본 소개 글은 STM Journals에서 발행한 ["Injection Parameters Setting in High-Pressure Die Casting"] 논문의 연구 내용입니다.
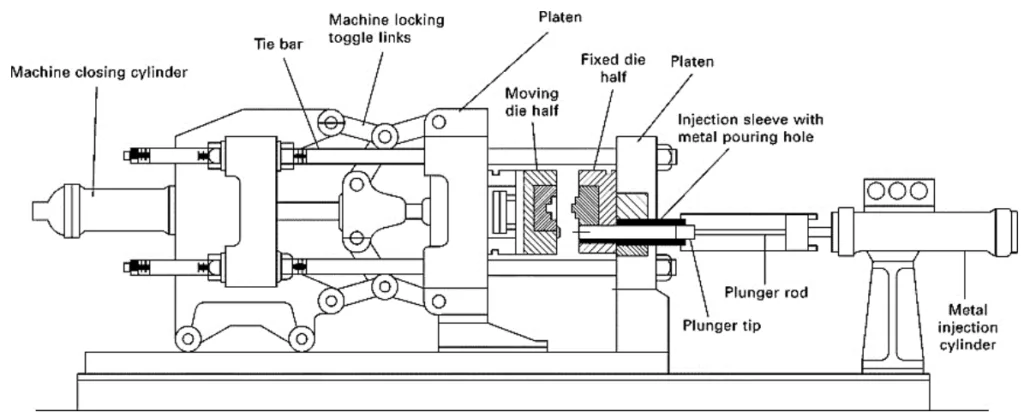
1. 개요:
- 제목: Injection Parameters Setting in High-Pressure Die Casting (고압 다이캐스팅에서 사출 파라미터 설정)
- 저자: Rahul B., Bhaskar M. Reddy, Tamilselvam Nallusamy, W. Brightlin Abisha, Suresh P.
- 출판 연도: 2023
- 게시된 저널/학회: Journal of Polymer & Composites (Volume 11, Special Issue 13)
- 키워드: Casting defects (주조 결함), Cavity pressure (캐비티 압력), Fill time (충진 시간), Gate area (게이트 면적), Injection velocity (사출 속도)
2. 초록
과학 및 가공 기술의 발전은 매우 중요합니다. 알루미늄 다이캐스트 부품이 널리 사용됩니다. 적절한 공정 변수가 필요합니다. 이 논문은 최적의 사출 파라미터를 연구합니다. 고압 다이캐스팅 공정(HPDC)에서 흔히 발생하는 결함은 미성형, 플로우 라인, 블로우홀, 핀홀, 수축, 가스 혼입 기공 등입니다. 본 연구는 저속, 고속 및 가압 기능의 효과를 분석합니다. 1단계 길이, 1단계 속도, 2단계 길이, 2단계 속도, 3단계 캐비티 압력 및 유지 시간과 같은 사출 파라미터의 최적값을 추정합니다.
3. 연구 배경:
연구 주제 배경:
알루미늄과 같은 금속 및 합금은 높은 비강도 및 내식성과 같은 특성으로 인해 자동차, 복합 재료 및 항공 우주를 포함한 엔지니어링 응용 분야에 널리 사용됩니다[1-6]. 다이캐스팅 공정은 중력 다이캐스팅(GDC), 저압 다이캐스팅(LPDC) 및 고압 다이캐스팅(HPDC)으로 분류됩니다[7–9].
이전 연구 현황:
- 중력 다이캐스팅(GDC): 중력 및 대기압을 사용합니다. 6mm보다 큰 벽 두께, 3~25kg의 주조 중량을 가진 부품에 권장되지만 HPDC보다 생산 속도가 낮습니다[10–14].
- 저압 다이캐스팅(LPDC): 가압 가스(0.1-0.3 bar)를 사용하여 금형 캐비티를 채웁니다[9, 17]. 휠 및 실린더 헤드와 같은 자동차 부품에 사용됩니다[18].
- 고압 다이캐스팅(HPDC): 피스톤이 고압 및 고속으로 용융 금속을 구동합니다[19–23]. 다이 세트는 H13 강철로 만들어지고 44-46 HRC로 경화되며 종종 질화 처리됩니다[24, 25, 26].
연구 필요성:
사출 파라미터(저속, 고속, 가압 등)의 변화는 주조 결함을 유발할 수 있습니다. 고품질의 결함 없는 주물을 얻으려면 적절한 설정이 필수적입니다.
