This article introduces the paper ['A Design and Analysis Method for Automotive and Aerospace Composite Structures including Manufacturing Variations'] published by ['ResearchGate'].
1. Overview:
- Title: A Design and Analysis Method for Automotive and Aerospace Composite Structures including Manufacturing Variations
- Author: Dirk Lukaszewicz, Simon Hesse, Lavinia Graff, Stefan Kerscher, Lyle Deobald, Chul Y Park, Nihar Desai
- Publication Year: September 2014
- Publishing Journal/Academic Society: Conference Paper, ResearchGate
- Keywords: Manufacturing variations, composite structures, automotive, aerospace, design method, analysis method
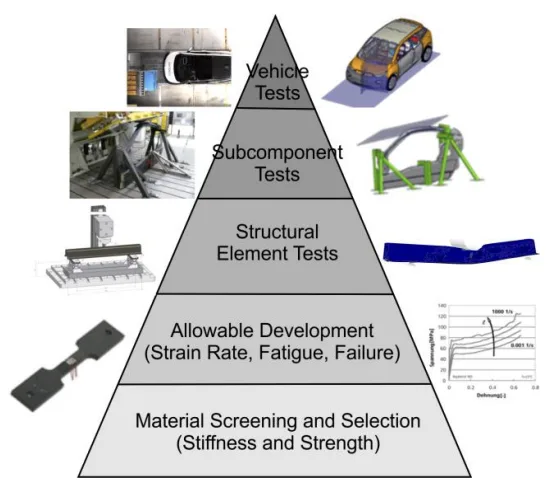
2. Abstracts
An approach for modeling the potential interaction of manufacturing and
geometry-induced variations (MV) during the design phase of composite automotive
structures and subsystems is presented. Initially, common design processes are
discussed with a focus on dealing with manufacturing variations. The effect of such
variations is then demonstrated using an advanced composite automotive side frame.
General methods applied in the crashworthiness demonstration of the automotive side
frame may be extended to strength predictions of typical aerospace structure. Actual
manufacturing variations, such as out-of-plane waviness, along with their position in
the component were recorded through destructive testing and then introduced into an
FE-model set up in Abaqus Explicit [1]. The variable areas were associated with
knockdown factors, some of which are derived in a complementary paper [2]. Two
FE-models with different MV maps were then validated against experimental results.
The level of multiple MV characteristics was stochastically varied
simultaneously and the impact on the intrusion of an impactor was recorded. From this
a response surface model (RSM) was generated. A novel optimization was also used
that decouples all knockdown factors and allows to separately access the impact of the
MVs. The result is a maximum allowable characteristic for each MV. The
methodology has significant benefits for high-volume composite manufacture and
design since it may reduce scrap rates, reduced expensive qualification test programs
and reduce component weight by eliminating the use of excessive safety factors to
account for unknown manufacturing variations.
3. Research Background:
Background of the Research Topic:
Composite design and manufacturing inherently introduces manufacturing variations (MVs) during component production. These MVs, influenced by part geometry, layup sequence, and processing conditions, can significantly affect the mechanical properties of composite structures, such as stiffness and strength. Unlike mechanical specimens prepared from flat plates, actual components often exhibit MVs that can lead to non-conservative design allowables.
Status of Existing Research:
Current aerospace industry practices address MVs by integrating several elements into the design process to ensure robustness. A key element is the use of allowables, derived by applying knockdown factors to nominal material properties. This approach, based on the "Building Block Approach", relies on extensive testing and non-destructive inspection (NDI). However, in high-volume automotive manufacturing, NDI is often impractical due to time and cost constraints. Existing methods often use a lumped global reduction of structural strength to account for MVs, which can be overly conservative.
Necessity of the Research:
The aerospace approach, while effective, is not directly transferable to high-volume automotive composite manufacturing due to production volume and cost considerations. There is a need for a methodology that accounts for MVs during product development in a way that informs both design and manufacturing processes. This includes identifying critical MVs and optimizing manufacturing processes to mitigate their impact, similar to approaches used in die-cast aluminum component design where porosity is explicitly considered.
