본 논문 요약은 ['Eco-sustainable lightweight automotive part manufacturing: GHGs-free die casting of brake leverage prototype made of AZ91D-1.5CaO magnesium alloy'] 논문을 기반으로 작성되었으며, ['La Metallurgia Italiana']에서 발행되었습니다.
1. 개요:
- 제목: Eco-sustainable lightweight automotive part manufacturing: GHGs-free die casting of brake leverage prototype made of AZ91D-1.5CaO magnesium alloy (친환경적인 경량 자동차 부품 제조: AZ91D-1.5CaO 마그네슘 합금으로 제작된 브레이크 레버리지 프로토타입의 GHG-free 다이캐스팅)
- 저자: F. D'Errico, D. Casari
- 발행 연도: 2022년 3월
- 발행 저널/학술 단체: La Metallurgia Italiana, International Journal of the Italian Association for Metallurgy (이탈리아 금속 협회 국제 저널)
- 키워드: MAGNESIUM (마그네슘), CALCIUM OXIDE (산화칼슘), SUSTAINABLE METALLURGY (지속 가능한 야금)
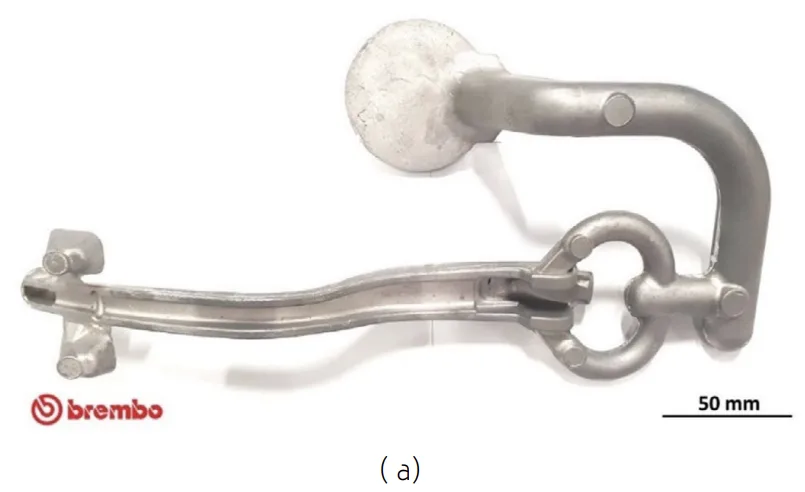
2. 초록 또는 서론
유럽 CRAL 프로젝트에서 비가연성 AZ91D-1.5CaO Eco-Magnesium® (Eco-Mg) 합금을 사용하여 마그네슘 주조 공정에서 가장 낮은 탄소 발자국을 달성했습니다. 비가연성 마그네슘 AZ91D 합금에 Ca (CaO 형태)을 첨가하여 SF6 커버 가스 없이 정지형 용해로에서 용융하고, EU CRAL 프로젝트에서 특별히 개발된 수직 단사출 변위 프레스 기계로 공기 중에서 주입하는 특정 주조 공정 조건을 실험적으로 성공적으로 처리했습니다.
AZ91-1.5CaO Eco-Mg 시리즈 합금으로 제작된 브레이크 레버리지는 단조 알루미늄 합금으로 만들어진 현재 부품을 대체하는 Mg 주조 부품의 실제 예로서 Brembo Spa 사업장에서 성공적으로 제조되었습니다. 실험 파트에서 논의된 바와 같이, 예비 컴퓨터 지원 시뮬레이션 테스트 캠페인은 주조 시험의 불확실성을 줄였습니다. Mg-SF6 free 주조 부품을 브레이크 시스템용으로 구현한 CRAL EU 프로젝트는 Mg 주조 공정 경로의 지구 온난화 지수(GWP)를 획기적으로 감소시켰습니다. Eco-Mg 시리즈는 자동차 부문에 비가연성 Mg 합금을 도입하기 위한 실용적이고 경제적인 주조 솔루션이며, 현재 다가오는 CO2 배출 제한으로 인해 비용 효율적인 경량 부품 연구에 매진하고 있습니다.
