본 논문 요약은 ['고압 다이캐스팅 공정에서 다이캐스팅 매개변수에 대한 유한 요소 해석'] 논문을 기반으로 작성되었으며, ['CHINA FOUNDRY']에 발표되었습니다.
1. 개요:
- 제목: 고압 다이캐스팅 공정에서 다이캐스팅 매개변수에 대한 유한 요소 해석 (Finite element analysis for die casting parameters in high-pressure die casting process)
- 저자: 신위친, 용수, 지안 첸, 란준 리우 (Xin-yu Qin, Yong Su, Jian Chen, Lan-jun Liu)
- 출판 연도: 2019년
- 출판 저널/학회: CHINA FOUNDRY
- 키워드: 알루미늄 합금; 다이캐스팅 공정; 시뮬레이션 최적화 (aluminum alloy; die casting process; simulation optimization)
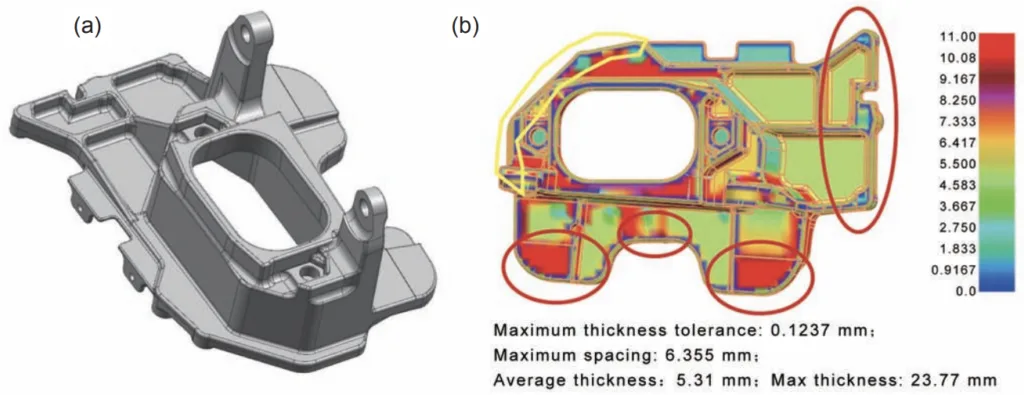
2. 연구 배경:
연구 주제 배경:
알루미늄 합금 다이캐스팅 기술은 액체 금속을 고속으로 캐비티에 채우고 고압 하에서 응고시키는 성형 방법입니다. 다이캐스팅에 대한 현재 연구는 주로 계면 열 전달, 사출 속도 및 다이캐스팅 온도에 중점을 두고 있습니다.
기존 연구 현황:
기존 연구에서는 다이캐스팅의 중요한 측면에 대한 기초 지식을 확립했습니다. Paliani [1]는 실험적 방법을 통해 역모델을 개발하여 액체 금속과 사출 챔버 사이의 열 전달 계수가 약 1.2 kW·m⁻²·K⁻¹임을 확인했습니다. El-Mahallawy 등 [2]은 주조 밀도와 게이트 속도 사이의 반비례 관계를 강조했습니다. Pitsaris 등 [3]은 다이캐스팅 온도가 다이캐스팅의 기계적 특성에 가장 큰 영향을 미친다고 강조하며, 온도 증가는 예비 결정화를 감소시키고 기계적 특성을 향상시킨다고 언급했습니다. Syrcros [4]는 사출 속도, 주조 온도, 충전 시간 및 압력이 다이캐스팅 품질에 영향을 미치는 주요 요인이라고 밝혔습니다.
연구의 필요성:
컴퓨터 기술의 발전으로 고압 다이캐스팅(HPDC) 공정을 시각화하는 것이 더욱 편리해졌습니다. 본 연구에서는 ProCAST 유한 요소 해석 소프트웨어를 활용하여 HPDC 공정 내 다이캐스팅 공정 매개변수를 시각화하고, 대표적인 쉘 부품의 다이캐스팅 공정 연구를 통해 쉘 부품 다이캐스팅 규칙을 밝히는 것을 목표로 합니다.
3. 연구 목적 및 연구 질문:
연구 목적:
주요 연구 목적은 쉘 부품 다이캐스팅을 지배하는 규칙을 밝히는 것입니다. 이는 ProCAST 유한 요소 해석 소프트웨어를 활용하여 공정을 시각화하고 분석함으로써 단일 대표 쉘 부품의 다이캐스팅 공정에 대한 상세한 연구를 통해 달성됩니다.
