본 기사에서는 [RWTH Aachen University]에서 발행한 논문 ['A cost-efficient process route for the mass production of thin-walled structural aluminum body castings']을 소개합니다.
1. 개요:
- 제목: A cost-efficient process route for the mass production of thin-walled structural aluminum body castings
- 저자: Mohamed Youssef Ahmed Youssef
- 출판 연도: 2021년
- 출판 학술지/학회: Ergebnisse aus Forschung und Entwicklung, Band 28 (2021) Gießerei-Institut der RWTH Aachen
- 키워드: High pressure die casting (HPDC), RheoMetalTM process, Thin-walled structural aluminum body castings, Cost calculation study, Mechanical properties, Rivetability, Crash resistance
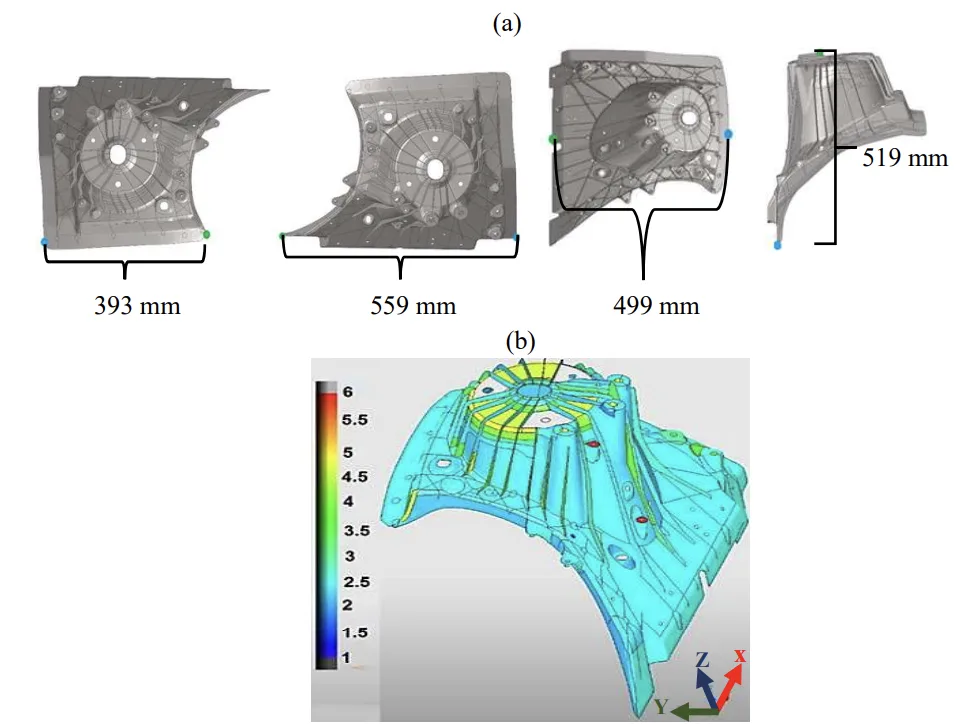
2. 초록 또는 서론
자동차 부문의 연비 향상 및 CO2 배출량 감소 요구에 부응하여, 본 논문에서는 더 무거운 강철 부품을 대체하는 얇은 벽 구조용 알루미늄 차체 주물의 대량 생산을 위한 비용 효율적인 공정 경로를 연구합니다. 연구는 고압 다이캐스팅(HPDC) 및 RheoMetalTM 공정에서 주요 비용 동인을 식별하기 위한 비용 계산 연구로 시작하며, 기계 유형, 합금 선택, 열처리, 진공 적용 및 다이 수명과 같은 요인에 중점을 둡니다.
이 연구는 열처리 없이 구조용 주물에 적합한 Al-Si, Al-Mg-Si 및 Al-Mg-Fe 계열을 포함한 다양한 알루미늄 합금을 평가합니다. 실험적 접근 방식에는 HPDC 및 RheoMetalTM을 사용하여 테스트 플레이트 및 부품을 생산하고, 인장 테스트, 굽힘 테스트, 밀도 측정 및 충돌 저항 및 접합 무결성을 평가하기 위한 자체 피어싱 리벳팅(SPR) 분석과 같은 기계적 테스트를 수행하는 것이 포함됩니다.
본 논문은 얇은 벽 구조용 알루미늄 차체 주물의 대량 생산을 위한 비용 효율적인 제조 방법을 결정하기 위해 HPDC와 RheoMetalTM 공정을 비교합니다.
3. 연구 배경:
연구 주제의 배경:
자동차 산업은 CO2 배출량 감소와 연비 향상에 대한 필요성에 의해 주도되고 있으며, 이는 차량 중량 감소에 초점을 맞춘 접근 방식으로 이어지고 있습니다. 강판을 더 가벼운 알루미늄 주물로 대체하는 것은 기능 통합 및 중량 절감을 제공하는 핵심 전략입니다. 그러나 얇은 벽 구조용 알루미늄 차체 주물의 대량 생산은 재료 비용으로 인해 경제성이 떨어집니다. 본 연구는 자동차 구조에 알루미늄 주물의 광범위한 채택을 용이하게 하기 위한 비용 효율적인 공정 경로의 필요성을 다룹니다.
기존 연구 현황:
자동차 OEM은 표준 Al-Si 주조 합금을 사용하여 구조용 차체 부품에 알루미늄 주물을 통합했습니다. 고압 다이캐스팅, 중력 다이캐스팅, 저압 다이캐스팅 및 그린 샌드 캐스팅과 같은 주조 방법이 널리 사용됩니다. 고압 다이캐스팅은 짧은 사이클 시간으로 인해 대량 생산에 특히 매력적입니다. 틱소캐스팅 및 레오캐스팅을 포함한 반용융 주조 방법은 가스 기공 감소 및 기계적 특성 향상과 같은 장점을 제공합니다. 레오캐스팅 유형인 RheoMetalTM 공정은 슬러리 생성을 위해 엔탈피 교환을 활용하며, 이는 온도 제어 방식과 다릅니다.
연구의 필요성:
특히 Al-Si 합금을 사용하는 구조용 알루미늄 주물을 생산하는 기존 방법은 기계적 특성 요구 사항(Rp0.2 > 120 MPa, Rm > 180 MPa, 연신율 > 10%)을 충족하기 위해 종종 고가의 열처리가 필요합니다. 열처리 비용을 줄이거나 제거하면서 구조적 무결성 및 충돌 저항을 유지하기 위해 비열처리 합금 및 RheoMetalTM과 같은 고급 주조 공정과 같은 비용 효율적인 대안을 모색해야 할 필요성이 있습니다. 본 연구는 박벽 구조용 알루미늄 차체 주물의 비용 효율적인 대량 생산에 적합한 합금 및 공정을 식별하는 것을 목표로 합니다.
4. 연구 목적 및 연구 질문:
연구 목적:
주요 연구 목적은 박벽 구조용 알루미늄 차체 주물의 대량 생산(1,000,000 - 2,000,000개 부품)을 위한 비용 효율적인 공정 경로를 개발하는 것입니다. 여기에는 자동차 응용 분야에 대한 엄격한 기계적 및 구조적 요구 사항을 충족하면서 생산 비용을 최소화하기 위해 합금 선택 및 주조 공정을 조사하고 최적화하는 것이 포함됩니다.
핵심 연구:
- HPDC 및 RheoMetalTM 공정을 사용하여 박벽 구조용 알루미늄 차체 주물 생산의 주요 비용 동인을 식별합니다.
- 기계적 특성, 충돌 저항 및 리벳팅 가능성 측면에서 구조용 자동차 주물에 적합한 다양한 알루미늄 합금, 특히 비열처리 합금의 적합성을 평가합니다.
- 주조 품질을 향상시키고 생산 비용을 절감하기 위해 HPDC 및 RheoMetalTM 주조 공정의 공정 매개변수를 최적화합니다.