4. 연구 목적 및 연구 질문:
연구 목적:
HPDC에서 사출 파라미터를 연구하고 최적화하여 주조 결함을 줄입니다.
핵심 연구:
사출의 세 단계(저속, 고속 및 가압)의 효과를 분석하고 다음에 대한 최적 값을 결정합니다.
- 1단계 길이 및 속도
- 2단계 길이 및 속도
- 3단계 캐비티 압력 및 유지 시간
5. 연구 방법
이 연구는 HPDC에서 3단계 사출 시스템(그림 2)을 분석하며 다음에 중점을 둡니다.
- 충진율(Filling Ratio): 주입된 액체 금속 부피와 전체 사출 슬리브 부피의 비율. 가스 혼입 기공을 최소화하기 위해 60-70%의 충진율이 권장됩니다[33–36].
- 1단계 (사전 충진 단계): 플런저는 용융 금속을 낮은 속도(0.1m/sec ~ 0.6m/sec)로 인게이트 근처로 이동시킵니다[37]. 1단계 길이 및 속도는 북미 다이캐스팅 협회(NADCA)에서 제공하는 공식을 사용하여 계산됩니다.
- 2단계 (다이 캐비티 충진 단계): 액체 금속이 고속(0.4m/sec–6m/sec)으로 주입됩니다. 금형 충진 시간은 매우 짧습니다(5~100밀리초). 2단계 길이 및 속도는 다이 설계 데이터, 게이트 면적 및 게이트 속도를 기반으로 계산됩니다.
- 3단계 (가압 단계): 응고 중에 수축을 보상하기 위해 추가 금속이 밀어 넣어집니다. 가압(캐비티 압력)이 계산되고 다양한 유형의 주조에 대해 다른 압력이 권장됩니다[38-42].
이 연구는 이러한 원리를 사용하여 엔진 하우징 구성 요소를 분석하며, 샷 중량, 주조 중량, 게이트 면적, 플런저 직경 및 활성 슬리브 길이에 대한 특정 데이터가 제공됩니다.
6. 주요 연구 결과:
주요 연구 결과 및 제시된 데이터 분석:
이 연구는 엔진 하우징 구성 요소에 대한 사출 파라미터를 단계별로 계산했습니다.
- 샷 중량 부피, 주조 중량 부피 및 샷 슬리브 부피: 제공된 데이터를 기반으로 계산.
- 충진율: 58.53%로 계산되어 최적의 60-70%에 가깝습니다.
- 2단계 길이: 12.03cm로 계산.
- 1단계 길이: 16.97cm로 계산.
- 1단계 속도: 0.077m/sec로 계산되어 권장 범위 내에 있습니다.
- 2단계 속도: 1.55m/sec로 계산.
- 가압(캐비티 압력): 933kg/cm²로 계산되어 압력 기밀 주조에 대한 권장 범위 내에 있습니다.
이러한 최적화된 파라미터는 생산 환경에서 구현되었습니다.
표 1은 연구 전후의 파라미터를 요약하여 공기 혼입, 캐비티 충진 시간, 압력 기밀성 개선 및 불량률이 8%에서 1.2%로 감소했음을 보여줍니다.
