본 논문 요약은 Archives of Foundry Engineering에 발표된 논문 "Advances in Technology of Soluble Cores for Die Castings"를 기반으로 작성되었습니다.
1. 개요:
- 제목: 다이캐스팅용 수용성 코어 기술의 발전 (Advances in Technology of Soluble Cores for Die Castings)
- 저자: P. Jelínek, E. Adámková, F. Mikšovský, J. Beňo
- 발행 연도: 2015년
- 발행 저널/학회: Archives of Foundry Engineering
- 키워드: 염 코어, 압착 및 사출 성형 제조, 식용 소금 사용, 코어 접합, 세척수 염도, 전기 전도도
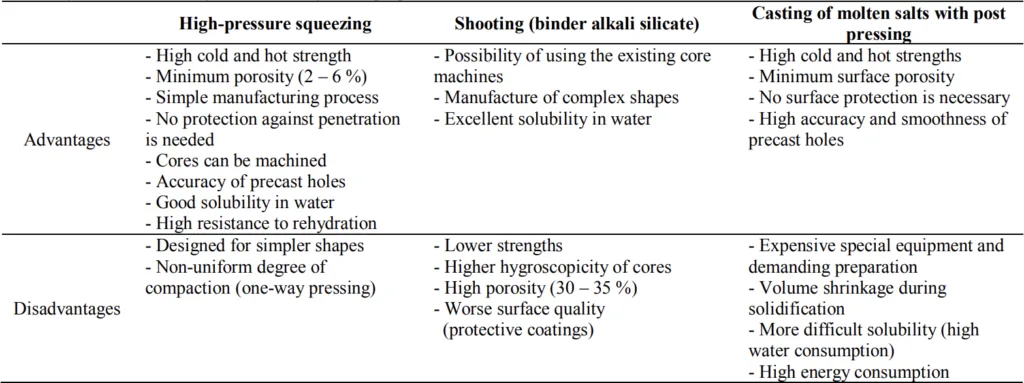
2. 연구 배경:
주조품 설계의 복잡성이 증가함에 따라 기존의 단순 금속 코어에 의존하는 다이캐스팅 기술로는 한계에 직면하고 있습니다. 기존 방식으로는 복잡한 내부 형상을 가진 주조품에 대한 증가하는 요구를 충족하기 어렵습니다. 따라서 "수용성" 코어, 즉 로스트 코어라고도 알려진 새로운 제조 공정에 대한 관심이 높아지고 있습니다[1]. 수용성 코어 재료 중에서도 무기염은 물에 대한 용해성이 뛰어나 주조 후 코어 제거를 간소화할 수 있다는 점에서 가장 큰 잠재력을 가지고 있습니다. 그러나 이러한 염 코어는 다음과 같은 여러 가지 중요한 요구 사항을 충족해야 합니다.
- 치수 정확도
- 충분한 보관 수명 (수화 저항성)
- 고온 강도 (최대 700 °C)
- 주조 공동 표면의 매끄러움 (낮은 Ra 값)
- 물에 대한 용이한 용해성
일부 연구에서는 염 코어가 낮은 금형 충전 속도 (35 m/s 미만) 및 레오캐스팅과 같은 공정에 적합하다고 제안하지만[2], 고압 다이캐스팅에 적용하기 위해서는 추가적인 개발이 필요합니다. 본 논문은 바인더를 사용하여 고압 압착 및 사출 성형 기술로 제조된 염 코어 개발을 다루고 있으며, 염 종류 및 첨가제가 코어 특성에 미치는 영향에 대해 탐구합니다. 또한 염 코어 접합 방법과 코어 제거에 사용되는 물의 염도 관리에 대해서도 조사합니다.
3. 연구 목적 및 연구 질문:
본 연구는 고압 다이캐스팅용 수용성 염 코어 기술을 발전시키는 것을 목표로 합니다. 주요 연구 목적은 염 코어의 제조 및 적용을 최적화하기 위해 다음과 같은 핵심 연구 질문을 해결하는 것입니다.
