본 페이퍼 요약은 ['Journal of Materials Processing Technology']에서 발행한 ['Impact behaviour of A356 alloy for low-pressure die casting automotive wheels'] 논문을 기반으로 작성되었습니다.
1. 개요:
- 제목: 저압 다이캐스팅 자동차 휠용 A356 합금의 충격 거동 (Impact behaviour of A356 alloy for low-pressure die casting automotive wheels)
- 저자: Mattia Merlin, Giulio Timelli, Franco Bonollo, Gian Luca Garagnani
- 발행 년도: 2009년 1월
- 발행 저널/학술 단체: Journal of Materials Processing Technology
- 키워드: 알루미늄 합금 (Aluminium alloys), 충격 강도 (Impact strength), 주조 결함 (Castings defects), 미세 구조 (Microstructure), 수치 시뮬레이션 (Numerical simulation)
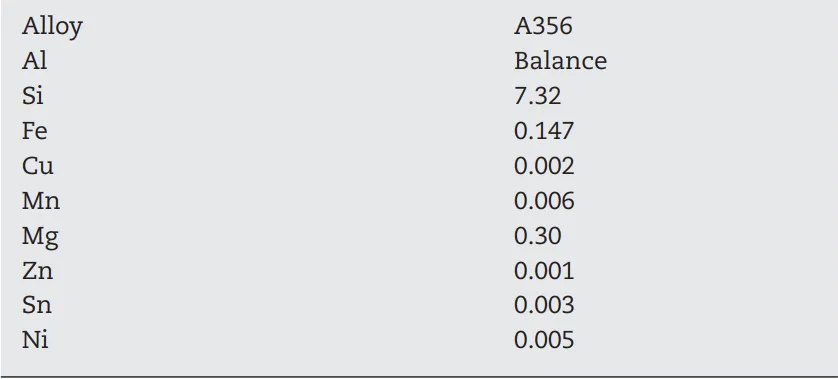
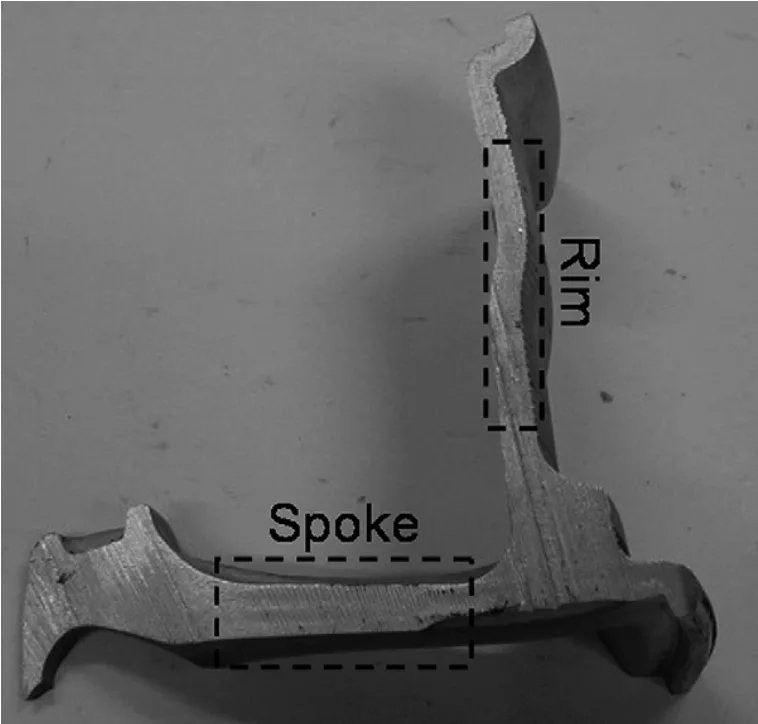
2. 초록 또는 서론
계장화된 충격 강도 시험은 저압 다이캐스팅으로 생산된 A356 알루미늄 합금 17인치 휠에서 채취한 KV 서브 사이즈 샤르피 시편에 대해 수행되었습니다. 휠은 서로 다른 형상과 열처리 상태를 보여줍니다. 본 논문에서는 미세 구조와 결함이 충격 특성에 미치는 영향을 연구합니다. 결과는 충격 에너지가 T6 열처리된 휠보다 주조 상태 휠에서 더 낮다는 것을 나타냅니다. 더 미세한 미세 구조는 항상 더 높은 충격 강도에 해당하며, 균열 전파 저항 값과 2차 덴드라이트 암 간격(SDAS) 사이에 직접적인 상관관계가 존재합니다. X선 및 밀도 측정 기술로 밝혀진 주조 결함은 샤르피 시편의 하중 지지 면적을 감소시키는 V-노치 주변에 집중될 때 결정적으로 작용합니다. 샤르피 시편의 파단면 프로파일과 표면을 조사하여 균열이 균열된 공정정 실리콘과 금속간 화합물이 상당 부분 발견되는 덴드라이트 간 공정 영역을 어떻게 가로지르는지 밝혔습니다.
수치 시뮬레이션은 분석된 휠 합금의 충전 및 응고 거동을 연구하기 위해 수행되었으며, 최종 미세 구조 및 수축 기공 형성을 예측하기 위함입니다. SDAS 측정으로 추정하고 수치 시뮬레이션 접근 방식으로 계산한 응고 시간은 양호한 일치를 보입니다. 핫스팟 및 수축 기공과 관련된 중요한 영역은 일반적으로 림 영역뿐만 아니라 스포크와 림 사이의 휠 영역에서 나타납니다.
3. 연구 배경:
연구 주제 배경:
오염 물질 배출량 감소는 에너지 소비량 감소 및 재활용 재료 증가와 함께 국제 정책의 우선 목표입니다. 자동차 분야에서 알루미늄 합금의 적용은 경제적으로 지속 가능한 혁신으로 간주됩니다. 알루미늄-실리콘 합금은 복잡한 형상의 부품을 주조하기 위해 널리 사용되는 주조 합금이며, 휠은 통합된 예입니다. 휠은 고품질 표면 마감, 충격 및 피로 성능의 조합을 충족해야 합니다. 저압 다이캐스팅(LPDC)은 알루미늄 합금 휠 주조의 주요 기술이며, 기계적 특성, 높은 생산성, 비용 효율성 및 설계 요구 사이에서 우수한 절충안을 제공합니다.
