이 소개 논문은 "[Journal of Materials Processing Technology]"에서 발행한 논문 "[Studies on Die Filling of A356 Al alloy and Development of a Steering Knuckle Component using Rheo Pressure Die Casting System]"을 기반으로 합니다.
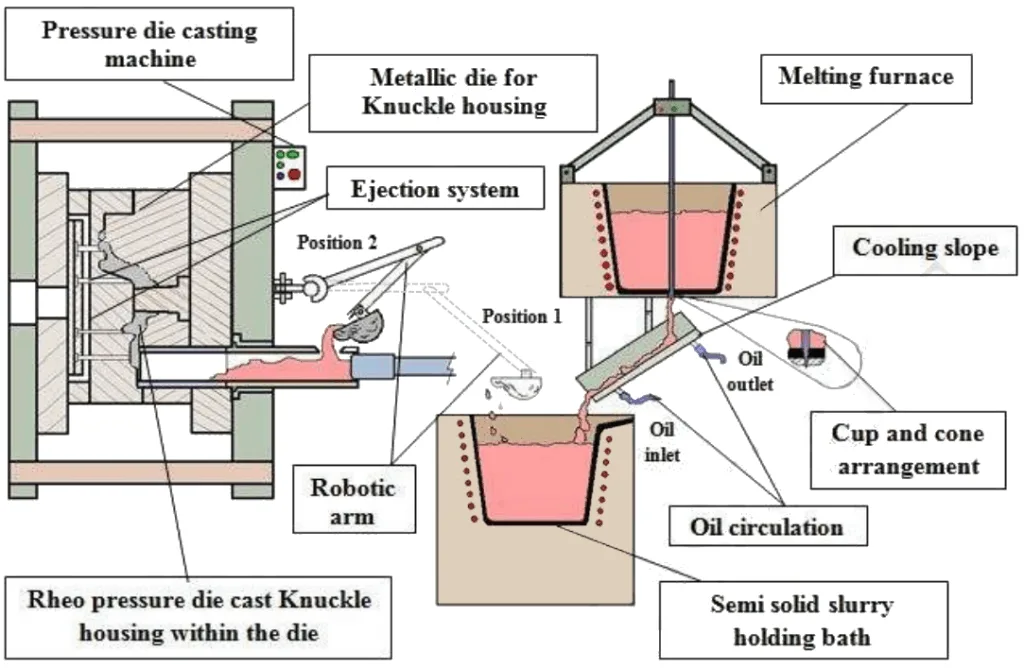
1. 개요:
- 제목: Studies on Die Filling of A356 Al alloy and Development of a Steering Knuckle Component using Rheo Pressure Die Casting System
- 저자: Prosenjit Das, Bikash Bhuniya, Sudip K. Samanta, Pradip Dutta
- 발행 연도: 2019년
- 발행 학술지/학회: Journal of Materials Processing Technology
- 키워드: 스티어링 너클, 반용융, RPDC, A356 합금, 다이 충전
2. 초록:
본 연구에서는 레오 압력 다이캐스팅(RPDC) 시스템의 일부로 반용융 슬러리의 다이 충전을 조사하기 위해 전산 유체 역학(CFD) 모델을 개발합니다. 다이 충전 캐비티는 자동차 스티어링 너클의 그것에 해당하며, 슬러리는 A356 알루미늄 합금으로 만들어집니다. CFD 시뮬레이션에 사용된 유변학적 모델은 실험적으로 결정됩니다. 현재 수치 모델에서 얻은 결과에는 다이 캐비티 내 슬러리의 유동장, 점도 변화, 고상 분율 분포, 다이 충전 단계 중 캐비티 내 응고 중 온도 및 압력 분포가 포함됩니다. 본 연구의 주요 목적은 개발된 부품의 바람직한 미세 구조 및 기계적 특성을 위한 게이팅 배열, 주입 온도 및 사출 조건을 결정하는 것입니다. 해당 합금 슬러리의 다이 충전 능력에 대한 사출 조건의 영향을 연구하기 위해, 최종 사출 속도를 2 ~ 3.2 m/s로 변화시키며 5가지 사출 프로파일을 연구합니다. 본 연구 결과를 확증하기 위해, 응고된 부품의 다른 위치에서 샘플을 채취하여 주로 광학 현미경 및 매크로 경도 측정 형태로 미세 구조 형태 및 구조-특성 상관 관계를 연구합니다.
3. 서론:
자동차 산업의 연비 향상 요구는 자동차 부품 경량화 노력, 특히 다른 경량 자동차 부품에 비해 우수한 강도 대 중량비 및 연신율 값을 요구하는 서스펜션 부품 경량화 노력의 동기가 됩니다. 알루미늄 및 마그네슘 합금의 단조 및 기존 다이캐스팅과 같은 전통적인 제조 공정은 다중 공정 단계, 일관성 없는 기계적 특성, 수지상 미세 구조 및 액상 편석과 같은 문제를 야기합니다. 반용융 다이캐스팅, 특히 레오 다이캐스팅(RDC) 및 그 변형인 레오 압력 다이캐스팅(RPDC)은 향상된 구조적 완전성과 비용 효율성을 갖춘 건전하고 정밀한 형상의 부품을 생산하기 위한 유망한 단일 단계 솔루션으로 부상했습니다. 이러한 공정의 성공은 복잡한 다이 캐비티의 적절한 충전을 보장하기 위해 거의 구형에 가까운 초정 입자를 가진 반용융 슬러리를 준비하는 데 크게 좌우됩니다. 수많은 연구에서 요변성 다이캐스팅(TDC) 및 RDC를 탐구했지만, RPDC에서의 다이 충전에 대한 CFD 시뮬레이션, 특히 실험적 검증을 통한 연구는 상대적으로 부족합니다. 본 연구는 CFD 시뮬레이션을 사용하여 A356 알루미늄 합금 스티어링 너클에 대한 RPDC 공정 변수를 최적화하고 실험 작업을 통해 검증함으로써 이러한 격차를 해소하는 것을 목표로 합니다.