- 고압 압착 및 사출 성형 방법이 염 코어의 특성, 특히 강도와 기공률에 어떤 영향을 미치는가?
- NaCl 염 결정의 모양과 다양한 첨가제의 첨가가 염 코어의 강도 특성에 어떤 영향을 미치는가?
- 복잡한 내부 형상을 만들기 위해 염 코어를 접합하고 염 코어와 금속 부품을 결합하는 효과적인 접합 기술을 개발할 수 있는가?
- 코어 제거에 사용되는 순환수의 염도를 효과적으로 모니터링하고 제어하여 효율적인 코어 제거와 잠재적인 물 재활용을 보장할 수 있는가?
본 연구는 다음과 같은 가설을 설정합니다.
- 특정 첨가제를 복합 염 제형에 첨가하면 염 코어의 기계적 강도가 향상될 것이다.
- 코어 제거에 사용되는 물의 전기 전도도를 모니터링하면 물 염도를 안정적으로 평가하고 관리하여 일관된 코어 용해를 보장할 수 있다.
4. 연구 방법론:
본 연구는 염 코어 기술의 다양한 측면을 평가하기 위해 실험적 설계를 채택했습니다. 조사된 코어 제조 방법은 알칼리 규산염 바인더를 사용한 고압 압착 및 사출 성형입니다. 데이터 수집은 제조된 염 코어의 주요 특성 및 관련 공정 측정에 중점을 두었습니다.
- 코어 강도: 굽힘 강도 (압착 코어용) 및 전단 강도 (접합 코어용)를 측정하여 기계적 성능을 평가했습니다.
- 기공률: 다양한 방법으로 제조된 코어의 밀도를 이해하기 위해 기공률 수준을 평가했습니다.
- 용해성: 물과 포화 염 용액에서 코어 용해 속도를 측정하여 코어 제거 효율성을 평가했습니다.
- 흡습성: 시간 경과에 따른 무게 증가 측정을 통해 공기 중 수분 흡수에 대한 코어의 민감도를 측정했습니다.
- 전기 전도도 및 pH: 코어 용해에 사용된 물에서 이러한 매개변수를 모니터링하여 염도 변화를 추적했습니다.
- 미세 구조 분석: 주사 전자 현미경 (SEM) 및 에너지 분산형 X선 분광법 (EDX)을 사용하여 염 입자의 모양과 첨가제 분포를 분석했습니다.
연구 범위는 다음을 포함합니다.
- 염 종류: 식용 암염, 알프스 소금, 고운 바다 소금, 화학적으로 순수한 NaCl (p.a.) 등 다양한 종류의 식용 소금을 테스트했습니다.
- 첨가제: ZrSiO4, Al2O3, Fe2O3 및 SiO2와 같은 첨가제를 사용하여 코어 특성을 향상시키기 위한 복합 염을 제형화했습니다.
- 바인더: 사출 성형법에는 알칼리 규산염을 바인더로 사용했습니다.
- 접착제: 시판되는 여러 종류의 접착제와 연구 개발 접착제 (VŠB-TUO)를 사용하여 염 코어 및 염-금속 접합부 접합을 평가했습니다.
5. 주요 연구 결과:
본 연구는 염 코어의 제조 및 특성에 대한 몇 가지 주요 결과를 도출했습니다.
- 제조 방법의 영향: 고압 압착 방식은 알칼리 규산염 바인더를 사용한 사출 성형 방식에 비해 일관되게 더 높은 굽힘 강도를 가진 염 코어를 생산했습니다.
- 염 종류 및 강도: KCl 염 코어가 NaCl 코어보다 더 높은 냉간 및 열간 강도를 나타냈습니다. NaCl 염 중에서는 분쇄 암염과 바다 소금이 알프스 소금보다 더 높은 강도를 나타냈지만, 표준 NaCl (p.a.) 또한 높은 강도를 보였습니다.