- 박벽 구조용 알루미늄 차체 주물의 대량 생산을 위한 HPDC 및 RheoMetalTM 공정의 비용 효율성 및 성능을 비교합니다.
연구 가설:
- Al-Mg-Si 및 Al-Mg-Fe 계열과 같이 열처리가 필요하지 않은 합금을 활용하면 T7 열처리가 필요한 기존 Al-Si 합금에 비해 비용 효율적인 생산 경로로 이어질 수 있습니다.
- RheoMetalTM 주조 공정은 다이 수명 연장 및 재료 사용량 감소 가능성으로 인해 박벽 구조용 알루미늄 차체 주물의 대량 생산에 HPDC보다 비용 효율적인 대안을 제공할 수 있습니다.
- MYFORD 합금은 수정된 조성과 향상된 레오캐스팅 가능성으로 인해 RheoMetalTM 주조에서 우수한 성능을 입증하고 HPDC에서 표준 합금과 비교하여 동등하거나 더 나은 기계적 특성 및 충돌 저항을 달성할 것입니다.
5. 연구 방법론
연구 설계:
본 연구는 두 가지 주요 주조 공정(HPDC 및 RheoMetalTM)과 다양한 알루미늄 합금 및 열처리 조합을 평가하는 비교 실험 설계를 채택합니다. 비용 계산 연구는 다양한 공정 경로의 경제적 타당성을 평가하기 위해 통합됩니다.
데이터 수집 방법:
- 비용 계산 연구: Bühler AG에서 제공한 상세한 비용 계산 도구를 사용하여 HPDC 및 RheoMetalTM 공정의 다양한 요인의 비용 영향을 분석했습니다.
- 기계적 테스트: 인장 테스트(단축 및 3점 굽힘), 밀도 측정(아르키메데스 원리) 및 자체 피어싱 리벳팅(SPR) 테스트를 수행하여 재료 특성, 충돌 저항 및 접합 성능을 평가했습니다.
- 미세 구조 분석: SEM-EDS 및 광학 현미경을 사용하여 미세 구조를 특성화하고 주물의 결함을 식별했습니다.
- 분광 화학 분석: 광학 방출 분광법을 사용하여 합금의 화학 조성을 확인했습니다.
분석 방법:
- 통계 분석: Minitab 및 Microsoft Excel을 사용하여 다양한 합금 및 공정을 비교하기 위해 ANOVA 및 그래픽 표현(상자 그림, 차트)을 포함한 기계적 테스트 데이터의 통계 분석을 수행했습니다.
- 비용 분석: 비용 계산 도구를 사용하여 합금, 공정, 다이 수명 및 열처리와 같은 요인을 고려하여 다양한 시나리오의 비용 효율성을 비교했습니다.
- 미세 구조 평가: 미세 구조 이미지의 질적 및 양적 분석을 통해 결정립 크기, 상 분포 및 결함 존재를 평가했습니다.
연구 대상 및 범위:
- 재료: AlSi10MnMg, AlSi9MnMoZr, AlMg4Fe2, MYFORD, AlSi7Mg0.3, EN AB-42000, AlMg5Si2Mn, AlMg6Si2MnZr를 포함한 Al-Si, Al-Mg-Si 및 Al-Mg-Fe 계열의 알루미늄 합금. SPR 테스트에는 DP600 강판을 사용했습니다.
- 주조 공정: 고압 다이캐스팅(HPDC) 및 RheoMetalTM 공정.
- 시험편: 시험판(두께 3.1mm 및 2.5mm)과 복잡한 형상 부품(쇼크 타워 시뮬레이션)을 다른 공급업체(RWTH Aachen University의 Foundry Institute(GI), Magna BDW technologies Soest GmbH, Comptech AB)에서 생산했습니다.
- 테스트 범위: 다양한 합금 및 열처리 공정으로 HPDC 및 RheoMetalTM 공정으로 생산된 주물의 기계적 특성, 충돌 저항 잠재력 및 리벳팅 가능성 평가.
6. 주요 연구 결과:
주요 연구 결과:
- 비용 계산 연구: 열처리 및 다이 수명이 HPDC의 주요 비용 동인으로 확인되었습니다. RheoMetalTM 공정은 다이 수명 연장으로 인해 비용 절감 가능성을 보여주었습니다. AlSi9MnMoZr 및 MYFORD와 같은 비열처리 합금은 열처리를 제거하여 비용 효율적인 대안으로 밝혀졌습니다.
- 기계적 특성: MYFORD 및 AlSi10MnMg-T7 합금은 2020 Ford Explorer 쇼크 타워의 요구 사항을 충족하거나 초과하는 우수한 기계적 특성을 입증했습니다. RheoMetalTM 공정 부품은 HPDC 부품에 비해 약간 낮은 충돌 저항 잠재력을 보였습니다.
- 충돌 저항: AlMg4Fe2 및 MYFORD 합금은 HPDC 및 RheoMetalTM 공정 모두에서 가장 높은 충돌 저항 잠재력을 보였습니다.
- 리벳팅 가능성: AlMg4Fe2 및 MYFORD 합금이 다른 합금보다 리벳팅 가능성이 더 높았습니다. AlSi10MnMg-T7도 우수한 리벳팅 가능성을 보였습니다. RheoMetalTM 공정 부품은 HPDC 부품과 비슷한 리벳팅 가능성을 보였습니다.
- 미세 구조 분석: HPDC 주물은 수지상 미세 구조를 보였고 RheoMetalTM 주물은 구상 미세 구조를 나타냈습니다. 수축 기공은 일부 합금, 특히 HPDC의 AlMg5Si2Mn 및 AlMg6Si2MnZr에서 관찰되었습니다. RheoMetalTM 공정의 MYFORD 합금은 결함이 최소화된 미세한 구상 미세 구조를 보였습니다.
제시된 데이터 분석:
- 그림 5.1: HPDC에서 AlMg4Fe2 합금의 총 연신율에 대한 용융 흐름 속도의 영향을 보여주며, 속도가 증가함에 따라 연신율이 약간 증가함을 보여줍니다.
- 그림 5.7 및 5.8: Al-Si 합금의 HPDC에서 힘-변위 및 에너지-변위 차트를 보여주며, AlSi10MnMg-T7 및 AlMg4Fe2 합금이 더 높은 충돌 저항을 갖는다는 것을 나타냅니다.
- 그림 5.9 및 5.10: Al-Si 합금에 대한 시뮬레이션된 힘-변위 및 에너지-변위 차트를 제시하여 실험적 경향을 검증합니다.
- 그림 5.11 및 5.12: 모든 HPDC 합금에 대한 힘-변위 및 에너지-변위 차트를 보여주며, AlMg4Fe2 및 AlSi10MnMg-T7이 충돌 저항에서 최고 성능을 나타냄을 강조합니다.
- 그림 5.15: SPR 접합부에 대한 HPDC 합금 및 합금-열처리 조합에 대한 힘-변위 차트를 제시하여 성능 변화를 보여줍니다.
- 그림 6.4 및 6.5: RheoMetalTM 합금에 대한 힘-변위 및 에너지-변위 차트를 보여주며, AlMg4Fe2 합금이 더 높은 충돌 저항을 갖는다는 것을 나타냅니다.
- 그림 6.6 및 6.7: RheoMetalTM 합금을 비교하는 힘-변위 및 에너지-변위 차트를 제시하여 MYFORD 및 AlMg4Fe2가 충돌 저항에서 최고 성능을 나타냄을 강조합니다.
- 그림 6.8: SPR 접합부에 대한 RheoMetalTM 공정에서 AlMg4Fe2 합금에 대한 힘-변위 차트를 보여주며, 접합 성능을 입증합니다.
