본 논문 요약은 ['Springer-Verlag London Limited']에서 발행한 ['Magnesium and its alloys applications in automotive industry'] 논문을 기반으로 작성되었습니다.
1. 개요:
- 제목: 자동차 산업에서의 마그네슘 및 마그네슘 합금 응용 (Magnesium and its alloys applications in automotive industry)
- 저자: 무스타파 케말 쿨렉치 (Mustafa Kemal Kulekci)
- 발행 연도: 2008년
- 발행 학술지/학회: 국제 첨단 제조 기술 저널 (International Journal of Advanced Manufacturing Technology)
- 키워드: 마그네슘, Mg 부품, Mg 응용, 자동차 산업, 운송, 연비 (Magnesium, Mg components, Mg applications, Automotive industry, Transportation, Fuel economy)
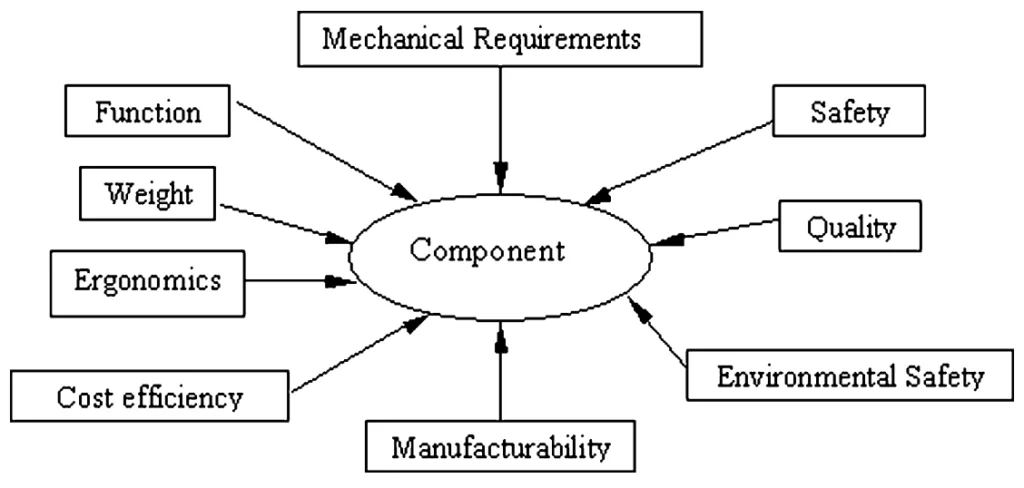
2. 초록 또는 서론
본 연구의 목적은 자동차 산업에서 마그네슘의 응용 분야를 검토하고 평가하는 것이며, 이는 연비 향상과 환경 보존에 크게 기여할 수 있습니다. 본 연구에서는 자동차 산업에서 Mg 합금의 현재 장점, 한계, 기술적 장벽 및 미래 전망을 제시합니다. 또한 자동차 응용 분야에서 마그네슘 사용이 환경 보존에 미치는 영향도 평가합니다. Mg 합금의 내크리프성 및 내식성을 향상시키기 위한 최근 코팅 및 합금화 개발은 고온 및 부식 환경에 대한 내용으로 다룹니다. 연구 결과는 합리적인 가격과 Mg 및 Mg 합금의 개선된 특성이 마그네슘의 대규모 사용으로 이어질 것이라는 결론을 내립니다. 대체 재료를 사용하는 것과 비교하여 Mg 합금을 사용하면 22%에서 70%의 무게 감소 효과를 얻을 수 있습니다. 마지막으로, Mg 합금의 성형 공정에 대한 지식이 증가함에 따라 자동차 부품에서 마그네슘 사용이 증가하고 있습니다.
3. 연구 배경:
연구 주제 배경:
자동차 산업은 더 가볍고, 환경 친화적이며, 안전하고 저렴한 자동차를 제조하려는 세계적인 추세에 의해 주도되고 있습니다 [4]. 주요 자동차 제조업체는 차량 무게 감축과 더 안전하고 깨끗한 차량에 대한 법적 및 소비자 요구 사항으로 인해 배기가스 배출량 제한에 집중하고 있습니다 [7]. CO2 배출량은 연료 소비량에 직접적으로 비례하므로 차량 무게는 설계 효율성 평가의 가장 중요한 기준이 되었습니다 [11]. 무게 감축은 에너지 절약뿐만 아니라 온실 가스 배출량 감소에도 기여합니다.
