본 소개 내용은 [MDPI]에서 발행한 ["Phase Field Simulation of Al–Fe–Mn–Si Quaternary Eutectic Solidification"] 의 연구 내용입니다.
![Figure 1. (a) Liquidus projection of the Al-Fe-Si ternary system and (b) Al-Mn-Si ternary system [28].](https://castman.co.kr/wp-content/uploads/image-1343-1024x429.webp)
1. Overview:
- Title: Al–Fe–Mn–Si 4원 공정의 상전이장 시뮬레이션
- Author: Kimiya NouraniNiaki, Murali Uddagiri, Daysianne Isidorio, Oleg Shchyglo, and Ingo Steinbach
- Publication Year: 2025
- Publishing Journal/Academic Society: Metals
- Keywords: 알루미늄; 응고; 금속간 화합물; 4원 합금; 다상 상전이장

2. Abstracts / Introduction
본 연구에서는 3차원 다상 상전이장 시뮬레이션을 통해 다성분계의 공정 평형상을 조사합니다. 방향성 응고 공정을 강조하면서, 본 연구는 특정 온도에서 응고된 액상으로부터 금속간 화합물 Al13Fe4, 라멜라 구조 (FCC-A1), 그리고 4원상 베타-AlMnSi의 성장 동역학을 검토합니다. 4상 반응 L → Al13Fe4 + FCC-A1 + 베타-AlMnSi로 기술되는 공정 변태를 미세 구조 선택 맵 개발을 위해 분석합니다. 이 맵은 초기 시스템 조성 및 라멜라 간격과 안정적인 성장 모드를 연관시킵니다. 결과는 합금 원소의 편석 거동과 변태 속도론에 미치는 영향에 대한 자세한 통찰력을 제공하여 복잡한 합금 시스템에서 공정 미세 구조 진화에 대한 이해를 향상시킵니다.
3. Research Background:
Background of the Research Topic:
알루미늄 합금은 뛰어난 기계적 성질과 지속 가능성 잠재력으로 인해 자동차, 항공 우주 및 운송 산업에서 광범위하게 활용됩니다. 환경 지속 가능성에 대한 세계적인 강조 증가와 알루미늄 합금에 대한 수요 증가는 재활용 알루미늄 합금의 통합으로 효과적으로 해결할 수 있습니다.
이 접근 방식은 생산 비용을 절감할 뿐만 아니라 에너지 소비도 감소시킵니다. 일반적으로 사용되는 알루미늄 합금 중에서 3000 시리즈는 경량성, 높은 기계적 강도 및 우수한 성형성으로 유명합니다 [1]. Fe, Mn 및 Si와 같은 주요 합금 원소는 이러한 특성을 향상시키는 데 중요한 역할을 합니다.
Fe는 다이캐스팅 중 금형 눌어붙음을 방지하고 [2], Si는 액상 유동성을 향상시키며 [3,4], Mn은 금속간 화합물을 안정화시켜 [5,6] 기계적 성질을 향상시킵니다.
그러나 이러한 원소의 적절한 조성을 선택하는 것이 중요하며, 중량 분율을 초과하면 취성 금속간 화합물이 형성되어 [7] 기계적 성능에 부정적인 영향을 미칠 수 있습니다. 따라서 상 형성을 효과적으로 제어하는 것은 설계 및 제조 중 알루미늄 합금의 기계적 성질을 최적화하는 데 필수적입니다 [8-11].
Status of Existing Research:
다성분 합금의 넓은 조성 공간을 탐색하기 위해 전산 방법이 응고 및 평형 조건에서 상 거동을 예측하는 데 사용됩니다. 열역학 모델은 알루미늄 합금 설계에 유용한 도구입니다 [12,13]. CALPHAD 접근 방식은 알루미늄 합금의 재료 설계 및 공정 최적화에 널리 사용됩니다 [1,14].
CALPHAD 방법의 강점은 다성분 시스템에서 열역학적 거동을 예측하기 위해 자체 일관성 매개변수를 사용하는 능력에 있습니다 [8,15]. 상전이장 모델링은 열역학적으로 근거한 편미분 방정식 [21]을 사용하여 응고 [16], 편석 [17-19] 및 결정립 성장 [20]과 같은 복잡한 시스템을 시뮬레이션하는 또 다른 전산 접근 방식입니다. 열처리 중 석출물 형태, 크기, 체적 분율 및 공간 분포의 변화를 정확하게 예측하는 것은 석출 경화 효과를 이해하는 데 매우 중요합니다.
Al2Cu 석출물에 대한 것과 같은 중간 규모 시뮬레이션은 이러한 과정에 대한 통찰력을 제공합니다 [22]. 특히 확산 계면 접근 방식을 사용하는 상전이장 방법은 명시적 계면 추적의 필요성을 제거하여 모델링을 단순화합니다 [21]. 열역학 모델을 통한 알루미늄 합금의 이해 및 설계는 수치 시뮬레이션에 의해 향상됩니다.
이러한 모델은 미세 구조 진화에 영향을 미치는 다양한 요인을 분석할 수 있게 합니다 [22-27]. 그러나 알루미늄 합금에서 뚜렷한 4원상에 대한 증거는 제한적입니다.
예를 들어, α-AlMnSi상은 4원 시스템으로 상당히 확장되어 3원 Al-Fe-Si 시스템에 접근하지만, Al-Fe-Mn-Si 시스템의 알루미늄이 풍부한 코너에는 안정적인 4원상이 존재하지 않습니다 [28]. 전산 열역학과 다상 상전이장 모델을 결합하면 다성분 시스템에서 상 분포에 대한 자세한 분석이 가능합니다.
Warmuzek [29]에 따르면, 막대 모양의 FCC-A1 형태는 두 가지 주요 반응을 포함하는 공정 변태를 통해 형성될 수 있습니다. 그러나 다성분 알루미늄 합금의 4원상에 대한 실험 데이터는 여전히 부족합니다. 더욱이 Al13Fe4는 Al 기반 합금의 미세 구조 및 특성에 미치는 영향 때문에 Al-Fe-Mn-Si 시스템에서 중요한 금속간 화합물상입니다.
이 상은 Al-Fe-Si 시스템의 Al이 풍부한 코너에서 형성되는 유일한 평형상이며 공정 반응의 일부로 응고 중에 형성됩니다. 이 상은 알루미늄에 대한 낮은 용해도 때문에 철이 축적되는 재활용 알루미늄 합금에서 특히 일반적입니다.
