본 논문 요약은 Materials and technology에 발표된 논문 "주조 응용을 위한 복합 솔트코어 개발"을 기반으로 합니다.
1. 개요:
- 제목: 주조 응용을 위한 복합 염심 개발 (DEVELOPMENT OF COMPOSITE SALT CORES FOR FOUNDRY APPLICATIONS)
- 저자: 야로슬라프 베뇨, 엘리슈카 아담코바, 프란티셰크 미크쇼프스키, 페트르 옐리네크 (Jaroslav Beňo, Eliška Adámková, František Mikšovský, Petr Jelínek)
- 발행 연도: 2015년
- 발행 저널/학술 단체: Materials and technology
- 키워드: 비철 합금, 염심, 무기염, 다이캐스팅, PUR 콜드 박스, 웜 박스, 코어 용해도 및 안정성 (non-ferrous alloys, salt cores, inorganic salts, die casting, PUR Cold Box, Warm Box, core solubility and stability)
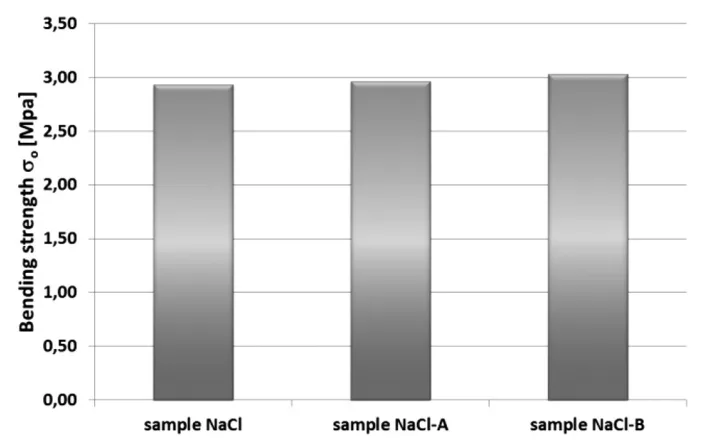
2. 연구 배경:
- 연구 주제의 사회적/학문적 맥락: 비철 합금 주조, 특히 다이캐스팅에서 복잡한 형상에 대한 수요가 증가함에 따라 개선된 코어 기술이 필요합니다. 기존의 금속 코어는 형상 복잡성이 증가하고 복잡한 내부 공동에서 코어 재료를 더 쉽게 제거해야 할 필요성에 의해 도전을 받고 있습니다. 1970년대부터 알려져 왔으며 이미 중력 및 저압 주조(예: 엔진 피스톤의 냉각 채널)에 사용된 염심 기술은 세척 용이성, 치수 복잡성, 환경 친화성 및 폐쇄 루프 재활용 측면에서 장점을 제공합니다.
- 기존 연구의 한계: 염심은 유익하지만 고압 다이캐스팅에서의 적용은 극한 조건으로 인해 제한됩니다. 이러한 조건에는 코어 침식을 유발하는 높은 금형 충전 속도, 금속 침투, 주조 합금의 높은 온도가 염 용융점에 접근함에 따른 치수 부정확성이 포함됩니다. 순수 염 매트릭스로만 만들어진 코어는 다이캐스팅에 충분하지 않을 수 있습니다.
- 연구의 필요성: 순수 염심의 다이캐스팅 한계를 극복하기 위해 복합 염심이 제안됩니다. 이러한 코어는 내열성 및 강도와 같은 특성을 개선하기 위해 첨가제로 기본 염 매트릭스를 강화합니다. 본 연구는 고품질 표면의 사전 주조 구멍을 가진 주조품 생산을 위해 서로 다른 방법(사출 및 압착)을 사용하여 제조된 복합 염심의 성능에 특정 첨가제가 미치는 영향을 결정하는 데 필요합니다.