3. 연구 배경:
연구 주제 배경:
마그네슘 합금 개발은 지난 세기 항공우주 산업에서 주도되었으며, 운송 산업의 경량화 전략에 대한 요구를 충족시키기 위해 역사적으로 발전해 왔습니다. 알루미늄 합금에 비해 마그네슘은 주조성이 우수하고 몰드 제작에 사용되는 강철과의 화학적 상용성이 낮습니다. 이러한 특성으로 인해 플라스틱으로 구현되는 것과 유사하게 매우 복잡한 형상의 부품을 실현할 수 있으며, 강철 몰드의 수명을 연장할 수 있습니다. 이러한 뛰어난 장점에도 불구하고, 마그네슘이 공기 중에서 처리될 때 높은 가연성으로 인해 안전 문제는 여전히 우려 사항입니다. 일단 점화되면 마그네슘은 발열 반응에 의해 유지되는 자기 연소를 진행하여 산화마그네슘을 형성하고 열을 방출합니다. 결과적으로 연소 불꽃은 2,000°K에서 4,000°K 사이의 온도에 빠르게 도달합니다. 이러한 문제로 인해 마그네슘은 안전하게 제어되어야 합니다.
기존 연구 현황:
마그네슘 합금은 특수한 용해 설비와 숙련된 인력이 필요하여 주조 부품의 생산 비용을 증가시킵니다. 용융 상태에서 Mg 합금을 안전하게 제어하려면 금속 용탕과 접촉하는 O2의 존재를 제거해야 합니다. 즉, Mg 연소 반응의 주요 트리거 소스를 제거해야 합니다. 산소 제거는 용융 Mg에 대해 불활성 분위기를 조성하여 가능합니다. Mg 주조 공장에서는 a) 진공 용해 설비, b) 불활성 및 보호 분위기를 갖춘 용해 설비 등 다양한 기술이 사용됩니다. 일반적으로 사용되는 불활성 분위기는 혼합 SF6 및 CO2, 프레온 가스 R-134a 및 SO2 기반입니다. SF6와 프레온 가스 R-134a는 지구 온난화 지수(GWP)가 매우 높은 온실 가스입니다. 대조적으로 SO2 가스는 환경적 관점에서 온실 가스 SF6 및 R-134a에 대한 유효한 대안이지만 작업자에 대한 높은 독성으로 인해 엄격한 적용 프로토콜이 필요합니다. SO2 가스는 SF6에 대한 친환경적인 솔루션이 될 수 있지만 강철로 만들어진 장비에 부식성이 매우 강합니다. 물과 쉽게 반응하여 H2SO3를 형성하여 작업자에게 건강상의 위험을 초래합니다. SO2와 비교했을 때 SF6는 무독성, 비부식성이지만 온실 효과에 대한 부정적인 영향으로 인해 2018년 1월 1일부터 유럽 연합에서 마그네슘 다이캐스팅 합금 재활용 시 SF6 사용이 금지되었습니다 [1].
연구의 필요성:
연소 엔진 자동차 제조를 위한 경량 재료 선택은 배출 가스 감소에 중요한 역할을 한다는 것은 오늘날 상식입니다. 자동차 제조업체의 경우, 중량 감량은 환경 및 사회적 영향에 대한 인식이 높아지는 친환경 의식 시장의 요구에 부응하는 핵심 전략입니다. EU에서 새로 설정된 신차 및 밴의 평균 배출량에 대한 엄격한 목표에는 초과 배출에 대한 벌금과 함께 제로 및 저배출 차량의 보급을 장려하는 메커니즘이 포함됩니다. 그러나 배기관에서의 차량 배출량 감축은 확대된 친환경 제조 관점에서 볼 때 효과적이지만 부분적인 조치입니다. 그림 1에 묘사된 바와 같이, 이동 거리에 따른 선형 함수 배출량을 지적하면, 중량 철 합금(1)으로 만들어진 부품의 기준 시나리오와 강철 부품과 동일한 기능적 속성을 충족할 수 있는 두 가지 경량 솔루션을 고려할 수 있습니다. "기울기"와 초기 탄소 발자국 "저장"에 따라 초기 합금 제조 및 부품 성형에서 직접적인 CO2 배출량이 감소하더라도 (솔루션 (1)과 (2)의 기울기 참조), 손익분기점은 장거리 이동 후에 도달할 수 있습니다. 그림 1의 (3)에 묘사된 문제는 마그네슘 광석(예: 백운석)에서 실리콘(일반적으로 페로실리콘 형태로 공급)을 사용하여 석탄 연소 레토르트 [2]에서 수행되는 소규모 Pidgeon 공정에서 시작하여 제조된 마그네슘 합금의 전형적인 문제입니다. 또한 높은 반응성으로 인해 마그네슘은 보호 가스를 사용하여 제품 성형을 위해 주조해야 합니다. 과거에는 선호되는 커버 가스인 SF6가 CO2 및 SO2 혼합물, HFC-134a로 대체되었습니다. 최근 3M Company에서 등록한 Novec 612 유체는 CO2와 동일한 매우 낮은 GWP 1을 약속합니다. 여러 연구에서 Pidgeon 공정으로 제조된 원자재와 2차 성형을 통해 생산된 마그네슘 자동차 부품은 오염 물질 커버 가스를 사용하여 주조해도 자동차 수명 [3] 내에서 CO2를 절약할 수 없음을 보여주었습니다.
