본 논문 요약은 Celal Bayar University Journal of Science에 발표된 논문 "Development of Salt Core Use as an Alternative in Aluminum Alloy Castings"을 기반으로 작성되었습니다.
1. 개요:
- 제목: 알루미늄 합금 주조에서 대체재로서의 솔트 코어 사용 개발 (Development of Salt Core Use as an Alternative in Aluminum Alloy Castings)
- 저자: 튤라이 한체르리오글루 (Tülay Hançerlioğlu)
- 발행 연도: 2022년
- 발행 저널/학회: Celal Bayar University Journal of Science
- 키워드: 코어 가스, 모래 코어, 솔트 코어 (Core gas, sand core, salt core)
2. 연구 배경:
- 연구 주제의 사회적/학문적 맥락: 자동차 산업은 주조 부품에서 점점 더 복잡한 형상을 요구하고 있습니다. 강철 코어가 복잡한 설계 및 주조 품질에 충분하지 않은 경우가 있는 반면, 모래 코어는 일반적으로 복잡한 구조와 내부 공동을 가진 부품 생산에 사용됩니다. 그러나 모래 코어는 어려움을 야기합니다. 솔트 코어 기술은 특히 중력 및 저압 다이캐스팅 분야에서 20세기 말부터 잠재적인 대안으로 부상했습니다.
- 기존 연구의 한계: 기존의 모래 코어 방법은 콜드 박스 또는 핫 박스 공정에서 수지 바인더를 사용하여 주조 중 코어 가스 발생을 유발할 수 있습니다. 또한 모래 코어 제거는 종종 에너지 집약적이고 소음과 먼지를 발생시키는 기계적 충격 및 진동을 포함하여 환경 및 건강 문제를 야기합니다. 기존 연구에서는 솔트 코어의 강점과 고압 주조에서 환경에 미치는 긍정적인 영향을 인정하지만, 실제 적용 및 특정 주조 시나리오에서의 상세 성능에 대한 추가 조사가 필요합니다.
- 연구의 필요성: 본 연구는 알루미늄 합금 주조에서 모래 코어의 실행 가능한 대체재로서 솔트 코어의 사용을 탐구하고 검증할 필요성을 다룹니다. 이 연구는 개선된 기계적 특성, 더 쉽고 깨끗한 제거, 폐기물 감소, 보다 환경 친화적인 주조 공정을 포함하여 솔트 코어의 잠재적 이점에 중점을 둡니다.
3. 연구 목적 및 연구 질문:
- 연구 목적: 본 연구의 주요 목적은 알루미늄 합금 주조 생산에서 기존 모래 코어의 대안으로서 솔트 코어의 개발 및 적용을 조사하는 것입니다.
- 주요 연구 질문: 명시적으로 질문으로 진술되지는 않았지만, 연구는 암묵적으로 다음 질문에 답하고자 합니다.
- 솔트 코어는 복잡한 형상의 알루미늄 합금 주조 생산에서 모래 코어를 효과적으로 대체할 수 있는가?
- 코어 가스 감소, 제거 효율, 주조 표면 품질 및 환경 영향 측면에서 솔트 코어는 모래 코어보다 어떤 장점이 있는가?
- 솔트 코어 생산 및 주조와 관련된 중요한 공정 매개변수 및 과제는 무엇이며, 어떻게 최적화할 수 있는가?
- 연구 가설: 근본적인 가설은 솔트 코어가 알루미늄 합금 주조에서 모래 코어보다 상당한 이점을 제공하며, 특히 코어 가스 결함을 줄이고, 물 용해를 사용하여 더 쉽고 잔류물이 없는 코어 제거를 가능하게 하며, 환경 영향을 최소화한다는 것입니다.
4. 연구 방법론:
- 연구 설계: 본 연구는 펌프 본체 부품 주조를 사용한 사례 연구에 초점을 맞춘 실험적 연구 설계를 채택합니다.
- 데이터 수집 방법:
- 주조 시험: 솔트 코어를 사용하여 펌프 본체 부품을 생산하기 위해 중력 금형 기울기 주조 방법을 사용하여 실험을 수행했습니다.
- 솔트 코어 생산: 솔트 코어는 용융 염(NaCl)을 사용한 사출 성형 방법으로 제조되었습니다.