4. Research Purpose and Research Questions:
Research Purpose:
The primary research purpose is to develop and demonstrate a design and analysis methodology that explicitly incorporates manufacturing variations (MVs) in the design phase of composite automotive and aerospace structures. This methodology aims to define allowable limits for MVs to ensure structural performance while optimizing manufacturing processes and reducing reliance on overly conservative safety factors.
Key Research:
- To model the interaction of manufacturing and geometry-induced variations during the design phase.
- To demonstrate the effect of MVs using an advanced composite automotive side frame and extend the methodology to aerospace structures.
- To develop a method for recording and incorporating actual MVs, such as out-of-plane waviness, into FE-models.
- To utilize a response surface model (RSM) and novel optimization techniques to decouple knockdown factors and assess the impact of individual MVs.
- To define maximum allowable characteristics for each MV to guide design and manufacturing process optimization.
Research Hypotheses:
The research implicitly hypothesizes that:
- Explicitly modeling MVs in FE-simulations will provide a more accurate prediction of composite structural performance compared to using global knockdown factors.
- Optimizing manufacturing processes based on the impact of specific MVs on structural performance can lead to reduced scrap rates, lower qualification costs, and lighter component weights.
- A methodology based on RSM and decoupled knockdown factors can effectively define allowable limits for MVs in composite structures.
5. Research Methodology
Research Design:
The research employs a combined approach of experimental testing and numerical simulation. It uses a case study of a composite automotive side frame to demonstrate the methodology. The design is iterated using a "Building Block Approach" adapted for composite vehicles.
Data Collection Method:
- Destructive Testing: Actual manufacturing variations (MVs) such as out-of-plane waviness were recorded through destructive testing of manufactured composite side frames.
- Visual Inspection: MV characteristics were visually inspected and recorded for each ply in manufactured parts using a grid projection method. Quality inspection staff categorized and characterized defects.
- Experimental Validation: Two FE-models with different MV maps were validated against experimental results from physical crash tests.
Analysis Method:
- Finite Element (FE) Modeling: FE-models were developed in Abaqus Explicit to simulate the structural behavior of the composite side frame under dynamic impact, incorporating recorded MV maps.
- Response Surface Model (RSM): A RSM was generated based on Monte Carlo simulations to analyze the impact of stochastically varied MV characteristics on structural performance (impactor intrusion).
- Monte Carlo Simulation: Monte Carlo sampling was used to vary MV characteristics in the FE-model to assess their impact on structural performance.
- Optimization Algorithm: A novel optimization algorithm was used to decouple knockdown factors and determine maximum allowable characteristics for each MV.
Research Subjects and Scope:
The research focuses on composite structures for automotive and aerospace applications, specifically using an automotive side frame as a case study. The scope includes manufacturing variations such as in-plane and out-of-plane waviness, longitudinal and transverse folding. The study is limited to the considered MV types and the specific geometry of the automotive side frame.
6. Main Research Results:
Key Research Results:
- A methodology for incorporating measured manufacturing variations (MVs) into FE-models of composite structures was developed and validated.
- The FE-model, incorporating MV maps, showed good correlation with experimental results for dynamic impact tests.
- A Response Surface Model (RSM) was generated to quantify the impact of different MV characteristics on structural performance.
- Maximum allowable characteristics for each MV type were determined using a novel optimization approach, decoupling knockdown factors.
- The study demonstrated that certain combinations of MVs can lead to a reduction in maximum intrusion during impact, potentially due to increased stiffness or altered failure modes.
Analysis of presented data:
- Table 1: Varied MVs and characteristic range: This table lists the types of manufacturing variations considered (Out-of-plane waviness, In-plane waviness, Longitudinal Folding, Transverse Folding) and their characteristic size range (1-6).
- Figure 3: Image of the FE-model with Impactor and supports, mapped MVs are also shown: This figure visually represents the FE-model setup, including the impactor, supports, and the mapped manufacturing variations on the composite side frame.