3. 연구 목적 및 연구 질문:
- 연구 목적: 주요 목적은 고품질 표면의 사전 주조 구멍을 가진 주조품 생산 중 복합 염심의 거동에 다양한 첨가제가 미치는 영향을 조사하는 것입니다. 본 연구는 사출(바인더를 사용한 코어 박스에 사출) 및 압착(습윤 염의 고압 압착)의 두 가지 다른 방법으로 제조된 코어에 초점을 맞춥니다.
- 주요 연구 질문:
- 사출 및 압착 방법으로 제조된 복합 염심의 굽힘 강도(1차, 고온 및 잔류)에 서로 다른 첨가제가 어떻게 영향을 미치는가?
- 첨가제가 복합 염심의 다공성, 보관 수명(흡습성) 및 용해도에 미치는 영향은 무엇인가?
- 첨가제 및 표면 코팅이 복합 염심을 사용하여 생산된 다이캐스팅의 사전 주조 구멍의 표면 품질(거칠기)에 어떻게 영향을 미치는가?
- 연구 가설: 본 연구는 특정 첨가제를 염 매트릭스에 통합하면 염심의 기계적 및 열적 특성이 향상되어 고압 다이캐스팅 응용 분야에 더 적합하고 사전 주조 구멍의 표면 품질이 향상될 것이라는 가설을 세웁니다.
4. 연구 방법론
- 연구 설계: 본 연구는 복합 염심의 특성을 평가하기 위해 실험적 연구 설계를 채택합니다. 여기에는 다양한 첨가제를 사용하여 두 가지 제조 방법(사출 및 압착)으로 염심을 준비하고 물리적 및 기계적 특성을 테스트하는 것이 포함됩니다. 실제 주조 환경에서 이러한 코어의 성능을 평가하고 결과적으로 사전 주조 구멍의 표면 품질을 평가하기 위해 다이캐스팅 실험을 수행합니다.
- 자료 수집 방법:
- 굽힘 강도 시험: 1차 강도(준비 후 48시간), 고온 강도(650°C에서 1시간 후) 및 잔류 강도(650°C에서 냉각 후)를 범용 시험기를 사용하여 측정했습니다.
- 다공성 측정: 겉보기 다공성은 KCl 매트릭스의 밀도와 코어 밀도를 기준으로 계산했습니다.
- 거칠기 측정: 사전 주조 구멍의 표면 거칠기(Ra)는 ISO 1997 표준에 따라 거칠기 측정기를 사용하여 측정했습니다. 샘플당 10회 측정했으며 평균값을 사용했습니다.
- 흡습성(보관 수명) 시험: 100% 상대 습도 및 26°C에서 보관된 코어의 질량 분율(%) 증가를 시간 경과에 따라 측정했습니다.
- 용해도 시험: 20°C의 물에 담근 코어의 무게 감소를 시간 경과에 따라 측정하여 용해도를 결정했습니다.
- 분석 방법: 굽힘 강도, 다공성, 거칠기, 흡습성 및 용해도 시험에서 수집된 데이터를 평가하기 위해 정량적 분석을 사용했습니다. 통계적 방법은 첨가제 및 제조 방법의 효과의 유의성을 결정하는 데 사용되었을 것입니다.
- 연구 대상 및 범위:
- 코어 재료: 화학적으로 순수한 염(KCl), 기술 염(NaCl) 및 다양한 입도 분포를 가진 세 가지 다른 첨가제(A, B, C)를 사용하여 복합 염심을 만들었습니다.
- 주조 합금: 알루미늄 합금 AlSi9Cu3(Fe)를 다이캐스팅 실험에 사용했습니다.
- 주조 방법: 76.8 MPa의 압착 압력과 690°C의 주조 온도를 가진 CLH 400 주조 기계를 사용한 고압 다이캐스팅.
- 코어 제조 방법: 습윤 염의 고압 압착 및 Na-실리케이트 바인더를 사용한 웜 코어 박스(190°C)에 사출.