Quan Li et al. [7]에서 보고한 바와 같이, Al13Fe4 금속간 화합물상은 응력 집중 장치 역할을 하여 연성 및 내식성을 감소시켜 철 함량이 높은 재활용 알루미늄 합금의 기계적 성질에 부정적인 영향을 미칩니다 [30].
따라서 이러한 상의 형성, 형태 및 기타 금속간 화합물과의 상호 작용을 이해하는 것은 유해한 영향을 완화하는 합금을 설계하는 데 필수적입니다 [31]. 이러한 연구는 알루미늄 합금의 구조적 성능, 재활용성, 기계적 및 내식성 특성을 개선하는 데 기여합니다 [32].
Necessity of the Research:
본 연구의 목적은 두 가지입니다. 첫째, 4원상 베타-AlMnSi의 출현으로 이어지는 주요 반응을 통해 형성된 공정 고체상의 미세 구조 선택 맵을 개발하는 것입니다. 둘째, 상전이장 방법을 사용하여 4원상을 질적 및 양적으로 특성화하는 것입니다.
본 연구는 FCC-A1의 라멜라 구조, 금속간 화합물 석출, 미세 구조 진화, 그리고 4원상으로서 베타-AlMnSi의 공간 분포에 중점을 둡니다. 다상 상전이장 시뮬레이션을 통해 수행된 이러한 연구는 복잡한 공정 시스템에서 미세 구조 형성을 지배하는 메커니즘에 대한 포괄적인 이해를 제공하는 것을 목표로 합니다.
4. Research Purpose and Research Questions:
Research Purpose:
본 연구의 목적은 두 가지입니다. 첫째, 4원상 베타-AlMnSi의 출현으로 이어지는 주요 반응을 통해 형성된 공정 고체상의 미세 구조 선택 맵을 개발하는 것입니다. 둘째, 상전이장 방법을 사용하여 4원상을 질적 및 양적으로 특성화하는 것입니다.
Key Research:
본 연구는 다음 사항에 중점을 둡니다.
- FCC-A1의 라멜라 구조,
- 금속간 화합물 석출,
- 미세 구조 진화, 그리고
- 4원상으로서 베타-AlMnSi의 공간 분포.
다상 상전이장 시뮬레이션을 통해 수행된 이러한 연구는 복잡한 공정 시스템에서 미세 구조 형성을 지배하는 메커니즘에 대한 포괄적인 이해를 제공하는 것을 목표로 합니다.
5. Research Methodology
Research Design:
본 연구에서는 방향성 응고 공정을 강조하면서 다성분계의 공정 평형상을 조사하기 위해 3차원 다상 상전이장 시뮬레이션을 사용합니다. 본 연구에서 사용된 모델은 Steinbach와 공동 연구자 [21,46]가 개발하고 OpenPhase 소프트웨어 버전 4.7을 사용하여 구현한 다성분 다상 상전이장 (MPF) 모델입니다. 시뮬레이션을 위해 60 × 60 × 120 격자 셀과 1 × 10−7 m의 격자 해상도를 가진 3차원 상자를 고려했습니다.
Data Collection Method:
열역학 정보는 Thermo-Calc 소프트웨어 버전 2021b에 구현된 CALPHAD 방법을 사용하여 COST-507 데이터베이스에서 얻습니다. 시스템 온도는 일정한 열 기울기 및 냉각 속도를 고려하는 동결 온도 방법을 사용하여 업데이트됩니다 [47]. 핵 생성은 핵 생성 장벽을 초과하는 국부 구동력과 관련된 AL Greer의 접근 방식 [49,50]을 기반으로 모델링되었습니다.
Analysis Method:
상전이장 접근 방식 [40]은 상 변태 중 재료의 미세 구조 진화를 모델링하는 데 사용되는 잘 확립된 수치 시뮬레이션 기술입니다. 이 방법은 상호 작용을 해결하기 위해 "확산 계면 모델"을 사용합니다. 다상 상전이장 (MPF) 모델은 상 전체의 용질 조성 진화를 나타내기 위해 확산 방정식을 통합합니다. 열역학적 최소화는 상전이장으로부터 유도된 혼합물 농도 및 개별 상 분율을 기반으로 상 농도를 결정하는 데 필수적입니다.
Research Subjects and Scope:
표 3에 제시된 4원 Al-Fe-Mn-Si 시스템의 공칭 조성은 실험 참조 [51]에서 유래되었습니다. 시뮬레이션 도메인은 시뮬레이션 상자의 제한된 크기로 인해 단일 결정립 내에서 다중 수지상 성장의 규모로 제한됩니다. 본 연구는 4상 반응 L → Al13Fe4 + FCC-A1 + 베타-AlMnSi에 중점을 둡니다.
6. Main Research Results:
Key Research Results:
- 시뮬레이션 결과는 선택된 합금 시스템의 경우 응고가 액체 전체에 걸쳐 구형 공정상 Al13Fe4의 핵 생성 및 성장으로 시작됨을 나타냅니다.
- 응고가 진행되고 시스템 온도가 감소함에 따라 1차 공정 FCC-A1상이 성장 방향을 따라 형성됩니다.
- 그 후, 잔류 액체의 과포화는 4원상 베타-AlMnSi상의 핵 생성을 유도합니다.
- 시뮬레이션 결과에서 얻은 이러한 상의 체적 분율은 Al-Fe-Mn-Si 시스템에 대한 개방형 데이터베이스를 사용하여 수행된 열역학적 계산과 밀접하게 일치합니다.
- 원소 분포 분석은 Al-Fe-Mn-Si 시스템에서 합금 원소의 편석 거동에 상당한 변화가 있음을 보여줍니다.
- 원소 Fe와 Mn은 주로 Al13Fe4상 형성과 관련이 있는 반면, 실리콘 (Si)은 주로 1차 공정 FCC-A1상에서 발견됩니다.
- 4원상 베타-AlMnSi상에서 안정제 역할을 하는 Mn과 Si의 확산성은 농도에서 상승 추세를 보입니다.
- 공정상에서 라인 스캔 분석은 베타-AlMnSi상에서 Fe의 뚜렷한 편석 거동을 보여줍니다. 초기에 Fe는 액상으로 더 높은 수준의 편석을 나타내지만, 액상이 4원상 베타-AlMnSi상으로 변환됨에 따라 점차 감소합니다. 이 상에서 Fe의 현저한 고갈이 관찰됩니다.
Analysis of presented data:
- 금속간 화합물 형성: 시뮬레이션은 공정 응고 중 Al13Fe4, FCC-A1 및 베타-AlMnSi 상의 순차적 형성을 성공적으로 포착했습니다. Al13Fe4 상이 먼저 핵 생성되고, FCC-A1이 뒤따르고, 마지막으로 잔류 액체에서 베타-AlMnSi가 형성됩니다.