기존 연구 현황:
이전 연구에서는 알루미늄 합금의 충격 특성을 탐구했습니다. Li et al.(2004)은 계장화된 충격 시험을 사용하여 A319 합금에서 합금 원소 및 열처리 효과를 분석했습니다. Paray et al.(2000)은 Al-Si 주조 합금의 흡수 에너지를 평가했습니다. Srivastava et al.(2006)은 주조 알루미늄 합금에서 노치가 충격 값에 미치는 영향을 보여주었습니다. Murali et al.(1992)은 AlSi7Mg0.3 합금에서 마그네슘 함량을 평가했고, Shivkumar et al.(1994)은 A356-T6 합금에서 스트론튬 개질 및 응고 속도를 연구했습니다. Zhang et al.(2002)은 주조 알루미늄 부품의 항복 강도 및 연성에 대한 T6 열처리 이점을 명시했으며, Cáceres et al.(1995) 및 Wang and Cáceres(1998)는 균열 핵 생성 및 전파에서 입자 간 간격의 역할을 관찰했습니다. Cáceres and Selling(1996)은 주조 결함이 기계적 특성에 미치는 영향을 정량화했습니다.
연구의 필요성:
T6 열처리 이점은 인정되지만 추가 비용과 시간이 상당합니다. 다양한 형상과 템퍼를 가진 LPDC A356 합금 휠의 충격 특성, 미세 구조 및 주조 결함의 영향을 고려한 연구가 필요합니다. LPDC 공정 중 미세 구조 및 결함 형성을 예측하기 위한 수치 시뮬레이션도 필요합니다.
4. 연구 목적 및 연구 질문:
연구 목적:
본 연구의 목적은 계장화된 샤르피 충격 시험을 통해 다양한 형상과 템퍼를 가진 A356 17인치 휠에서 채취한 KV 서브 사이즈 샤르피 시편의 충격 특성을 조사하고, 파단 중 개별 에너지 부분에 대한 논의를 포함하는 것입니다.
핵심 연구:
- 2차 덴드라이트 암 간격(SDAS) 및 공정정 실리콘 입자와 같은 미세 구조적 특징과 충격 특성(흡수 에너지, 최대 하중, 균열 핵 생성 및 전파 에너지) 간의 상관관계 분석.
- 밀도 측정 및 X선 조사를 사용하여 기공 존재 여부 평가.
- 수치 시뮬레이션을 활용하여 휠의 충전 및 응고 거동을 평가하여 미세 구조 및 수축 기공 형성을 예측.
연구 가설:
본 논문에서는 연구 가설을 명시적으로 언급하지 않았습니다. 그러나 연구 목적 및 질문에 따라 내재된 가설은 다음과 같습니다.
- T6 열처리는 주조 상태 휠에 비해 A356 합금 휠의 충격 특성을 향상시킬 것이다.
- 더 미세한 미세 구조(더 낮은 SDAS)는 더 높은 충격 강도로 이어질 것이다.
- 주조 결함, 특히 기공은 충격 특성에 부정적인 영향을 미칠 것이다.
- 수치 시뮬레이션은 응고 및 미세 구조를 정확하게 예측할 수 있으며, 실험적 관찰과 상관관계가 있을 것이다.
5. 연구 방법론
연구 설계:
본 연구에서는 저압 다이캐스팅으로 생산된 A356 합금 휠의 충격 거동을 조사하기 위해 실험적 및 수치 시뮬레이션 접근 방식을 사용했습니다. 계장화된 샤르피 충격 시험은 다양한 템퍼 및 형상을 가진 휠의 KV 서브 사이즈 시편에 대해 수행되었습니다. 미세 구조 분석, 기공 측정, X선 조사, 파단면 분석 및 수치 시뮬레이션을 수행하여 공정, 미세 구조, 결함 및 충격 특성 간의 상관관계를 분석했습니다.
데이터 수집 방법:
- 계장화된 충격 시험: Ceast 계장화된 샤르피 진자를 사용하여 KV 서브 사이즈 샤르피 충격 시험을 수행했습니다. 총 충격 에너지(Wt), 최대 하중(Fm), 최대 하중 시 에너지(Wm) 및 균열 전파 에너지(Wp)를 측정했습니다.
- 미세 구조 분석: 광학 현미경 및 이미지 분석을 사용하여 미세 구조를 관찰하고 정량화했으며, 선형 절편법을 사용하여 SDAS 측정을 포함했습니다. SEM 및 EDS는 파단면 분석 및 파단면 분석에 사용되었습니다.
- 기공 측정: 아르키메데스 원리에 기반한 밀도 측정 및 X선 조사(매크로 포커스 및 마이크로 포커스)를 사용하여 기공을 정량화하고 국소화했습니다.
- 수치 시뮬레이션: MAGMAlpdc 모듈이 있는 MAGMASOFT® v.4.2 소프트웨어를 사용하여 충전 및 응고 거동을 시뮬레이션했습니다. 가상 열전대를 사용하여 온도 프로파일을 검증했습니다.
분석 방법:
- 상관관계 분석: 통계적 상관관계를 사용하여 SDAS, 기공 및 충격 특성(충격 에너지, Wp) 간의 관계를 분석했습니다.
- 파단면 분석: SEM 및 광학 현미경을 사용하여 파단면 및 프로파일을 분석하여 미세 구조 및 결함과 관련된 균열 시작 및 전파 메커니즘을 이해했습니다.
- 수치 시뮬레이션 검증: 시뮬레이션된 응고 시간 및 온도 프로파일을 SDAS 측정 및 열전대 데이터와 비교하여 수치 모델을 검증했습니다.
연구 대상 및 범위:
연구 대상은 저압 다이캐스팅(LPDC)으로 생산된 3개의 A356 알루미늄 합금 17인치 자동차 휠입니다.
- 휠-1: 7-스포크, 주조 상태 템퍼.
- 휠-2: 5-스포크, T6 열처리 조건.
- 휠-3: 5-스포크, T6 열처리 조건 (휠-2와 비교하여 다른 형상 및 스포크 두께).
시편은 시험 및 분석을 위해 이 휠의 스포크 및 림 영역에서 채취했습니다.
6. 주요 연구 결과:
핵심 연구 결과:
- 충격 에너지 및 열처리: 충격 에너지는 T6 열처리된 휠(휠-2 및 휠-3)에 비해 주조 상태 휠-1에서 더 낮습니다. T6 열처리는 충격 에너지를 60% 이상 증가시킵니다.
