1. 개요:
- 제목: 자동차 경량화를 위한 재료 (Materials for Automotive Lightweighting)
- 저자: Alan Taub, Emmanuel De Moor, Alan Luo, David K. Matlock, John G. Speer, Uday Vaidya
- 발행 연도: 2019년
- 발행 학술지/학회: Annual Review of Materials Research
- Keywords:
- advanced high-strength steel (고강도강)
- aluminum (알루미늄)
- magnesium (마그네슘)
- polymer composites (고분자 복합재료)
- lightweighting (경량화)
- multimaterial joining (이종재료 접합)
2. 연구 배경:
- 연구 주제의 사회적/학문적 맥락:
- 차량 무게 감소는 연비 향상에 크게 기여합니다.
- 기존 차량 제작의 기본 재료인 저탄소강 및 주철은 더 높은 비강도 및 비강성을 가진 재료로 대체되고 있습니다.
- 주요 과제는 이러한 새로운 경량 재료로 구조물을 제조하는 비용을 줄이는 것입니다.
- 무게 감소를 극대화하려면 다양한 형태의 이종 재료를 활용하는 최적화된 설계가 필요합니다.
- 혼합 재료의 사용은 접합 및 갈바닉 부식 방지에 추가적인 어려움을 제시합니다.
- 기존 연구의 한계점:
- 기존의 경량 재료 제조 공정은 특정 응용 분야의 비용 요구 사항을 충족해야 합니다.
- 이종 재료 구조에서 접합 및 갈바닉 부식 방지는 추가적인 과제입니다.
- 연구의 필요성:
- 자동차 경량화를 위한 고강도강, 알루미늄, 마그네슘 및 고분자 복합재료와 같은 재료 시스템의 발전을 검토합니다.
- 알루미늄과 마그네슘의 사용 증가를 가능하게 하는 제조 기술을 논의합니다.
- 경량 재료의 광범위한 채택을 위한 재료 특성 개선 및 비용 절감 방안을 모색합니다.
3. 연구 목적 및 연구 질문:
- 연구 목적:
- 자동차 경량화를 위한 재료 및 제조 기술의 최신 기술 동향을 검토하고, 특히 고강도강, 알루미늄, 마그네슘 및 고분자 복합재료에 중점을 둡니다.
- 핵심 연구 질문:
- 자동차 경량화를 위해 철강 합금, 특히 고강도강 및 연성 주철 분야에서 최근 발전은 무엇입니까?
- 자동차 구조에서 알루미늄과 마그네슘의 사용 증가를 가능하게 하는 제조 기술은 무엇이며, 최근 합금 개발은 무엇입니까?
- 자동차 경량화를 위한 고분자 복합재료의 현재 응용 분야와 발전은 무엇이며, 재료 개발 및 가공 기술을 포함하여 설명하십시오.
- 자동차 경량 구조를 위한 이종 재료 접합의 과제와 발전은 무엇입니까?
- 연구 가설: (논문에 명시적으로 가설로 제시되지는 않았지만, 함축적으로 내포됨)
- 재료 과학, 제조 공정 및 설계 최적화의 발전은 성능 및 안전성, 비용 효율성을 유지하면서 상당한 자동차 경량화를 달성하고 연비를 향상시키는 데 매우 중요합니다.
4. 연구 방법론:
- 연구 설계: 자동차 경량화 재료 및 제조 분야의 기존 문헌 및 연구 결과를 요약하는 리뷰 논문입니다.
- 데이터 수집 방법: 자동차 재료, 제조 및 경량화 기술과 관련된 출판된 연구 논문, 산업 보고서 및 기술 간행물에 대한 문헌 검토를 수행했습니다.
- 분석 방법: 검토된 문헌에서 얻은 정보를 질적으로 종합하고 요약하여, 해당 분야의 주요 동향, 발전, 과제 및 미래 방향을 파악하는 데 중점을 두었습니다.
- 연구 대상 및 범위: 자동차의 차체, 섀시 및 내부 부품에 사용되는 재료에 중점을 둡니다. 주로 고강도강, 알루미늄, 마그네슘 및 고분자 복합재료를 검토합니다. 범위는 경량화 재료 고려 사항을 넘어선 파워트레인 전동화 측면은 제외합니다.
5. 주요 연구 결과:
- 핵심 연구 결과:
- 고강도강 (AHSS) 및 연성 주철:
- 향상된 강도 및 성형성을 위해 복잡한 미세 구조 (마르텐사이트, 베이나이트, 초미세 결정립 페라이트, 잔류 오스테나이트) 를 가진 3세대 AHSS 개발.
- 3세대 AHSS를 위한 새로운 가공 경로로서 Q&P (Quenching and Partitioning, 담금질 및 분배) 및 TBF (TRIP-aided bainitic ferrite, TRIP 보조 베이나이트 페라이트) 강 개발.
- 높은 강도 대 밀도 비율과 비용 효율성을 제공하는 박벽 오스템퍼드 연성 주철 (ADI) 주조.
- 알루미늄 및 마그네슘:
- 연비 요구 및 제조 혁신에 의해 알루미늄 및 마그네슘 사용 증가.
- 알루미늄 및 마그네슘 합금의 성형성을 향상시키기 위한 열간 성형과 같은 판재 성형 기술.
- 최소 기공률과 향상된 연성을 가진 부품을 생산하기 위한 알루미늄 및 마그네슘용 고진공 다이캐스팅 공정 (SVDC).
- CALPHAD 접근 방식을 사용한 고온 마그네슘 합금 (예: AE44) 개발.
- 고분자 복합재료:
- 높은 강도 대 중량비 및 설계 유연성으로 인해 경량화를 위한 핵심 가능 요소로서 섬유 강화 고분자 복합재료.
- 차체 외장, 내장, 안전, 섀시, 파워트레인, 연료 시스템 및 엔진 부품의 다양한 응용 분야.
- 비용 효율적인 복합재료 제조를 위한 탄소 섬유 기술 및 가공 방법 (HP-RTM, 습식 압축, IOM, 프리프레그 스탬핑, 압출-압축) 의 발전.
- 비용 절감 및 지속 가능성 향상을 위해 중요성이 커지고 있는 고분자 복합재료 재활용 기술.
- 이종 재료 접합:
- 자동차 설계에서 다양한 경량 재료를 통합하는 데 필수적인 이종 재료 접합.