- 미세 구조 진화: 3차원 상전이장 시뮬레이션은 미세 구조 진화를 효과적으로 시각화하여 다양한 상의 공간 분포 및 상호 작용을 보여줍니다. FCC-A1 상은 라멜라 또는 막대 모양의 공정 구조를 형성합니다.
- 원소 편석: 시뮬레이션은 합금 원소의 상당한 편석을 보여줍니다. Fe와 Mn은 Al13Fe4 상에서 농축되는 반면, Si는 FCC-A1 상에서 더 농축됩니다. 베타-AlMnSi 상은 Mn 및 Si 농축과 Fe 고갈을 나타냅니다.
- 상 체적 분율: 시뮬레이션에서 얻은 상의 체적 분율은 COST-507 데이터베이스 및 Thermo-Calc 소프트웨어를 사용한 열역학적 계산과 일치합니다.
Figure Name List:
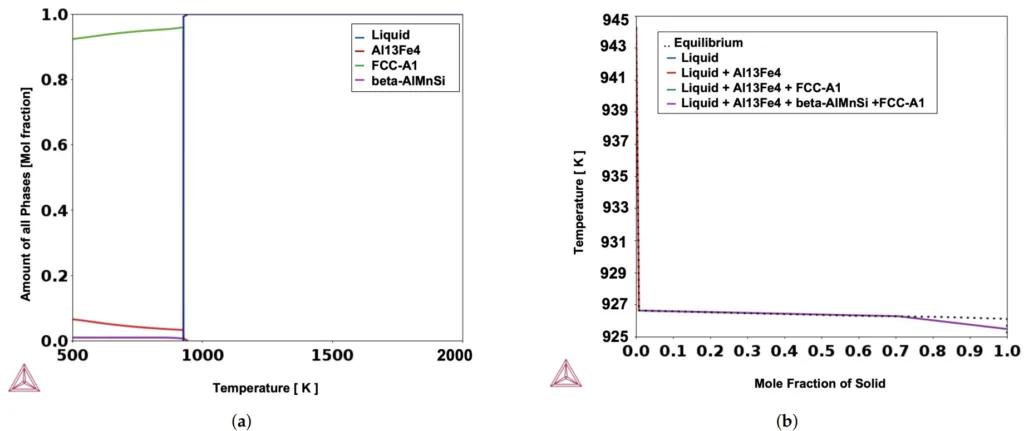
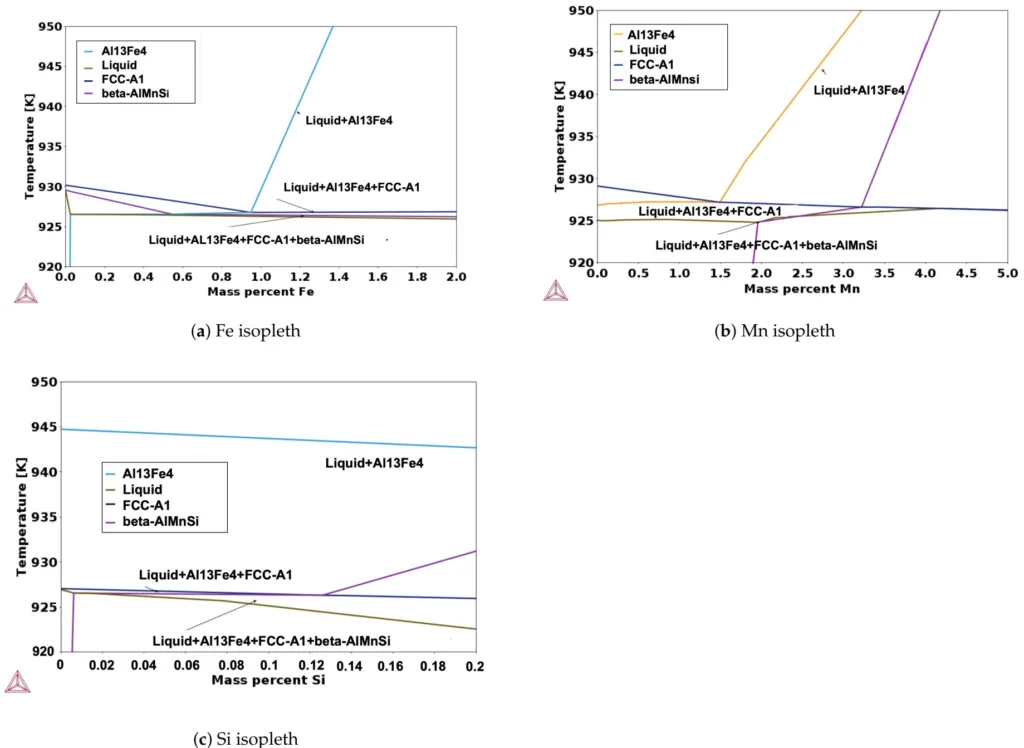
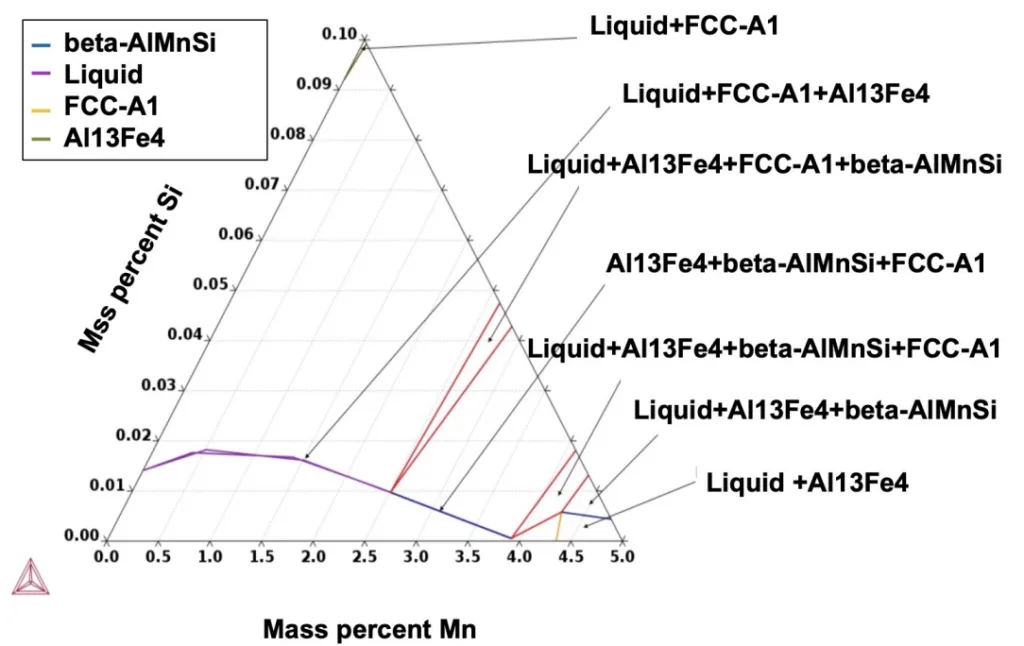
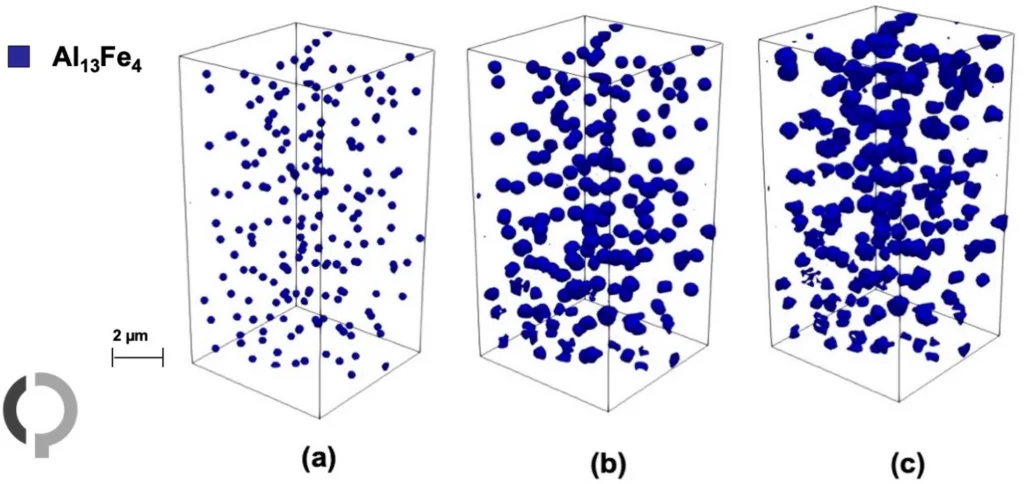
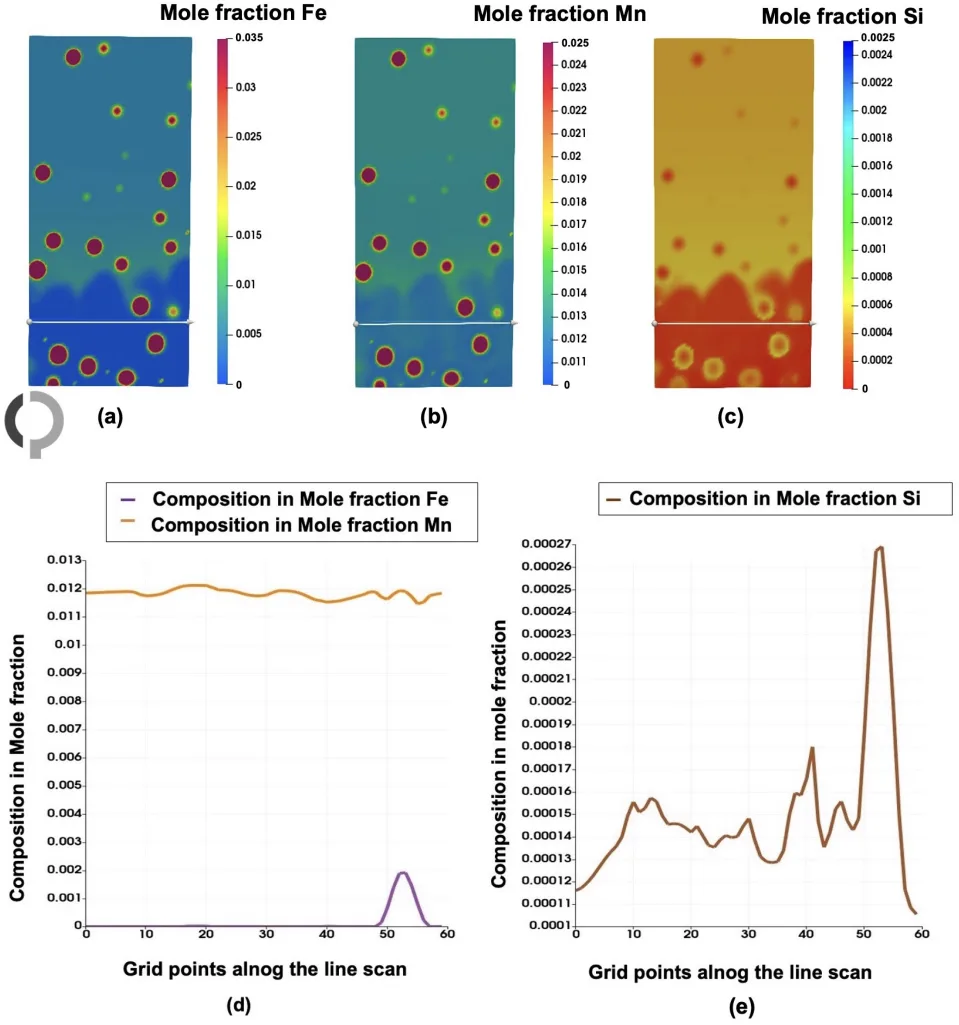
