벤토나이트 함량이 아연 합금 주물의 표면 품질과 기계적 강도를 결정하는 핵심 요소인 이유
이 기술 브리핑은 Zatil Alyani Mohd Amin 외 저자가 발표한 학술 논문 "Properties of Zinc alloy cast product with different composition of Silica Sand and Bentonite in Green Sand Mould"를 기반으로 합니다. HPDC(고압 다이캐스팅) 전문가를 위해 CASTMAN의 전문가들이 요약 및 분석하였습니다.
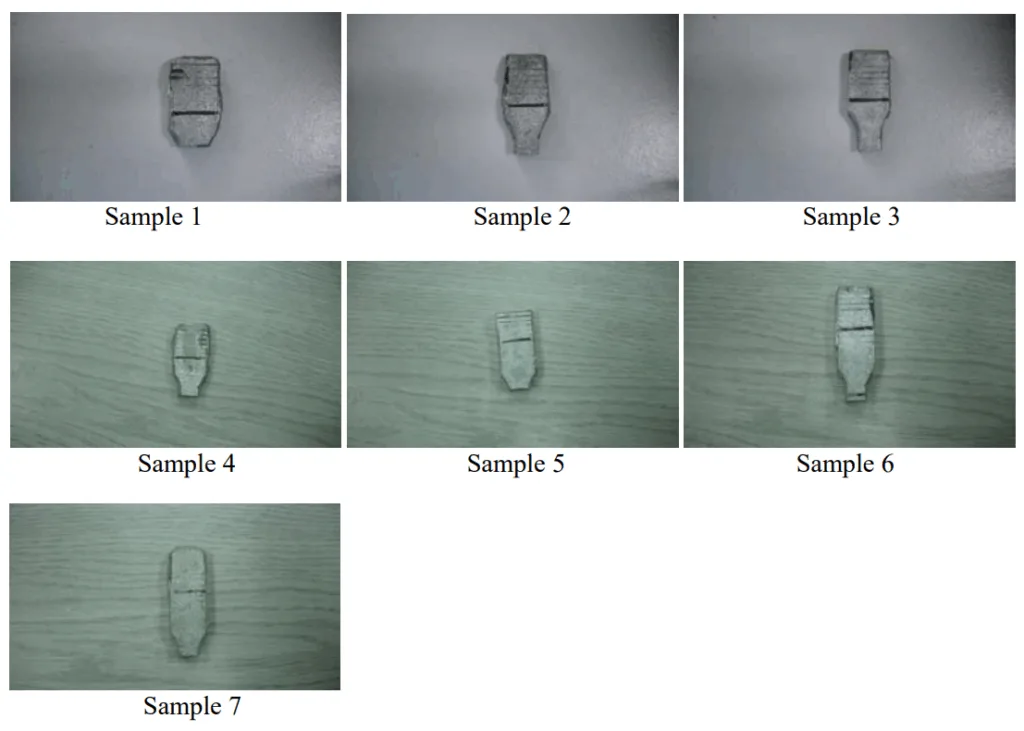
키워드
- Primary Keyword: 아연 합금 주조 (Zinc alloy casting)
- Secondary Keywords: 생사 주형 (Green sand mould), 벤토나이트 (Bentonite), 규사 (Silica sand), 기계적 특성 (Mechanical properties), 주물 표면 (Casting surface), 인장 강도 (Tensile strength)
Executive Summary
(핵심 문제, 접근 방식, 가장 중요한 발견 사항을 3-4개의 글머리 기호로 요약)
- 도전 과제: 녹사 주형(Green Sand Mould)을 사용한 아연 합금 주조 시, 주형의 구성 요소인 규사와 벤토나이트의 비율이 최종 제품의 기계적 특성과 표면 품질에 어떤 영향을 미치는지 규명하는 것이 중요합니다.
- 연구 방법: 연구팀은 벤토나이트 함량을 5%에서 17%까지 7단계로 다르게 조정한 녹사 주형을 제작하고, 동일한 아연-알루미늄-마그네슘(Zn-3Al-2Mg) 합금을 주입하여 시편을 만들었습니다.
- 핵심 발견: 벤토나이트 함량이 15%일 때 가장 우수한 표면 광택과 최고의 인장 강도를 보였으며, 13%일 때 가장 높은 경도를 기록했습니다. 이는 주형의 조성이 최종 제품의 품질을 결정하는 핵심 변수임을 증명합니다.
