1. 개요:
- 제목: 가변 두께 알루미늄 합금 판재 주조 시뮬레이션 (Simulation of variable thickness aluminum alloy plate casting)
- 저자: G. S. Reddy, Md. Hafeez
- 발행 연도: 2024년
- 발행 학술지/학회: Journal of Physics: Conference Series
- 키워드: 주조 시뮬레이션, 열 흐름, 유체 흐름, 냉각 곡선, 응고 (Casting simulation, heat flow, fluid flow, cooling curves, solidification)
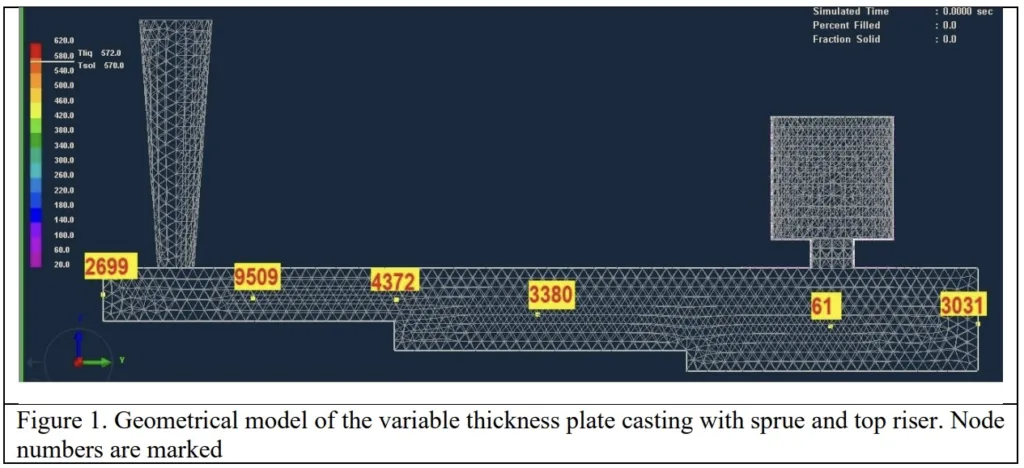
2. 연구 배경:
- 연구 주제의 사회적/학문적 맥락: 알루미늄 합금은 다재다능한 특성으로 인해 점점 중요해지고 있으며, 특히 성장하는 전기 자동차 제조 분야에서 두드러집니다. 자동차 산업은 알루미늄 부품 사용을 늘리는 방향으로 전환하고 있습니다.
- 기존 연구의 한계: 주조 시뮬레이션 예측과 실제 주조 결과 사이에는 인지된 격차가 존재합니다.
- 연구의 필요성: 본 연구는 알루미늄 합금 주물의 응고 과정을 더 잘 이해하고 거시적 수축을 완화하기 위해 필요합니다. 주조 공정에서 응고 모델의 신뢰성과 실제 적용 가능성을 향상시키는 것을 목표로 합니다.
3. 연구 목적 및 연구 질문:
- 연구 목적: 본 연구의 주요 목적은 가변 두께 알루미늄 합금 판재 주조의 시뮬레이션을 조사하여 응고 과정을 더 잘 이해하고 주물에서 거시적 수축을 줄이는 방법을 찾는 것입니다.
- 주요 연구 질문: 본 연구는 시뮬레이션을 가변 두께 알루미늄 합금 판재의 주조 공정을 이해하고 최적화하는 데 효과적으로 사용할 수 있는 방법, 특히 응고 과정 및 수축 완화에 초점을 맞춰 답하고자 합니다.
- 연구 가설: 본 연구는 시뮬레이션이 가변 두께 알루미늄 합금 판재 주조에서 수축 기공을 최소화하거나 제거하기 위해 주조 공정을 이해하고 최적화하는 데 유용한 도구가 될 수 있다는 가설 하에 진행됩니다.
4. 연구 방법론
- 연구 설계: 본 연구는 가변 두께 알루미늄 합금 판재 주조의 응고 과정을 모델링하기 위해 유한 요소 해석을 사용하는 시뮬레이션 기반 접근 방식을 채택합니다.