- 견고한 설계 도구, 신뢰할 수 있는 시험 방법 및 비용 효율적인 접합 기술의 필요성.
- 접합 접근 방식의 규모 확장, 가속 노화 시험 개발 및 제3자 데이터 평가에 중점을 둔 연구.
- 고강도강 (AHSS) 및 연성 주철:
- 통계적/정성적 분석 결과:
- 중량 감소 효과: 경차: 중량 감소 가치 "$4.50/kg". 대형 트럭: 중량 감소 가치 "$5-11/kg 건식 밴 전용 경로" 및 "$13-24/kg 벌크 운반선" (표 1).
- 재료 대체 효과: 경강/주철 대비 다양한 경량 재료의 질량 감소 및 상대적 부품당 비용 (표 2). 예를 들어, 마그네슘: 질량 감소 "60-75%", 상대적 부품당 비용 "1.5 ~ 2.5". 탄소 섬유 복합재료: 질량 감소 "50-60%", 상대적 부품당 비용 "2 ~ 10+".
- AHSS 연신율: 그림 5는 기존 강종 및 AHSS 강종의 인장 강도 및 총 연신율 조합의 속성 맵을 보여줍니다. 3세대 AHSS는 이 맵에서 특정 대역 내의 속성을 목표로 합니다.
- Q&P 강 응력-변형률 곡선: 그림 6과 그림 8은 다양한 가공 조건에서 Q&P 강의 응력-변형률 곡선을 보여주며, 인장 특성의 변화를 나타냅니다.
- 중간 Mn 강에서 오스테나이트 변태: 그림 10은 다양한 어닐링 온도에서 중간 Mn 강의 변형률 및 해당 응력-변형률 곡선에 따른 오스테나이트에서 마르텐사이트로의 변태 진화를 보여줍니다.
- 피로 수명 및 개재물 함량: 그림 11은 강철의 개재물 함량과 피로 응력/수명 간의 관계를 보여줍니다. 개선된 제강 기술은 1980년 이후 "피로 수명이 2배 증가"하는 결과를 가져왔습니다.
- 연성 주철의 구상 흑연 밀도: 그림 12는 박벽 대 후벽 연성 주철 주물의 구상 흑연 밀도를 비교합니다.
- 탄소 섬유 복합재료 특성: 표 3은 직물 탄소 섬유 (TCF) 에폭시 복합재료의 대표적인 특성을 보여줍니다. 예: 인장 강도: "548 MPa (79.48 ksi)", 인장 탄성률: "84 GPa (12.18 Msi)".
- 오버몰딩 복합재료의 하중 지지 용량: 그림 24는 PA6-C LFT와 비교하여 오버몰딩된 PA6-C LFT의 "하중 지지 및 변형률 용량이 275% 향상"되었음을 보여줍니다.
- 데이터 해석:
- 재료 대체 및 최적화된 설계는 자동차 경량화를 위한 핵심 전략입니다.
- 첨단 재료 및 제조 공정은 더 가볍고, 더 강하고, 더 비용 효율적인 자동차 구조에 대한 요구를 충족하기 위해 지속적으로 발전하고 있습니다.
- 고분자 복합재료 및 이종 재료 설계는 미래 경량화 노력에 점점 더 중요해지고 있습니다.
- Figure Name List:
- 그림 1: 1975-2016년 모델 연도의 조정된 연비, 무게 및 마력 변화.
- 그림 2: (a) 기존 성형 기술 대비 저용량 생산에서 점진적 성형 및 비용 효율성. (b) 다양한 성형 공정에 대한 부품 복잡성과 생산량의 균형.
- 그림 3: 이종 재료 경량 차량 Mach-II 차체 백색 차체 재료 분포.
- 그림 4: 미국 자동차 금속 시장 역사 및 전망.
- 그림 5: 다양한 종류의 기존 강종 및 AHSS 강종에 대한 인장 강도 및 총 연신율 조합의 속성 맵.
- 그림 6: 300°C ~ 500°C 범위의 다양한 온도에서 200초 동안 오스템퍼링된 0.2 wt% C–1.5 wt% Mn–1.0 wt% Si-0.5 wt% Al 강철의 공학적 응력-변형률 곡선.
- 그림 7: 완전 오스테나이트 미세 구조로 시작하는 2단계 담금질 및 분배 열처리 공정을 보여주는 개략도.
- 그림 8: 0.2 ~ 0.4 wt%의 다양한 탄소 함량을 가진 x wt% C-1.5 wt% Mn–1.6 wt% Si 강철에서 담금질 및 분배 처리 후, 400°C에서 10초 및 300초의 분배 시간 (Pt) 으로 수행된 공학적 응력-변형률 곡선.
- 그림 9: 40 vol% 오스테나이트를 생성하기 위해 620°C에서 24시간 동안 어닐링된 7 wt% Mn 강철에 대한 전자 후방 산란 회절 이미지 품질 맵.
- 그림 10: (a) 다양한 어닐링 온도에서 인장 변형에 따른 마르텐사이트로 변형된 오스테나이트 분율의 진화. (b) 0.1 wt% C–7.1 wt% Mn–0.1 wt% Si 샘플에 대한 해당 인장 응력-변형률 곡선.
- 그림 11: (a) 허용 가능한 피로 응력 및 (b) 베어링 피로 수명에 대한 개재물 함량의 영향.
- 그림 12: 단면 두께가 구상 흑연 수에 미치는 영향을 보여주는 에칭되지 않은 시편의 광학 현미경 사진.
- 그림 13: 주요 알루미늄 및 마그네슘 자동차 응용 분야의 타임라인.
- 그림 14: 성형 직후의 Corvette Z06용 수압 성형 알루미늄 레일.
- 그림 15: (a) Al-8 wt% Si-0.35 wt% Mg-0.6 wt% Fe-x% Mn에 대해 계산된 등압 단면도. (b) Al-Si-Mg-Fe-Mn 합금 시스템에서 β-Al5FeSi 금속간 화합물 상의 형성에 대한 Fe 및 Mn 함량의 영향.
- 그림 16: 합금 최적화 및 공정 시뮬레이션을 통한 박벽 알루미늄 및 마그네슘 다이캐스팅 달성.
