본 소개 자료는 "China Foundry"에서 발행한 "[Mechanism of die soldering during aluminum die casting]" 논문을 기반으로 작성되었습니다.
![Figure 1: Schematic illustration showing possible aluminum composition and temperature profiles at the die surface, and the resulting phases for the case of pure aluminum cast in an iron die. Three regions at the die surface can be identified. Soldering occurs in Region I [4].](https://castman.co.kr/wp-content/uploads/image-1853-png.webp)
1. 개요:
- 제목(Title): Mechanism of die soldering during aluminum die casting
- 저자(Author): Q. Han
- 발행 연도(Year of publication): 2015
- 발행 학술지/학회(Journal/academic society of publication): China Foundry, vol. 12, no. 2, pp. 136-143.
- 키워드(Keywords): 용착(Soldering), 다이 스티킹(die sticking), 알루미늄 합금(aluminum alloys), 다이캐스팅(die casting)
2. 초록 (Abstract):
용착(Soldering)은 알루미늄 합금의 다이캐스팅 또는 금형 주조와 관련된 독특한 주조 결함입니다. 이는 용융된 알루미늄이 금형강 표면에 달라붙거나 용착되어 주물 취출 후에도 남아있게 되어, 주물의 표면 결함 및 치수 부정확성을 유발하고 기계 가동 중단 시간을 증가시키는 현상입니다. 용착은 표면 처리가 되지 않은 금형강 금형을 사용하여 알루미늄 합금을 다이캐스팅할 때 쉽게 발생합니다. 용융 알루미늄이 임계 온도보다 높은 온도에서 금형강과 접촉하면, 철과 알루미늄 원자가 서로 확산하여 일련의 금속간 화합물 상과 액체 상태의 알루미늄이 풍부한 fcc 상을 형성합니다. 이 액상은 금속간 화합물 상 사이에 존재합니다. 냉각 시 액체 fcc 상은 금속간 화합물 상 위에서 응고되어 주물 내부로 성장하여 용착을 유발합니다. 임계 온도는 상평형도의 알루미늄 코너 근처의 공정 온도입니다. 만약 금형이 비반응성 세라믹 코팅으로 보호된다면, 용착은 국부적인 코팅 파손이 발생하는 위치에서 시작됩니다. 용융 알루미늄은 코팅 파손 부위를 통해 금형강과 접촉하고 강 기지(steel matrix)를 침식하여 작은 피트(pit)를 형성합니다. 이러한 작은 피트가 성장함에 따라 코팅은 점차 제거되고 용착은 더욱 심해집니다. 표면 처리가 되지 않은 강재 금형과 코팅된 금형 재료에서의 금형 용착 단계에 대한 세부 사항이 논의됩니다.
3. 서론 (Introduction):
다이캐스팅(Die casting) 또는 고압 다이캐스팅(HPDC)은 고압을 사용하여 용융 금속을 강철 금형에 주입하는 100년 역사의 공정입니다. 이 비용 효율적인 공정은 빠른 생산 속도와 높은 금형당 금속 수율로 정밀 형상(net-shape) 제품을 생산할 수 있습니다. 다른 어떤 금속 주조 공정도 이보다 더 다양한 형상, 정교한 디자인 또는 엄격한 치수 공차를 허용하지 않습니다. 오늘날 다이캐스팅 공정은 전체 금속 주물의 1/3 이상을 생산하는 데 사용되며, 그 대부분은 알루미늄 주물입니다[1].
알루미늄 다이캐스팅의 생산성을 제한하는 주요 문제 중 하나는 금형 용착(die soldering)입니다. 용착 또는 다이 스티킹(die sticking)은 용융 알루미늄이 금형 표면에 "용접"되는 현상입니다. 심한 경우, 금형 용착은 단 몇 번의 주조 사이클 후에 발생하여 기계 가동 중단 시간 증가, 주물의 표면 품질 및 압력 또는 누설 기밀성과 관련된 불량, 그리고 금형이 일반적으로 고가이고 가동 중단 시간이 생산 손실을 초래하므로 비용 증가를 야기합니다. 금형 용착은 저압 영구 금형 주조를 포함한 다른 금속 금형 주조 공정과도 관련이 있습니다.