- 입자 모양의 영향: "쌍뿔형, 규칙적인" 모양의 NaCl 입자 (표준 NaCl p.a.에서 발견됨)는 압착 및 사출 성형 코어 모두에서 높은 강도를 나타냈습니다. 반대로 입방형 입자 (알프스 소금)는 강도가 낮았습니다.
- 첨가제의 효과: 복합 염, 특히 α-Al2O3의 첨가는 염 코어의 냉간 및 열간 강도를 크게 증가시켰습니다. 1차 굽힘 강도는 PUR 콜드 박스 코어보다 약 3배 높은 9 MPa를 초과했습니다.
- 기공률 및 강도: 압착 성형법에서 압착력을 증가시키면 코어 기공률이 6% 미만으로 감소하여 유리질의 단일체형 코어가 생성되었고, 강도와 표면 매끄러움 (Ra < 5 µm)이 향상되었습니다.
- 염 코어 접합: 다양한 산업용 접착제와 연구 개발 접착제 (VŠB-TUO)를 사용하여 염 코어 접합 (염-염 및 염-금속)의 효과를 입증했습니다. 염-염 접합부의 전단 강도는 63~105 N/cm² 범위였고, 염-금속 접합부는 160~232 N/cm² 범위였습니다.
- 수질 염도 모니터링: 전기 전도도는 코어 용해 중 수질 염도를 안정적으로 나타내는 지표임이 입증되었습니다. 염도 (NaCl 농도)가 증가하면 용해 속도가 느려졌습니다. 폐쇄 루프 수순환 시스템에서 효과적인 코어 용해를 보장하기 위해 전기 전도도의 임계값을 결정할 수 있습니다.