- Figure 4: Comparison of load-displacement curves for the baseline FE Simulation and MV map A and B: This figure compares the load-displacement curves from FE simulations: a baseline simulation without MVs, and simulations incorporating two different MV maps (A and B). It shows the impact of MVs on the structural response.
- Table 2: Variability of 3-point-bending dynamic impact tests: This table presents the results of variability tests on nominally identical specimens, showing the maximum intrusion and mean intrusion with standard deviation. This data is used to define the allowable change due to MVs.
- Table 3: Monte Carlo Simulation Results and No of designs above the critical limit: This table summarizes the results of the Monte Carlo simulations across iterations, showing the R² value of the RSM, the number of outlier designs, and the percentage of outliers. It indicates the convergence and quality of the RSM.
- Table 4: Corridor Limits on MV Characteristics: This table shows the corridor limits (maximum allowable MV characteristic) for each MV type (Out-of-plane waviness, In-plane waviness, Longitudinal Folding, Transverse Folding) across different iterations of the optimization process. It demonstrates how the allowable limits are refined.
Figure Name List:
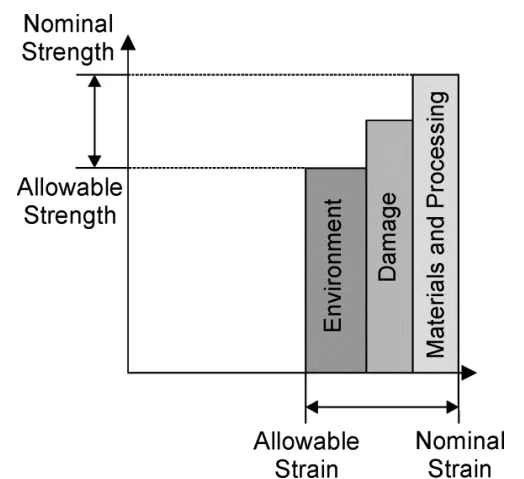
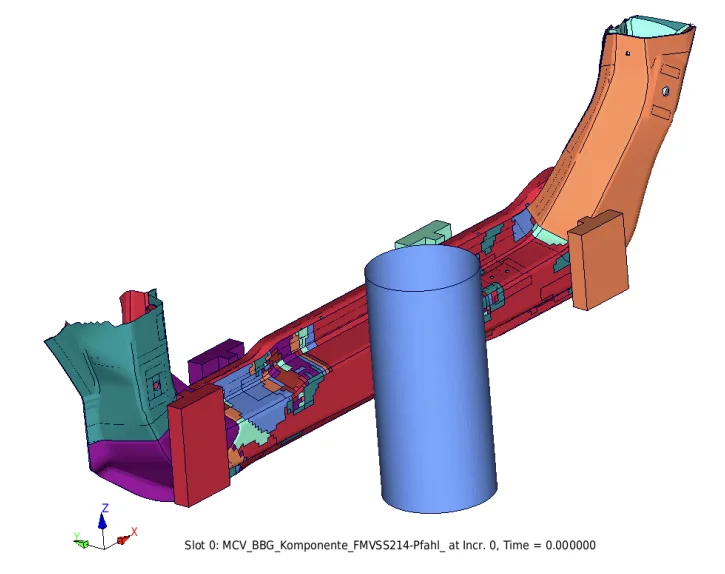
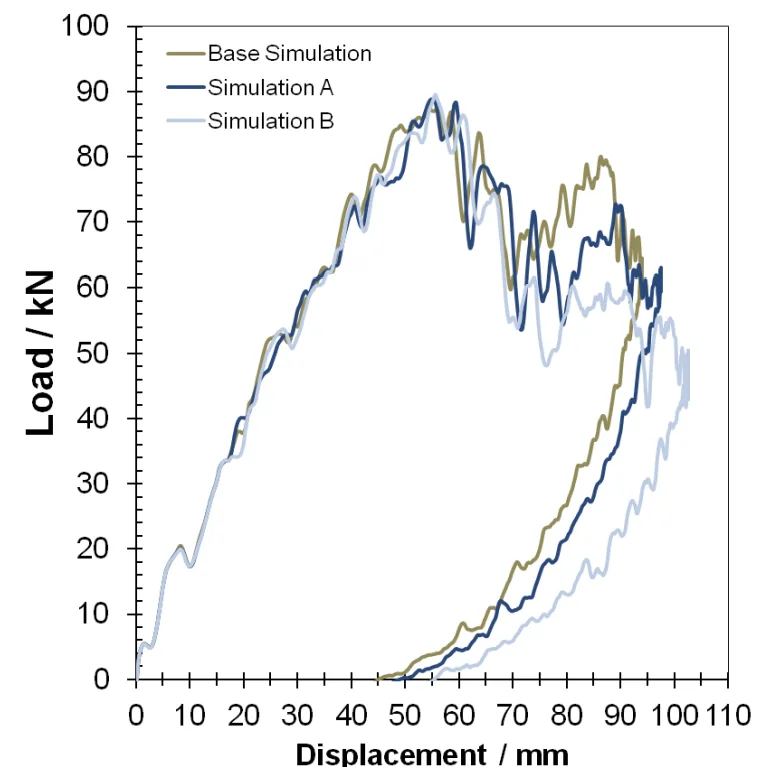
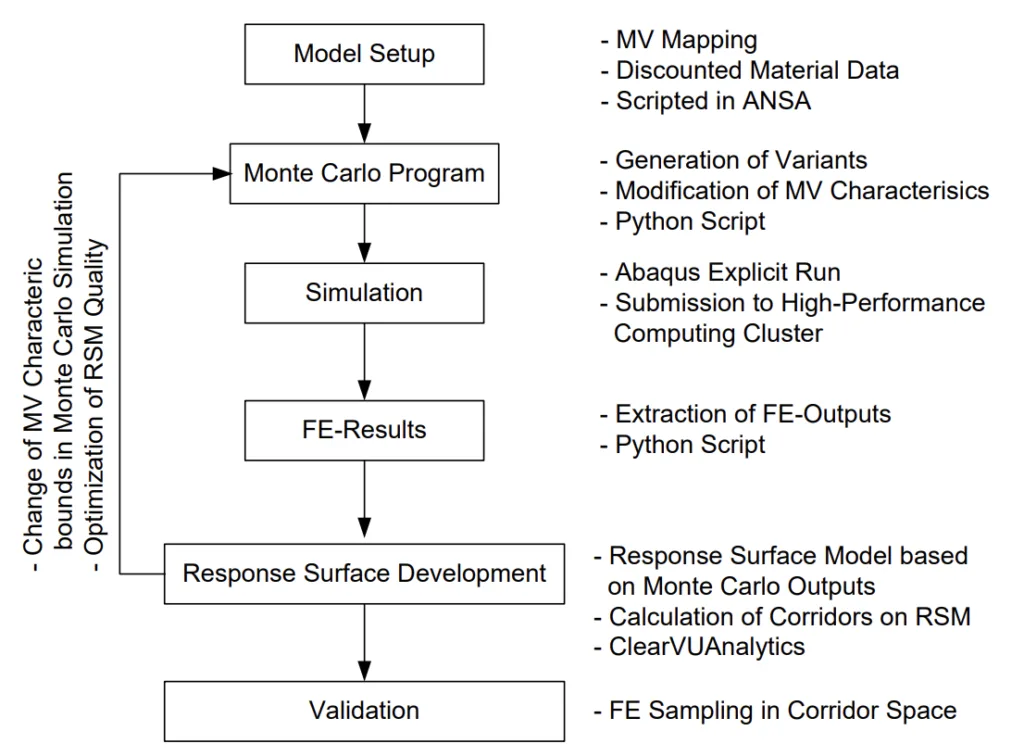
- Figure 1: Definition of nominal values for a composite material and derived design allowables.