- 그림 17: (a) 계산된 Mg-Al 상 다이어그램. (b) 실험적 Mg-Al-Ce 합금의 계산된 Mg-Al-Ce 액상선 투영 및 응고 경로.
- 그림 18: 차량 경량화를 위한 관련 제조 공정을 갖춘 고분자 및 고분자 복합재료에 대한 포괄적인 기회.
- 그림 19: 미국 및 캐나다 경차의 다양한 플라스틱 및 복합재료의 역사적 평균 재료 사용량.
- 그림 20: 미국/캐나다 경차에 사용되는 평균 플라스틱 및 고분자 복합재료.
- 그림 21: Oak Ridge 국립 연구소의 탄소 섬유 기술 시설에서 생산된 광폭 토우 직물 등급 탄소 섬유.
- 그림 22: (a) 고압 수지 이송 성형 (RTM). (b) 습식 압축 가공.
- 그림 23: 자동차 부품의 오버몰딩 단계.
- 그림 24: 탄소 PA6와 오버몰딩된 탄소 PA6의 비교.
- 그림 25: 장섬유 열가소성 압출-압축 성형 공정의 재료 단계.
- 그림 26: (a) 45초의 사이클 시간에서 성형된 시트 몰딩 컴파운드 (SMC) 시트백. (b) SMC 몰딩 플라크 및 오버몰딩된 SMC 플라크.
- 그림 27: 스탬핑/압축 성형하여 네트 셰이프에 가깝게 만들 수 있는 재활용 탄소 섬유 폴리아미드 6 (PA6) 매트의 예.
- 그림 28: Oak Ridge 국립 연구소의 제조 시연 시설에서 BAAM (대면적 적층 제조) 프린터로 제작된 Strati 자동차의 육각형 기하학적 단면.
- 그림 29: (a) 프리프레그 스탬핑, 사출 성형, 압축 및 적층 제조를 위한 포괄적인 기능을 갖춘 IACMI Purdue University의 모델링 및 시뮬레이션 허브. (b) 아크릴로니트릴 부타디엔 스티렌 재료의 층별 적층 압출 증착에서 개발된 국부 열 응력 모델.
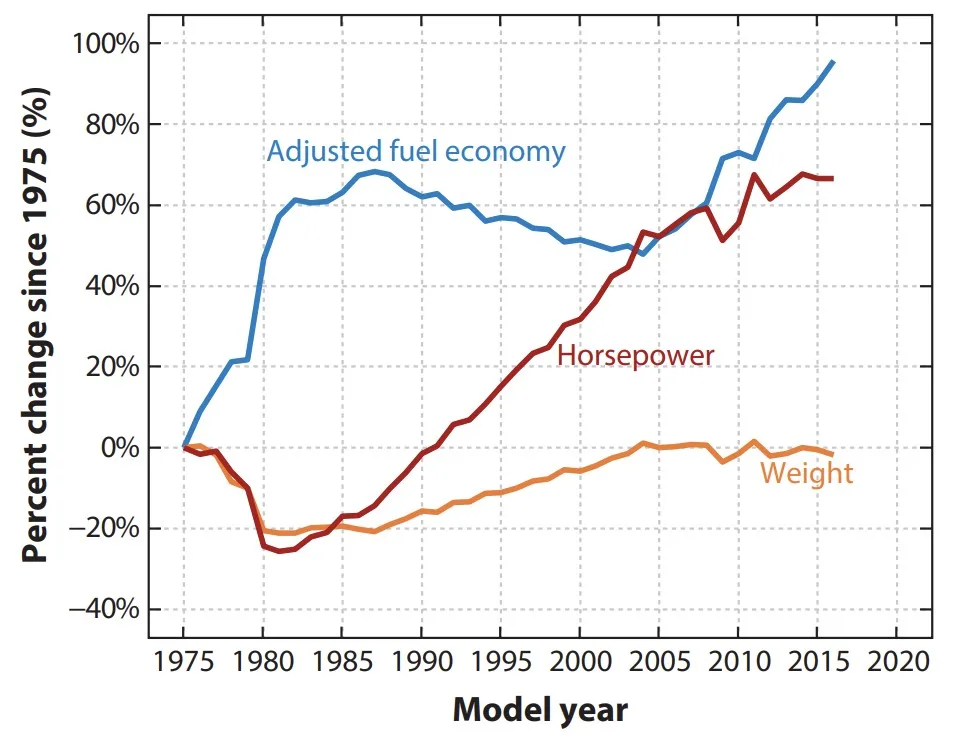
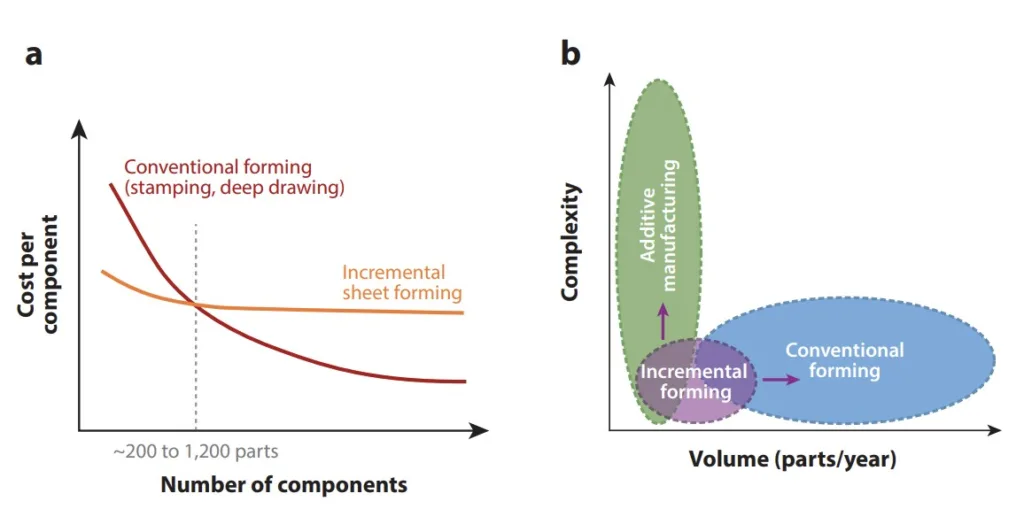
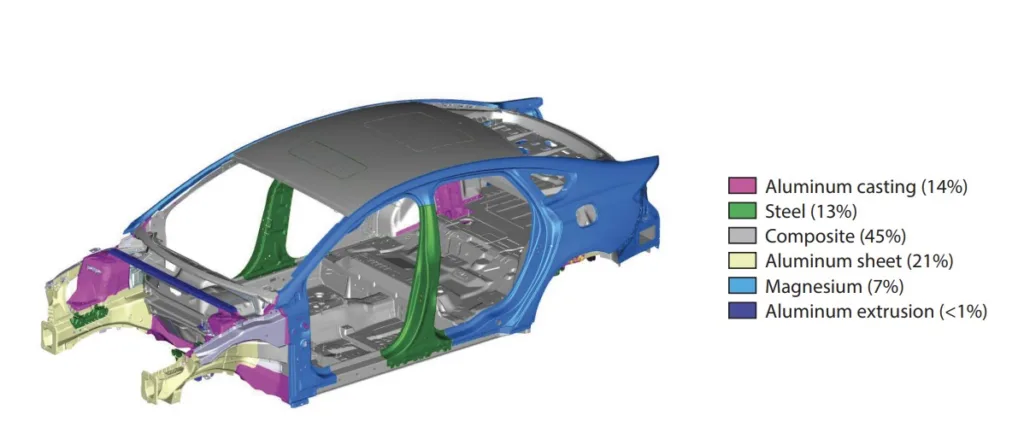
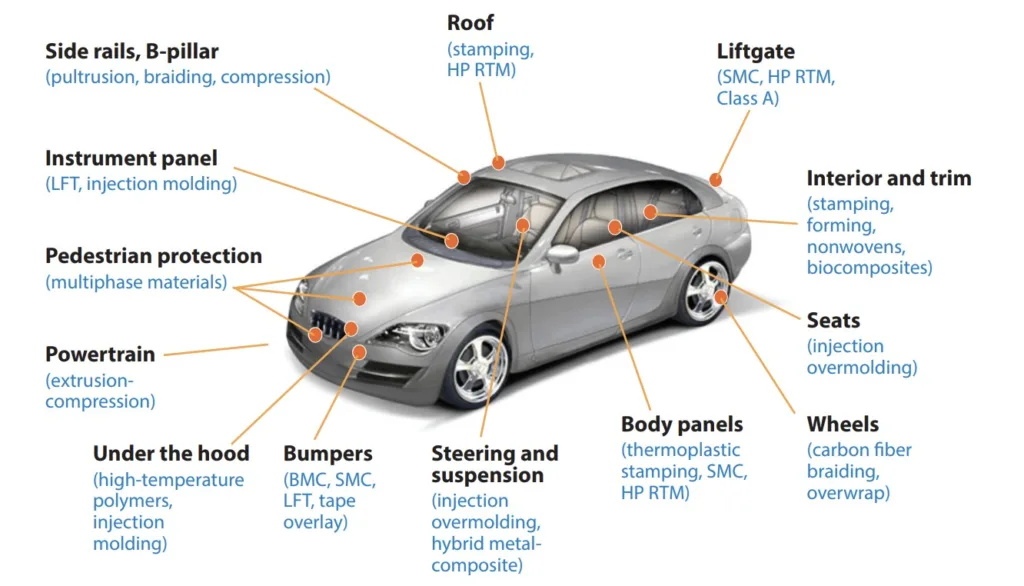
6. 결론 및 논의:
- 주요 결과 요약:
- 자동차 산업은 AHSS, 알루미늄, 마그네슘 및 고분자 복합재료와 같은 첨단 재료를 채택하여 경량화로 적극적으로 전환하고 있습니다.
