본 논문 소개는 ['노르웨이 과학 기술 대학교 (NTNU)']에서 발행한 ['알루미늄 및 마그네슘 합금의 고압 다이캐스팅 - 결정립 구조 및 편석 특성'] 논문을 기반으로 작성되었습니다.
1. 개요:
- 제목: 알루미늄 및 마그네슘 합금의 고압 다이캐스팅 - 결정립 구조 및 편석 특성 (High Pressure Die Casting of Aluminium and Magnesium Alloys - Grain Structure and Segregation Characteristics)
- 저자: 한스 이바르 라우클리 (Hans Ivar Laukli)
- 발행 연도: 2004년 4월
- 발행 저널/학술 단체: 노르웨이 과학 기술 대학교 (NTNU)
- 키워드: 제공된 문서에 명시적으로 나열되지는 않았지만, 제목과 초록에서 유추할 수 있는 키워드는 다음과 같습니다: 고압 다이캐스팅, 알루미늄 합금, 마그네슘 합금, 결정립 구조, 편석 특성, 응고.
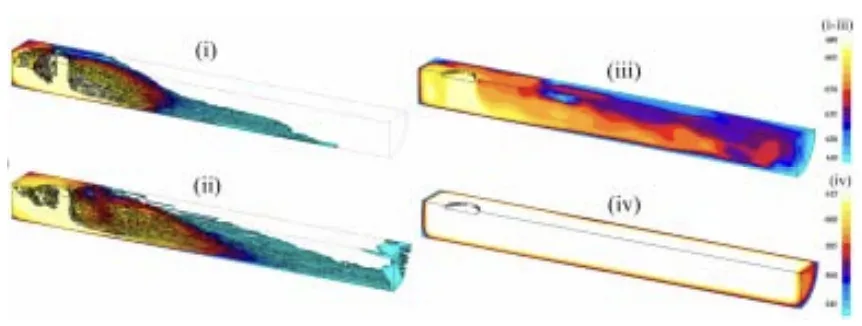
2. 초록 또는 서론
냉간 챔버 고압 다이캐스팅(HPDC)은 복잡한 형상의 알루미늄 및 마그네슘 합금 주조품 생산에 중요한 상업적 공정입니다. 본 논문에서 제시된 연구는 이러한 유형의 주조에서 미세 구조 형성을 조사하는 것을 목표로 합니다. 공정 및 합금과 관련된 응고 특성은 결정립 및 결함 형성을 제어합니다. 이는 다시 주조품의 기계적 특성에 상당한 영향을 미칩니다.
본 연구는 주로 AM60 마그네슘 합금과 A356 알루미늄 합금을 사용하여 수행되었습니다. 서로 다른 유동 및 응고 조건을 허용하는 냉간 챔버 HPDC 및 중력 다이캐스팅 방법의 두 가지 주조 배열이 사용되었습니다. 주조품의 미세 구조는 광학 현미경, 이미지 분석, 주사 전자 현미경, 전자 후방 산란 회절 측정 및 전자 탐침 미세 분석을 사용하여 조사되었습니다.
HPDC 실험에서 숏 슬리브 응고 조건은 주로 주입 시 용융 과열도를 변경하여 조사되었습니다. 이는 주조품의 미세 구조에 상당한 영향을 미쳤습니다. 외부 응고 결정(ESC)의 분율은 AM60 및 A356 다이캐스팅 모두에서 게이트 근처에서 가장 큰 것으로 일관되게 나타났습니다. 이는 고유한 숏 슬리브 응고 조건과 플런저 이동에 의해 설정된 유동에 기인합니다. 과열도가 증가하면 주조품에서 ESC의 분율이 더 낮게 나타났습니다. 또한 높은 과열도는 가지상/연장된 줄기 형태의 ESC를 제공하는 반면, 낮은 과열도는 AM60 및 A356 주조품 모두에서 더 조대하고 구형인 ESC를 생성했습니다. ESC는 일반적으로 다이캐스팅에서 게이트에서 더 먼 거리에서 단면의 중앙 영역으로 편석되었습니다.
AM60 다이캐스팅 생산 시 숏 슬리브 벽에 얇은 단열 코팅층을 적용했을 때 주조품에서 거의 모든 ESC가 제거되었습니다. A356 합금(및 숏 슬리브 코팅 없음)을 사용했을 때 용액에 Ti가 없으면 ESC의 분율이 현저히 낮아진 반면, AlTi5B1 결정립 미세화제 첨가는 ESC의 분율 증가와 주조품에서 현저히 미세한 결정립 크기를 유도했습니다. 구형 ESC의 형성은 AlTi5B1 결정립 미세화제가 A356 합금에 첨가되었을 때 향상되었습니다.