주요 연구 내용:
본 연구는 다음 네 가지 주요 다이캐스팅 공정 매개변수에 중점을 둡니다.
- 사출 온도 (Injection temperature)
- 저압 속도 (Low-pressure velocity)
- 저압 및 고압 속도 전환 위치 (Switching position of low- and high-pressure velocity)
- 고압 속도 (High-pressure velocity)
연구 가설:
본 연구는 앞서 언급한 다이캐스팅 매개변수의 체계적인 시뮬레이션 및 최적화를 통해 예비 결정화 및 공기 혼입과 같은 결함을 완화하여 HPDC 부품의 품질을 향상시킬 수 있다는 가설을 암묵적으로 설정합니다.
4. 연구 방법론
연구 설계:
본 연구는 ProCAST 소프트웨어를 활용한 시뮬레이션 기반 설계를 채택하여 다이캐스팅 공정을 시각화하고 최적화합니다. 이는 시뮬레이션 결과를 검증하기 위해 YZM-800T 다이캐스팅 기계에서 수행된 실험적 검증으로 보완됩니다.
자료 수집 방법:
자료는 다음 방법을 통해 수집됩니다.
- ProCAST 소프트웨어 시뮬레이션: 다양한 공정 매개변수 하에서 유체 흐름, 온도 분포 및 응고 패턴에 대한 데이터를 생성합니다.
- YZM-800T 다이캐스팅 기계의 실험적 시험: 특정 매개변수 세트에서 물리적 주물을 생산합니다.
- 생산된 주물의 X선 검사: 내부 품질을 평가하고 수축과 같은 결함을 감지합니다.
분석 방법:
분석은 ProCAST 내에서 유한 요소 해석을 사용하여 HPDC 공정을 시뮬레이션하고 시각화하여 수행됩니다. 그런 다음 시뮬레이션 결과를 실험 결과 및 X선 검사 데이터와 비교하여 최적화된 매개변수를 검증합니다.
연구 대상 및 범위:
본 연구는 쉘 다이캐스팅, 특히 ADC12 알루미늄 합금 활용에 중점을 둡니다. 범위는 단일 대표 쉘 부품 형상에 대한 HPDC 공정 내 사출 매개변수 최적화로 제한됩니다. 주물의 재료는 ADC12 알루미늄 합금이며 주물의 모양은 그림 1(a)에 나와 있습니다.
5. 주요 연구 결과:
주요 연구 결과:
본 연구는 다이캐스팅 매개변수의 영향에 대한 몇 가지 주요 결과를 도출했습니다.
- 사출 온도 및 저압 속도: 더 높은 사출 온도와 저압 속도는 사출 챔버 내 예비 결정화를 완화하는 것으로 나타났습니다.
- 저압 속도 제한: 0.2 m·s⁻¹를 초과하는 저압 속도는 챔버 내 공기 혼입을 유발합니다.
- 고압 속도 제한: 고압 속도가 2.5 m·s⁻¹를 초과하면 최종 충전 위치의 오버플로우 채널이 액체 금속에 의해 너무 일찍 덮입니다.
- 최적 매개변수: 시뮬레이션을 통해 최적 매개변수는 다음과 같이 결정되었습니다.
- 사출 온도: 650 °C
- 저압 속도: 0.2 m·s⁻¹
- 저압 및 고압 속도 전환 위치: 320 mm
- 고압 속도: 2 m·s⁻¹
데이터 해석:
그림 4 및 그림 5와 같은 그림에 시각화된 시뮬레이션 결과는 저압 속도 및 사출 온도 변화가 예비 결정화 및 공기 혼입에 미치는 영향을 보여주었습니다. 그림 4는 0.1 m·s⁻¹의 저압 속도에서 챔버에서 예비 결정화가 발생하는 반면, 0.3 m·s⁻¹에서는 심각한 공기 혼입이 관찰됨을 보여줍니다. 그림 5는 다이캐스팅 온도를 높이면 예비 결정화 영역이 감소함을 보여줍니다. 그림 7은 고압 속도가 충전 공정 및 오버플로우 채널 막힘에 미치는 영향을 더욱 명확히 합니다.
