이 소개 자료는 "[CSIRO Mathematical and Information Sciences, Victoria, Australia]"에서 발행한 논문 "[Modelling the High Pressure Die Casting Process Using SPH]"에 기반하여 작성되었습니다.
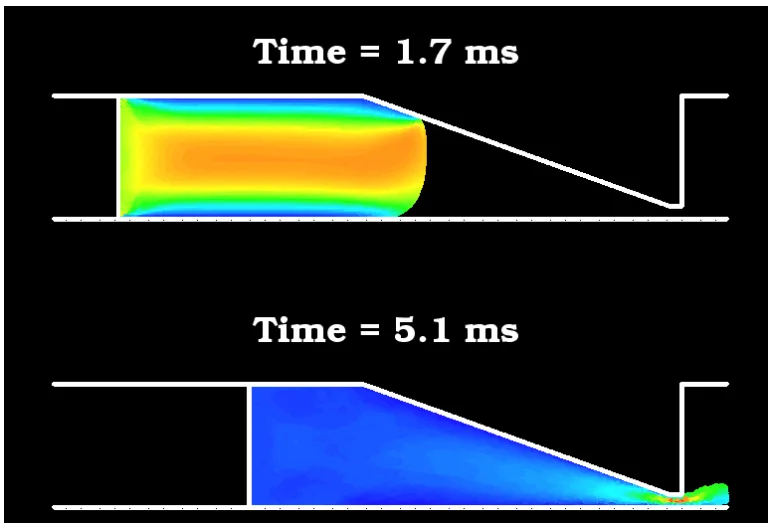
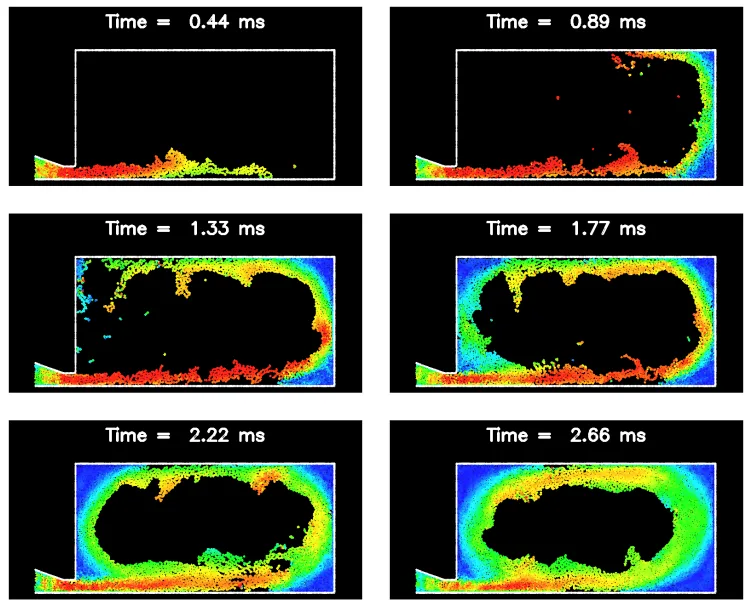
1. 개요:
- 논문명: Modelling the High Pressure Die Casting Process Using SPH
- 저자: Paul W. Cleary and Joseph Ha
- 발표 연도: 2011년 (10월)
- 게재 학술지/학회: CRC for Cast Metals Manufacturing (CAST), CSIRO Mathematical and Information Sciences, Victoria, Australia.
- 키워드: 고압 다이캐스팅 (HPDC), SPH (Smoothed Particle Hydrodynamics), 수치 모델링, 유동, 금형 충전, 열전달, 응고, 자유 표면 유동
2. 초록:
본 논문에서는 지난 4년간 CAST 지원 프로젝트를 통해 이루어진 HPDC의 SPH 모델링 연구 진행 상황을 검토합니다. 2차원 단순 금형 충전 초기 예시들은 유동 패턴의 복잡성, 특히 자유 표면 거동 및 분열의 역할을 보여줍니다. 이러한 단순 금형 충전에 열전달 포함 효과, 특히 금형 내부의 열경계 조건 효과와 금형 자체로의 결합 전도 모델링의 중요성이 제시됩니다. SPH 예측의 정확성을 입증하기 위해 수류 상사 실험을 이용한 두 가지 검증 예시가 제공됩니다. 3D 모델링으로의 확장 및 복잡한 3차원 금형 형상을 표현하는 데 사용된 방법론이 기술됩니다. 실제 산업 부품의 충전을 모델링하기 위한 이 SPH 시스템의 사용이 제시됩니다. 금형 충전 순서의 중요성과 모서리 및 완만하게 곡선진 표면에서의 유동 분리 역할이 나타납니다. 표면 파편화 정도, 액적 형성 및 보이드의 강한 과도기적 특성 또한 보여줍니다. 마지막으로 실제 자동차 피스톤 헤드의 러너, 게이트 및 금형 충전이 제시되고 이러한 대규모 계산에 내재된 어려움이 논의됩니다.