그림 목록:
- 그림 1. 압착 및 사출 성형 코어의 흡습성 비교
- 그림 2. 다양한 종류의 식용 소금으로 압착 및 사출 성형된 염 코어의 강도 비교
- 그림 3. 분쇄 암염 (샘플 No 1, 2)의 파단면 및 EDX 화학 성분 분석
- 그림 4. 알프스 소금 (샘플 No 3, 4)의 규칙적인 입방형 입자 및 염 입자 표면에 항응고 첨가제 (MgCO3, CaCO3) 존재를 확인하는 EDX 분석
- 그림 5. 표준 NaCl (p.a.) (샘플 No 6)의 쌍뿔형 규칙적인 모양 및 EDX 화학 성분 분석
- 그림 6. 접합된 코어의 용해 중 H 2400 접착제 상태
- 그림 7. 접합된 코어의 용해 중 VŠB – TUO 접착제 상태
- 그림 8. 순수한 물과 두 종류의 포화 용액에서 염 코어 용해 비교
- 그림 9. pH 및 전기 전도도에 따른 염 코어 용해 속도 변화
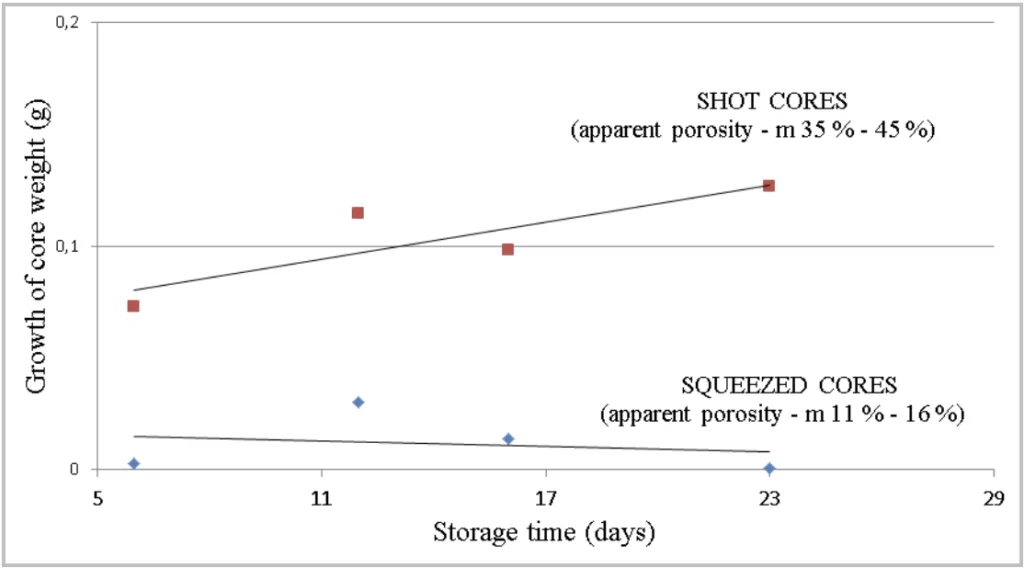
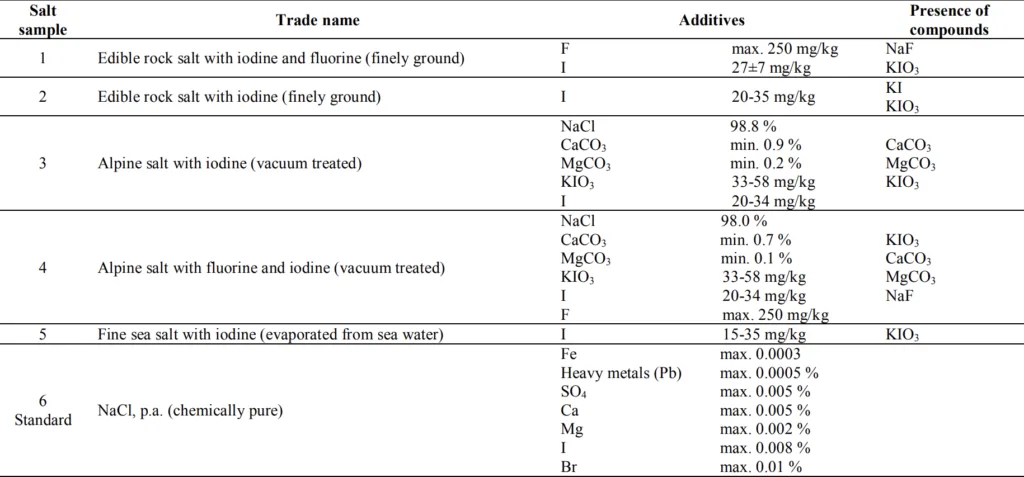
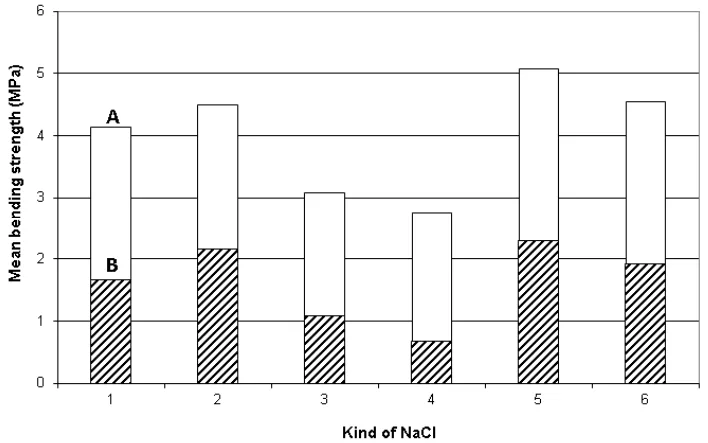