제어된 실험실 중력 다이캐스팅 실험에서 전형적인 HPDC 미세 구조는 반용융 금속을 강철 다이에 주입하여 생성되었습니다. ESC는 유동 중에 중앙 영역으로 편석/이동하여 최대 패킹(ESC 분율 ~35-40%)에 도달하는 것으로 나타났습니다. 편석 정도는 ESC의 분율에 의해 결정되며, 다이 온도는 ESC의 위치에 영향을 미칩니다. ESC의 편석은 양력의 결과로 유동 중에 발생하는 것으로 설명되었습니다.
띠형 결함의 형성 또한 연구되었습니다. 띠의 위치는 다이 온도와 ESC의 분율에 의해 영향을 받았습니다. 띠의 특성과 발생을 기반으로 결함 띠 형성에 대한 새로운 이론이 제안되었습니다. 유동 중 다이 벽으로부터의 고체 분포는 세 가지 영역으로 구성됩니다. 1) 벽면에서의 고체 분율 기울기; 2) (3) ESC 네트워크를 운반하는 낮은 고체 분율 영역. 변형률이 수지상정 간 유동률을 초과하는 임계 분율 고체가 존재합니다. 유도 응력이 네트워크 강도를 초과하면 변형은 슬립에 의해 발생하고 액체 유동이 뒤따릅니다. 액체 유동은 응고 수축, 내부 ESC 네트워크에 대한 정수압 및 액체를 끌어들이는 간극 형성에 의해 발생합니다.
3. 연구 배경:
연구 주제 배경:
본 연구는 상업적으로 중요한 공정인 고압 다이캐스팅(HPDC)에서 미세 구조 형성에 대한 중요한 영역을 다룹니다. 특히 복잡한 형상의 알루미늄 및 마그네슘 합금 주조품 생산에 있어서 중요합니다. 본 논문은 단조 제품에 비해 HPDC 부품의 기계적 특성이 일관성이 없다는 문제점을 강조하며, 이는 종종 공정 변수 변화에 기인하지만 충분한 문서화가 부족합니다. 이러한 불일치는 특히 자동차 산업과 같이 내충격성 및 피로 저항성이 중요한 분야에서 HPDC의 광범위한 적용을 저해합니다.
기존 연구 현황:
기존 연구에서는 공정 변수가 HPDC 품질에 미치는 영향을 인지하고 있지만, 특히 숏 슬리브 조건과 미세 구조에 미치는 영향에 대한 체계적인 조사가 불충분하다고 판단되었습니다. 서문에서는 공정 변수 변화와 그 효과에 대한 문서화가 종종 "불만족스럽다"고 언급합니다. 서론에서는 자동차 분야의 광범위한 적용을 위해 내충격성 및 피로 특성을 개선하려면 "공정 및 금속 거동에 대한 과학적 이해"가 필요하다고 언급합니다.
연구의 필요성:
본 연구는 HPDC 부품의 기계적 특성 일관성을 개선해야 할 필요성에 의해 시작되었습니다. 공정 변수와 주조 품질 간의 연관성에 대한 "문서화가 종종 불만족스럽다"는 점이 프로젝트 시작의 계기가 되었습니다. Norsk Hydro의 최첨단 HPDC 기계 설치는 "HPDC 공정 및 다양한 매개변수가 미치는 영향에 대한 보다 체계적인 조사"를 가능하게 했습니다. 박사 과정 연구는 특히 "다이에 공급되는 금속으로 인한 주조품의 미세 구조에 대한 숏 슬리브 조건 및 영향 분석"을 위해 시작되었습니다. 이는 최종 주조 미세 구조 및 특성을 향상시키기 위해 숏 슬리브의 초기 응고 단계를 이해하고 제어해야 할 필요성이 분명함을 나타냅니다.
4. 연구 목적 및 연구 질문:
연구 목적:
주요 연구 목적은 알루미늄 및 마그네슘 합금의 고압 다이캐스팅(HPDC)에서 미세 구조 형성을 조사하는 것입니다. 특히 본 논문은 공정 변수 및 합금 조성에 의해 영향을 받는 응고 특성이 결정립 형성 및 결함, 그리고 결과적으로 HPDC 주조품의 기계적 특성을 어떻게 제어하는지 이해하는 것을 목표로 합니다.
핵심 연구:
본 연구에서 탐구된 주요 연구 분야는 다음과 같습니다.
- 숏 슬리브 응고 조건: 특히 용융 과열도가 미세 구조에 미치는 영향 조사.