- 최적화된 설계 및 첨단 제조 기술은 비용 효율적인 경량 재료 구현에 매우 중요합니다.
- 성능을 향상시키고 무게를 줄이기 위해 각 재료 범주에 대한 새로운 합금 및 가공 경로 개발에 상당한 진전이 있었습니다.
- 이종 재료 설계 및 접합 기술은 무게 감소를 극대화하고 원하는 성능 특성을 달성하는 데 필수적입니다.
- 연구의 학술적 의의:
- 자동차 경량화를 위한 재료 및 제조 분야의 최신 발전에 대한 포괄적인 개요를 제공합니다.
- 설계 최적화 및 재료 선택에 있어 ICME (Integrated Computational Materials Engineering, 통합 전산 재료 공학) 의 중요성을 강조합니다.
- 이종 재료 설계로의 전환과 관련된 과제와 기회를 강조합니다.
- 실무적 시사점:
- 자동차 엔지니어 및 재료 과학자가 경량 재료 및 제조 공정을 선택하고 구현하는 데 유용한 통찰력을 제공합니다.
- 자동차 경량화의 추가 발전에 필요한 주요 연구 분야 및 기술 발전을 식별합니다.
- 새로운 경량화 기술 채택에 있어 비용 효율성 및 재활용성의 중요성을 강조합니다.
- 연구의 한계점:
- 본 리뷰는 주로 재료 측면과 제조 기술에 초점을 맞추고 있으며, 전체 수명 주기 분석 또는 상세한 비용 모델링과 같은 더 넓은 시스템 수준의 영향에 대한 논의는 제한적입니다.
- 범위는 차체, 섀시 및 내부 부품으로 제한되며, 재료 고려 사항을 넘어선 파워트레인 전동화가 경량화에 미치는 영향에 대한 심층 분석은 제외합니다.
7. 향후 후속 연구:
- 후속 연구 방향:
- 저비용 탄소 섬유 및 효율적인 복합재료 제조 공정의 추가 개발.
- 이종 재료 접합 기술 및 갈바닉 부식 방지 방법의 발전.
- 가속화된 재료 설계 및 공정 최적화를 위한 ICME 도구의 개발 및 개선.
- 지속 가능성을 향상시키기 위한 복합재료 재활용 기술 연구.
- 향상된 특성 및 비용 절감을 통해 AHSS, 알루미늄 및 마그네슘을 위한 새로운 합금 설계 및 가공 기술 탐구.
- 추가 탐구가 필요한 영역:
- 다양한 경량화 전략 및 재료 선택에 대한 기술 경제 분석.
- 복합재료 충돌 시뮬레이션 모델의 검증 및 견고한 설계 지침 개발.