- 미세 구조 및 충격 강도: 더 미세한 미세 구조(더 낮은 SDAS)는 더 높은 충격 강도에 해당합니다. 균열 전파 에너지(Wp)와 SDAS 사이에 직접적인 상관관계가 관찰되었습니다.
- 주조 결함 및 충격 특성: 주조 결함, 특히 기공은 충격 특성을 감소시키며, 특히 샤르피 시편의 V-노치 주변에 집중될 때 하중 지지 면적을 감소시킵니다.
- 파단 메커니즘: 균열 전파는 균열된 공정정 실리콘 및 금속간 화합물을 포함하는 덴드라이트 간 공정 영역을 따릅니다. 파단면은 스포크 시편에서 결정립계 파단 및 연성 파단을 보였고, 림 시편에서 덴드라이트 간 파단을 보였습니다.
- 수치 시뮬레이션 검증: SDAS 측정 및 수치 시뮬레이션으로 추정된 응고 시간은 양호한 일치를 보였습니다. 핫스팟 및 수축 기공에 대한 중요한 영역은 스포크와 림 사이의 접합 영역과 림 영역에서 확인되었습니다.
- 기공 분포: 휠-3은 가장 높은 기공 함량을 나타냈으며, 주로 스포크 영역에 집중되었습니다. 기공 분포는 비균질적이었습니다. 마이크로 포커스 X선은 샤르피 시편의 노치 주변에 기공이 존재함을 밝혔습니다.
제시된 데이터 분석:
- 그림 6: T6 열처리가 주조 상태 조건에 비해 충격 에너지와 최대 하중을 모두 크게 증가시키는 것을 보여줍니다. 림 영역은 일반적으로 동일한 휠 템퍼 조건 내에서 스포크 영역보다 약간 더 높은 충격 에너지와 최대 하중을 나타냅니다.
- 그림 8: 균열 전파 에너지(Wp)가 총 충격 에너지의 상당 부분(60-75%)을 구성함을 나타냅니다. 주조 상태 휠-1은 전체 충격 에너지가 가장 낮음에도 불구하고 Wp 비율이 가장 높습니다.
- 그림 9: SDAS와 Wp% 간의 음의 상관관계를 보여주며, 더 미세한 미세 구조(더 낮은 SDAS)는 더 미세한 구조에서 균열 시작 저항이 증가하여 균열 전파에 흡수되는 에너지 비율이 더 낮은 경향이 있음을 시사합니다.
- 표 2: SDAS와 충격 에너지 간의 역관계를 정량화합니다. 더 낮은 SDAS 값(더 미세한 미세 구조)은 더 높은 충격 에너지와 관련이 있으며, 특히 림과 스포크 영역 및 주조 상태와 T6 조건을 비교할 때 분명합니다.