- 치수 측정: Faro Edge Scan Arm HD를 사용한 레이저 스캔과 3D 데이터 모델과의 비교를 통해 솔트 코어의 치수 정확도 및 수축률을 평가했습니다.
- 표면 거칠기 측정: 솔트 코어와 모래 코어로 생산된 주물의 표면 거칠기를 측정하고 비교했습니다.
- 육안 검사 및 단면 분석: 주조 부품을 육안으로 검사하여 결함을 확인하고, 단면을 연마 후 분석하여 내부 품질 및 코어 제거 효율성을 조사했습니다.
- 분석 방법: 본 연구는 솔트 코어 주조와 기존 모래 코어 주조를 비교 분석했습니다. 질적 평가는 육안 검사를 통해 이루어졌으며, 양적 데이터는 치수 및 표면 거칠기 측정에서 얻었습니다. 이 연구는 실제 주조 시나리오에서 솔트 코어 사용의 타당성, 장점 및 과제를 평가하는 데 중점을 두었습니다.
- 연구 대상 및 범위: 본 연구는 알루미늄 합금으로 만든 펌프 본체 부품 생산에 초점을 맞추었습니다. 사용된 솔트 코어 재료는 NaCl이었습니다. 시험은 네막 이즈미르 도쿰 사.A.Ş.(Nemak İzmir Döküm San.A.Ş.)의 산업 환경 내에서 시설과 전문 지식을 활용하여 수행되었습니다.
5. 주요 연구 결과:
- 주요 연구 결과:
- 코어 가스 감소: 솔트 코어 사용은 수지 연소로 인해 가스가 발생하고 금형의 에어 필터를 막는 모래 코어에서 관찰된 코어 가스 문제를 제거했습니다. 솔트 코어 주조 후 수지 스택 또는 에어 필터 막힘이 관찰되지 않았습니다.
- 효율적인 코어 제거: 솔트 코어는 짧은 시간 안에 물에 용해시켜 쉽고 완벽하게 제거되었으며, 주조 부품에 잔류물이 남지 않았습니다. 용해된 염은 물에서 재활용될 가능성이 있습니다.
- 향상된 표면 품질: 표면 거칠기 측정 결과 솔트 코어로 생산된 주물이 모래 코어로 만든 주물보다 더 매끄러운 표면 마감을 나타냈습니다.
- 솔트 코어 주조 거칠기: Rz = 17.86 µm, Ra = 2.51 μm, Rmax = 34.63 µm (그림 8).
- 모래 코어 (60 AFS) 주조 거칠기: Rz = 60.9 µm, Ra = 11.4 µm, Rmax = 86.2 µm (그림 8.1).
- 중요 공정 매개변수: 솔트 코어 생산 중 수축률 제어 및 냉각이 중요한 매개변수로 확인되었습니다. 온도 변화는 표면 품질, 스케일 및 코어 강도에 상당한 영향을 미쳤습니다. 균열을 방지하고 균질한 응고를 보장하려면 최적화된 냉각 채널 및 매개변수가 필요했습니다.
- 통계적/질적 분석 결과: 양적 거칠기 측정은 솔트 코어에서 더 매끄러운 표면이라는 질적 관찰을 확인했습니다. 주조 부품의 육안 검사 결과 성공적인 코어 제거와 코어 가스 또는 잔류물과 관련된 심각한 결함이 없는 것으로 나타났습니다.
- 데이터 해석: 결과는 솔트 코어가 테스트된 알루미늄 합금 펌프 본체 부품에 대해 모래 코어에 비해 코어 가스 결함 감소, 단순화되고 깨끗한 코어 제거, 향상된 주조 표면 마감 측면에서 상당한 이점을 제공함을 나타냅니다. 그러나 성공적인 솔트 코어 생산을 위해서는 냉각 및 수축률에 대한 정밀한 제어가 필수적입니다.
- 그림 목록:
- 그림 1. 펌프 본체의 단면도.
- 그림 2.1. 솔트 코어 제조용 이동측 사출 금형.
- 그림 2.2. 솔트 코어 제조용 고정측 사출 금형.
- 그림 3. 솔트 코어 사출 성형.
- 그림 4. 3D 데이터 모델과 비교한 솔트 코어 레이저 스캔.
- 그림 5. 솔트 코어 외부 표면 균열.
- 그림 6. 육안으로 보이는 솔트 코어 내부 직경 표면 균열.
