This introductory paper is the research content of the paper ["Experimental-Numerical Model of the Initiation and Propagation of Cracks in Die Inserts"] published by ['ARCHIVES of FOUNDRY ENGINEERING'].
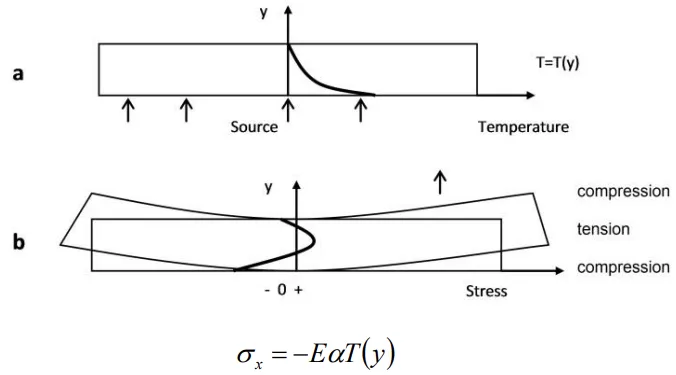
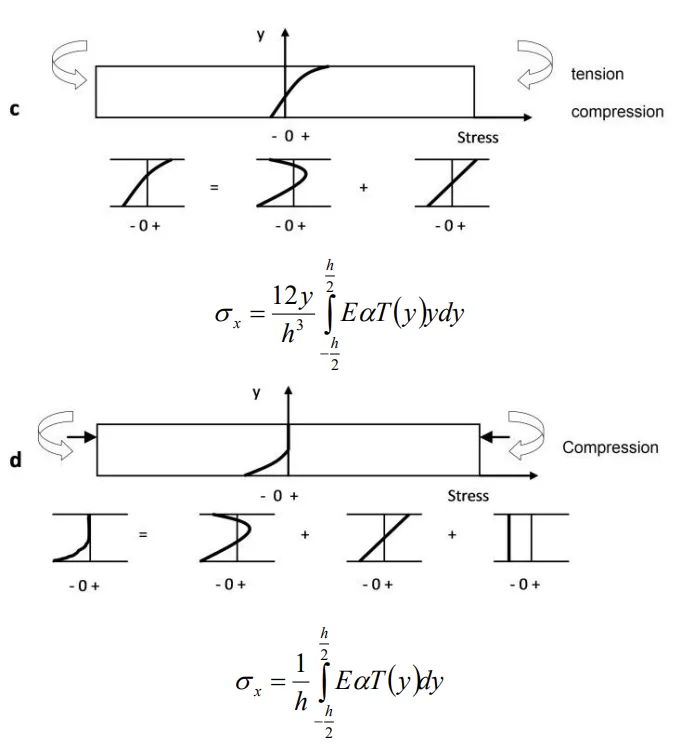
1. Overview:
- Title: Experimental-Numerical Model of the Initiation and Propagation of Cracks in Die Inserts
- Author: J. Piekło, M. Maj, St. Pysz
- Publication Year: 2013
- Publishing Journal/Academic Society: ARCHIVES of FOUNDRY ENGINEERING, Volume 13, Special Issue 1/2013
- Keywords: (The paper does not explicitly list keywords, so this section must be omitted based on the provided instructions.)
2. Abstracts / Introduction
The aim of the research presented in this paper was to develop an experimental - numerical model for predicting the life of die inserts. For this purpose, using FEM, the temperature and stress fields in the insert during stable operating cycle of a die casting machine were determined. The study of WCL steel, of which inserts are made, included fatigue tests and tests from the range of fracture mechanics. From the results obtained, a relationship was derived between the number of the die casting machine operating cycles and the propagation speed of cracks formed on the insert working surface.
3. Research Background:
Background of the Research Topic:
Inserts installed in dies for the pressure die casting process are operating under the conditions of thermal and mechanical loads changing in cycles and caused by the successively performed operations of metal injection, die opening and spraying of protective coating.
Status of Existing Research:
Thermal cracks, stress-induced cracks and spallings can be classified.
Thermal cracks are formed on flat surfaces. Stress-induced cracks appear in the areas of stress concentration. Spallings are formed as a result of the brittle precipitates getting detached from the die surface.
Necessity of the Research:
(This is implicitly stated within the context of predicting die insert life, but no single sentence directly addresses this. Based on the rules, we cannot synthesize this point.)