4. 연구 목적 및 연구 질문:
연구 목적:
본 연구의 목적은 마그네슘 주조 부품의 제품 수명 주기 전반에 걸쳐 총 GHG 배출량 감소 문제를 해결하는 것입니다. 본 연구는 CRAL EU 프로젝트 내에서 브레이크 시스템 부품을 구체적으로 목표로 하여 마그네슘 부품의 다이캐스팅 공정 중 보호 가스 제거에 초점을 맞추고 있습니다. 궁극적인 목표는 Eco-Mg 시리즈를 자동차 부문의 비가연성 마그네슘 합금을 위한 실행 가능하고 비용 효율적인 주조 솔루션으로 검증하여 CO2 배출 제한 증가 속에서 비용 효율적인 경량 부품을 추구하는 산업의 방향과 일치시키는 것입니다.
핵심 연구 질문:
핵심 연구 목표는 다음과 같습니다.
- SF6 커버 가스 없이 정지형 용해로에서 칼슘(CaO 형태)이 첨가된 비가연성 AZ91D 합금을 용융하기 위한 특정 주조 공정 조건을 실험합니다.
- EU CRAL 프로젝트 내에서 개발된 수직 단사출 변위 프레스 기계를 사용하여 공기 중에서 이 합금을 주입하여 가공합니다.
- 단조 알루미늄을 대체하는 마그네슘 주조 부품의 실제 예로서 Brembo Spa에서 AZ91-1.5CaO Eco-Mg 시리즈 합금으로 브레이크 레버리지 프로토타입을 제조합니다.
- 주조 시험의 불확실성을 최소화하기 위해 예비 컴퓨터 지원 시뮬레이션 테스트를 수행합니다.
연구 가설:
명시적으로 가설로 제시되지는 않았지만, 본 연구는 다음과 같은 전제를 기반으로 합니다.
- AZ91D-1.5CaO Eco-Mg 합금을 사용하면 SF6 보호 가스 없이 마그네슘 다이캐스팅이 가능합니다.
- 최적화된 주조 매개변수와 수직 사출 다이캐스팅 프레스는 공기 주입 마그네슘 주조의 성공적인 수행을 용이하게 합니다.
- 이 접근 방식은 마그네슘 주조 공정 경로의 지구 온난화 지수(GWP)를 크게 감소시킵니다.
5. 연구 방법론
연구 설계:
본 연구는 AZ91D-1.5CaO Eco-Mg 합금을 사용한 브레이크 레버리지 프로토타입의 다이캐스팅에 초점을 맞춘 실험적 설계를 채택했습니다. 연구는 수직 사출 다이캐스팅 프레스 기계를 사용하여 수행되었습니다.
자료 수집 방법:
자료는 Brembo Spa 시설에서 브레이크 레버리지 프로토타입의 실제 제조를 통해 수집되었습니다. 여기에는 보호 가스 없이 공기 환경에서 성공적인 생산을 달성하기 위해 주조 매개변수를 모니터링하고 조정하는 과정이 포함되었습니다. SEM 이미징을 사용한 미세 구조 분석은 주조 빌렛에 대해 수행되었습니다. 기계 특성 및 주조 매개변수가 문서화되었습니다.
