본 소개 자료는 Pergamon에서 발행한 ["다이캐스트 AZ91D의 미세구조가 부식에 미치는 영향"] 논문의 연구 내용입니다.
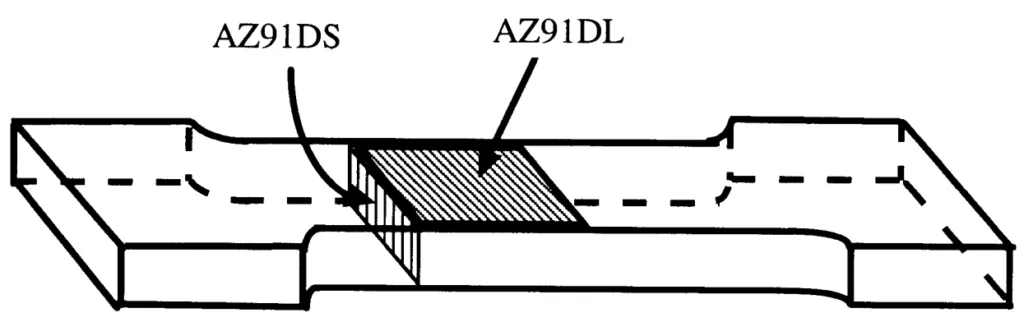
1. 개요:
- 제목: 다이캐스트 AZ91D의 미세구조가 부식에 미치는 영향 (Influence of microstructure on the corrosion of diecast AZ91D)
- 저자: Guangling Song, Andrej Atrens, Matthew Dargusch
- 출판 연도: 1999
- 발표 저널/학회: Corrosion Science
- 키워드: 마그네슘 합금; AZ91D; 다이캐스팅; 부식; 미세구조
2. 초록 (Abstract)
다이캐스트 AZ91D의 부식을 미세구조와 관련하여 연구했습니다. 다이캐스트 AZ91D의 거동을 더 완벽하게 이해하고 비교하기 위해, 서냉 응고된 고순도 AZ91, Mg-2%Al, Mg-9%Al, 저순도 마그네슘 및 고순도 마그네슘을 사용하여 부식 연구 및 미세구조 검사를 수행했습니다. 부식은 1N NaCl, pH 11 조건에서 (1) 부식 형태 관찰, (2) 전기화학적 분극 곡선 측정, (3) 수소 발생 속도와 마그네슘 용해 속도 동시 측정을 통해 연구했습니다. 다이캐스트 AZ91D의 표면층(skin)은 내부보다 더 우수한 내식성을 보였습니다. 이는 (1) 더 높은 β 상의 체적 분율, (2) 더 미세한 α 입자 주위에 더 연속적인 β 상 분포, (3) 다이캐스팅 내부보다 표면층의 더 낮은 기공률의 조합에 기인합니다. 이 연구는 합금 미세구조에 대한 주조 방법의 영향을 통해 주조 방법이 부식 성능에 영향을 줄 수 있음을 보여주었습니다. © 1999 Elsevier Science Ltd. All rights reserved.
3. 연구 배경:
연구 주제 배경:
주조, 특히 다이캐스팅은 마그네슘 합금 부품을 생산하는 일반적인 방법입니다. 마그네슘 합금 다이캐스팅은 비하중 지지 응용 분야 및 자동차의 구조 부품에 사용됩니다. AZ91 합금은 널리 사용되는 마그네슘 주조 합금이며, 고순도 등급은 내식성이 우수합니다.
선행 연구 현황:
AZ91은 α 입자와 α 입자 경계를 따라 β 상(Mg17Al12)으로 구성된 2상 미세구조[1]를 가집니다. 상세한 미세구조는 주조 방법 및 열처리에 의해 결정되며, 주조 유형 및 영역에 따라 달라집니다. 구성 상의 화학 조성 및 분포가 부식 거동의 주요 원인으로 여겨지지만, 자세히 연구되지 않았습니다.
연구 필요성:
다이캐스트 AZ91의 부식 거동에 대한 원인을 조사하는 것이 중요하며, 구성 상의 화학 조성 및 분포가 부식 거동에 미치는 영향에 대한 상세한 연구가 부족합니다.