기존 연구 현황:
자동차 제조 회사들은 Mg 및 Mg 합금에 대한 연구 개발에 상당한 투자를 해왔습니다. 폭스바겐은 자동차 산업에 마그네슘을 처음으로 적용한 회사로, Beetle 모델에 마그네슘을 사용했습니다 [7]. 포르쉐는 1928년에 마그네슘 엔진을 처음 연구했습니다 [8]. 과거에는 일부 자동차 부품에 알루미늄과 일부 플라스틱이 선호되는 재료로 사용되었습니다. 그러나 최근 몇 년 동안 자동차 부문에서 마그네슘 응용 분야가 증가하고 있습니다 [9]. 현재 연구 개발 노력은 무게 감축, 에너지 절약 및 환경 영향 제한에 초점을 맞추고 있습니다 [10].
연구의 필요성:
환경 보존은 Mg 및 Mg 합금에 대한 관심의 주요 원인 중 하나입니다. 환경 보존은 운송 산업, 특히 운송 차량에서 발생하는 CO2 배출량에 크게 좌우됩니다 [16]. 무게 감축은 연료 소비와 CO2 배출량을 크게 줄이는 가장 비용 효율적인 방법입니다 [9, 16]. 유럽과 북미 자동차 제조업체는 2010년까지 연료 소비를 25% 줄여 CO2 배출량을 30% 감축하는 것을 목표로 계획하고 있습니다 [9, 16, 17]. 최근 20년 동안 마그네슘 소비가 광범위하게 증가했지만, 여전히 대부분의 마그네슘은 알루미늄 합금에 사용되고 있으며, 마그네슘 부품에 직접 사용되는 비율은 약 34%에 불과합니다 [4, 19]. 높은 비용은 자동차 산업에서 마그네슘 사용 확대를 가로막는 주요 장애물이며, 완제품의 가격 경쟁력이 확보되어야 합니다.
4. 연구 목적 및 연구 질문:
연구 목적:
본 연구는 최근 개발 동향에 발맞춰 연비와 환경 보존에 크게 기여할 수 있는 자동차 산업에서의 마그네슘 및 마그네슘 합금의 과학, 기술 및 응용 분야를 검토하는 것을 목표로 합니다. 또한 Mg 합금의 자동차 산업 활용에 대한 현재의 장점, 한계, 기술적 장벽 및 미래 전망을 조사하고자 합니다.
핵심 연구 질문:
본 연구에서 탐구하는 핵심 연구 질문은 다음과 같습니다.
- 자동차 산업에서 마그네슘 응용 분야는 무엇인가?
- 마그네슘 사용의 장점, 한계 및 기술적 장벽은 무엇인가?
- 자동차 응용 분야에서 마그네슘 합금의 미래 전망은 어떠한가?
- 자동차 부품에서 마그네슘 사용이 환경 보존에 미치는 영향은 무엇인가?
- 재료 특성을 개선하기 위한 마그네슘 코팅 및 합금화의 최근 개발 동향은 무엇인가?
연구 가설:
본 논문에서는 명시적인 연구 가설을 제시하지 않습니다. 그러나 암묵적으로 다음과 같은 전제하에 연구가 진행됩니다.
- 자동차 부품에 마그네슘 합금 사용을 늘리면 차량 무게가 크게 감소하고 연비가 향상될 것이다.
- 비용 및 재료 특성과 관련된 한계를 극복하면 자동차 산업에서 마그네슘의 대규모 채택이 가능해질 것이다.
- 마그네슘 합금 가공 및 코팅 기술의 발전은 마그네슘 응용 분야 확장에 매우 중요하다.
5. 연구 방법론
연구 설계:
본 연구는 문헌 검토 기반 연구 설계를 채택합니다. 기존 문헌 및 연구 결과를 종합하여 자동차 산업에서 마그네슘 응용 분야에 대한 포괄적인 개요를 제공합니다.
자료 수집 방법:
자료 수집 방법은 마그네슘 합금 및 자동차 공학 분야에서의 응용과 관련된 출판된 논문, 보고서 및 산업 데이터를 문헌 검토하는 방식으로 이루어집니다.
분석 방법:
분석 방법은 수집된 문헌에 대한 기술적 종합 및 평가를 포함하는 질적 분석입니다. 본 논문은 검토된 자료를 바탕으로 차량 내 마그네슘 사용과 관련된 추세, 과제 및 기회를 분석합니다.
연구 대상 및 범위:
본 연구는 자동차 산업 맥락 내에서 마그네슘 및 마그네슘 합금에 초점을 맞춥니다. 연구 범위는 다음을 포함합니다.
- 자동차 응용 분야와 관련된 마그네슘 합금의 재료 특성.
- 마그네슘 부품 가공 기술.
- 다양한 자동차 부품에서의 마그네슘 응용.
- 비용, 성능 및 환경적 고려 사항과 같은 마그네슘 채택에 영향을 미치는 요인.