- 그림 17: 계산된 응고 시간과 추정된(SDAS 기반) 응고 시간 간의 합리적인 일치를 보여주며, 응고 거동을 예측하는 수치 시뮬레이션의 능력을 검증합니다.
그림 목록:
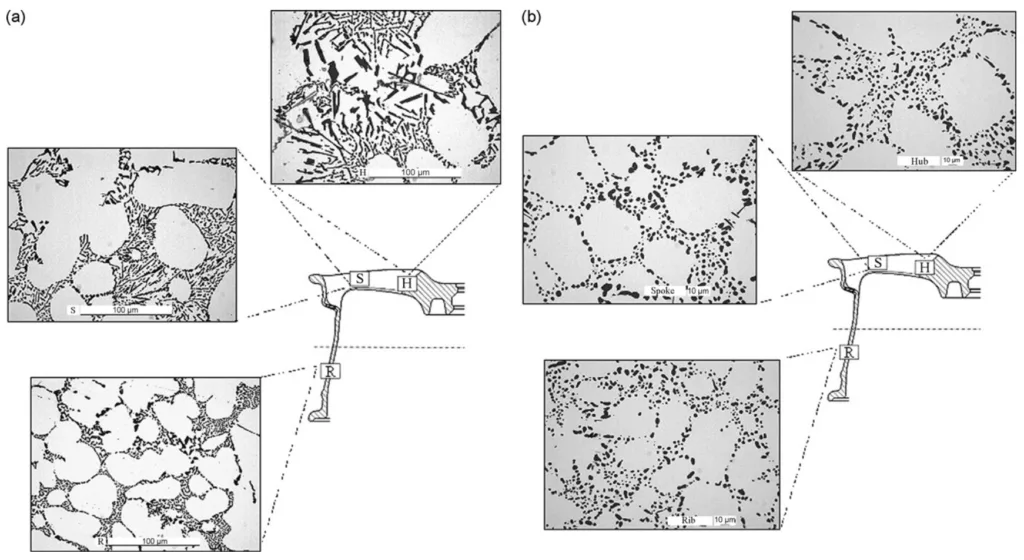
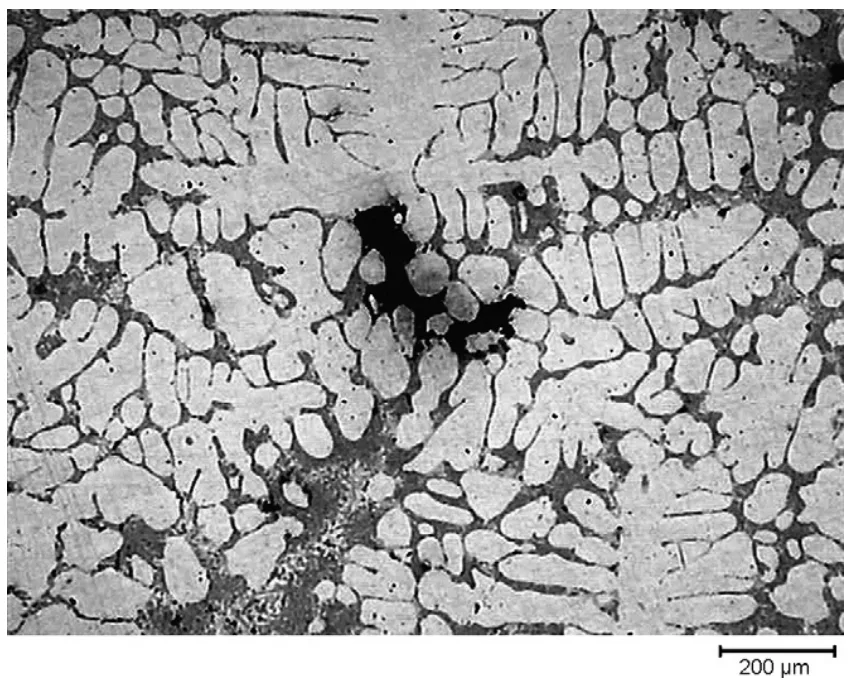
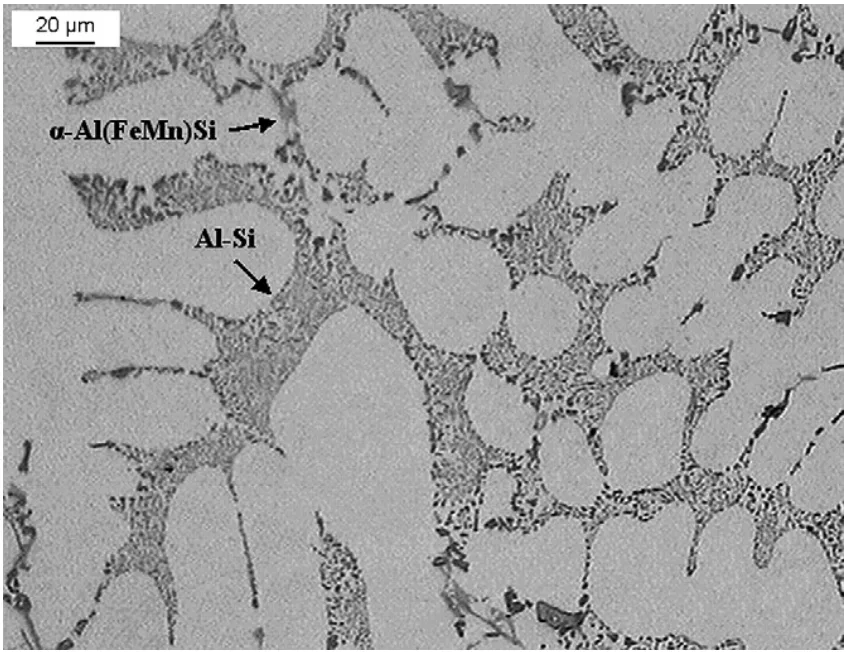
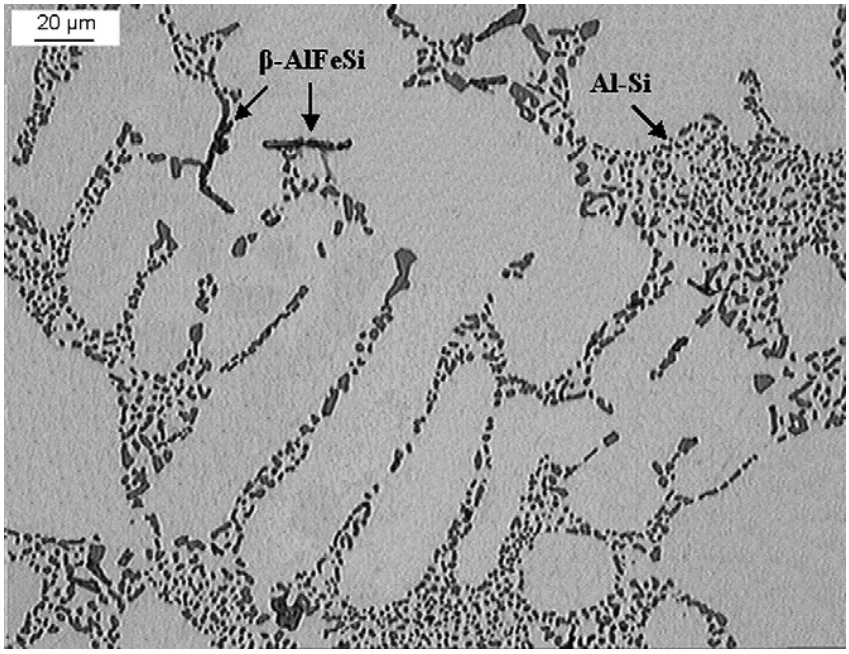
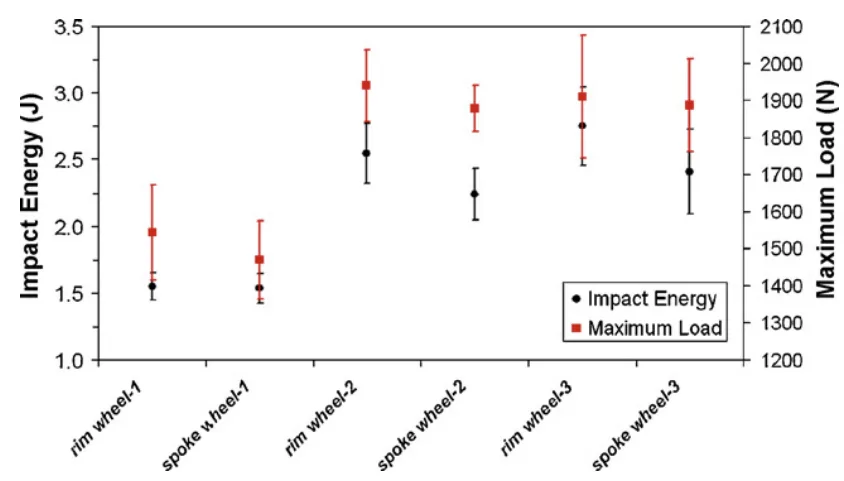
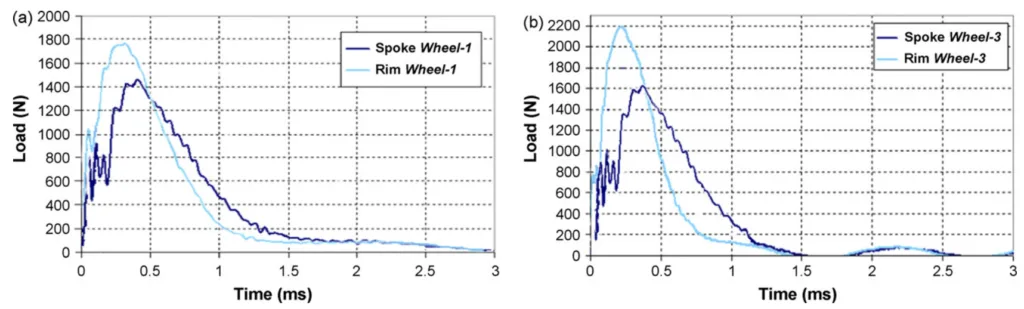
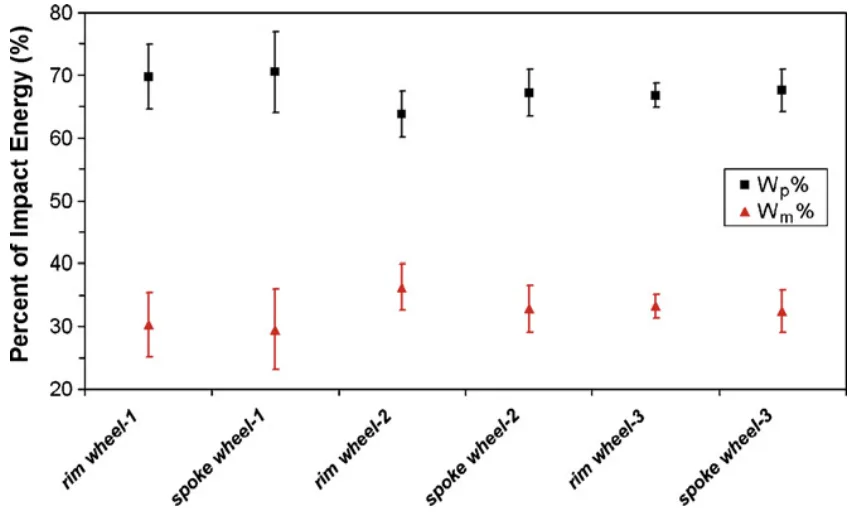
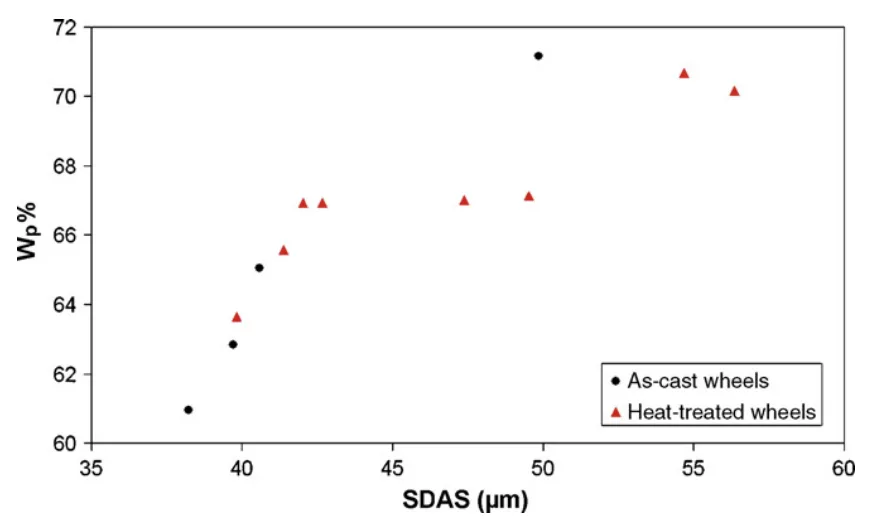
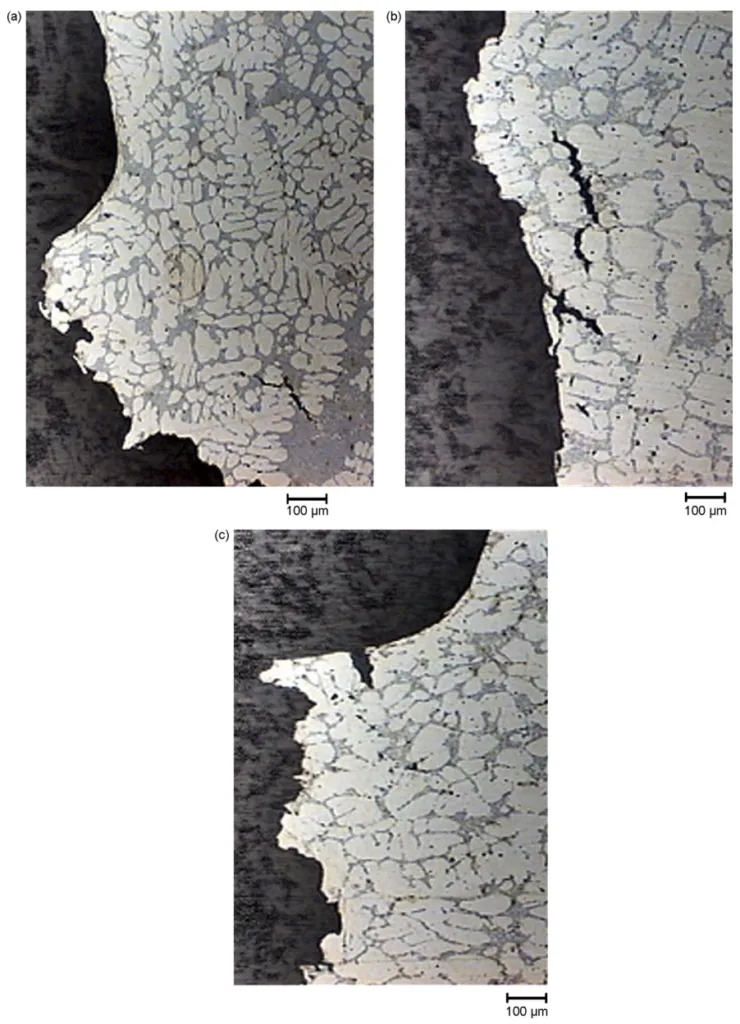
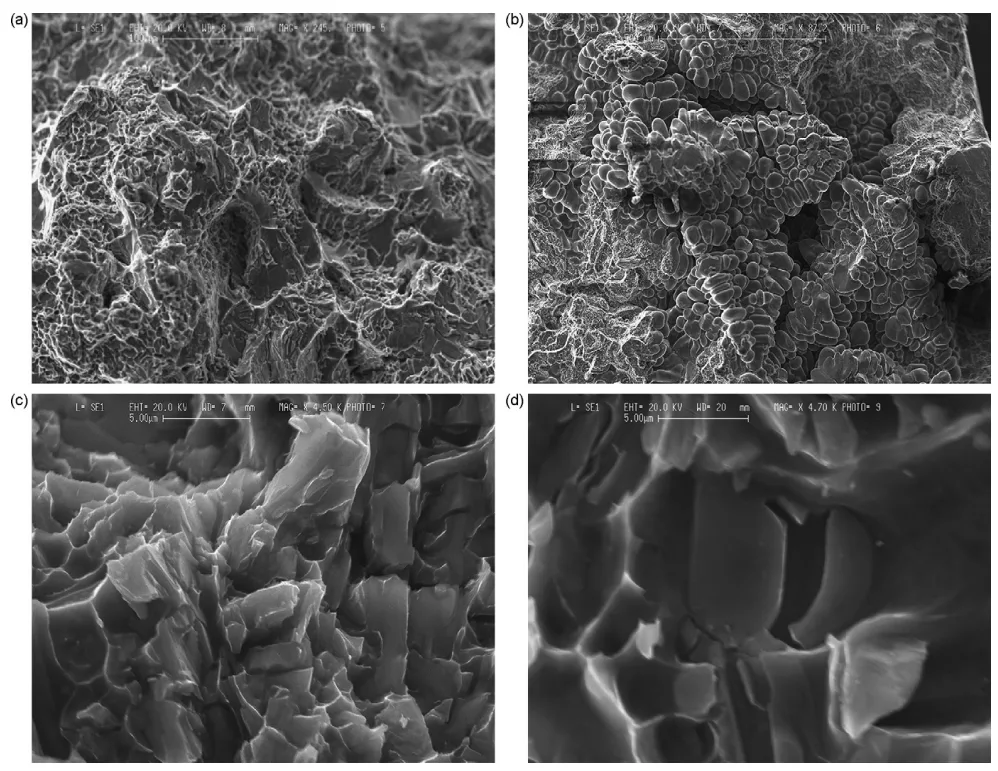
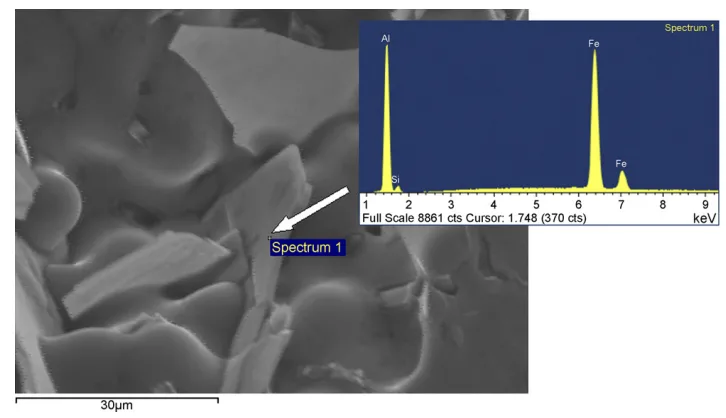
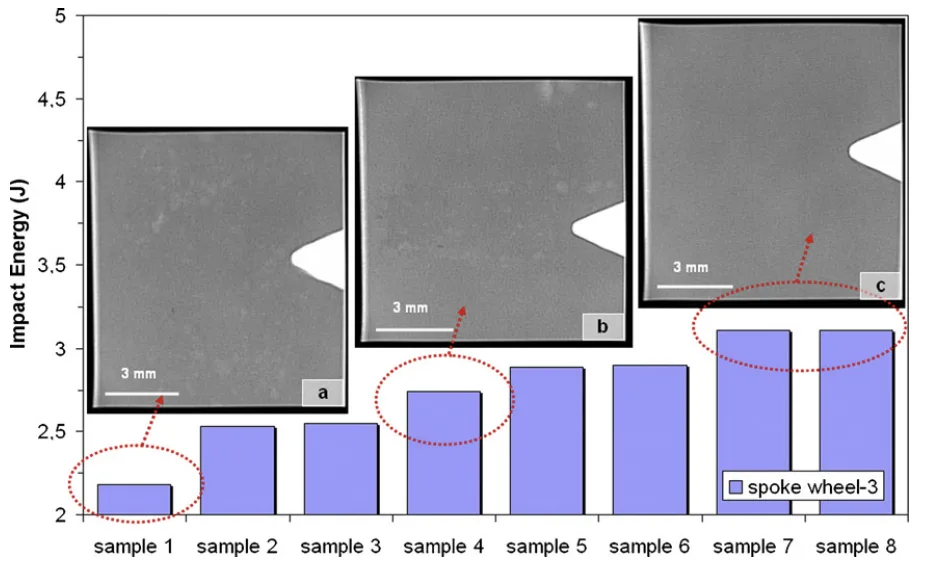
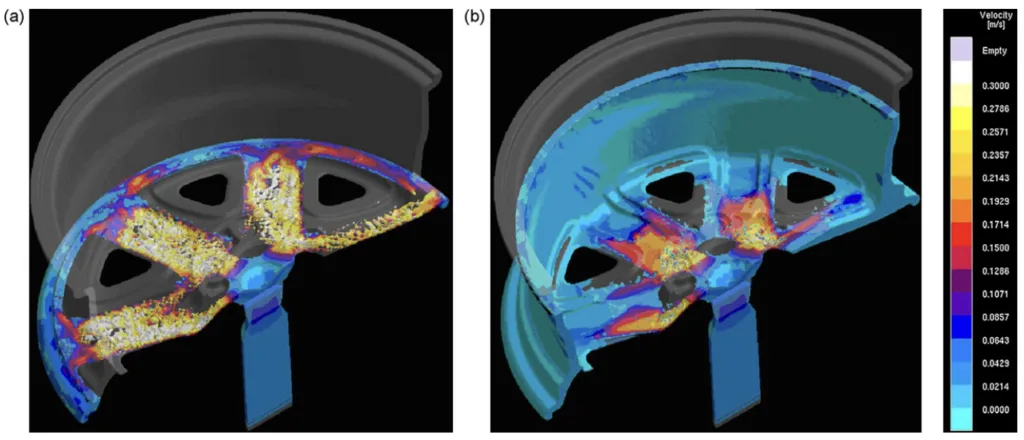
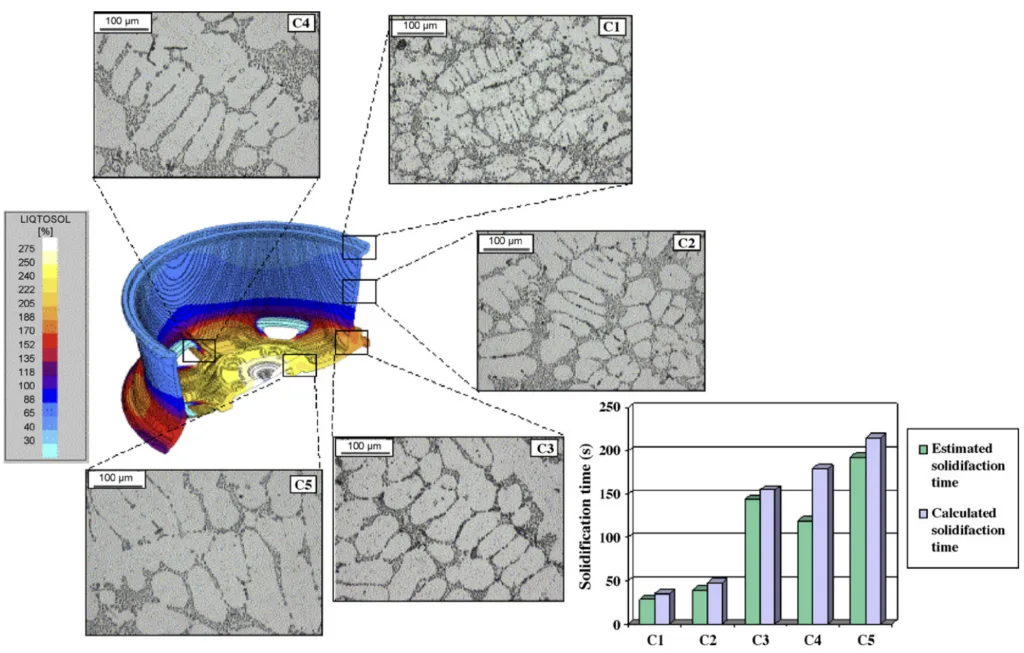
- Fig. 1 - Position of the spoke and the rim zone in the wheels analysed.
- Fig. 2- Microstructure of (a) wheel-1 and (b) wheel-2 with reference to the different positions analysed.
- Fig. 3 - Optical micrograph of a shrinkage porosity in the rim zone.