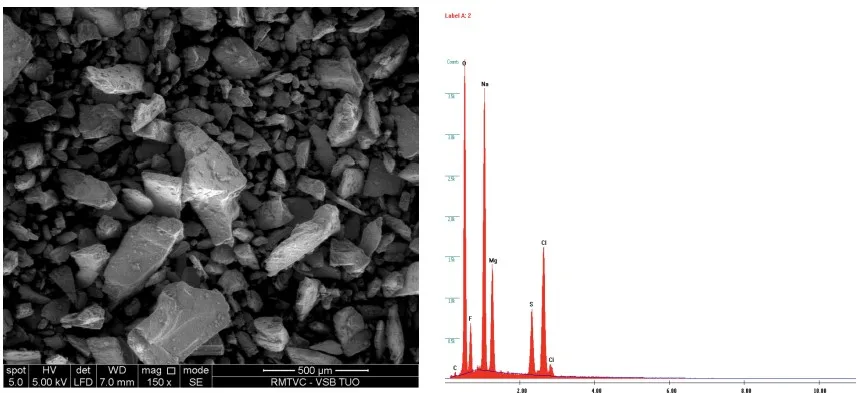
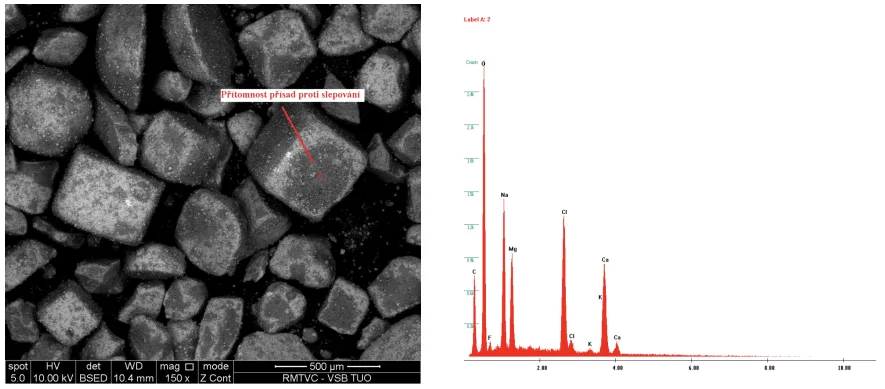
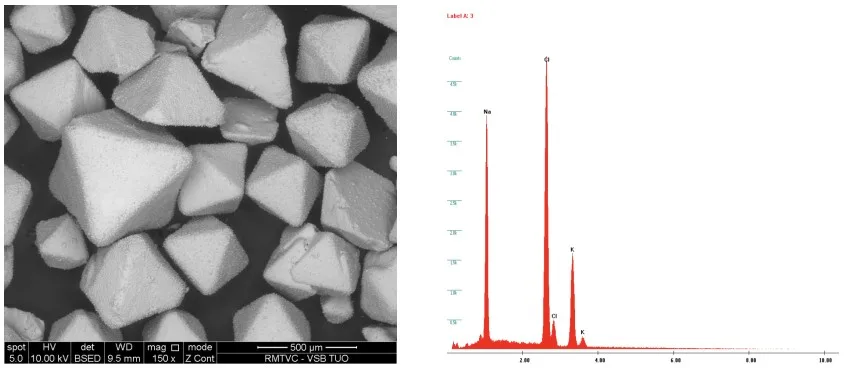
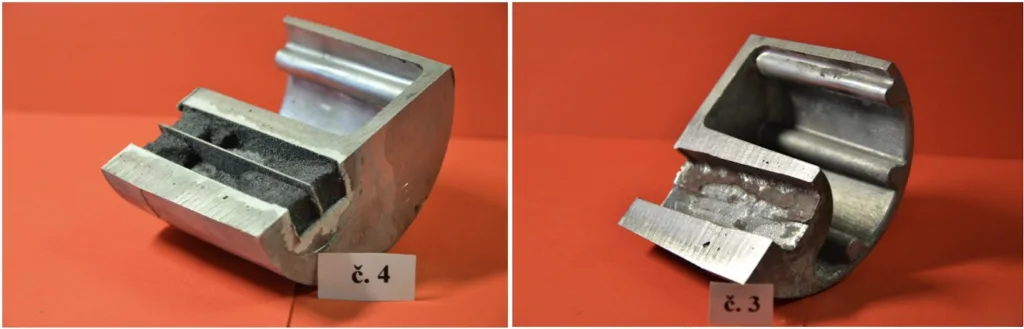
6. 결론 및 논의:
본 연구는 수용성 염 코어가 고압 다이캐스팅 공정과 같이 까다로운 주조 기술에도 상당한 잠재력을 제공한다는 것을 확인시켜 줍니다. 본 연구는 제조 방법, 염 종류, 입자 모양 및 첨가제가 염 코어의 특성에 미치는 중요한 영향을 강조합니다. 고압 압착 성형은 고강도 코어를 얻는 데 우수한 방법으로 나타났습니다. NaCl의 "쌍뿔형, 규칙적인" 입자 모양과 첨가제를 사용한 복합 염은 코어 강도를 향상시키는 핵심 요소입니다. 또한 접합 기술의 성공적인 개발은 염 코어를 사용하여 복잡한 내부 주조 형상에 대한 설계 가능성을 확장하며, 금속 부품과의 조합도 가능합니다. 전기 전도도 모니터링의 적용은 코어 제거 공정에서 수질 염도를 관리하는 실용적인 방법을 제공하며, 잠재적으로 폐쇄 루프 수재활용 시스템을 가능하게 합니다.