분석 방법:
분석은 주로 질적 분석으로, GHG-free 다이캐스팅의 성공적인 시연에 초점을 맞추었습니다. 본 연구에서는 AZ91D-1.5CaO 합금의 공기 중 주조 가능성, 수직 사출 프레스의 효율성, 결과 프로토타입 품질을 평가했습니다. 자료 분석에는 주조 미세 구조(그림 3) 검토 및 기계 매개변수 평가(표 1)가 포함되었습니다. 알루미늄 대비 달성된 중량 감소가 정량적으로 평가되었습니다.
연구 대상 및 범위:
본 연구는 다음 사항에 초점을 맞추었습니다.
- 재료: 1.5% CaO로 개질된 AZ91D Eco-Mg 시리즈 합금.
- 부품: 자동차 브레이크 레버리지 프로토타입.
- 제조 공정: 수직 사출 프레스를 사용한 고압 다이캐스팅.
- 장소: 이탈리아 스테자노 Brembo 시설의 첨단 재료 연구 개발 연구소.
6. 주요 연구 결과:
핵심 연구 결과:
실험 절차는 SF6 또는 기타 보호 가스 없이 AZ91D-1.5CaO Eco-Mg 합금으로 브레이크 레버리지 프로토타입의 다이캐스팅을 성공적으로 시연했습니다. 주요 연구 결과는 다음과 같습니다.
- 수직 사출 다이캐스팅 프레스를 사용하여 AZ91D-1.5CaO Eco-Mg 합금의 공기 주입 다이캐스팅이 성공적으로 달성되었습니다.
- 현재 알루미늄 부품에 비해 마그네슘 프로토타입에서 32%의 중량 감소가 달성되었습니다.
- 주조 공정은 수직 사출 프레스의 짧은 사이클 시간 덕분에 주변 공기 중에서 안전하게 수행되었습니다.
- 정지형 용해로에서 700°C까지 과열된 AZ91D-1.5CaO 합금은 예열된 사출 챔버(220-250°C)에 주입 시 630°C 이상의 주입 온도를 유지했습니다.
- 용광로의 질소 캡은 산소 함량을 효과적으로 감소시켜 보호 플럭스의 필요성을 없앴습니다.
- 용융 마그네슘 합금은 점화 문제 없이 과열 조건에서 최대 1시간 동안 안전하게 유지되었습니다.
제시된 데이터 분석:
- 그림 1 (Fig.1)은 제품 수명 주기 전반에 걸쳐 중금속(1)과 경금속(2, 3)의 환경 영향 비교를 보여주는 세 가지 시나리오를 보여주며, 경량 솔루션의 잠재력과 1차 마그네슘 생산의 탄소 발자국 문제를 강조합니다.
- 그림 2 (Fig.2)는 고온 산화 거동에 대한 Pilling-Bedworth Ratio (PBR) 설명을 제공하며, 산화막 다공성을 응력 유형(인장 또는 압축) 및 산화막 균열과 연관시킵니다.
- 그림 3 (Fig.3)은 주조된 AZ91D-1.5CaO 빌렛 미세 구조의 SEM 이미지를 보여주며, α-Mg 및 결정립계에서 불연속적인 β-Mg17Al12 화합물과 함께 높은 알루미늄 함량 주조 마그네슘 합금의 일반적인 특징을 보여줍니다.
- 그림 4 (Fig.4)는 다이캐스팅된 브레이크 레버리지 프로토타입을 보여줍니다. (a) 인게이트 채널 및 스프루 포함, (b) 스프루 및 인게이트 제거 후 기계적 테스트 준비 완료.
- 표 1 (Tab.1)은 사출 플런저 속도, 플런저 스트로크, 형체 결합력, 투영 샷 면적, 특정 압력 및 사출력을 포함한 수직 사출 다이캐스팅 프레스의 주요 기계 특성을 요약합니다.