- 이종 재료 접합부에 대한 표준화된 시험 방법 및 데이터베이스 개발.
- 경량화 전략과 차량 전동화 및 자율 주행 기술의 통합.
8. 참고문헌:
- US Natl. Res. Counc. 2003. Materials Research to Meet 21st Century Defense Needs.Washington, DC: Natl. Acad. Press
- Roeth M. 2015. Confidence report: lightweighting. Rep., North American Council for Freight Efficiency.
https://nacfe.org/technology/lightweighting-2/. Accessed Nov. 20, 2017 - Taub AI, Krajewski PE, Luo AA, Owens JN. 2007. The evolution of technology for materials processing
over the last 50 years: the automotive example. JOM 59(2):48–57 - Schutte C, Joost WJ. 2014. Lightweight materials for cars and trucks. https://www.energy.gov/eere/
vehicles/lightweight-materials-cars-and-trucks - Joost W. 2015.Energy, materials and vehicle weight reduction. Rep., US Dep. Energy. http://www.nist.gov/
mml/acmd/structural_materials/upload/Joost-W-DOE-VTP-NIST-ASP-AHSS-WorkshopR03.pdf - Picker L. 2017. Vehicle weight and automotive fatalities. Digest, NBER. http://www.nber.org/digest/
nov11/w17170.html. Accessed Dec. 3, 2017 - Plumer B. 2014. Cars in the US are more fuel-efficient than ever. Here are 5 reasons why. Vox,
Sept. 4. https://www.vox.com/2014/9/4/6107203/cars-in-the-us-are-more-fuel-efficient-thanever-here-are-5-reasons. Accessed Dec. 3, 2017 - US Envir. Prot. Agency (EPA). 2015. Light-duty automotive technology, carbon dioxide emissions, and fuel economy trends: 1975 through 2015. Rep., US EPA
- Baron JS, Modi S. 2016. Assessing the fleet-wide material technology and costs to lightweight vehicles. Rep.,
Cent. Automot. Res. - Isenstadt A, German J, Bubna P, Wiseman M, Venkatakrishnan U, et al. 2016. Lightweighting technology development and trends in U.S. passenger vehicles. Work. Pap., Int. Counc. Clean Transp.
- US EPA. 2016. Light-duty vehicle CO2 and fuel economy trends. Rep. EPA-420-S-16-001, US EPA
- Bullis K. 2013. Automakers shed the pounds to meet fuel efficiency standards. MIT Technol. Rev., Feb. 20
- Kunkel GA, Hovanski Y. 2016. From the lab to your driveway: aluminum tailor-welded blanks. Weld. J.
95(8):36–39 - Joost WJ, Krajewski PE. 2017. Towards magnesium alloys for high-volume automotive applications. Scr. Mater. 128:107–12
- Winters J. 2014. Light vehicles’ lightweight future. Mech. Eng. CIME, Aug. 1. Accessed Nov. 28, 2017
- Hartfield-Wünsch SE, Hall JN. 2012. Manufacturing challenges for aluminum sheet in the automotive
industry. In ICAA13, ed. H Weiland, AD Rollett, WA Cassada, pp. 885–90. Cham, Switz.: Springer - Xia L. 2016. Multiscale Structural Topology Optimization. London: Elsevier
- Fiedler K, Rolfe BF, De Souza T. 2017. Integrated shape and topology optimization: applications in
automotive design and manufacturing. SAE Int. J. Mater. Manuf. 10(3):385–94 - Keough JR, Hayrynen KL. 2000. Automotive applications of austempered ductile iron (ADI): a critical
review. SAE Trans. 109:344–54 - Horstemeyer MF. 2012. Integrated Computational Materials Engineering (ICME) for Metals: Using Multiscale Modeling to Invigorate Engineering Design with Science. Hoboken, NJ: Wiley
- Pollock DGB, Tresa M, Allison JE. 2008. Integrated Computational Materials Engineering: A Transformational Discipline for Improved Competitiveness and National Security. Washington, DC: Natl. Acad. Press
- Allison J, Li M, Wolverton C, Su XM. 2006. Virtual aluminum castings: an industrial application of
ICME. JOM 58(11):28–35 - Sames WJ, List FA, Pannala S, Dehoff RR, Babu SS. 2016. The metallurgy and processing science of
metal additive manufacturing. Int. Mater. Rev. 61(5):315–60 - Daehn G. 2017. Metamorphic manufacturing. Abstract, LIFT. https://lift.technology/pillar/novelagile-processing/. Accessed Nov. 30, 2017
- Allwood JM, Utsunomiya H. 2006. A survey of flexible forming processes in Japan. Int. J. Mach. Tools
Manuf. 46(15):1939–60 - Allwood J, Houghton N, Jackson K. 2005. The design of an incremental sheet forming machine. Adv.
Mater. Res. 6–8:471–78 - Cao J, Huang Y, Reddy NV, Malhotra R, Wang Y. 2008. Incremental sheet metal forming: advances
and challenges. In Proceedings of International Conference on Technology of Plasticity (ICTP 2008). Gyeongju,
Korea: Korean Soc. Technol. Plastic. - Taub AI, Babu SS. 2018. Opportunities and challenges for introducing new lightweight metals in transportation. Int. J. Powder Metall. 54(2):27–33
- Taub AI, Luo AA. 2015. Advanced lightweight materials and manufacturing processes for automotive
applications. MRS Bull. 40(12):1045–54 - Skszek T, Conklin J, Zaluzec M,Wagner D. 2014. Multi-material lightweight vehicles: Mach-II design. Rep. for US Dep. Energy. https://energy.gov/sites/prod/files/2014/07/f17/lm088_skszek_2014_o.pdf.
Accessed Dec. 1, 2017 - Skszek T. 2015. Demonstration project for a multi-material lightweight prototype vehicle as part of the clean energy dialogue with Canada. Final Rep. for US Dep. Energy (award DE-EE0005574)
- Henriksson F. 2016. An outlook on multi material body solutions in the automotive industry: possibilities and
manufacturing challenges. Tech. Pap. 2016-01-1332, SAE - US Dep. Energy. 2010. 2010 annual progress report: lightweight material. Rep., US Dep.
Energy. https://www.energy.gov/sites/prod/files/2014/03/f8/2010_lightweighting_materials.pdf.