그림 목록:
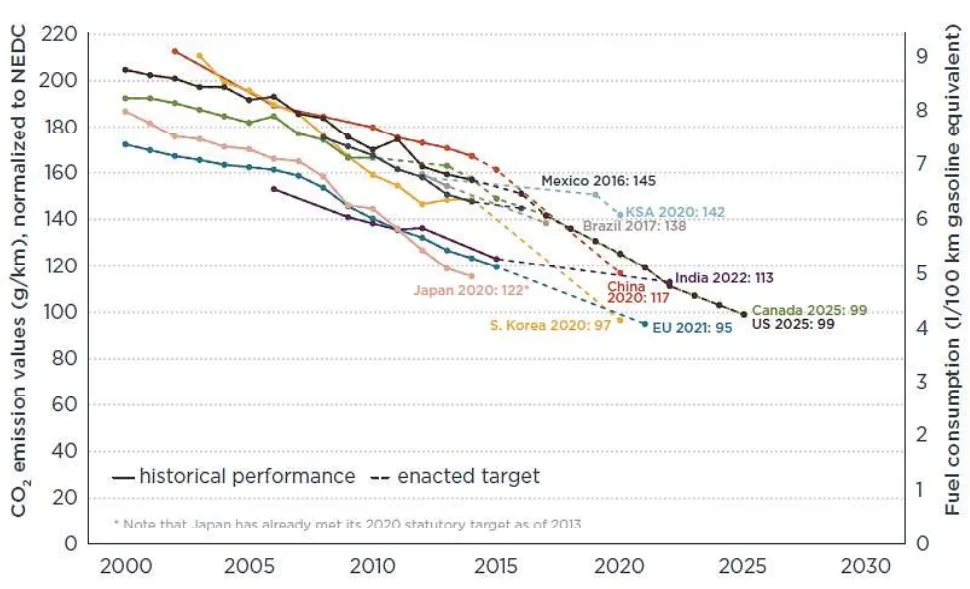
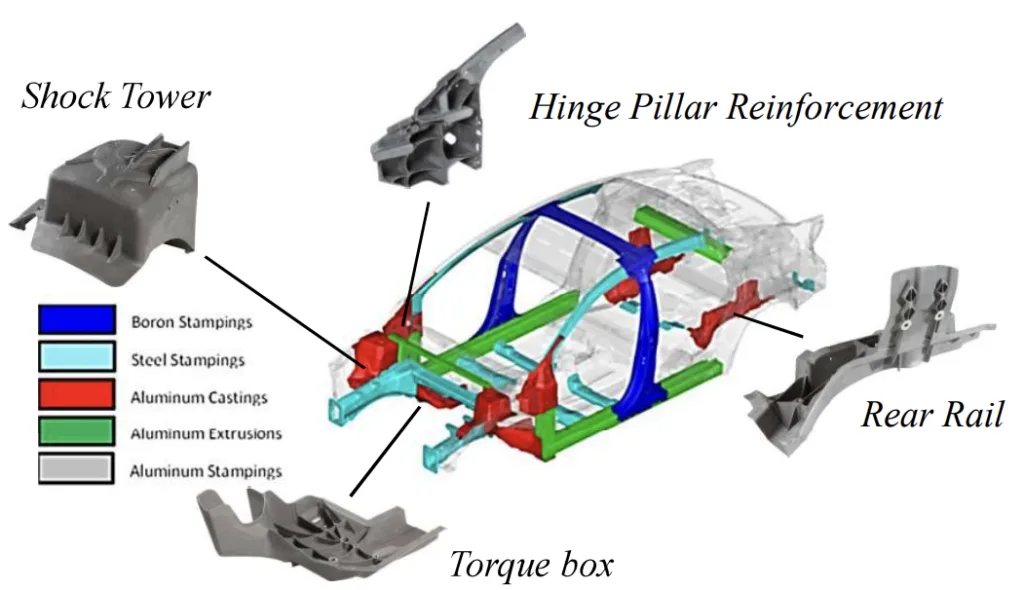
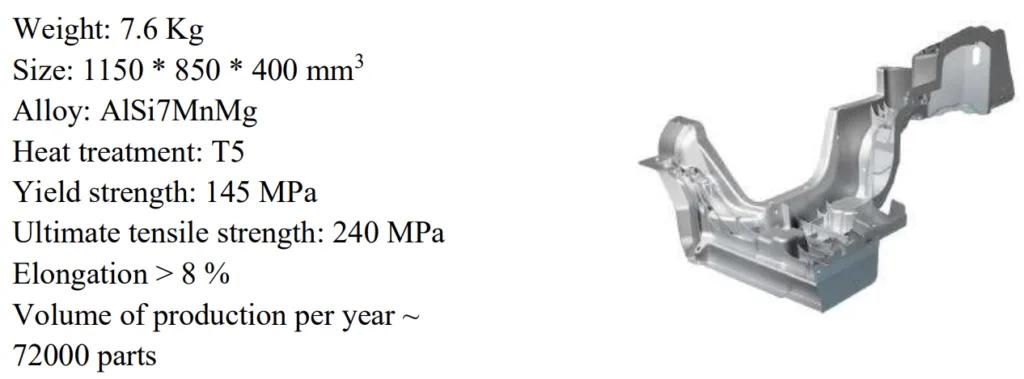
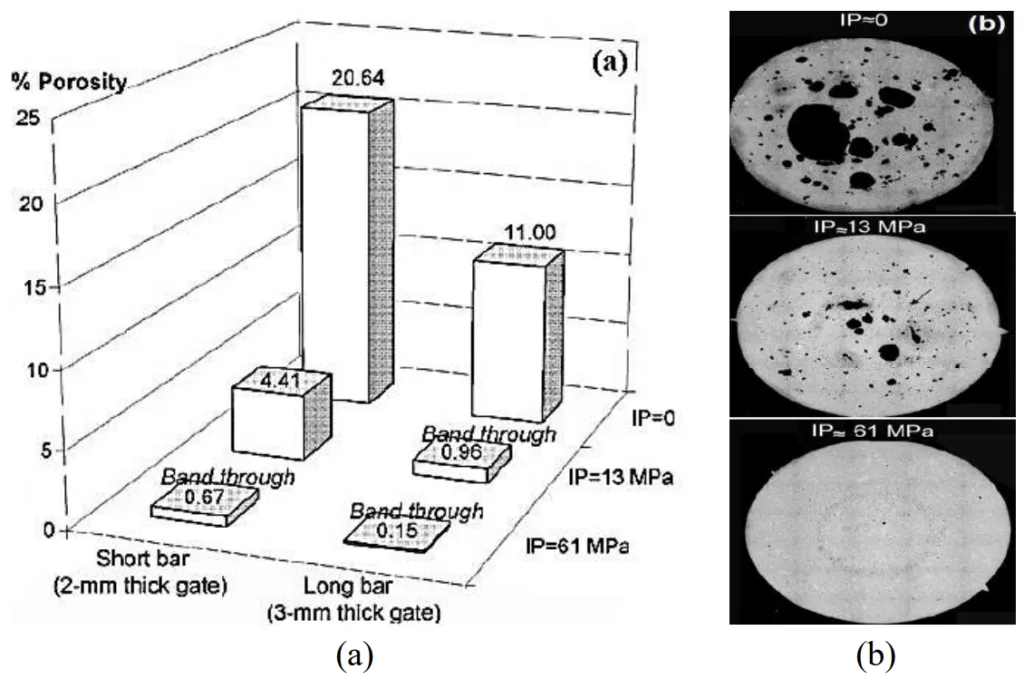
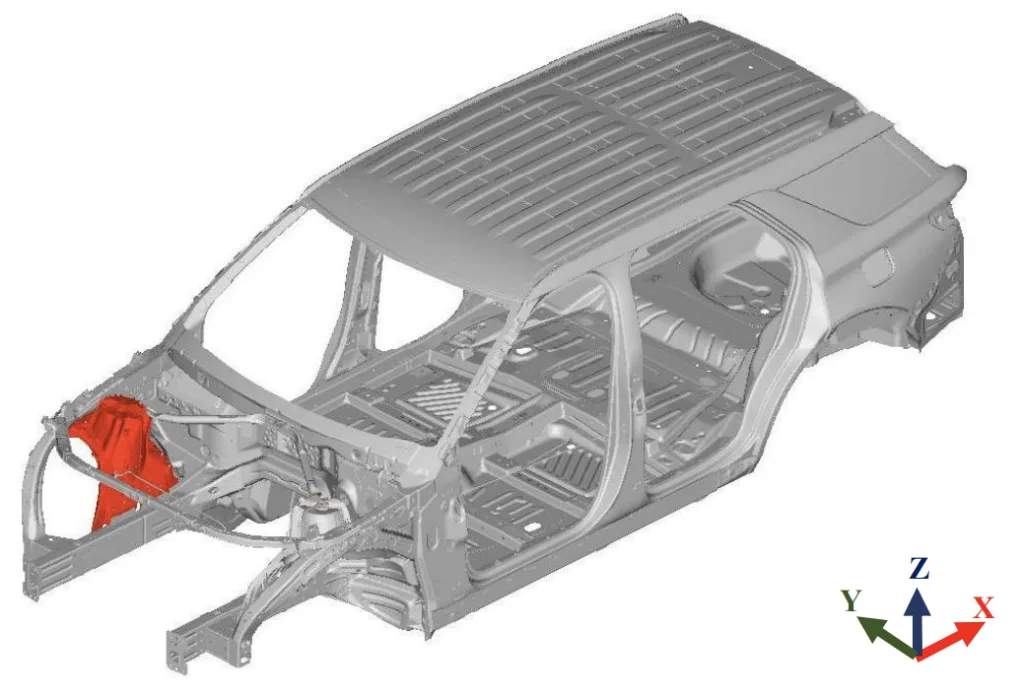
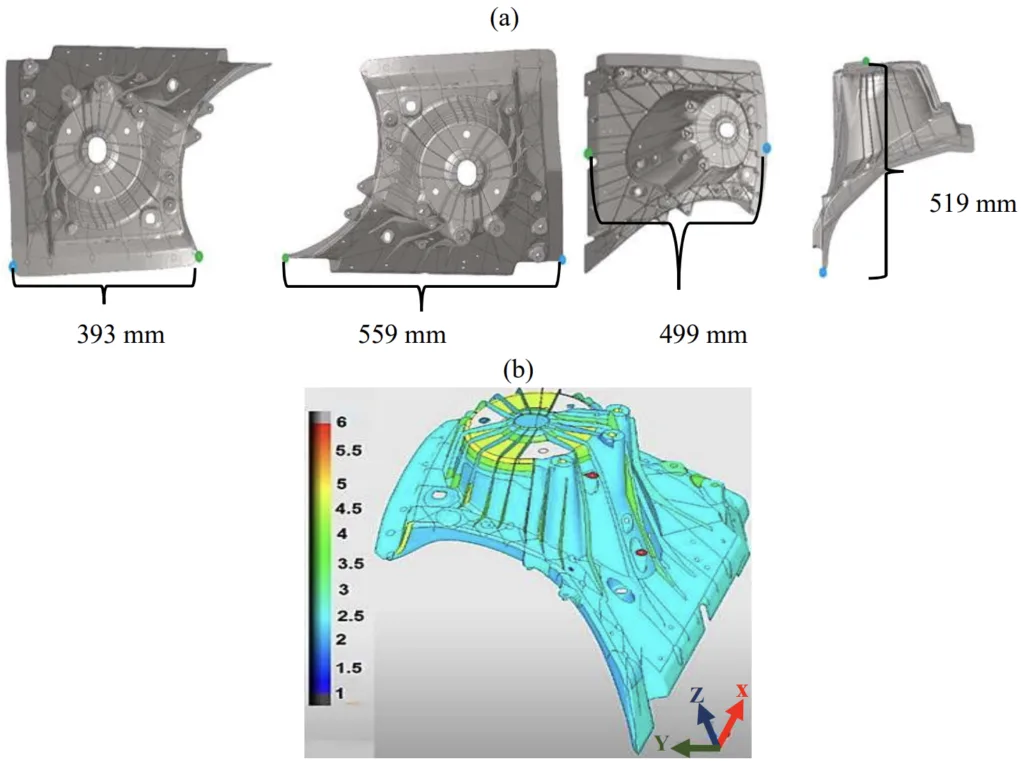
- 그림 0.1: (a) X= 1.3% Fe 및 (b) X= 0.5% Fe (MYFORD)인 AlMg4FeX 합금의 JMatPro® 시뮬레이션.
- 그림 0.2: 2020 Ford Explorer 알루미늄 쇼크 타워의 (a) 기하학적 치수 및 (b) 두께 분포(mm).
- 그림 2.7: (a) 기공 분율에 대한 게이트 속도의 영향 및 (b) 기계적 특성(수정됨 (18)).
- 그림 2.8: (a) 기공 함량 및 (b) 고압 다이캐스팅의 거시 구조에 대한 증압(IP)의 영향(수정됨 (21)).
- 그림 2.10: 콜드 플레이크의 구조와 동반되는 산화물 층(28).
- 그림 2.11: AlSi7Mg0.3 합금의 HPDC 테스트 바에서 전단 밴드(30).
- 그림 2.12: (a) 기존 액체 다이캐스팅 공정 및 (b) 반용융 다이캐스팅 공정(38)을 사용하여 형성된 AlSi7 합금의 일반적인 다이캐스팅 미세 구조.
- 그림 2.22: (a) α1-Al상의 평균 크기, (b) α1-Al상의 분율, (c) 슬러리 형성 시간 및 냉각 속도에 대한 회전 속도의 영향.
- 그림 2.23: (a) α1-Al상의 평균 크기, (b) α1-Al상의 분율, (c) 슬러리 형성 시간 및 냉각 속도에 대한 용융 과열의 영향.