4. 연구 요약:
연구 주제의 배경:
주요 동기는 연비 향상을 위한 경량 자동차 부품의 필요성입니다. 전통적으로 강철이나 주철로 만들어진 자동차 서스펜션 부품은 알루미늄 및 마그네슘 합금을 사용하여 개발되고 있습니다. 그러나 이러한 경합금에 대한 기존 제조 방법은 종종 결함과 일관성 없는 특성을 초래합니다.
이전 연구 현황:
이전 연구에서는 기존 중력 다이캐스팅(GDC), 고압 다이캐스팅(HPDC), 스퀴즈 캐스팅 및 요변성 다이캐스팅(TDC)과 레오 다이캐스팅(RDC)을 포함한 반용융 금속(SSM) 공정과 같은 다양한 주조 공정을 탐구했습니다. 연구에서는 HPDC에서 편석 밴드, 미세 기공 및 열간 균열과 같은 결함이 강조되었습니다. RDC는 TDC에 비해 에너지 및 비용 효율성이 뛰어난 것으로 알려져 있습니다. 여러 연구자들이 다양한 부품 및 합금에 대해 RDC를 조사했으며, 일부는 다양한 유변학적 모델을 사용하여 다이 충전을 시뮬레이션하기 위해 CFD를 사용했습니다. 그러나 RPDC에 대한 포괄적인 이해, 특히 스티어링 너클과 같은 복잡한 부품에 대한 검증된 시뮬레이션을 통한 이해는 아직 발전 중입니다.
연구 목적:
본 연구의 주요 목적은 A356 알루미늄 합금으로 자동차 스티어링 너클 부품을 개발하기 위한 레오 압력 다이캐스팅(RPDC) 시스템의 공정 변수를 최적화하는 것입니다. 여기에는 다이 충전 공정을 조사하고 바람직한 미세 구조 및 기계적 특성을 달성하기 위한 이상적인 게이팅 배열, 주입 온도 및 사출 조건을 결정하기 위해 CFD 시뮬레이션을 사용하는 것이 포함됩니다. 또한 이 연구는 시뮬레이션 결과를 실험적으로 검증하는 것을 목표로 합니다.
핵심 연구:
본 연구의 핵심은 스티어링 너클 다이 캐비티에서 A356 반용융 슬러리의 다이 충전을 시뮬레이션하기 위한 CFD 모델을 개발하는 것입니다. 여기에는 A356 합금에 대한 실험적 유변학적 모델을 구축하는 것이 포함됩니다. 본 연구는 주입 온도, 게이팅 설계(게이트 위치 및 수) 및 사출 속도 프로파일이 고상 분율 분포, 혼입 공기, 슬러리 점도, 속도, 온도장 및 압력 분포와 같은 다이 충전 특성에 미치는 영향을 조사합니다. 그런 다음 수치 결과는 자체 개발한 RPDC 설비를 사용한 실험적 시험을 통해 검증되며, 주조된 스티어링 너클의 미세 구조 특성화 및 기계적 특성 시험(경도, 인장 강도)이 이어집니다.
5. 연구 방법론
연구 설계:
본 연구는 두 가지 접근 방식을 사용합니다:
- 전산 유체 역학(CFD) 모델링: 스티어링 너클 부품에 대한 RPDC 시스템에서 반용융 A356 알루미늄 합금 슬러리의 다이 충전 공정을 시뮬레이션하기 위한 수치 모델이 개발되었습니다. 여기에는 질량, 운동량 및 에너지 보존 방정식과 금속-공기 계면 추적을 위한 VOF(volume-of-fluid) 방법 해결이 포함되었습니다. 실험적으로 파생된 유변학적 모델이 통합되었습니다.
- 실험적 검증: 자체 RPDC 설비를 사용하여 물리적 실험을 수행했습니다. CFD 시뮬레이션에서 파생된 최적의 매개변수를 사용하여 스티어링 너클을 주조했습니다. 그런 다음 주조된 부품에 대해 미세 구조 분석 및 기계적 시험을 수행하여 시뮬레이션 예측을 검증하고 부품 품질을 평가했습니다.
데이터 수집 및 분석 방법:
- CFD 시뮬레이션:
- 지배 방정식(연속성, 운동량, 에너지, VOF)은 상용 CFD 소프트웨어 FOLW-3D Cast를 사용하여 해결되었습니다.
- 실험 데이터(Das et al., 2015)에서 파생된 상수를 가진 Ostwald-De Waale 거듭제곱 법칙 기반 유변학적 모델을 사용하여 슬러리 점도를 설명했습니다 (μ = (2.786 E - 05) e^(14430.50 / T) γ⁻¹, Eq. 10).