그림 목록:
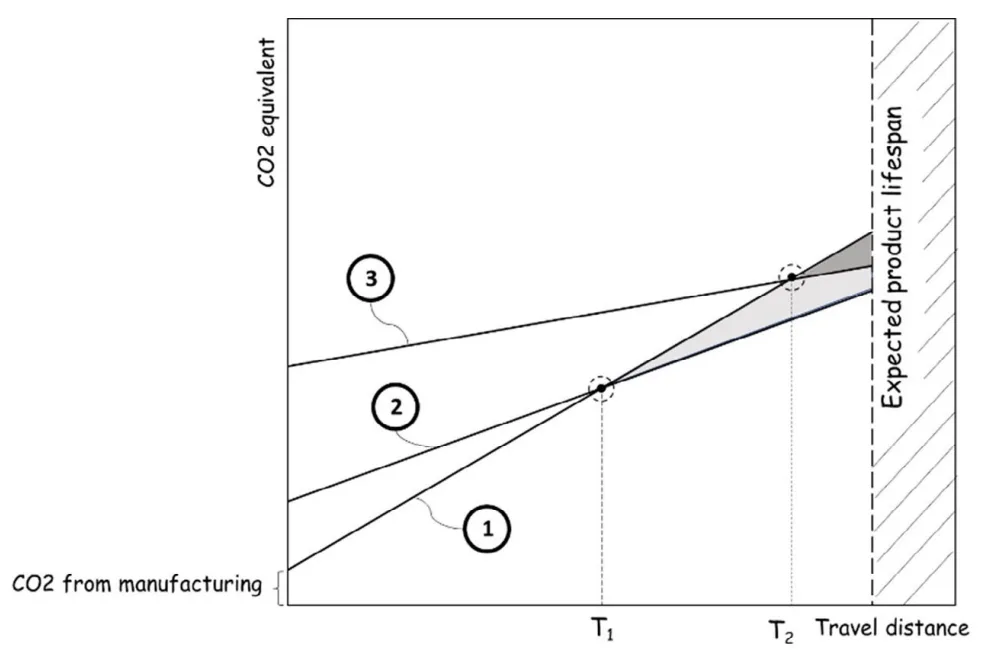
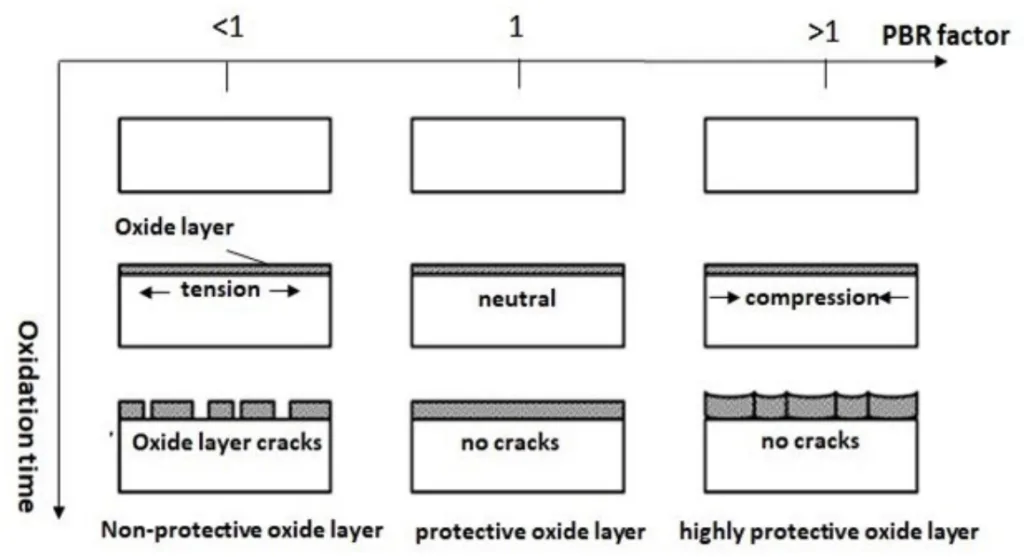
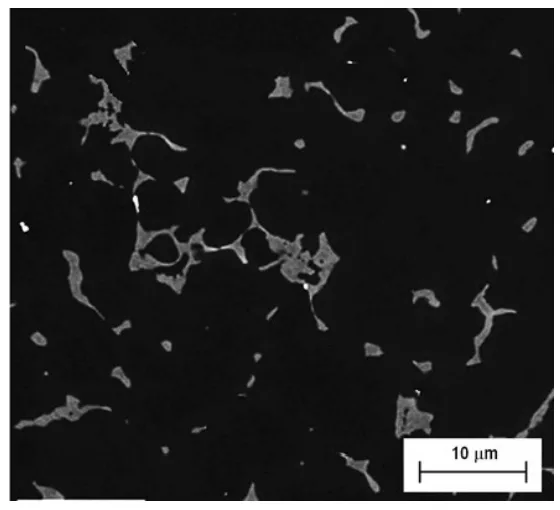
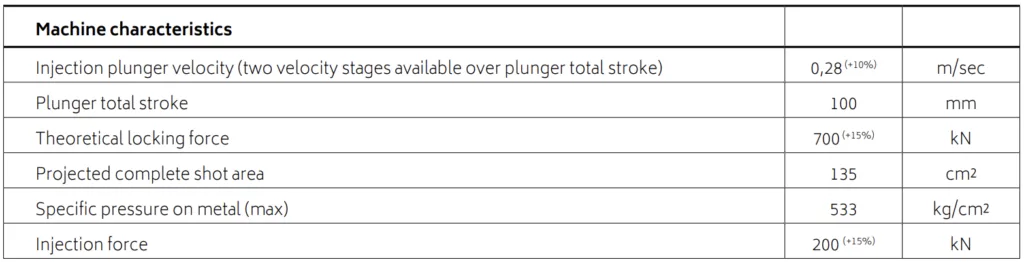
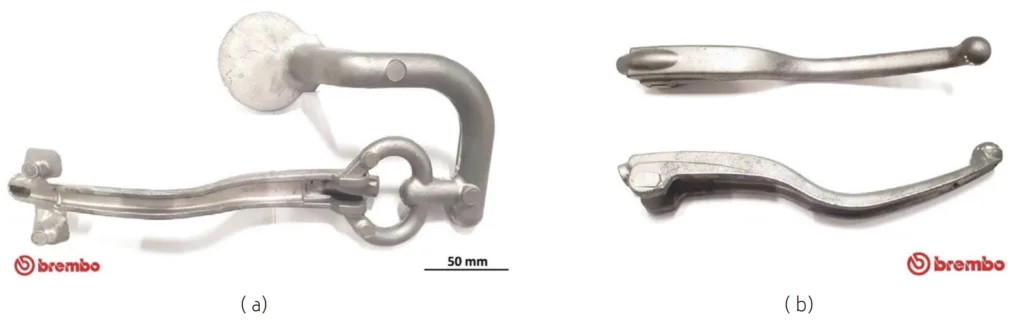
- Fig.1 - Three qualitative scenarios for addressing at-a-whole the environmental impact over the product lifespan of using light metals (2) and (3) to substitute the heavy solution (1). (경금속 (2) 및 (3)을 사용하여 무거운 솔루션 (1)을 대체하는 제품 수명 주기 전반에 걸친 전체적인 환경 영향을 해결하기 위한 세 가지 질적 시나리오)
- Fig.2 - The PBR explanation of the high temperature oxidation behavior of different metals and their oxides in correlation with porous or non-porous oxide film developed by air oxidation. (공기 산화에 의해 개발된 다공성 또는 비다공성 산화막과 관련된 다양한 금속 및 산화물의 고온 산화 거동에 대한 PBR 설명)