- 그림 2.24: (a) α1-Al상의 평균 크기, (b) α1-Al상의 분율, (c) 슬러리 형성 시간 및 냉각 속도에 대한 용융 과열 및 EEM 첨가량(%EEM)의 복합 영향.
- 그림 2.25: (a) 레오캐스트 부품에서 발생할 수 있는 공정 과잉 밴드 및 (b) 기공 밴드(54).
- 그림 2.26: 레오캐스트 라디오 필터의 미세 구조 (a) 게이트 근처 및 (b) 벤트 근처(49).
- 그림 3.1: 2020 Ford Explorer 차체의 알루미늄 쇼크 타워(빨간색).
- 그림 3.2: 계산 도구에서 투자 섹션의 비용 개요.
- 그림 3.3: 2016년 1월부터 2018년 12월까지 런던 금속 거래소(수정됨 (71))에 따른 톤당 달러 기준 알루미늄 합금 가격.
- 그림 4.1: 2020 Ford Explorer 알루미늄 쇼크 타워의 (a) 기하학적 치수 및 (b) 두께 분포(mm).
- 그림 4.2: 실험적 접근 방식.
- 그림 4.3: (a) 전기 저항 유지로, (b) 쇼트 슬리브, 래들 및 로봇 팔, (c) 진공 보조 다이로 구성된 HPDC 설정.
- 그림 4.4: 공급업체 1의 플레이트 치수.
- 그림 4.5: 공급업체 1의 HPDC 시험을 위한 다이 캐비티 설계.
- 그림 4.6: 공급업체 2의 플레이트 치수.
- 그림 4.7: (a) 유도 로, (b) EEM 생산 스테이션, (c) 슬러리 생산 스테이션으로 구성된 설정.
- 그림 4.8: (a) EEM의 높이 조정 전(주조 EEM), (b) 톱질 기계, (c) EEM의 높이 조정 후(hEEM).
- 그림 4.9: 슬러리 제조 공정.
- 그림 4.10: 공급업체 1의 RheoMetalTM 주조 시험을 위한 다이 캐비티 설계.
- 그림 4.11: (a) 상단 뷰, (b) 하단 뷰, (c) 부품의 측면 뷰.