- 게이팅이 있는 너클 하우징의 3D CAD 모델을 생성하고(Fig. 3a), 도메인을 육면체 격자로 이산화했습니다(Fig. 3b). 격자 독립성을 연구했습니다.
- 경계 조건, 벤트 위치(Fig. 3c), 합금(Table 1, Table 2) 및 다이 재료(Table 3)의 열물리적 특성을 지정했습니다.
- 고상 분율 변화는 실험적 DTA 결과(Fig. 4) 및 Scheil 방정식(Eq. 11)을 기반으로 했습니다.
- 실험 작업:
- A356 알루미늄 합금을 용해, 탈가스 처리하고 냉각 경사로를 통해 처리하여 반용융 슬러리를 생성했습니다.
- 슬러리를 RPDC 기계로 옮기기 전에 등온 유지했습니다(Fig. 17은 슬러리 형태를 보여줌).
- 최적화된 매개변수를 사용하여 스티어링 너클을 주조했습니다.
- 주조 부품의 다양한 위치에서 샘플을 절단하여(Fig. 19) 다음을 수행했습니다:
- 미세 구조 분석: 광학 현미경, FESEM(Fig. 22)을 사용하여 입자 크기, 형태 및 공정 구조를 관찰했습니다. 입자 직경과 구형도를 정량화했습니다(Eqs. 13, 14, Fig. 20).
- 기계적 시험: 매크로 경도 측정(Fig. 21) 및 인장 시험(ASTM E8 지침)을 수행했습니다. 파단면을 분석했습니다(Fig. 23).
- 최대 캐비티 압력을 측정하고 수치 예측과 비교했습니다(Fig. 18).
연구 주제 및 범위:
본 연구는 다음에 중점을 두었습니다:
- RPDC 공정을 사용하여 복잡한 스티어링 너클 다이 캐비티에서 A356 알루미늄 합금 반용융 슬러리의 다이 충전 거동 조사.
- RPDC 공정에 대한 CFD 모델 개발 및 검증.
- 주요 공정 매개변수의 영향 연구:
- 슬러리 주입 온도 (585°C, 600°C, 605°C, 610°C).
- 게이트 위치 및 수 (단일 게이트, 2개 게이트, 인장 시험편 위치가 다른 3개 게이트, Fig. 11 참조).
- 사출 속도 프로파일 (5가지 다른 프로파일, Fig. 13).
- 다이 충전 특성 분석: 고상 분율 분포, 혼입 공기의 부피 분율, 슬러리 점도, 슬러리 속도, 온도 분포 및 캐비티 압력.
- 주조된 스티어링 너클의 미세 구조(초정 Al 입자 크기, 구형도, 공정 Si 형태) 및 기계적 특성(매크로 경도, 인장 강도)과 공정 매개변수 간의 상관 관계 분석.
- CFD 모델에 의해 예측된 최적 공정 조건의 실험적 검증.
6. 주요 결과:
주요 결과:
- 최적 주입 온도: 610°C의 슬러리 주입 온도가 다이 충전 능력 및 부품 주조에 최적인 것으로 밝혀졌으며, 이는 균일한 고상 분율 분포(Fig. 6a)를 보장하고 낮은 온도에 비해 미충전 영역을 최소화했습니다. 수정된 벤트 위치는 이 온도에서 공기 배출을 더욱 개선했습니다(Fig. 7d).
- 최적 게이팅 설계: 3게이트 배열(Fig. 11e에서와 같이)이 부품 내 균일한 응고 속도를 보장하는 데 가장 효과적인 것으로 확인되었으며, 이는 균질한 미세 구조 형태에 중요합니다.
- 최적 사출 속도 프로파일: 사출 프로파일 1(최종 속도 3 m/s, Fig. 13a)은 최적의 슬러리 압력 및 고상 분율 분포(Fig. 14a, Fig. 15a)를 산출하여 부드러운 다이 충전과 우수한 구조적 완전성을 촉진했습니다.
- 유변학 및 유동 거동: 실험적으로 결정된 유변학적 모델은 A356 슬러리의 전단 박화 거동을 효과적으로 포착했습니다. 슬러리 점도는 다이 내 국부 전단 속도 및 온도에 크게 의존하는 것으로 나타났습니다(Fig. 8).
- 실험적 검증:
- 최적화된 매개변수(610°C 슬러리, 3게이트, 사출 프로파일 1)를 사용한 실험에서 스티어링 너클을 성공적으로 생산했습니다.
- 슬러리는 구상 미세 구조의 심각한 열화 없이 약 14분 동안 610°C에서 유지될 수 있었습니다(Fig. 17).
- 최대 캐비티 압력의 수치 예측은 실험값을 과소 예측했지만 경향은 유사했습니다(Fig. 18). 난류 및 가스 흡수로 인한 결함이 증가하는 최적 캐비티 압력이 확인되었습니다.
- 미세 구조: RPDC 주조 너클은 일반적으로 균일한 초정 α-Al 입자 분포(약 55% 면적 분율)를 가진 이중 모드 입자 구조를 나타냈습니다. 초정 입자의 중앙값 크기는 24µm이었고 평균 구형도는 0.88이었습니다(Fig. 20). 중간에 채워진 위치는 최상의 구상 초정 Al 입자를 보였습니다(Fig. 19).