그림 목록:
- Fig. 1: (a) 3차원 주조 모델; (b) 주조의 벽 두께 분포 (Three-dimensional casting model; Wall thickness distribution of casting)
- Fig. 2: 주입 시스템의 개략도 (Schematic diagram of pouring scheme)
- Fig. 3: 기하학적 모델의 개략도 (Schematic diagram of geometric model)
- Fig. 4: 저압 속도에 따른 충전 다이어그램: (a) 0.1 m·s⁻¹, (b) 0.2 m·s⁻¹, (c) 0.3 m·s⁻¹ (Filling diagram for different low-pressure velocities)
- Fig. 5: 사출 온도에 따른 예비 결정화 다이어그램: (a) 640 °C, (b) 650 °C, (c) 660 °C (Pre-crystallization diagram of different injection temperatures)
- Fig. 6: 전환 위치에 따른 충전 다이어그램: (a) 300 mm, (b) 320 mm, (c) 340 mm (Filling diagram of different switching positions)
- Fig. 7: 고압 속도에 따른 충전 다이어그램: (a1) 2 m·s⁻¹, 70% 충전; (a2) 2 m·s⁻¹, 80% 충전; (a3) 2 m·s⁻¹, 90% 충전; (b1) 2.5 m·s⁻¹, 70% 충전; (b2) 2.5 m·s⁻¹, 80% 충전; (b3) 2.5 m·s⁻¹, 90% 충전; (c1) 3 m·s⁻¹, 70% 충전; (c2) 3 m·s⁻¹, 80% 충전; (c3) 3 m·s⁻¹, 90% 충전 (Filling diagram for different high-pressure velocities)