- 자료 수집 방법: 자료는 시뮬레이션 결과에서 수집하며, 주조 모델 내의 온도 분포, 냉각 곡선, 유체 흐름 및 응고 패턴에 중점을 둡니다.
- 분석 방법: 분석은 시뮬레이션 결과를 수치적으로 검토하여 응고 과정을 이해하고, 잠재적인 수축 영역을 식별하고, 주조 설계의 효과를 평가하는 것을 포함합니다. 연구는 열 전달, 유체 흐름 및 응고 역학에 중점을 둡니다.
- 연구 대상 및 범위: 연구는 Al-13%Si 합금과 사형 주형을 사용한 가변 두께 판재 주조의 시뮬레이션에 초점을 맞춥니다. 기하학적 모델에는 블라인드 상부 라이저와 개방형 스프루가 포함됩니다. 비교 분석을 위해 측면 라이저를 특징으로 하는 대안적 구성도 구현되었습니다.
5. 주요 연구 결과:
- 주요 연구 결과: 시뮬레이션 결과는 가변 두께 알루미늄 합금 판재 주조에서 수축 기공이 없음을 나타냅니다. 최종 응고 이벤트는 라이저와 스프루에서 관찰됩니다. 온도 분포 및 냉각 곡선은 원하는 온도 구배에 맞춰 방향성 응고를 확인합니다.
- 통계적/정성적 분석 결과: 시뮬레이션 결과에 대한 정성적 분석은 다음을 보여줍니다:
- 수축 기공의 부재: "시뮬레이션 결과는 수축 기공의 부재를 보여줍니다 (Simulation outcomes reveal the absence of shrinkage porosity)".
- 최종 응고 위치: "최종 응고 이벤트는 라이저와 스프루에서 발생합니다 (with the last solidification events occurring in risers and sprue)".
- 방향성 응고: "온도 분포 및 냉각 곡선은 원하는 온도 구배에 맞춰 방향성 응고를 확인합니다 (The temperature distribution and cooling curves affirm directional solidification, aligning with desired temperature gradients)."
- 자료 해석: 결과는 알루미늄 합금에서 수축 기공을 줄이는 데 있어 실리콘의 역할을 강조합니다. 본 연구는 정확한 시뮬레이션 결과를 위해 온도 의존적 특성 및 초기 경계 조건을 포함한 고품질 입력 데이터의 중요성을 강조합니다. 난류, 탄성률 비, 방향성 응고와 같은 요소에 초점을 맞춘 시뮬레이션 프로세스 데이터의 지속적인 모니터링은 예측 모델을 개선하는 데 중요합니다.
- 그림 목록:
- 그림 1. 스프루 및 상부 라이저가 있는 가변 두께 판재 주조의 기하학적 모델 (Geometrical model of the variable thickness plate casting with sprue and top riser).
- 그림 2. 주형 공동으로 액체 알루미늄 합금 충전. 유체 흐름 속도 벡터는 난류 없는 단방향 흐름을 보여줍니다 (Filling of liquid aluminum alloy into a mold cavity. Fluid flow velocity vectors show unidirectional flow without turbulence).
- 그림 3. 라이저 공동으로 충전. 관찰된 최대 유체 속도는 0.621 m/s입니다 (Filling into riser cavity. The maximum fluid velocity observed is 0.621 m/s).
- 그림 4. 스프루 및 라이저에서 발견된 수축 기공 (Shrinkage porosity found in sprue and riser).
- 그림 5. 응고 후 온도 분포 (Temperature distribution during post-solidification).
- 그림 6. 냉각 곡선은 스프루에서 라이저로의 방향성 응고를 보여줍니다 (Cooling curves demonstrate directional solidification from the sprue into the riser).