3. 서론:
고압 다이캐스팅(HPDC)은 특히 자동차 산업에서 변속기 하우징 및 피스톤 헤드와 같은 부품의 대량 생산, 저비용 제조를 위한 중요한 공정입니다. HPDC에서는 액체 금속(일반적으로 알루미늄 합금)이 고속(약 50~100 m/s) 및 초고압으로 복잡한 금형으로 사출됩니다. 이 공정은 상당한 자유 표면 파편화를 동반하는 강한 3차원 유체 유동을 포함합니다. 최소한의 기공을 가진 균일한 주조 부품을 형성하는 데에는 금형의 여러 부분이 채워지는 순서와 가스 배출구의 위치가 중요하며, 이는 게이팅 시스템 설계와 금형 형상에 의해 결정됩니다. 효과적인 금형 충전 제어 및 금형 열 성능 개발을 포함한 개선된 금형 설계를 통해 제품 품질과 공정 생산성을 모두 향상시킬 수 있습니다. 수치 시뮬레이션은 다양한 금형 설계 및 충전 공정의 효과를 연구하는 강력하고 비용 효율적인 방법을 제공합니다.
4. 연구 요약:
연구 주제의 배경:
HPDC는 고속, 고압으로 용융 금속을 복잡한 금형에 주입하는 것이 특징인 핵심 산업 공정입니다. 복잡한 유동 패턴, 자유 표면 파편화, 그리고 기공 발생 가능성은 고품질 주물 생산에 상당한 어려움을 야기합니다. 금형 충전 공정을 이해하고 제어하는 것은 결함을 최소화하는 데 매우 중요합니다.
선행 연구 현황:
주조에서 계면 유동을 모델링하기 위해 MAC(marker and cell) 및 VOF(volume of fluid)와 같은 오일러리안 기법이 사용되어 왔습니다. VOF는 널리 사용되며 상용 소프트웨어(예: MAGMAsoft, Flow-3D)에도 적용되지만, 복잡한 계면 현상의 파편화 및 합체에 어려움이 있을 수 있으며 수치 확산 문제가 발생할 수 있습니다. 라그랑지안 입자법인 SPH(Smoothed Particle Hydrodynamics)는 HPDC에서 발견되는 복잡한 자유 표면 운동, 액적 형성 및 스플래싱을 포함하는 유동에 특히 적합합니다. SPH는 복잡한 자유 표면 모델링, 운동량 지배 유동 처리, 응고 및 다상 유동과 같은 복잡한 물리 현상 구현에 장점이 있습니다. 저자들의 이전 연구(Cleary, et al. 2000; Ha and Cleary, 2000)에서는 2D HPDC에 대한 SPH 적용 및 수류 상사 실험과의 양호한 비교 결과를 보여주었습니다.
연구 목적:
본 논문은 4년간의 CAST 지원 프로젝트를 통해 SPH를 사용하여 HPDC 공정을 모델링하는 데 있어 이루어진 진전을 검토하는 것을 목표로 합니다. 또한 실제 HPDC 예제에서 상세한 유체 유동 시뮬레이션에 대한 새로운 결과를 제시하여 복잡한 3D 형상 및 현상을 처리하는 SPH의 능력을 보여줍니다.
핵심 연구 내용:
본 연구는 HPDC 시뮬레이션을 위한 SPH 방법의 적용 및 개발에 중점을 둡니다. 이는 다음을 포함합니다:
- SPH 방법론: 연속 방정식, 운동량 방정식, 에너지 방정식, 상태 방정식 등 SPH 지배 방정식과 경계 조건 및 수치 구현 측면을 상세히 설명합니다.