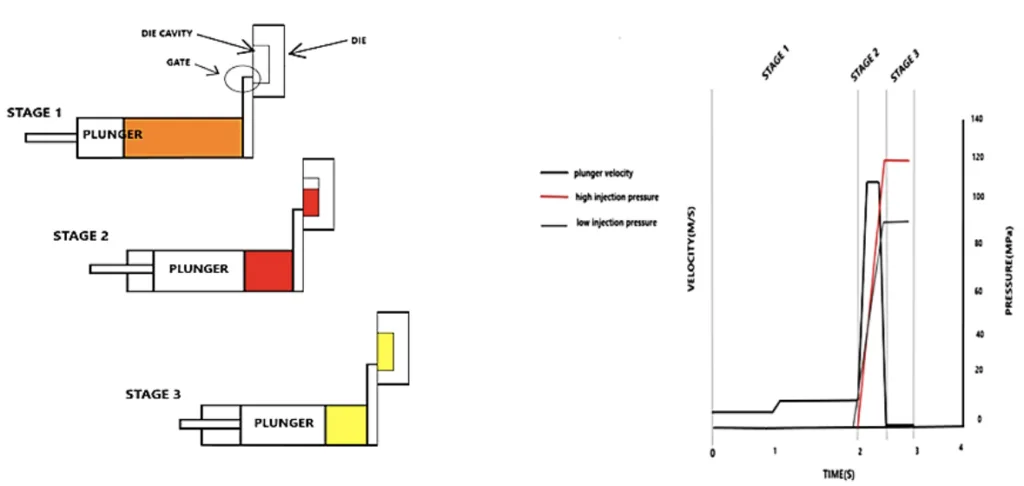
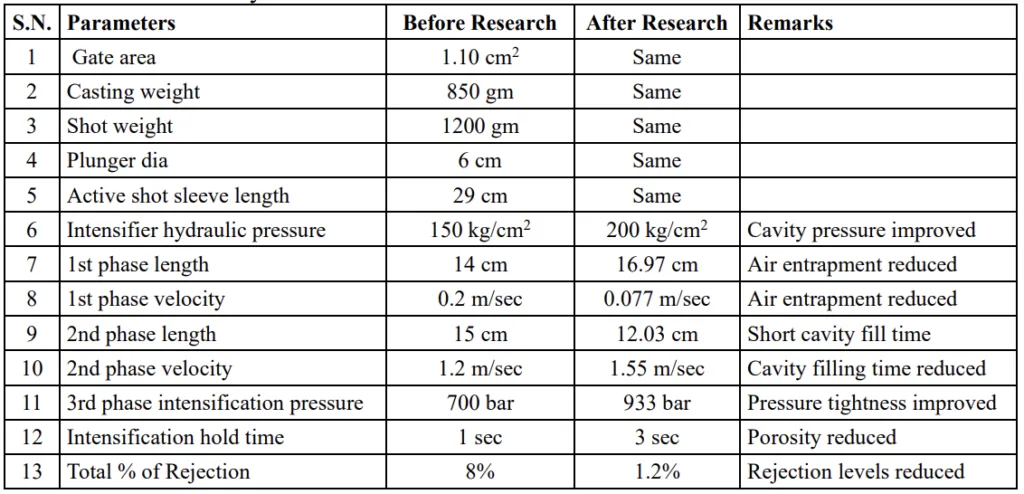
그림 이름 목록:
- 그림 1. 냉각 챔버 수평 고압 다이캐스팅 기계.
- 그림 2. 3단계 사출 시스템.
7. 결론:
주요 결과 요약:
사출 파라미터(1단계 길이 및 속도, 2단계 길이 및 속도, 3단계 캐비티 압력 및 유지 시간)를 최적화하여 주조 불량률이 8%에서 1.2%로 크게 감소했습니다.
{연구 결과 요약. 연구의 학문적 의의, 연구의 실제적 함의}
이 연구는 HPDC에서 사출 파라미터를 신중하게 제어하고 계산하는 것이 고품질의 결함 없는 주물을 생산하는 데 중요하다는 것을 보여줍니다. 실제적인 의미는 스크랩을 크게 줄이고 생산 효율성을 개선하여 이익과 고객 만족도를 높이는 것입니다.
8. 참고 문헌:
- [1] Koli D K, Agnihotri G, Purohit R. Advanced aluminium matrix composites: the critical need of automotive and aerospace engineering fields. Materials Today: Proceedings. 2015; 2(4-5): 3032-041p.
- [2] Sharma A K, Rakesh Bhandari, Amit Aherwar, et al. A study of advancement in application opportunities of aluminum metal matrix composites. Materials Today: Proceedings. 2020; 26: 2419-2424p.
- [3] Eliasson J, Sandström R. Applications of Aluminium Matrix Composites. Key Engineering Materials. 1995; 104–107: 3-36p.
- [4] Ashkenazi D. How aluminum changed the world: A metallurgical revolution through technological and cultural perspectives. Technological Forecasting and Social Change. 2019; 143: 101–113р.
- [5] Richards J W. Aluminium: its history, occurrence, properties, metallurgy and applications, including its alloys. Walnut Street, U S A: HC Baird & Company; 1890.
- [6] Sukiman N L, Zhou X, Birbilis N, et al. Durability and corrosion of aluminium and its alloys: overview, property space, techniques and developments. In: Zaki Ahmad, editor. Aluminium Alloys-New Trends in Fabrication and Applications. London: Intech Open Limited; 2012; 5: 47–97p.