Accessed Sept. 1, 2015 - US EPA. 2012. Light-duty vehicle mass reduction and cost analysis—midsize crossover utility vehicle. Rep. EPA-420-R-12-026, US EPA. https://nepis.epa.gov/Exe/ZyPDF.cgi/P100EWVL.PDF?Dockey=
P100EWVL.PDF - Gehm R. 2016. Multi-material structures move mpg upward. Automot. Eng. 2016(3):18–21
- Singh H. 2012. Mass reduction for light-duty vehicles for model years 2017–2025. Rep. DOT HS 811 666,US Dep. Transp.
- US EPA. 2015. Mass reduction and cost analysis: light duty pickup model years 2020–2025. Rep. EPA-420-R15-006, US EPA
- Vasalash GS. 2017. Light vehicles and how they got that way. Automotive Design and Production, Oct. 11.
https://www.adandp.media/articles/light-vehicles-and-how-they-got-that-way - Monaghan M. 2012. Light and mighty. Automot. Eng. 2012(7):20–24
- Steven A. 2015. Mixing metals. Automot. Eng. 2015:27–29
- Wagner DA, Zaluzec MJ. 2015. Mixed materials drive lightweight vehicle design. Adv. Mater. Process.
2015(3):18–23 - Meschut G, Janzen V, Olfermann T. 2014. Innovative and highly productive joining technologies for
multi-material lightweight car body structures. J. Mater. Eng. Perform. 23(5):1515–23 - Ghosh D, Pancholi L, Sathaye A. 2014. Forming a strong bond. Automot. Eng. 2014:24–29
- Gould JE. 2012. Joining aluminum sheet in the automotive industry—a 30 year history. Weld. J. 91:23–34
- WorldAutoSteel. 2017. Advanced high-strength steels application guidelines version 6.0. https://www.
worldautosteel.org/projects/advanced-high-strength-steel-application-guidelines/. Accessed
Oct. 2018 - De Moor E, Gibbs PJ, Speer JG, Matlock DK, Schroth JG. 2010. Strategies for third-generation advanced high-strength steel development. AIST Trans. 7(3):133–44
- Matlock DK, Speer JG. 2009. Third generation of AHSS: microstructure design concepts. In Microstructure and Texture in Steels and Other Materials, ed. A Haldar, S Suwas, D Bhattacharjee, pp. 185–205. New York: Springer
- Matlock DK, Speer JG. 2006. Design considerations for the next generation of advanced high strength steels. In Proceedings of the Third International Conference on Advanced Structural Steels, ed. HC Lee, pp. 774–81. Seoul, Korea: Korean Institute of Metals and Materials
- Olson GB. 1984. Transformation plasticity and the stability of plastic flow. In Deformation, Processing and Structure, ed. G Krauss, pp. 391–424. Materials Park, OH: ASM
- Matlock DK, Speer JG, De Moor E, Gibbs PJ. 2011. TRIP steels—historical perspectives and recent
developments. In Proceedings of the 1st International Conference on High Manganese Steels, HMnS2011.
Seoul, Korea: Yonsei Univ. Press - De Cooman BC. 2004. Structure-properties relationship in TRIP steels containing carbide-free bainite.
Curr. Opin. Solid State Mater. Sci. 8(3–4):285–303 - Sugimoto K, Murata M, Song SM. 2010. Formability of A1-Nb bearing ultra high-strength TRIP-aided
sheet steels with bainite ferrite and/or martensite matrix. ISIJ Int. 50(1):162–68 - Rana R, De Moor E, Speer JG, Matlock DK. 2018. On the importance of adiabatic heating on deformation behavior of medium-manganese sheet steels. JOM 70(5):706–13
- Lee S, De Cooman BC. 2014. Tensile behavior of intercritically annealed 10 pct Mn multi-phase steel.
Metall. Mater. Trans. A 45(2):709–16 - Merwin MJ. 2007. Low-carbon manganese TRIP steels. Mater. Sci. Forum 539–543:4327–32
- Merwin MJ. 2007. Hot- and cold-rolled low-carbon manganese TRIPS steels. Tech. Pap. 2007-01-0336, SAE
- Bhadeshia HKDH. 2010. Nanostructured bainite. Proc. R. Soc. A 466(2113):3–18
- Speer JG, De Moor E, Findley KO, Matlock DK, De Cooman BC, Edmonds DV. 2011. Analysis of
microstructure evolution in quenching and partitioning automotive sheet steel. Metall. Mater. Trans. A 42(12):3591–601 - Wang L, Speer JG. 2013. Quenching and partitioning steel heat treatment. In ASM Handbook, Volume 4A: Steel Heat Treating Fundamentals and Processes, ed. GE Dossett, J Totten, pp. 317–26. Materials Park, OH:ASM Int.
- Sugimoto K, Iida T, Sakaguchi J, Kashima T. 2000. Retained austenite characteristics and tensile properties in a TRIP type bainitic sheet steel. ISIJ Int. 40(9):902–8
- Sugimoto K, Tsunezawa M, Hojo T, Ikeda S. 2004. Ductility of 0.1-0.6C-1.5Si-1.5Mn ultra highstrength TRIP-aided sheet steels with bainitic ferrite matrix. ISIJ Int. 44(9):1608–14
- Speer JG, Matlock DK, De Cooman BC, Schroth JG. 2003. Carbon partitioning into austenite after
martensite transformation. Acta Mater. 51(9):2611–22 - Matlock DK, Bräutigam VE, Speer JG. 2003. Application of the quenching and partitioning (Q&P)
process to a medium-carbon, high-Si microalloyed bar steel. Mater. Sci. Forum 426–432(1):1089–94 - Pierce DT, Coughlin DR, Williamson DL, Clarke KD, Clarke AJ, et al. 2015. Characterization of transition carbides in quench and partitioned steel microstructures by Mössbauer spectroscopy and complementary techniques. Acta Mater. 90:417–30
- Speer JG, Striecher AM, Matlock DK, Rizzo F, Krauss G. 2003. Quenching and partitioning a fundamentally new process to create high strength TRIP sheet microstructures. In Austenite Deformation and
Decomposition, ed. EB Damm, MJ Merwin, pp. 502–22. Warrendale, PA: ISS/TMS - Kahkonen MJ, De Moor E, Speer JG, Thomas GA. 2015. Carbon and manganese effects on quenching
and partitioning response of CMnSi-steels. SAE Int. J. Mater. Manuf. 8(2):419–24 - Wang L, Zhong Y, Feng W, Jin X, Speer JG. 2013. Industrial application of Q&P sheet steels. In Proceedings of the International Symposium on New Developments in Advanced High-Strength Steels, ed. E De Moor, HJ Jun, JG Speer, MJ Merwin, pp. 141–51. Warrendale, PA: AIST
- Gibbs PJ, De Moor E, Merwin MJ, Clausen N, Speer JG, Matlock DK. 2011. Austenite stability
effects on tensile behavior of manganese-enriched-austenite transformation-induced plasticity steel.