- 결론: 주물의 품질 최적화를 위해서는 단순히 합금 성분뿐만 아니라, 주형의 조성, 특히 벤토나이트의 비율을 정밀하게 제어하는 것이 필수적입니다.
도전 과제: 이 연구가 HPDC 전문가에게 중요한 이유
(논문의 Introduction
및 Background
섹션을 요약합니다. 업계 사람들이 직면한 일반적이고 시급한 문제로 구성합니다.)
자동차 및 장식 산업에서 경량화 요구가 증가함에 따라 아연 합금 주조 산업의 경쟁이 치열해지고 있습니다. 다이캐스팅, 사형 주조 등 다양한 방법이 있지만, 녹사(Green Sand) 주조법은 저비용으로 다품종 소량 생산이 가능하고 주물사를 재활용할 수 있다는 장점 덕분에 여전히 중요한 역할을 차지하고 있습니다.
하지만 녹사 주형의 핵심 구성 요소인 규사(silica sand)와 벤토나이트(bentonite)의 배합 비율은 최종 주조 제품의 품질에 직접적인 영향을 미칩니다. 이 비율이 최적화되지 않으면 표면 결함, 기계적 강도 저하 등 다양한 문제가 발생할 수 있습니다. 본 연구는 이 배합 비율, 특히 벤토나이트 함량의 변화가 아연 합금 주물의 표면 상태, 경도, 인장 강도 및 미세 조직에 미치는 영향을 체계적으로 분석하여 최적의 생산 조건을 찾는 것을 목표로 합니다.
비록 이 연구는 사형 주조에 초점을 맞추고 있지만, 용탕과 금형/주형 표면의 상호작용이 최종 제품의 품질을 결정한다는 근본 원리는 HPDC 전문가들에게도 중요한 시사점을 제공합니다. 다이캐스팅의 이형제, 다이 온도 제어와 같은 요소들이 주물 표면 및 내부 품질에 미치는 영향을 이해하는 데 유용한 비교 자료가 될 수 있습니다.
접근 방식: 연구 방법론 분석
(논문의 연구 방법론을 간략하게 설명합니다. 과도한 세부 사항에 얽매이지 않고 그들이 무엇을 왜 했는지에 초점을 맞춥니다.)
연구팀은 아연 합금 주물의 특성에 대한 주형 조성의 영향을 규명하기 위해 다음과 같은 체계적인 실험을 설계했습니다.
- 주형 제작: 총 7개의 녹사 주형을 제작했으며, 각 주형은 규사와 벤토나이트의 비율을 다르게 설정했습니다. 벤토나이트의 비율은 전체 주물사(규사+벤토나이트) 무게 대비 5%에서 17%까지 2%씩 증가시켰습니다 (예: 95:5, 93:7, …, 83:17). 수분 함량은 모든 주형에서 동일하게 유지되었습니다.
- 합금 주조: Zn-3Al-2Mg 조성을 가진 3원계 아연 합금을 용해하여 준비된 각 주형에 주입했습니다. 이를 통해 인장 시험 및 경도 시험에 사용될 표준 시편(dog bone 형태)을 제작했습니다.
- 특성 평가: 제작된 7종류의 시편에 대해 다음과 같은 특성을 평가했습니다.
- 물리적 특성: 육안 검사를 통해 주물 표면의 광택 및 상태를 비교 분석했습니다.
- 기계적 특성: 경도 시험과 인장 강도 시험을 통해 각 시편의 기계적 성능을 측정했습니다.
- 미세 조직: 광학 현미경을 사용하여 각 시편의 미세 조직을 관찰하고 비교했습니다.
핵심 발견: 주요 결과 및 데이터
(요약의 핵심입니다. 논문의 가장 중요한 결과를 자세히 설명합니다. 글머리 기호나 짧은 단락을 사용하여 주요 데이터와 결과를 제시합니다. 그림과 표를 직접 인용합니다.)
