본 소개 논문은 "[The Evolution of Dilatant Shear Bands in High Pressure Die Casting for Al-Si Alloy]" 제목으로 "[Preprints.org]"에서 발행한 논문을 기반으로 합니다.
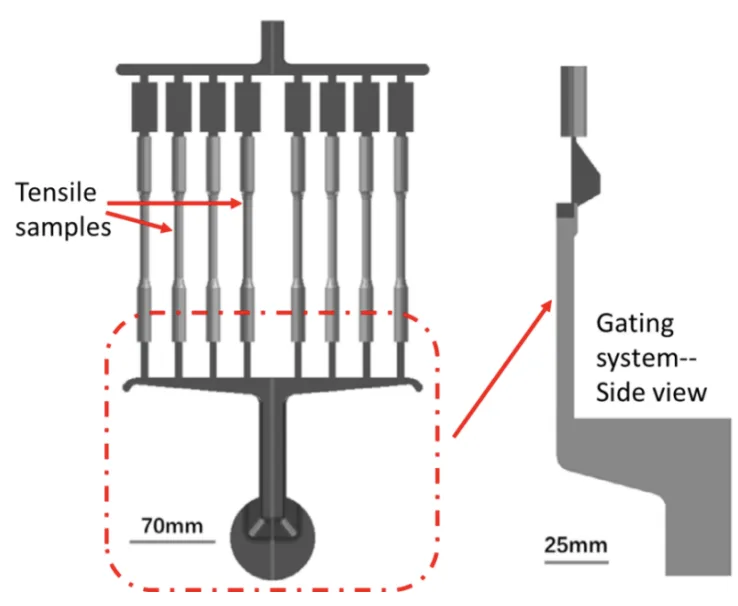
1. 개요:
- 제목: 알루미늄-실리콘 합금 고압 다이캐스팅에서 딜라턴시 전단 밴드의 진화
- 저자: JINGZHOU LU, ewan lordan, Kun Dou
- 발행 연도: 2024년
- 발행 저널/학회: Preprints.org (비 동료 심사 버전)
- 키워드: 전단 밴드; 편석; 결함; 알루미늄 합금; 고압 다이캐스팅
2. 초록:
수지상 간 기공과 양의 거시적 편석 밴드는 압력 다이캐스팅에서 흔히 관찰되며, 이전 연구에서는 이들이 입상 재료의 딜라턴시 전단 밴드와 밀접한 관련이 있음을 입증했습니다. 최근 기술 개발에도 불구하고 액상선과 고상선 온도 영역 사이의 합금에 대한 고압 다이캐스팅(HPDC) 공정에서 딜라턴시를 지배하는 미세 메커니즘은 여전히 완전히 이해되지 않고 있습니다. HPDC에서 딜라턴시 전단 밴드의 진화에 대한 유체 흐름과 외부 응고 결정(ESC) 크기의 영향을 조사하기 위해 Al8SiMnMg 합금의 HPDC 샘플을 생산하기 위해 다양한 충전 속도를 시험했습니다. 본 연구에서는 결정 파편화가 딜라턴시 농도의 감소를 동반하여 불분명한 전단 밴드를 생성함을 입증합니다. 일단 결정 파편화가 정체되면 충전 속도의 추가 증가(2.2 ms-1에서 4.6 ms-¹)와 관련된 향상된 변형률은 딜라턴시를 고농축 전단 밴드로 국한시킵니다. 최적 피스톤 속도는 3.6 ms-1이며, 이 속도에서 평균 ESC 크기는 최소값에 도달하고 평균 항복 응력과 강도 및 연신율의 전체 곱은 각각 144.6 MPa 및 3.664 GPa%의 최대값에 도달합니다. 입상 매질에서 힘 사슬 좌굴의 개념을 채택함으로써 등축 응고 합금에서 딜라턴시 전단 밴드의 진화는 OpenFOAM에서 DEM 유형 모델링을 통한 추가 검증을 기반으로 적절하게 설명될 수 있습니다. ESC 강화 팽창에 대한 세 가지 메커니즘이 제시되어 ESC의 존재와 후속 전단 밴드 특성 간의 관계에 대한 이전 보고서를 명확히 합니다. 등축 응고 합금에 입상 재료의 물리학을 적용함으로써 HPDC의 공정 최적화 및 미세 구조 모델링에 대한 독특한 기회가 제시됩니다.