- 외부 응고 결정(ESC): HPDC 주조품에서 ESC의 형성, 형태 및 편석 분석.
- 결정립 크기 분포: 결정립 크기 분포와 이봉형 결정립 구조 생성에 있어서 ESC의 역할 조사.
- 띠형 결함: 편석 띠 및 기공 띠를 포함한 띠형 결함의 형성 메커니즘 연구.
- 결정립 미세화제 효과: A356 합금에서 결정립 구조 및 ESC 형성에 대한 결정립 미세화제(AlTi5B1) 첨가의 영향 평가.
- 결정 이동: HPDC 조건과 유사한 중력 다이캐스팅 실험에서 반용융 유동 중 결정 이동 및 편석 조사.
연구 가설:
공식적인 가설로 명시되지는 않았지만, 본 연구는 다음과 같은 암묵적 가설 하에 진행됩니다.
- 숏 슬리브 응고 조건, 특히 용융 과열도는 ESC 형성 및 특성, 그리고 HPDC 주조품의 전체 미세 구조에 상당한 영향을 미칩니다.
- ESC는 결정립 크기 분포 및 띠형 구조와 같은 결함 형성에 중요한 역할을 합니다.
- 결정립 미세화제 첨가는 ESC 형성을 수정하고 HPDC 알루미늄 합금의 결정립 구조를 미세화할 수 있습니다.
- HPDC 주조품에서 ESC의 편석은 유동 역학과 응고 결정에 작용하는 양력에 의해 발생합니다.
- HPDC의 띠형 결함은 다이 충전 중 반용융 금속의 고체 분율 기울기, ESC 이동 및 유변학적 특성의 상호 작용과 관련이 있습니다.
5. 연구 방법론
연구 설계:
본 연구는 산업 규모의 HPDC와 제어된 실험실 중력 다이캐스팅을 사용한 실험 연구와 분석 모델링 및 미세 구조 특성 분석 기술을 결합하여 사용합니다. HPDC 실험은 용융 과열도 및 숏 슬리브 코팅과 같은 공정 변수를 조작하는 데 중점을 두었고, 중력 다이캐스팅 실험은 제어된 조건에서 HPDC 미세 구조를 시뮬레이션하도록 설계되었습니다.
자료 수집 방법:
자료 수집 방법은 다음과 같습니다.
- HPDC 실험: 최첨단 HPDC 기계를 사용하여 AM60 마그네슘 합금 및 A356 알루미늄 합금 박스형 부품 주조. 용융 과열도 및 숏 슬리브 코팅을 포함한 공정 변수를 체계적으로 변경했습니다.
- 중력 다이캐스팅 실험: HPDC 미세 구조를 모방하고 ESC 편석 및 띠형 결함 형성을 조사하기 위해 반용융 A356 알루미늄 합금을 강철 다이에 주입하는 제어된 실험실 실험.
- 중단된 다이 충전 테스트: 금속 유동 패턴 및 미세 구조 진화를 관찰하기 위해 다이 충전의 여러 단계에서 HPDC 공정을 중단했습니다.
- 온도 측정: 숏 슬리브 온도의 적외선 열화상 측정 및 용융 온도의 열전대 측정.
분석 방법:
본 연구에서 사용된 분석 방법은 다음과 같습니다.
- 현미경 검사: 광학 현미경, 주사 전자 현미경(SEM) 및 전자 후방 산란 회절(EBSD)을 사용하여 미세 구조, 결정립 크기 분포 및 ESC 형태를 분석했습니다.
- 이미지 분석: 정량적 이미지 분석을 사용하여 ESC 및 공정상의 면적 분율을 측정했습니다.
- 전자 탐침 미세 분석(EPMA): EPMA를 사용하여 다양한 미세 구조적 특징, 특히 실리콘 및 티타늄 분포의 화학적 조성을 분석했습니다.
- 분석 모델링: 숏 슬리브의 응고를 이해하고 고체 분율을 예측하기 위한 분석 모델 개발 및 적용.
- 수치 시뮬레이션: 수치 시뮬레이션을 사용하여 숏 슬리브 충전, 온도 진화 및 유체 유동 거동을 모델링했습니다.
연구 대상 및 범위:
- 재료: AM60 마그네슘 합금 및 A356 알루미늄 합금이 주요 연구 재료였습니다.
- 주조 방법: 냉간 챔버 고압 다이캐스팅(HPDC) 및 중력 다이캐스팅.
- 초점: 박막 주조품의 결정립 구조, 편석 특성 및 결함 형성.
- 규모: 산업용 HPDC 기계 및 실험실 규모의 중력 다이캐스팅 설정.