6. 주요 연구 결과:
핵심 연구 결과:
- 마그네슘 합금은 자동차 부품에서 대체 재료에 비해 22%에서 70%의 무게 감소 효과를 제공합니다.
- 마그네슘의 비강도는 알루미늄 및 철보다 훨씬 높지만, 비강성은 유사합니다 (그림 4).
- 마그네슘 합금 비용은 2004년 이후 알루미늄 대비 상대적으로 감소했습니다 (그림 3).
- AE42 및 Mg-Al-Sr 시스템과 같은 새로운 마그네슘 합금은 향상된 내크리프성을 나타냅니다 (그림 5, 그림 6).
- 알루미늄 증착으로 얻은 테프론 수지 코팅은 마그네슘 합금에 저비용, 크롬 프리 내식성 코팅을 제공합니다 (그림 7).
- 다이캐스팅은 마그네슘 자동차 부품의 주요 제조 방법입니다.
- Mg 합금으로 제작된 자동차 부품 및 얻어진 무게 감소 효과는 그림 8에 나와 있습니다.
- Mg 합금으로 제작된 자동차 부품의 예는 그림 9에 나와 있습니다.
- VW의 마그네슘 기술 개발 전략은 그림 11에 나와 있습니다.
제시된 데이터 분석:
- 그림 1: 기능, 무게, 인체 공학, 비용 효율성, 제조 가능성, 안전, 품질 및 환경 안전을 포함한 차량 부품에 대한 기본 요구 사항을 보여줍니다 [1].
- 그림 2: 차량 무게와 연료 소비량 간의 관계를 보여주며, 차량 무게 감소가 연비 향상으로 이어진다는 것을 입증합니다 [5].
- 그림 3: 마그네슘 및 알루미늄 가격 변화를 보여주며, 2004년 이후 알루미늄 대비 마그네슘 가격 하락을 나타냅니다 [20].
- 그림 4: 마그네슘, 알루미늄 및 철의 기본 구조적 특성을 비교하여 마그네슘의 우수한 비강도를 강조합니다 [1].
- 그림 5: 다이캐스팅 Mg 합금의 크리프 변형을 비교하여 AZ91D에 비해 AE42 및 Mg-Al-Sr 합금에서 향상된 내크리프성을 보여줍니다 [31].