3. 서론:
고압 다이캐스팅(HPDC)은 경금속의 대중적인 제조 공정이며 높은 생산성, 치수 정확도 및 우수한 기계적 성질로 알려져 있습니다. 그러나 HPDC의 사출 단계는 빠른 충전 속도와 캐스팅 시스템의 좁은 인게이트로 인해 격렬한 난류가 발생합니다. VanRens 방정식으로 정의되는 J 인자 [Eq.1]는 초기 유동 체제를 나타내는 중요한 매개변수로, 제품 품질과의 관계를 확립하려는 최근 연구에서 상당한 주목을 받고 있습니다.
논문에서는 사출 시 러너와 인게이트에서 도입되는 것과 같은 집중적인 용융 금속 전단이 최종 미세 구조에서 관찰되는 조대한 외부 응고 결정(ESC)의 형태와 분포에 상당한 영향을 미친다고 언급합니다. 이전 연구에서는 충전 속도가 증가하면 마그네슘 합금 AM60B에서 결정 파편화 및 재용융이 발생하며, 이는 용융물 내에서 유도된 열충격 및 대류에 기인한다고 보고되었습니다. 또한 ESC의 존재는 응고 합금의 유변학 및 결함 밴드 특성에 영향을 미칠 수 있다고 지적합니다.
이전 연구를 바탕으로 저자들은 등축 응고 합금의 유변학이 무결속 압축 입상 재료로 해석될 수 있다고 주장합니다. 이러한 집합체 내의 입자는 압축 및 전단 하중에 반응하여 수축 및 팽창 영역을 형성합니다. Al-7Si-0.3Mg 및 Mg-9A1-0.7Z와 같은 합금에서 전단 응력이 증가하면 체적 팽창(레놀즈 딜라턴시)이 발생하고, 이는 궁극적으로 전단 밴드 형성에 이르게 됩니다. 연구에서는 HPDC 공정 매개변수, 특히 증압 단계와 열 조건이 전단 밴드 형성에 미치는 영향을 강조하며, 흐름 조건이 밴드 특성에 미치는 영향에 대한 연구의 필요성을 제기합니다. 본 연구는 힘 사슬 좌굴이 딜라턴시 전단 밴딩에 미치는 영향을 탐구하고 HPDC에서 ESC 강화 팽창에 대한 세 가지 새로운 메커니즘을 제시하는 것을 목표로 합니다. 충전 속도가 딜라턴시 전단 밴드 진화 및 결정 형태에 미치는 영향을 논의할 것입니다.
4. 연구 요약:
연구 주제 배경:
본 연구는 압력 다이캐스팅에서 흔히 발생하는 수지상 간 기공과 양의 거시적 편석 문제를 다룹니다. 이전 연구에서는 이러한 결함과 입상 재료에서 잘 문서화된 현상인 딜라턴시 전단 밴드 간의 밀접한 관계를 확립했습니다. HPDC 기술의 발전에도 불구하고 HPDC 공정 중 액상선-고상선 온도 범위 내 합금의 딜라턴시를 지배하는 미세 메커니즘은 아직 완전히 밝혀지지 않았습니다.
선행 연구 현황:
베인 레오메트리 및 직접 전단 셀을 활용한 이전 연구에서는 등축 응고 합금의 유변학이 무결속 압축 입상 재료로 모델링될 수 있음을 시사했습니다 [12, 13]. 이러한 연구에서는 이러한 집합체의 입자가 수축 및 팽창 영역으로 재배열되어 압축 및 전단 하중에 반응하는 것으로 나타났습니다. Al-7Si-0.3Mg 및 Mg-9A1-0.7Z와 같은 합금에서 전단 응력이 증가하면 체적 팽창(레놀즈 딜라턴시) [14]이 발생하여 궁극적으로 전단 밴드로 국한됩니다. 연구에서는 HPDC 매개변수가 전단 밴드 특성에 영향을 미친다는 점도 시사합니다 [8, 12, 16, 17]. 이산 요소 시뮬레이션(DEM)을 통한 입상 집합체 내 응력-딜라턴시 진화에 대한 Tordesillas의 연구는 주기적인 재밍-언재밍 이벤트와 힘 사슬 좌굴을 기본 메커니즘으로 강조합니다 [18, 19].