- 그림 4.12: (a) 800톤 HPDC 기계, (b) 다이 및 두 번째 로봇 팔, (c) 이동 트레이.
- 그림 4.13: 반용융 슬러리 생산을 위한 다양한 사전 단계.
- 그림 4.14: 1.5-1.7%Fe 및 4.5% Mg(수정됨 (77))의 표준 AlMg4Fe2 합금의 상 다이어그램.
- 그림 4.15: 원과 화살표(수정됨 (77))로 입증된 표준 AlMg4Fe2 합금에 대한 제안된 개선 사항.
- 그림 4.16: 1.3%Fe의 Al-Mg-Fe 합금에 대한 JMatPro® 시뮬레이션.
- 그림 4.17: MYFORD 합금에 대한 JMatPro® 시뮬레이션.
- 그림 4.18: mm 단위 Type E 샘플의 정확한 기하학적 치수(6).
- 그림 4.19: mm 단위 미니 샘플의 정확한 기하학적 치수.
- 그림 4.20: 공급업체 1 플레이트 및 인장 테스트 샘플의 3D 모델.
- 그림 4.21: (a) 초기 치수, (b) 추가 1mm, (c) mm 단위 (i) 미니 샘플 및 (ii) Type E 샘플의 최종 치수.
- 그림 4.22: 미니 샘플의 상단 및 측면 뷰 (a) 준비 전 및 (b) 준비 후.
- 그림 4.23: (a) 공급업체 1 플레이트, (b) 공급업체 2 플레이트, (c) 공급업체 3 부품에서 추출한 인장 테스트 샘플.
- 그림 4.24: 미니 및 Type E 샘플에 대한 인장 테스트 설정.
- 그림 4.25: 인장 테스트 중 다양한 테스트 속도.
- 그림 4.26: (a) 3점 굽힘 테스트 설정 및 (b) 중요한 치수(4).
- 그림 4.27: 굽힘 테스트 샘플의 치수.
- 그림 4.28: (a) 공급업체 1 플레이트, (b) 공급업체 2 플레이트, (c) 공급업체 3 부품에서 3점 굽힘 테스트 샘플의 위치.
- 그림 4.29: (a) 굽힘 각도의 예 및 (b) 굽힘 각도 측정 도구.
- 그림 4.30: 밀도 측정 시험 설정.
- 그림 4.31: (a) 공급업체 1 플레이트(두께 = 3.1mm) 및 (b) 공급업체 2 플레이트(두께 = 2.65mm)에서 SPR 샘플의 위치.
- 그림 4.32: 양호한 SPR 접합의 예(86).
- 그림 4.33: 플랫 다이 설계(88).
- 그림 4.34: 수동 시험을 위한 Henrob SPR 설정.
- 그림 4.35: (a) SPR 공정(86)을 사용한 접합 제작 및 (b) 연결된 구조.
- 그림 4.36: (a) 원주형 균열, (b) 깊은 방사형 균열, (c) 가벼운 방사형 균열의 예.
- 그림 4.37: 25mm * 100mm 랩 전단 테스트 샘플.
- 그림 4.38: 공급업체 3의 부품에 대한 SPR 시험.
- 그림 4.39: (a) 공급업체 1 플레이트, (b) 공급업체 2 플레이트, (c) 공급업체 3 부품에서 추출한 샘플의 위치.
- 그림 4.40: 핫 마운트 샘플의 예.
- 그림 4.41: 공급업체 1 플레이트에서 위치 a, b, c.
- 그림 4.42: (a) 다양한 샘플의 총 연신율 값(%) 및 (b) 플레이트의 해당 위치. (표 4.3, P54의 지정)
- 그림 4.43: (a) 다양한 샘플 유형의 총 연신율 값(%) 및 (b) 조사된 플레이트 중 하나의 샘플 개요. (표 4.3, P54의 지정)
- 그림 4.44: (a) 총 연신율 값에 대한 샘플 방향의 영향(%), (b) 서로에 대한 세로 및 수직 샘플의 위치, (c) 추출된 세로 샘플의 위치, (d) 추출된 수직 샘플의 위치. (표 4.3, P54의 지정)
- 그림 4.45: (a) Type E 샘플 및 (b) 미니 인장 테스트 샘플을 사용하여 공급업체 1에서 HPDC 공정의 일관성. (표 4.3, P54의 지정)
- 그림 5.1: AlMg4Fe2의 총 연신율(%)에 대한 용융 흐름 속도의 영향. (표 4.3, P54의 지정)
- 그림 5.2: (a) AlSi7Mg0.3 및 (b) AlMg6Si2MnZr의 총 연신율(%)에 대한 용융 흐름 속도의 영향. (표 4.3, P54의 지정)
- 그림 5.3: AlMg5Si2Mn의 총 연신율(%)에 대한 용융 흐름 속도의 영향. (표 4.3, P54의 지정)
- 그림 5.4: AlMg4Fe2의 총 연신율(%)에 대한 증압의 영향. (표 4.3, P54의 지정)
- 그림 5.5: (a) Rp0.2 값(MPa), (c) Rm 값(MPa), (c) 총 연신율 값(%) 측면에서 다양한 HPDC 합금 및 합금-열처리 조합 간의 비교. (표 4.3, P54의 지정)
- 그림 5.6: (a) Rp0.2 값(MPa), (c) Rm 값(MPa), (c) 총 연신율 값(%) 측면에서 다양한 HPDC 합금 간의 비교. (표 4.9, P65의 지정)
- 그림 5.7: Al-Si 합금 및 합금-열처리 조합의 힘-변위 차트. (표 4.3, P54의 지정)
- 그림 5.8: Al-Si 합금 및 합금-열처리 조합의 에너지-변위 다이어그램. (표 4.3, P54의 지정)
- 그림 5.9: Al-Si 합금 및 합금-열처리 조합의 시뮬레이션된 힘-변위 차트. (표 4.3, P54의 지정)
- 그림 5.10: Al-Si 합금 및 합금-열처리 조합의 시뮬레이션된 에너지-변위 차트. (표 4.3, P54의 지정)
- 그림 5.11: 플레이트 주조에 사용된 모든 HPDC 합금 및 합금-열처리 조합의 힘-변위 차트. (표 4.3, P54의 지정)
- 그림 5.12: 플레이트 주조에 사용된 모든 HPDC 합금 및 합금-열처리 조합의 에너지-변위 차트. (표 4.3, P54의 지정)
- 그림 5.13: 공급업체 3에서 사용된 HPDC 합금의 힘-변위 차트. (표 4.9, P65의 지정)
- 그림 5.14: 공급업체 3에서 사용된 HPDC 합금의 에너지-변위 차트. (표 4.9, P65의 지정)
- 그림 6.1: AlMg4Fe2 합금의 총 연신율(%)에 대한 증압의 영향. (표 4.5, P58의 지정)
- 그림 6.2: (a) Rp0.2 값(MPa), (c) Rm 값(MPa), (c) 총 연신율 값(%) 측면에서 다양한 RheoMetalTM 합금 간의 비교. (표 4.5, P58의 지정)
- 그림 6.3: (a) Rp0.2 값(MPa), (c) Rm 값(MPa), (c) 총 연신율 값(%) 측면에서 다양한 RheoMetalTM 합금 간의 비교. (표 4.9, P65의 지정)
- 그림 6.4: 공급업체 1에서 플레이트 주조에 사용된 RheoMetalTM 합금의 힘-변위 차트. (표 4.5, P58의 지정)
- 그림 6.5: 공급업체 1에서 플레이트 주조에 사용된 RheoMetalTM 합금의 에너지-변위 차트. (표 4.5, P58의 지정)
- 그림 6.6: 공급업체 3에서 사용된 RheoMetalTM 합금의 힘-변위 차트. (표 4.9, P65의 지정)
- 그림 6.7: 공급업체 3에서 사용된 RheoMetalTM 합금의 에너지-변위 차트. (표 4.9, P65의 지정)
- 그림 6.8: D-(50-4.63-575-1000)-R에 대한 힘-변위 차트. (표 4.5, P58의 지정)
- 그림 7.1: (a) AlMg5Si2Mn (B-(3.5-650)) 및 (b) AlMg6Si2MnZr (C-(3.5-650))의 미세 구조에서 수축 기공. (표 4.3, P54의 지정)
- 그림 7.2: (a) AlSi10MnMg-F 및 (b) AlSi10MnMg-T7의 500배 미세 구조 이미지. (표 4.3, P54의 지정)
- 그림 7.3: 전단 또는 b) 루핑(Orowan 메커니즘)에 의해 석출물을 극복하는 전위 및 c) 합금의 총 항복 강도에 대한 전위 통과 메커니즘의 영향(65).