- 그림 6: 135°C, 85 MPa 응력 하에서 AZ91 및 AE42 합금과 비교하여 새로운 합금의 내크리프성을 보여줍니다 [17].
- 그림 7: 테프론 수지 코팅의 단면도를 개략적으로 보여줍니다 [34].
- 그림 8: Mg 합금으로 제작된 일부 자동차 부품과 얻어진 무게 감소 효과를 보여줍니다.
- 그림 9: Mg 합금으로 제작된 자동차 부품의 예를 제공합니다.
- 그림 10: 북미 자동차 마그네슘 사용량을 보여줍니다 [15].
- 그림 11: VW의 마그네슘 기술 개발 전략을 보여줍니다 [7].
그림 목록:
![Fig. 2 The relation between vehicle mass and fuel consumption [5]](https://castman.co.kr/wp-content/uploads/image-775-png.webp)
![Fig. 3 Changes in the prices of magnesium and aluminium [20]](https://castman.co.kr/wp-content/uploads/image-776-1024x384.webp)
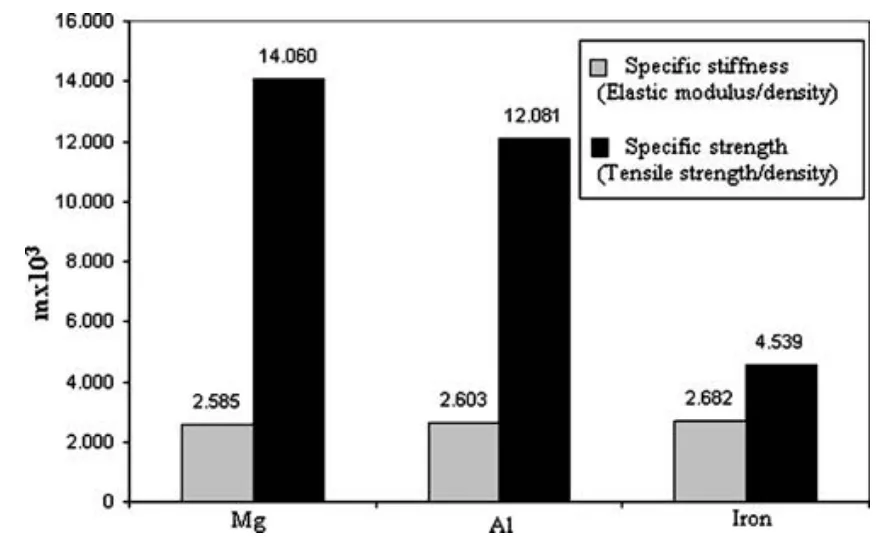
![Fig. 5 Comparison at creep deformation of die-cast Mg-alloys
(35 MPa, 150°C, 200 h) [31]](https://castman.co.kr/wp-content/uploads/image-778-png.webp)
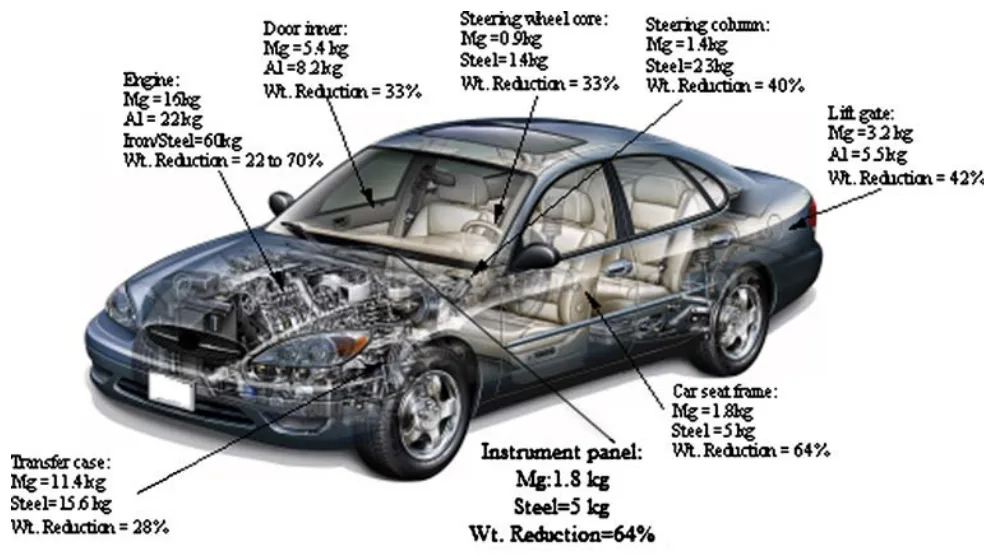
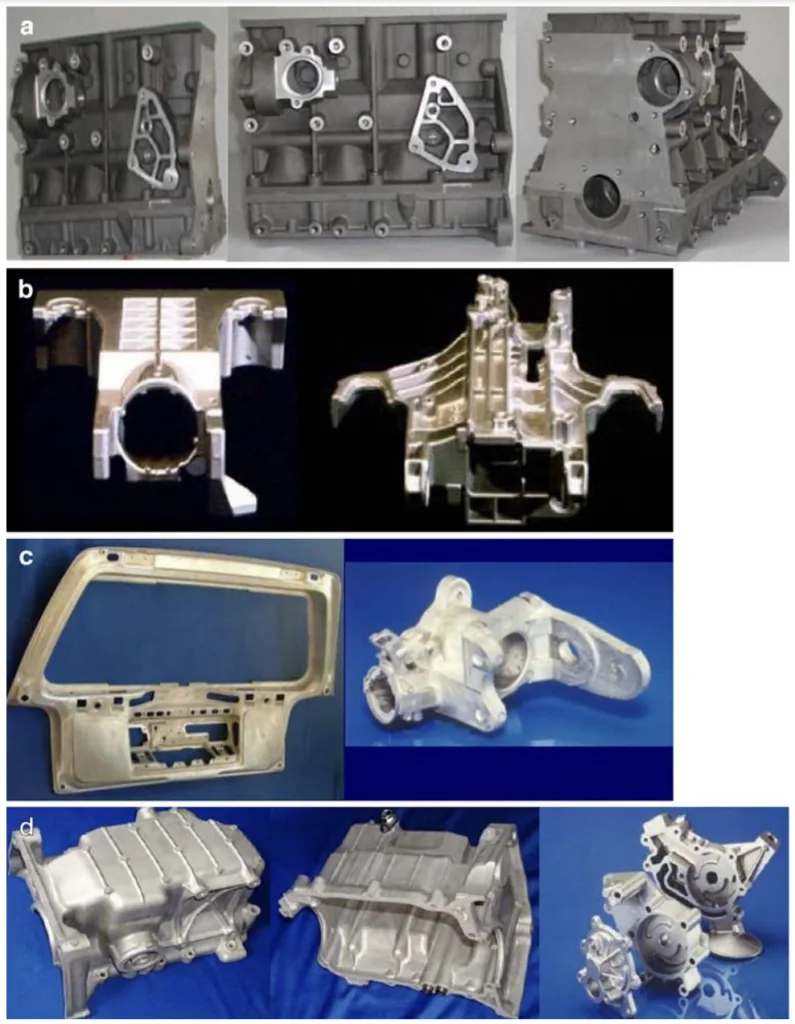
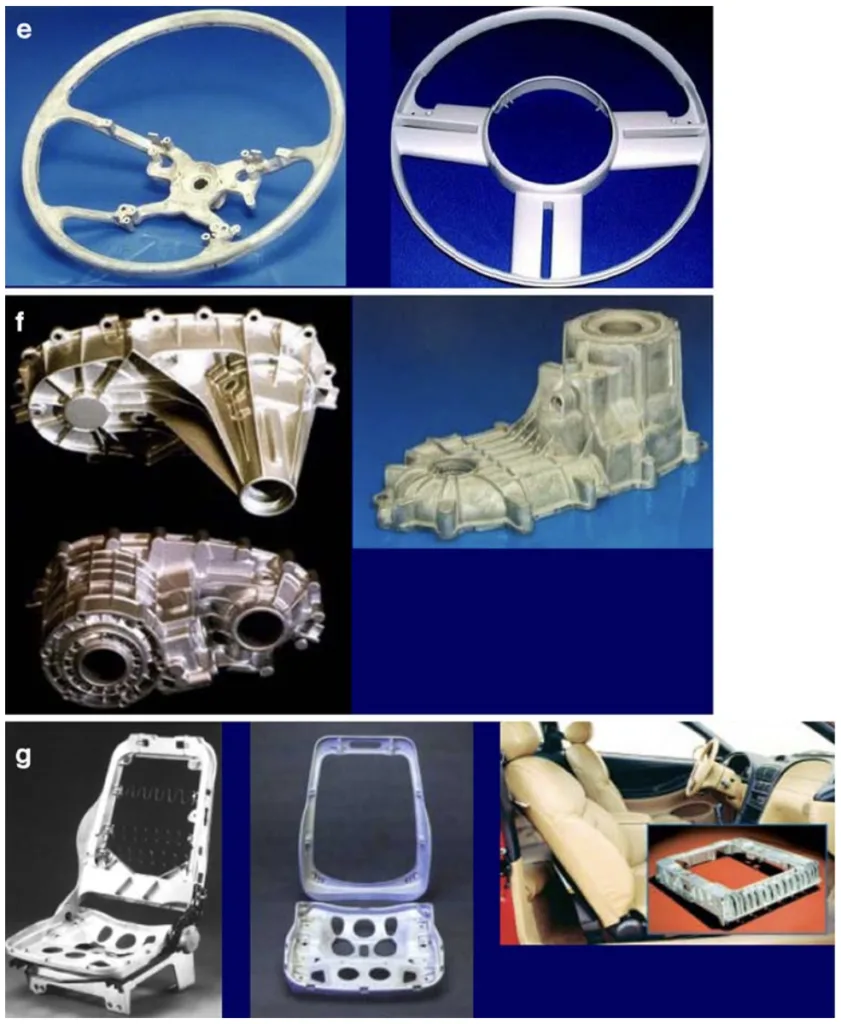
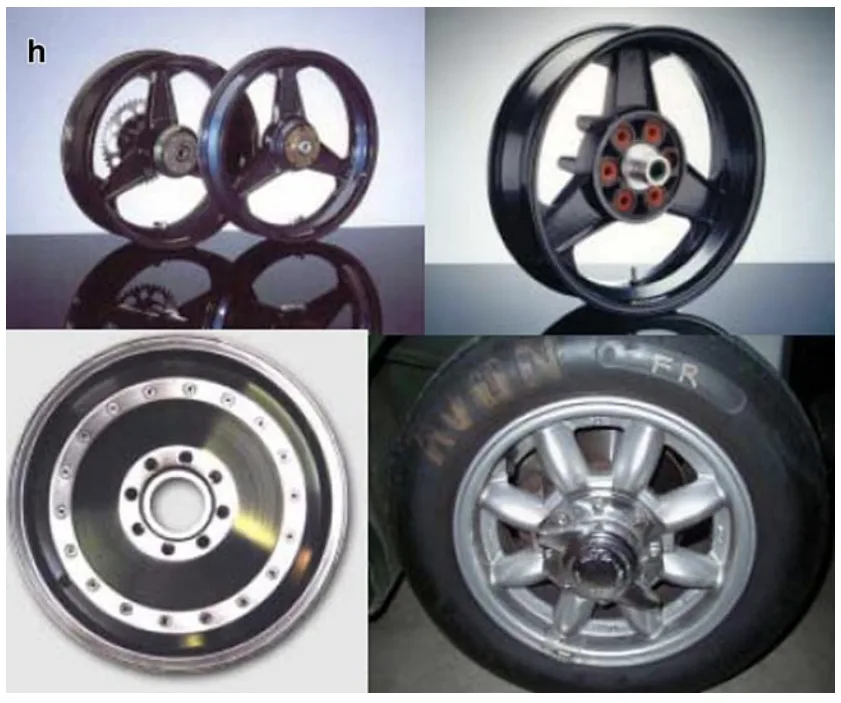