연구 목적:
본 연구의 목적은 HPDC 공정 중 딜라턴시 전단 밴드의 진화에 대한 유체 흐름과 외부 응고 결정(ESC) 크기의 영향을 조사하는 것입니다. 특히, 본 연구는 입상 재료의 힘 사슬 좌굴 개념을 등축 응고 합금에 적용하여 HPDC에서 ESC 강화 팽창의 미세 메커니즘을 밝히고자 합니다.
핵심 연구:
본 연구의 핵심은 다양한 충전 속도를 사용하여 Al8SiMnMg 합금을 실험적 HPDC를 수행하는 것입니다. 연구에서는 다양한 흐름 조건에서 딜라턴시 전단 밴드의 진화를 조사하고 결과 결정 형태를 분석합니다. 본 연구에서는 관찰된 현상을 설명하기 위해 입상 매질에서 힘 사슬 좌굴 개념을 채택하고 OpenFOAM에서 DEM 유형 모델링을 사용하여 검증합니다. 또한 HPDC 공정 최적화 및 미세 구조 모델링에 대한 통찰력을 제공하기 위해 HPDC에서 ESC 강화 팽창에 대한 세 가지 새로운 메커니즘을 제시합니다.
5. 연구 방법론
연구 설계:
본 연구는 Al8SiMnMg 합금의 고압 다이캐스팅(HPDC)을 포함하는 실험 설계를 채택합니다. 샘플은 2.2 ms-1, 3.6 ms-1 및 4.2 ms-1의 다양한 충전 속도를 사용하여 Frech 4500 kN 잠금력 콜드 챔버 HPDC 기계로 제작되었습니다. ASTM 표준에 따라 인장 샘플을 제작했습니다. 제안된 메커니즘의 검증을 위해 OpenFOAM을 사용한 DEM 유형 모델링을 활용했습니다.
데이터 수집 및 분석 방법:
- 인장 시험: 기계적 성질을 평가하기 위해 ASTM 표준 E8/E8M을 준수하여 Instron 5500 만능 전기 기계 시험 시스템을 사용하여 인장 시험을 수행했습니다.
- 미세 구조 특성 분석: 부식된 미세 구조를 관찰하기 위해 광학 현미경 및 주사 전자 현미경(SEM)을 사용하여 샘플을 분석했습니다. Keller 시약을 사용하여 부식했습니다. 고대비 SEM 현미경 사진을 사용하여 결정립 크기를 측정하고 Fiji/ImageJ 소프트웨어로 분석했습니다. EDX 매핑을 사용하여 공정 결정립 분율을 강조했습니다.
- 열화상 데이터: FLIR T650sc 적외선 카메라를 사용하여 다이 온도를 모니터링하여 실험 중 정상 상태 다이 온도를 보장했습니다. FLIR Tools 소프트웨어를 분석에 사용했습니다.
- 이미지 분석: Fiji/ImageJ 소프트웨어를 사용하여 결정립과 모재를 구별하기 위해 SEM 현미경 사진의 이진화를 포함한 이미지 처리와 Si 농축 영역의 정규화된 폭을 추정하는 데 사용했습니다.
- DEM 유형 모델링: OpenFOAM v5.0 플랫폼을 사용하여 Navior-Stokes 방정식, 표준 k-epsilon 방정식 및 DPMFoam을 사용하여 용융 흐름 및 ESC 운동을 모델링했습니다.
연구 주제 및 범위:
연구는 다음 사항에 중점을 둡니다.
- Al-Si 합금의 HPDC에서 딜라턴시 전단 밴드의 진화.
- 딜라턴시 전단 밴드 특성에 대한 다양한 충전 속도의 영향.
- 딜라턴시 강화를 위한 외부 응고 결정(ESC)의 역할.