- 결과 1: 표면 특성 - 벤토나이트 15%에서 최상의 광택
논문의 초록(Abstract)에 따르면, 벤토나이트 함량이 가장 낮거나(5%) 가장 높은(17%) 경우 표면이 무광(dull)으로 나타난 반면, 벤토나이트 함량이 15%인 주형에서 제작된 시편이 가장 빛나는(shiniest) 표면을 보였습니다. 이는 주형 내 적절한 벤토나이트 함량이 용탕과의 반응을 최적화하여 우수한 표면 조도를 형성하는 데 기여함을 시사합니다. - 결과 2: 경도 - 벤토나이트 13%에서 최고치 기록
Figure 2의 경도 시험 결과, 벤토나이트 함량이 13%인 시편 5번이 131.74로 가장 높은 경도 값을 보였습니다. 흥미롭게도, 벤토나이트 함량이 15%인 시편 6번의 경도는 106.06으로 가장 낮은 수준에 속했습니다. 이는 특정 지점까지는 벤토나이트가 경도를 높이는 데 기여하지만, 그 이상이 되면 다른 요인으로 인해 경도가 다시 감소할 수 있음을 보여줍니다. - 결과 3: 인장 강도 - 벤토나이트 15%에서 최고치 기록
Figure 3의 인장 강도 그래프에 따르면, 벤토나이트 함량이 15%인 시편 6번이 112.113 MPa로 가장 높은 인장 강도를 나타냈습니다. 반면, 벤토나이트 함량이 11%인 시편 4번은 77.892 MPa로 가장 낮은 강도를 보였습니다. 이는 주형의 결합력과 가스 배출 능력 등이 복합적으로 작용하여 최종 제품의 인장 강도에 영향을 미친 결과로 해석됩니다. - 결과 4: 미세 조직 - 큰 차이 없음
논문의 초록에 따르면, 각기 다른 조성의 주형에서 만들어진 시편들의 미세 조직(morphologies)은 서로 큰 차이를 보이지 않았습니다. 이는 본 실험 조건에서는 주형의 조성이 미세 조직보다는 표면 특성과 기계적 강도에 더 지배적인 영향을 미쳤음을 의미합니다.
귀사의 HPDC 운영을 위한 실질적 시사점
(마케팅에 가장 중요한 섹션입니다. 논문의 결과와 결론에만 근거하여 이러한 발견이 실제 제조 환경에 어떤 의미가 있는지 설명합니다. CASTMAN이 지원할 수 없는 주장을 하지 마십시오. "이 연구는 X를 고려함으로써 Y를 달성할 수 있음을 시사합니다."와 같이 구성합니다.)
- 공정 엔지니어에게: 본 연구는 주형/다이와 용탕의 계면이 최종 품질에 얼마나 중요한지를 명확히 보여줍니다. HPDC 공정에서 이는 다이 표면 온도, 이형제(윤활제)의 종류 및 도포 상태가 용탕의 유동, 응고 과정 및 최종 표면 품질에 미치는 영향과 직접적으로 연결됩니다. 사형 주조에서 벤토나이트 함량이 열전달과 표면 품질에 미치는 영향은 HPDC 공정 변수를 최적화하는 데 유용한 참고 자료가 될 수 있습니다.
- 품질 관리 담당자에게: Figure 2와 Figure 3에서 보듯이, 주형 조성의 미세한 변화가 경도와 인장 강도 같은 핵심 품질 지표에 큰 차이를 만듭니다. 이는 HPDC 공정에서 다이 온도, 이형제 분사량, 사출 속도 및 압력 등 모든 공정 변수를 매우 엄격하게 관리해야만 일관된 품질의 제품을 생산할 수 있다는 점을 다시 한번 강조합니다.
- 금형 설계자에게: 이 연구는 열 전달 관리의 중요성을 보여줍니다. 녹사 주형의 규사가 주물로부터 열을 흡수하고 외부로 전달하는 역할은 HPDC 다이의 냉각 채널 기능과 유사합니다. 효과적인 열 추출은 응고 시간을 제어하고 최종 제품의 미세 조직과 기계적 특성을 결정하는 핵심 요소입니다. 본 연구 결과는 금형 설계 시 냉각 효율을 최적화하는 것이 왜 중요한지에 대한 근본적인 이유를 제시합니다.