연구의 학문적 의의:
본 연구는 염 코어의 성능에 영향을 미치는 요인에 대한 포괄적인 조사를 제공함으로써 다이캐스팅 분야에 귀중한 지식을 제공합니다. 수용성 코어의 재료 선택, 제조 공정 및 접합 기술에 대한 깊이 있는 이해를 제공하여 고압 다이캐스팅에 적용하기 위한 과학적 기반을 발전시킵니다.
실용적 의미:
본 연구 결과는 염 코어 기술을 구현하려는 다이캐스팅 전문가에게 실용적인 지침을 제공합니다. 본 연구는 다음과 같은 통찰력을 제공합니다.
- 원하는 코어 강도 및 용해성을 달성하기 위한 적절한 염 종류 및 첨가제 선택.
- 필요한 코어 특성 및 복잡성에 따른 제조 방법 (압착 vs. 사출 성형) 최적화.
- 복잡한 코어 형상 조립을 위한 효과적인 접합 기술 활용.
- 효율적이고 지속 가능한 코어 제거 공정을 위한 전기 전도도 모니터링 구현.
연구의 한계:
본 연구는 귀중한 통찰력을 제공하지만, 주로 실험실 규모의 실험에 초점을 맞추고 있다는 점에 유의해야 합니다. 이러한 결과를 산업 다이캐스팅 환경에서 검증하고 대량 생산에서 염 코어 기술의 장기적인 성능과 비용 효율성을 평가하기 위해서는 추가 연구가 필요합니다.
7. 향후 후속 연구:
향후 연구 방향은 다음 사항에 초점을 맞춰야 합니다.
- 접합된 염 코어의 치수 정확도를 조사하고 개선 방법을 개발합니다.
- 주조 중 성능을 향상시키기 위해 접합부에 보호 코팅 적용을 탐구합니다.
- 염 코어의 제조 및 적용을 산업 생산 수준으로 확장합니다.
- 산업 응용 분야를 위한 폐쇄 루프 코어 제거 시스템에서 수질 염도 제어를 최적화합니다.
- 기존 방법과 비교하여 염 코어 기술의 포괄적인 비용-편익 분석 및 환경 영향 평가를 수행합니다.
8. 참고 문헌:
- [1] Pacyniak, R. & Kaczorowski, R. (2010). Ductile cast iron obtaining by Inmold method with use of LOST FOAM process. Archives of Foundry Engineering. 10(1), 101-104. ISSN: 1897-3310.
- [2] Michels, H., Bűnck, M. & Bührig - Polaszek, A. (2010). Suitability of lost cores in rheocasting process. Transactions of Nonferrous Metals Society of China. 20, 948-953. DOI: 10.1016/S1003-6326(10)60612-7.
- [3] Dańko, J., Dańko, R. (2009). Theoretical and technological aspects of the production processes of foundry cores blown In 50. Konferencji Krzepniecie i Krystalizacja Metali (pp. 71-86). Katowice - Gliwice, Poland: Polska Academia Nauk, Komisja Odlewnictwa. ISBN: 978-83-929266-0-3. (폴란드어)
- [4] Holtzer, M., Dańko, R. (2009). Theory and practice of regeneration and utilization of waste molding and core. In 50. Konferencji Krzepniecie i Krystalizacja Metali (pp. 133-152). Katowice - Gliwice, Poland: Polska academia nauk, Komisja Odlewnictwa. ISBN: 978-83-929266-0-3. (폴란드어).