- Fig.3 - SEM image of as-cast billet received. (주조 빌렛 SEM 이미지)
- Fig.4 - a) The die-cast brake leverage with in-gate channels and sprue; b) die-cast brake leverage after re-moving sprue and in-gate channels. (a) 인게이트 채널 및 스프루가 있는 다이캐스트 브레이크 레버리지; b) 스프루 및 인게이트 제거 후 다이캐스트 브레이크 레버리지)
7. 결론:
주요 연구 결과 요약:
본 연구는 환경에 유해한 보호 가스 없이 AZ91D-CaO 합금을 사용하여 마그네슘 브레이크 레버리지 프로토타입을 제조하기 위한 수직 고압 다이캐스팅 공정을 성공적으로 시연했습니다. 이 GHG-free 공정은 알루미늄에 비해 32%의 중량 감소를 달성했습니다. 공정은 수직 프레스의 짧은 사이클 시간 덕분에 공기 중에서 안전하게 수행되었습니다. 본 연구는 경제적인 커버 가스 없는 다이캐스팅의 타당성과 Mg 및 Al 합금 모두에 사용할 수 있는 소형 저비용 프레스를 사용하여 상용 Eco-Mg 시스템 합금을 공기 중에서 가공할 수 있는 가능성을 시사합니다.