용융 금속으로 둘러싸인 금형의 작은 형상 부위는 다이캐스팅 공정의 각 실행 동안 금형 본체보다 일반적으로 더 높은 온도로 가열되기 때문에 용착 형성이 일어나기 쉽습니다. 주물에 작은 구멍을 형성하는 데 사용되는 코어핀(Core pins)은 다이캐스팅 공정 중 용착이 발생하기 쉬운 금형의 그러한 형상 부위입니다. 코어핀의 사용은 주물에 구멍을 뚫는 요구 사항을 줄여 주조 공정을 더욱 비용 효율적으로 만듭니다. 일반적인 다이캐스팅 기계는 약 10개에서 100개의 핀을 사용합니다. 다이캐스팅 산업은 H-13 강이 열 균열(heat checking)과 마모에 강하다는 사실 때문에 금형 및 코어핀 제작에 H-13 강을 사용합니다.
다이캐스팅 업계에서는 두 가지 유형의 용착이 주장됩니다. 하나는 용융 알루미늄 합금과 금형 간의 화학적/야금학적 반응으로 인해 고온에서 발생하며[2], 다른 하나는 기계적 상호작용으로 인해 저온에서 발생합니다[3]. 북미 다이캐스팅 산업이 강력한 국제 경쟁에 직면했던 1990년대까지 금형 용착을 조사하기 위한 체계적인 연구는 제한적이었습니다. 다이캐스터들이 생존하기 위해 가동 중단 시간을 최소화하고 생산성을 높이는 것이 중요해졌지만, 북미의 대부분 다이캐스터는 연구 자원이 부족한 중소기업입니다. 결과적으로 금형 용착에 대한 연구는 산업 단체와 정부 기관의 후원을 받아왔습니다. 화학 반응으로 인해 발생하는 금형 용착을 이해하는 데 상당한 진전이 있었습니다. 기계적 상호작용으로 인한 용착에 대해서는 거의 알려진 바가 없습니다.
이 글은 화학적 상호작용의 결과로 발생하는 금형 용착에 대해 논의합니다. 이러한 유형의 용착은 금형 표면의 보호 필름 "세척(washout)"과 밀접하게 관련되어 있다고 일반적으로 인정됩니다[2]. 세척은 용융 알루미늄 합금이 금형의 보호 필름(코팅 또는 윤활제)을 파괴할 때 발생합니다. 그러면 용융 알루미늄이 금형 표면과 접촉하여 일반적으로 H-13 강인 금형 재료와 반응합니다. 금형 윤활제는 용융 금속에 의해 쉽게 파괴될 수 있지만, 코팅, 특히 물리 기상 증착(PVD) 공정을 사용하여 만든 코팅은 여러 주조 사이클 동안 금형에 남아 있을 수 있습니다. 금형 윤활제의 상당 부분이 제거되면, 용착은 용융 금속과 표면 처리가 되지 않은 금형강 간의 직접적인 화학 반응에 의해 제어됩니다. 금형에 강력한 PVD 코팅이 있는 경우, 용착은 코팅의 국부적인 파손에 의해 제어됩니다. 이 글은 표면 처리가 되지 않은 강철 금형과 코팅된 금형 또는 코어핀에서의 용착을 설명합니다.
4. 연구 요약 (Summary of the study):
연구 주제 배경 (Background of the research topic):
용융 알루미늄이 금형 표면에 부착되는 금형 용착은 알루미늄 고압 다이캐스팅(HPDC)의 생산성에 중대한 장애물입니다. 이는 주조 결함(표면 결함, 치수 부정확성), 금형 유지보수를 위한 기계 가동 중단 시간 증가, 불량률 증가, 고가의 금형 및 생산 손실과 관련된 비용 증가로 이어집니다. 일반적으로 H-13 강으로 만들어진 코어핀과 같은 형상 부위는 더 높은 작동 온도로 인해 특히 취약합니다.
