이 소개 자료는 "[International Journal of Engineering and Management Research]"에 게재된 "[Analysis and Optimisation of High Pressure Die Casting Parameters to Achieve Six Sigma Quality Product Using Numerical Simulation Approach]" 논문을 기반으로 합니다.
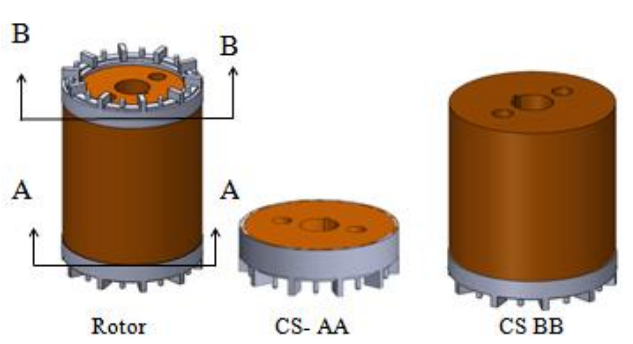
1. 개요:
- 제목: 수치 시뮬레이션 접근법을 이용한 식스 시그마 품질 제품 달성을 위한 고압 다이캐스팅 공정 변수 분석 및 최적화 (Analysis and Optimisation of High Pressure Die Casting Parameters to Achieve Six Sigma Quality Product Using Numerical Simulation Approach)
- 저자: Suraj R. Marathe¹ and Dr. Carmo E. Quadros² (¹연구원, 기계공학과, ASSAM DON BOSCO 대학교, 인도; ²교수, 기계공학과, ASSAM DON BOSCO 대학교, 인도)
- 발행 연도: 2021년 (2월)
- 발행 학술지/학회: International Journal of Engineering and Management Research
- 키워드: 고압 다이캐스팅(HPDC), 공정 변수, ProCAST, 시뮬레이션, 식스 시그마 품질
2. 초록:
고압 다이캐스팅 중 최적의 공정 변수 설정을 예측하기 위해 수치 시뮬레이션 접근법이 제안되었습니다. 최적 변수 중 온도는 다른 변수보다 주조 품질에 더 큰 영향을 미치는 것으로 나타났습니다. 본 연구 결과는 다이캐스팅에서 잘못된 공정 변수 설정으로 인해 발생하는 주조 결함 해결책을 찾는 데 유용했습니다. 따라서 수치 최적화 기법과 주조 시뮬레이션의 조합은 다이캐스팅 산업에서 주조 제품 품질을 개선하는 도구 역할을 합니다. 본 논문은 결함 발생에 기여하는 사출 압력, 용탕 온도, 유지 시간, 플런저 속도와 같은 핵심 변수를 분석하고 최적화하는 것을 목표로 합니다. 본 연구에서는 유한 요소 해석 기술을 사용하는 ProCAST 시뮬레이션 소프트웨어를 이용하여 최적의 압력, 온도, 유지 시간 및 플런저 속도 변수를 제시하고자 노력했습니다. 용탕 온도, 사출 압력, 유지 시간, 플런저 속도를 변화시켜 변수를 최적화하는 수치 해석은 열점에서의 응고 시간과 관련하여 시뮬레이션 모델의 결함 분석 연구에 필수적인 변수입니다.
3. 서론:
다이캐스팅 공정은 종종 품질 저하와 생산성 문제로 어려움을 겪으며, 보고된 불량률은 기포(blowhole), 불충분한 사출 압력, 부적절한 충전 시간, 기공(porosity), 열점(hot spot)과 같은 결함으로 인해 11~13%에 달합니다. 무결점 부품을 달성하기 위해서는 공정 변수를 제어하는 것이 중요하며, 이를 위해서는 이러한 변수가 주조 결함에 미치는 영향을 이해해야 합니다. 본 연구는 로터(rotor) 부품의 다이캐스팅을 조사하며, 수치 시뮬레이션을 사용하여 공정 변수의 영향을 분석하고, 부품과 두 개의 단면(용탕 주입구 및 하단부, 그림 1 참조)에 초점을 맞춥니다.
4. 연구 요약:
연구 주제 배경:
고압 다이캐스팅(HPDC) 공정은 공정 변수의 변동으로 인해 품질 문제와 낮은 생산성에 취약합니다. 이러한 변동은 기포, 기공, 부적절한 충전, 열점과 같은 주조 결함을 유발하여 상당한 불량률(11-13%)을 초래할 수 있습니다.