- 등축 응고 합금에서 딜라턴시 전단 밴드 형성에 대한 메커니즘으로서의 힘 사슬 좌굴 조사.
- OpenFOAM에서 DEM 유형 모델링을 사용하여 제안된 메커니즘의 검증.
- HPDC의 공정 최적화 및 미세 구조 모델링에 대한 시사점.
6. 주요 결과:
주요 결과:
- 딜라턴시 전단 밴드 및 충전 속도: 양의 거시적 편석 밴드가 테스트된 모든 충전 속도에서 관찰되었습니다. 딜라턴시 농도는 속도가 2.2 ms-1에서 3.6 ms-1로 증가함에 따라 처음에는 감소했다가 4.2 ms-1에서 다시 증가하여 국소화된 팽창에서 전체 팽창으로, 다시 국소화된 팽창으로의 전환을 나타냅니다.
- 최적 피스톤 속도: 최적 피스톤 속도는 3.6 ms-1로 확인되었습니다. 이 속도에서 평균 ESC 크기는 최소값에 도달하고 평균 항복 응력(YS)과 강도 및 연신율의 곱은 최대값(각각 144.6 MPa 및 3.664 GPa%)에 도달했습니다.
- ESC 크기 및 딜라턴시: 결정 파편화는 딜라턴시 농도의 감소와 상관관계가 있는 것으로 나타났습니다. 충전 속도를 높이면 초기에는 평균 ESC 크기가 감소했지만 추가 증가는 ESC 크기를 크게 변경하지 않았지만 공동 응고 결정립 크기는 감소했습니다.
- 힘 사슬 좌굴 및 ESC 강화 팽창 메커니즘: 본 연구에서는 힘 사슬 좌굴 개념을 기반으로 HPDC에서 ESC 강화 팽창에 대한 세 가지 새로운 메커니즘을 제안하고 설명했습니다. 이러한 메커니즘은 그림 8에 그래픽으로 설명되어 있으며 다음을 포함합니다.
- 힘 사슬 내에 큰 ESC가 존재하여 접촉 지점 수를 줄이고 간질 유체 부피를 증가시켜 구조를 약화시키는 '적층 결함'.
- 횡방향 리프트 힘으로 인해 밴드 최외곽 영역에 위치한 ESC가 피벗 역할을 함.
- 난류 흐름에서 충돌 시 높은 에너지 소산으로 인해 큰 ESC가 힘 사슬 세그먼트를 이탈시킴.
- 모델 검증: OpenFOAM의 DEM 유형 시뮬레이션은 제안된 메커니즘을 뒷받침하여 ESC 응집 및 딜라턴시 전단 밴드 진화를 정확하게 예측했습니다.
그림 목록:
- 그림 1. 게이팅 시스템 및 8개의 인장 샘플 HPDC 인장 영역을 갖는 캐스팅 영역.
- 그림 2. HPDC 인장 샘플을 생산하는 데 사용된 충전 속도를 강조하는 샷 프로필.
- 그림 3. HPDC 공정의 다양한 주기 동안 적외선 이미지 및 온도 판독값.
- 그림 4. 2.2 ms-1(상단 행), 3.6 ms-1(중간 행) 및 4.2 ms-1(하단 행)의 충전 속도로 생산된 HPDC 샘플에서 관찰된 딜라턴시 전단 밴드. 게이지 섹션 중앙에서 채취한 부식된 샘플의 일반적인 거시 구조(왼쪽)와 공정 결정립 분율을 강조하는 해당 EDX 맵(오른쪽)이 표시됩니다.
- 그림 5. 영역 A에서 채취한 광학 현미경 사진으로, (i) 2.2 ms-1, (ii) 3.6 ms-1 및 (iii) 4.2 ms-1의 충전 속도에 따라 딜라턴시가 어떻게 변하는지 보여줍니다. (ii)에는 변형을 통해 지속된 잠재적 힘 사슬이 윤곽선으로 표시되어 있습니다. 벌크 충전 방향은 페이지 밖으로 향합니다.