논문 상세 정보
Properties of Zinc alloy cast product with different composition of Silica Sand and Bentonite in Green Sand Mould
1. 개요:
- 제목: Properties of Zinc alloy cast product with different composition of Silica Sand and Bentonite in Green Sand Mould
- 저자: Zatil Alyani Mohd Amin, Faizul Che Pa, P.M Ir. Mohd Ichwan Nasution
- 발행 연도: 2014 (ResearchGate 업로드 기준)
- 학술지/학회: (명시되지 않음, 연구 프로젝트 결과로 추정)
- 키워드: green sand mould, zinc alloy, silica sand
2. 초록:
이 프로젝트는 녹사 주형에서 벤토나이트와 규사의 조성을 달리하여 아연-알루미늄-마그네슘(Zn-3Al-2Mg) 3원계 합금을 생산하는 것을 목표로 합니다. 녹사 주형을 이용한 아연 합금 주조 산업은 다이캐스팅, 사형 주조 등 다양한 주조법과 자동차 및 장식 산업의 경량화 요구로 인해 경쟁이 심화되고 있습니다. 그러나 녹사 주조는 저비용 생산이 가능하고 모래를 재활용할 수 있어 여전히 주조 업계에서 중요한 역할을 합니다. 이 방법은 다품종 소량 생산에 적합합니다. 본 연구에서는 벤토나이트 함량을 5%에서 17%까지 변화시켜 주형을 제작했습니다. 벤토나이트와 규사의 조성 차이는 다른 결과를 낳았습니다. 특성은 표면, 경도 시험, 인장 시험 및 미세 조직으로부터 얻어졌습니다. 가장 낮고 가장 높은 벤토나이트 비율은 중간 비율에 비해 무광의 표면 특성을 보였습니다. 가장 빛나는 표면은 15% 벤토나이트에서 나왔습니다. 한편, 경도 및 인장 강도 시험 결과는 표면 특성과 동일한 경향을 보였습니다. 미세 조직은 서로 큰 차이를 보이지 않았습니다.
3. 서론 요약:
금속 주조 산업에서 사용되는 주물사는 주로 규사에 점토나 유기 화학 바인더를 혼합하여 만듭니다. 가장 널리 사용되는 바인더는 벤토나이트 점토(나트륨 벤토나이트 및 칼슘 벤토나이트)이며, 이러한 주물사를 녹사(green sand)라고 합니다. 녹사 주조는 용탕을 부을 수 있는 주형을 만드는 여러 방법 중 하나입니다. '녹사'라는 용어는 용탕이 부어질 때, 마치 생나무가 수분을 포함하고 있는 것처럼 주형 혼합물에 수분이 존재함을 의미합니다. 녹사는 모래 입자를 점토-물 혼합물로 코팅하여 힘을 가하면 모래를 단단한 덩어리로 결합시켜 준비됩니다. 녹사는 점토-물 결합을 사용하여 높은 생산 속도로 주형을 생산할 수 있게 합니다. 점토 결합사의 주된 장점은 냉각 후 물, 새 점토, 석탄 가루 등을 추가하여 지속적으로 재사용할 수 있다는 점입니다. 원자재는 비교적 저렴하며 용탕과 접촉하는 매우 높은 열 부하를 받는 부분에서만 완전히 분해됩니다.
4. 연구 요약:
연구 주제의 배경:
아연 합금 주조는 저비용, 재활용성, 다품종 소량 생산의 용이성 때문에 녹사 주조법을 통해 널리 이루어지고 있습니다. 녹사 주형은 주로 규사, 벤토나이트, 물로 구성되며, 이들의 조성비가 최종 주물의 품질에 결정적인 영향을 미칩니다.
이전 연구 현황:
기존 연구들은 녹사 주조에서 각 구성 요소의 역할에 대해 다루어 왔습니다. 벤토나이트는 결합제 역할을 하며, 규사는 내화성과 형상을 유지하고, 물은 벤토나이트를 활성화시켜 강도를 발현하게 합니다. 하지만 특정 아연 합금(Zn-3Al-2Mg)에 대해 벤토나이트와 규사의 비율을 체계적으로 변화시키며 그 영향을 종합적으로 분석한 연구는 부족했습니다.
연구 목적:
본 연구의 목적은 녹사 주형에서 규사와 벤토나이트의 조성비를 변화시켰을 때, Zn-3Al-2Mg 아연 합금 주조물의 물리적, 기계적 특성(표면 품질, 경도, 인장 강도) 및 미세 조직에 미치는 영향을 규명하고 최적의 조성비를 찾는 것입니다.
핵심 연구:
연구의 핵심은 벤토나이트 함량을 5%에서 17%까지 7단계로 조절한 주형을 제작하고, 각 주형에서 생산된 아연 합금 시편의 특성을 비교 분석하는 것입니다. 이를 통해 주형의 조성이 최종 제품의 품질에 미치는 직접적인 인과 관계를 실험적으로 증명하고자 했습니다.