5. 주요 연구 결과:
- 주요 연구 결과:
- 코어 박스에 사출(웜 박스):
- Na-실리케이트 바인더로 생산된 코어의 가장 높은 굽힘 강도는 원래 입도 분포 염(NaCl)에서 달성되었습니다. 수정된 입도 분포(더 미세한 염)는 강도가 더 낮았습니다.
- 첨가제 A와 B는 사출로 생산된 코어의 굽힘 강도를 크게 향상시키지 못했습니다.
- 사출된 코어의 굽힘 강도는 압착된 코어의 약 25%였습니다.
- 이러한 코어는 중력 및 저압 주조에만 적합한 것으로 간주됩니다.
- 고압 압착:
- KCl 염은 NaCl 기술 염에 비해 더 높은 1차 및 2차 강도를 나타냈습니다.
- KCl 및 첨가제를 사용한 복합 염심은 1차 및 2차 강도 증가와 향상된 열 안정성(고온 강도)을 보였습니다.
- 압착된 코어의 겉보기 다공성은 4% 미만으로 유지되었습니다.
- 보관 수명 및 용해도:
- 극한 습도 조건에서도 염심의 보관 수명은 매우 우수했으며 기본 염 매트릭스(KCl 샘플)와 복합 염심 모두에서 무게 증가는 최소화되었습니다.
- 용해도 시험 결과 복합 염심의 용해도가 높았으며, 22분 이내에 완전히 용해되었고 냉간 경화 코어와 열 노출 코어 사이에 유의미한 차이가 없었습니다.
- 표면 품질:
- 표면 코팅을 사용하여 복합 코어(KCl + 15% A 및 KCl + 15% C)를 사용하면 사전 주조 구멍의 표면 품질이 향상되었습니다.
- 가장 우수한 표면 거칠기(Ra = 7.5-10.4 µm)는 지르콘 실리케이트 기반 코팅(코팅 c)을 사용한 KCl + 15% A 코어로 달성되었습니다.
- 코어 박스에 사출(웜 박스):
- 통계적/정성적 분석 결과:
- 표 2는 사출된 코어의 경우 원래 입도 분포(조성 III 및 IV)가 수정된 입도 분포(조성 I, II 및 V)에 비해 더 높은 굽힘 강도(각각 2.332 MPa 및 2.115 MPa)를 나타냈으며, 수정된 입도 분포는 1.332 MPa에서 1.794 MPa 범위였습니다.
- 표 3은 압착된 복합 코어의 경우 KCl에 첨가제 A, B 또는 C를 10% 첨가하면 일반적으로 순수 KCl에 비해 굽힘 강도(1차, 고온 및 잔류)가 증가했음을 나타냅니다. 예를 들어, 고온 강도는 순수 KCl의 > 8.9 MPa에서 첨가제 A 10% 첨가 시 > 13.2 MPa로 증가했습니다.
- 표 4는 복합 염심의 흡습성을 보여줍니다. 32일 후, 순수 KCl(K)는 0.06%의 무게 증가를 보였지만, K+30% A 및 K+30% B는 각각 2.20% 및 2.73%로 상당히 높은 증가를 보였고, K+30% C는 0.08%의 최소 증가를 보였습니다.
- 표 6은 시험 주조품의 표면 거칠기(Ra)를 나타냅니다. 코팅 c를 사용한 K+15% A는 Ra 7.5-10.4 µm을 달성했으며, 코팅 c를 사용한 K+15% C는 Ra 15.4 µm, 코팅 b를 사용한 K+15% C는 Ra 18.6 µm을 나타냈습니다. 코팅 a를 사용한 K+15% C는 Ra 7.86 µm을 달성했습니다.
