본 소개 논문은 "Effect of Core Temperature at HPDC on the Internal Quality of the Casting", [출판:"Archives of Foundry Engineering"]에서 발행한 논문을 기반으로 작성되었습니다.
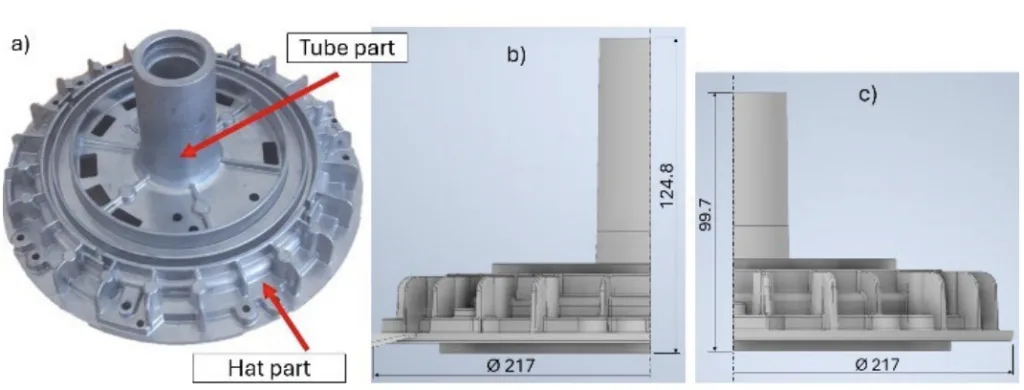
1. 개요:
- 제목: HPDC에서 코어 온도가 주조의 내부 품질에 미치는 영향
- 저자: M. Matejka, D. Bolibruchová, R. Podprocká, P. Oslanec
- 발행 연도: 2024년
- 발행 학술지/학회: Archives of Foundry Engineering
- 키워드: HPDC, Al-Si-Cu 합금, 기공, 미세 구조
2. 초록:
고압 다이캐스팅(HPDC)은 높은 치수 정확도와 복잡한 형상을 가진 광범위한 알루미늄 부품을 생산하는 가장 생산적인 주조 방법 중 하나입니다. 고압 주조의 공정 변수는 일반적으로 주조의 기공 존재 또는 미세 구조와 같은 주조의 최종 품질에 직접적인 영향을 미칩니다. 공기 혼입 외에도 기공은 수소 용해로 인해 발생할 수도 있습니다. 수소는 고온에서 수증기와 용융물의 반응에 의해 방출되고 응고 중에 방출됩니다. 이러한 결함은 강도 및 연성과 특히 피로 특성과 같은 기계적 특성을 크게 저하시킬 수 있습니다. 본 논문의 목적은 고압 금형 코어의 온도가 두 가지 형상 변형에서 알루미늄 주조의 기공 존재 및 분포와 미세 구조에 미치는 영향을 설명하는 것입니다. 코어의 온도 변화는 코어의 온도 조절 회로에서 두 가지 유동 매체, 즉 탈이온수와 열전달유를 사용하여 코어 온도 130 ± 5℃ 및 165 ± 5℃에서 작동함으로써 발생했습니다. 두 가지 형상 변형 모두에서 물(코어 온도 130 ± 5℃)을 사용했을 때 기름(코어 온도 165 ± 5℃)을 사용했을 때보다 기공률이 더 높았습니다. 반대로 미세기공률의 경우 템퍼링 오일에서 더 높은 미세기공률이 관찰되었습니다. 수냉식 코어 주조의 미세 구조는 α상(Al)과 공정 Si의 더 미세한 결정립을 특징으로 했습니다. 템퍼링 오일에서 미세 구조는 α상(Al)의 거친 결정립과 날카로운 모서리 형상의 Si 라멜라를 특징으로 했습니다.