5. 연구 방법론
연구 설계:
7가지 다른 비율의 주형을 사용하여 실험을 설계했습니다. 각 주형은 규사와 벤토나이트의 비율(95:5, 93:7, 91:9, 89:11, 87:13, 85:15, 83:17)을 달리했으며, 물의 양(0.24 kg)은 일정하게 유지했습니다. Zn-3Al-2Mg 합금을 용해하여 각 주형에 주입한 후, 생성된 시편의 특성을 평가했습니다.
데이터 수집 및 분석 방법:
- 표면 분석: 제작된 시편의 표면을 육안으로 관찰하고 사진으로 기록하여 광택과 결함 유무를 비교했습니다.
- 경도 시험: 표준 경도 시험기를 사용하여 각 시편의 경도를 측정했습니다.
- 인장 시험: 만능 재료 시험기를 사용하여 각 시편의 인장 강도를 측정했습니다.
- 미세 조직 분석: 시편을 절단하고 연마한 후 광학 현미경으로 미세 조직을 관찰했습니다.
연구 주제 및 범위:
본 연구는 녹사 주형의 조성, 특히 벤토나이트 함량 변화에 초점을 맞춥니다. 연구 범위는 Zn-3Al-2Mg 아연 합금에 한정되며, 평가 항목은 표면 특성, 경도, 인장 강도, 미세 조직입니다.
6. 주요 결과:
주요 결과:
- 표면 품질: 벤토나이트 15% 함량에서 가장 우수한 표면 광택을 보였습니다.
- 경도: 벤토나이트 13% 함량에서 131.74로 가장 높은 경도를 기록했습니다.
- 인장 강도: 벤토나이트 15% 함량에서 112.113 MPa로 가장 높은 인장 강도를 기록했습니다.
- 결론: 전반적으로 벤토나이트 13%와 15% 함량이 최적의 결과를 나타냈습니다.
Figure Name List:
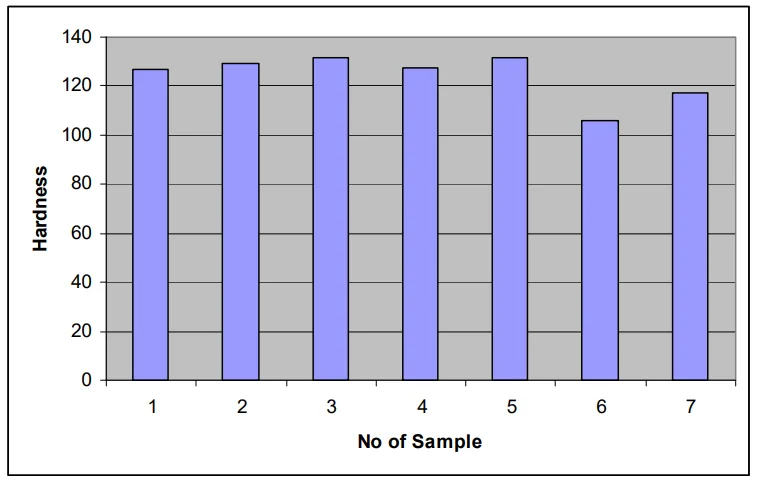
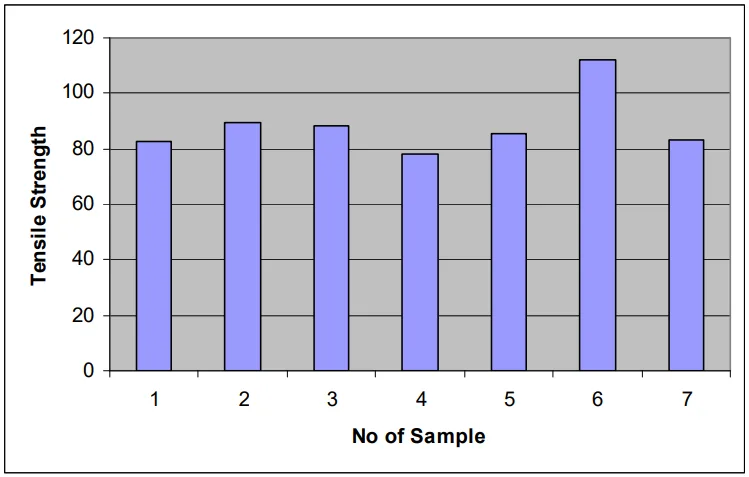
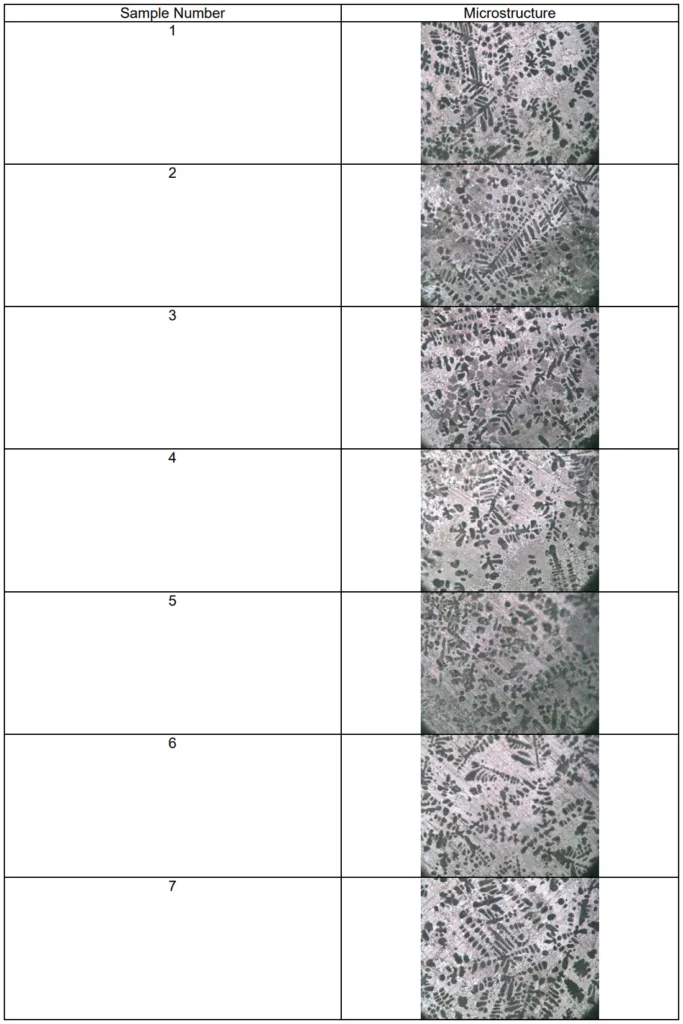
- Figure 1: Surface properties for all the ratios
- Figure 2: Hardness for the Zn-3AI-2Mg for 7 different moulds
- Figure 3: Tensile strength for the Zn-3AI-2Mg for 7 different moulds
7. 결론:
I. 벤토나이트와 규사의 최적 비율은 벤토나이트 13%와 15%입니다.
II. 벤토나이트와 규사는 경도와 표면 결과에 실질적인 영향을 미칩니다.
III. 마지막 두 비율을 제외하고 모든 혼합물은 경도에서 거의 동일한 결과를 보였습니다.
8. 참고 문헌:
- Yujue Wang, 2006, Study on the application of advanced oxidation processing in green sand foundries Luther, N.B., Metal casting and molding processes 1007-1998.7,29-35