4. 연구 목적 및 연구 질문:
연구 목적:
AZ91 다이캐스팅의 미세구조가 부식 성능에 미치는 영향을 밝히는 것입니다.
핵심 연구:
다이캐스트 AZ91D의 미세구조와 부식 거동 간의 관계를 서냉 응고된 고순도 AZ91 및 기타 Mg-Al 합금과 비교하여 조사합니다.
5. 연구 방법
- 연구 설계: 비교 실험 연구.
- 데이터 수집 방법:
- XRD, SEM 및 광학 현미경을 사용한 미세구조 검사.
- 1N NaCl, pH 11 조건에서 부식 연구:
- 부식 형태 관찰.
- 전기화학적 분극 곡선 측정.
- 기체 수집 및 유도 결합 플라즈마 원자 방출 분광법(ICPAES)을 사용한 수소 발생 속도 및 마그네슘 용해 속도 동시 측정.
- 분석 방법:
- 서로 다른 샘플 및 영역 간의 부식 형태 및 속도 비교.
- 분극 곡선 분석.
- 미세구조 특징(결정립 크기, β 상 분포, 기공률)과 부식 거동의 상관 관계 분석.
- 연구 재료:
- 다이캐스트 AZ91D, 서냉 응고된 고순도 AZ91 (H.P.AZ91), Mg-2%Al, Mg-9%Al, 저순도 마그네슘, 고순도 마그네슘.
- 서로 다른 표면 방향을 가진 샘플 준비 (AZ91DS: 단면; AZ91DL: 평평한 표면). (Fig. 1)
