본 게시물은 "AM60 합금을 사용한 고진공 고압 다이캐스팅 공정을 이용한 버스 팔걸이 제작 공정 개발" 연구 논문을 요약한 것입니다. 이 논문은 마그네슘 합금과 특수 다이캐스팅 공정을 사용하여 더 가볍고 효율적인 버스 팔걸이를 만드는 방법을 탐구합니다.
1. 개요:
- 제목: AM60 합금을 사용한 고진공 고압 다이캐스팅 공정을 이용한 버스 팔걸이 제작 공정 개발 (Development of a bus armrest fabrication process with a high-vacuum, high-pressure die-casting process using the AM60 alloy)
- 저자: 유명한, 송준혁, 오제하, 강신재, 김광석, 양승모, 문민석 (MyeongHan Yoo, JoonHyuk Song, JeHa Oh, ShinJae Kang, KwangSeok Kim, SungMo Yang, MinSeok Moon)
- 발행 연도: 2018년
- 발행 학술지: 로보틱스 및 컴퓨터 통합 제조 (Robotics and Computer–Integrated Manufacturing)
- 키워드: 경량 차량, 마그네슘 합금, 진공 다이캐스팅, AM60 합금, 버스 팔걸이 (light-weight vehicle, magnesium alloy, vacuum die-casting, AM60 alloy, bus armrest)
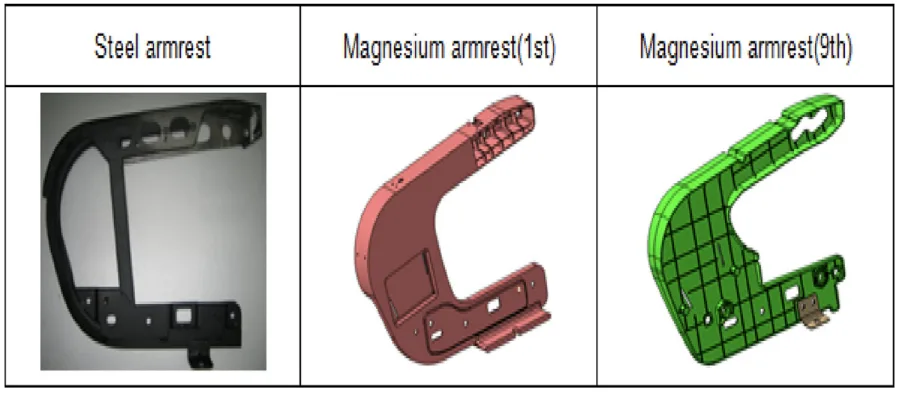
2. 연구 배경:
- 연구 주제의 사회적/학문적 맥락: 전 세계적으로 환경 문제, 특히 오염과 지구 온난화에 대한 관심이 증가하면서 선진국에서는 더욱 엄격한 환경 규제가 시행되고 있습니다. 자동차 제조업체들은 이러한 강화된 기준을 충족하기 위해 적극적으로 노력하고 있습니다. 경량 차량 설계는 연비 향상과 자동차의 CO2 배출량 감소를 위한 핵심 분야입니다.
- 기존 연구의 한계: 경량 소재가 다양한 차량 유형에 적용되고 있지만, 버스는 승용차보다 크기와 승객 수용량이 더 큼에도 불구하고 여전히 특정 부품에 알루미늄 합금을 주로 사용하고 있습니다. 다른 상용 금속 재료보다 뛰어난 경량성과 성능으로 알려진 마그네슘 합금은 아직 버스 제조에 일반적으로 사용되지 않고 있습니다.
- 연구의 필요성: 본 연구는 마그네슘 다이캐스팅을 사용하여 경량 차량 부품, 특히 버스용 부품을 개발해야 할 필요성을 다룹니다. 버스 부품, 예를 들어 팔걸이와 같은 부품에서 더 무거운 재료를 마그네슘 합금으로 대체하는 것은 중량 감소에 상당한 기회를 제공하여 연비 향상과 환경 영향 감소에 기여합니다.