이전 연구 현황 (Status of previous research):
금형 용착에 대한 체계적인 조사는 1990년대까지 제한적이었습니다. 연구는 화학적/야금학적 반응으로 인한 고온 용착과 기계적 상호작용으로 인한 저온 용착을 구분합니다. 용융 알루미늄 합금에 의한 보호 필름(윤활제 또는 코팅)의 "세척" 또는 파괴와 종종 연관되는 화학 반응 메커니즘을 이해하는 데 상당한 진전이 있었습니다[2]. PVD 코팅과 같은 내구성 있는 코팅이 용착을 완화하는 역할은 인정되지만, 국부적인 코팅 파손 시 여전히 용착이 발생할 수 있습니다. 기계적 용착에 대한 이해는 여전히 제한적입니다.
연구 목적 (Purpose of the study):
본 연구는 용융 알루미늄 합금과 금형강(특히 H-13) 간의 화학적 상호작용 결과로 발생하는 금형 용착 메커니즘을 명확히 하는 것을 목표로 합니다. 표면 처리가 되지 않은 강철 표면과 비반응성 세라믹 코팅으로 보호된 표면 모두에 대해 용착을 유발하는 조건과 금형 손상 진행 과정을 상세히 설명합니다.
핵심 연구 내용 (Core study):
본 연구의 핵심은 화학 반응에 기반한 금형 용착의 근본적인 메커니즘을 분석하는 것입니다. 표면 처리가 되지 않은 강철 금형의 경우, 알루미늄의 강철 내부로의 확산과 철의 알루미늄 내부로의 확산을 조사하여 금속간 화합물 상 형성을 유도합니다. 중요한 측면은 금형 표면 온도가 임계 온도(Tc, 순수 Al-Fe의 경우 공정 온도 655°C로 확인됨)를 초과할 때 액체 상태의 알루미늄이 풍부한 fcc 상이 형성된다는 것입니다. 이 액상은 응고 시 주물과 금형 사이의 결합을 용이하게 합니다. 코팅된 금형의 경우, 연구는 5단계 파손 메커니즘을 설명합니다: (1) 국부적 코팅 파손(균열/박리), (2) 노출된 강철에서의 반응을 통한 피트 형성, (3) 금속간 화합물 및 Al-풍부 fcc 상 형성을 포함하는 피트의 깊이 및 측면 성장, (4) 인접한 피트의 연결, (5) 파손된 영역에서의 침식으로 인한 역구배(negative draft) 또는 언더컷(undercut) 형성. 순수 알루미늄 및 A380 합금에 대한 임계 온도 개념을 검증하기 위해 실험적인 침지 테스트가 수행되었습니다. 사용된 코어핀의 미세 구조 분석은 코팅된 표면에서 제안된 메커니즘에 대한 증거를 제공했습니다.
5. 연구 방법론 (Research Methodology)
연구 설계 (Research Design):
본 연구는 상평형도(Al-Fe 시스템) 및 야금학적 원리(확산, 반응 속도론, 상 변태)에 기반한 이론적 분석과 실험적 검증을 결합하여 수행되었습니다. 두 가지 주요 시나리오가 조사되었습니다: 표면 처리가 되지 않은 강철 표면에서의 용착 및 코팅된 강철 표면(특히 코어핀)에서의 용착 시작 및 진행.
데이터 수집 및 분석 방법 (Data Collection and Analysis Methods):
- 표면 처리되지 않은 강철 분석:
- 순수 알루미늄 및 A380 알루미늄 합금 용탕에 담근 연강 실린더(직경 12mm, 길이 25mm)를 사용하여 단순 침지 및 침지 코팅 테스트를 수행했습니다.
- 시편 표면 온도는 용접된 열전대를 사용하여 모니터링하고, 용탕 침지 또는 로(furnace)에서의 유지를 조절하여 (±3°C) 제어했습니다.