- 그림 6. 평균 ESC 및 공동 응고 결정립 크기(표 1)를 얻기 위해 사용된 일반적인 고대비 2차 전자 SEM 현미경 사진, (i) 2.2 ms-1, (ii) 3.6 ms-1 및 (iii) 4.2 ms-1의 충전 속도.
- 그림 7. 다양한 인장 샘플의 항복 응력, 연신율 및 극한 인장 응력.
- 그림 8. 전단 밴드 내에서 ESC 강화 팽창을 지배하는 세 가지 메커니즘을 강조하는 그래픽 그림: (i) 힘 사슬을 따라 ESC의 존재로 인해 도입된 '적층 결함'; (ii) 밴드의 최외곽 영역에 위치한 ESC는 효과적으로 피벗 역할을 합니다. (iii) 난류 흐름 조건에 의해 추진되는 ESC는 힘 사슬에서 결정을 이탈시킬 가능성이 있습니다. σ는 주요 주응력 축을 나타냅니다.
- 그림 9. (i) 모델의 계산 영역 및 메시, (ii) 용융물의 유체 속도 분포, (iii) 충전 중 인장 샘플의 ESC 운동 및 속도 분포.
- 그림 10. 충전 중 인장 샘플에서 ESC 응집 경향.
7. 결론:
본 연구는 HPDC 중 등축 응고 합금에서 딜라턴시 전단 밴드의 진화가 입상 재료의 힘 사슬 좌굴 개념을 채택함으로써 효과적으로 설명될 수 있다고 결론 내립니다. 유체 흐름과 결정립 크기는 딜라턴시에 상당한 영향을 미치는 요인으로 확인되어 딜라턴시 농도와 전단 밴드 내 편석 정도를 제어합니다. 최대 딜라턴시는 2.2 ms-1의 충전 속도에서 관찰되었으며, 이는 더 큰 평균 ESC 크기와 관련이 있습니다. 충전 속도를 높이면 초기에는 결정 파편화가 촉진되어 딜라턴시 농도와 불분명한 전단 밴드가 감소했지만 임계 J 인자까지였습니다. 그러나 과도하게 높은 충전 속도는 변형률 증가, 딜라턴시 농도 증가 및 뚜렷한 전단 밴드를 유발하는 동시에 분무화로 인해 공동 응고 결정립을 미세화시켰습니다. 최적 피스톤 속도 3.6 ms-1은 ESC 크기를 최소화하고 기계적 성질을 최대화하는 것으로 나타났습니다. 본 연구에서는 ESC 강화 팽창에 대한 세 가지 새로운 메커니즘을 제안하고 DEM 시뮬레이션으로 검증하여 HPDC 공정 최적화 및 미세 구조 모델링에 대한 귀중한 통찰력을 제공합니다. 등축 응고 합금에 입상 재료 물리학을 적용하면 HPDC에서 공정 최적화 및 미세 구조 제어를 위한 새로운 길이 열립니다.
8. 참고 문헌:
- T. Kaneuchi, H. Nakano, Effect of J-value for internal quality of HPDC products at various casting alloys, in: Japan Die Cast. Congr. Trans., 2008: pp. 131-136.
- T. Kaneuchi, K. Motegi, T. Imamura, Properties of castings produced by high vacuum die cast process, in: Japan Die Cast. Congr. Trans., 2004: pp. 277-282.
- Y. Yamada, H. Yoshii, S. Mochizuki, Evaluation of J factor and leakage quality for high pressure die casting applied to closed-deck type cylinder block, SAE Tech. Pap. (2011).
- E. Koya, M. Nakagawa, S. Kitagawa, J. Ishimoto, Y. Nakano, N. Ochiai, Research of Atomization Phenomena in HPDC-Step 1 Feature of Gas Porosity Dispersion and Photography of Atomized Flow, SAE Tech. Pap. 2018–April (2018) 1–8. doi:10.4271/2018-01-1392.
- E. Koya, M. Nakagawa, S. Kitagawa, J. Ishimoto, Y. Nakano, N. Ochiai, Atomization in High-Pressure Die Casting - Step 2 Simulation of Atomized Flow of Molten Aluminum by LES-VOF Method, SAE Tech. Pap. 2018-April (2018) 1–10. doi:10.4271/2018-01-1393.