3. 연구 목적 및 연구 질문:
- 연구 목적: 본 연구의 주요 목적은 경량 마그네슘 합금 AM60으로 만든 버스 팔걸이를 개발하고 평가하는 것입니다. 이는 설계, 시뮬레이션, 금형 제작 및 공정 개발을 포함하는 고진공 고압 다이캐스팅 공정을 통해 달성됩니다.
- 주요 연구 질문:
- AM60 마그네슘 합금과 고진공 고압 다이캐스팅 공정을 사용하여 버스 팔걸이를 효과적으로 제작할 수 있는가?
- 마그네슘 합금 팔걸이는 버스 적용에 필요한 기계적 물성 요구 사항 및 내구성 기준을 충족할 것인가?
- 연구 가설: 본 연구는 고진공 고압 다이캐스팅으로 제조된 마그네슘 합금 버스 팔걸이가 기존의 강철 팔걸이보다 훨씬 가벼우면서도 필요한 구조적 및 기능적 성능 기준을 충족할 것이라는 가설을 세웠습니다.
4. 연구 방법론:
- 연구 설계: 본 연구는 개발 및 실험적 접근 방식을 채택합니다. 부품 설계 및 시뮬레이션부터 시작하여 금형 제작 및 다이캐스팅 공정 개발을 거쳐 기계적 물성 및 내구성 테스트로 마무리되는 일련의 단계를 포함합니다.
- 자료 수집 방법: 자료는 다음을 통해 수집되었습니다.
- 시뮬레이션 결과: 구조 시뮬레이션은 Nastran FX (ver. 2.0) 프로그램을 사용하여 수행되었으며, 유동 및 응고 시뮬레이션은 Anycasting (ver. 7.0) 프로그램을 사용하여 수행되었습니다.
- 기계적 물성 시험 데이터: 마그네슘 합금 팔걸이의 기계적 물성을 평가하기 위해 ASTM-E8M 표준에 따라 인장 시험을 수행했습니다.
- 수직 파괴 하중 시험 데이터: ES88001-50 사양에 따라 팔걸이의 하중 하에서의 구조적 무결성을 평가하기 위해 수직 파괴 하중 시험을 수행했습니다.
- 피로 시험 데이터: ES88001-50 사양에 따라 반복 하중 하에서 팔걸이의 내구성을 평가하기 위해 피로 시험을 수행했습니다.
- 분석 방법: 수집된 데이터는 다음을 통해 분석되었습니다.
- 구조 및 응고 시뮬레이션 분석: 시뮬레이션 결과를 사용하여 팔걸이 설계 및 다이캐스팅 공정 매개변수를 최적화했습니다.
- 기계적 물성 분석: 인장 시험 데이터를 분석하여 항복 강도 및 극한 인장 강도와 같은 주요 기계적 물성을 결정했습니다.
- 수직 파괴 하중 및 피로 시험 분석: 시험 결과를 ES88001-50 사양 요구 사항과 비교하여 마그네슘 팔걸이의 구조적 성능 및 내구성을 평가했습니다. 마그네슘 팔걸이와 강철 팔걸이의 성능을 시뮬레이션 및 실험 결과를 기반으로 비교했습니다.
- 연구 대상 및 범위: 본 연구는 AM60 마그네슘 합금으로 만든 버스 팔걸이 부품 개발에 중점을 둡니다. 범위는 초기 설계부터 최종 성능 테스트까지 고진공 고압 다이캐스팅을 사용하는 전체 제작 공정을 포함합니다. 마그네슘 팔걸이의 성능은 기존 강철 팔걸이와 비교하여 평가됩니다.