- 2D 수치 연구: 단순한 금형 형상(직사각형, C자형)의 등온 충전을 시뮬레이션하여 유동 패턴, 자유 표면 거동, 파편화 및 금형, 게이트 또는 러너 형상 변경 효과를 이해합니다.
- 검증: 원형 코어가 있는 원판형 금형과 S자형 캐비티에 대한 수류 상사 실험 결과와 2D SPH 시뮬레이션 결과를 비교하여 SPH 예측의 정확성을 평가합니다.
- 열전달 및 응고 포함: C자형 금형의 충전 과정에서 열전달, 온도 의존적 점성, 열경계 조건(등온 대 결합된 금형 전도), 잠열 방출 효과를 조사합니다.
- 3D 모델링: 복잡한 3D 산업 부품(일반 부품 및 실제 자동차 피스톤 헤드)의 등온 유동 모델링으로 SPH를 확장하여 유동 분리, 파편화 및 충전 순서를 강조합니다.
5. 연구 방법론
연구 설계:
본 연구는 라그랑지안 수치 방법인 SPH(Smoothed Particle Hydrodynamics)를 사용합니다. SPH에서 유체는 물리적 특성(질량, 온도, 밀도, 속도)을 가진 입자 집합으로 표현됩니다. 이 입자들은 움직이는 보간점이며, 이들의 운동은 SPH 형태로 변환된 나비에-스토크스 방정식에 의해 지배됩니다. 보간 과정은 주변 입자로부터 정보를 평활화하기 위해 커널 함수를 사용합니다.
데이터 수집 및 분석 방법:
SPH 공식은 다음을 포함합니다:
- 연속 방정식:
dρa/dt = Σb mb(va - vb) · ∇Wab
(식 3) - 운동량 방정식:
dva/dt = - Σb mb [(Pa/ρa²) + (Pb/ρb²) + Πab] ∇Wab + g
(식 4의 수정된 형태, 여기서 Πab는 점성 항 포함:(ξ 4μaμb)/(ρaρb(μa+μb)) (vab·rab)/(rab²+η²)
) - 상태 방정식:
P = P₀[ (ρ/ρ₀)γ - 1 ]
(식 5),P₀/ρ₀ = cs² = 100V²
(식 6) 및 γ=7. - 에너지 방정식 (엔탈피 공식):
dHa/dt = Σb 4mb(kakb)/(ρaρb(ka+kb)) (Tab rab·∇Wab)/(rab²+η²) - Σb 2mb (ξμaμb)/(ρaρb(μa+μb)) ((vab·rab)² rab·∇Wab)/((rab²+η²)²)
(식 7), 여기서H = ∫cp(θ)dθ + L[1-fs(T)]
(식 8). - 경계 조건: 법선 방향 경계력에 대한 반발형 레너드-존스 포텐셜 힘장 및 비활강 조건을 위한 전단력 합산에 경계 입자 포함.
- 이웃 탐색: 이웃 입자의 효율적인 식별을 위해 연결 리스트가 있는 검색 그리드 사용.
- 3D 초기 설정: CAD 모델에서 형상 설명 획득, 상용 메시 생성기 사용, 그리고 SPH 경계 및 유체 입자, 질량 및 초기 특성을 정의하기 위한 자체 개발 전처리기 사용.
다양한 시나리오에 대해 시뮬레이션을 수행했으며, 결과는 속도, 온도 또는 점성으로 음영 처리된 입자 플롯과 3D 유동에 대한 렌더링된 표면 메시를 통해 시각화되었습니다. 검증을 위해 SPH 결과는 수류 상사 실험의 실험 데이터와 비교되었습니다.
연구 주제 및 범위:
본 연구는 HPDC 모델링의 여러 측면을 다룹니다:
- 2D 등온 금형 충전:
- 단순 금형(짧은 직사각형, 긴 직사각형, 인서트가 있는 C자형 금형) 충전을 통해 유동 패턴, 제트 거동, 파편화 및 기공 형성을 연구합니다. 레이놀즈 수(Re) 500 및 2,500이 사용되었습니다.
- C자형 금형, 게이트 또는 러너 형상 변경(역방향 샷 슬리브, 대칭형 샷 슬리브, 쐐기형 주입구)이 충전 패턴에 미치는 영향.