- 그림 7. 금형 내부 직경 코어 삽입.
- 그림 8. 솔트 코어를 사용한 주조 부품의 거칠기 값 측정.
- 그림 8.1. 60 AFS 모래 코어를 사용한 주조 부품의 거칠기 값 측정.
- 그림 9. 솔트 코어 내부 모습.
- 그림 10.1. 저온 및 단시간에 생산된 솔트 코어.
- 그림 10.2. 고온 및 장시간에 생산된 솔트 코어.
- 그림 11.1. 틸트 주조기.
- 그림 11.2. 틸트 주조 국자.
- 그림 11.3. 틸트 주조기는 180도 회전합니다.
- 그림 12. 주조 금형에서 나온 솔트 코어가 있는 주조 부품.
- 그림 13. 용해되기 시작하는 염, 코어 및 주조 부품.
- 그림 14. 주조 부품 단면.
- 그림 15. 연마된 주조 부품 단면.
- 그림 16. 주조 부품 확대 이미지.
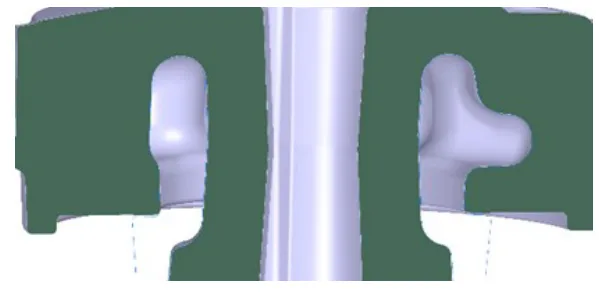
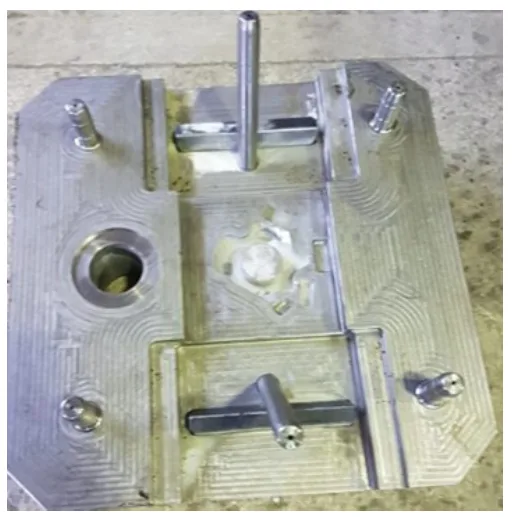
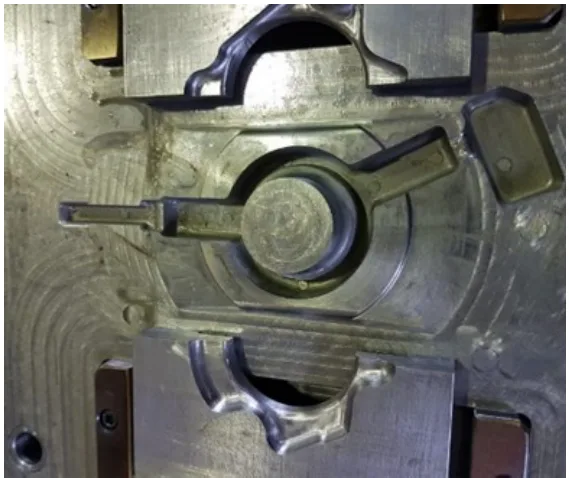
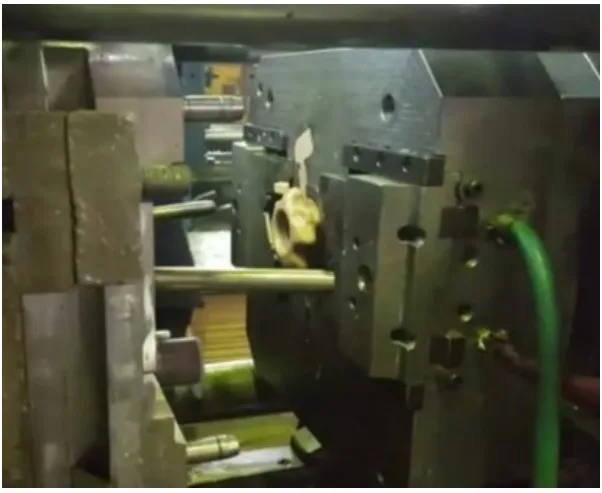
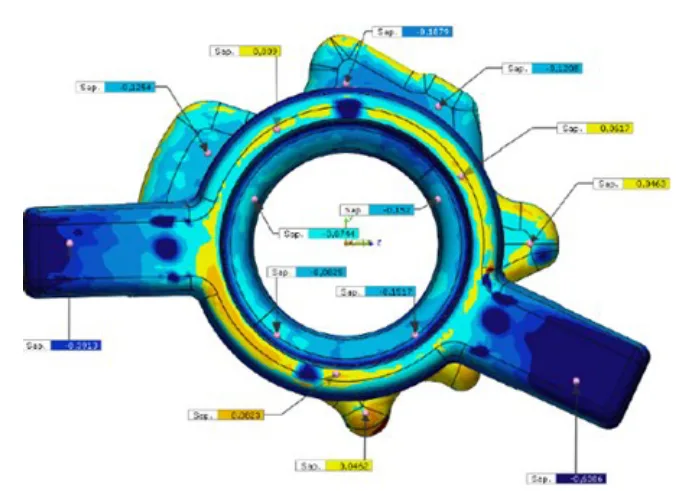