5. 주요 연구 결과:
- 주요 연구 결과: 본 연구는 고진공 고압 다이캐스팅 공정을 사용하여 마그네슘 합금 버스 팔걸이를 성공적으로 개발했습니다. 결과적으로 팔걸이는 강철에 비해 상당한 중량 감소를 달성하면서도 필요한 기계적 물성 및 내구성 기준을 충족했습니다. 또한 버스 좌우측 모두에 사용할 수 있는 단일 부품을 만들어 제조 효율성을 최적화했습니다.
- 통계적/정성적 분석 결과:
- 중량 감소: 최종 마그네슘 팔걸이 설계는 기존 강철 팔걸이에 비해 35%의 중량 감소를 달성했습니다. 해당 부품의 무게는 36% 감소했습니다.
- 수직 파괴 하중 시험: 150 kgf (약 1471 N)의 수직 하중에서 마그네슘 팔걸이의 변위는 6.99 mm로 측정되었습니다. 이는 ES88001-50 사양 제한인 20 mm 이내입니다.
- 피로 시험: 마그네슘 팔걸이는 ES88001-50 요구 사항에 따라 목표인 65,000 사이클을 초과하여 피로 시험을 성공적으로 통과했습니다.
- 항복 강도: AM60 마그네슘 합금 팔걸이의 항복 강도는 130 MPa 이상으로 확인되었습니다.
- 변형 시뮬레이션: 수직 하중 시뮬레이션 결과 강철 팔걸이는 5.80 mm의 변형을 보였습니다. 초기 마그네슘 팔걸이 설계는 더 높은 13.4 mm의 변형을 보였습니다. 그러나 설계 최적화 후 최종 마그네슘 팔걸이 설계는 2.34 mm의 현저히 감소된 변형을 나타냈습니다.
- 데이터 해석: 결과는 고진공 고압 다이캐스팅 공정으로 가공된 AM60 마그네슘 합금이 버스 팔걸이 제조에 실행 가능한 재료임을 입증합니다. 마그네슘 팔걸이는 상당한 중량 감소를 달성했을 뿐만 아니라 필요한 구조적 성능 및 내구성 기준을 충족하고 초과합니다. 초기 마그네슘 설계 및 강철 설계와 비교하여 최종 설계에서 향상된 변형 성능은 설계 최적화 프로세스의 효과를 강조합니다.
- 그림 목록:
- Fig. 1. 강철 팔걸이 및 마그네슘 팔걸이 설계 비교 (Design comparison with steel armrest and magnesium armrest design).
- Fig. 2. 각 재료에 대한 수직 파괴 하중 시뮬레이션 결과 (Result of vertical fracture load simulation with each material).
- Fig. 3. 마그네슘 팔걸이 응고 시뮬레이션 조건 (Simulation condition of the magnesium armrest solidification).
- Fig. 4. 금형 충전 중 산화물 트래핑 (Oxide trapping on the mold during filling).
- Fig. 5. 금형 베이스 및 최종 금형 (Mold base and final mold).
- Fig. 6. 기계적 물성 시험편 및 결과 요약 (Mechanical property specimen and results summary).
- Fig. 7. 팔걸이 수직 파괴 하중 평가 (Armrest vertical fracture load evaluation).