- S. Otarawanna, C.M. Gourlay, H.I. Laukli, A.K. Dahle, hypoeutectic Al 및 Mg 합금의 응고 중 등축 결정의 응집 및 굽힘, Acta Mater. 58 (2010) 261-271. doi:10.1016/j.actamat.2009.09.002.
- H.R. Kotadia, N. Hari Babu, H. Zhang, S. Arumuganathar, Z. Fan, 집중적으로 전단된 hypoeutectic Al-Si 합금 액체의 응고 거동, Metall. Mater. Trans. A Phys. Metall. Mater. Sci. 42 (2011) 1117–1126. doi:10.1007/s11661-010-0516-8.
- H. Cao, M. Wessén, 다이캐스트 AM50 마그네슘 부품의 미세 구조 및 밴드 결함의 특성, Int. J. Cast Met. Res. 18 (2005) 377–384. doi:10.1179/136404605225023216.
- M. Wu, X. Li, Z. Guo, S.Xiong, 마그네슘 합금 다이캐스팅의 미세 구조에서 외부 응고 결정의 형태 및 분포에 대한 공정 매개변수의 영향, China Foundry. 15 (2018) 139–144. doi:10.1007/s41230-018-7242-z.
- X. Li, Z. Guo, S. Xiong, AZ91D 마그네슘 합금의 고압 다이캐스팅에서 결함 밴드 형성에 대한 용융 흐름의 영향, Mater. Charact. 129 (2017) 344–352.
- C.M. Gourlay, H.I. Laukli, A.K. Dahle, Mg-Al 및 Al-Si 고압 다이캐스팅의 결함 밴드 특성, Metall. Mater. Trans. A Phys. Metall. Mater. Sci. 38 (2007) 1833–1844. doi:10.1007/s11661-007-9243-1.
- A.K. Dahle, D.H. StJohn, 머시 존의 유변학적 거동과 응고 중 캐스팅 결함 형성에 미치는 영향, Acta Mater. 47 (1998) 31–41. doi:10.1016/S1359-6454(98)00342-5.
- AZ91 마그네슘 합금, Acta Mater. 56 (2008) 3403–3413. doi:10.1016/j.actamat.2008.03.020.
- C.M. Gourlay, A.K. Dahle, 응고 금속의 딜라턴시 전단 밴드, Nature. 445 (2007) 70–73. doi:10.1038/nature05426.
- S. Otarawanna, C.M. Gourlay, H.I. Laukli, A.K. Dahle, 고압 다이캐스팅의 결함 밴드 두께, Mater. Charact. 60 (2009) 1432–1441. doi:10.1016/j.matchar.2009.06.016.
- H. Gjestland, S. Sannes, J. Svalestuen, H. Westengen, 자동차 응용 분야에서 신뢰성을 달성하기 위한 마그네슘 다이캐스팅 공정 최적화, SAE Tech. Pap. Ser. SAE 2005-0 (2005). doi:10.4271/2005-01-0333.
- S. Otarawanna, H.I. Laukli, C.M. Gourlay, A.K. Dahle, 고압 다이캐스팅의 공급 메커니즘, Metall. Mater. Trans. A Phys. Metall. Mater. Sci. 41 (2010) 1836-1846. doi:10.1007/s11661-010-0222-6.
- A. Tordesillas, J. Shi, T. Tshaikiwsky, 응력-팽창 및 힘 사슬 진화, Int. J. Numer. Anal. Meth. Geomech. 35 (2011) 264-292.
- A. Tordesillas, 조밀한 입상 집합체의 힘 사슬 좌굴, 언재밍 전환 및 전단 밴딩, Philos. Mag. 87 (2007) 4987–5016. doi:10.1080/14786430701594848.
- E. Lordan, J. Lazaro-Nebreda, Y. Zhang, Z. Fan, 고압 다이캐스팅 성능의 변동성 감소를 위한 효과적인 탈기, JOM. (2018). doi:10.1007/s11837-018-3186-4.