- Smiernow, G. A,; Doheny, E.L,; Kay, J.G. 1980. Bonding mechanisms in sand aggregates. Am Foundry Soc. Transaction, 88, 659-682
- Odom, I.E. 1998 Functional properties of Na and Ca bentonites in green sand system. Am Foundry Soc. Transaction. 96, 229-236
- Odom, I.E. 1992. Chemical and physical factors that influence MB analysis of bentonites and system sand. Am. Foundry. Soc. Transaction. 100, 313-321
- Amen, C.W. 2000, Metalcasting, Mc Graw-hill, New York,
- Kawatra, S.K.; Ripke, S.J. 2001. Developing and understanding the bentonite fiber bonding mechanism. Miner. Eng, 14, 647-659
- M.A.savas, S.altintas. 1993. The microstructural control of cast and mechanical properties of zinc-aluminium alloys. Journal of material science 28. 1775-1780
- Kauffmann, P.; Voigt, R.C. 1997. Empirical study of impact of casting process changes on VOC and benzene emission levels and factors, am. Foundry soc. Trans. 105, 297-303
- Crandell, G.R.; Knight, S.M,; Schito, J.F,; Rarick, T.W. 2002. An examination of the effects of process variables on air emission from metal casting. Am. Foundry soc. Trans. 110, 1311-1320
결론 및 다음 단계
이 연구는 HPDC 공정에서 핵심 공정/결과를 향상시키기 위한 귀중한 로드맵을 제공합니다. 이 결과는 품질을 개선하고, 결함을 줄이며, 생산을 최적화하기 위한 명확하고 데이터 기반의 경로를 제공합니다.