- 각각의 융점/액상선 온도 이상 및 이하의 다양한 표면 온도(순수 Al: 630°C ~ 740°C; A380: 500°C ~ 680°C)에서 다양한 시간 동안 테스트를 수행했습니다(Table 1).
- 테스트 후 시편은 금속간 화합물 층 및 야금학적 결합 형성을 포함하여 용착의 존재 및 특성을 평가하기 위해 단면을 절단하고 금속 조직학적으로 검사했을 것으로 추정됩니다(Figure 3에서 암시됨).
- 결과는 Al-Fe 상평형도(Figure 1)와 연관시켜 액상 형성을 위한 임계 온도를 식별했습니다.
- 코팅된 금형/코어핀 분석:
- 다양한 시간 동안 산업용 다이캐스팅 기계에서 사용된 코어핀을 수집했습니다.
- 주사 전자 현미경(SEM)을 사용하여 이 핀들의 표면을 검사했습니다.
- SEM 이미징은 용착의 다양한 단계를 기록했습니다: 초기 코팅 파손 모드(균열, 박리 - Figure 4), 피트 형성 및 성장(Figure 5), 형성된 용착 영역의 형태(Figure 6a, Figure 7), 언더컷의 증거(Figure 8).
- 에너지 분산형 X선 분광법(EDS) 라인 스캔(Figure 6b, 6c에서 암시됨)을 사용하여 피트 내 H-13 기지, 반응 영역(금속간 화합물) 및 Al 합금 영역에 걸쳐 원소 분포(Al, Fe, Si, Cr, Cu)를 분석하여 상 식별 및 확산 과정 이해를 가능하게 했습니다.
연구 주제 및 범위 (Research Topics and Scope):
본 연구는 화학적/야금학적 상호작용으로 인한 알루미늄 다이캐스팅에서의 금형 용착 메커니즘에만 초점을 맞췄습니다. 범위는 다음과 같습니다:
- 순수 알루미늄 및 A380 합금에 대해 표면 처리가 되지 않은 강철 표면에서 용착 시작을 위한 조건(임계 온도) 정의.
- 형성된 금속간 화합물 상 및 액체 Al-풍부 fcc 상의 역할 특성화.
- 세라믹 코팅된 H-13 강 코어핀에서 국부적인 코팅 파손에서 시작하여 심각한 금형 손상(언더컷)으로 진행되는 용착 발생의 순차적 단계 상세 설명.
- 코팅된 표면에서 피트 형성 및 성장과 관련된 미세 구조 진화 및 원소 확산 조사.
- 본 연구는 기계적 상호작용으로 인한 용착은 조사하지 않았습니다.
6. 주요 결과 (Key Results):
주요 결과 (Key Results):
- 표면 처리되지 않은 강철에서의 금형 용착은 금형 표면 온도(TD)가 임계 온도(Tc)를 초과할 때 발생하며, 이는 Fe-Al 금속간 화합물 반응층 내에 알루미늄이 풍부한 액체 fcc 상의 형성을 가능하게 합니다(Region I, Figure 1). 이 액상의 응고는 주물과 금형 사이에 야금학적 결합을 생성합니다(Figure 2).
- 철/강철에 주조된 순수 알루미늄의 경우, 임계 온도 Tc는 Al-Fe 공정 온도인 655°C에 해당합니다. 실험적 침지 테스트는 표면 온도가 661°C 이상일 때 용착이 발생했지만 643°C 이하에서는 발생하지 않음을 확인했습니다(Table 1, Figure 3).
- 강철에 주조된 A380 합금의 경우, 용착을 위한 임계 온도는 덴드라이트 응집 온도(약 560°C) 또는 액상선 온도(575°C)와 관련이 있는 것으로 제안됩니다. 실험 결과 575°C에서는 용착이 발생했지만 550°C에서는 발생하지 않았습니다(Table 1).
- 세라믹 코팅된 H-13 강 금형/코어핀에서는 균열이나 코팅이 기판에서 박리된 영역과 같은 국부적인 코팅 파손 부위에서 용착이 시작됩니다(Figure 4).