Metall. Mater. Trans. A 42(12):3691–702 - De Moor E, Matlock DK, Speer JG, Merwin MJ. 2011. Austenite stabilization through manganese enrichment. Scr. Mater. 64:185–88
- Zhang Y, Wang L, Findley KO, Speer JG. 2017. Influence of temperature and grain size on austenite
stability in medium manganese steels. Metall. Mater. Trans. A 48:2140–49 - Rana R, Lahaye C, Ray RK. 2014. Overview of lightweight ferrous materials: strategies and promises.
JOM 66(9):1734–46 - Ghanbari ZN, Speer JG. 2016. Elevated- and room-temperature mechanical behaviour of Zn-coated
steel sheet for hot stamping. AST Trans. 13(4):170–77 - Matlock DK, Speer JG. 2009. Microalloying concepts and application in long products. Mater. Sci. Technol. 25:1118–25
- Thompson RE, Matlock DK, Speer JG. 2007. The fatigue performance of high temperature vacuum
carburized Nb modified 8620 steel. SAE Trans. J. Mater. Manuf. 116(5):392–407 - Darragh CV. 2002. Engineered gear steels: a review. Gear Technol. Nov.–Dec.:33–40
- Gynther D. 2018. UltrapremiumTM and endurance steels. Presented at Great Designs in Steel, Livonia, MI. https://www.autosteel.org/-/media/files/autosteel/great-designs-in-steel/gdis-2018/track2- - -gynther- - -timkensteel.ashx. Accessed July 2018
- Findley KO, Cryderman RL, Nissan AB, Matlock DK. 2013. The effects of inclusions on fatigue performance of steel alloys. AIST Trans. 10(6):234–44
- Jhaveri K, Lewis GM, Sullivan JL, Keoleian GA. 2018. Life cycle assessment of thin-wall ductile cast
iron for automotive lightweighting applications. Sustain. Mater. Technol. 15:1–8 - Labrecque C, Gagné M, Javaid A, Sahoo M. 2003. Production and properties of thin-wall ductile iron
castings. Int. J. Cast Met. Res. 16:313–17 - Borrajo JM, Martínez RA, Boeri RE, Sikora JA. 2002. Shape and count of free graphite particles in thin
wall ductile iron castings. ISIJ Int. 42(3):257–63 - Fras E, Górny M, Lopez H. 2014. Thin wall ductile iron castings as substitutes for aluminum alloy ´
castings. Arch. Metall. Mater. 59(2):459–65 - Stefanescu DM, Dix LP, Ruxanda RE, Corbitt-Coburn C, Piwonka TS. 2002. Tensile properties of
thin-wall ductile iron. AFS Trans. 2(178):1149–61 - Górny M, Tyrała E. 2013. Effect of cooling rate on microstructure and mechanical properties of thinwalled ductile iron castings. J. Mater. Eng. Perform. 22(1):300–5
- Krajewski P, Sachdev A, Luo A, Carsley J, Schroth J. 2009. Automotive aluminum and magnesium:
innovation and opportunities. Light Met. Age 67(5):6–13 - Healey JR. 2014. 2015 Ford F-150 makes radical jump to aluminum body. USA Today, Jan. 13. https://
www.usatoday.com/story/money/cars/2014/01/13/redesigned-2015-ford-f-series-pickup-f150-aluminum/4421041/ - Ducker Worldwide. 2017.Aluminum content in North American light vehicles 2016 to 2028: summary report. Rep. for DriveAluminum
- Krajewski PE, Schroth JG. 2007. Overview of quick plastic forming technology. Mater. Sci. Forum 3:551–52
- Carter JT, Krajewski PE, Verma R. 2008. The hot blow forming of AZ31 Mg sheet: formability assessment and application development. JOM 60:77
- Shehata F, Painter MJ, Pearce R. 1978. Warm forming of aluminium/magnesium alloy sheet. J. Mech.
Work. Technol. 2:279–90 - Ayres RA. 1977. Enhanced ductility in an aluminum–4 Pct magnesium alloy at elevated temperature.
Metall. Trans. A 8:487–92- Warmed-up aluminum could beat steel to the draw. Mater. Eng. 88:52–54
- Luo AK, Sachdev AA. 2007. Development of light metals automotive structural subsystems. In Proceedings of the Light Metals Technology Conference. Ottawa, Can.: Nat. Resour. Can.
- Luo AA, Fu PH, Yu YD, Jiang HY, Peng LM, et al. 2008. Vacuum-assisted high pressure die casting of
AZ91 magnesium alloy. North Am. Die Cast. Assoc. Trans. 2008:T08–83 - Brown Z, Szymanowski B, Musser M, Saha D, Seaver S. 2009. Development of super-vacuum die casting
process for magnesium alloys. North Am. Die Cast. Assoc. Trans. - Brown Z, Szymanowski B, Musser M, Saha D, Seaver S. 2007. Manufacturing of thin wall structural automotive components through high vacuum die casting technology. Presented at International Die Casting
Congress and Exposition, Houston, TX, May 15–18 - Casarotto F, Franke AJ, Franke R. 2012.High-pressure die cast (HPDC) aluminum alloys for automotive
applications. In Advanced Materials in Automotive Engineering, ed. J Rowe, pp. 109–49. Sawston, UK:
Woodhead - Apelian D. 2009. Aluminum Cast Alloys: Enabling Tools for Improved Performance. Wheeling, IL: N. Am.Die Cast. Assoc.