![Fig. 10 North American automotive magnesium usage [15]](https://castman.co.kr/wp-content/uploads/image-783-png.webp)
![Fig. 11 VW strategy of magnesium technology development [7]](https://castman.co.kr/wp-content/uploads/image-784-png.webp)
- 그림 1. 차량 부품에 대한 기본 요구 사항 [1]
- 그림 2. 차량 무게와 연료 소비량 간의 관계 [5]
- 그림 3. 마그네슘 및 알루미늄 가격 변화 [20]
- 그림 4. 마그네슘과 Al 및 철의 기본 구조적 특성 비교
- 그림 5. 다이캐스팅 Mg 합금의 크리프 변형 비교 (35 MPa, 150°C, 200시간) [31]
- 그림 6. 135°C, 85 MPa 응력 하에서 AZ91 및 AE42 합금과 비교한 새로운 합금의 내크리프성: (1) AZ91; (2) AE42; (3) MRI 155; (4) MRI 153; (5) MRI 154; (6) MRI 151; (7) MRI 152 [17]
- 그림 7. 테프론 수지 코팅의 단면 개략도 [34]
- 그림 8. Mg 합금으로 제작된 일부 자동차 부품 및 얻어진 무게 감소 효과
- 그림 9. Mg 합금으로 제작된 자동차 부품의 예 (a: 엔진 블록, b: 스티어링 컬럼 모듈, c: 도어 프레임/키 잠금 장치 하우징, d: 오일 팬, e: 스티어링 휠, f: 트랜스퍼 케이스/변속기 하우징, g: 시트 프레임, h: 휠)
- 그림 10. 북미 자동차 마그네슘 사용량 [15]
- 그림 11. VW 마그네슘 기술 개발 전략 [7]
7. 결론:
주요 연구 결과 요약:
본 연구는 마그네슘 합금이 자동차 응용 분야에서 무게 감축에 상당한 잠재력을 제공하여 연비 향상과 CO2 배출량 감소에 기여한다는 결론을 내립니다. 주요 연구 결과로는 마그네슘의 우수한 비강도, 비용 감소 추세, 그리고 크리프 및 내식성과 같은 한계를 해결하는 합금 개발 및 코팅 기술의 발전이 있습니다. 다이캐스팅은 여전히 주요 제조 공정으로 남아 있지만, 마그네슘 사용 확대를 위해서는 성형 공정에 대한 추가 연구가 필요합니다. 마그네슘은 반응성 및 갈바닉 부식과 같은 문제에 직면하지만, 이러한 문제는 설계 및 보호 조치를 통해 완화할 수 있습니다.
연구의 학문적 의의:
본 논문은 자동차 산업 내 마그네슘 합금 응용 분야의 최신 기술에 대한 포괄적인 개요를 제공합니다. 다양한 연구 결과를 통합하여 재료의 잠재력, 한계 및 미래 방향에 대한 귀중한 통찰력을 제공합니다. 본 논문은 재료 과학, 자동차 공학 및 제조 기술 분야의 전문가 및 연구자를 위한 핸드북 수준의 자료 역할을 합니다.
실용적 의미:
본 연구의 실용적 의미는 자동차 산업에 매우 중요합니다. 연구 결과는 연비 및 환경 규제에 대한 증가하는 요구 사항을 충족하기 위해 마그네슘 합금의 채택 확대를 뒷받침합니다. 본 논문은 비용 효율적인 합금화, 향상된 내식성 코팅 (예: 테프론 수지 코팅), 고급 성형 기술과 같이 기술 개발의 특정 영역을 강조하며, 이는 차량 제조에서 마그네슘의 더 넓고 효과적인 사용을 가능하게 할 수 있습니다.
연구의 한계 및 향후 연구 분야:
본 연구는 기존 문헌 검토에 국한되며 독창적인 실험 연구는 포함하지 않습니다. 향후 연구 분야는 다음과 같습니다.
- 특히 고온 파워트레인 응용 분야를 위한 내크리프성이 향상된 마그네슘 합금의 추가 개발.
- 특히 판재 및 압출 응용 분야에서 마그네슘의 육방정계 결정 구조로 인한 한계를 극복하기 위한 마그네슘 합금 성형 공정 최적화.