- 용융 알루미늄은 이러한 파손 부위를 통해 침투하여 하부 H-13 강과 반응하여 철 알루미나이드(iron aluminides)를 포함하는 작은 피트 또는 반응 영역을 형성합니다(Figure 5).
- 이러한 피트는 측면으로 성장하여 인접한 코팅을 약화시키고, 또한 강철 기지 내부로 깊이 성장합니다. 이 성장은 복잡한 철 알루미나이드(예: Al12Fe6Si5, Al15Fe6Si5, Al4FeSi) 및 특히 반응 영역의 바깥쪽 가장자리에서 Al-풍부 fcc 상의 형성을 포함합니다(Figure 6).
- Al-풍부 fcc 상은 다이캐스팅 온도에서 액체 상태일 수 있으며(Al 함량이 61.5 wt% 초과하고 T > 655°C인 경우), 금속간 화합물의 추가 침식을 촉진하고 확산을 향상시켜 피트 성장을 가속화합니다.
- 인접한 피트는 결국 연결되어 종종 지그재그 형태를 나타내는 더 크고 연속적인 용착 영역을 형성합니다(Figure 7).
- 코팅이 완전히 제거된 심하게 영향을 받은 영역에서는 충돌하는 용융 알루미늄에 의한 강철 기지의 지속적인 침식 및 용해가 금형 표면에 역구배(negative draft) 또는 언더컷(undercuts) 형성을 유발할 수 있으며(Figure 8), 이는 주물 취출을 심각하게 방해하고 잠재적으로 손상을 일으킬 수 있습니다.
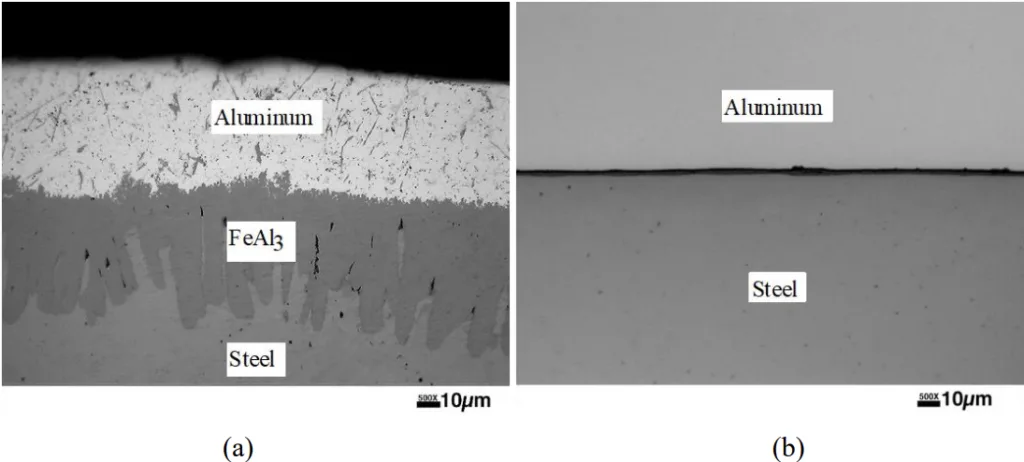
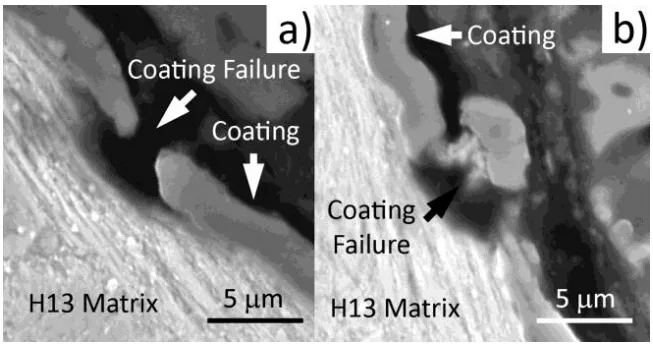
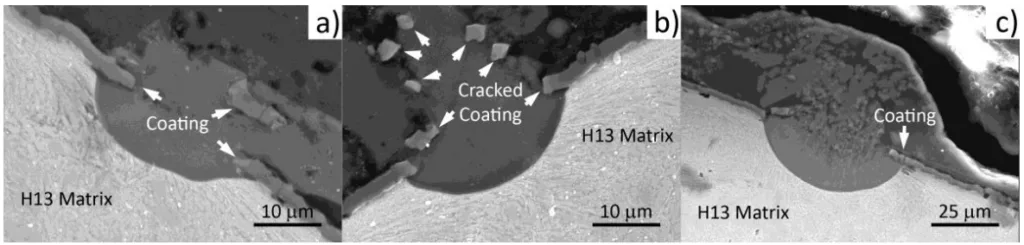
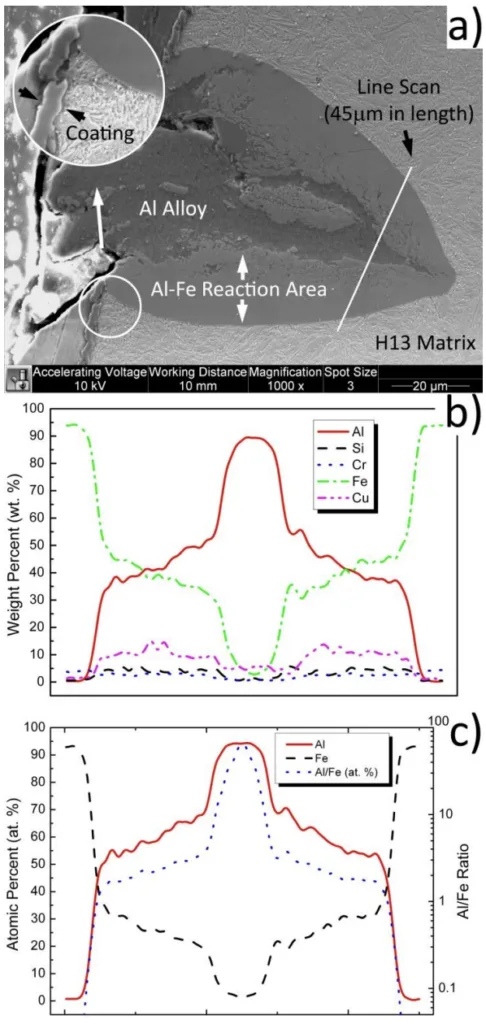
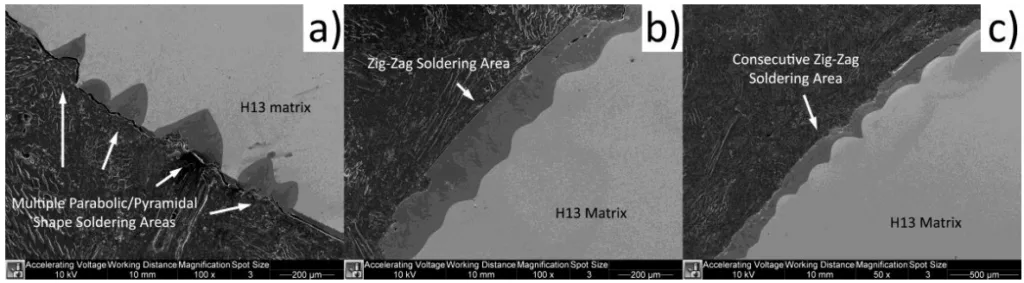
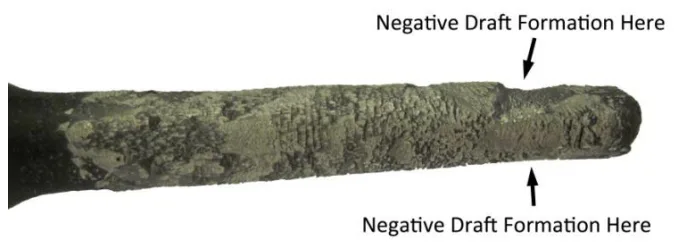
그림 목록 (Figure Name List):
- Figure 1: 순수 알루미늄을 철 금형에 주조하는 경우 금형 표면에서의 가능한 알루미늄 조성 및 온도 프로파일, 그리고 결과 상을 보여주는 개략도. 금형 표면에서 세 영역을 식별할 수 있음. 용착은 영역 I에서 발생함 [4].