- 그림 7.4: (a) Rp0.2 값(MPa), (b) Rm 값(MPa), (c) AlSi10MnMg-T7의 총 연신율 값(%). (표 4.3, P54의 지정)
- 그림 7.5: (a) AlSi10MnMg (H) 및 (b) AlMg4Fe2 (D-(3-650))의 200배 미세 구조 이미지. (표 4.3, P54의 지정)
- 그림 7.6: (a) AlMg4Fe2 (F-740C) 및 (b) MYFORD (G-755C)의 500배 미세 구조 이미지. (표 4.9, P65의 지정)
- 그림 7.7: 공급업체 1에서 조사된 RheoMetalTM 합금에 대한 총 연신율(%) 차트. (표 4.5, P58의 지정)
- 그림 7.8: (a) AlMg4Fe2 합금 (F-750R-1100-30C) 및 (b) MYFORD 합금 (G-755R-1100-30C)의 500배 미세 구조 이미지. (표 4.9, P65의 지정)
- 그림 7.9: RheoMetalTM 부품(빨간색) 및 HPDC(검은색)로 생산된 부품의 충돌 저항 잠재력.
7. 결론:
주요 결과 요약:
본 연구는 박벽 구조용 알루미늄 차체 주물의 대량 생산에 HPDC로 가공된 MYFORD 합금이 가장 비용 효율적인 경로라는 결론을 내립니다. MYFORD 합금(Al-Mg-Fe 합금 변형)은 HPDC에서 현재 사용 중인 AlSi10MnMg-T7 합금과 비교하여 동등한 기계적 특성, 충돌 저항 및 리벳팅 가능성을 제공하지만 고가의 열처리가 필요하지 않습니다. RheoMetalTM 공정은 다이 수명 연장을 통해 잠재적인 비용 이점을 제공하지만 HPDC는 박벽 주물에 대해 더 우수한 충돌 저항을 입증합니다.
연구의 학문적 의의:
본 연구는 박벽 구조용 알루미늄 차체 주물의 비용 효율적인 공정 경로에 대한 포괄적인 핸드북 수준의 분석을 제공합니다. 다양한 합금과 주조 공정을 체계적으로 평가하여 자동차 구조 부품용 알루미늄 다이캐스팅 최적화에 대한 귀중한 데이터와 통찰력을 제공합니다. 이 연구는 대량 생산에서 높은 성능과 비용 효율성을 모두 달성하는 데 있어 합금 선택 및 공정 매개변수 최적화의 중요성을 강조합니다.
실용적 의미:
연구 결과에 따르면 자동차 제조업체는 열처리 비용을 절감하면서 구조적 무결성을 손상시키지 않고 박벽 구조용 차체 주물에 AlSi10MnMg-T7의 비용 효율적인 대안으로 HPDC에서 MYFORD 합금을 채택할 수 있습니다. HPDC 및 RheoMetalTM 공정에 대해 식별된 최적화된 공정 매개변수는 산업 구현을 위한 실용적인 지침을 제공합니다. 이 연구는 또한 더 두껍고 작은 부품에 대한 RheoMetalTM 공정의 잠재력을 강조하여 향후 응용 분야에 대한 길을 제시합니다.
연구의 한계 및 향후 연구 분야:
- 공급업체 1의 RheoMetalTM 주조 시험은 효율성이 떨어져 HPDC와의 직접적인 비교에 영향을 미칠 수 있습니다. RheoMetalTM 공정 매개변수, 특히 용융 과열, %EEM 및 회전 속도를 추가로 최적화하면 성능과 비용 효율성을 향상시킬 수 있습니다.
- 부식 테스트는 본 연구에 포함되지 않았습니다. 향후 연구에서는 자동차 응용 분야에서 장기적인 내구성을 보장하기 위해 MYFORD 합금 및 기타 후보 합금의 내식성을 평가해야 합니다.
- 최소량 윤활(MQL) 기술 및 고급 다이 재료를 통해 다이 수명을 연장하는 것에 대한 추가 조사는 HPDC의 생산 비용을 더욱 절감할 수 있습니다.
- 더 두껍고 작은 구조 부품에 대한 RheoMetalTM 공정의 성능을 탐구하면 잠재력을 최대한 활용하고 자동차 제조에서 응용 범위를 넓힐 수 있습니다.
8. 참고 문헌:
- Rio Tinto. Aluminium: Your guide to automotive innovation. [Online] 2019. [Cited: November 11, 2019.]
- Aluminium Rheinfelden GmbH. Handbook- Primary aluminum casting alloys. [Online] 2017. [Cited: September 12, 2019.]
- Stena Aluminium. Aluminium alloy EN AB-42000. [Online] [Cited: October 30, 2019.]
- Verband der Automobilindustrie (VDA). VDA 238-100 : Plate bending test for metallic materials. Berlin : VDA, 2010.
- International Organization for Standardization (ISO). ISO 6892-1. METALLIC MATERIALS - TENSILE TESTING - Part 1: Method of test at room temperature. Geneva : ISO, 2016.
- Deutsches Institut für Normung (DIN). DIN 50125: Prüfung metallischer Werkstoffe- Zugproben. Berlin : Beuth Verlag, 2016.
- Hoegh-Guldberg, O., et al. Impacts of 1.5ºC Global Warming on Natural and Human Systems. [book auth.] V. Masson-Delmotte, et al. Global Warming of 1.5°C. An IPCC Special Report on the impacts of global warming of 1.5°C above pre-industrial levels and related global greenhouse gas emission pathways, in the context of strengthening the global response to the threat of climate change. Geneva : The intergovernmental panel on climate change (ipcc), 2018.
- Yang, Z. and Bandivadekar, A. 2017 Global update: Light-duty vehicle greenhouse gas and fuel economy standards. [Online] [Cited: May 29, 2018.]
- Ducker Worldwide LLC. 2015 North American Light Vehicle Aluminum Content Study. [Online] 2014. [Cited: November 7, 2019.]
- Goede, M., et al. Super Light Car—lightweight construction thanks to a multi-material design and function integration. European Transport Research Review. 2009, Vol. 1, 1, pp. 5-10.
- NADCA Design. Die Casting vs Metal Extrusion. [Online] NADCA Design. [Cited: November 11, 2019.]
- Yuksel, G., et al. MMLV: NVH Sound Package Development and Full Vehicle testing, SAE Technical Paper 2015-01-1615. SAE International. 2015.
- European Aluminum Association. The Aluminum Automotive manual, Manufacturing-casting methods. [Online] 2002. [Cited: May 23, 2019.]
- The American Foundry Society Technical Dept. Aluminium Alloys. Engineered casting solutions. 2006, Vol. 8, 4, pp. 30-34.
- AZoM. Aluminium Casting Techniques - Sand Casting and Die Casting Processes. [Online] 2002. [Cited: July 4, 2018.]
- Foundry Lexicon. [Online] Foundry Lexicon. [Cited: April 24, 2019.]
- Karban, Robert. The effects of intensification pressure, gate velocity, and intermediate shot velocity on the internal quality of aluminum die castings. s.l. : Purdue University, PHD thesis, 2000.