- 기계적 특성:
- 주조 상태 RPDC 부품의 평균 매크로 경도는 약 70 VHN이었으며(Fig. 21), 이는 기존 HPDC 부품에 비해 크게 개선된 것입니다.
- 평균 인장 특성은 항복 강도 170 MPa, 극한 인장 강도 219 MPa, 연신율 9.72%였습니다. 파단면은 혼합 모드 파괴를 보였습니다(Fig. 23).
그림 이름 목록:
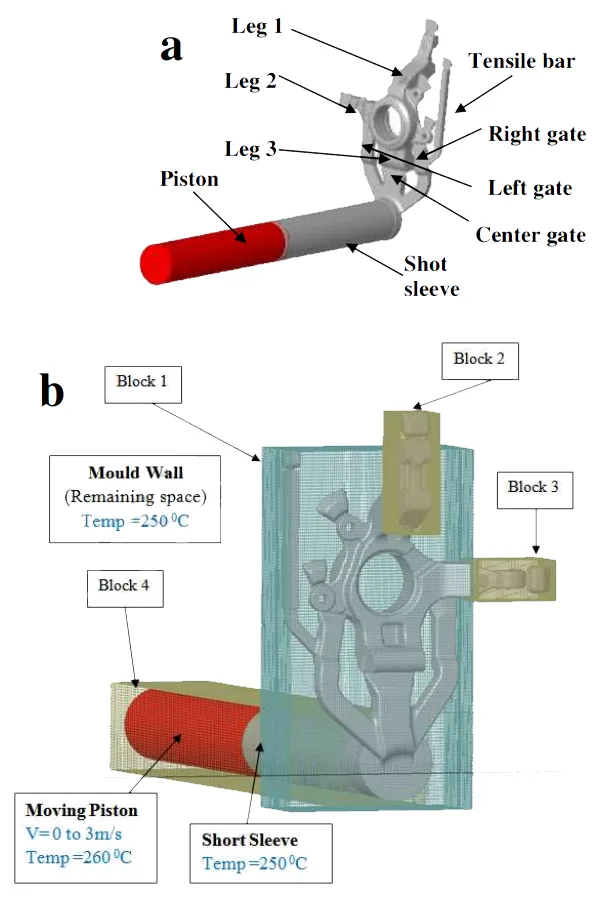
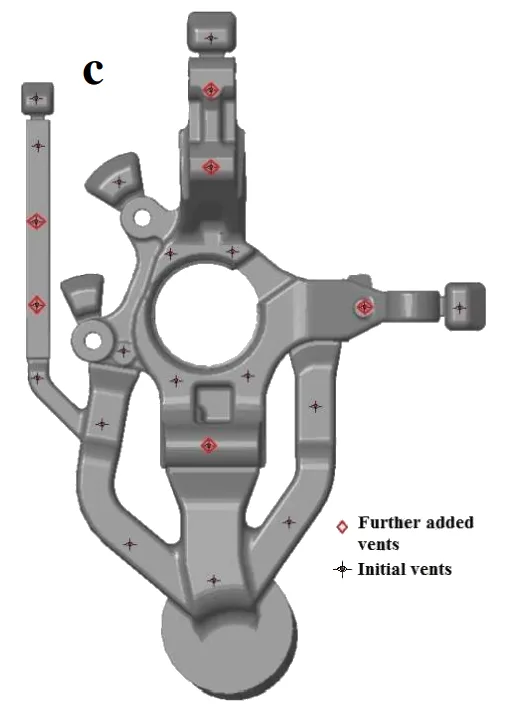
- Fig. 1: Schematic of the Rheo pressure die casting system, showing its functional parts.
- Fig. 2: Slurry viscosity as a function of (a) shear rate, and (b) temperature.
- Fig. 3: (a) Solid model of Knuckle housing with gating arrangement, (b) discretized solution domain, and (c) location of vents considered to perform die filling simulations.
- Fig. 4: (a) Solid fraction vs. temperature curve, and (b) DTA analysis results.
- Fig. 5: Flowchart of the numerical scheme.
- Fig. 6: Solid fraction and temperature distribution within the die cavity after filling completion: (a) Solid fraction and (b) Temperature (Das et al., 2015).
- Fig. 7: Volume fraction of entrained air within the die cavity for different slurry pouring temperatures: (a) 585°C, (b) 600°C, (c) 605°C, and (d) 610°C.
- Fig. 8: Slurry viscosity profiles for different slurry pouring temperatures: (a) 585°C, (b) 600°C, (c) 605°C, and (d) 610°C.
- Fig. 9: Variation of slurry velocity with filling time, for the central gate.
- Fig. 10: Slurry temperature distribution vs. filling time.
- Fig. 11: Slurry temperature distribution for different cavity designs: (a) with central gate, (b) with central and left gate, (c) with central and right gate, (d) three gates with tensile sample position 1, and (e) three gates with tensile sample position 2.
- Fig. 12: Effect of gate no. and locations on (a) solid fraction evolution, (b) viscosity, and (c) velocity of the semi solid slurry.
- Fig. 13: Injection velocity profiles considered for the present study: (a) profile 1, (b) profile 2, (c) profile 3, (d) profile 4, and (e) profile 5.