- Figure 2. 금형 용착 메커니즘의 개략도, (a) 표면 온도가 임계 온도 655°C보다 높을 때 금형 표면에 액체가 존재하는 것, (b) 이 액상의 응고 시 주물과 금형 사이에 접합부가 형성되는 것을 나타냄.
- Figure 3. 세 가지 경우에 대해 금형 표면에서 관찰된 전형적인 미세 구조: (a) 용착을 초래하는 야금학적 결합, (b) 강철과 알루미늄 사이의 반응 부재.
- Figure 4: 두 가지 방식의 코팅 파손을 보여주는 SEM 이미지: (a) 균열 및 (b) 박리.
- Figure 5 반응 영역의 SEM 이미지: (a) 용착 영역에서 측면 성장으로 인해 파손된 코팅, (b) 균열되어 이동한 코팅, (c) 씻겨 나간 코팅.
- Figure 6: 포물선/피라미드 형태의 전형적인 피트 또는 용착 영역: (a) SEM 이미지 및 라인 스캔 위치, (b) 스캔된 라인을 따른 다섯 가지 원소의 중량 백분율 곡선 및 (c) 원자 백분율 곡선 및 Al/Fe 비율 곡선.
- Figure 7: 용착 영역의 SEM 이미지: (a) 포물선/피라미드 형태의 여러 피트, (b) 및 (c) 연속적인 지그재그 형태의 용착 영역 두 가지 모습.
- Figure 8: 코어핀에 역구배 또는 언더컷 형성의 개략도 (화살표 표시).
7. 결론 (Conclusion):
화학적 상호작용에 의해 구동되는 알루미늄 다이캐스팅에서의 금형 용착은 금형 표면 온도가 임계 임계값(Tc)을 초과할 때 발생하며, 금형-주물 계면의 Fe-Al 금속간 화합물 층 내에 Al-풍부 액상의 형성을 유도합니다. 이 액상은 응고되어 주물을 금형에 결합시킵니다. 강철에 대한 순수 알루미늄의 경우, Tc는 Al-Fe 공정 온도(655°C)입니다. A380과 같은 합금의 경우, Tc는 액상선 또는 덴드라이트 응집 온도와 관련이 있습니다. 표면 처리되지 않은 강철에서는 이 과정이 Tc 이상에서 직접적으로 이 액상 형성을 유도하는 확산 및 반응을 포함합니다. 코팅된 금형(예: H-13 강 위의 세라믹)에서는 국부적인 코팅 결함(균열, 박리)에 의해 시작되는 점진적인 파손 메커니즘을 따릅니다. 용융 알루미늄은 노출된 강철과 반응하여 측면 및 깊이 방향으로 성장하는 피트를 형성합니다. 이 성장은 철 알루미나이드 및 Al-풍부 fcc 상의 형성을 포함하며, 액체 상태인 경우 침식 및 추가 반응을 가속화합니다. 피트는 결국 합쳐지고 심각한 침식은 언더컷 또는 역구배를 유발하여 부품 취출을 방해할 수 있습니다. Al-풍부 fcc 상의 존재와 거동은 표면 처리되지 않은 경우와 코팅된 경우 모두에서 용착 메커니즘의 핵심입니다.
(참고: 원 논문에는 "4. Conclusions"라는 제목이 있지만 그 아래에 본문이 없습니다. 이 결론은 논문 전체에 걸쳐 제시된 초록과 주요 연구 결과로부터 종합되었습니다.)
8. 참고 문헌 (References):
- [1] NADCA website, http://www.diecasting.org/].