- D. R. Gunasegaram, B. R. Finnin, F. B. Polivka. Melt flow velocity in high pressure die casting: its effect of microstructure and mechanical properties in an Al-Si alloy. Materials Science and Technology. 2007, Vol. 23, 7, pp. 847-856.
- Herman, E.A. Gating Die Casting Dies. Rosemont,IL : NADCA, 1996.
- Fiorese, E, et al. Influence of injection parameters on the porosity and tensile properties of high-pressure die cast Al-Si alloys: A review. International Journal of metalcasting. 2015, Vol. 1, 9, pp. 43-53.
- Otarawanna, S., et al. Feeding mechanisms in High-pressure die castings. Metallurgical and Materials Transactions A. 2010, Vol. 41, 7, pp. 1836-1846.
- Niu, X.P., et al. Vaccum assisted high pressure die casting of aluminium alloys. Journal of Materials Processing Technology. 2000, Vol. 105, 1-2, pp. 119-127.
- SUN, S., Yuan, B. and Liu, M. Effects of moulding sands and wall thickness on microstructure and mechanical properties of Sr-modified A356 Aluminum casting alloy. Transactions of Nonferrous Metals Society of China. 2012, Vol. 22, 8, pp. 1884-1890.
- Djurdjevic, M.B. and Grzincic, M. The Effect of Major Alloying Elements on the size of secondary dendrite arm spacing in the As-cast Al-Si-Cu Alloys. ARCHIEVES of FOUNDARY ENGINEERING. 2012, Vol. 12, 1, pp. 19-24.
- K. Radhakrishna and S. Seshan. Dendritic arm spacing and mechanical properties of Aluminium Alloy castings. Cast Metals. 1989, Vol. 2, 1, pp. 34-38.
- Hartlieb, M. High Integrity Die Casting: A Holistic Approach To Improved Die Casting Quality. [Online] [Cited: November 7, 2019.]
- Pasligh, Niels. Hybride formschlüssige Strukturverbindungen in Leichtbaustrukturen aus Stahlblech und Aluminiumdruckguss. s.l. : Giesserei-Instiut der RWTH Aachen, Dissertation, 2011.
- Ahamed, A. and Kato, H. Influence of Casting Defects on Tensile properties of ADC12 Aluminum Allo Die-Castings. Materials Transactions. 2008, Vol. 49, 7, pp. 1621-1628.
- Cao, X. and Campbell, J. Oxide inclusion defects in Al-Si-Mg cast alloys. Canadian Metallurgical Quarterly. 2005, Vol. 44, 4, pp. 435-448.
- C.M.Gourlay and A.K.Dahle. Dilatant shear bands in solidifying metals. Nature. 2007, Vol. 445, 7123, pp. 70-73.
- Ghosh, A. Segregation in cast products. SADHANA. 2001, Vol. 26, 1-2, pp. 5-24.
- Midson, S.P. and Jackson, A. A comparison of Thixocasting and Rheocasting. 67th World Foundry Congress (wfc06): Casting the Future. Harrogate, UK : Institute of Cast Metals Engineers, 2006, pp. 1081-1090.
- Midson, S.P., Thornhill, L.E. and Young, K. Proc.5th Int.Conf. On Semi-Solid Processing of Alloys & Composites. Golden, Colorado : Colorado School of Mines, 1998. p 181.
- Jolly, M. Prof. John Campbell's Ten Rules for Making Relaible Castings. JOM. 2005, Vol. 57, 5, pp. 19-28.
- Nafisi, Shahrooz and Ghomashchi, Reza. Grain refining of conventional and semi-solid A356 Al-Si alloy. s.l. : Journal of Materials Processing Technology, 2006. Vol 174 pp 371-383.
- Flemings, M.C. Behaviour of metal alloys in the semi-solid state. Metallurgical Transactions A. 1991, Vol. 22, 5, pp. 957-981.
- McCartney, D.G. Grain refining of aluminium and its alloys using inoculants. International Material Reviews. 1989, Vol. 13, 5, pp. 247-260.
- Pola, A, Toci, M and Kapronas, P. Microstructure and properties of Semi-Solid Aluminum Alloys: A literature review. 2018, Vol. 8, 3, p. 181.
- Gerhard, H., et al. Semi-solid Forming of Aluminium and Steel-Introduction and overview. [book auth.] H. Gerhard and R Kopp. Thixoforming: Semi-Solid Metal Processing. Weinheim : WILEY-VCH Verlag GmbH & Co. KGaA, 2009.
- Czerwinski, F. The basics of modern semi-solid metal processing. JOM. 2006, Vol. 58, 6, pp. 17-20.
- Yurko, James A, Martinez, Raul A. and C.Flemmings, Merton. The use of Semi Solid Rheocasting (SSR) for Aluminum automotive castings. s.l. : SAE paper 2003-01-0433., 2003.
- Fan, Z. Semisolid metal processing. International Materials Reviews. 2002, Vol. 47, 2, pp. 49-85.
- Kirkwood, D. H., et al. Semi-Solid Processing of Alloys. Berlin, Heidelberg : Springer, 2010.
- Modigell, M., Annalisa, P. and Marialaura, T. Rheological Characterization of Semi-Solid Metals: A Review. Metals. 2018, Vol. 8, 4, pp. 245-268.
- Basner, T. Rheocasting of semi solid A357 Aluminum, SAE paper :2000-01-0059. SAE International. 2000.
- Midson, S.P. Rheocasting processes for Semi-Solid Casting of Aluminium Alloys. Die Casting Engineer. 2006, Vol. 1, pp. 48-51.
- C.P, Hong, and J.M, Kim. Development of Advanced Rheocasting Process and its applications. Solid State Phenomena. 2006, Vols. 116-117, pp. 44-53.
- Patent: WO/2006/062, 482. A method of and a device for producing a liquid-solid metal composition. Filling date: 2006, Inventors: Wessen, M; Cao, H.
- Payandeh, Mostafa. Rheocasting of Aluminium Alloys, Process and components characteristics. Jönköping university, PhD thesis, 2016.
- H.Cao, M.Wessén & O.Granath. Effect of injection velocity on porosity formation in Al rheocast component using Rheometal process. International Journal of Cast Metals Research. 2010, Vol. 23, 3, pp. 158-163.
- Lee, J., Seok, H. and Lee, H. Effect of the Gate Geometry and the Injection Speed on the Flow. Metals and Materials International. 2003, Vol. 9, 4, pp. 351-357.
- O.Granath, M.Wessen and H.Cao. Determining the effect of the slurry process parameters on semisolid A356 alloy microstructures produced by Rheometal process. International Journl of Cast Metals Research. 2008, Vol. 21, 5, pp. 349-356.
- Bladh, M., Wessen, M. and Dahle, A.K. Shear band formation in shaped Rheocast Aluminium component at various plunger velocities. Trans.Nonferrous Met. Soc. China. 2010, Vol. 20, 9, pp. 1749-1755.
- Payandeh, M., Jarfors, A. and Wessen, M. Influence of microstructural inhomogenity on fracture behaviour in SSM-HPDC Al-Si-Cu-Fe component with low Si content. Solid state phenomena. Vols. 216-217, pp. 67-74.
- Zhu, Baiwei. On the influence of Si on Anodising and Mechanical properties of Cast Aluminium Alloys. Jönköping University, Licentiate thesis, 2017.
- Hegde, S. and Prabhu, K.N. Modification of eutectic silicon in Al-Si alloys. Journal of Materials science. 2008, Vol. 43, 9, pp. 3009-3027.
- Zhu, X., et al. The effects of varying Mg and Si levels on the microstructural inhomogenity and eutectic Mg2Si morphology in die-cast Al-Mg-Si alloys. Journal of Materials Science. 2019, Vol. 54, 7, pp. 5773-5787.
- Yuan, W. and Liang, Z. Effect of Zr addition on properties of Al-Mg-Si aluminum alloy used for all aluminium alloy conductor. Materials and Design. 2011, Vol. 32, 8, pp. 4195-4200.