- Fig. 8: 측면도 (a) 및 정면도 (b) X선 주조 검출 (Side view and front view of X-ray detection of casting)
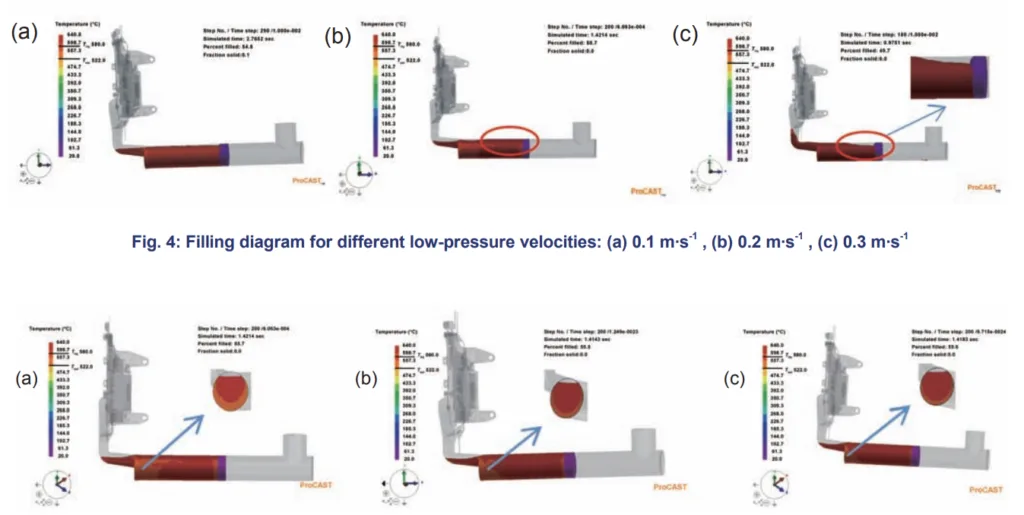

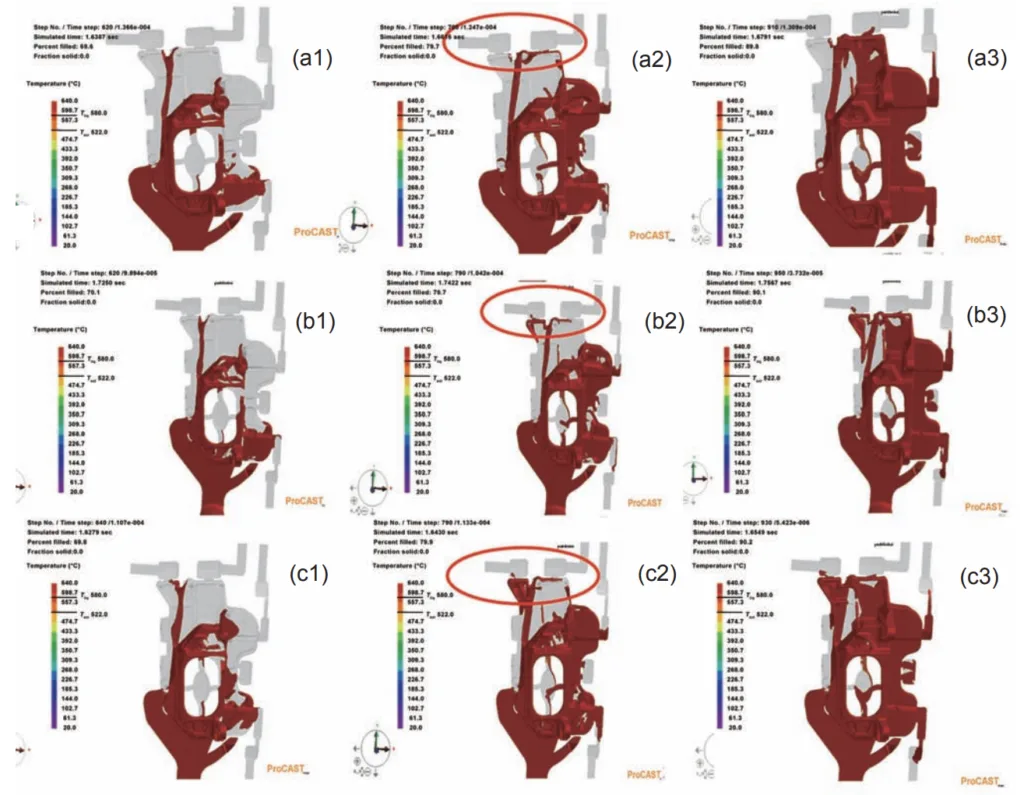
6. Conclusion:
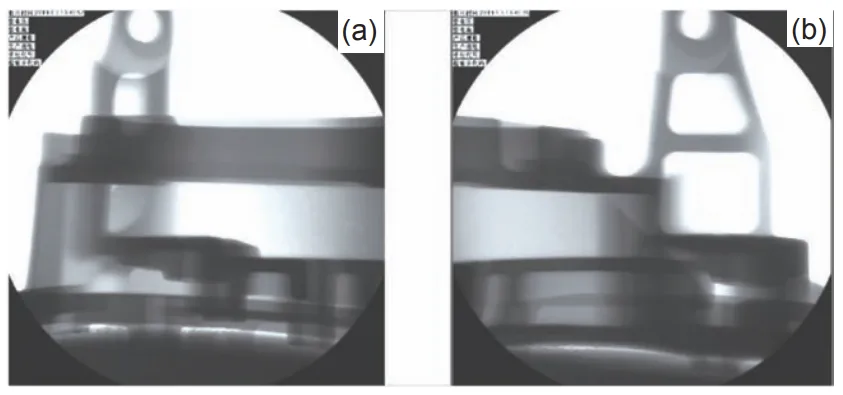
6. 결론:
주요 결과 요약:
본 연구에서는 주조 구조 분석 및 벽 두께 고려 사항을 기반으로 게이팅 시스템과 오버플로우 시스템을 성공적으로 설계했습니다. 본 연구에서는 ProCAST 시뮬레이션 및 실험적 검증을 통해 ADC12 알루미늄 합금 쉘 부품의 HPDC에 대한 최적 다이캐스팅 매개변수를 확인했습니다. 최적 매개변수(사출 온도 650 °C, 저압 속도 0.2 m·s⁻¹, 전환 위치 320 mm, 고압 속도 2 m·s⁻¹)는 예비 결정화 및 공기 혼입을 효과적으로 최소화하여 주조 품질을 향상시킵니다.
연구의 학문적 의의:
본 연구는 유한 요소 해석, 특히 ProCAST 소프트웨어를 다이캐스팅 공정 매개변수 최적화에 효과적으로 적용한 사례를 보여줍니다. HPDC에서 사출 매개변수와 주조 결함 간의 복잡한 상호 작용에 대한 귀중한 통찰력을 제공하여 공정에 대한 이론적 이해에 기여합니다.