3. 서론:
고압 다이캐스팅은 최종 주조 부품의 품질에 상당한 영향을 미치는 여러 요소를 고려하는 복잡한 공정입니다. 고압 다이캐스팅 공정의 기본 매개변수는 주로 유지 온도, 주조 및 금형 온도, 정수압 또는 가압 압력, 유입 채널의 합금 유량입니다. 고압 다이캐스팅 제품의 기계적 특성은 주로 금형 온도, 유입구에서의 금속 속도 및 적용된 주조 압력과 관련이 있습니다 [1-3].
금형 온도, 용융 금속의 유동성, 부품 형상의 복잡성 및 고압 다이캐스팅 중 냉각 속도는 모두 주조 부품의 건전성에 영향을 미칩니다. 이러한 요소를 적절하게 제어하지 않으면 최종 주조물에 다양한 결함이 나타날 수 있습니다. 작동 중 공구의 열 프로파일은 고품질 부품 생산의 또 다른 중요한 측면입니다. 금형 온도는 용융 금속에서 열을 제거하고 금형을 채우고 주조 특성을 올바르게 설정하는 데 영향을 미치는 핵심 요소입니다 [4-6]. 다이캐스팅에서 결함의 일반적인 원인은 금형이 최적의 온도에 있지 않다는 것입니다. 이 문제는 온도 조절 장치 [7,8]를 사용하여 피할 수 있습니다.
본 논문의 목적은 고압 다이캐스팅 금형 코어의 온도 조절 회로에서 흐르는 매체가 주조 튜브 높이의 두 가지 형상 변형에서 주조의 내부 품질 변화에 미치는 영향을 평가하는 것입니다. 본 논문의 실험 파트에서는 코어 온도 조절 매체로 탈이온수와 열전달유를 사용하여 작업했습니다. 고압 다이캐스팅의 내부 품질은 주조물의 선택된 중요한 위치에서 기공 분석과 구조 분석의 조합으로 평가되었습니다. 이러한 평가는 온도 조절 매체 변경이 주조물의 내부 품질에 어떻게 영향을 미치는지 더 잘 이해하는 데 도움이 될 것입니다.
4. 연구 요약:
연구 주제 배경:
고압 다이캐스팅(HPDC)은 정밀한 치수와 복잡한 형상을 가진 알루미늄 부품을 제조하는 데 매우 생산적인 방법입니다. HPDC 부품의 품질은 공정 변수, 특히 기공률과 미세 구조에 크게 영향을 받습니다. 기공은 공기 혼입 외에도 응고 중 수소 용해 및 방출로 인해 발생하여 강도 및 피로 저항과 같은 기계적 특성을 저하시킬 수 있습니다. 최적의 금형 온도를 유지하는 것은 HPDC에서 결함을 최소화하고 주조 건전성을 보장하는 데 중요하며, 종종 온도 조절 장치를 통해 달성됩니다.
기존 연구 현황:
기존 연구에서는 고압 다이캐스팅에서 금형 온도의 중요한 역할을 확립했습니다. 금형 온도, 용융 금속 유동성, 부품 형상 복잡성 및 냉각 속도와 같은 요소는 주조 건전성에 영향을 미치는 것으로 알려져 있습니다. 올바른 금형 온도를 유지하는 것은 열 제거, 금형 충진 및 주조 특성 설정에 필수적입니다. 기존 연구에서는 다이캐스팅에서 금형이 최적 온도에 있지 않은 일반적인 문제를 해결하기 위해 온도 조절 장치를 사용하는 것을 강조합니다 [7, 8]. 연구에서는 금형 온도 제어를 개선하기 위해 등각 냉각 [8] 및 대체 냉각 시스템 [9]과 같은 방법도 탐구했습니다.
연구 목적:
본 연구의 목적은 고압 다이캐스팅 금형에서 코어 온도가 알루미늄 주조물의 내부 품질에 미치는 영향을 조사하는 것입니다. 특히, 금형 코어의 온도 조절 회로 내에서 다양한 냉각 매체가 기공률과 미세 구조에 어떻게 영향을 미치는지에 초점을 맞춥니다. 본 연구에서는 이러한 효과를 평가하기 위해 주조 튜브의 두 가지 형상 변형을 사용하여 온도 조절 매체가 주조 품질에 미치는 영향에 대한 이해를 높이는 것을 목표로 합니다.