- [2] Y.L. Chu, P.S. Cheng and R. Shivpuri, Transactions (Rosemont, Illinois: North American Die Casting Association, 1993), pp.361-371
- [3] D. Argo, R.J. Barnhurst, and W. Walkington, “NADCA Sponsored Research: The cause of Soldering in Zinc Die Casting,” Transactions (Rosemont, Illinois: North American Die Casting Association, 1997), pp. 77-82
- [4] Q. Han and S. Viswanathan, “Analysis of the Mechanism of Die Soldering in Aluminum Die Casting," Metall. Mater. Trans., 2003, 34A, pp. 139-46.
- [5] H. Baker et al. (Eds), ASM Handbook, vol.3, Alloy Phase Diagrams (Materials Park, OH: ASM International), 1992.
- [6] W. Kajoch and A. Fajkiel, “Testing the Soldering Tendencies of Aluminum Die Casting Alloys," Transactions (Rosemont, Illinois: North American Die Casting Association, 1991), pp.67-74.
- [7] S. Shankar and D. Apelian, "Die Soldering – A Metallurgical Analysis of the Molten Aluminum/Die Interface Reactions,” Transactions (Rosemont, Illinois: North American Die Casting Association, 1997), pp. 243-251.
- [8] V.G. Rivlin and G.V. Raynor, “Critical Evaluation of Constitution of Aluminum-Iron-Silicon System,” Int. Met. Rev., 26 (1981) pp. 133-152.
- [9] R.W. Richards, R.D. Jones, P.D. Clements and H. Clarke, “Metallurgy of Continuous Hot Dip Aluminizing,” Int. Mat. Rev., 39 (1994) pp. 191-212.
- [10] J. Wallace, D. Schwam, Y. Zhu, S. Birceanu, “Soldering Characteristics of Die Materials and the Effect on Cooling Link Placement on Die Life,” Transactions of the North American Die Casting Association, Rosemont, IL, 2002, T03-041.
- [11] G. Engleman, S. Viswanathan, C.A. Blue, Q. Han, and N.B. Dahotre, “High Density Infrared Coatings for Soldering Resistance,” Transactions of the North American Die Casting Association, Rosemont, IL, 2002, T02-43.
- [12] J. Moore, S. Carrera, J. Lin, O. Salas, B. Mishra, G. Mustoe, and P. Ried, “The Development of Surface Engineered Coating Systems for Aluminum Pressure Die Casting Dies: An Evaluation of Six Commercial Coatings,” Transactions of the North American Die Casting Association, Rosemont, IL, 2003, T03-025.
- [13] L. Arnberg, L. Bäckerud, and G. Chai, Solidification Characteristics of Aluminum Alloys, vol.3, Dendrite Coherency (American Foundrymen's Society, Inc., 1996), 115
- [14] Z. W. Chen and M. Z. Jahedi, Die Erosion and Its Effect on Soldering Formation in High Pressure Die Casting of Aluminum Alloys, Materials and Design, 1999, vol. 20, pp.303-309.
- [15] J. Song, T. Denouden, and Q. Han, “Mechanisms of Soldering Formation on Coated Core Pins," Metall Mater Trans, 2012, 43A, pp. 415-421.
- [16] S. Shankar, and D. Apelian, “Die Soldering: Mechanism of the Interface Reaction between Molten Aluminum Alloy and Tool Steel,” Metall. Mater. Trans., 2002, 33B, pp. 466-476.
- [17] J. V. Skoff, "A New Approach to the Cause of High Pressure Die Steel Erosion, Pitting and Breakout", NADCA Transactions, 2010, pp. T10-051.
9. 저작권 (Copyright):
- 본 자료는 "Q. Han"의 논문입니다. "[Mechanism of die soldering during aluminum die casting]"을 기반으로 합니다.
- 논문 출처: https://doi.org/10.1007/s41230-015-1116-6
본 자료는 상기 논문을 바탕으로 요약되었으며, 상업적 목적의 무단 사용을 금지합니다.
Copyright © 2025 CASTMAN. All rights reserved.