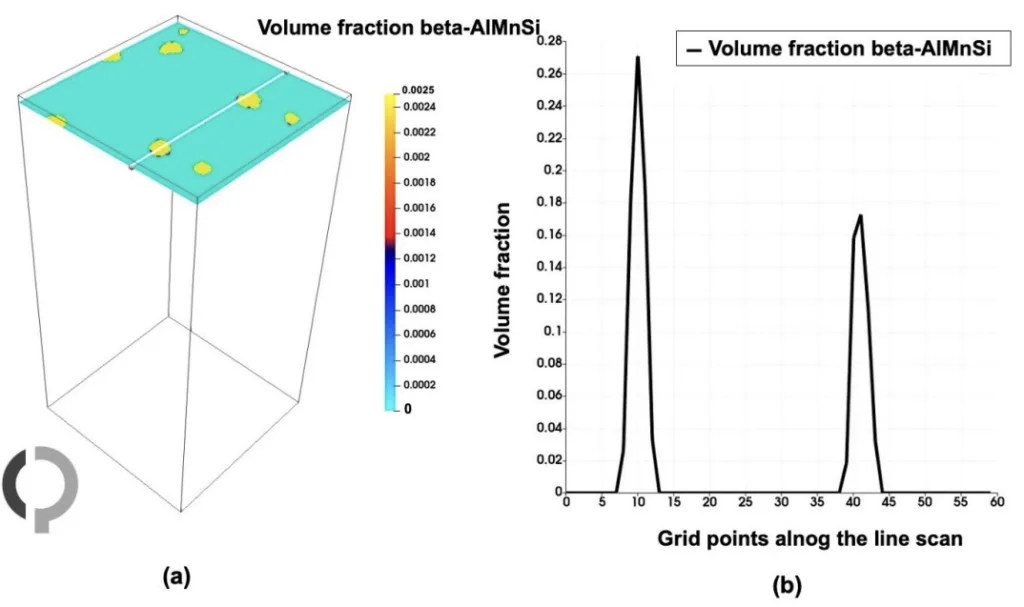
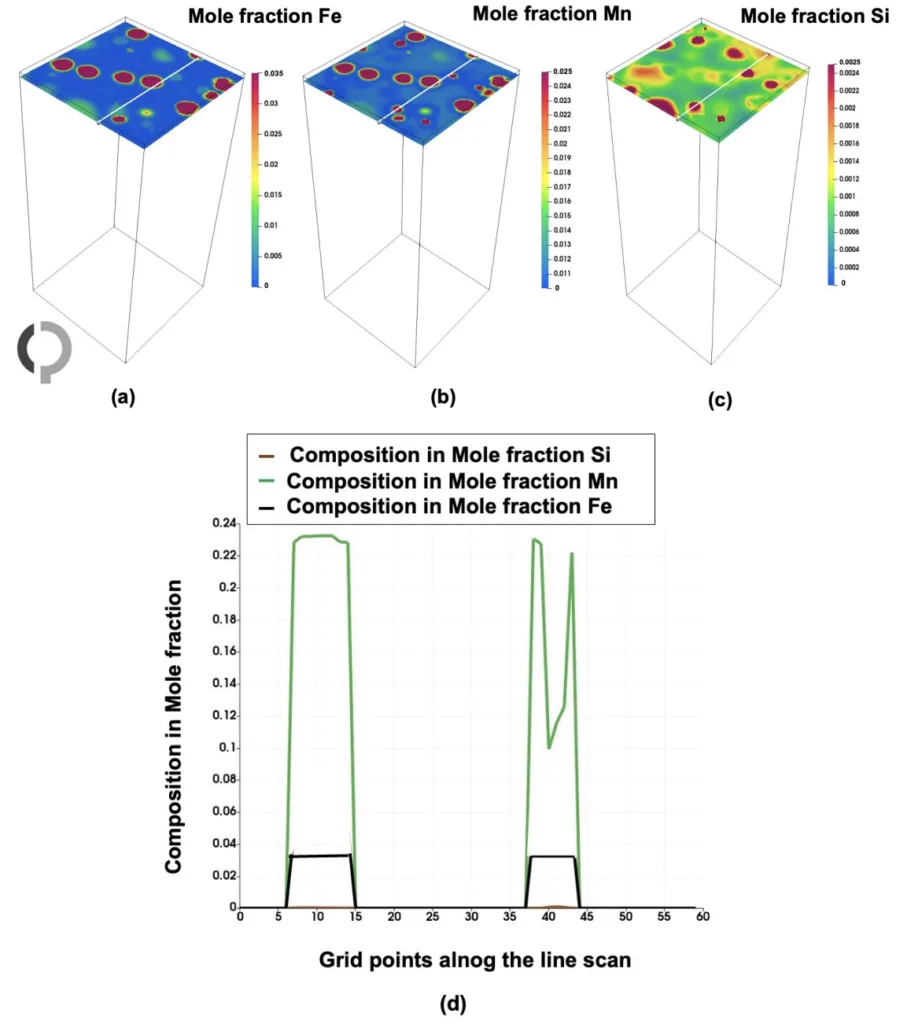
- Figure 1. (a) Al-Fe-Si 3원계의 액상 투영도 및 (b) Al-Mn-Si 3원계의 액상 투영도 [28].
- Figure 2. 표 3의 원소 백분율을 기준으로 온도 함수로서 평형 조건에서 안정적인 상 분율 계산: (a) 및 (b) 표 3의 원소 함량을 기준으로 Scheil-Gulliver 응고 사용.
- Figure 3. 등온 단면 상 다이어그램 (a−c)은 과냉각된 액체로부터 FCC-A1, Al13Fe4 및 fi-AlMnSi의 핵 생성 및 성장을 보여줍니다. X축은 온도에 따른 (a) Fe, (b) Mn 및 (c) Si의 화학 조성을 나타냅니다.
- Figure 4. FCC-A1, Al13Fe4 및 베타-AlMnSi와 액체가 풍부한 코너 알루미늄에서 Mn 및 Si 원소가 삼각형 변에 있는 Al-Fe-Mn-Si 합금 시스템의 액체.
- Figure 5. (a) t0 = 0.0195 s에서 Al13Fe4의 핵 생성, (b) t1 = 0.031 s에서 이 석출물의 성장, (c) t2 = 0.052 s에서 석출물의 완료.
- Figure 6. (a) t0 = 0.0255 s에서 FCC-A1의 핵 생성, (b) t1 = 0.031 s에서 이 상의 성장, (c) t2 = 0.052 s에서 고체상의 완료.
- Figure 7. (a) t0 = 0.039 s에서 베타-AlMnSi의 핵 생성, (b) t1 = 0.04 s에서 이 상의 성장, (c) t2 = 0.052 s에서 상의 완료.
- Figure 8. 4가지 다른 시간 단계에서 공정 반응을 통한 방향성 응고 중 다성분 Al-Fe-Mn-Si 시스템의 미세 구조 진화: (a) t0 = 0.0255 s, (b) t1 = 0.032 s, (c) t2 = 0.039 s 및 (d) t3 = 0.052 s, 다상 상전이장 시뮬레이션에서 Al13Fe4 (진한 파란색), FCC-A1 (밝은 파란색) 및 베타-AlMnSi (주황색)의 상 분율을 보여줍니다.
- Figure 9. 다성분 Al-Fe-Mn-Si 시스템에서 모든 용질 성분의 농도 분포 (a) Fe, (b) Mn, (c) t = 0.04 s에서 Si. (d) 상 정보가 있는 형태가 오른쪽에 표시됩니다.