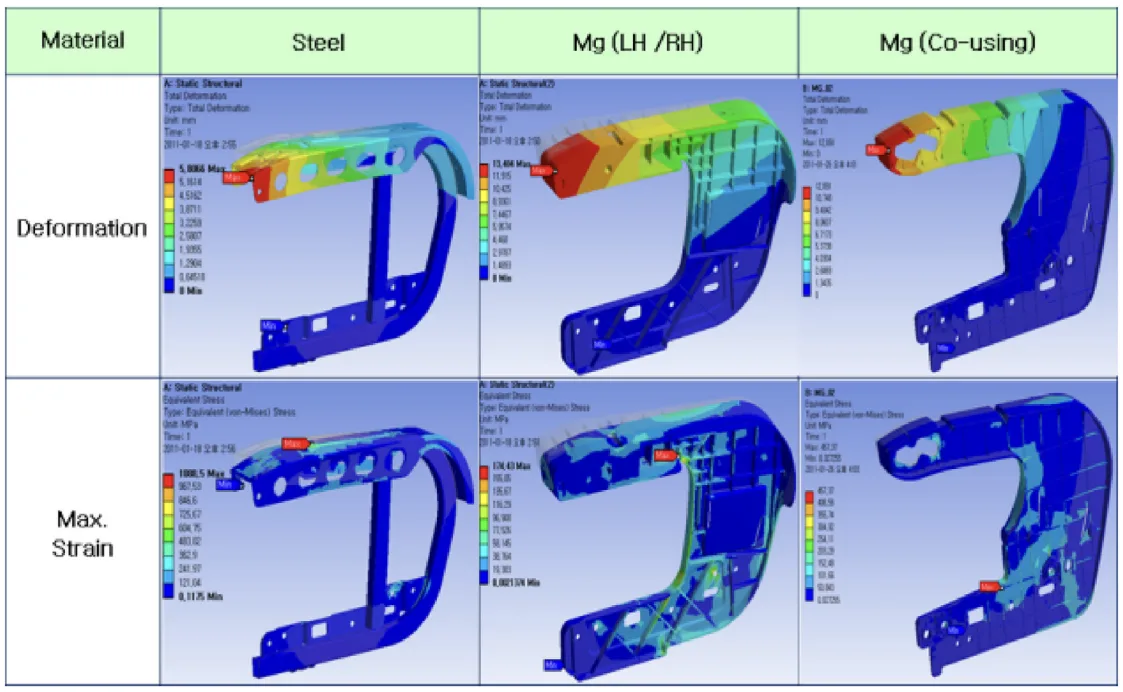
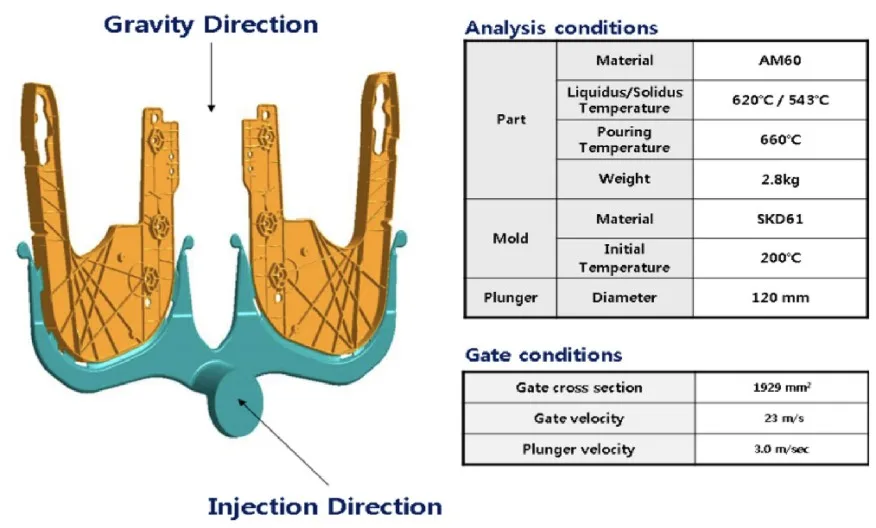
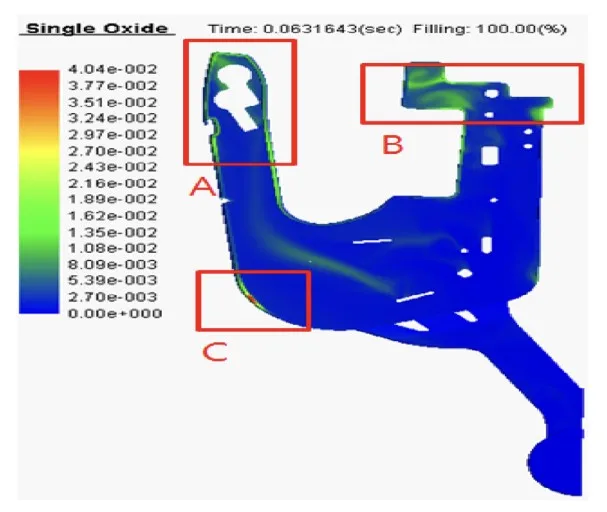
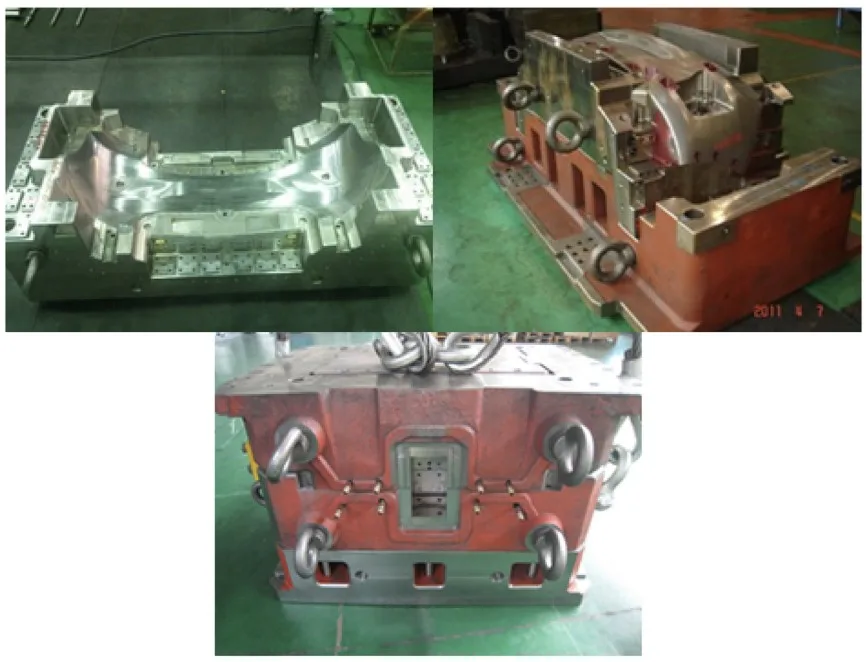
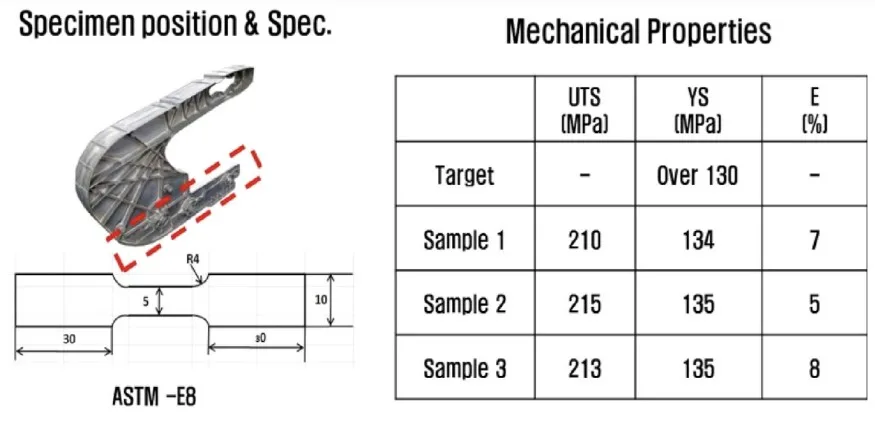
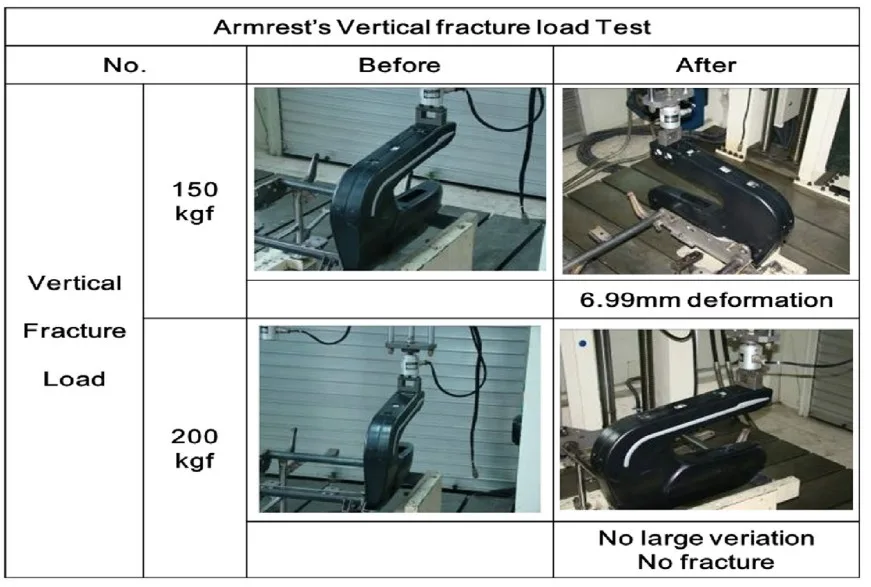
6. 결론 및 논의:
- 주요 결과 요약: 본 연구는 강철을 마그네슘 합금 AM60으로 대체하고 고진공 다이캐스팅 공정을 활용하여 경량 버스 팔걸이를 성공적으로 개발했습니다. 