기존 연구 현황:
Mohanty와 Jena(2014)와 같은 이전 연구에서는 무결점 부품을 달성하기 위한 공정 변수 제어의 필요성을 강조했으며, 업계의 높은 불량률을 지적했습니다. 불량의 주요 원인으로는 잘못된 변수 설정과 직접적으로 관련된 결함이 확인되었습니다.
연구 목적:
본 연구는 수치 시뮬레이션 접근법을 사용하여 핵심 HPDC 변수, 특히 사출 압력, 용탕 온도, 유지 시간, 플런저 속도를 분석하고 최적화하는 것을 목표로 합니다. 목표는 응고 시간을 최소화하여 주조 결함을 줄이고 제품 품질을 식스 시그마 수준으로 향상시키는 최적의 변수 설정을 결정하는 것입니다.
핵심 연구:
본 연구의 핵심은 유한 요소 해석(FEA)을 사용하는 ProCAST 시뮬레이션 소프트웨어를 이용하여 로터 부품의 HPDC 공정을 모델링하는 것입니다. 체계적인 수치 최적화 기법이 적용되었으며, 정의된 범위 내에서 네 가지 주요 변수(온도, 압력, 속도, 유지 시간)를 변화시켰습니다(표 2). 연구는 이러한 변화가 로터 및 특정 단면(CS AA 및 CS BB, 그림 1)의 열점에서의 응고 시간에 미치는 영향을 분석합니다. 목표는 결함 분석 및 품질 개선에 필수적인 것으로 간주되는 최소 응고 시간을 산출하는 변수 조합을 식별하는 것입니다.
5. 연구 방법론
연구 설계:
본 연구는 수치 시뮬레이션 및 최적화 방법론을 사용합니다. 로터 부품의 HPDC 공정은 유한 요소법(FEM) 기반의 ProCAST 소프트웨어를 사용하여 시뮬레이션되었습니다. 다단계 최적화 접근법(그림 5, 그림 6)이 사용되었으며, 네 가지 주요 변수(온도, 압력, 속도, 유지 시간) 각각을 정의된 범위 내에서 25개 수준으로 순차적으로 분석하여(표 2, 그림 4) 응고 시간을 최소화했습니다.
데이터 수집 및 분석 방법:
- 모델링: 로터 주물, 게이팅 시스템 및 금형의 3D 기하학적 모델이 Unigraphics NX4.0을 사용하여 생성되었고 *.x_t 파일로 변환되었습니다.
- 메싱: 유한 요소 메시는 ProCAST의 MeshCAST 모듈을 사용하여 생성되었습니다(그림 7).
- 시뮬레이션: ProCAST 소프트웨어를 사용하여 HPDC 공정을 시뮬레이션했습니다. 초기 경계 조건 및 공정 변수(표 2)는 전처리기에서 정의되었습니다. 총 7800개의 시뮬레이션 실험이 계획되었습니다(그림 4).
- 분석: 시뮬레이션 결과(예: 응고 시간, 고상 분율, 수축 기공, 열점, 충전 시 온도, 가스 미충전 민감도, 사출 압력)는 Visual-Viewer (Cast) 후처리기를 사용하여 분석되었습니다. 주요 분석은 각 최적화 단계에서 로터 부품 및 단면 AA, BB의 응고 시간을 최소화하는 데 중점을 두었습니다(그림 8-15). 최적 변수는 이러한 결과를 기반으로 결정되었습니다(표 3-10). Crompton Greaves Ltd (CGL)의 산업 데이터는 열 사이클(그림 2, 표 1) 및 실험 설정(그림 3)에 대한 맥락을 제공했습니다.
연구 주제 및 범위:
본 연구는 알루미늄 합금 로터 부품(외경 100mm, 내경 25mm, 높이 135mm)의 고압 다이캐스팅(HPDC)에 초점을 맞춥니다. 범위에는 네 가지 중요한 공정 변수의 수치 시뮬레이션 및 최적화가 포함됩니다:
- 용탕 온도 (T): 680 °C ~ 752 °C
- 사출 압력 (P): 300 bar ~ 348 bar
- 플런저 속도 (V): 116.6 m/s ~ 121.4 m/s
- 유지 시간 (HT): 52 s ~ 76 s
목표는 주조 결함을 줄이고 식스 시그마 품질을 달성하기 위한 수단으로 응고 시간을 최소화하는 것입니다.