- Fig. 14: Cavity pressure distribution for different injection velocity profiles: (a) profile 1, (b) profile 2, (c) profile 3, (d) profile 4, and (e) profile 5.
- Fig. 15: Effect of injection velocity profile on solid formation: (a) profile 1, (b) profile 2, (c) profile 3, (d) profile 4, and (e) profile 5.
- Fig. 16: Temporal variation of slurry velocity during filling of the die cavity for different injection velocity profile: (a) profile 1, (b) profile 2, (c) profile 3, (d) profile 4, and (e) profile 5.
- Fig. 17: Representative optical micrographs of oil quenched samples showing slurry morphology, at different slurry formation stages.
- Fig. 18: Comparative plot of numerical and experimental findings of maximum cavity pressure and radiographs of Leg 1 (Fig. 2) of the solidified Knuckle housing for all five injection conditions.
- Fig. 19: Digital photograph of the Rheo pressure die cast prototype Knuckle housing, and optical micrographs of different locations of the solidified component.
- Fig. 20: Distribution of (a) primary Al particle size and their (b) sphericity for the samples taken from different sections of the solidified knuckle housing.
- Fig. 21: Distribution of macro hardness for the samples taken from different sections of the solidified knuckle housing.
- Fig. 22: Representative FESEM micrographs: (a) distribution of globular primary solid grains and eutectic Si particles, (b) high magnification image of eutectic morphology.
- Fig. 23: Representative SEM factographs: (a) at 1000X magnification, and (b) at 1500X magnification.
7. 결론:
본 연구에서는 레오 압력 다이캐스팅 경로를 따라 너클 하우징을 개발하기 위한 다이 형상 및 공정 변수의 최적화가 제시되었습니다. 본 연구에서 도출된 결론은 다음과 같습니다.
- 시뮬레이션 결과에 따르면, 0.15의 고상 분율에 해당하는 610°C의 슬러리 주입 온도, 3.0 m/s의 사출 팁 속도 및 250°C의 예열 온도를 가진 3게이트 다이 캐비티가 건전한 구조적 완전성을 가진 3족 너클 하우징을 성공적으로 개발하는 데 최적인 것으로 밝혀졌습니다.
- 초정 Al 입자의 미세 구조 형태는 RPDC 주조 부품 전체에 걸쳐 등방성이며, 약 70 VHN의 평균 매크로 경도를 가집니다. 이는 기존 고압 다이캐스트(HPDC) 부품에 비해 현저히 개선된 것으로 밝혀졌습니다.
- 냉각 경사로 생성 슬러리는 부품 개발에 활용하기 전에 미세 구조 형태의 큰 저하 없이 등온 슬러리 유지조 내에서 약 14분 동안 유지될 수 있는 것으로 관찰되었습니다.
- 응고된 부품의 수치 결과 및 대표 방사선 사진에서, 최대 캐비티 압력의 특정 값까지 RPDC 주조 부품의 구조적 완전성이 증가하고, 그 이상의 압력은 다이 충전 중 가능한 난류 및 후속 가스 흡수로 인해 주조 부품 내 결함 형성을 초래한다는 것이 분명합니다.
- 충전된 부품 캐비티의 응고 단계에 대한 시뮬레이션 연구와 주조 및 열처리 상태에서 RPDC 주조 부품의 미세 구조 및 인장 특성에 대한 상세한 조사가 현재 진행 중이며, 그 결과는 향후 간행물에 보고될 것입니다.
8. 참고문헌:
- Blanco, A., Azpilgain, Z., Lozares, J., Kapranos, P., Hurtado, I., 2010. Rheological characterization of A201 aluminum alloy. Trans. Nonferrous Met. Soc. China, 20, 1638-1642.
- Brabazon, D., Browne, D.J., Carr, A.J., 2003. Experimental investigation of the transient and steady state rheological behaviour of Al–Si alloys in the mushy state. Materials Science and Engineering A, 356, 69-80.
- Campbell, J., 2003. Castings. Butterworth-Heinemann: Oxford, UK; Chapter 9.
- Campo, K. N., Proni, C. T. W., Zoqui, E. J., 2013. Influence of the processing route on the microstructure of aluminum alloy A356 for thixoforming. Materials Characterization, 85, 26-37.
- Choi, B. H., Jang, Y. S., Sim, J. G., Kim, H. S., Hong, C. P., 2013. Application of Rheo-diecasting of a High Strength Al-Si-Mg Alloy to Automotive Suspension Arms. ISIJ International, 53, 502-510.
- Das, P., Dutta, P., 2016. Phase field modelling of microstructure evolution and ripening driven grain growth during Cooling Slope processing of A356 Al alloy. Computational Materials Science, 125, 8–19.
- Das, P., Samanta, S.K., Chattopadhyay, H., Dutta, P., 2012. Effect of pouring temperature on cooling slope casting of semi-solid Al-Si-Mg alloy. Acta Metallurgica Sinica (English Letters), 25, 329-339.
- Das, P., Samanta, S.K., Chattopadhyay, H., Sharma, B.B., Dutta, P., 2013. Eulerian two-phase flow simulation and experimental validation of semisolid slurry generation process using cooling slope. Material Science and Technology, 29, 83-92.
- Das, P., Samanta, S.K., Das, R., Dutta, P., 2014. Optimization of degree of sphericity of primary phase during cooling slope casting of A356 Al alloy: Taguchi method and regression analysis. Measurement, 55, 605–615.