실용적 의미:
결정된 최적 매개변수는 다이캐스팅 산업에 직접적인 실질적 이점을 제공합니다. ADC12 알루미늄 합금 쉘 부품 생산에 이러한 매개변수를 구현하면 주조 품질 향상, 결함률 감소 및 생산 효율성 향상으로 이어질 수 있습니다. 그림 2에 제시된 게이팅 시스템 및 오버플로우 시스템 설계는 유사한 응용 분야에 대한 청사진을 제공합니다.
연구의 한계
본 연구는 주로 단일 대표 쉘 부품 형상 및 ADC12 알루미늄 합금에 초점을 맞추고 있습니다. 최적화된 매개변수의 다양한 주조 형상, 합금 시스템 및 다이캐스팅 기계 유형에 대한 일반적인 적용 가능성은 추가 연구가 필요합니다.
7. 향후 후속 연구:
- 후속 연구 방향
향후 연구에서는 다음 사항에 대한 조사를 확대해야 합니다.- 더 넓은 범위의 주조 형상 및 복잡성에 대한 최적화된 매개변수의 적용 가능성을 탐색합니다.
- 다양한 알루미늄 합금 및 기타 다이캐스팅 재료를 조사하여 연구 결과의 범위를 넓힙니다.
- 다이 온도 및 냉각 속도와 같은 추가 공정 매개변수가 주조 품질에 미치는 영향을 조사합니다.
- 예측 정확도를 높이고 추가 결함 메커니즘을 통합하기 위해 보다 정교한 시뮬레이션 모델을 개발합니다.
- 추가 탐구가 필요한 영역
다음 영역에 대한 추가 탐구가 필요합니다.- CAE 도구를 사용하여 복잡한 형상에 대한 게이팅 및 오버플로우 시스템을 최적화합니다.
- 시뮬레이션 피드백을 기반으로 공정 매개변수를 동적으로 조정하는 실시간 제어 시스템을 조사합니다.
- 시뮬레이션 최적화된 매개변수를 사용하여 생산된 주물의 장기적인 성능 및 신뢰성을 연구합니다.
8. 참고 문헌:
- [1] Paliani P. Thermoelastic Deformation of Cold Chamber Die Casting Machine Shot Sleeves [MS Thesis]. US: Ohio State University, 1993.
- [2] El-Mahallawy AN, Taha M A, Pokora E, et al. On the influence of process variables on the thermal conditions and properties of high pressure die-cast magnesium alloys. Journal of Materials Processing Technology, 1997, 73(1): 125-138.
- [3] Pitsaris C, Abbott T, Davies C, et al. Influence of Process Parameters on the Microstructure and Mechanical Properties of Magnesium Die Castings. In: Magnesium: Proceedings Applications of the 6th International Conference Magnesium Alloys and Their Applications, 2005.
- [4] Syrcos G P. Die casting process optimization using Taguchi methods. Journal of Materials Processing Technology, 2003, 135(1): 68-74.
- [5] Kwon H J, Kwon H K. Computer aided engineering (CAE) simulation for the design optimization of gate system on high pressure die casting (HPDC) process. Robotics and Computer-Integrated Manufacturing, 2018, 55: 147-153.
- [6] Kwon H K, Seo K K. Simulation Study on HPDC Process for Automobile Part with Aluminum Alloy. Materials Science Forum, 2013, 761: 4.
- [7] Duan H Z, Shen J N, Li Y P. Comparative Analysis of HPDC Process of an Auto Part with ProCAST and FLOW-3D. Applied Mechanics and Materials, 2012, 184-185: 90-94.
- [8] Rai JK, Lajimi A M, Xirouchakis P. An intelligent system for predicting HPDC process variables in interactive environment. Journal of Materials Processing Technology, 2008, 203(1-3): 72-79.
- [9] Kwon H J, Kwon H K. Computer aided engineering (CAE) simulation for the design optimization of gate system on high pressure die casting (HPDC) process. Robotics and Computer-Integrated Manufacturing, 2019, 55: 147-153.
9. 저작권:
- 본 자료는 "용수"의 논문: "고압 다이캐스팅 공정에서 다이캐스팅 매개변수에 대한 유한 요소 해석"을 기반으로 합니다.
- 논문 출처: https://doi.org/10.1007/s41230-019-8088-8
본 자료는 위 논문을 기반으로 요약되었으며, 상업적 목적으로 무단 사용하는 것을 금지합니다.
Copyright © 2025 CASTMAN. All rights reserved.