- Ji, S., et al. Effect of iron on the microstructure and mechanical property of Al-Mg-Si-Mn and Al-Mg-Si diecast alloys. Materials Science and Engineering A. 2013, Vol. 564, pp. 130-139.
- Hwang, J.Y., Doty, H.W. and Kaufman, M.J. The effects of Mn additions on the microstructure and mechanical properties of Al-Si-Cu casting alloys. Materials Science and Engineering A. 2008, Vol. 488, 1-2, pp. 496-504.
- Murray, J.L. and McAlister, A.J. Bulletin of Alloy Phase Diagrams. 1984, Vol. 5, 1, pp. 86-112.
- Zeru, G.T., Mose, B.R. and Mutuli, S.M. The fluidity of a Model Recycle-Friendly Al-Si Cats Alloy for Automotive Engine Cylinder Head Application. International Journal of Engineering Research & Technology (IJERT). 2014, Vol. 3, 8.
- Timelli, G. and Bonollo, F. Fluidity of aluminium die casting alloys. International Journal Of Cast Metals Research. 2007, Vol. 20, 6, pp. 304-311.
- Gwózdz, M and Kwapisz, K. Influence of ageing process on the microstructure and mechanical properties of aluminium-silicon cast alloys - Al-9%Si-3%Cu and Al-9%Si-0.4%Mg. s.l. : Jönköping University, Bachelor thesis, 2008.
- Mohamed, A.M.A. and Samuel, F.H. A Review on the Heat Treatment of Al-Si-Cu/Mg Casting Alloys. Heat treatment - Conventional and novel applications. s.l. : IntechOpen, 2012, pp. 55-72.
- Katgerman, L and Eskin, D. Hardening, annealing and aging. [book auth.] G.E Totten and D.S Mackenzie. Handbook of Aluminum: Vol. 1: Physical Metallurgy and Processes. New York : Marcel Dekker, Inc, 2003, pp. 269-271.
- Bühler AG. Carat. The solution with highest value creation for sophisticated parts. [Online] 2018. [Cited: May 24, 2019.]
- Tecnopres. Hydraulic 4 columns Trimming presses. [Online] 2018. [Cited: May 24, 2019.]
- KMA Umwelttechnik GmbH. KMA press release GIFA 2007. [Online] 2007. [Cited: November 8, 2019.]
- STØTEK Inc. Holding Furnace (STE) / (STET). [Online] STØTEK Inc. [Cited: July 27, 2018.]
- The London Metal Exchange. LME Aluminum alloy. [Online] The London Metal Exchange, 2019. [Cited: January 24, 2019.]
- Kaufmann, H. and Uggowitzer, P.J. Metallurgy and Processing of High Integrity Light Metal Pressure Castings. Berlin : SCHIELE & SCHÖN, 2014.
- Han, Q., Kenik, E.A. and Viswanathan, S. Die soldering in aluminium die casting. Office of Scientific & Technical Information Technical Reports. 2000.
- Abdulhadi, H.A., et al. Thermal Fatigue of Die-Casting Dies: An Overview. MATEC Web of Conferences, ICMER 2015. 2016, Vols. 74, 00032.
- Visi-trak worldwide, LLC. High-Q-Cast. [Online] [Cited: July 23, 2018.]
- Midson, S.P., Minkler, R.B. and Brucher, H.G. Gating of Semi-Solid Aluminum Castings. Proc 6th Inter. Conf. on Semi-Solid Processing of Alloys and Composites. Turin, Italy : s.n., 2000, pp. 67-71.
- Aluminium Rheinfelden GmbH. Primary aluminum- HPDC alloys for Structural Casts in Vehicle Construction. [Online] 2017. [Cited: November 8, 2019.]
- Gulliver, G.H. The quantitative effect of rapid cooling upon the constitution of binary alloys. J.Inst.Met. 1909, Vol. 9, pp. 120-157.
- Scheil, E. Comments on the layer crystal formation. Z.Metallkd. 1942, Vol. 34, pp. 70-72.
- ESAB. ESAB knowledge center. [Online] ESAB. [Cited: May 24, 2019.]
- Techni waterjet. Waterjet advantages. [Online] Techni waterjet, 2018. [Cited: May 24, 2019.]
- SMU department of physics. Mechanics laboratery manual - Archimedes' Principle and Buoyancy. [Online] SMU department of physics, 2002. [Cited: March 8, 2019.]
- Abbas, M., St.Pierre, G.R. and Mobley, C.E. Microporosity of Air Cast and Vacuum Cast Aluminium Alloys. AFS Transactions. 1986, Vol. 49, pp. 47-56.
- He, X., Pearson, I. and Young, K. Self-pierce riveting for sheet materials: State of the art. Journal of Materials Processing Technology. 2008, Vol. 199, 1-3, pp. 27-36.
- Li, D., et al. Self-piercing riveting- a review. The International Journal of Advanced Manufacturing Technology. 2017, Vol. 92, 5-8, pp. 1777-1824.
- Atlas Copco Group. Henrob self-pierce riveting. [Online] [Cited: August 6, 2019.]
- . Henrob BG-Rivet. [Online] [Cited: August 7, 2019.]
- . Henrob die catalogue. [Online] [Cited: November 8, 2019.]
- Stephens, E.V. Mechanical strength of self-piercing riveting. [book auth.] A Chrysanthou and X Sun. Self-Piercing Riveting: Properties, Processes and Applications. s.l. : Woodhead Publishing Limited, 2014.
- Li, D, et al. Influence of Die Profiles and Cracks on Joint Quality and Mechanical Strengths of High Strength Aluminium Alloy Joint. Advanced Materials Research. 2012, Vol. 548, pp. 398-405.
- SCG polymer solutions incorporated. SEM Analysis | SEM-EDS Analysis. [Online] SCG polymer solutions incorporated. [Cited: March 20, 2019.]
- Encyclopaedia Britannica. Spectrochemical analysis. [Online] Encyclopaedia Britannica. [Cited: January 22, 2019.]
- OTARAWANNA, S. and DAHLE, A.K. Casting of aluminium alloys. [book auth.] Roger Lumely. Fundemetals of Aluminium Metallurgy: Production, Processing and Applications. s.l. : Woodhead Publishing Limited, 2011.
- Porcaro, R., et al. The behaviour of a self-piercing riveted connection under quasi-static loading conditions. International Journal of solids and structures. 2006, Vol. 43, 17, pp. 5110-5131.
- Park, J.M., et al. High-strength bulk Al-based bimodal ultrafine eutectic composite with enhanced plasticity. Journal of Materials Research. 2009, Vol. 24, 8, pp. 2605-2609.
- Wang, Q.G., Caceres, C.H. and Griffiths, J.R. Damage by Eutectic Particle Cracking in Aluminum Casting Alloys A356/357. Metallurgical and Materials Transactions A. 2003, Vol. 34, 12, pp. 2901-2912.
- Verma, A., et al. Influence of cooling rate on the Fe intermetallic formation in an AA6063 Al alloy. Journal of Alloys and Compounds. 2013, Vol. 555, pp. 274-282.
- Bielomatik. Minimal Quantity Lubrication (MQL) Systems in Metal Cutting. [Online] [Cited: October 25, 2019.]
- Vicario, I., et al. Development of high pressure die casting dies with internal refrigeration and sensors with reinforced cast steels. International Journal of Manufacturing Engineering. 2014, Vol. 2015, Article ID 287986, pp. 1-10.
9. 저작권:
- 본 자료는 "[Mohamed Youssef Ahmed Youssef]"의 논문: "[A cost-efficient process route for the mass production of thin-walled structural aluminum body castings]"을 기반으로 합니다.
- 논문 출처: 10.18154/RWTH-2021-03555
본 자료는 위에 제시된 논문을 기반으로 요약되었으며, 상업적 목적으로 무단 사용하는 것을 금지합니다.
Copyright © 2025 CASTMAN. All rights reserved.