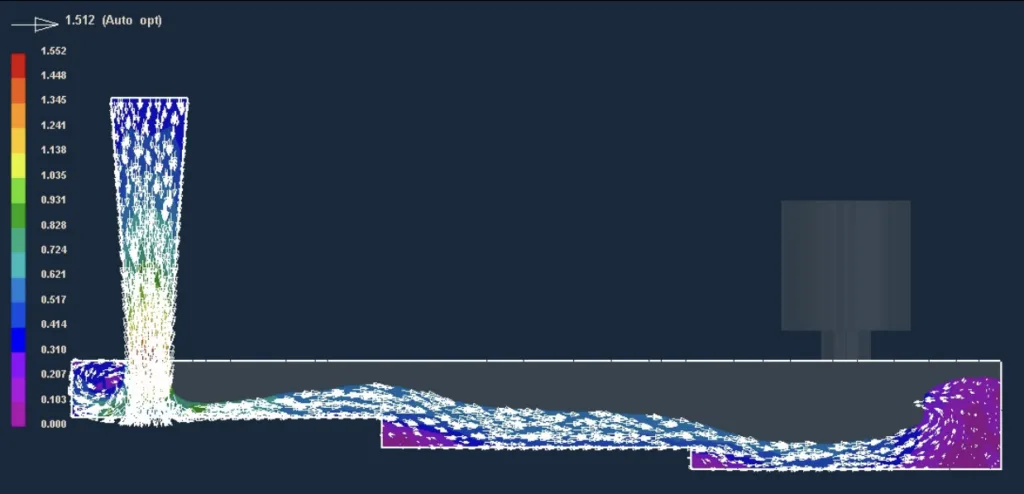
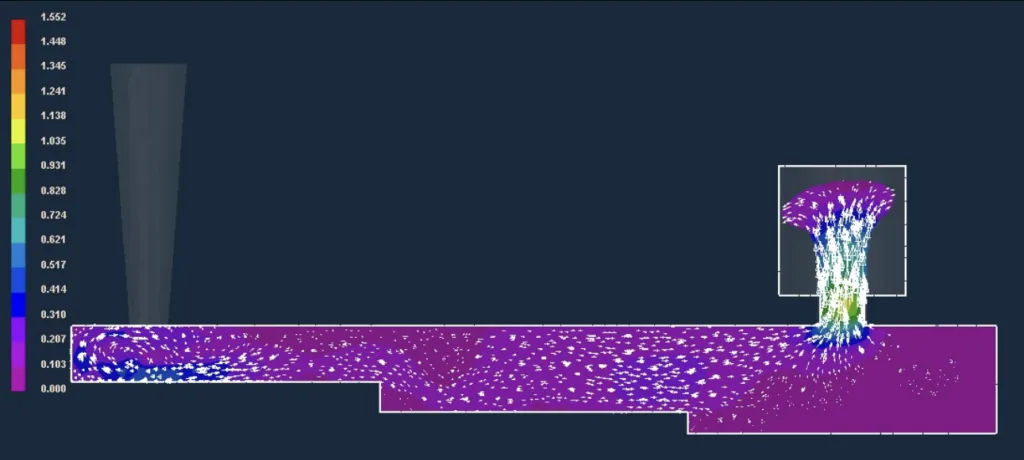
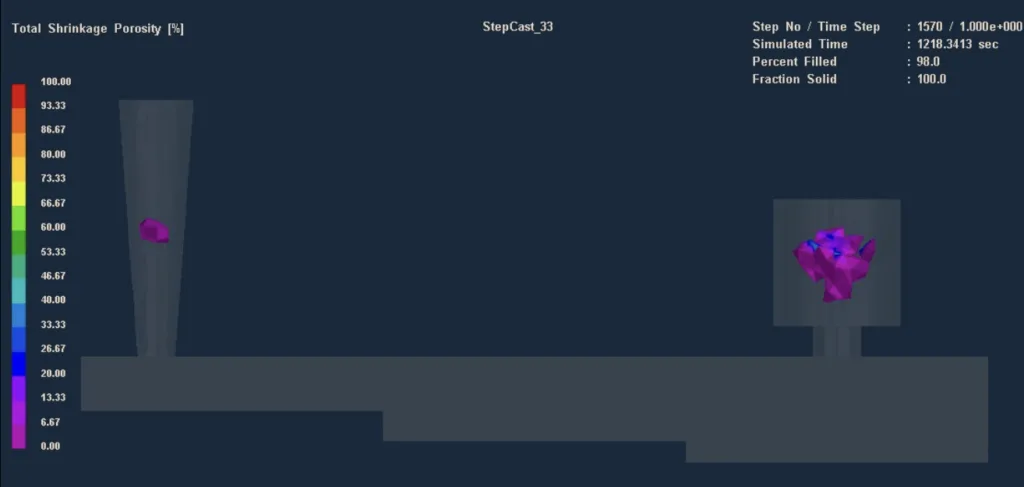
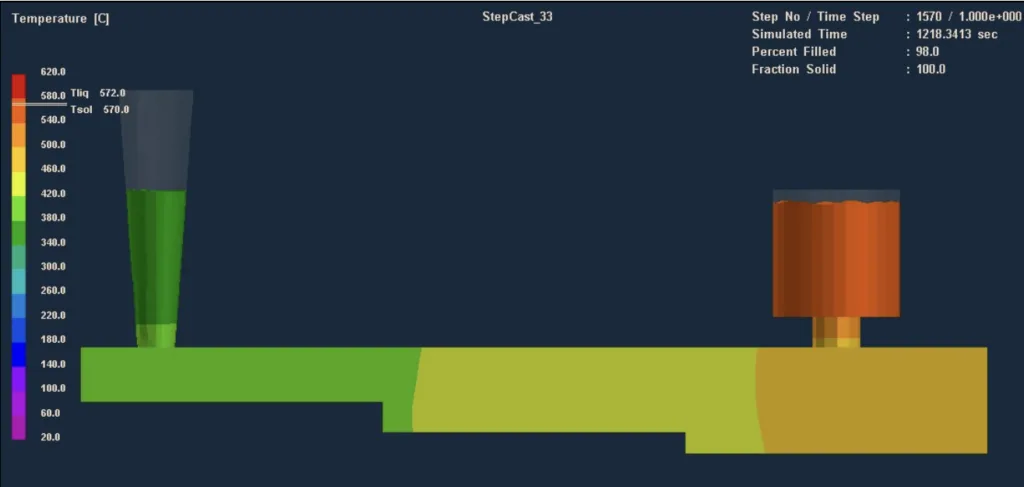