6. 주요 결과:
주요 결과:
- ProCAST를 사용한 수치 시뮬레이션 접근법은 HPDC 로터 부품의 응고 시간을 최소화하기 위한 최적의 공정 변수 설정을 성공적으로 식별했습니다.
- 온도는 연구된 다른 변수(압력, 속도, 유지 시간)에 비해 주조 품질에 더 큰 영향을 미치는 것으로 밝혀졌습니다.
- 다단계 최적화 프로세스를 통해 다음과 같은 최적의 변수 범위가 도출되었습니다(표 11):
- 온도 (T): 728 ≤ T ≤ 731 °C
- 압력 (P): 330 ≤ P ≤ 332 bar
- 속도 (V): 119.6 ≤ V ≤ 120 m/s
- 유지 시간 (HT): 67 ≤ HT ≤ 69 s (참고: 표 11에는 65 ≤ HT ≤ 69로 명시되어 있으나, 단계별 결과 표 3, 6, 8, 10에서는 최적 시간이 각각 67, 69, 69, 68초로 나타남. 최종 결론에서는 67초를 언급함. 해당 요약 표와의 일관성을 위해 표 11의 범위를 사용함).
- 식별된 평균 최적 설정은 T = 730 °C, P = 331 bar, V = 119.8 m/s, HT = 67 s였습니다.
- 이러한 최적 변수로 수행된 확인 실험 결과, 로터 기여로 인한 모터 불량률이 4.35%에서 0.89%로 감소했다고 보고되었습니다(CGL 데이터).
- 최적 설정으로 수행된 ProCAST 시뮬레이션 결과, 충전 시간, 총 수축 기공 및 미충전 민감도 측면에서 심각한 결함이 없는 것으로 나타났습니다(그림 16).
- Figure 3: Experimentation setup: vertical die casting machine of the capacity of 100 Tons (Industrial caseCGL)
- Figure 4: The proposed experimentation set up for solving flow for optimisation of parameters
- Figure 5: Block diagram showing four stages of numerical simulation for the optimisation of solidification time
- Figure 6: Flow diagram showing the final stage of a numerical simulation approach
- Figure 7: Meshed and position of cross-sections of the rotor component
- Figure 8: Graphical representation of temperature analysis of the rotor and at cross-sections AA and BB
- Figure 14: Graphical representation of holding time at various sections
- Figure 15: (a, b, and c) Simulation output for solidification time at rotor component, Cross-Section AA and BB.
그림 목록:
- Figure 1: 수치 해석을 위한 다이캐스팅 로터 부품 및 AA, BB 단면
- Figure 2: 초 단위 타임라인으로 표시된 다이캐스팅 열 공정 사이클 (산업 사례-CGL)
- Figure 3: 실험 설정: 100톤 용량의 수직 다이캐스팅 기계 (산업 사례-CGL)
- Figure 4: 파라미터 최적화를 위한 유동 해결을 위한 제안된 실험 설정
- Figure 5: 응고 시간 최적화를 위한 수치 시뮬레이션의 4단계를 보여주는 블록 다이어그램
- Figure 6: 수치 시뮬레이션 접근법의 최종 단계를 보여주는 흐름도
- Figure 7: 로터 부품의 메싱 및 단면 위치
- Figure 8: 로터 및 AA, BB 단면에서의 온도 분석 그래픽 표현
- Figure 9: (a, b, c) 로터 부품, 단면 AA 및 BB에서의 응고 시간 시뮬레이션 결과
- Figure 10: 다양한 단면에서의 압력 분석 그래픽 표현
- Figure 11: (a, b, c). 로터 부품, 단면 AA 및 BB에서의 응고 시간 시뮬레이션 결과
- Figure 12: 다양한 단면에서의 플런저 속도 분석 그래픽 표현
- Figure 13: (a, b, c) 로터 부품, 단면 AA 및 BB에서의 응고 시간 시뮬레이션 결과
- Figure 14: 다양한 단면에서의 유지 시간 분석 그래픽 표현
- Figure 15: (a, b, c) 로터 부품, 단면 AA 및 BB에서의 응고 시간 시뮬레이션 결과
- Figure 16: (a, b, c,) 충전 시간, 총 수축 기공 및 미충전 민감도에 대한 ProCAST 시뮬레이션 결과
7. 결론:
수치 시뮬레이션 알고리즘은 응고 시간을 최소화함으로써 HPDC 공정 변수를 효과적으로 최적화했습니다. 낮은 응고 시간은 일반적으로 기포 및 기공과 같은 내부 결함 감소와 관련이 있습니다. 본 연구는 다이캐스팅 공정 변수의 영향을 연구하기 위해 7800개의 시뮬레이션 실험을 수행했습니다. 식별된 최적 변수(주입 온도 730 °C, 압력 331 bar, 플런저 속도 119.8 m/s, 유지 시간 67 s)는 확인 실험을 통해 검증되었으며, 로터 결함으로 인한 모터 불량률이 크게 감소(4.35%에서 0.89%로, CGL 데이터)한 것으로 나타났습니다. 이러한 최적 설정에서의 ProCAST 시뮬레이션은 최소한의 결함(충전 시간, 수축 기공, 미충전)을 확인했습니다. 온도는 주조 품질에 가장 큰 영향을 미치는 것으로 나타났습니다. 수치 최적화 기법과 주조 시뮬레이션의 조합은 다이캐스팅 산업에서 주조 제품 품질을 개선하는 귀중한 도구 역할을 하며, 식스 시그마 품질을 향한 최적 변수 설정을 위한 의사 결정 도구를 제공합니다.