- 검증:
- Schmid와 Klein(1995, 1998)의 수류 상사 실험과 SPH 시뮬레이션 비교:
- 코어가 있는 원판형 금형 (금형 두께 2 mm, 게이트 속도 18.0 m/s).
- S자형 캐비티 (금형 두께 2 mm, 게이트 속도 8.7 m/s).
- Schmid와 Klein(1995, 1998)의 수류 상사 실험과 SPH 시뮬레이션 비교:
- 열전달 및 응고 포함:
- 온도 의존적 점성 모델(Thomas 방정식:
μ= 4.5×10⁻⁶ ρm (1 + 2.5 fs + 10.05 fs² + 0.000273 exp(16.6fs))
)을 사용하여 열전달을 포함한 C자형 금형 충전 모델링. - 열경계 조건의 영향 조사 (27°C 등온 금형 벽 대 외부 온도 350°C의 강철 금형 벽으로의 결합 열전도).
- 잠열 방출 효과 평가 (Al-1Cu-10Si 합금의 경우 495 kJ/kg).
- 온도 의존적 점성 모델(Thomas 방정식:
- 3D 등온 유동 모델링:
- 일반 산업 부품(원통형 구멍이 있는 슬롯형 환형 확장부, 길이 약 200 mm, 입자 292,931개, Re=27,875, 게이트 속도 44 m/s)의 충전.
- 실제 자동차 피스톤 헤드(원통 대칭 상부, 복잡한 하부, 폭 3mm x 길이 38mm 게이트)의 충전.
6. 주요 결과:
주요 결과:
- 2D 등온 충전:
- SPH 시뮬레이션은 단순한 2D 금형에서도 제트 유동, 모서리에서의 유동 분리, 자유 표면 파편화, 액적 형성 등 복잡한 유동 패턴을 보여주었습니다.
- 충전 순서는 금형 형상에 크게 의존하며, 얇은 벽 부분에서는 역충전이 일반적이었습니다.
- 러너 형상은 게이트에서의 유체 속도 프로파일과 후속 금형 충전에 상당한 영향을 미칩니다.
- 게이트/러너 설계 변경(예: 역방향 샷 슬리브, 쐐기형 주입구)은 유체 분포에 약간의 영향을 미칠 수 있으며, 주입이 쉬울수록 유동이 더 넓게 퍼지고 초기 영역의 충전이 덜 완전해질 수 있습니다.
- 검증:
- SPH 시뮬레이션은 코어가 있는 원판형 금형과 S자형 캐비티 모두에 대한 수류 상사 실험과 잘 일치하여 유동의 미세한 세부 사항, 제트 형상, 기공 형성 및 전체 충전 패턴을 포착했습니다.
- 열전달 및 응고:
- 열전달 및 응고를 포함하면 등온 경우에 비해 충전 패턴이 크게 변경됩니다. 금형 벽 근처의 응고 물질은 자유 유동 제트를 금형 중앙으로 밀어낼 수 있습니다.
- 등온 금형 경계 조건은 너무 많은 열을 제거하여 조기 응고(콜드셧)를 유발하므로 금형으로의 결합 열전도 모델링이 중요합니다. 실제 금형 열 특성은 냉각 및 응고 속도를 제한합니다.
- 잠열 방출은 예측된 응고량을 줄이고 머시존(고액공존영역)을 좁히며, 자유 흐름에서 응고된 입자의 '슬러리'를 형성할 수 있습니다.
- 3D 등온 유동:
- SPH는 복잡한 3D 금형 충전을 성공적으로 모델링하여 상당한 유동 분리, 자유 표면 파편화 및 과도기적 기공 형성을 보여주었습니다.
- 3D 부품의 충전 순서는 복잡하며 반드시 게이트 근접성에 따라 결정되지 않습니다.
- 금형 내 '가상 카메라'를 사용한 시각화는 국부적인 유동 거동에 대한 상세한 통찰력을 제공했습니다.
- 일반 부품 및 자동차 피스톤 헤드의 시뮬레이션은 대규모 입자 수 관리 및 미세한 기하학적 특징 해결과 같은 과제를 강조하면서 산업적으로 관련된 대규모 문제를 처리하는 SPH의 능력을 입증했습니다.