- 화학 조성은 ICPAES로 결정 (Table 1).
6. 주요 연구 결과:
주요 연구 결과 및 제시된 데이터 분석:
- 다이캐스트 AZ91D의 표면층은 내부보다 더 우수한 내식성을 나타냈습니다.
- 부식 속도(수소 발생 및 Mg 용해)는 인가된 전류 밀도에 따라 달라졌습니다 (Fig. 10, Fig. 11).
- 분극 곡선은 알루미늄 함량과 순도가 다른 합금 간의 차이를 보여주었습니다 (Fig. 12).
- 음의 차이 효과(NDE)가 관찰되었고 부식 저항성과 상관 관계가 있었습니다.
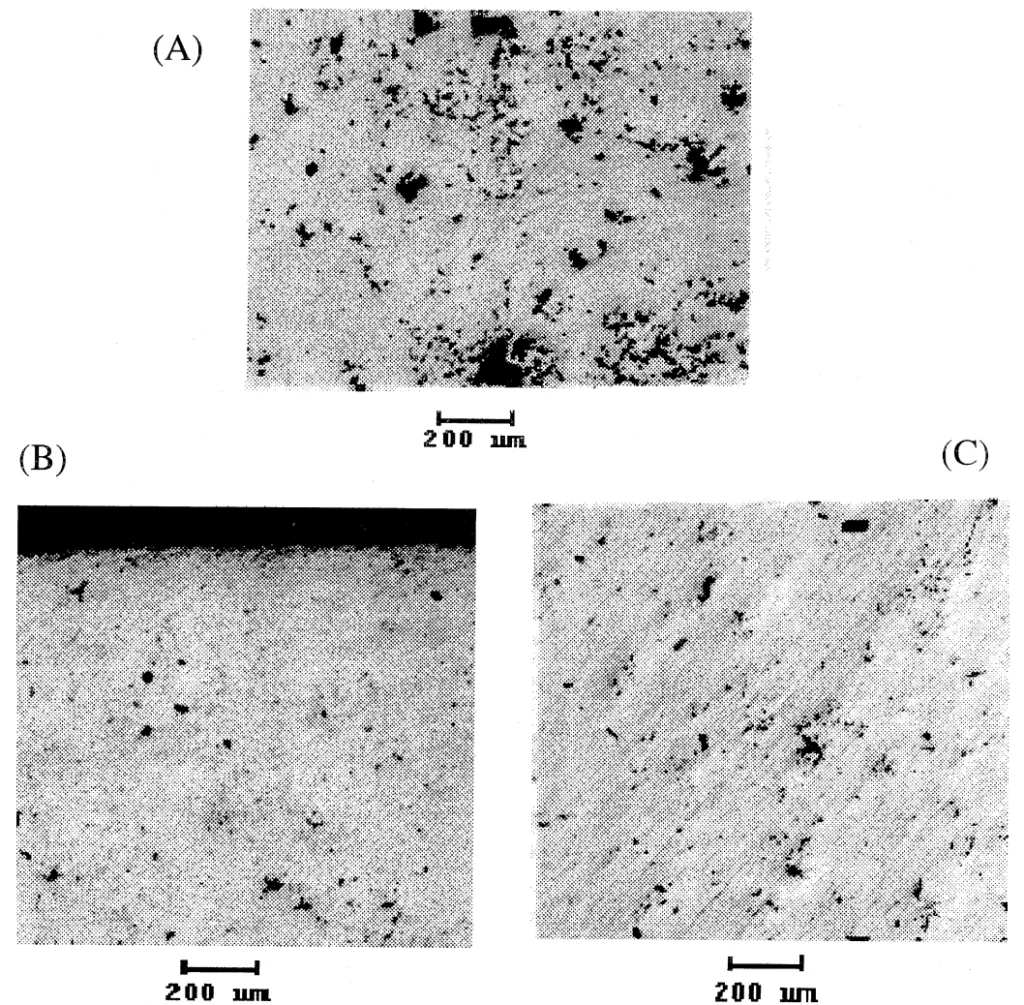
perpendicular to the tensile direction of the tensile sample[ "B# AZ80DS\ edge area[ The surface is
perpendicular to the tensile direction of the tensile sample[ "C# AZ80DL\ central area[ The surface is
parallel to the tensile direction of the tensile sample.