- Das, P., Samanta, S.K., Dutta, P., 2015. Rheological Behavior of Al-7Si-0.3Mg Alloy at Mushy State, Metall. Mater. Trans. B. 46, 1302-1313.
- Das, P., Samanta, S.K., Tiwari, S., Dutta, P., 2015. Die Filling Behaviour of Semi Solid A356 Al Alloy Slurry During Rheo Pressure Die Casting, Trans Indian Inst Met. 68, 1215–1220.
- Das, P., Samanta, S.K., Mondal, B., Dutta, P., 2018. Multiphase Model of Semisolid Slurry Generation and Isothermal Holding During Cooling Slope Rheoprocessing of A356 Al Alloy. Metallurgical and Materials Transactions B, 49, 1925-1944.
- Gourlay, C. M., Laukli, H. I., Dahle, A. K., 2004. Segregation Band Formation in Al-Si Die Castings, Metall. Mater. Trans. A. 35, 2881-2891.
- Gourlay, C. M., Laukli, H. I., Dahle, A. K., 2007. Defect Band Characteristics in Mg-Al and Al-Si High-Pressure Die Castings, Metall. Mater. Trans. A. 38, 1833-1844.
- Guanglei, Z., Jun, X., Zhifeng, Z., Guojun, L., 2010. Numerical simulation of die filling behavior of AZ91D in the semisolid process, China Foundry. 7(2), 127-131.
- Guan-hai, Y., Sheng-dun, Z., Zheng-hui S., 2010. Simulation of semisolid diecasting process of four-way valve of HPb59-1 alloy for air-conditioner, Nonferrous Met. Soc. China. 20, s931-s936.
- Hirt, C. W., 2012. Modeling Turbulent Entrainment of Air at a Free Surface, Flow Science Report, 01-12.
- Hirt, C. W., 2013. Void Regions and Bubble Models in FLOW-3D, Flow Science Report, 01-13.
- Hitchcock, M., Wang, Y., Fan, Z., 2007. Secondary solidification behaviour of the Al–Si-Mg alloy prepared by the rheo-diecasting process. Acta Materialia, 55, 1589–1598.
- Hongmin, G., Xiangjie, Y., Bin, H., Guanglei, Z., 2007. Rheo-diecasting Process for Semi-solid Aluminum Alloys, Journal of Wuhan University of Technology-Mater. Sci. Ed. 22(4), 590-595.
- Kang, C. G., Lee, S. M., 2008. Effect of Solid Fraction and Pressure on Microstructure and Mechanical Properties and Reduction in Liquid Segregation in the Thixo-Die-Casting Process with Al-7 Pct Si Alloy, Metallurgical and Materials Transactions A, 39, 1213-1224.
- Kang, C. G., Lee, S. M., Kim, B. M., 2008. A study of die design of semi-solid die casting according to gate shape and solid fraction, Journal of Materials Processing Technology. 204, 8-21.
- Kang, C.G., Seo, P.K., 2003. The effect of gate shape on the filling limitation in the semi-solid forging process and the mechanical properties of the products, Journal of Materials Processing Technology. 135, 144–157.
- Kang, C.G., Seo, P.K., Kang, S. S., 2006. The effect of injection velocity on liquid segregation and mechanical properties in arm part fabricated by semi-solid die casting process, Journal of Materials Processing Technology. 176, 32-40.
- Kapranos, P., Haga, T., Bertoli, E., Pola, A., Azpilgain, Z., Hurtado, I., 2008. Thixo-extrusion of 5182 aluminium alloy. Solid State Phenom. 141–143, 115–120.
- Kleiner, S., Ogris, E., Beffort, O., Uggowitzer, P. J., 2003. Semi Solid Metal Processing of Aluminum Alloy A356 and Magnesium Alloy AZ91: Comparison Based on Metallurgical Considerations. 5, 653–658.
- Lakshmi, H., Kumar, M.C.V., Raghunath, Kumar, P., Ramanarayanan, V., Murthy, K. S. S., Dutta, P., 2010. Induction Reheating of Aluminum Alloy A356 and Thixocasting of an Automobile Component, Transaction of Nonferrous Metals Society of China. 20, S961-S967.
- Laukli, H.I., Gourlay, C.M., Dahle, A.K., 2005. Migration of Crystals during the Filling of Semi-Solid Castings, Metall. Mater. Trans. A, 36, 805-818.
- Liu, Z. Y., Mao, W. M., Wang, W. P., Zheng, Z. K., Yue, R., 2017. Investigation of rheo-diecasting mold filling of semi-solid A380 aluminum alloy slurry, International Journal of Minerals, Metallurgy and Materials, 24, 691-700.
- Pola, A., Tocci, M., Kapranos, P., 2018. Microstructure and Properties of Semi-Solid Aluminum Alloys: A Literature Review, Metals, 8, 181, doi:10.3390/met8030181.
- Ri, K., Mao, W. M., Zheng, Z. K, Kim, M., Sin, Y., 2016. Effect of rheo-diecast process on the mechanical properties of A390 alloy by serpentine channel, International Journal of Minerals, Metallurgy and Materials, 23, 1177-1186.