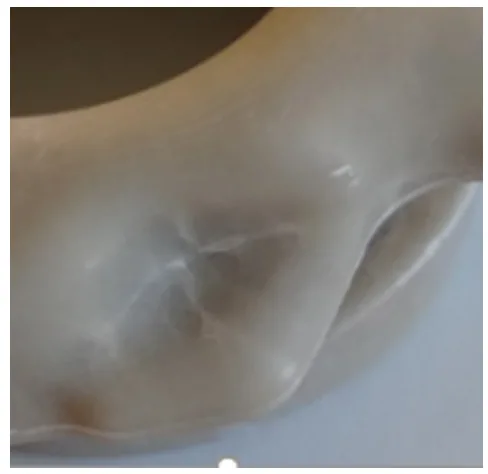
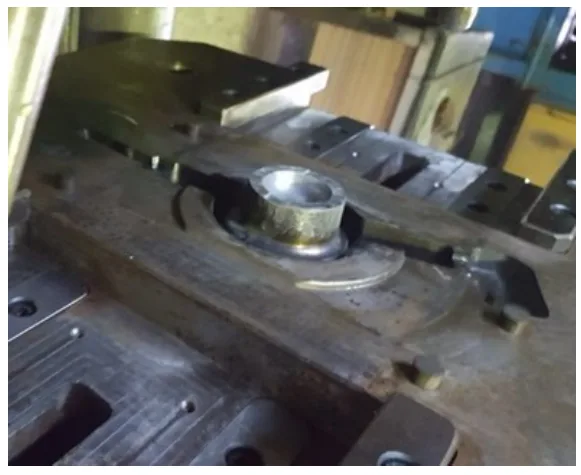
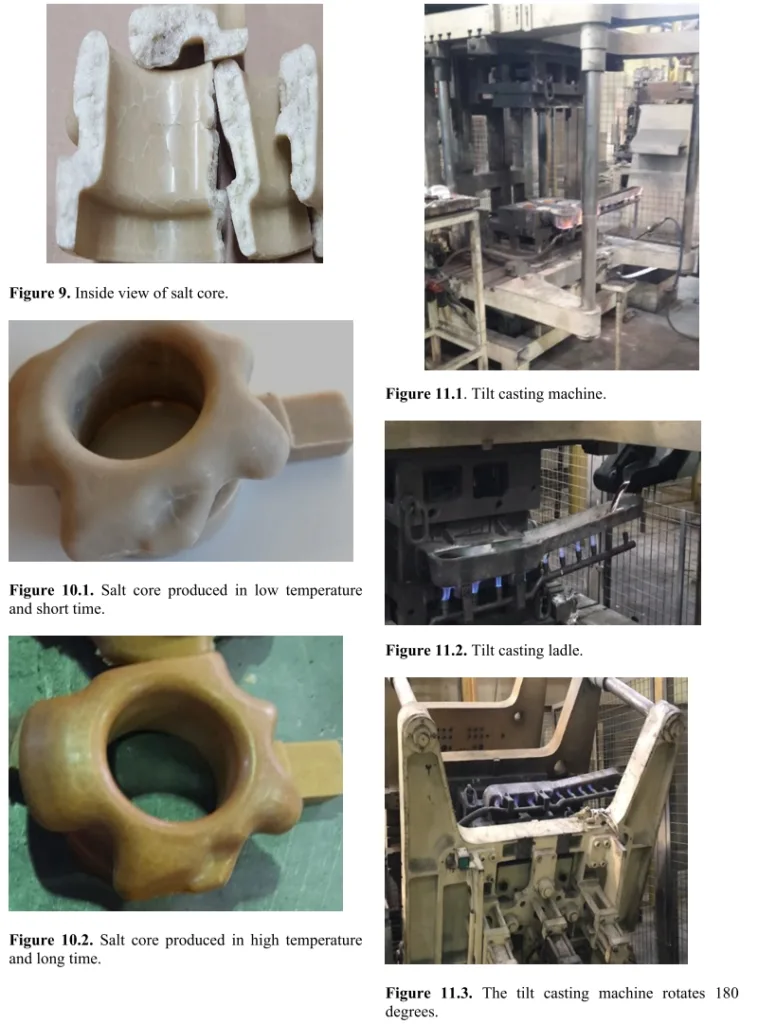
6. 결론 및 논의:
- 주요 결과 요약: 본 연구는 솔트 코어 주조가 복잡한 알루미늄 합금 부품 생산에 모래 코어 주조의 유망한 대안임을 입증합니다. 코어 가스 문제를 효과적으로 해결하고, 잔류물 없이 물 용해를 통해 코어 제거를 단순화하며, 주조 표면 마감을 향상시키고, 기계적 코어 제거와 관련된 먼지와 소음을 제거하여 환경적 이점을 제공합니다.
- 연구의 학문적 의의: 본 연구는 산업 환경에서 솔트 코어 기술의 실행 가능성을 뒷받침하는 귀중한 실제 증거를 제공합니다. 이는 첨단 주조 기술 및 환경을 고려한 제조 공정에 대한 지식 기반을 넓히는 데 기여합니다.
- 실용적 의미: 연구 결과는 특히 복잡한 부품에 대한 알루미늄 합금 주조를 활용하는 산업에서 솔트 코어 기술을 채택함으로써 이익을 얻을 수 있음을 시사합니다. 이는 주조 품질 향상, 불량률 감소, 간소화된 후처리 공정 및 보다 지속 가능한 제조 발자국으로 이어질 수 있습니다. 수성 코어 제거 공정은 기존의 기계적 방법에 비해 에너지 절감 효과를 제공하고 소음 공해를 제거합니다.