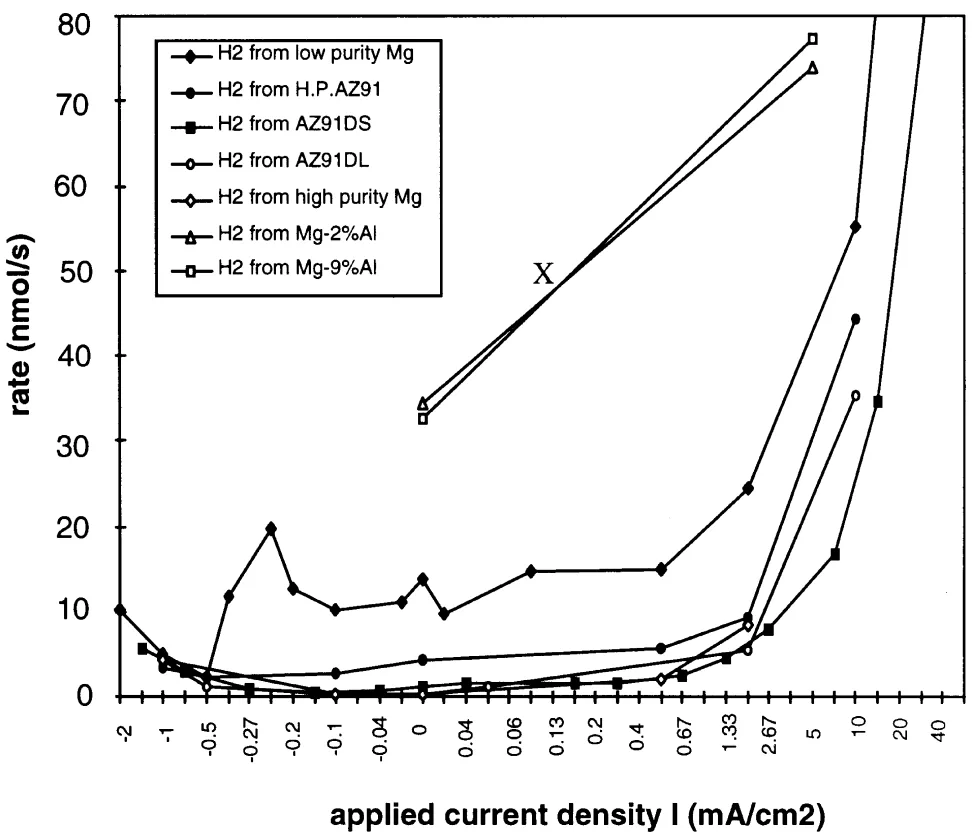
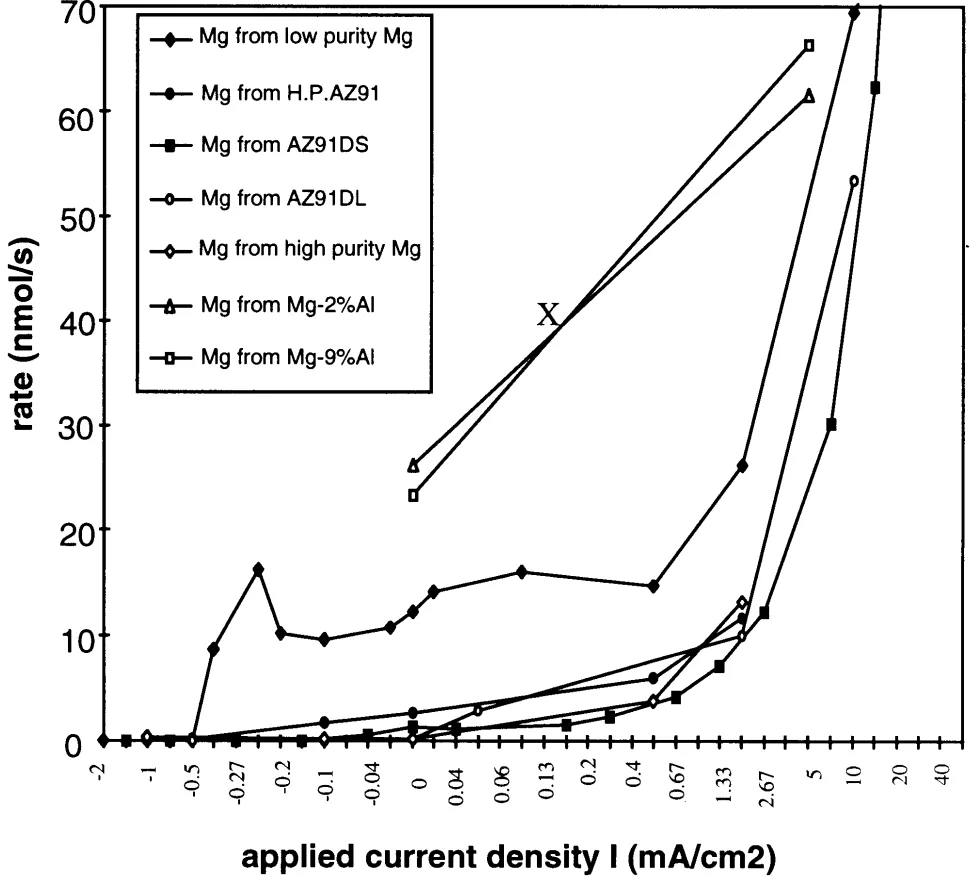
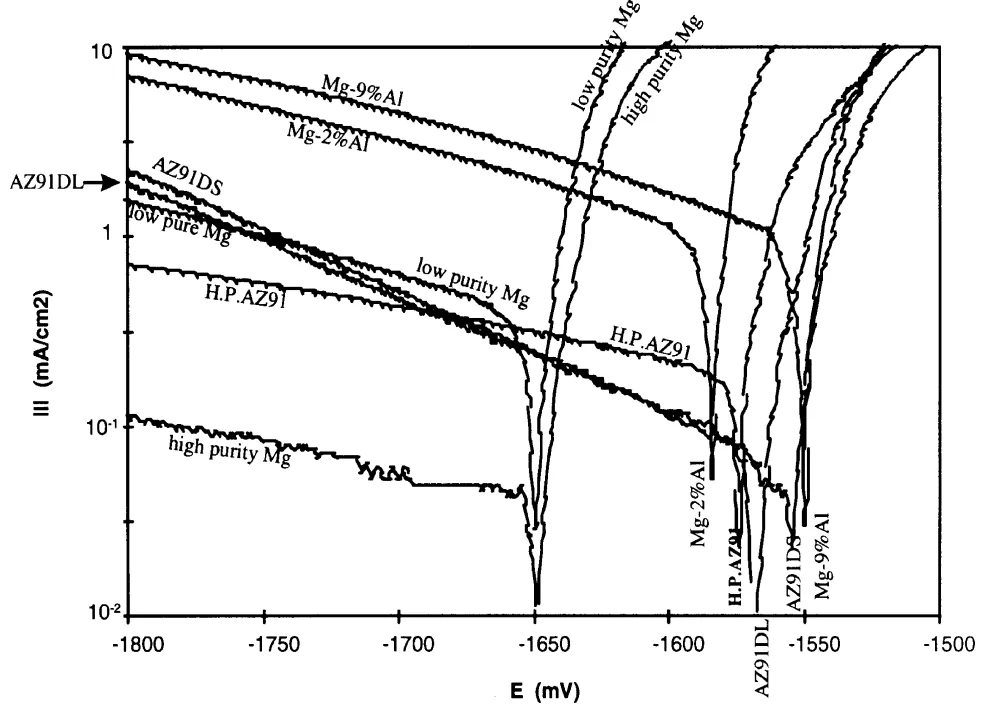
그림 이름 목록:
- Fig. 1. 인장 시편에서 채취한 AZ91DL 및 AZ91DS 샘플의 위치를 나타내는 개략도.
- Fig. 2. 에칭 전 다이캐스트 AZ91D의 광학 현미경 사진.
- Fig. 3. 다이캐스트 AZ91D 합금의 서로 다른 부분을 에칭한 후의 광학 미세구조.
- Fig. 4. 다이캐스트 AZ91D 합금의 광학 미세구조.
- Fig. 5. 다이캐스트 AZ91D의 후방 산란 SEM 이미지.
- Fig. 6. H.P.AZ91의 후방 산란 SEM 이미지.
- Fig. 7. pH 11의 1N NaCl에서 H.P.AZ91의 일반적인 위치 A, B, C 및 D에서의 미세 부식 형태.
- Fig. 8. pH 11의 1N NaCl에서 AZ91D의 일반적인 위치 A, B, C 및 D에서의 미세 부식 형태.
- Fig. 9. 1N NaCl (pH=11)에 몇 분 동안 절반 침지 후 다이캐스트 AZ91DS의 두 가지 다른 부식 형태에 대한 일반적인 현미경 사진.