핵심 연구:
핵심 연구는 HPDC로 생산된 AlSi12Cu1(Fe) 합금 주조물의 기공률과 미세 구조에 대한 다양한 냉각 매체(탈이온수 및 열전달유)로 조절되는 코어 온도의 영향을 실험적으로 조사합니다. 튜브 높이가 다른 두 가지 형상의 주조 부품인 Statorbuchse EC 75와 EC 55를 냉각 매체로 물(코어 온도 130 ± 5℃)과 열전달유(코어 온도 165 ± 5℃)를 모두 사용하여 주조했습니다. 내부 품질은 CT 스캔을 사용한 기공률 분석과 광학 및 주사 전자 현미경을 사용한 미세 구조 분석을 통해 평가했으며, 주조물의 중요한 위치에 초점을 맞췄습니다.
5. 연구 방법론
연구 설계:
본 연구에서는 두 가지 다른 코어 냉각 매체(탈이온수 및 열전달유)가 HPDC 알루미늄 합금 주조물의 내부 품질에 미치는 영향을 비교하는 실험 설계를 사용했습니다. 주조 부품의 두 가지 형상 변형(Statorbuchse EC 75 및 EC 55)을 사용하여 다양한 형상에서 이러한 효과의 일관성을 평가했습니다. 코어 온도는 물(130 ± 5℃)과 기름(165 ± 5℃)의 두 가지 수준으로 제어하면서 다른 HPDC 매개변수는 일정하게 유지했습니다.
데이터 수집 및 분석 방법:
- 기공률 평가: NIKON - XT H225 ST 장치를 사용한 컴퓨터 단층 촬영(CT 스캔)을 활용하여 기공률을 평가했습니다. CT 이미지는 Quickphoto industrial 3.2 프로그램을 사용하여 정량적으로 분석하여 주조물 단면에서 기공의 면적 비율과 최대 기공 길이(Feret 직경)를 결정했습니다.
- 미세 구조 분석: 중요한 위치에서 샘플을 준비하고 다음을 사용하여 분석했습니다.
- NEOPHOT 32 광학 현미경을 사용한 광학 현미경(OM).
- VEGA LMU II 주사 전자 현미경을 사용한 주사 전자 현미경(SEM).
- 에너지 분산 X선 분광법(EDX)을 통한 원소 분석.
연구 주제 및 범위:
본 연구는 다음 주제에 초점을 맞췄습니다.
- HPDC AlSi12Cu1(Fe) 합금 주조물에서 거시 기공률 및 미세 기공률에 대한 코어 온도(물 대 오일 냉각으로 조절)의 영향.
- 냉각 매체가 미세 구조, 특히 α상(Al)의 결정립 크기, 공정 실리콘 형태 및 금속간 화합물에 미치는 영향.
- 스테이터 하우징 주조물의 두 가지 형상 변형(EC 75 및 EC 55)에서 이러한 효과의 비교.
- 사용된 냉각 매체와 관련된 기공 분포 및 형태 조사.
6. 주요 결과:
주요 결과:
- 기공률: EC 55 및 EC 75 변형 모두에서 오일 냉각 코어(더 높은 코어 온도 165 ± 5℃)에 비해 수냉식 코어(더 낮은 코어 온도 130 ± 5℃)로 생산된 주조물에서 더 높은 거시 기공률이 관찰되었습니다. 반대로 미세 기공률은 오일 템퍼링 주조물에서 더 높게 나타났습니다.
- 미세 구조: 수냉식 주조물은 α상(Al)과 둥근 모양과 라멜라를 가진 공정 Si의 더 미세한 결정립을 나타냈습니다. 오일 템퍼링 주조물은 α상(Al)의 더 거친 결정립과 날카로운 모서리 라멜라의 공정 Si를 보였습니다.