- Fig. 4- Optical micrograph showing secondary phase particles in rim area of wheel-1. The eutectic silicon is in the form of fibrous particles in the interdendritic channels.
- Fig. 5 Optical micrograph showing secondary phase particles in rim area of wheel-3. The distribution of eutectic silicon is homogeneous and globular.
- Fig. 6 - Impact energy and maximum load measured in the different positions of the wheels. The standard deviations are shown as error bars.
- Fig. 7 - Load-time curves of samples obtained from spoke and rim area of (a) wheel-1 and (b) wheel-3.
- Fig. 8 - Percentage of energy absorbed during crack nucleation and propagation and measured at different positions of the wheels analysed. The standard deviations are shown as error bars.
- Fig. 9 - Correlation between SDAS and Wp% (percentage of energy absorbed during crack propagation).
- Fig. 10 Optical micrographs of the fracture profiles of samples drawn from (a) the rim of wheel-1 and from (b) the spoke of wheel-2 and (c) wheel-3. Secondary cracks are evident.
- Fig. 11 - Features of the fracture surfaces of the Charpy specimens drawn from the wheels analysed as revealed by SEM. (a) Transcrystalline and ductile fracture from the spoke of wheel-2; (b) interdendritic fracture from the rim of wheel-1; (c) micronecks and dimples from the rim of wheel-1; (d) cleavage fracture in the silicon precipitate from the rim of wheel-3.
- Fig. 12 - SEM micrograph of β-AlFeSi platelet, on the fracture surface of sample drawn from the spoke of wheel-3, with EDS spectra.
- Fig. 13 - Percentage porosity measured at different positions of the wheels analysed. The standard deviations are shown as error bars.
- Fig. 14 - Micro-focus X-ray image of Charpy sample showing the presence of porosity around the notch.
- Fig. 15 - Impact energy of some samples drawn from the spoke of wheel-3 associated with respective X-ray images, taken in the zone around the V-notch. The X-ray images refer to a high-defect (a), medium-defect (b) and low-defect (c) content.