- Fig. 10. 서로 다른 인가 전류 밀도에서 마그네슘 합금의 수소 발생 속도.
- Fig. 11. 서로 다른 인가 전류 밀도에서 마그네슘 합금의 금속 용해 속도.
- Fig. 12. 1N NaCl (pH = 11)에서 마그네슘 합금의 분극 곡선.
- Fig. 13. 거의 연속적인 β 상이 표면층 위에 있는 합금의 부식 중 표면 조성 변화를 나타내는 개략도.
- Fig. 14. β 상과 1차 또는 공정 α 사이의 갈바닉 효과로 인한 부식을 나타내는 개략도.
7. 결론:
주요 결과 요약:
- 다이캐스트 AZ91D의 부식 거동은 조성, 기공률, 결정립 크기, β 상 분포를 포함하는 미세구조에 의해 결정됩니다.
- 빠른 응고는 더 작은 결정립 크기, 더 많은 β 상, 더 미세하게 분산된 β 상을 초래합니다.
- 주조 방법은 미세구조 제어를 통해 부식 성능에 큰 영향을 미치며, 더 높은 응고 속도가 잠재적인 이점을 가집니다.
- 다이캐스트 AZ91D의 표면층은 더 높은 β 상 분율, 더 연속적인 β 상, 더 미세한 α 입자, 더 낮은 기공률로 인해 내부보다 훨씬 더 우수한 (거의 10배) 내식성을 보입니다.
- β 상은 미세구조에 따라 장벽 또는 갈바닉 음극으로 작용할 수 있습니다.