- 내식성을 개선하고 갈바닉 부식 문제를 해결하기 위한 비용 효율적이고 환경 친화적인 표면 처리 및 코팅에 대한 연구.
- 차량 내 마그네슘 합금 대체재의 환경적 이점을 완전히 정량화하기 위한 전과정 평가 (생산, 사용 및 재활용 단계 고려).
8. 참고 문헌:
- [1] Davies G (2003) Magnesium. Materials for automotive bodies, Elsevier, G. London, pp 91, 158, 159
- [2] Kuo JL, Sugiyama S, Hsiang SH, Yanagimoto J (2006) Investigating the characteristics of AZ61 Magnesium alloy on the hot and semi-solid compression test. Int J Adv Manuf Technol 29(7-8):670-677
- [3] Jain CC, Koo CH (2007) Creep and corrosion properties of the extruded magnesium alloy containing rare earth. Mater Trans 2:265-272
- [4] Blawert C, Hort N, Kainer KV (2004) Automotive applications of magnesium and its alloys. Trans Indian Inst Met 57(4):397-408
- [5] Eliezer D, Aghion E, Froes FH (1998) Magnesium science and technology. Adv Mat Performance 5:201-212
- [6] Aghion E, Bronfin B (2000) Magnesium alloys development towards the 21(st) century. Magnesium alloys 2000 Mat Sci Forum 350(3):19-28
- [7] Friedrich H, Schumann S (2001) Research for a "new age of magnesium" in the automotive industry. J Mater Process Technol 117:276-281
- [8] Schuman S (2005) The paths and strategies for increased magnesium application in vehicles. Mat Sci Forum 488-489:1-8
- [9] Dieringa H, Kainer KU (2007) Magnesium-der zukunftswerkstoff für die automobilindustrie. Mat-wiss U Werkstofftech 38(2):91-95
- [10] Tang B, Wang Xs, Li SS, Zeng DB, Wu R (2005) Effects of Ca combined with Sr additions on microstructure and mechanical properties of AZ91D. Mater Sci Technol 21(29):574-578
- [11] Michalek JJ, Papalambros PY, Skerlos SJ (2004) A study of fuel efficiency and emission policy impact on optimal vehicle design decisions. J Mech Des 126(6):1062-1070
- [12] Medraj M, Parvez A (2007) Analyse the importance of Magnesium-aluminium-strontium alloys for more fuel-efficient automobiles. Automotive 45-47
- [13] Aichinger HM (1996) Reduced fuel consumption through weight-saving in passenger vehicles-importance of steel as a lightweight material. Stahl Und Eisen 116(6):71
- [14] Kurihara Y (1994) The role of aluminum in automotive weight-reduction. 2. JOM J Miner Metals Mater Society 46(2):33-35
- [15] Das S (2003) Magnesium for automotive applications: primary production cost assessment. JOM J Miner Metals Mater Society 55(11):22-26
- 16 Emission control, Automotive World 4:10-15
- [17] Aghion E, Bronfin B, Eliezer D (2001) The role of the magnesium industry in protecting the environment. J Mater Process Technol 117(3):381-385
- 18 Annual Report. Int. Magnesium Association
- [19] Kammer C (2001) Magnesium Taschenbuch. Aluminium, Verlag, Germany p 1
- [20] Brown B (2007) Magnesium application in the short term. http://www.magnesium.com/W3/data-bank/article.php?mgw=199&magnesium-286
- [21] Commission of the European Communities (2007), Results of the review of the Community Strategy to reduce CO2 emissions from passenger cars and light-commercial vehicles, {SEC(2007) 60} {SEC(2007) 61}, COM(2007) 19 final
- [22] United Nations (February 2007), Kyoto protocol reference manual on accounting of emissions and assigned amounts
- [23] Price on Magnesium and Aluminium (2007) http://www.lightmetals.org/e/documents/LMTinretospect.pdf
- [24] Hakamada M, Furuta T, Chino Y, Chen Y, Kusuda H, Mabuchi M (2007) Life cycle inventory study on magnesium alloy substitution in vehicles. Energy 32(8):1352-1360
- [25] Fitch P, Cooper JS (2005) Life-cycle modeling for adaptive and variant design. Res Eng Design 15(4):216-228
- [26] Das S (2000) The life-cycle impacts of aluminum body-in-white automotive. JOM J Miner Metals Mater Society 50(8):41-44
- [27] Tkachenko VG, Maksimchuk IN, Volosevich PY, Lashuk NK, Malka AN, Friezel VV (2006) Creep resistance and long-term strength of structural magnesium alloys. High Temp Mater Proc 25(1-2):97-107