- Figure 10. (a) 흰색 선을 따라 Al13Fe4의 체적 분율의 라인 스캔. (b) Al13Fe4 및 액상의 체적 분율을 묘사합니다.
- Figure 11. 흰색 선으로 표시된 Al13Fe4 및 액상에서 특정 시간 단계에서 Al-Fe-Mn-Si 시스템의 용질 원소의 라인 스캔. (a−c) 각각 Fe, Mn 및 Si의 몰 분율을 보여줍니다. (d,e) Fe와 Mn이 편석되고 Si가 고갈된 상 존재를 강조 표시합니다.
- Figure 12. (a) 흰색 선을 따라 액체의 체적 분율의 라인 스캔. (b) FCC-A1 및 액상의 체적 분율을 보여줍니다.
- Figure 13. 흰색 선으로 표시된 FCC-A1 및 액상에서 특정 시간 단계에서 Al-Fe-Mn-Si 시스템의 용질 원소의 라인 스캔. (a−c) 각각 Fe, Mn 및 Si의 몰 분율을 보여줍니다. (d,e) Fe와 Mn이 고갈되고 Si가 편석된 상 존재를 강조 표시합니다.
- Figure 14. (a) 흰색 선으로 표시된 베타-AlMnSi의 체적 분율의 라인 스캔. (b) 베타-AlMnSi 상의 체적 분율을 보여줍니다.
- Figure 15. 흰색 선으로 표시된 베타-AlMnSi 상을 따라 특정 시간 단계에서 Al-Fe-Mn-Si 시스템의 용질 원소의 라인 스캔. (a−c) 각각 Fe, Mn 및 Si의 몰 분율을 보여줍니다. (d) Fe가 고갈되고 Si와 Mn이 편석된 상 존재를 강조 표시합니다.
7. Conclusion:
Summary of Key Findings:
방향성 응고 조건에서 다성분 Al-Fe-Mn-Si 시스템의 공정 응고 형태를 CALPHAD 열역학 데이터베이스와 결합된 다상 상전이장 모델을 사용하여 조사합니다. 3차원 미세 구조 선택 맵은 세 가지 뚜렷한 고체상, 즉 금속간 화합물 Al13Fe4, 1차 공정 FCC-A1 및 4원상 베타-AlMnSi의 형성을 보여줍니다.
응고는 Al13Fe4 핵 생성으로 시작되고, FCC-A1 성장이 뒤따르고, 마지막으로 과포화된 액체에서 베타-AlMnSi 핵 생성이 일어납니다.
원소 분포 분석은 Al13Fe4에서 Fe 및 Mn 편석, FCC-A1에서 Si, 베타-AlMnSi에서 Fe 고갈과 함께 Mn 및 Si 농축을 보여줍니다. 라인 스캔은 베타-AlMnSi에서 Fe 고갈과 다양한 상에서 Fe, Mn 및 Si의 뚜렷한 편석 거동을 확인합니다.
Academic Significance of the Study:
본 연구는 고급 상전이장 시뮬레이션을 사용하여 복잡한 4원 Al-Fe-Mn-Si 합금 시스템에서 공정 응고 과정에 대한 자세한 이해를 제공합니다. 본 연구는 다상 상전이장 모델이 CALPHAD 데이터베이스와 결합되어 다성분 합금에서 미세 구조 진화 및 원소 편석을 예측하고 분석하는 능력을 성공적으로 입증합니다.
결과는 특히 4원상 형성과 관련하여 복잡한 합금 시스템에서 상 변태 및 응고 속도론에 대한 기본적인 지식을 향상시킵니다.
Practical Implications:
개발된 미세 구조 선택 맵과 상 형성 및 원소 편석에 대한 통찰력은 Al-Fe-Mn-Si 합금의 설계 및 가공을 최적화하는 데 활용될 수 있습니다. 각 합금 원소의 역할과 상 형성 순서를 이해하면 미세 구조를 제어하고 다이캐스팅 알루미늄 합금의 기계적 성질을 개선하는 데 도움이 될 수 있습니다.
이는 철이 일반적인 불순물이고 Al13Fe4와 같은 금속간 화합물의 형성이 성능에 상당한 영향을 미치는 재활용 알루미늄 합금과 특히 관련이 있습니다. 본 연구는 다이캐스팅 산업의 합금 설계자 및 공정 엔지니어에게 전산 도구 및 지식 기반을 제공합니다.
Limitations of the Study and Areas for Future Research:
다양한 상에서 계면 이방성의 영향을 정량화하려면 추가 연구가 필요합니다. 또한 본 연구의 시뮬레이션은 실험 데이터와 열역학적 모델링 결과를 모두 참조하여 설계되었습니다. 그러나 얻어진 시뮬레이션 결과는 동일한 합금 조성으로 수행된 실험 연구를 통해 직접 검증해야 합니다.
향후 연구는 시뮬레이션 결과의 실험적 검증과 계면 이방성 및 보다 자세한 동역학 데이터를 통합하여 모델을 더욱 개선하는 데 초점을 맞출 수 있습니다. 더 넓은 범위의 합금 조성 및 응고 조건을 조사하는 것도 유익할 것입니다.
8. References:
- [1] Chen, H.L.; Chen, Q.; Engström, A. Development and applications of the TCAL aluminum alloy database. Calphad 2018, 62, 154-171.
- [2] Otani, L.B.; Soyama, J.; Zepon, G.; Costa e Silva, A.; Kiminami, C.S.; Botta, W.J.; Bolfarini, C. Predicting the formation of intermetallic phases in the Al-Si-Fe system with Mn additions. J. Phase Equilibria Diffus. 2017, 38, 298-304.
- [3] Zolotorevsky, V.S.; Belov, N.A.; Glazoff, M.V. Casting Aluminum Alloys; Elsevier: Amsterdam, The Netherlands, 2007; Volume 12.
- [4] Callegari, B.; Lima, T.N.; Coelho, R.S. The influence of alloying elements on the microstructure and properties of Al-Si-based casting alloys: A review. Metals 2023, 13, 1174.
- [5] Tian, N.; Wang, G.; Zhou, Y.; Liu, C.; Liu, K.; Zhao, G.; Zuo, L. Phase Formation and Microstructure Evolution of Al-5Si-0.8 Mg Alloys with Different Mn Concentrations. Metals 2021, 11, 308.
- [6] Zhenjie, C.; Haichang, J.; Duo, Z.; Qijuan, D.; Junjun, P.; Luanluan, J. Influence of Mn on the precipitates in 6082 aluminum alloy. J. Mater. Sci. 2024, 59, 9734-9748.