- α 상의 부식 거동은 알루미늄 함량과 국부 전류 밀도에 따라 달라집니다.
- 다이캐스트 AZ91D는 음의 차이 효과(NDE)를 보였습니다.
- 양극 분극 곡선은 Tafel 거동을 보이지 않았지만, 음극 분극 곡선은 Tafel 거동을 보였습니다.
다이캐스트 AZ91D 합금의 미세구조는 응고 속도에 큰 영향을 받으며, 이는 내식성에 영향을 미칩니다.
이 연구는 다이캐스트 AZ91D에서 미세구조와 부식 간의 관계에 대한 상세한 이해를 제공하여 응고 제어의 중요성을 강조합니다.
이 연구 결과는 다이캐스팅의 원래 표면이 더 보호적이므로 가공해서는 안 된다는 것을 시사합니다.
8. 참고 문헌:
- [1] C. Suman, The effects of direct aging on mechanical properties and corrosion resistance of diecast magnesium alloys AZ91D and AM60B, SAE Transactions 99 (5) (1990) 849.
- [2] W.P. Sequeira, G.L. Dunlop, M.T. Murray, Effect of section thickness and microstructure on the mechanical properties of high pressure die cast magnesium alloy AZ91D, in: G.W. Lorimer (Ed.), Proceedings of the Third International Magnesium Conference, The Institute of Materials, Manchester, UK, 1996, p. 63.
- [3] G.L. Maker, J. Kruger, International Materials Reviews 38 (3) (1993) 138.
- [4] J.D. Ganawalt, C.E. Nelson, J.A. Peloubet, Corrosion studies of magnesium and its alloys, Trans. Am. Inst. Mining Met. Eng. 147 (1942) 273.
- [5] K.N. Reichek, K.J. Clark, K.E. Hills, in: Int. Cong. and Exposition, Society of Automotive Engineers, paper No. 850417, 1985.
- [6] J.E. Hillis, S.O. Shook, Composition and performance of an improved magnesium AS41 Alloy, SAE Technical Paper Series #890205, Detroit, 1989.
- [7] W.P. Sequeira, M.T. Murray, G.L. Dunlop, D.H. St John, Effect of section thickness and gate velocity on the microstructure and mechanical properties of high pressure die cast magnesium alloy AZ91D. Automotive Alloys, A Special symposium—TMS Annual Meeting and Exhibition, Orlando, Florida, February 9–13, 1997.
- [8] E.H. Adolf Beck, The technology of magnesium and its alloys, trans. The technical staffs of F.A. Hughes and Co. Ltd and Magnesium Elekton Ltd of Magnesium und seine Legierungen. London, Chapter 3, 1940.
- [9] S.K. Das, L.A. Davis, Mater. Sci. Eng. 98 (1988) 1.
- [10] O. Lunder, J.E. Lein, T. Kr. Aune, K. Nisancioglu, Corrosion 45 (9) (1989) 741.
- [11] G.L. Makar, J. Kruger, K.J. Sieradzki, Electrochem. Soc. 139 (1) (1992) 47.
- [12] G. Song, A. Atrens, X. Wu, B. Zhang, Submitted to Corrosion Science.
- [13] G. Song, A. Atrens, D. St John, X. Wu, J. Nairn, Anodic dissolution of magnesium in chloride and sulphate solutions, Corrosion Science 39 (10–11) (1997) 1981.
- [14] G. Song, A. Atrens, D. St John, J. Nairn, Y. Li, Corrosion Science 39 (5) (1997) 855.
- [15] J. Campbell, Castings, Butterworth Heinemann, 1991.
9. 저작권:
- 본 자료는 "Guangling Song, Andrej Atrens, Matthew Dargusch"의 논문: "다이캐스트 AZ91D의 미세구조가 부식에 미치는 영향"을 기반으로 합니다.
- 논문 출처: DOI: 10.1016/S0010-938X(98)00121-8
본 자료는 위 논문을 소개하기 위해 작성되었으며, 상업적 목적으로 무단 사용하는 것을 금합니다. Copyright © 2025 CASTMAN. All rights reserved.