CASTMAN은 최신 산업 연구를 적용하여 고객의 가장 어려운 다이캐스팅 문제를 해결하는 데 전념하고 있습니다. 이 백서에서 논의된 문제가 귀사의 운영 목표와 관련이 있다면, 저희 엔지니어링 팀에 연락하여 귀사의 부품에 이러한 고급 원칙을 구현하는 방법을 논의해 보십시오.
전문가 Q&A: 자주 묻는 질문
Q1: 이 연구에서 전반적으로 가장 좋은 결과를 보인 벤토나이트 함량은 얼마였습니까?
A1: 연구의 "결론(Conclusion)" 섹션에 명시된 바와 같이, 벤토나이트 함량이 13%와 15%일 때가 최적의 비율로 나타났습니다. 13%에서는 경도가 가장 높았고, 15%에서는 인장 강도와 표면 광택이 가장 우수했습니다.
Q2: 벤토나이트 함량이 주물 표면 품질에 구체적으로 어떤 영향을 미쳤나요?
A2: 논문의 "초록(Abstract)"에 따르면, 벤토나이트 함량이 15%일 때 가장 빛나는(shiniest) 표면을 얻을 수 있었습니다. 반면, 함량이 너무 낮거나(5%) 너무 높으면(17%) 표면이 무광(dull)으로 나타나, 적정 함량 유지가 중요함을 보여주었습니다.
Q3: 이 연구에 사용된 합금의 정확한 조성은 무엇이었나요?
A3: "초록(Abstract)" 및 "연구 방법론(Methodology)" 섹션에 설명된 바와 같이, 이 연구는 Zn-3Al-2Mg (아연-3%알루미늄-2%마그네슘) 조성을 가진 3원계 아연 합금을 사용하여 수행되었습니다.
Q4: 연구원들은 시편들 간의 미세 조직에서 유의미한 차이를 발견했나요?
A4: 아니요. "초록(Abstract)"에 따르면, "미세 조직은 서로 큰 차이를 보이지 않았다(The morphologies give not much difference from each other)"고 명시되어 있습니다. 이는 실험 조건 하에서 주형 조성이 미세 조직보다는 거시적 특성에 더 큰 영향을 미쳤음을 시사합니다.
Q5: 이 연구 결과에서 경도와 인장 강도 사이에는 어떤 관계가 있었나요?
A5: 단순한 비례 관계는 아니었습니다. Figure 2와 Figure 3에서 볼 수 있듯이, 가장 높은 경도를 보인 시편(13% 벤토나이트)과 가장 높은 인장 강도를 보인 시편(15% 벤토나이트)이 일치하지 않았습니다. 이는 각 기계적 특성에 영향을 미치는 최적의 주형 조건이 다를 수 있음을 의미합니다.
Q6: 이 논문이 주조 시설에 주는 직접적이고 실용적인 교훈은 무엇입니까?
A6: "[논문 제목]"에 근거한 핵심 교훈은, 주형의 조성이 단순히 용탕을 담는 용기가 아니라 최종 주조 제품의 기계적 특성(경도, 인장 강도)과 표면 품질에 직접적으로 영향을 미치는 능동적인 공정 변수라는 것입니다. 이는 모든 주조 공정에서 금형/주형의 상태 관리가 매우 중요함을 강력히 뒷받침합니다.
저작권
- 이 자료는 Zatil Alyani Mohd Amin 외 저자의 논문 "[Properties of Zinc alloy cast product with different composition of Silica Sand and Bentonite in Green Sand Mould]"에 대한 분석 자료입니다.
- 논문 출처: https://www.researchgate.net/publication/228508414
- 본 자료는 정보 제공 목적으로만 사용됩니다. 무단 상업적 사용을 금합니다.
- Copyright © 2025 CASTMAN. All rights reserved.