- [7] Alok Singh Chauhan, Boddapati Anirudh, Satyanarayana A, et al. FEA optimization of injection parameters in ceramic core development for investment casting of a gas turbine blade. Materials Today: Proceedings. 2020; 26: 2190–2199p.
- [8] He Li, Yongsheng Liu, Yansong Liu, et al. Influence of debinding holding time on mechanical properties of 3D-printed alumina ceramic cores. Ceramics International. 2021; 47(4): 4884–4894p.
- [9] Bonollo F, Urban J, Bonatto B, et al. Gravity and low pressure die casting of aluminium alloys: a technical and economical benchmark. la metallurgia italiana. 2005; 6: 23–31р.
- [10] Prosenjit Das, Bikash Bhuniya, Sudip K. Samanta, et al. Studies on die filling of A356 Al alloy and development of a steering knuckle component using rheo pressure die casting system. Journal of Materials Processing Technology. 2019; 271: 293-311p.
- [11] Byoung Hee Choi, Young Soo Jang, Jae Gi Sim, et al. Application of rheo-diecasting of a high strength Al-Si-Mg alloy to automotive suspension arms. ISIJ international. 2013; 53(3): 502-510p.
- [12] Reddy A C, Rajanna C. Design of gravity die casting process parameters of Al-Si-Mg alloys. Journal of Machining and Forming Technologies. 2009; 1(1/2): 1–25p.
- [13] Malhotra V, Kumar Y. Study of process parameters of gravity die casting defects. Int. J. Mech. Eng. Technol. 2016; 7: 208-211p.
- [14] Teng X, Mae H, Bai Y, et al. Pore size and fracture ductility of aluminum low pressure die casting. Engineering Fracture Mechanics. 2009; 76(8): 983–996p.
- [15] Dou K, Lordan E, Zhang Y J, et al. A complete computer aided engineering (CAE) modelling and optimization of high pressure die casting (HPDC) process. Journal of Manufacturing Processes. 2020; 60: 435-446p.
- [16] Yang H, Ji S, Watson D, et al. Repeatability of tensile properties in high pressure die-castings of an Al-Mg-Si-Mn alloy. Metals and Materials International. 2015; 21(5): 936–943p.
- [17] Fu M W, Zheng J Y. Die Casting for Fabrication of Metallic Components and Structures. In: Encyclopedia of Materials-Metals and Alloys. Elsevier; 2021: 54–72p.
- [18] Chen Hu, Haidong Zhao, Xueling Wang, et al. Microstructure and properties of AlSi12Fe alloy high pressure die-castings under different vacuum levels. Vacuит. 2020; 180: 109561p.
- [19] Jadhav A R, Hujare D P, Hujare P P. Design and optimization of gating system, modification of cooling system position and flow simulation for cold chamber high pressure die casting machine. Materials Today: Proceedings. 2021; 46(17): 7175–7181p.
- [20] Patnaik L, Saravanan I, Kumar S. Die casting parameters and simulations for crankcase of automobile using MAGMAsoft. Materials Today: Proceedings. 2020; 22: 563-571p.
- [21] Chavan R and Kulkarni P. Die design and optimization of cooling channel position for cold chamber high pressure die casting machine. IOP Conference Series: Materials Science and Engineering. 2020; 810: 012017р.
- [22] Niu X P, Hu B H, Pinwill I, et al. Vacuum assisted high pressure die casting of aluminium alloys. Journal of Materials Processing Technology. 2000; 105(1-2): 119–127р.
- [23] Bonollo F, Gramegna N, Timelli G. High-pressure die-casting: contradictions and challenges. JOM. 2015; 67(5): 901–908p.
- [24] Kohlstädt S, Vynnycky M, Jäckel J. Towards the modelling of fluid-structure interactive lost core deformation in high-pressure die casting. Applied Mathematical Modelling. 2020; 80: 319–333p.
- [25] Kohlstädt S, Vynnycky M, Neubauer A, et al. Comparative RANS turbulence modelling of lost salt core viability in high pressure die casting. Progress in Computational Fluid Dynamics, an International Journal. 2019; 19(5): 316–327р.