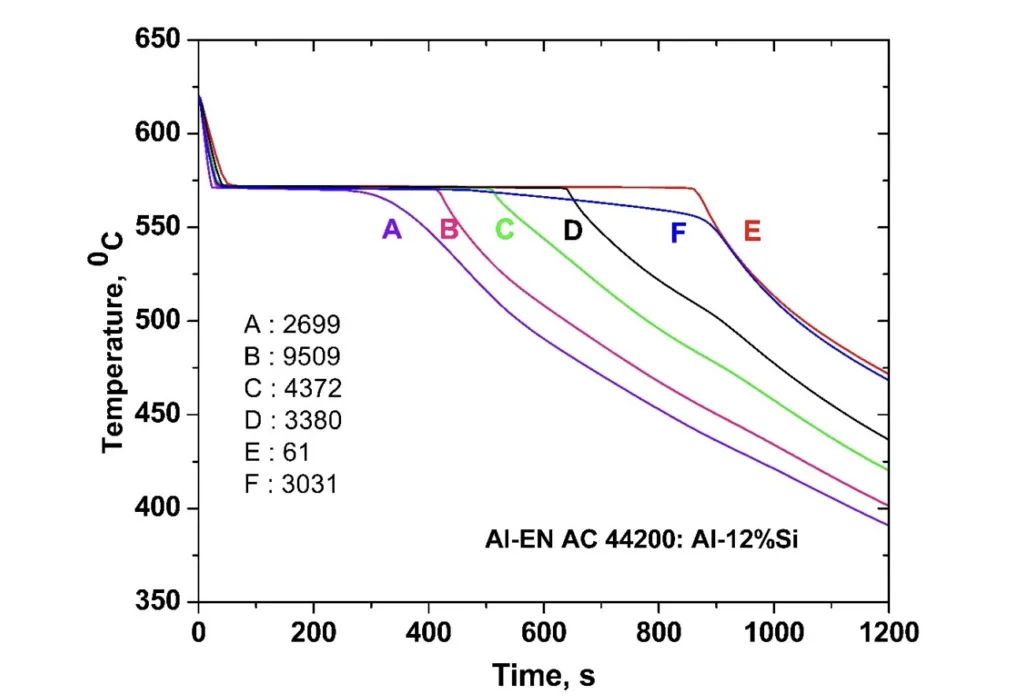
6. 결론 및 논의:
- 주요 결과 요약: 가변 두께 알루미늄 합금 판재 주조의 시뮬레이션은 수축 기공이 없음을 성공적으로 입증했으며, 최종 응고는 라이저와 스프루에서 발생했습니다. 시뮬레이션은 또한 방향성 응고를 확인했습니다.