8. 참고 문헌:
- [1] Domkin, K., Hattel, J., & Thorborg, J. (2009). Modelling of high temperature and diffusion controlled die soldering in high aluminium pressure die casting. Journal of Material Processing Technology, 209(8), 4051-4061.
- [2] Fiorese, E., Richiedei, D., & Bonollo, F. (2016). Improving the quality of die castings through optimal plunger motion planning: analytical computation and experimental validation. International Journal of Advanced Manufacturing Technology, 88, 1475–1484.
- [3] Fu, J. & Wang, K. (2014) Modelling and simulation of the die casting process for A356 semi-solid alloy. Procedia Engineering, 81, 1565–1570.
- [4] Jorstad, J. & Apelian, D. (2009). Pressure assisted processes for high integrity aluminium castings - part 1. International Journal of Metal Casting, 250-254.
- [5] Kumar, S., Gupta, A., & Chandna, P. (2012). Optimisation of process parameters of pressure die casting using taguchi methodology. World Academy of Science, Engineering and Technology, 6, 590-594.
- [6] Lattanzi, L., Fabrizi, A., Fortini, A., Merlin, M., & Timelli, G. (2017). Effects of microstructure and casting defects on the fatigue behaviour of the high-pressure die-cast AlSi9Cu3 (Fe) alloy. Procedia Structural Integrity, 7, 505-512.
- [7] Mohanty, C. & Jena, B. (2014). Optimisation of aluminium die casting process using artificial neural network. International Journal of Emerging Technology and Advanced Engineering, 4(7), 146-149.
- [8] Syrcos, G. (2002). Die casting process optimisation using taguchi methods. Journal of Material Processing Technology, 135, 68-74.
- [9] Wang, L., Turnley, P., & Savage, G. (2011) Gas content in high pressure die castings. Journal of Materials Processing Technology, 211, 1510–1515.
- [10] Zhang, M., Xing, S., Xiao, L., Bao, P., Liu, W., & Xin, Q. (2008). Design of process parameters for direct squeeze casting. Journal of University of Science and Technology, 15(3), 339-343.
- [11] Zhang, X., Xiong, S., & Xu, Q. (2006). Numerical methods to improve the computational efficiency of solidification simulation for the investment casting process. Journal of Materials Processing Technology, 173, 70-74.
9. 저작권:
- 본 자료는 "Suraj R. Marathe and Dr. Carmo E. Quadros"의 논문입니다. "[Analysis and Optimisation of High Pressure Die Casting Parameters to Achieve Six Sigma Quality Product Using Numerical Simulation Approach]" 논문을 기반으로 합니다.
- 논문 출처: https://doi.org/10.31033/ijemr.11.1.15
본 자료는 상기 논문을 바탕으로 요약되었으며, 상업적 목적의 무단 사용을 금지합니다.
Copyright © 2025 CASTMAN. All rights reserved.