- Otarawanna, S., Gourlay, C. M., Laukli, H. I., Dahle, A. K., 2009. Microstructure Formation in AlSi4MgMn and AlMg5Si2Mn High-Pressure Die Castings, Metall. Mater. Trans. A, 40, 1645-1659.
- Otarawanna, S., Gourlay, C. M., Laukli, H. I., Dahle, A. K., 2009. The thickness of defect bands in high-pressure die castings, Materials Characterisation, 60, 1432-1441.
- Pirovano, R., Mascetti, S., 2016. Tracking of collapsed bubbles during a filling simulation Die-casting. Metall. Ital., 6, 37–40.
- Qi, M., Kang, Y., Zhou, B., Liao, W., Zhu, G., Li, Y., Li, W., 2016. A forced convection stirring process for Rheo-HPDC aluminum and magnesium alloys, Journal of Materials Processing Technology, 234, 353-367.
- Qi, M., Kang, Y., Qiu, Q., Tang, W., Li, J., Li, B., 2018. Microstructures, mechanical properties, and corrosion behavior of novel high-thermal-conductivity hypoeutectic Al-Si alloys prepared by rheological high pressure die-casting and high pressure die-casting, Journal of Alloys and Compounds, 749, 487-502.
- Reikher, A., Pillai, K.M., 2013. A fast simulation of transient metal flow and solidification in a narrow channel. Part I: Model development using lubrication approximation, International Journal of Heat and Mass Transfer. 60, 797-805.
- Reikher, A., Pillai, K.M., 2013. A fast simulation of transient metal flow and solidification in a narrow channel. Part II. Model validation and parametric study, International Journal of Heat and Mass Transfer. 60, 806-815.
- Rosso, M., 2012. Thixocasting and rheocasting technologies, improvements going on, Journal of Achievements in Materials and Manufacturing Engineering. 54(1), 110-119.
- Sabau, A. S., Porter, W. D., Frankel, J. I., 2004. Conduction and Radiation parameters for analytical models of Differential Scanning Calorimetry instruments, TMS (The Minerals, Metals & Materials Society), 1-10.
- Seo, P.K., Kim, D.U., Kang, C.G., 2006. Effects of die shape and injection conditions proposed with numerical integration design on liquid segregation and mechanical properties in semi-solid die casting process, Journal of Materials Processing Technology. 176, 45-54.
- Seo, P.K., Kim, D.U., Kang, C.G., 2007. The effect of the gate shape on the microstructural characteristic of the grain size of Al–Si alloy in the semi-solid die casting process, Materials Science and Engineering A, 20–30, 445–446.
- Seo, P.K., Kim, H.C., Kang, C.G., 2007. Numerical integration design process to development of suspension parts by semi-solid die casting process, Journal of Materials Processing Technology, 183, 18-32.
- Sigworth, G.K., 1996. Rheological Properties of Metal Alloys in the Semi-Solid State, Can. Metall. Q., 35, 101–22.
- Taghavi, F., Ghassemi, A. 2009. Study on the effects of the length and angle of inclined plate on the thixotropic microstructure of A356 aluminum alloy, Mater. Des., 30, 1762–1767.
- Wei-min, M., Qiu, Z., Da-ping, Z., 2010. Rheo-squeeze casting of semi-solid A356 aluminum alloy slurry, Trans. Nonferrous Met. Soc. China, 20, 1769-1773.
- Xu, C., Zhao, J., Guo, A., Li, H., Dai, G., Zhang, X., 2017. Effects of injection velocity on microstructure, porosity and mechanical properties of a rheo-diecast Al-Zn-Mg-Cu aluminum alloy, Journal of Materials Processing Tech., 249, 167–171.
- Yue-long, B., Wei-min, M., Jun, X., Hong, X., Hua, H., 2008. Numerical simulation on rheo-diecasting mould filling of semi-solid key-shaped component, Nonferrous Met. Soc. China, 18, 682-685.
- Zhang, F., Song, N., Zhang, J., Kang, Y., Zhu, Q., 2013. Numerical simulation on the filling process of rheological die casting and forming defects analysis, Solid State Phenomena, 192-193, 293-298.
- Zhang, F., Hu, X. G., Li, D. Q., He, Y. F., Xu, X. J., Zhu, Q., 2015. Simulation on the Thixocasting Process of the Turbocharger Impellers and Selection of the Viscosity Models, Solid State Phenomena, 217-218, 219-224.
- Zheng, Z. K., Ji, Y. J., Mao, W. M., Yue, R., Liu, Z.Y., 2017. Influence of rheo-diecasting processing parameters on microstructure and mechanical properties of hypereutectic Al-30%Si alloy, Trans. Nonferrous Met. Soc. China, 27, 1264–1272.
9. 저작권:
- 이 자료는 "Prosenjit Das, Bikash Bhuniya, Sudip K. Samanta, Pradip Dutta"의 논문입니다. "Studies on Die Filling of A356 Al alloy and Development of a Steering Knuckle Component using Rheo Pressure Die Casting System"을 기반으로 합니다.
- 논문 출처: https://doi.org/10.1016/j.jmatprotec.2019.04.014
이 자료는 위 논문을 바탕으로 요약되었으며, 상업적 목적의 무단 사용을 금합니다.
Copyright © 2025 CASTMAN. All rights reserved.