- 연구의 학문적 의의: 본 연구는 알루미늄 합금 응고 과정에 대한 이해를 발전시키는 데 기여합니다. 시뮬레이션과 실제 주조 결과 사이의 격차를 해소하여 응고 모델의 신뢰성과 적용 가능성을 향상시킵니다.
- 실용적 의미: 본 연구는 특히 알루미늄 합금 주물에서 거시적 수축을 완화하기 위해 시뮬레이션을 통해 주조 공정을 최적화하는 데 유용한 통찰력을 제공합니다. 본 연구 결과는 알루미늄 부품 채택을 늘리고 있는 자동차 산업과 특히 관련이 있습니다.
- 연구의 한계: 본 연구는 시뮬레이션 결과의 정확도가 온도 의존적 재료 특성 및 초기 경계 조건을 포함한 입력 데이터의 품질에 크게 의존한다는 점을 강조합니다. 이는 주조 시뮬레이션에서 신중한 데이터 관리 및 검증의 필요성을 강조합니다.
7. 향후 후속 연구:
- 후속 연구 방향: 향후 연구는 합금 조성, 다양한 주조 기술 및 시뮬레이션 방법론의 지속적인 탐구에 초점을 맞춰야 합니다. 이는 다양한 산업 분야에서 알루미늄 합금의 성능을 더욱 향상시키고 유용성을 넓힐 것입니다.
- 추가 탐구가 필요한 영역: 시뮬레이션 프로세스 데이터를 지속적으로 감사하여 예측 모델을 개선하는 데 추가 탐구가 필요합니다. 주요 영역에는 주형 충전 중 난류 역학, 체적 대 표면적 비의 탄성률, 방향성 응고 제어가 포함됩니다.
8. 참고 문헌:
- G.M. Scamans, N. Birbilis, R.G. Buchheit, “Corrosion of Aluminium and its Alloys", Shreir's Corrosion, Volume 3, 2010, Pages 1974-2010; https://doi.org/10.1016/B978-044452787-5.00095-0
- J. Gilbert Kaufman, and Elwin L. Rooy, “Aluminum alloy castings: Properties, Processes, and applications", 2004 ASM International. pp 1-321.
- Baser, T. A., Umay, E., & Akinci, V. (2022). “New trends in aluminum casting alloys for automotive applications. The Eurasia Proceedings of Science Technology engineering and mathematics, 21, 79-87. https://doi.org/10.55549/epstem.1227541.
- C. Berlanga-Labari, M. V. Biezma-Moraleda, and Pedro J. Rivero, “Corrosion of Cast Aluminum Alloys: A Review", MDPI journal, Metals 2020, 10, 1384; doi:10.3390/met10101384
- Mariem Ben Saada, Mohamed El Mansouri, “Assessment of the effect of 3D printed sand mold thickness on solidification process of AlSi13 casting alloy", International Journal of Advanced Manufacturing Technology, 2021, 114 (5-6), pp.1753-1766. 10.1007/s00170-021-06999-3. HAL-03220855
- Meet Upadhyay, Tharmalingam Sivarupan, Mohamed El Mansori, “3D printing for rapid sand casting- A review", Journal of Manufacturing Processes, 2017, 29, pp.211-220. 10.1016/j.jmapro.2017.07.017. hal-02417595.