- Taylor JA. 2012. Iron-containing intermetallic phases in Al-Si based casting alloys. Proc. Mater. Sci. 1:19–33
- Dinnis CM, Taylor JA, Dahle AK. 2006. Interactions between iron, manganese, and the Al-Si eutectic
in hypoeutectic Al-Si alloys. Metall. Mater. Trans. A 37:3283–91 - Ceschini L, Boromei I, Morri A, Seifeddine S, Svensson IJ. 2009. Microstructure, tensile and fatigue
properties of the Al–10% Si–2% Cu alloy with different Fe and Mn content cast under controlled conditions. J. Mater. Proc. Technol. 209:5669–79 - Cinkilic E, Sun W, Klarner AD, Luo AA. 2015. Use of CALPHAD modeling in controlling microstructure of cast aluminum alloys. Pap. 15-044, Am. Foundry Soc.
- Klarner AD, et al. 2017. A new fluidity die for castability evaluation of high pressure die cast alloys.Trans.
North Am. Die Cast. Assoc. T17–101 - Luo AA. 2013. Application of computational thermodynamics and CALPHAD in magnesium alloy development. In Proc. 2nd World Congr. Integr. Comput. Mater. Eng., ed. M Li, C Campbell, K Thornton, E Holm, P Gumbsch, pp. 3–8. Warrendale, PA: TMS
- Am. Chem. Counc. 2018. Plastics and polymer composites in light vehicles. Rep., Am. Chem. Counc.
- Institute for Advanced Composites Manufacturing Innovation (IACMI). 2017. Phase two roadmap. Feb. http://www.iacmi.org
- Vaidya U. 2017. Advanced composite materials and manufacturing in vehicles, wind and compressed gas storage. Text. World, Mar. 21
- Cedric B. 2016. New developments for mass production of epoxy automotive composites. Presented at Global Automotive Lightweight Materials Conference, Detroit. Accessed Aug. 2018
- Gardiner G. 2015. HP-RTM on the rise. Compos. World, Apr. 14
- Gardiner G. 2016. Wet compression molding. Compos. World, Jan. 2
- Rocky Mt. Inst. 2013. Kickstarting the widespread adoption of automotive carbon fiber composites: key findings and next steps. Rep., Rocky Mt. Inst.
- Thattaiparthasarathy K, Pillay S, Bansal D, Ning H, Vaidya U. 2013. Processing and characterization
of continuous fibre tapes co-moulded with long fibre reinforced thermoplastics. Polym. Polym. Compos. 21(8):483–94 - Emerson D, Grauer D, Hang B, Reif M, Henning F, et al. 2012. Using unidirectional glass tapes to improve impact performance of thermoplastic composites in automotive applications. Presented at Soc. Plast. Eng.
Automot. Compos. Conf. Exhib., Troy, MI, Sept. 11–13 - LayStitch Technology. 2018. Print technology. http://www.laystitch.com/Technology.html. Accessed
Aug. 2018 - Behrens BA, Raatz A, Hubner S, Bonk C, Bohne F, et al. 2017. Automated stamp forming of continuous
fiber reinforced thermoplastics for complex shell geometries. Proc. CIRP 66:113–18 - Vaidya UK. 2010. Composites for Automotive, Truck and Mass Transit. Lancaster, PA: DEStech
- Thattaiparthasarathy KB. 2008. Process simulation, design and manufacturing of a long fiber thermoplastic composite for mass transit application. Composites A Appl. Sci. Manuf. 39(9):1512–21
- Thomason JL, Vlug MA. 1996. Influence of fiber length and concentration on the properties of glass
fibre–reinforced polypropylene. 1. Tensile and flexural modulus.Composites A Appl. Sci.Manuf. 27(6):477–84 - IDI Compos. 2018. Structural thermoset composites. http://www.idicomposites.com/technology-stc.
php - Cabrera-Rios M, Castro JM. 2006. An economical way of using carbon fibers in sheet molding compound
compression molding for automotive applications. Polym. Compos. 27(6):718–22 - Carberry W. 2008. Airplane recycling efforts benefit Boeing operators. AERO, Quart. 4. http://www.
boeing.com/commercial/aeromagazine/articles/qtr_4_08/pdfs/AERO_Q408_article02.pdf - IACMI. 2016. Pioneering partnerships announced for composite recycling. News Release, IACMI. http://iacmi.org/2016/07/01/pioneering-partnerships-announced-composite-recycling/. Accessed Aug. 1
- Janney M, Ledger J, Vaidya U. 2012. Long fiber thermoplastic composites from recycled carbon fiber. Presented at ISTC, 44th, Charleston, SC, Oct. 22–25
- Janney M, Vaidya U, Sutton R, Ning H. 2014.Re-grind study of PPS-based long fiber thermoplastic composites. Presented at SAMPE, Seattle
- Okine RK, Edison DH, Little NK. 1990. Properties and formability of an aligned discontinuous fiber
thermoplastic composite sheet. J. Reinf. Plast. Compos. 9(1):70–90 - Sloan J, ed. 2016. Composites recycling becomes a necessity. Compos. World, May 16. https://www.
compositesworld.com/articles/composites-recycling-becomes-a-necessity - Blackman B, Kinloch A, Watts J. 1994. The plasma treatment of thermoplastic fibre composites for
adhesive bonding. Composites 25(5):332–41 - Brosius D, Armstrong K. 2017. IACMI baseline cost and energy metrics. Presentation, Mar.
- Das S, Armstrong K. 2018. FRPC energy use estimation tool. https://ornlenergyestimatortools.
shinyapps.io/frpc-energy-estimator2/ - USDRIVE. 2015. Materials technical team roadmap. Rep. https://www.energy.gov/…/MTT%
20Roadmap%20UPDATE%20Apprvd%2003-11-1 - Baldan A. 2004. Adhesively-bonded joints and repairs in metallic alloys, polymers and composite materials: adhesives, adhesion theories and surface pretreatment. J. Mater. Sci. 39(1):1–49
9. Copyright:
본 자료는 [Alan Taub 외] 저자의 논문: [Materials for Automotive Lightweighting]을 기반으로 작성되었습니다.
논문 출처: [https://doi.org/10.1146/annurev-matsci-070218-010134]
본 자료는 위 논문을 바탕으로 요약 작성되었으며, 정보 제공 목적으로만 사용됩니다. 무단 상업적 사용은 금지됩니다.
Copyright © 2025 CASTMAN. All rights reserved.