- Figure 2: Building Block approach for a composite vehicle.
- Figure 3: Image of the FE-model with Impactor and supports, mapped MVs are also shown.
- Figure 4: Comparison of load-displacement curves for the baseline FE Simulation and MV map A and B
- Figure 5: Simulation Workflow for the MV corridors and the maximum allowable characteristic.
7. Conclusion:
Summary of Key Findings:
The study successfully developed and validated a methodology for designing composite structures that explicitly accounts for manufacturing variations (MVs). By integrating measured MVs into FE-models and employing RSM and novel optimization techniques, the research defined allowable limits for MVs while maintaining structural integrity. The methodology was demonstrated on an automotive composite side frame, showing good correlation between simulations and experimental results.
Academic Significance of the Study:
This research contributes to the field of composite structural design by providing a robust methodology for incorporating manufacturing variability directly into the design process. It moves beyond traditional approaches that rely on global knockdown factors and offers a more refined and accurate way to predict structural performance in the presence of MVs. The use of RSM and decoupled knockdown factors represents an advancement in the analysis and optimization of composite structures with manufacturing uncertainties.
Practical Implications:
The developed methodology has significant practical implications for high-volume composite manufacturing, particularly in the automotive and aerospace industries. By enabling the design of composite components with explicit consideration of MVs, it can lead to:
- Reduced scrap rates through optimized manufacturing processes.
- Lower qualification costs by reducing the need for extensive physical testing.
- Lighter component weights by minimizing the use of excessive safety factors.
- Improved link between manufacturing and design, facilitating simultaneous optimization.
Limitations of the Study and Areas for Future Research:
The study is limited to specific types of manufacturing variations and a particular automotive component. Future research should:
- Expand the methodology to include a broader range of MV types and composite materials.
- Apply the methodology to different structural geometries and loading conditions, including aerospace structures.
- Further investigate the interaction and combined effects of different MV types on structural performance.
- Explore the optimization of manufacturing processes based on the identified critical MVs and their allowable limits.
- Investigate the numerical noise and domain decomposition effects observed in the results to further refine the methodology.
8. References:
- [1] Dassault Simulia. Abaqus 6.11-2A; 2013.
- [2] Deobald L, Park C, Desai N, et al. Simulation of Composite Manufacturing Variations to Determine Stiffness and Strength Reductions in Automotive and Aerospace Structure. ACS 29th Technical Conferences. San Diego 2014.
- [3] Potter K. In: (unpublished), 2013.
- [4] Huang H, Talreja R. Effects of void geometry on elastic properties of unidirectional fiber reinforced composites. Comp Sci Tech. 2005;65(13):1964-81.
- [5] Feraboli P. Composite Materials Strength Determination Within the Current Certification Methodology for Aircraft Structures. 2009;46(4):1365-74.
- [6] Graff L. Stochastic Algorithm for the identification of solution spaces in high-dimensional design spaces [PhD Thesis]: University of Basel, 2013.
- [7] Baxter B. The interpolation theory of radial basis functions [PhD Thesis]: Cambridge University, 1992.
- [8] Piret C. Analytical and numerical advances in radial basis functions [PhD Thesis]: University of Colorado, 2007.
- [9] Zimmermann M, von Hoessle J. Computing solution spaces for robust design. Int J Num Methods Eng. 2013;94(3):290-307.
- [10] Lukaszewicz D. Automotive Composite Design Process. FISITA World Automotive Congress. Maastricht, The Netherlands, 2014.
- [11] Beta CAE. ANSA; 2014.
- [12] Divis. ClearVU Analytics; 2014.
9. Copyright:
- This material is "[Dirk Lukaszewicz et al.]"'s paper: Based on "[A Design and Analysis Method for Automotive and Aerospace Composite Structures including Manufacturing Variations]".
- Paper Source: https://www.researchgate.net/publication/268925382
This material was summarized based on the above paper, and unauthorized use for commercial purposes is prohibited.
Copyright © 2025 CASTMAN. All rights reserved.