑을 결합한 알루미늄 재활용 및 제조에 대한 새로운 접근 방식을 보여줍니다. PIG 시스템에서 알루미늄 용융물의 흐름 거동과 표면 처리가 공구 수명에 미치는 영향에 대한 통찰력을 제공합니다.
- 실용적 의미: 개발된 시스템은 기존 다이캐스팅에 비해 보다 지속 가능하고 효율적인 대안을 제공하여 에너지 소비와 재료 낭비를 줄입니다. 고정밀 소형 복합 알루미늄 부품 생산에 적합합니다.
8. 참고 문헌:
- [1] Edwards, N. With green aluminum flowing, manufactures struggle to make product ESG top priority. Forbes 22 July 2020.
- [2] Aizawa, T.; Luangvaranunt, T.; Kondoh, K. Solid state recycling from green wastes to aluminum alloys with high material efficiency. J. JIM 2001, 65, 581–588.
- [3] Jeong, M.-S.; Lee, S.-Y.; Lee, I.-K.; Lee, S.-K.; Kim, D.; Cho, Y.-J.; Ko, D.-C. Green alternative aluminum extrusion process through process convergence. Int. J. Prec. Eng. Manuf. 2014, 15, 1173–1177.
- [4] Hartlieb, M.; Anderson, K. Die casting. 2A. In Aluminum Science and Technology; ASM International: Almere, The Netherlands, 2018.
- [5] Aizawa, T.; Yamaguchi, T.; Sakayori, H. JP-Patent 2019 with P19HS-001, 31 December 2019.
- [6] Aizawa, T.; Yamaguchi, T.; Sakayori, H. Die Casting System and Manufacturing Procedure of Die Cast Products. JP-Patent 2021 with P21SL-001, 31 December 2021.
- [7] Aizawa, T.; Yamaguchi, T.; Sakayori, H. Metal Forming System and Production Procedure. JP-Patent 2021 with P21SL-002, 31 December 2021.
- [8] Aizawa, T.; Kurihara, T.; Yamaguchi, T.; Sakayori, H. Near-net shaping of aluminum alloy parts by pin-injection-gate die-casting. In Proceedings of the 13th AWMFT, Shanghai, China, 6 December 2021; pp. 253–262.
- [9] Funazuka, T.; Dohda, K.; Takatsuji, N.; Hu, C.; Ngernbamrung, S. Effect of die coating on surface crack depth of hot extruded 7075 aluminum alloy. Friction 2022, 143, 21–32.
- [10] Aizawa, T. Low Temperature Plasma Nitriding of Austenitic Stainless Steels. Chapter 3 in Stainless Steels and Alloys; IntechOpen: London, UK, 2019; pp. 31–50.
- [11] Aizawa, T.; Dohda, K.; Shiratori, T. Nano-structured tribo-coating for cold and hot stamping. In Proceedings of the 52nd ICFG Plenay Meeting, San Sebastian, Spain, 16 September 2019; pp. 116–123.
- [12] Shiratori, T.; Aizawa, T.; Saito, Y.; Dohda, K. Fabrication of micro-punch array by plasma printing for micro-embossing into copper substrates. Materials 2019, 12, 2640.
- [13] Shiratori, T.; Aizawa, T.; Saito, Y.; Wasa, K. Plasma printing of an AISI316 micro-meshing punch array for micro-embossing onto copper plates. Metals 2019, 9, 396.
- [14] Borgioli, F.; Galvanetto, E.; Bacco, T. Low temperature nitriding of AISI300 and 200 series austenitic stainless steels. Vacu**um *2016*, *12*, 51–60.
- [15] Domain, C.; Becquart, C.S.; Foct, J. Ab initio study of foreign interstitial atom (C, N) interactions with intrinsic point defects in a-Fe. Phys. Rev. B 2004, 69, 144122.
- [16] ECO, Aluminum Die Casting. Available online: https://www.ecodiecasting.com/aluminum-die-casting/ (accessed on 3 June 2022).
- [17] Xie, Z.; Jiao, J.; Yang, K. Theoretical and experimental study on the fluid-structure—Acoustic coupling dynamics of a new water lubricated bearing. Tribol. Int. 2023, 177, 107982.
- [18] Cleary, P.W.; Ha, J.; Prkash, M.; Nguyen, T. Short shots and industrial case studies: Understanding fluid flow and solidification in high pressure die casting. Appl. Math. Model. 2010, 34, 2018–2033.
- [19] Seow, L.W.; Lm, Y.C. Optimizing flow in plastic injection molding. J. Mater. Process. Technol. 1997, 72, 333–341.
- [20] JST, Aluminum Alloy Gear. Available online: http://www.precise-gear.com/aluminum-alloy-gear.html (accessed on 3 June 2022).
- [21] Gangopadhyay, S.; Acharya, R.; Chattopadhyay, A.K.; Sargade, V.G. Effect of cutting speed and surface chemistry of cutting tools on the formation of bul or bue and surface quality of the generated surface in dry turning of AA6005 aluminum alloy. Mach. Sci. Technol. 2010, 14, 208–223.
- [22] Maeno, T.; Mori, K.-I.; Yachi, R. Hot stamping of high-strength aluminum alloy aircraft parts using quick heating. CIRP Ann. 2017, 66, 269–272.
- [23] Kumaraguruparan, G.; Sornakumar, T. Development of testing of aluminum micro channel heat sink. J. Therm. Sci. 2010, 19, 245–252.
- [24] Gong, M.F.; Li, Z.; Dong, J. Mechanics analysis of reinforcing rib structure in aluminum heating-plate automatic casting system. Adv. Mater. Res. 2012, 538-541, 1755–1761.
- [25] Ohashi, T.; Tabetabei, H.M.; Nishimura, T. Rib-structure on A5083 aluminum alloy sheet generated friction stir forming. Preced. Eng. 2017, 207, 1153–1158.
- [26] Ma, Z.; Ji, H.; Huang, X.; Xiao, W.; Tang, X. Research on high temperature stamping forming performance and process parameters optimization of 7075 aluminum alloy. Materials 2021, 14, 5435.
- [27] Chemical Resistance Reference Chart. Available online: https://www.calpaclab.com/content/chemical-charts/Aluminum.pdf (accessed on 6 November 2022).
- [28] Kumar, S.; Maity, S.R.; Patnaik, L. Friction and tribological behavior of bare nitrided, TiAlN and AlCrN coated MDC-K hot work tool steel. Ceram. Int. 2020, 46, 17280–17294.
- [29] Tollmann, W.; Grisales, D.; Stangier, D.; Butzke, T. Tribomechanical behavior of TiAlN and CrAlN coatings deposited onto AISI H11 with different pre-treatments. Coatings 2019, 9, 519.
- [30] Dohda, K.; Aizawa, T.; Funazuka, T. Process tribology of PVD nitride coated dies in hot metal forming. Friction 2022; in press.
9. 저작권:
- 본 자료는 "Tatsuhiko Aizawa, Takeshi Kurihara and Hiroki Sakayori"의 "Manufacturing of Aluminum Alloy Parts from Recycled Feedstock by PIG Die-Casting and Hot Stamping" 논문을 바탕으로 작성되었습니다.
- 논문 출처: https://doi.org/10.3390/lubricants11010013
본 자료는 위 논문을 소개하기 위해 제작되었으며, 상업적 목적으로 무단 사용하는 것을 금합니다. Copyright © 2025 CASTMAN. All rights reserved.