6. 주요 연구 결과:
핵심 연구 결과:
- 숏 슬리브 응고: 숏 슬리브 조건은 미세 구조에 상당한 영향을 미칩니다. 낮은 용융 과열도와 더 차가운 숏 슬리브는 ESC의 분율을 높입니다. 단열 숏 슬리브 코팅은 AM60 주조품에서 ESC를 거의 제거합니다.
- ESC 형태: 용융 과열도는 ESC 형태에 영향을 미칩니다. 낮은 과열도는 더 조대하고 구형인 ESC를 유발하는 반면, 높은 과열도는 가지상, 수지상/연장된 ESC를 유발합니다.
- 결정립 미세화제 효과: A356 합금에서 AlTi5B1 결정립 미세화제 첨가는 구형 ESC 형성을 촉진하고 결정립 크기를 미세화합니다. 용액 내 Ti는 ESC 분율을 증가시키는 반면, AlTi5B1 첨가는 구형 ESC를 더욱 향상시킵니다.
- ESC 편석: ESC는 HPDC 주조품의 게이트 영역으로 일관되게 편석되고 중력 다이캐스팅 실험에서 유동 중 중앙 영역으로 이동하여 최대 패킹 분율(~35-40%)에 도달합니다. 편석은 유동 중 양력 메커니즘에 기인합니다.
- 띠형 결함 형성: 띠형 결함은 다이 온도와 ESC 분율에 의해 영향을 받습니다. 새로운 이론에서는 결함 띠가 응고 수축 및 정수압에 의해 구동되는 ESC 네트워크를 운반하는 낮은 고체 분율 영역에서 변형 및 액체 유동의 결과로 형성된다고 제안합니다.
제시된 데이터 분석:
- 용융 과열도 및 ESC: 용융 과열도가 증가하면 ESC 분율이 감소하고 형태가 구형에서 가지상으로 변경됩니다. 이는 더 높은 온도에서 ESC의 핵 생성 감소 및 재용융 증가에 기인합니다.