- 데이터 해석: 결과는 염심 사출 성형의 경우 염 입도 분포를 제어하는 것이 강도에 매우 중요하다는 것을 시사합니다. 고압 압착의 경우 기본 염으로 KCl을 사용하고 첨가제를 통합하면 코어 강도와 열 안정성이 향상됩니다. 첨가제가 일부 경우(첨가제 A 및 B)에서 흡습성을 약간 증가시킬 수 있지만, 첨가제 C는 영향이 최소화되는 것으로 나타났습니다. 복합 염심을 사용하여 다이캐스팅에서 우수한 표면 품질을 달성하려면 표면 코팅이 필수적이며, 코팅 및 첨가제 조합의 선택은 최종 표면 마감에 큰 영향을 미칩니다.
- 그림 목록:
- 그림 1: 웜 박스 방법으로 준비된 복합 염심의 굽힘 강도
- 그림 2: 복합 염심의 용해도(냉간 경화 및 열 노출 후), K = KCl
- 그림 3: 평균 산술 거칠기 Ra 측정을 위한 모델 주조품의 사전 주조 구멍 영역
- 그림 4: 시험 주조품 표면 상세, K+15% A
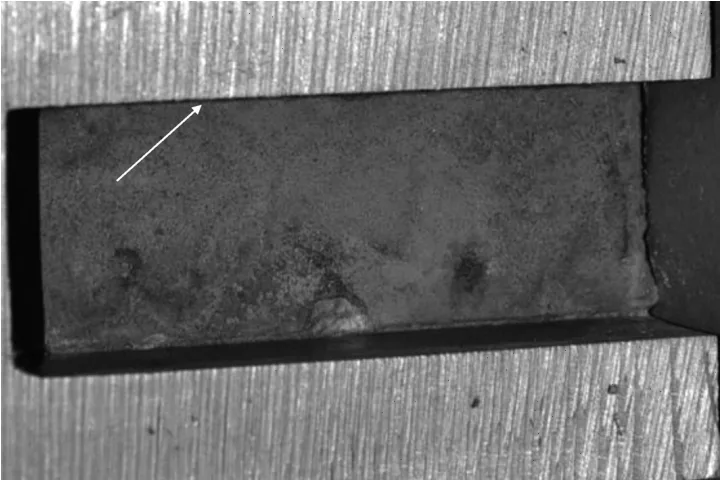
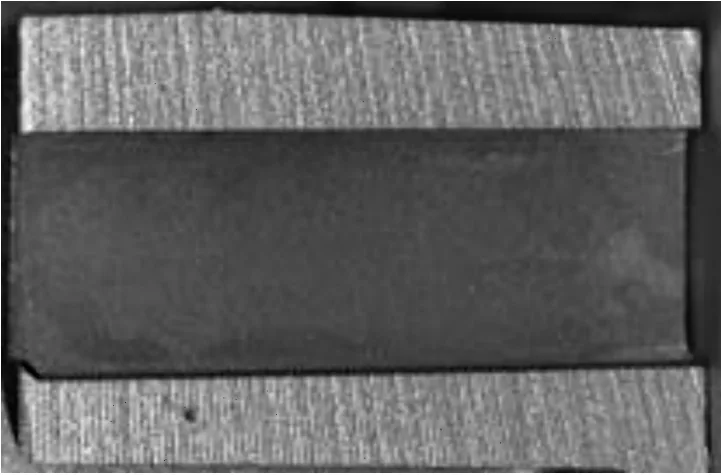
6. 결론 및 논의:
- 주요 결과 요약: 본 연구는 복합 염심, 특히 KCl과 특정 첨가제를 사용하여 고압 압착으로 제조된 복합 염심이 다이캐스팅에 적합한 향상된 기계적 및 열적 특성을 나타냄을 입증했습니다. 바인더를 사용한 사출 성형은 현재 중력 및 저압 응용 분야로 제한됩니다. 첨가제는 코어 강도와 열 안정성을 향상시키고, 표면 코팅은 고품질 표면의 사전 주조 구멍을 달성하는 데 중요합니다. 첨가제 C는 강도 향상과 최소 흡습성의 균형을 맞추는 데 유망한 결과를 보였습니다.