요약:
본 논문은 A356 알루미늄 합금 스티어링 너클 제조를 위한 레오 압력 다이캐스팅(RPDC) 공정 최적화에 대한 포괄적인 연구를 제시합니다. 전산 유체 역학(CFD) 시뮬레이션과 실험적 검증을 통해 슬러리 주입 온도(610°C), 사출 속도(3.0 m/s) 및 다이 게이팅(3게이트 시스템)에 대한 최적의 매개변수가 결정되었습니다. 본 연구는 이러한 최적화된 조건이 기존 다이캐스팅 방법에 비해 향상된 미세 구조 균질성(중앙값 입자 크기 24µm, 구형도 0.88)과 향상된 기계적 특성(평균 매크로 경도 ~70 VHN, UTS 219 MPa)을 가진 건전한 주물을 생산함을 보여주며, 고강도 경량 자동차 부품 생산을 위한 RPDC의 잠재력을 강조합니다.
연구에 대한 주요 질문과 답변:
본 연구는 전산 유체 역학(CFD) 모델을 개발하고 검증하여 A356 알루미늄 합금 스티어링 너클 생산을 위한 레오 압력 다이캐스팅(RPDC) 공정 매개변수를 최적화하는 것을 목표로 했습니다. 본 연구는 610°C의 슬러리 주입 온도, 3.0 m/s의 사출 속도 및 3게이트 다이 설계를 포함한 최적의 조건을 성공적으로 식별했으며, 이는 실험적으로 검증되었습니다. 그 결과 부품은 기존 다이캐스팅 방법에 비해 평균 매크로 경도 70 VHN과 같은 향상된 미세 구조 균질성 및 기계적 특성을 나타냈습니다.
Q1. A356 알루미늄 합금 스티어링 너클에 대한 RPDC 공정과 관련하여 이 연구의 주요 목적은 무엇이었습니까?
A1. 주요 목적은 CFD 모델과 실험적 검증을 사용하여 스티어링 너클 부품에서 바람직한 미세 구조와 기계적 특성을 달성하기 위한 최적의 게이팅 배열, 주입 온도 및 사출 조건을 결정하는 것이었습니다. (출처: 초록; Studies on Die Filling of A356 Al alloy and Development of a Steering Knuckle Component using Rheo Pressure Die Casting System)
Q2. RPDC 시스템에 대해 시뮬레이션으로 확인된 주요 최적 공정 매개변수는 무엇이었습니까?
A2. 시뮬레이션 결과에 따르면 0.15의 고상 분율에 해당하는 610°C의 슬러리 주입 온도, 3.0 m/s의 사출 팁 속도 및 250°C의 예열 온도를 가진 3게이트 다이 캐비티가 건전한 스티어링 너클을 생산하는 데 최적인 것으로 나타났습니다. (출처: Section 6. Conclusions; Studies on Die Filling of A356 Al alloy and Development of a Steering Knuckle Component using Rheo Pressure Die Casting System)
Q3. RPDC 주조 스티어링 너클의 기계적 특성은 기존 방법과 어떻게 비교되었습니까?
A3. RPDC 주조 부품은 약 70 VHN의 평균 매크로 경도를 보였으며, 이는 기존 고압 다이캐스트(HPDC) 부품에 비해 현저히 개선된 것입니다. 인장 특성 또한 RDC A356 알루미늄 합금 샘플에 대해 보고된 것과 유사했습니다. (출처: Section 5.2 Mechanical properties, Section 6. Conclusions; Studies on Die Filling of A356 Al alloy and Development of a Steering Knuckle Component using Rheo Pressure Die Casting System)
Q4. 이 연구에서 개발된 유변학적 모델의 중요성은 무엇이었습니까?
A4. Ostwald-De Waale 거듭제곱 법칙에 기반한 실험적으로 결정된 유변학적 모델은 A356 반용융 슬러리의 전단 박화 거동을 정확하게 설명하기 위해 개발되었으며, 이는 다이 충전 공정의 CFD 시뮬레이션 예측 능력에 매우 중요합니다. (출처: Section 2.2 Rheology model; Studies on Die Filling of A356 Al alloy and Development of a Steering Knuckle Component using Rheo Pressure Die Casting System)
Q5. 주입 온도가 다이 충전 능력과 최종 부품 품질에 미치는 영향은 무엇이었습니까?
A5. 610°C의 주입 온도가 완전한 다이 충전 및 균일한 고체 함량 분포에 적합한 것으로 밝혀졌으며, 반면 낮은 온도(예: 585°C)는 불완전한 충전 및 불균일한 고상 분율을 초래하여 부품 개발에 부적합했습니다. (출처: Section 4.1.1 Solid fraction distribution; Studies on Die Filling of A356 Al alloy and Development of a Steering Knuckle Component using Rheo Pressure Die Casting System)
Q6. 냉각 경사로 생성 슬러리는 심각한 열화 없이 주조 전에 얼마나 오래 유지될 수 있었습니까?
A6. 냉각 경사로 생성 슬러리는 부품 주조 전에 미세 구조 형태의 큰 저하 없이 등온 슬러리 유지조 내에서 약 14분 동안 유지될 수 있는 것으로 관찰되었습니다. (출처: Section 5. Experimental validation, Section 6. Conclusions; Studies on Die Filling of A356 Al alloy and Development of a Steering Knuckle Component using Rheo Pressure Die Casting System)