- 결정립 미세화제 및 ESC: 결정립 미세화제, 특히 AlTi5B1은 구형 ESC 형성 및 더 미세한 결정립 크기를 촉진하여 이종 핵 생성을 향상시키는 것으로 보입니다.
- ESC 편석 메커니즘: 중력 다이캐스팅 실험은 유동 중 ESC 편석을 확인하여 패킹 한계에 도달합니다. 양력이 중앙 영역으로의 ESC 이동을 유도하는 메커니즘으로 제안됩니다.
- 띠형 결함 이론: 유동 중 고체 분포에 대한 제안된 3영역 모델은 특정 고체 분율 영역에서 변형 및 액체 편석의 결과로 띠형 결함 형성을 설명합니다.
그림 목록:
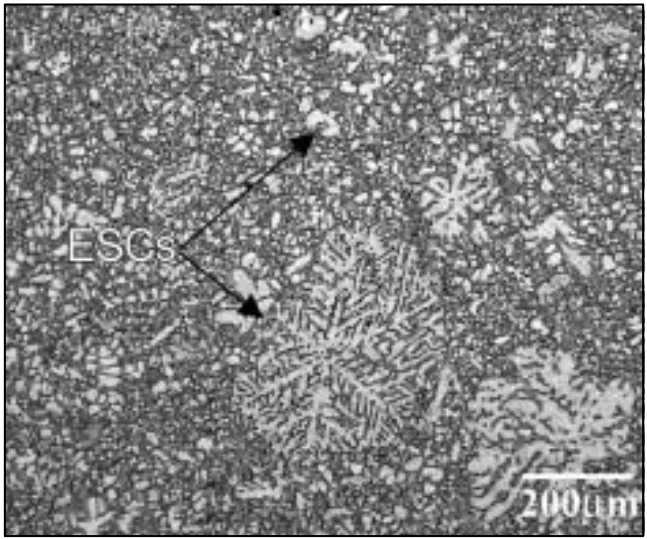
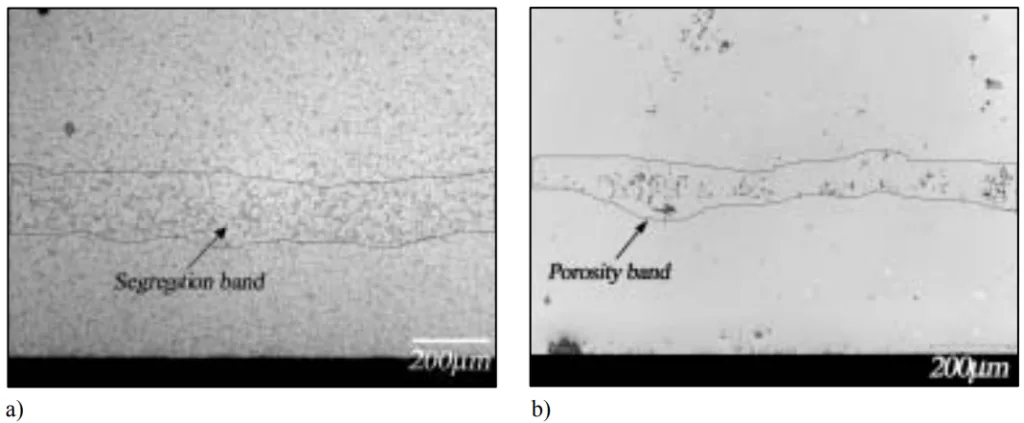
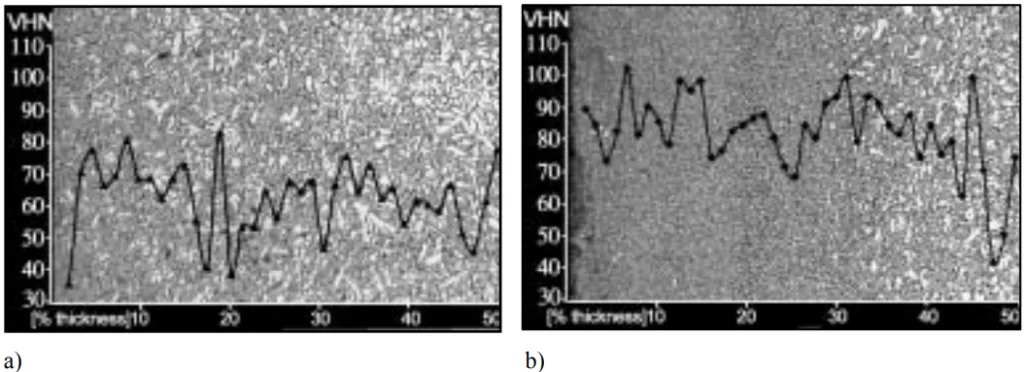
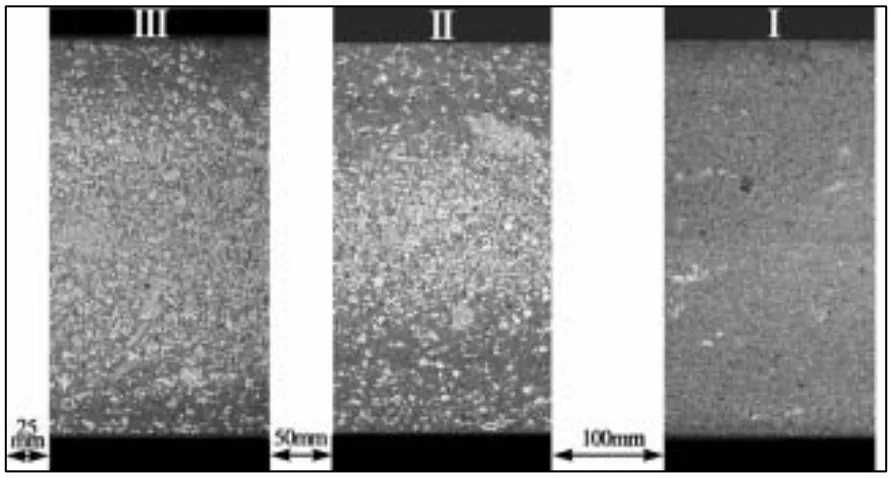
- 그림 1: 냉간 챔버 고압 다이캐스팅 그림.
- 그림 2: 용융 과냉각 ΔTt가 필요한 핵 생성 과냉각 ΔTn을 초과할 때 다이 벽에 인접한 열적으로 과냉각된 영역에서 핵 생성이 가능합니다.
- 그림 3: 구속된 성장에서의 구성 과냉각 원리 그림.
- 그림 4: Al-Si(검은색 선) 및 Mg-Al(파란색 선) 2원계 상태도의 저용질 부분.
- 그림 5: 두 가지 극단적인 결정 형태에 대한 분율 고체(fs)의 함수로서 재료의 전단 강도 측정; 큰 가지상 결정과 작은 구형 결정.
- 그림 6: a) A380 알루미늄 합금 충전 시뮬레이션. b) 충전 중 입자 위치 시뮬레이션.
- 그림 7: A356 알루미늄 합금에 대한 숏 슬리브의 용융 온도 진화 시뮬레이션(세로 단면).