- [7] Li, Q.; Wang, J.; Xue, C.; Wang, S.; Yang, X.; Tian, G.; Su, H.; Li, X.; Miao, Y. Transforming detrimental intermetallics by accumulative thermal and strain energies in the Al-Fe-Si alloy. J. Mater. Sci. 2024, 59, 1699–1720.
- [8] Moore, E.; Turchi, P.; Lordi, V.; Weiss, D.; Sims, Z.; Henderson, H.; Kesler, M.; Rios, O.; McCall, S.; Perron, A. Thermodynamic Modeling of the Al-Ce-Cu-Mg-Si System and Its Application to Aluminum-Cerium Alloy Design. J. Phase Equilibria Diffus. 2020, 41, 764-783.
- [9] Liu, G.; Müller, D.B. Addressing sustainability in the aluminum industry: A critical review of life cycle assessments. J. Clean. Prod. 2012, 35, 108-117.
- [10] Shabestari, S. The effect of iron and manganese on the formation of intermetallic compounds in aluminum-silicon alloys. Mater. Sci. Eng. A 2004, 383, 289–298.
- [11] Wang, E.; Hui, X.; Chen, G. Eutectic Al-Si-Cu-Fe-Mn alloys with enhanced mechanical properties at room and elevated temperature. Mater. Des. 2011, 32, 4333-4340.
- [12] Liu, C.; Garner, A.; Zhao, H.; Prangnell, P.B.; Gault, B.; Raabe, D.; Shanthraj, P. CALPHAD-informed phase-field modeling of grain boundary microchemistry and precipitation in Al-Zn-Mg-Cu alloys. Acta Mater. 2021, 214, 116966.
- [13] Liu, C.; Davis, A.; Fellowes, J.; Prangnell, P.B.; Raabe, D.; Shanthraj, P. CALPHAD-informed phase-field model for two-sublattice phases based on chemical potentials: η-phase precipitation in Al-Zn-Mg-Cu alloys. Acta Mater. 2022, 226, 117602.
- [14] Zhang, F.; Liang, S.; Zhang, C.; Chen, S.; Lv, D.; Cao, W.; Kou, S. Prediction of cracking susceptibility of commercial aluminum alloys during solidification. Metals 2021, 11, 1479.
- [15] Jha, R.; Dulikravich, G.S. Temperature Regimes and Chemistry for Stabilizing Precipitation Hardening Phases in Al-Sc Alloys: Combined CALPHAD-Deep Machine Learning. ASME Open J. Eng. 2022, 1. spanning 12 pages.
- [16] Jreidini, P.; Pinomaa, T.; Wiezorek, J.M.; McKeown, J.T.; Laukkanen, A.; Provatas, N. Orientation gradients in rapidly solidified pure aluminum thin films: comparison of experiments and phase-field crystal simulations. Phys. Rev. Lett. 2021, 127, 205701.
- [17] Chen, J.; Guo, M.; Yang, M.; Cui, T.; Cui, B.; Zhang, J. Insight into element segregation mechanisms during creep in γ'-strengthened Co-based superalloy by elastoplastic phase-field simulation. Prog. Nat. Sci. Mater. Int. 2024, 34, 873–879.
- [18] Liu, X.; Shen, W.; Liu, W. Phase-Field Simulation of Precipitation and Grain Boundary Segregation in Fe-Cr-Al Alloys under Irradiation. Nanomaterials 2024, 14, 1198.
- [19] Gong, T.Z.; Chen, Y.; Hao, W.Y.; Chen, X.Q.; Li, D.Z. Modeling segregation of Fe-C alloy in solidification by phase-field method coupled with thermodynamics. Metals 2023, 13, 1148.
- [20] Staublin, P.; Mukherjee, A.; Warren, J.A.; Voorhees, P.W. Phase-field model for anisotropic grain growth. Acta Mater. 2022, 237, 118169.
- [21] Steinbach, I. Phase-field models in materials science. Model. Simul. Mater. Sci. Eng. 2009, 17, 073001.
- [22] Ji, Y.; Ghaffari, B.; Li, M.; Chen, L.Q. Phase-field modeling of e' precipitation kinetics in 319 aluminum alloys. Comput. Mater. Sci. 2018, 151, 84-94.
- [23] Provatas, N.; Elder, K. Phase-Field Methods in Materials Science and Engineering; John Wiley & Sons: Hoboken, NJ, USA, 2011.
- [24] Jokisaari, A.M.; Voorhees, P.W.; Guyer, J.E.; Warren, J.A.; Heinonen, O.G. Phase field benchmark problems for dendritic growth and linear elasticity. Comput. Mater. Sci. 2018, 149, 336-347.
- [25] Biswas, S.; Schwen, D.; Singh, J.; Tomar, V. A study of the evolution of microstructure and consolidation kinetics during sintering using a phase field modeling based approach. Extrem. Mech. Lett. 2016, 7, 78–89.
- [26] Biswas, S.; Schwen, D.; Tomar, V. Implementation of a phase field model for simulating evolution of two powder particles representing microstructural changes during sintering. J. Mater. Sci. 2018, 53, 5799–5825.
- [27] Militzer, M. Phase field modeling of microstructure evolution in steels. Curr. Opin. Solid State Mater. Sci. 2011, 15, 106–115.
- [28] Lacaze, J.; Eleno, L.; Sundman, B. Thermodynamic assessment of the aluminum corner of the Al-Fe-Mn-Si system. Metall. Mater. Trans. A 2010, 41, 2208-2215.
- [29] Warmuzek, M.; Ratuszek, W.; Sęk-Sas, G. Chemical inhomogeneity of intermetallic phases precipitates formed during solidification of Al-Si alloys. Mater. Charact. 2005, 54, 31-40.
- [30] Allen, C.; O'reilly, K.; Cantor, B.; Evans, P. Intermetallic phase selection in 1XXX Al alloys. Prog. Mater. Sci. 1998, 43, 89–170.
- [31] Arbeiter, J.; Vončina, M.; Volšak, D.; Medved, J. Evolution of Fe-based intermetallic phases during homogenization of Al-Fe hypoeutectic alloy. J. Therm. Anal. Calorim. 2020, 142, 1693–1699.
- [32] Wang, X.; Guan, R.; Misra, R.; Wang, Y.; Li, H.; Shang, Y. The mechanistic contribution of nanosized Al3Fe phase on the mechanical properties of Al-Fe alloy. Mater. Sci. Eng. A 2018, 724, 452-460.
- [33] Ansara, I.; Dinsdale, A.; Rand, M. Thermochemical Database for Light Metal Alloys; Office for Official Publications of the European Communities: Luxembourg, 1998.