그림 목록:
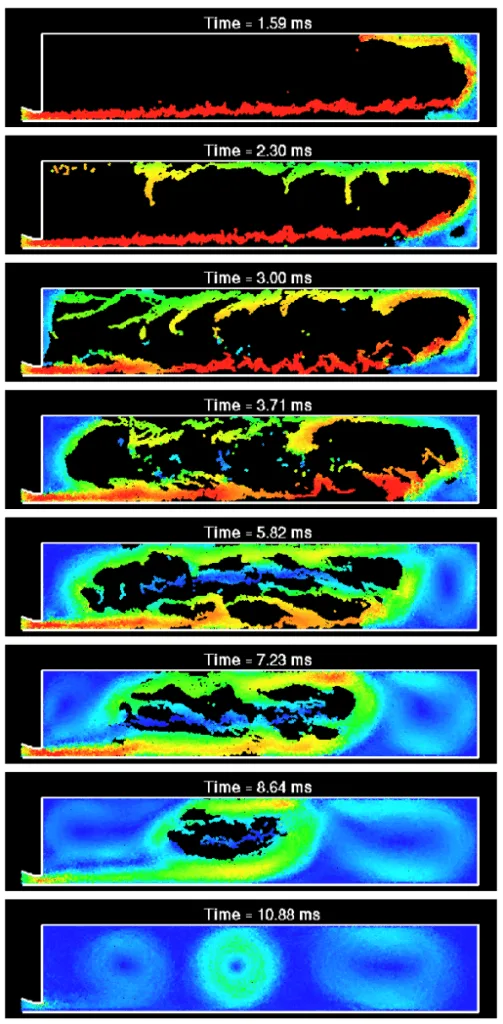
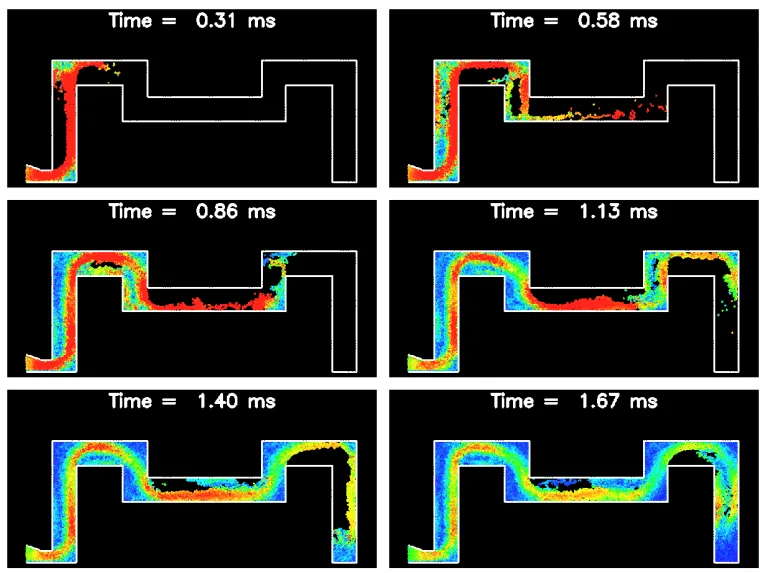
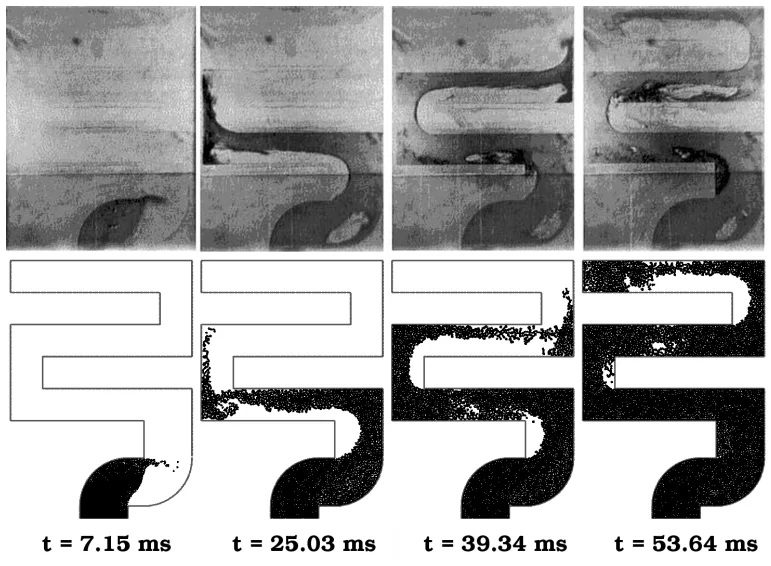
- Figure 1: View of the shot sleeve and piston used to accelerate the metal through the gate and into the die.