마그네슘 팔걸이는 상당한 중량 감소를 달성했으며, 제조 부품 수를 5개에서 2개로 줄였고, 수직 파괴 하중, 피로 시험 및 항복 강도 요구 사항을 성공적으로 충족했습니다.
- 연구의 학문적 의의: 본 연구는 복잡한 자동차 부품 제조에 마그네슘 합금 AM60과 고진공 다이캐스팅을 적용하는 데 대한 귀중한 통찰력을 제공합니다. 마그네슘 합금을 구조 부품에서 강철과 같은 더 무거운 재료를 대체하는 데 사용할 수 있음을 입증하여 경량 차량 설계 원칙에 기여합니다.
- 연구의 실제적 의미: 경량 마그네슘 버스 팔걸이의 성공적인 개발은 자동차 산업, 특히 버스 및 상용차 제조에 상당한 실제적 의미를 갖습니다. 달성된 중량 감소는 잠재적인 연료 절감 및 배출 감소로 이어집니다. 또한 좌우측 모두를 위한 올인원 디자인은 제조 공정을 간소화하여 잠재적으로 생산 비용을 절감하고 재고 관리를 개선합니다. 연구 결과는 점점 더 엄격해지는 환경 규제를 충족하고 차량 효율성을 개선하기 위해 차량 부품에 마그네슘 합금을 더 널리 채택할 수 있는 경로를 제시합니다.
- 연구의 한계: 논문은 마그네슘 팔걸이의 성공적인 개발을 입증하지만, 특정 부품 및 합금에 주로 초점을 맞추고 있습니다. 이러한 연구 결과의 일반화 가능성을 다른 차량 부품 및 다른 마그네슘 합금에 평가하려면 추가 연구가 필요할 수 있습니다. 실제 작동 조건에서의 장기적인 내구성과 대량 생산을 위한 포괄적인 비용 분석 또한 추가 조사가 필요한 영역입니다.