- 연구의 학문적 의의: 본 연구는 주조 응용 분야, 특히 다이캐스팅을 위한 복합 염심 기술에 대한 이해에 기여합니다. 첨가제 및 제조 방법이 코어 특성 및 주조 품질에 미치는 영향에 대한 귀중한 데이터를 제공합니다. 본 연구 결과는 이 분야의 추가 연구 개발을 안내할 수 있습니다.
- 실용적 의미: 본 연구는 염심 기술을 구현하려는 다이캐스팅 전문가에게 실용적인 지침을 제공합니다. 복합 염심이 우수한 표면 마감으로 복잡한 내부 형상을 생산하는 데 잠재력이 있음을 강조합니다. 본 연구는 최적화된 첨가제 및 표면 코팅을 사용한 KCl 기반 복합 코어의 고압 압착이 다이캐스팅 응용 분야에 실행 가능한 접근 방식임을 시사합니다. 첨가제 C와 지르콘 실리케이트 기반 코팅 c의 선택은 특성의 균형을 달성하는 데 특히 유망해 보입니다.
- 연구의 한계: 본 연구는 특정 첨가제와 제한된 실험 조건 세트에 초점을 맞추었습니다. 더 넓은 범위의 첨가제, 바인더 시스템 및 주조 매개변수를 탐색하기 위한 추가 연구가 필요합니다. 이러한 복합 염심의 장기적인 성능과 산업적 확장성은 추가 조사가 필요합니다.
7. 향후 후속 연구:
- 후속 연구 방향:
- 코어 특성을 더욱 최적화하기 위해 더 넓은 범위의 첨가제와 농도를 조사합니다.
- 더 넓은 응용 분야를 위해 강도를 개선하기 위해 복합 염심의 사출 성형을 위한 다양한 바인더 시스템을 탐색합니다.
- 복합 염심의 성능과 확장성을 검증하기 위해 다양한 산업 조건에서 더 광범위한 다이캐스팅 시험을 수행합니다.
- 산업 보관 및 취급 환경에서 복합 염심의 장기적인 거동을 연구합니다.
- 더 큰 규모로 복합 염심 재료의 재활용 및 환경 영향에 대해 조사합니다.
- 추가 탐색이 필요한 영역: 표면 품질 및 코어-금속 상호 작용에 대한 다양한 코팅 재료 및 적용 기술의 영향에 대한 추가 탐색이 필요합니다. 특정 주조 합금 및 형상에 대한 코어 조성 및 제조 매개변수의 최적화는 향후 연구 분야로 남아 있습니다.
8. 참고 문헌:
- P. Stingl, G. Schiller, Leichte und rückstandfreie Entkernung, Giesserei Erfahrungsaustausch, (2009) 6, 4-8
- P. Jelínek et al., Ověření solných jader na tlakově litém odlitku, Technológ, 4 (2013) 2, 17-22
- P. Lichý, M. Cagala, D. Žáček, Thermomechanical properties of foundry magnesium alloys, Proc. of 20th Anniversary International Metallurgical and Materials Conference METAL 2011, Ostrava, 2011, 890-896
- J. Malík, P. Futaš, I. Vasková, Š. Eperješi, Influence of technological factors of pressure die casting on quality of castings from silumin, Slévárenství, 55 (2007) 5/6, 259-262
- P. Jelínek et al., Influencing the strength characteristics of salt cores soluble in water, Slévárenství, 60 (2012) 3/4, 85-89
9. 저작권:
- 본 자료는 야로슬라프 베뇨, 엘리슈카 아담코바, 프란티셰크 미크쇼프스키, 페트르 옐리네크의 논문: "주조 응용을 위한 복합 솔트코어 개발"을 기반으로 합니다.
- 논문 출처: doi:10.17222/mit.2013.160
본 자료는 위 논문을 기반으로 요약되었으며, 상업적 목적으로 무단 사용하는 것을 금지합니다.
Copyright © 2025 CASTMAN. All rights reserved.