- Fig. 16 - Calculated melt velocity at (a) 20% and (b) 70% of die filling of wheel-1.
- Fig. 17 - Calculated solidification times with corresponding microstructure within wheel-2. Solidification times, estimated by means of SDAS measurements and calculated with a numerical simulation approach, were compared.
- Fig. 18 - Shrinkage porosity in the rim area and in the junction between the spoke and the rim within wheel-2. These zones are critical for feeding. The casting shrinkage is indicated by a feeding criterion.
7. 결론:
주요 연구 결과 요약:
본 연구에서는 LPDC A356 알루미늄 합금 자동차 휠의 충격 거동을 조사했습니다. 주요 결과는 다음과 같습니다. T6 열처리는 충격 특성을 크게 향상시킵니다. 더 미세한 미세 구조는 충격 강도를 향상시킵니다. 주조 결함, 특히 응력 집중 지점 근처의 기공은 해롭습니다. 균열 전파는 덴드라이트 간 공정 영역을 따라 발생합니다. 수치 시뮬레이션은 응고 및 결함 형성을 효과적으로 예측합니다.
연구의 학문적 의의:
본 연구는 공정 변수(LPDC, 열처리), 미세 구조(SDAS, 공정정 실리콘), 주조 결함(기공) 및 A356 알루미늄 합금 휠의 충격 특성 간의 관계에 대한 더 깊은 이해에 기여합니다. 다이캐스팅 부품에서 원하는 기계적 성능을 달성하는 데 있어 미세 구조 제어 및 결함 최소화의 중요성을 강조합니다. 또한 본 연구는 수치 시뮬레이션이 다이캐스팅 공정 설계 및 최적화에서 예측 도구로서의 사용 가능성을 검증합니다.