- 기공 분포: 수냉식은 주조물 전체 부피에 분포된 기공을 초래한 반면, 오일 냉각은 EC 55 주조물에서 기공 발생을 주로 튜브 높이의 상위 2/3로 제한했습니다. EC 75 주조물에서 수냉식은 특히 중요한 영역에서 기공 크기와 수를 크게 증가시켰습니다.
- 냉각 속도: 더 높은 열전달 계수를 가진 수냉식은 냉각 속도를 증가시켜 거시 기공률을 감소시켰지만 미세 기공률을 증가시키고 미세 구조를 개선했습니다. 더 낮은 냉각 속도를 가진 열전달유는 더 높은 거시 기공률을 초래했지만 미세 기공률을 감소시키고 더 거친 미세 구조를 초래했습니다.
그림 목록:
- 그림 1. Statorbuchse EC, a) 형상, b) EC 75, c) EC 55
- 그림 2. 코어를 통과하는 단면 및 주조물 내 코어 위치, 빨간색 타원으로 주조물의 중요한 위치 표시 및 빨간색 타원으로 미세 구조 분석을 위한 샘플링 위치 표시
- 그림 3. EC 55 주조물의 CT 이미지; a) 수냉식(코어 온도 130 ± 5℃), b) 오일 템퍼링(코어 온도 165 ± 5℃)
- 그림 4. EC 75 주조물의 CT 이미지; a) 수냉식(코어 온도 130 ± 5℃), b) 오일 템퍼링(코어 온도 165 ± 5℃)
- 그림 5. 기공 면적 비율 및 평균 최대 기공 길이 평가 후 EC 75 주조물의 CT 이미지; a) 수냉식(코어 온도 130 ± 5℃), b) 오일 템퍼링(코어 온도 165 ± 5℃)
- 그림 6. EC 55 주조물 미세 구조; a) 수냉식, b) 오일 템퍼링
- 그림 7. EC 75 주조물 미세 구조; a) 수냉식, b) 오일 템퍼링
- 그림 8. EC 55 주조물의 공정 Si 상세; a) 수냉식, b) 오일 템퍼링
- 그림 9. EC 55 주조물 미세 구조; a) 수냉식, b) 오일 템퍼링
7. 결론:
본 연구는 코어 온도 조절 회로에서 냉각 매체의 선택이 HPDC 알루미늄 주조물의 내부 품질에 상당한 영향을 미친다고 결론 내립니다. 열전달유를 사용하면 거시 기공률이 낮아지는 반면, 물을 사용하면 거시 기공률은 증가했지만 중요한 영역에서 더 미세한 결정립과 감소된 미세 기공률로 미세 구조가 개선되었습니다. 결과는 거시 기공률을 최소화하는 것이 가장 중요한 응용 분야의 경우 열전달유가 더 나을 수 있음을 시사합니다. 반대로 미세 구조 개선을 우선시하고 더 높은 거시 기공률을 수용할 수 있는 응용 분야의 경우 수냉식이 유리할 수 있습니다. 작업 표면의 정확한 온도 제어를 유지하는 것이 중요하며, 본 연구에서는 미세 구조의 잠재적인 절충 및 수축 관련 기공률 증가에도 불구하고 가스 기공률을 최소화하는 데 열전달유가 더 최적인 것으로 간주되었습니다.
8. 참고 문헌:
- [1] Kalpakjian, S., Schmid, S.R. (2009). Manufacturing Engineering and Technology. (6th ed.). Pearson Ed Asia.
- [2] Sadeghi, M. & Mahmoudi, J. (2012). Experimental and theoretical studies on the effect of die temperature on the quality of the products in high-pressure die-casting process. Advances in Materials Science and Engineering. 1, 1-9. https://doi.org/10.1155/2012/434605.
- [3] Bruna, M., Bolibruchová, D., Pastircák, R. & Remisová, A. (2019). Gating system design optimization for investment casting process. Journal of Materials Engineering and Performance. 28(54), 3887-3893. DOI: 10.1007/s11665-019-03933-3.