- 그림 8: a) 비스킷의 단면 현미경 사진. b) 플런저 근처의 미세 구조 확대.
- 그림 9: 미세 구조에 큰 냉각 플레이크가 박혀 있는 A380 알루미늄 합금 다이캐스팅의 단면 현미경 사진.
- 그림 10: 산업적으로 생산된 HPDC AM60 계기판의 광학 현미경 사진.
- 그림 11: AM60 마그네슘 합금 다이캐스팅의 숏 프로파일.
- 그림 12: 플런저 팁 앞쪽의 속도 vw, 플런저 속도 vp를 갖는 서지파.
- 그림 13: 느린 숏 플런저 이동 및 동시 금속 유동 및 분율 고체 분포 시뮬레이션.
- 그림 14: 약 70% 플런저 이동 시 사진: a) 파편화된 유동 전면; b) 다이 충전 중 두께를 통해 금속이 얼어붙은 위치(화살표로 표시).
- 그림 15: a) A356 다이캐스팅의 편석 띠; b) AM60 다이캐스팅의 기공 띠.
- 그림 16: 그림 설명: a) 분율 고체 프로파일; b) 해당 강도 프로파일; c) 중앙 영역이 편석된 전단면을 따라 슬립을 용이하게 하는 결과 미세 구조.
- 그림 17: a) A356 알루미늄 합금 다이캐스팅의 편석 띠. b) 전형적인 HPDC 미세 구조.
- 그림 18: 박막(2.5mm) AM60 마그네슘 합금 다이캐스팅 단면의 절반에서 표면에서 중심으로의 미세 경도(VHN) 측정(10g 압입 하중): a) ESC의 큰 분율 ~균일하게 분포, 평균 VHN 63; b) ESC는 중앙 영역에만 위치합니다.
- 그림 19: AM60 마그네슘 합금 다이캐스팅에서 채취한 인장 시험편의 단면 현미경 사진: a) 게이트 근처, 일반적인 연신율: 3-10%; b) 게이트에서 더 멀리, 일반적인 연신율: 15-25%.
- 그림 20: 플런저 이동 및 해당 분율 고체 분포의 정성적 설명의 개략도.
- 그림 21: 숏 슬리브의 응고 및 금속 유동은 주조품에서 서로 다른 열 이력을 가진 미세 구조를 초래합니다.
- Figure 22: 중앙 영역에서 ESCs의 패킹 개략도. 특정 분율 고체에서 추가 패킹이 제한되고 ESCs가 있는 중앙 영역은 양 r(2r+r)만큼 더 커진다.
7. 결론:
주요 연구 결과 요약:
본 연구는 HPDC 공정에서 알루미늄 및 마그네슘 합금의 결정립 구조 및 편석 특성에 대한 심층적인 이해를 제공한다. 주요 연구 결과는 다음과 같이 요약할 수 있다.
- ESCs 분포: ESCs는 주조품의 게이트 근처에 집중되어 있으며, 게이트에서 멀어질수록 분율이 감소한다. 이는 샷 슬리브 내 응고 조건과 플런저 이동으로 인한 유동 패턴에 기인한다.
- 과열도의 영향: 용탕 과열도가 증가하면 ESCs 분율이 감소하고, ESCs 형태가 수지상에서 구형으로 변화한다. 낮은 과열도는 조대하고 구형의 ESCs를, 높은 과열도는 미세하고 수지상의 ESCs를 생성한다.
- 결정립 미세화제의 영향: AlTi5B1 결정립 미세화제는 A356 합금에서 구형 ESCs 형성을 촉진하고 결정립 크기를 미세화한다. 반면, Ti 단독 첨가는 ESCs 분율을 증가시킨다.
- ESCs 편석 메커니즘: ESCs는 유동 중 양력에 의해 중앙 영역으로 편석되며, 편석 정도는 ESCs 분율과 다이 온도에 의해 영향을 받는다.
- 띠형 결함 형성 메커니즘: 띠형 결함은 다이 온도, ESCs 분율, 그리고 유동 중 고체 분율 기울기에 의해 형성되며, 새로운 띠형 결함 형성 메커니즘이 제안되었다.
연구의 학문적 의의:
본 연구는 HPDC 공정에서 미세 구조 형성, 특히 ESCs 및 띠형 결함 형성에 대한 학문적 이해를 심화시켰다. 샷 슬리브 조건, 용탕 과열도, 결정립 미세화제 첨가와 같은 공정 변수가 미세 구조에 미치는 영향을 체계적으로 분석하여 HPDC 공정의 과학적 기반을 강화하였다.