- [34] Eleno, L.; Vezelỳ, J.; Sundman, B.; Cieslar, M.; Lacaze, J. Assessment of the Al corner of the ternary Al-Fe-Si system. Mater. Sci. Forum 2010, 649, 523-528.
- [35] Zakharov, A.; Guldin, I.; Arnold, A. Phase Diagram of the Al-Si-Fe-Mn System in the 10-14% Si, 0-3% Fe, and 0-4% Mn Concentration Ranges. (Translation). Russ. Metall. 1989, 209-213. Issue 4.
- [36] Flores-V, A.; Sukiennik, M.; Castillejos-E, A.; Acosta-G, F.; Escobedo-B, J. A kinetic study on the nucleation and growth of the Al8FeMnSi2 intermetallic compound for aluminum scrap purification. Intermetallics 1998, 6, 217-227.
- [37] Onderka, B.; Sukiennik, M.; Fitzner, K. Determination of the stability of Al11. 8FeMn1. 6Si1. 6 phase existing in the quaternary Al-Fe-Mn-Si system. Arch. Metall. 2000, 45, 119–132.
- [38] Munson, D. A clarification of the phases occurring in aluminium-rich aluminium-iron-silicon alloys, with particular reference to the ternary phase alpha-AlFeSi. Inst. Met. J. 1967, 95, 217–219.
- [39] Tibballs, J.; Horst, J.; Simensen, C. Precipitation of a-Al (Fe, Mn) Si from the melt. J. Mater. Sci. 2001, 36, 937–941.
- [40] Steinbach, I.; Pezzolla, F.; Nestler, B.; Seeßelberg, M.; Prieler, R.; Schmitz, G.J.; Rezende, J.L. A phase field concept for multiphase systems. Phys. D Nonlinear Phenom. 1996, 94, 135-147.
- [41] Uddagiri, M.; Shchyglo, O.; Steinbach, I.; Tegeler, M. Solidification of the Ni-based superalloy CMSX-4 simulated with full complexity in 3-dimensions. Prog. Addit. Manuf. 2023, 1-12.
- [42] Wang, Z.; Liang, C.; Wang, D.; Yue, X.; Li, J.; Ding, X. Unveiling the Co effect on the temporal evolution kinetics of γ' phase in Ni-Al-Co model superalloys via CALPHAD-informed phase field simulations. Acta Mater. 2023, 258, 119247.
- [43] Wang, Z.; Liang, C.; Wang, D.; Ding, X. Uncovering the effect of Mo addition on the precipitation kinetics of the y' phase in Ni-Al-Mo model superalloys using CALPHAD-assisted phase-field simulations. J. Mater. Sci. 2024, 1–20.
- [44] Thakur, A.K.; Kovacevic, S.; Manga, V.R.; Deymier, P.A.; Muralidharan, K. A first-principles and CALPHAD-assisted phase-field model for microstructure evolution: Application to Mo-V binary alloy systems. Mater. Des. 2023, 235, 112443.
- [45] Warnken, N.; Ma, D.; Drevermann, A.; Reed, R.C.; Fries, S.; Steinbach, I. Phase-field modelling of as-cast microstructure evolution in nickel-based superalloys. Acta Mater. 2009, 57, 5862-5875.
- [46] Steinbach, I.; Böttger, B.; Eiken, J.; Warnken, N.; Fries, S. CALPHAD and phase-field modeling: A successful liaison. J. Phase Equilibria Diffus. 2007, 28, 101–106.
- [47] Keller, T.; Lindwall, G.; Ghosh, S.; Ma, L.; Lane, B.M.; Zhang, F.; Kattner, U.R.; Lass, E.A.; Heigel, J.C.; Idell, Y.; et al. Application of finite element, phase-field, and CALPHAD-based methods to additive manufacturing of Ni-based superalloys. Acta Mater. 2017, 139, 244-253.
- [48] Tegeler, M.; Shchyglo, O.; Kamachali, R.D.; Monas, A.; Steinbach, I.; Sutmann, G. Parallel multiphase field simulations with OpenPhase. Comput. Phys. Commun. 2017, 215, 173–187.
- [49] Greer, A. Overview: Application of heterogeneous nucleation in grain-refining of metals. J. Chem. Phys. 2016, 145.
- [50] Uddagiri, M.; Shchyglo, O.; Steinbach, I.; Wahlmann, B.; Koerner, C. Phase-field study of the history-effect of remelted microstructures on nucleation during additive manufacturing of ni-based superalloys. Metall. Mater. Trans. A 2023, 54, 1825-1842.
- [51] Park, J.; Oh, C.S.; Kang, J.H.; Jung, J.G.; Lee, J.M. Solidification and Precipitation Microstructure Simulation of a Hypereutectic Al-Mn-Fe-Si Alloy in Semi-Quantitative Phase-Field Modeling with Experimental Aid. Metals 2020, 10, 1325.
- [52] Hallstedt, B.; Khvan, A.V.; Lindahl, B.B.; Selleby, M.; Liu, S. PrecHiMn-4-A thermodynamic database for high-Mn steels. Calphad 2017, 56, 49-57.
- [53] Michael, K.; Philipp, S.; Britta, N.; et al. Applications of the phase-field method for the solidification of microstructures in multi-component systems. J. Indian Inst. Sci. 2016, 96, 235-256.
- [54] Thesis, D. Characterization of equilibrium phases in 8xxx alloys for the optimization of the thermodynamic database for MatCalc. Ph.D. Thesis, Technische Universität Wien, Vienna, Austria, 2022.
- [55] Que, Z.; Fang, C.; Mendis, C.L.; Wang, Y.; Fan, Z. Effects of Si solution in 0-A113Fe4 on phase transformation between Fe-containing intermetallic compounds in Al alloys. J. Alloy. Compd. 2023, 932, 167587.
- [56] Yan, X.; Ding, L.; Chen, S.; Xie, F.; Chu, M.; Chang, Y.A. Predicting microstructure and microsegregation in multicomponent aluminum alloys. In Essential Readings in Light Metals: Volume 3 Cast Shop for Aluminum Production; Springer: Berlin/Heidelberg, Germany, 2016; pp. 512–518.
9. Copyright:
- This material is "Kimiya NouraniNiaki"의 논문: "Phase Field Simulation of Al–Fe–Mn–Si Quaternary Eutectic Solidification"을 기반으로 함.
- 논문 출처: https://doi.org/10.3390/met15020135
본 자료는 위 논문을 소개하기 위해 제작되었으며, 상업적 목적으로 무단 사용하는 것을 금지합니다.
Copyright © 2025 CASTMAN. All rights reserved.