- [28] Pekguleryuz MO, Kaya AA (2003) Creep resistant magnesium alloys for powertrain applications. Adv Eng Mater 5(12):866-878
- [29] Baril E, Labelle P, Pekguleryuz MO (2003) Elevated temperature Mg-Al-Sr: Creep resistance, mechanical properties, and microstructure. Jom-Journal of the Minerals Metals & Materials Society 55(11):A34-A39
- [30] Aghion E, Bronfin B, Von Buch F, Schumann S, Friedrich H (2003) Newly developed magnesium alloys for powertrain applications. Jom-J Miner Metals Mater Society 55(11):A30-A33
- [31] Pekguleryuz MO, Baril E, Labelle P, Argo D (2003) Creep resistant Mg-Al-Sr alloys. J Adv Mater 35(3):32-38
- [32] Grieve DJ (2001) Magnesium Die Castings. http://www.tech.plym.ac.uk/sme/mech330/magcast.htm
- [33] Bavarian Motor Works (2007) Magnesium fosters rebirth of an automotive engine. International magnesium association: The global voice for magnesium (May):1-3
- [34] AIST (2007) New technology for increasing the application for magnesium alloys. http://www.aist.go.jp/aist_e/latest_research/2001/20011203/20011203.html
- [35] Robots 4 welding (2007) Welding magnesium. http://www.robots4welding.com/magnesium-welding-automation.htm
- [36] Kulekci MK, Şik A, Kaluç E (2007) Effects of tool rotation and pin diameter on fatigue properties of friction stir welded lap joints. Int J Adv Manuf Technol DOI 10.1007/s00170-006-0901-z
- [37] Chi CT, Chao CG (2007) Characterization on electron beam welds and parameters for AZ31B-F extrusive plates. J Mater Process Technol 182(1-3):369-373
- [38] Liu LM, Wang SX, Zhu ML (2006) Study on TIG welding of dissimilar Mg alloy and Cu with Fe as interlayer. Sci Technol Weld Join 11(5):523-525
- [39] Chang WS, Kim HJ, Noh JS, Bang HS (2006) The evaluation of weldability for AZ31B-H24 and AZ91C-F Mg alloys in friction stir welding. Key Eng Mater 321-323:1723-1728
- [40] Welding Magnesium (2007) http://www.robots4welding.com/magnesium-welding-automation.htm
- [41] Huang ZH, Guo XF, Zhang ZM (2006) Effects of alloying on microstructure and mechanical property of AZ91D magnesium alloy. Rare Met Mater Eng 35(3):363-366
- [42] Garmo EPD, Black JT, Kohser RA (1997) Magnesium and magnesium alloys. Materials and processes in manufacturing (8th Edition). Wiley, USA, pp 182-184
- [43] Novotny S, Geiger M (2003) Process design for hydroforming of lightweight metal sheets at elevated temperatures. J Mater Process Technol 138:594-599
- [44] Haferkamp H, Boehm R, Holzkamp U, Jaschik C, Kaese V, Niemeyer M (2001) Alloy development, processing and applications in magnesium lithium alloys. Mater Trans 42(7):1160–1166
- [45] Sreejith PS, Ngoi BKA (2000) Dry machining: machining of the future. J Mater Process Technol 101:287-291
- [46] ASM Handbook vol. 2, 1961, p. 1081
- [47] Report (2001) "Magnesium in the aerospace industry", NFPA: National fire protection association. Ref: ANM-112N-04-07, Rev.c.USA
- [48] Shi ZM, Song GL, Atrens A (2006) Influence of anodising current on the corrosion resistance of anodised AZ91D magnesium alloy. Corros Sci 48(8):1939-1959
- [49] Niu LY, Jiang ZH, Li GY, Gu CD, Lian JS (2006) A study and application of zinc phosphate coating on AZ91D magnesium alloy. Surf Coat Technol 200(9):3021-3026
- [50] Polmear IJ (1994) Magnesium alloys and applications. Mater Sci Technol 10(1):1-14
- [51] Magnesium Pure and Alloys, Norsk Hydro Report
- [52] Mg application in automotive industry (2007) http://www.avisma.ru/mg/eng/03-2.htm
9. 저작권:
- 본 자료는 무스타파 케말 쿨렉치 (Mustafa Kemal Kulekci)의 논문 "자동차 산업에서의 마그네슘 및 마그네슘 합금 응용 (Magnesium and its alloys applications in automotive industry)"을 기반으로 합니다.
- 논문 출처: DOI 10.1007/s00170-007-1279-2
본 자료는 상기 논문을 요약한 것으로, 상업적 목적으로 무단 사용하는 것을 금지합니다.
Copyright © 2025 CASTMAN. All rights reserved.