실용적 의미:
본 연구 결과는 HPDC 공정의 실용적인 개선에 기여할 수 있다. 샷 슬리브 조건 제어, 용탕 과열도 최적화, 결정립 미세화제 활용 등을 통해 주조품의 미세 구조 및 기계적 물성을 개선하고 결함 발생을 줄일 수 있다. 특히, ESCs 제어 및 띠형 결함 방지는 HPDC 주조품의 품질 향상에 중요한 역할을 할 수 있다.
연구의 한계 및 향후 연구 분야:
본 연구는 AM60 및 A356 합금에 초점을 맞추어 진행되었으며, 다른 합금에 대한 추가 연구가 필요하다. 또한, ESC 핵생성 메커니즘, 띠형 결함 형성 메커니즘, 그리고 유동 및 응고 거동에 대한 모델링 연구가 향후 연구 분야로 제시되었다. 특히, 다양한 합금, 공정 조건, 다이 형상에 대한 추가 실험 및 모델링 연구를 통해 HPDC 공정에 대한 보다 포괄적인 이해를 구축할 필요가 있다.
8. 참고 문헌:
- [1] E.J. Vinarcik, High Integrity Die Casting Processes, John Wiley & Sons, Inc., 2003.
- [2] L.J.D. Sully, Metals Handbook, 15, 286-295.
- [3] M. M. Avedesian, H. Baker, Magnesium and Magnesium Alloys, ASM International, 1999.
- [4] A. Kaye, A. Street, Die Casting Metallurgy, Butterworth scientific, 1982.
- [5] N. Fantetti, O. Holta, J.B. R¯nhaug, D. Albright, NADCA Trans., 1997, 19, T97-054.
- [6] Melting and handling magnesium for die casting, Hydro Magnesium Data Sheet, 2002.
- [7] Introduction to Die Casting, NADCA, 1997.
- [8] A.D. Figueredo, Science and Technology of Semi-Solid Metal Processing, NADCA, 2001.
- [9] Die Casting - Process Optimization, B¸hler Druckguss, 2001.
- [10] L. B‰ckerud, C. Chai, J. Tamminen, Solidification Characteristics of Aluminium Alloys, AFS/Skanaluminium, 2, 1990.
- [11] W.G. Walkington, Die Casting Defects - Causes and Solutions, NADCA, 1997.
- [12] M.C. Flemings, Solidification Processing, McGraw-Hill, 1974.
- [13] W. Kurz, D.J. Fisher, Fundamentals of Solidification, Trans Tech Publications, 1998.
- [14] P.A. T¯ndel, PhD thesis, Norwegian Institute of Technology (Trondheim), 1994.
- [15] D.A. Porter, K.E. Easterling, Phase Transformations in Metals and Alloys, Chapman & Hall, 1997.
- [16] J. Campbell, Castings, Butterworth-Heinemann, 1997.
- [17] A. Ohno, Solidification - The Separation Theory and its Practical Applications, Springer Verlag, 1987.
- [18] B. Chalmers, J. Aust. Inst. of Metals, 1963, 8, 255-263.
- [19] R.T. Southin, Trans. AIME, 1966, 239, 220-225.
- [20] W.C. Winegard, B. Chalmers, Trans. ASM, 1954, 46, 1214-1224.
- [21] I. Maxwell, A. Hellawell, Acta Met., 1975, 23, 229-237.
- [22] K.A. Jackson, J.D. Hunt, D.R. Uhlmann, T.P. Seward, Trans. AIME, 1966, 236, 149-158.
- [23] E.F. Emley, Principles of Magnesium Technology, Pergamon Press Ltd., 1966.
- [24] A.W. Woods, J. Fluid Mech., 1992, 239, 429-448.
- [25] G. Hansen, A. Hellawell, S.Z. Lu, R.S. Steube, Met. Mat. Trans. A, 1996, 27A, 569-581.
- [26] Die Cast Magnesium Alloys, Hydro Magnesium Data Sheet, 2001.
- [27] J.R. Davis, Aluminum and Aluminum Alloys, ASM International, 1993.
- [28] A. Hellawell, 4th Int. Conf. on Semi-Solid Proc. Alloys Comp., 1996, 60-65.
- [29] Q. Han, A. Hellawell, Met. Mat. Trans. B, 1997, 28B, 169-173.
- [30] A.K. Dahle, D.H. StJohn, Acta Mat., 1998, 47, 31-41.
- [31] A.K. Dahle, L. Arnberg, J. of Met., 1996, 48, 34-37.
- [32] L. Wang, T. Nguyen, G. Savage, C.J. Davidson, Int. J. C.Met.R., 2003, 16, 409-417.