- 연구의 한계: 본 연구는 단일 펌프 본체 부품 설계 및 특정 중력 기울기 주조 조건으로 제한됩니다. 다양한 알루미늄 합금, 부품 형상 및 주조 방법(예: 고압 다이캐스팅)에 걸쳐 솔트 코어 기술의 일반적인 적용 가능성을 평가하기 위한 추가 연구가 필요합니다. 솔트 코어 생산에서 수축률 제어 및 냉각 최적화와 관련된 과제는 추가 조사 및 개선이 필요합니다.
7. 향후 후속 연구:
- 후속 연구 방향:
- 기계적 및 열적 특성: 추가 실험 연구는 솔트 코어의 기계적 및 열적 특성을 포괄적으로 평가하고 모래 코어와 직접 비교하는 데 초점을 맞춰야 합니다.
- 공정 최적화: 균질한 응고를 달성하고 균열을 최소화하기 위해 솔트 코어 생산을 위한 냉각 시스템 및 냉각 매개변수를 최적화하기 위한 심층 연구가 필요합니다.
- 비용 절감: 용해된 염의 재활용 및 지역 대체 염 공급업체 식별을 포함하여 비용 효율적인 전략을 모색하는 것이 산업적 채택에 중요합니다.
- 추가 탐구가 필요한 영역:
- 장기 안정성: 특히 습한 환경에서 솔트 코어의 장기 안정성 및 성능을 조사하는 것이 실제 적용에 중요합니다.