- Figure 2: Filling of a short rectangular die for Re=500.
- Figure 3: Filling of a long rectangular die for Re=500.
- Figure 4: Filling of C shaped die with insert for Re=2500
- Figure 5: Fill patterns for a C shaped die with different gates at time 0.50 ms.
- Figure 6: Fill patterns for a C shaped die with different gates at time 1.50 ms.
- Figure 7: Fill patterns for a C shaped die with different gates at time 3.00 ms.
- Figure 8: Filling of the circular die with a solid core using μ= 0.001 kg/ms
- Figure 9: Filling of the S shaped die using μ= 0.001 kg/ms
- Figure 10: (a) Original input viscosity data versus (b) modified viscosity temperature relation used in the SPH simulations with a finite value of μ below T₀ representing solidified metal.
- Figure 11: Temperature distribution in the liquid metal during the filling of an isothermal C shaped die for μs/μl=100. Light grey corresponds to hot metal above the liquidus temperature and dark grey to colder metal.
- Figure 12: Viscosity distribution in the liquid metal during the filling of an isothermal C shaped die for μs/μl=100. Dark grey corresponds to low viscosity and shows liquid metal while light grey corresponds to high viscosity and represents solid metal.
- Figure 13: Viscosity distribution when the conduction in the mould is also simulated.
- Figure 14: Viscosity distribution when the conduction in the mould is also simulated and latent heat is included.
- Figure 15: Geometry of the generic 3D HPDC component.
- Figure 16: Isothermal SPH simulation of the filling of the generic component.
- Figure 17: Two perspective views of the final filled die at 14 ms.
- Figure 18: Two internal views of the filling of the generic component.
- Figure 19: Geometry of the piston head, runner and venting system.
- Figure 20: Oblique upper view of the filling of the piston head.
- Figure 21: Side view of the filling of the piston head.
7. 결론:
SPH(Smoothed Particle Hydrodynamics)를 사용한 고압 다이캐스팅 공정 모델링의 여러 측면이 기술되었습니다. 매우 단순한 형상의 2차원 등온 모델링은 충전이 균일한 전면 충전이 아님을 보여주었습니다. 충전 순서는 금형 형상에 크게 의존하며, 얇은 벽 단면의 많은 부분을 채우는 데 역충전이 기여하는 것으로 밝혀졌습니다. 모서리에서의 유동 분리는 기공 형성의 중요한 기회를 제공합니다. 수치 시뮬레이션을 통해 게이트 및 러너 형상 변경이 충전 패턴에 미치는 영향을 쉽게 검토할 수 있는 능력이 입증되었습니다.
온도 의존적 점성을 통한 열전달 및 응고 포함이 기술되었습니다. 금형 벽 열경계 조건 선택의 중요성은 특히 중요하며, 이는 냉각 속도 및 따라서 응고 속도를 제한하므로 금형으로의 결합 전도 모델링의 명확한 필요성이 발견되었습니다. 잠열 방출이 예측된 응고량을 줄이고 머시존(고액공존영역)을 좁히며 자유 흐름에서 고체 금속 슬러리가 형성되도록 하는 역할이 검토되었습니다.
마지막으로, SPH 패키지를 사용하여 두 개의 실제 복잡한 형상 부품을 3차원으로 모델링하는 것이 시연되었습니다. 각 경우에서 유동 분리 및 자유 표면의 상당한 파편화는 큰 과도기적 기공 형성을 초래했습니다. 이러한 더 복잡한 부품에 대해 금형 충전 순서의 중요성이 확인되었습니다.
8. 참고문헌:
- Cleary, P.W. (1998a). SPH Technical Note #29, CSIRO Division of Mathematical and Information Sciences, Technical Report CMIS 1998/166.
- Cleary, P.W. (1998b). Applied Mathematical Modelling, 22, 981–993.
- Cleary, P.W., Ha, J., & Ahuja, V. (2000). Int. J. Cast Metals Res, 12, 335–355.