- [33] L. Wang, T. Nguyen, M. Murray, NADCA Trans., 2001, 21, T01-014.
- [34] H.T. Haaland, PhD thesis, Norwegian University of Science and Technology (Trondheim), 2000.
- [35] F.M. White, Fluidmechanics, McGraw-Hill, 1999.
- [36] S. Sannes, 2003. Personal communication.
- [37] H. Iwahori, M. Nakamura, K. Tozawa, Y. Yamamoto, NADCA Trans., 1985, 13, 1-9.
- [38] P. Paliani, L. Zalewski, J. Barreto, N. Tsumagari, J. Brevick, C. Mobley, NADCA Trans., 1995, 18, 149-155.
- [39] S. Sannes, Fill Tests - Simulations and Microstructures in U-profile Castings, Hydro Aluminium, Porsgrunn, 2003, 03P_BN2.doc.
- [40] P. Schmidt, PhD thesis, Royal Institute of Technology (Stockholm), 1994.
- [41] W. Sequeira, PhD thesis, The University of Queensland (Brisbane), 2000.
- [42] S. Sannes, H. Gjestland, H. Westengen, H.I. Laukli, Proc. Int. Conf. Mg. Alloys & Appl., 2003, 6, 725-731.
- [43] R. Chatfield, P.W. Rohan, ADCA Die Casting Conf., 2000, paper15; 11-15.
- [44] N. Tsumagari, T. Liang, J. Brevick, C. Mobley, NADCA Trans., 2001, 21, 251-256.
- [45] M. Gershenzon, P.W. Rohan, M.T. Murray, NADCA Trans., 1999, 20, 305-315.
- [46] T. Abbott, M. Easton, Mat. Forum, 2001, 25, 181-201.
- [47] D. StJohn, A.K. Dahle, T. Abbott, M.D. Nave, M. Qian, Proc. Magnesium Techn., 2003, 95-100.
- [48] S. Sannes, H. Gjestland, 2004. Personal communication.
- [49] P. Koch, Die Casting Eng., 1974, 18, 44-46.
- [50] L.W. Garber, Die Casting Eng., 1982, 26, 14-22.
- [51] J. Brevick, M. Duran, Y. Karni, NADCA Trans., 1991, 15, 399-404.
- [52] OSU Center for Die Casting, Effects of ESP on wave celerity and die cast products - 2D athermal model, 2002, http://www.mse.eng.ohio-state.edu/~mobley/diecasting/.
- [53] E.A. Herman, Heat Flow in the Die Casting Industry, NADCA, 1997.
- [54] A. Bowles, PhD thesis, The University of Queensland (Brisbane), 2002.
- [55] Z.W. Chen, Mat. Sci. Eng. A, 2003, 348, 145-153.
- [56] T.B. Hill, BNF Guide to Better Magnesium Die Casting, BNF Metals Technology Centre, 1976.
- [57] S. Sannes, H. Westengen, Proc. Int. Conf. Mg. Alloys & Appl., 1998, 4, 223-228.
- [58] P.D.D. Rodrigo, V. Ahuja, Proc. Int. Conf. Mag. Sci. Techn., 2000, 97-104.
- [59] C. Pitsaris, T. Abbott, C.J. Davidson, Light Met. Techn., 2003, 223-226.
- [60] H. Cao, M. Wessen, 11th Mg Autom.End User Sem., 2003, 1-22.
- [61] G.K. Batchelor, Theoretical and Applied Mechanics, Elsevier Science publishers, 1989, 27-40.
- [62] G.E. Dieter, Mechanical Metallurgy, McGraw-Hill, 1988.
- [63] C. Pitsaris, T. Abbott, C.H.J. Davies, G. Savage, Proc. Int. Conf. Mg. Alloys & Appl., 2003, 6, 694-699.
- [64] C. D¯rum, O.S. Hopperstad, O.-G. Lademo, M. Langseth, Int. J. Sol. Struct., 2004, submitted.
- [65] C. D¯rum, 2004. Personal communication.
- [66] H. Gjestland, 2004. Personal communication.
##9. 저작권:
- 본 자료는 "[Hans Ivar Laukli]"의 논문: "[High Pressure Die Casting of Aluminium and Magnesium Alloys - Grain Structure and Segregation Characteristics]"을 기반으로 합니다.
- 논문 출처: [DOI URL] (DOI URL을 찾을 수 없습니다. )
본 자료는 위 논문을 기반으로 요약되었으며, 상업적 목적으로 무단 사용하는 것을 금지합니다.
Copyright © 2025 CASTMAN. All rights reserved.