- [5] Kallien, L., Böhnlein, Ch., Dworak, A. & Müller, B. (2013). Ergebnisse aus dem Forschungsprojekt 3-D-Freiform medienführende Kanäle im Druckguss. Giesserei Praxis. 100(12), 36-43. ISSN: 0016-9781
- [6] Fuchs, B., Eibisch, H. & Körner, C. (2013). Core viability simulation for salt core technology in high pressure die casting. International Journal of Metalcasting. 7(3), 39-45. ISSN: 1939-5981.
- [7] Fuchs, B., et. all (2014). Angepasste Wärmebehandlung von druckgegossenen Aluminiumstrukturbauteilen mit verlorenem Salzkerne. Giesserei Praxis. 101(06), 52-59. ISSN:0016-9781
- [8] Yaokawa, J., Miura, D., Anzai, K., Yamada, Y., & Yoshii, H. (2007). Strength of salt core composed of alkali carbonate and alkali chloride mixtures made by casting technique. Materials transactions. 48(5), 1034-1041.
- [9] Stingl, P., & Shiller, G. (2009). Gichte und rückstandfreie Entkernung - Salzkerne für den Aluminiumguss. Giesserei-Erfahrungsaustausch. 6, 4-8.
- [10] Adámková, E., Jelínek, P., & Študentová, S. (2013). Application of cooking salts in manufacture of water soluble cores for high pressure die casting (Aplikace kuchyňských solí při výrobě vodou rozpustných jader odlitků tlakového lití). Materials and technology. 61(11-12), 689-693. ISSN: 1580-2949, 1580-3414.
- [11] Jelínek, P., Mikšovský, F., Beňo, J. & Adámková, E. (2013). Development of Foundry Cores Based on Inorganic Salts. Materials and technology. 47(6), 689-693. ISSN: 1580-2949, 1580-3414.
- [12] Fuchs, B. & Körner, C. (2013). Dwell pressure induced compression of lost salt cores in high pressure die casting. International Foundry Research. 3, 18-23. ISSN: 0046-5933.
- [13] Rupp, S. & Heppes, F. (2013). Combicore – Giesskerne für den Druckguss. Giesserei-Erfahrungsaustausch. 3/4, 6-9.
- [14] Fabbroni, M. (2013) Lost Core Ein industrieller Prozesspfad für hochwertige Salzkerne. Giesserei Praxis. 100(07), 82-83. ISSN: 0016-9781
- [15] Kaneko, Y. & Morita, A. (1970) 6th SDCE international die casting congress. PAPER NO. 91, Cleveland, Ohio, November 16-19.
- [16] Loper, C. R. et. all. (1985) The Use of Salt In Foundry Cores. AFS Transactions, 85-82, 545-560.
- [17] Jelínek, P., Mikšovský, F., & Adámková, E. (2012). Influencing the strength characteristics of salt cores soluble in water. Slévárenství. 60(3-4), 85-89. ISSN: 0037-6825.
- [18] Major Gabryś, K., & Dobosz, M. (2009). A new ester hardener for moulding sands with water glass having slower activity. Archives of Foundry Engineering. 9(4), 125-128. ISSN: 1897-3310.
9. 저작권:
본 자료는 [P. Jelínek, E. Adámková, F. Mikšovský, J. Beňo]의 논문: [다이캐스팅용 수용성 코어 기술의 발전 (Advances in Technology of Soluble Cores for Die Castings)]을 기반으로 합니다.
논문 출처: [https://doi.org/10.2478/afe-2015-0005]
본 자료는 위 논문을 기반으로 요약되었으며, 상업적 목적으로 무단 사용하는 것을 금지합니다.
Copyright © 2025 CASTMAN. All rights reserved.