실용적 의미:
본 연구 결과는 고성능 알루미늄 합금 휠 제조를 위한 LPDC 공정 및 열처리 최적화를 위한 실용적인 지침을 제공합니다. 특히 중요한 응력 영역에서 기공을 최소화하고 공정 제어를 통해 더 미세한 미세 구조를 달성하는 것이 충격 저항성을 향상시키는 데 중요합니다. 수치 시뮬레이션은 휠 제조에서 공정 설계, 결함 예측 및 품질 관리를 위한 귀중한 도구로 사용될 수 있습니다.
연구의 한계 및 향후 연구 분야:
본 연구는 A356 합금 및 특정 휠 설계로 제한됩니다. 향후 연구에서는 다음 사항을 탐구할 수 있습니다.
- 다른 알루미늄 합금 및 휠 설계의 충격 거동.
- 충격 특성에 대한 다양한 T6 열처리 변수의 영향.
- 특정 유형 및 분포의 주조 결함의 영향에 대한 상세 분석.
- LPDC 휠의 피로 성능과 미세 구조 및 주조 결함의 상관관계.
- 보다 정확한 결함 예측 및 공정 최적화를 위한 고급 수치 시뮬레이션 기술의 적용.
8. 참고 문헌:
- Berto, F., Lazzarin, P., Wang, C.H., 2004. Three-dimensional linear elastic distributions of stress and strain energy density ahead of V-shaped notches in plates of arbitrary thickness. Int. J. Fract. 127, 265-282.
- Blackmun, E.V., 1968. Casting. In: Kent, R., Van Horn (Eds.), Aluminum Vol. III—Fabrication and Finishing, 3rd ed. American Society for Metals, Metals Park, OH, pp. 43–80.
- Bonollo, F., Gramegna, N., Odorizzi, S., 1999. La pressocolata delle leghe di alluminio: simulazione numerica del processo, 1st ed. Edimet, Brescia.
- Brown, R., 1999. Foseco Non-Ferrous Foundryman's Handbook, 11th ed. Butterworth-Heinemann, Oxford.
- Cáceres, C.H., Davidson, C.J., Griffiths, J.R., 1995. The deformation and fracture behaviour of an Al-Si-Mg casting alloy. Mater. Sci. Eng. A 197, 171–179.
- Cáceres, C.H., Selling, B.I., 1996. Casting defects and the tensile properties of an Al-Si-Mg alloy. Mater. Sci. Eng. A 220, 109-116.
- Campbell, J., 2003. Castings, 2nd ed. Elsevier/Butterworth-Heinemann, Oxford.
- Flinn, R.A., 1963. Fundamentals of Metal Casting, 1st ed. Addison-Wesley Publishing Company, Massachusetts.
- Kuo, J.-H., Hsu, F.-L., Hwang, W.-S., 2001. Development of an interactive simulation system for the determination of the pressure-time relationship during the filling in a low pressure casting process. Sci. Technol. Adv. Mater. 2, 131-145.
- Kurz, W., Fisher, D.J., 1998. Fundamentals of Solidification, 4th ed. Trans. Tech. Publications, Switzerland.
- Li, Z., Samuel, A.M., Samuel, F.H., Ravindran, C., Doty, H.W., Valtierra, S., 2004. Parameters controlling the performance of AA319-type alloys. Part II. Impact properties and fractography. Mater. Sci. Eng. A 367, 111-122.
- MAGMASOFT® v.4.2, 2002. MAGMAlpdc Module Manual, MAGMA Giessereitechnologie GmbH.
- Murali, S., Raman, K.S., Murthy, K.S.S., 1992. Effect of magnesium, iron (impurity) and solidification rates on the fracture toughness of Al-7Si-0.3Mg casting alloy. Mater. Sci. Eng. A 151, 1-10.
- Paray, F., Kulunk, B., Gruzleski, J.E., 2000. Impact properties of Al-Si foundry alloys. Int. J. Cast Met. Res. 13, 17-37.
- Pedersen, L., 1999. Solution Heat Treatment of AlSiMg Foundry Alloys. PhD Thesis. Norwegian University of Science and Technology (NTNU), Trondheim.
- Schroth, A., Schemme, D., 2003. Simulation in modern quality management systems-simulation assists the implementation of quality management systems in foundries. Cast. Plant Technol. 19, 8-18.
- Shivkumar, S., Wang, L., Keller, C., 1994. Impact properties of A356-T6 alloys. J. Mater. Eng. Perform. 3, 83-90.
- Sicha, W.E., 1971. Properties of commercial casting alloys. In: Kent, R., Van Horn (Eds.), Aluminum Vol. I-Properties, Physical Metallurgy and Phase Diagram, 4th ed. American Society for Metals, Metals Park, OH, pp. 277-302.
- Srivastava, M.C., Lohne, O., Arnberg, L., Laukli, H.I., Gjestland, H., 2006. Energy absorption of HPDC aluminium and magnesium alloys. In: Proc. High Tech Die Casting 2006, Vicenza, Italy, paper 10.
- Street, A.C., 1986. The Diecasting Book, 2nd ed. Portcullis Press, London.
- Vedani, M., Mapelli, C., 2001. Effect of thermal treatments on microstructure and impact toughness of die-cast Mg-Al-Mn alloys. Mater. Sci. Technol. 17, 938-944.
- Wang, Q.G., Cáceres, C.H., 1998. The fracture mode in Al-Si-Mg casting alloys. Mater. Sci. Eng. A 241, 72-82.
- Warmuzek, M., 2004. Aluminium-Silicon Casting Alloys: Atlas of Microfractographs, 1st ed. ASM International.
- Zhang, D.L., Zheng, L.H., StJohn, D.H., 2002. Effect of a short solution treatment time on microstructure and mechanical properties of modified Al-7 wt.% Si-0.3 wt.% Mg alloy. J. Light Met. 2, 27-36.
9. 저작권:
- 본 자료는 "Mattia Merlin, Giulio Timelli, Franco Bonollo, Gian Luca Garagnani"의 논문: "Impact behaviour of A356 alloy for low-pressure die casting automotive wheels"를 기반으로 합니다.
- 논문 출처: https://www.researchgate.net/publication/222707551
본 자료는 상기 논문을 요약한 것으로, 상업적 목적으로 무단 사용하는 것을 금지합니다.
Copyright © 2025 CASTMAN. All rights reserved.