- F. Radjai, D. Wolf, M. Jean, J.J. Moreau, F. Radjai, D. Wolf, M. Jean, J. Jacques, M. Bimodal, 입상 패킹에서 응력 전달의 바이모달 특성 이 버전을 인용하려면 : HAL Id : hal-01407369 입상 패킹에서 응력 전달의 바이모달 특성, (2016) 0-4.
- D. walker, A. tordesillas, Reynolds' 팽창 및 전단 밴드 진화에 대하여: 새로운 관점, Int. J. Bifurc. Chaos. 23 (2013) 1330034. doi:10.1142/S0218127413300346.
- M. Oda, J. Konishi, S. Nemat-Nasser, 입상 재료의 강도에 대한 실험적 미세역학적 평가: 입자 롤링의 영향, Stud. Appl. Mech. 7 (1983) 21–30. doi:10.1016/B978-0-444-42192-0.50009-8.
- K. Iwashita, M. Oda, 수정된 별개의 요소 방법을 기반으로 한 전단 밴딩 공정의 미세 변형 메커니즘, Powder Technol. 109 (2000) 192–205. doi:10.1016/S0032-5910(99)00236-3.
- T.S. Majmudar, R.P. Behringer, 입상 재료의 접촉력 측정 및 응력 유도 이방성, Nature. 435 (2005) 1079–1082. doi:10.1038/nature03805.
- H.I. Laukli, C.M. Gourlay, A.K. Dahle, 반고체 캐스팅 충전 중 결정의 이동, Metall. Mater. Trans. A Phys. Metall. Mater. Sci. 36 (2005) 805-818. doi:10.1007/s11661-005-1011-5.
- H.I. Andersson, L. Zhao, M. Barri, 토크 결합 및 입자-난류 상호 작용, J. Fluid Mech. 696 (2012) 319-329. doi:10.1017/jfm.2012.44.
- C. Bi, S. Xiong, X. Li, Z. Guo, 고압 다이캐스팅에서 외부 응고 결정의 운동 및 결함 밴드 진화를 시뮬레이션하는 유체-입자 모델 개발, Metall. Mater. Trans. B Process Metall. Mater. Process. Sci. 47 (2016) 939–947. doi:10.1007/s11663-016-0591-3.
- X. Li, W. Yu, J. Wang, S. Xiong, 게이팅 시스템의 용융 흐름이 고압 다이캐스팅 AZ91D 마그네슘 합금의 미세 구조 및 기계적 성질에 미치는 영향, Mater. Sci. Eng. A. 736 (2018) 219-227. doi:10.1016/j.msea.2018.08.090.
- I. Graco, 분무화 개념 및 이론, 1995.
- K. Dou, E. Lordan, Y. Zhang, A. Jacot, Z. Fan. 완전한 컴퓨터 지원 엔지니어링(CAE) 모델링 및 고압 다이캐스팅(HPDC) 공정 최적화. Journal of Manufacturing Processes, 2020. doi.org/10.1016/j.jmapro.2020.10.062.
- K. Dou, E. Lordan, Y. Zhang, A. Jacot, Z. Fan. 실험 및 모델링을 결합한 고압 다이캐스팅(HPDC) 공정에서 알루미늄 합금의 기계적 성질을 최적화하는 새로운 접근 방식. Journal of Materials Processing Technology, 2021. doi.org/10.1016/j.jmatprotec.2021.117193.
- Bi, C., Xiong, S., Li, X. et al. 고압 다이캐스팅에서 외부 응고 결정의 운동 및 결함 밴드 진화를 시뮬레이션하는 유체-입자 모델 개발. Metall Mater Trans B 47, 939–947 (2016). https://doi.org/10.1007/s11663-016-0591-3.
9. 저작권:
- 본 자료는 "[JINGZHOU LU, ewan lordan, Kun Dou]"의 논문입니다. "[알루미늄-실리콘 합금 고압 다이캐스팅에서 딜라턴시 전단 밴드의 진화]"를 기반으로 합니다.
- 논문 출처: doi: 10.20944/preprints202410.0105.v1
본 자료는 위의 논문을 기반으로 요약되었으며, 상업적 목적으로 무단 사용하는 것을 금지합니다.
Copyright © 2025 CASTMAN. All rights reserved.