- D. Martinez, C. Bate, and G. Manogharan, “Towards functionally graded sand molds for metal casting: Engineering thermo-mechanical properties using 3D sand printing", 2020 The Minerals, Metals & Materials Society, https://doi.org/10.1007/s11837-019-03975-x, Materials properties, ESI Group, 04-June-2013
- Cusato, N.; Nabavizadeh, S.A.; Eshraghi, M. A Review of large-scale simulations of microstructural evolution during alloy solidification. Metals 2023, 13, 1169. https://doi.org/10.3390/met13071169, Academic editors: Changing Fang and Chang Yong Jo.
- Philip King and Guha Manogharan, “Novel experimental method for metal flow analysis using open molds for sand casting”, International Journal of Metal casting/Volume 17, Issue 4, 2023. Pp 2892-2903.
- Bate, C.; King, P.; Sim, J.; Manogharan, G, “A novel approach to visualize liquid aluminum flow to advance casting science, Materials, 2023, 16, 756. https://doi.org/10.3390/ma16020756.
- Griffiths, W. D., & Atkinson, H. V. (1999). The influence of alloy composition on shrinkage porosity formation during the solidification of aluminum alloys. Metallurgical and Materials Transactions A, 30(2), 361-372.
- El-Bealy, M. M., Abd-Elhady, E. A., & Abdel-Rahman, A. M. (2019). Simulation of shrinkage defects in aluminum alloy castings using numerical modeling. Journal of Manufacturing Processes, 41, 72-80.
- GS Reddy, WJ Mascarenhas, JN Reddy, Metallurgical Transactions B 24, 677 -684.
- Cheng Guª, Colin D. Ridgewaya, Emre Cinkilica, Yan Luª, Alan A. Luo a,*
- Olawale Olarewaju Ajibola, et al, "Effects of molding sand permeability and pouring temperatures on properties of cast 6061 aluminum alloy", International Journal of Metals, Volume 2015, Article ID 632021, pp 21-13, http://dx.doi.org/10.1155/2015/632021
- Neuser, M.; Grydin, O.; Andreiev, A.; Schaper, M. Effect of Solidification Rates at Sand Casting on the Mechanical Joinability of a Cast Aluminium Alloy. Metals 2021, 11, 1304. https://doi.org/10.3390/met11081304
- Dash, S.S.; Chen, D. A, “Review on processing-microstructure-property relationships of Al-Si alloys"; Recent advances in deformation behavior, Metals 2023, 13, 609. https://doi.org/10.3390/met13030609.
- For a Livable Climate: Net-Zero Commitments Must Be Backed by Credible Action. Available online: https://www.un.org/en/climatechange/net-zero-coalition (accessed on 20 January 2023).
- Svendsen, A. Aluminum Continues Unprecedented Growth in Automotive Applications. Available online: https://www.lightmetalage.com/news/industry-news/automotive/aluminum-continues-unprecedented-growth-in-automotiveapplications/(accessed on 20 January 2023
- Javidani, M.; Larouche, D. Application of CastAl-Si Alloys in Internal Combustion Engine Components. Int. Mater. Rev. 2014, 59, 132–158. [CrossRef].