4. Research Purpose and Research Questions:
Research Purpose:
To develop an experimental-numerical model for predicting the life of die inserts.
Key Research:
- temperature and stress fields in the insert during stable operating cycle of a die casting machine were determined.
- fatigue tests and tests from the range of fracture mechanics.
- a relationship was derived between the number of the die casting machine operating cycles and the propagation speed of cracks.
5. Research Methodology
Research Design:
Experimental-numerical modeling.
Data Collection Method:
- Thermocouples placed in drilled holes within ejectors, and between the insert and die cavity.
- Tests were carried out on an AK 11 alloy.
- Parameters included injection temperature (680°C), cycle times, locking force (150 T), and metal pressure (70 MPa).
Analysis Method:
- Finite Element Method (FEM) was used to determine temperature and stress fields.
- Two numerical models were used: a temperature model and a stress model.
- Non-linear elements with reduced integration were used.
- Morrow fatigue life equation and Paris equation were employed.
Research Subjects and Scope:
- WCL steel die inserts.
- Stable operating cycle of a die casting machine.
6. Main Research Results:
Key Research Results:
- A conventional division of the insert into three zones (A, B, C) was made based on stress and temperature analysis.
- Zone A (surface to 5mm depth) experiences the greatest temperature changes (260°C - 670°C) and sign changes in thermal stress. Thermal fatigue is the main cause of destruction in this zone.
- Zone B (5mm to 25mm depth) has compressive stresses with high and changing values. Cyclic creep is assumed to influence metal strength.
- Zone C (beyond 25mm depth) has compressive stresses not exceeding 200 MPa. Monotonic creep is assumed to control high-temperature strength.
- Morrow equation (with experimentally determined constants) was used to predict the number of cycles to crack initiation (approximately 60,000 cycles).
- The crack propagation velocity was predicted from Paris equation, for which the constants m = 2.88 and C = 7.9 * 10-12 were experimentally determined.
- Paris equation, where ΔK is expressed as a function of the instantaneous crack length, assumes the form: da/dN = 1.25 * 10^(-4) * a.
Analysis of presented data:
- Table 1: Shows a comparison between numerically calculated and experimentally measured cycles for various crack lengths. The difference between calculated and measured values is noted as "not really very great."
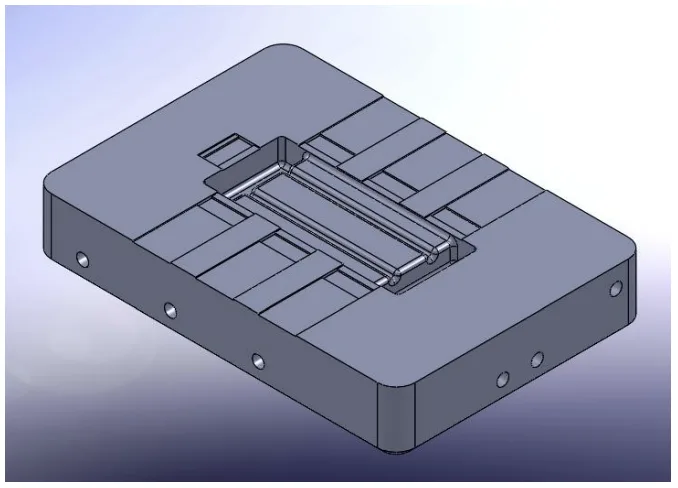
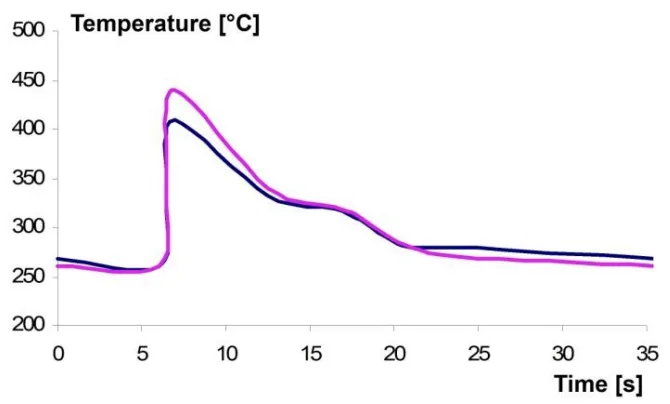
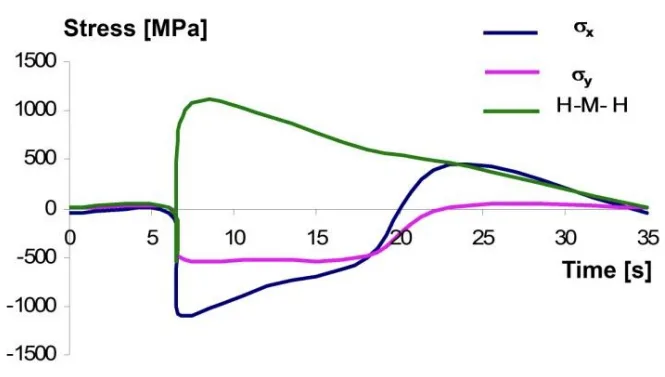