- [26] Kohlstädt S, Vynnycky M, Goeke S, et al. On Determining the Critical Velocity in the Shot Sleeve of a High-Pressure Die Casting Machine Using Open Source CFD. Fluids. 2021; 6(11): 386p.
- [27] Li Zixin, Li Dejiang, Zhou Wenke, et al. Characterization on the formation of porosity and tensile properties prediction in die casting Mg alloys. Journal of Magnesium and Alloys. 2022; 10(7): 1857-1867p.
- [28] Ewan Lordan, Jaime Lazaro-Nebreda, Yijie Zhang, et al. On the relationship between internal porosity and the tensile ductility of aluminium alloy die-castings. Materials Science and Engineering: A. 2020; 778; 139107p.
- [29] Mahesh N Adke, Shrikant V Karanjkar. Optimization of die-casting process parameters to identify optimized level for cycle time using Taguchi method. International Journal of Innovations in Engineering and Technology. 2014; 4(4): 365–375p.
- [30] Singh R. Modeling of surface hardness in hot chamber die casting using Buckingham's π approach. Journal of Mechanical Science and Technology. 2014; 28(2): 699–704p.
- [31] Dańko J, Stojek J, Dańko R. Model testing of casting process in cold-chamber die casting machine. Archives of Metallurgy and Materials. 2007; 52(3): 503–513p.
- [32] Singh R, Singh H. Effect of Some Parameters on the Cast Component Properties in Hot Chamber Die Casting. Journal of The Institution of Engineers (India): Series C. 2016; 97(2): 131–139p.
- [33] Lee J, Lee Y C, Kim J T. Migration from the traditional to the smart factory in the die casting industry: Novel process data acquisition and fault detection based on artificial neural network. Journal of Materials Processing Technology. 2021; 290: 116972p.
- [34] Bataineh O, Al-Dwairi A. Application of statistical process control tools to improve product quality in manufacturing processes. Applied Mechanics and Materials. 2012; 110–116: 4023-4027р.
- [35] Bruckmeier L, Ringel A, Vroomen U. Influence of High-Pressure Die Casting Process Parameters on the Compound Strength of Hybrid Components with Undercut Sheet Metal. Metals. 2023; 13(10): 1717р.
- [36] Wan Mahmood W H, Mohd Rosdi M N H, Muhamad M R. A Conceptual Framework in Determining Manufacturing Complexity. Applied Mechanics and Materials. 2015; 761: 550–554p.
- [37] Outmani, I, Laurence Fouilland-Paille, Jérôme Isselin, et al. Effect of Si, Cu and processing parameters on Al-Si-Cu HPDC castings. Journal of Materials Processing Technology. 2017; 249: 559-569p.
- [38] Rathinam N, Dhinakaran R, Sharath E. Optimizing process parameters to reduce blowholes in high pressure die casting using Taguchi methodology. Materials Today: Proceedings. 2021; 38: 2871–2877р.
- [39] Mohd U, Pandulu G, Jayaseelan R. Strength evaluation of eco-friendly concrete using Taguchi method. Materials Today: Proceedings. 2020; 22: 937–947p.
- [40] Balikai V G, Siddlingeshwar I, Gorwar M. Optimization of process parameters of High Pressure Die Casting process for ADC12 Aluminium alloy using Taguchi method. International Journal of Pure and Applied Mathematics. 2018; 120(6): 959–969p.
- [41] Anilchandra R. Adamane, Lars Arnberg, Elena Fiorese, et al. Influence of injection parameters on the porosity and tensile properties of highpressure die cast Al-Si alloys: a review. International Journal of Metalcasting. 2015; 9(1): 43–53р.
- [42] Karthik A, Karunanithi R, Srinivasan S A, et al. The optimization of squeeze casting process parameter for AA2219 alloy by using the Taguchi method. Materials Today: Proceedings. 2020; 27: 2556-2561р.
9. 저작권:
- 본 자료는 "Rahul B., Bhaskar M. Reddy, Tamilselvam Nallusamy, W. Brightlin Abisha, Suresh P."의 "Injection Parameters Setting in High-Pressure Die Casting" 논문을 기반으로 합니다.
- 논문 출처: DOI (Journal): 10.37591/JoPC
본 자료는 위 논문을 소개하기 위해 제작되었으며, 상업적 목적으로 무단 사용하는 것을 금합니다. Copyright © 2025 CASTMAN. All rights reserved.