- Cleary, P.W., Ha, J., Mooney, J., & Ahuja, V. (1998). in Proc. Proc. 13th Australasian Fluid Mechanics Conference, Melbourne, Australia, 679–682.
- Cleary, P.W. & Monaghan, J. J. (1999). J. Comp. Phys., 148, 227–264.
- Cleary, P.W., Sawley, M., and Ha, J. (2001). in Proc. 5th International Workshop on Bifurcation and Localisation in Soils and Rock, Balkema.
- Gartling, D.K. (1980). in Morgan, K., Taylor, C. and Brebbia, C.A. (Eds), Computer Methods in Fluids, Pentech, London, 257-284.
- Ha, J., Cleary, P.W., Alguine, V. and Nguyen, T. (1999). in Proc. 2nd Int. Conf. on CFD in Minerals & Process Industries, Melbourne, Australia, 423-428.
- Ha, J. and Cleary, P.W. (2000). SPH Technical Note #28, CSIRO Division of Mathematical and Information Sciences, Technical Report CMIS 2000/105.
- Ha, J. and Cleary, P.W. (2000). Int. J. Cast Metals Res, 12, 409–418.
- Ha, J., Schuhmann, R., Alguine, V., Cleary, P.W. and Nguyen, T. (2000). in Proc. Modeling of Casting, Welding and Advanced Solidification Processes IX, 151–158.
- Hirt, C.W. and Nichols, B.D. (1981). J. Comp. Phys., 39, 201–225.
- Hwang, W-S, and Stoehr, R.A. (1988). Metals Handbook, Casting ASM International, 15, 867-876.
- Jai, L.R., Xiong, S.M. and Lui, B.C. (1998) in Proc. Modeling of Casting, Welding and Advanced Solidification Processes IX, Aachen, Germany, 303–310.
- Kothe, D., Brackbill, J.U. and Choi, C.K. (1990). Physics of Fluids B, 2, 1898–1906.
- Kothe, D., Juric, D., Lam, K. and Lally, B. (1998). in Proc. Modeling of Casting, Welding and Advanced Solidification Processes VIII, San Diego, California, 17–28.
- Lee, Y.C., Hwang, H.Y. and Choi, J.K. (2000). in Proc. Modeling of Casting, Welding and Advanced Solidification Processes IX, Aachen, Germany, 349–356.
- Monaghan, J. J. (1992). Ann. Rev. Astron. Astrophys., 30, 543.
- Monaghan, J. J. (1994). J. Comp. Phys., 110, 399–406.
- Morris, J.P. (2000). Int. J. Numer. Methods Fluids, 33, 333-353.
- Scheppe, F., Sahm, P.R., Hermann, W., Paul, U. and Preuhs, J. (2000). in Proc. Modeling of Casting, Welding and Advanced Solidification Processes IX, Aachen, Germany, 207–214.
- Schmid, M., and Klein F. (1995). in Proc. NADCA 18. International Die Casting Congress and Exposition, October 2-5, 1995, Indianapolis, Indiana, Paper No.I-T95-034, 93-99.
- Schmid, M. (1998). (Private Communication),
- Schmid, M. and Klein, F. (1998). in Proc. Modeling of Casting, Welding and Advanced Solidification Processes VIII, San Diego, California, 1131–1136.
- Schneider, M.C., Beckermann, C., Lipinski, D.M. and Schaefer, W. (2000). in Proc. Modeling of Casting, Welding and Advanced Solidification Processes IX, Aachen, Germany, 257–264.
- Thomas (1965). J. Colloid Science, 20, 267–277.
- Voller, V.R. and Prakash, C. (1987). Int. J. Heat Mass Transfer, 30, 1709–1719.
- Welch, J.E. and Harlow, F.H. (1966). Physics of Fluids, 9, 842-851.
- Xu, Z.A. (2000). in Proc. Modeling of Casting, Welding and Advanced Solidification Processes IX, Aachen, Germany, 312–319.
9. 저작권:
- 이 자료는 "Paul W. Cleary and Joseph Ha"의 논문입니다. "[Modelling the High Pressure Die Casting Process Using SPH]"에 기반합니다.
- 논문 출처: https://www.researchgate.net/publication/246854585
이 자료는 위 논문을 바탕으로 요약되었으며, 상업적 목적의 무단 사용을 금합니다.
Copyright © 2025 CASTMAN. All rights reserved.