- Torres, R.; Esparza, J.; Velasco, E.; Garcia-Luna, S.; Colas, R. Characterisation of an Aluminum Engine Block. Int. J. Microstructure. Mater. Prop. 2006, 1, 129. [CrossRef]
- Czerwinski, F. Thermal Stability of Aluminum Alloys. Materials 2020, 13, 3441. [CrossRef]
- Fan, Y.; Makhlouf, M.M. The Al-Al3Ni Eutectic Reaction: Crystallography and Mechanism of Formation. Metall. Mater. Trans. A 2015, 46, 3808–3812. [CrossRef]
- Czerwinski, F.; Kasprzak, W.; Sediako, D.; Emadi, D.; Shaha, S.; Friedman, J.; Chen, D.L. High-Temperature Aluminum Alloys for Automotive Powertrains; Cast Aluminum AlloysWere Developed with High-Temperature Tensile and Fatigue Strengths to Withstand Elevated-Temperature Applications in Modern Engines. Adv. Mater. Process. 2016, 174, 16–21.
- Geoffrey Sigworth, and Timothy A. Kuhn, “Grain Refinement of Aluminum Casting Alloys", International Journal of Metal casting, September 2007, 115(2):1-12; DOI:10.1007/BF03355416.
- Jun Wang, Shuxian He, and Baode Sun, "Grain refinement of Al-Si alloy (A356) by melt thermal treatment", Journal of Materials Processing Technology, October 2003, 141(1):29-34, DOI:10.1016/S0924-0136(02)01007-5
- Zamani, Mohammadreza, “Al-Si Cast alloys - Microstructure and mechanical properties at ambient and elevated temperatures”, Ph.D. thesis, 2017, Jönköping University, School of Engineering.
- Fracchia, E.; Gobber, F.S.; Rosso, M. "Effect of alloying elements on the Sr modification of Al-Si cast alloys”. Metals 2021, 11, 342. https:// doi.org/10.3390/met11020342.
- Sathyapal Hegde and K. Narayan Prabhu, “Modification of eutectic silicon in Al-Si alloys", J Mater Sci (2008) 43:3009–3027, DOI 10.1007/s10853-008-2505-5, pp 1-19.
- X Cao and J Campbell, "Hard spot defects in aluminum-silicon cast alloys", Shape Casting: The John Campbell Symposium Edited by Murat Tiryakioglu and Paul N. Crepeau TMS (The Minerals, Metals, & Materials Society), 2005 https://www.researchgate.net/publication/287911378
- Anil Saigal, Edwin R. Fuller Jr, “Analysis of stresses in aluminum-silicon alloys", Computational Materials Science, Volume 21, Issue 1, May 2001, Pages 149-158.
- R.B. Gundlach et al, “Thermal fatigue resistance of hypoeutectic aluminum-silicon casting alloys", AFS Trans. (1994)
- Bao Quoc Doan, Dinh Tuyen Nguyen, Minh Nhat Nguyen, Tri Hieu L, Thi Minh Hao Dong, Le Hung Duong, “A Review on Properties and Casting Technologies of Aluminum Alloy in The Machinery Manufacturing", Journal of Mechanical Engineering Research and Developments ISSN: 1024-1752 CODEN: JERDFO Vol. 44, No. 8, pp. 204-217 the Published Year 2021.
- G.S. Reddy and G.R.K. Murthy, "Liquid forging of an aluminum alloy”, Trans of the IIM, 31 (5), 484-487, 1978.
- G.S. Reddy, Ph.D. thesis, “Solidification of metals and alloys under pressure", 1987, Institute of Technology, BHU, Varanasi, India.
- GS Reddy, K Saurabh, DM Krishna, ‘Numerical Simulation Of Directionally Solidified CM247LC High Pressure Turbine Blade', Materials Today: Proceedings 4 (8), 7820-7830.
- GS Reddy, K. Saurabh, R Yedu Krishnan, Numerical Simulation of CM247SX Single Crystal High-Pressure Turbine Vane, Materials Today Proceedings Science Direct, 7837 – 7847.
9. 저작권:
- 본 자료는 G. S. Reddy, Md. Hafeez의 논문: Simulation of variable thickness aluminum alloy plate casting을 기반으로 합니다.
- 논문 출처: doi:10.1088/1742-6596/2837/1/012092
This material was summarized based on the above paper, and unauthorized use for commercial purposes is prohibited.
Copyright © 2025 CASTMAN. All rights reserved.