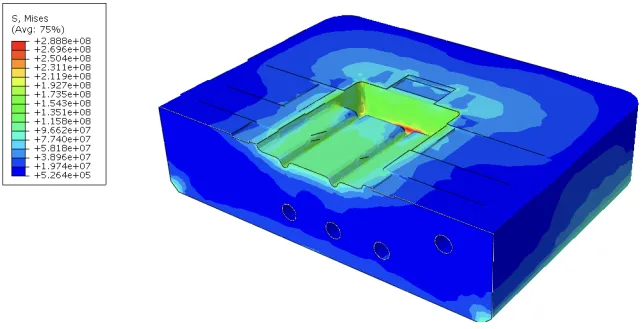
Figure Name List:
- Fig.1 a-d. Different stress states in a beam heated unilaterally
- Fig. 2 CAD model of the die insert
- Fig. 3 Recorded experimentally (curve 1) and calculated numerically (curve 2) temperature changes in the die insert during one operating cycle of the die casting machine
- Fig. 4. Calculated by FEM changes in stress components and in reduced stress in the die insert during one operating cycle of the die casting machine
- Fig. 5. Field of reduced instantaneous thermal stresses induced by temperature field
7. Conclusion:
Summary of Key Findings:
- Cyclic stress changes mainly occur on the surface and penetrate to a depth of 5 mm.
- Compressive stress is predominant, but tensile stress during cooling controls crack propagation.
- The computational model can determine likely crack locations and growth rates.
Academic Significance of the Study:
Provides a coupled experimental-numerical model for analyzing crack initiation and propagation in die casting inserts.
Practical Implications:
- Enables prediction of die insert life.
- The adopted computational model enabled determining places where there is the greatest likelihood of the occurrence of cracks, enabling also their growth rate to be calculated with reasonable accuracy,
Limitations of the Study and Areas for Future Research:
- Experimental results are from measurements made on one specimen only.
8. References:
- [1] Suzuki, M., Ishihara, M. & Miyachi, H. (1974). Innere Spannung und Bradrissbildung In Druckgiessformen. Giesserei - Praxis. 4, 63-70.
- [2] Danzer, R., Strum, F., Schindler, A. & Zlepping, W. (1983). Temperaturwechselrisse in Druckgiessformen. Giesserei Praxis. 19, 287-297.
- [3] Rosbrook, C., Shivpuri, R. (1993). A Computer Aided Investigation of Heat Checking and Die Life Predictions in Die Casting Dies, Materiały z konferencji w Cleveland.
- [4] Kocańda, S., Szala, J. (1985). Podstawy obliczeń zmęczeniowych. Warszawa: PWN.
- [5] German, J., Biel-Gołaska, M. (2004). Podstawy i zastosowanie mechaniki pękania W zagadnieniach inżynierskich. Kraków: Instytut Odlewnictwa.
- [6] Neimitz, A. (1998). Mechanika pękania. PWN.
- [7] Statute study 11.11.170.318 Task 10/11
9. Copyright:
- This material is "J. Piekło, M. Maj, St. Pysz"'s paper: Based on "Experimental-Numerical Model of the Initiation and Propagation of Cracks in Die Inserts".
- Paper Source: (The provided OCR does not contain a DOI URL, so this must be omitted.)
This material was created to introduce the above paper, and unauthorized use for commercial purposes is prohibited.
Copyright © 2025 CASTMAN. All rights reserved.