- 더 넓은 적용 범위: 고압 및 저압 다이캐스팅과 같은 다양한 주조 방법과 다양한 알루미늄 합금 및 부품 복잡성으로 솔트 코어의 적용 범위를 확장하면 기술의 영향력이 확대될 것입니다.
8. 참고 문헌:
- [1]. Brůna, M., Sládek, A. & Kucharčík, L. (2012). Formation of porosity in Al-Si alloys. Archives of Foundry Engineering. 12(1), 5-8. DOI: 10.2478/v10266-012-0001-5.
- [2]. Lichý, P., Bednářová, V. & Elbel, T. (2012). Casting routes for porous metals production. Archives of Foundry Engineering. 12(1), 71-74. DOI: 10.2478/v10266-012-0014-0.
- [3]. Dańko, J., Dańko, R. (2009). Theoretical and technological aspects of the production processes of foundry cores blown In 50. Konferencji i Krystalizacja Metali (pp. 71-86). Katowice - Gliwice, Poland: Polska ademia Nauk, Komisja Odlewnictwa. ISBN: 978-83-929266-0-3. (in Polish).
- [4]. Fuchs, B., Eibisch, H. & Körner, C. (2013). Core viability simulation for salt core technology in high pressure die casting. International Journal of Metalcasting. 7(3), 39-45. ISSN: 1939-5981
- [5]. Stingl, P., & Shiller, G. (2009). Gichte und rückstandfreie Entkernung - Salzkerne für den Aluminiumguss. Giesserei-Erfahrungsaustausch. 6, 4-8.
- [6]. Adámková, E., Jelínek, P., & Študentová, S. (2013). Application of cooking salts in manufacture of water soluble cores for high pressure die. Materials and technology. 61(11-12), 689-693. ISSN: 1580-2949, 1580-3414.
- [7]. P. Jelínek, E. Adámková "Lost Cores for High-Pressure Die Casting" Department of Metallurgy and Foundry Engineering, VŠB-Technical University of Ostrava DOI:10.2478/afe-2014-0045.
- [8]. P. Jelínek, E. Adámková, F. Mikšovský, J. Beňo Advance in Technology of Soluble Cores for Die Castings, Department of Metallurgy and Foundry, VŠB - Technical University of Ostrava ISSN (1897-3310) Volume 15 Issue 2/2015 29-34.
- [9]. Eliska Adámková, Petr Jelínek, Jaroslav Beòo Frantiek Mik{ovský, Water-Soluble Cores-Verifying Development Trends, V[B-Technical University of Ostrava, Faculty of Metallurgy and Materials Engineering, Department of Metallurgy and Foundry, ISSN 1580-2949 MTAEC9,49(1)61(2015).
- [10]. Mr. Vijaykumar A. Radadiya, Dr. Komal G. Dave, Mr. Kalpeshkumar R. Patel, Design and Analysis of Salt Core for a Casting of Alüminium Alloys Core casting, International Journal Of Advance Engineering and Research Development, Volume 2, Issue 3-2015.
- [11]. Jun Yaoka wa, Daisuke Miura, Koichi Anzail, Youji Ya mada and Hiroshi Yoshii, "Strength of Salt Core Composed of Alkali Carbonate and Alkali Chloride Mixtu res Made by Casting" Journal of Technique Mate rials Transactions, Vol. 48, No. 5 (2007) pp. 1034 to 1041, Japan Foundry Engineering Society.
- [12]. Petr Jelinek, Frantisek Miksovsky, Jaroslav Beoo, Eliska Adamkova, " Development of Foundry Cores Based On Inorganic Salts" MTAEC9, 47(6)689(2013), ISSN 1580-2949.
- [13]. Bühler AG: Lost Core An Industrial Process Path for High-Quality Salt Cores. https://www.foundry-planet.com (Date of access: 25.06.2021).
9. 저작권:
본 자료는 튤라이 한체르리오글루(Tülay Hançerlioğlu)의 논문 "알루미늄 합금 주조에서 대체재로서의 솔트 코어 사용 개발(Development of Salt Core Use as an Alternative in Aluminum Alloy Castings)"을 기반으로 합니다.
논문 출처: https://doi.org/10.18466/cbayarfbe.1033177
본 자료는 상기 논문을 기반으로 요약되었으며, 상업적 목적으로 무단 사용하는 것을 금지합니다.
Copyright © 2025 CASTMAN. All rights reserved.