7. 향후 후속 연구:
- 후속 연구 방향: 향후 연구는 마그네슘 합금과 고진공 고압 다이캐스팅을 활용한 상용차 시트 모듈 개발에 초점을 맞춰야 합니다. 여기에는 시트 모듈 내의 다른 부품으로 적용 범위를 확장하고 버스, 트럭 및 전기 자동차에 이러한 경량 솔루션의 채택을 모색하는 것이 포함됩니다.
- 추가 탐구가 필요한 영역: 추가 연구에서는 다음을 탐구해야 합니다.
- 대량 생산 및 비용 효율성을 위한 다이캐스팅 공정 최적화.
- 잠재적으로 향상된 특성 또는 비용 이점을 가진 다른 마그네슘 합금 조사.
- 실제 버스 작동 환경에서 마그네슘 팔걸이의 장기적인 내구성 및 성능 평가.
- 상용차에 마그네슘 합금 부품을 대규모로 구현하기 위한 상세한 비용-편익 분석.
8. 참고 문헌:
- [1] 문민석, 우경동, 강신재, 송준혁, 오제하, 양승모, 작동 중 PEMFC에서 표면 전처리 조건에 따른 STS304 및 STS430의 부식 거동 연구, Int. J. Precis. Eng. Man. 15 (6) (2014) 1201–1205.
- [2] K. Pettersen, P. Bakke, D. Albright, 마그네슘 다이캐스팅 합금 설계, 132차 TMS 컨퍼런스 마그네슘 기술 2002 회의록, 2002년 TMS 연례 회의 240–246.
- [3] P. Bakke, K. Pettersen, S. Guldberg, S. Sannes, 다이캐스트 마그네슘 합금 AM50의 기계적 물성에 대한 금속 청결도의 영향, K.U. Kainer (편집), 마그네슘 합금 및 응용 분야, Wiley-VCH Verlag GmbH, 독일, 2006, pp. 739–745.
- [4] 신현우, 한병수, 유희종, 정희헌, 진공 다이캐스팅 공정을 이용한 마그네슘 시트 프레임 개발, J. KSPE 26 (3) (2009) 88–97.
- [5] P. Bakke, K. Pettersen, H. Westengen, 희토류 첨가를 통한 마그네슘 다이캐스팅 합금의 강도 및 연성 개선, JOM 55 (11) (2003) 46–51.
- [6] G. Gu, S. Lin, Y Xia, Q Zhou, 다이캐스트 AM60 마그네슘 합금의 기계적 거동에 대한 단면 두께의 영향에 대한 실험적 연구, Mater. Des. 38 (2012) 124–132.
- [7] A. Kiełbus, T. Rzychoń, R. Cibis, AM50 다이캐스팅 마그네슘 합금의 미세 구조, J. Achiev. Mater. Manuf. Eng. 18 (1-2) (2006) 135–138.
- [8] 서정훈, 김성균, 상온 및 고온에서 0.25-0.65wt% CaO 첨가된 AM60B Eco-Mg 다이캐스팅의 기계적 물성, J. Korea Foundry Soc. 31 (1) (2011) 11–17.
- [9] O. Unal, M. Tiryakioğlu, Mg 합금 주조물의 연성 잠재력 및 구조적 품질 평가, Mater. Sci. Eng. A 643 (2015) 51–54.
- [10] K. Máthis, F. Chmelík, M. Janeček, B. Hadzima, Z. Trojanová, P. Lukác, 음향 방출 기술을 이용한 AM60 마그네슘 합금의 변형 과정 조사, Acta Mater. 54 (2006) 5361–5366.
9. 저작권:
- 본 자료는 유명한 외 [논문 제목: AM60 합금을 사용한 고진공 고압 다이캐스팅 공정을 이용한 버스 팔걸이 제작 공정 개발] 논문을 기반으로 작성되었습니다.
- 논문 출처: https://doi.org/10.1016/j.rcim.2018.01.004
본 자료는 위 논문을 요약한 것으로, 상업적 목적으로 무단 사용하는 것을 금지합니다.
Copyright © 2025 CASTMAN. All rights reserved.