연구의 학문적 의의:
본 연구는 마그네슘 다이캐스팅에서 환경에 영향을 미치는 보호 가스를 제거하는 것의 타당성을 입증함으로써 학문 분야에 기여합니다. 특히 AZ91D-CaO 합금 및 수직 다이캐스팅 기술 적용을 통해 경량 금속 부품의 지속 가능한 제조 관행에 대한 귀중한 통찰력을 제공합니다.
실용적 의미:
본 연구의 실용적 의미는 자동차 산업에 매우 중요하며, 경량 자동차 부품 제조에 대한 친환경적인 접근 방식을 제공합니다. GHG-free 다이캐스팅 공정은 SF6 및 기타 유해 가스에 대한 의존도를 줄여 마그네슘 부품 생산을 위한 비용 효율적이고 환경적으로 책임 있는 솔루션을 제공합니다. 이는 자동차에 비가연성 마그네슘 합금의 광범위한 채택을 촉진하여 차량 중량 감소 및 연비 향상에 기여합니다.
연구의 한계 및 향후 연구 분야:
본 연구는 예비 테스트 캠페인을 나타냅니다. 산업적 적용을 위해 시연된 공정을 최적화하고 확장하기 위한 추가 연구가 권장됩니다. 브레이크 레버리지 프로토타입의 지속적인 기계적 테스트 및 검증이 필요합니다. 향후 연구에서는 공정 최적화, 장기 성능 평가, 그리고 이 GHG-free 다이캐스팅 방법의 다른 마그네슘 부품 및 합금 시스템에 대한 광범위한 적용을 탐구해야 합니다.
8. 참고 문헌:
[1] EU Regulation (EU) No 517/2014.
[2] S. Ramakrishnan et all., "Global warming impact of the magnesium produced in China using the Pidgeon process," Resources, Conservation and Recycling, Volume 42, 1: 49–64, 2004.
[3] D'Errico, F., Ranza, L. "Guidelines for the market competitiveness of sustainable lightweight design by magnesium solution: a new Life Cycle Assessment integrated approach”, Paper presented at the 72nd Annual World Magnesium Conference, Vancouver, Canada, 17-19 May 2015.
[4] H.E. Friedrich, et all., "Solutions for Next Generation Automotive Lightweight Concepts Based on Material Selection and Functional Integration", Magnesium Technology 2018, The Minerals, Metals & Materials Society, 343-348, 2018.
[5] N. B. Pilling, R. E. Bedworth, "The oxidation of metals at high temperatures", J. Inst. Met, 29: 529-591, 1923.
[6] E. F. Emley, "Principles of magnesium technology" Pergamon Press, Oxford, New York, 1966.
[7] G. C. Wood, "High-temperature oxidation of alloys", Oxidation of Metals, 2:11-57, 1970.
[8] F. Czerwinski, "Oxidation Characteristics of Magnesium Alloys", JOM, 64 (12):1477-1483, 2012.
[9] Y. M. Kim, et all., "Key factor influencing the ignition resistance of magnesium alloys at elevated temperatures", Scripta Materialia, 65(11):958-961, 2011.
[10] M. Sakamoto, et all., "Suppression of ignition and burning of molten Mg alloys by Ca bearing stable oxide", Journal of Materials Science Letters, 16 (12):1048-1050, 1997.
[11] S.H. Ha et all., "Effect of CaO on oxidation resistance and microstructure of pure Mg", Materials Transactions, 49(5) 1081-1083, 2008
[12] S.K. KIM and J. H. SEO, "Magnesium-based alloy for high temperature and manufacturing method thereof", US Patent 8,808,423, 2014.
[13] J.K. Lee, S.K. Kim, "Effect of CaO Addition on the Ignition Resistance of. Mg-Al Alloys", Materials Transactions, Vol. 52, 1483-1488, 2011.
9. 저작권:
- 본 자료는 "F. D'Errico, D. Casari"의 논문: "Eco-sustainable lightweight automotive part manufacturing: GHGs-free die casting of brake leverage prototype made of AZ91D-1.5CaO magnesium alloy"를 기반으로 합니다.
- 논문 출처: [DOI URL] (DOI URL은 텍스트에 제공되지 않았습니다. 가능한 경우 추가하고, 그렇지 않으면 저널 링크를 사용하십시오.)
본 자료는 위 논문을 요약한 것으로, 상업적 목적으로 무단 사용하는 것을 금지합니다.
Copyright © 2025 CASTMAN. All rights reserved.