- [4] Tavakoli, S., Ranc-Darbord, I. & Wagner, D. (2014). Thermal behavior of the mold surface in HPDC process by infrared thermography and comparison with simulation. In Proceedings of the 12th International Conference on Quantitative Infrared Thermography, July 2014. France, Bordeaux. DOI: 10.21611/qirt.2014.054.
- [5] Shin, S.-S. & Lee, S.-K., Kim, D. & Lee, B. (2021). Enhanced cooling channel efficiency of high-pressure die-casting molds with pure copper linings in cooling channels via explosive bonding. Journal of Materials Processing Technology. 297. 117235, 1-19. DOI: 10.1016/j.jmatprotec.2021.117235.
- [6] Pastircák, R., Scury, J. & Moravec, J. (2017). The effects of pressure during the crystallization on properties of the AlSi12 alloy. Archives of Foundry Engineering. 17(3), 103-106. DOI: 10.1515/afe-2017-0099.
- [7] Hu, H., Chen, F. Chen, X., Chu, Y. & Cheng, P. (2004). Effect of cooling water flow rates on local temperatures and heat transfer of casting dies. Journal of Materials Processing Technology. 148(1). 57-67. DOI: 10.1016/j.jmatprotec.2004.01.040.
- [8] Jarfors, A., Sevastopol, R., Karamchedu, S., Zhang, Q., Steggo, J. & Stolt, R. (2021). On the use of conformal cooling in high-pressure die-casting and semisolid casting. Technologies. 9(2), 39. https://doi.org/10.3390/technologies9020039.
- [9] Fiorentini, F., Curcio, P., Armentani, E., Rosso, C. & Baldissera, P. (2019). Study of two alternative cooling systems of a mold insert used in die casting process of light alloy components. Procedia Structural Integrity. 24, 569-582. DOI: 10.1016/j.prostr.2020.02.050.
- [10] Kimura, T, Yamagata, H. & Tanikawa, S. (2015). FEM stress analysis of the cooling hole of an HPDC die. IOP Conference Series: Materials Science and Engineering. 84, 012052, 1-7. DOI: 10.1088/1757-899X/84/1/012052.
- [11] Tool-Temp. (2023 April). Die casting - we provide you with perfect tool tempering. Retrieved April 08, 2024, form https://tool-temp.ch/en/industries-temperature-control-units/die-casting-industry-temperature-control-unit/.
- [12] Wang, R., Zuo, Y., Zhu, Q., Liu, X. & Wang, J. (2022). Effect of temperature field on the porosity and mechanical properties of 2024 aluminum alloy prepared by direct chill casting with melt shearing. Journal of Materials Processing Technology. 307, 117687, 1-13. https://doi.org/10.1016/j.jmatprotec.2022.117687.
- [13] Shen, X., Liu, S., Wang, X., Cui, C., Gong, P., Zhao, L., Han, X. & Li, Z. (2022). Effect of cooling rate on the microstructure evolution and mechanical properties of iron-rich Al-Si alloy. Materials. 15(2), 411, 1-10. DOI: 10.3390/ma15020411.
- [14] Li, L., Li. D., Mao. F., Feng, J., Zhang, Y. & Kang, Y. (2020). Effect of cooling rate on eutectic Si in Al-7.0Si-0.3Mg alloys modified by La additions. Journal of Alloys and Compounds. 826, 154206, 1-10. https://doi.org/10.1016/j.jallcom.2020.154206.
- [15] Niklas, A., Abaunza, U., Isabel, F. Lacaze, J. & Suarez, R. (2010). Thermal analysis as a microstructure prediction tool for A356 aluminium parts solidified under various cooling conditions. China Foundry. 59(11), 1167-1171.
9. 저작권:
- This material is a paper by "M. Matejka, D. Bolibruchová, R. Podprocká, P. Oslanec". Based on "Effect of Core Temperature at HPDC on the Internal Quality of the Casting".
- Source of the paper: https://doi.org/10.24425/afe.2024.151295
본 자료는 위 논문을 기반으로 요약되었으며, 상업적 목적으로 무단 사용하는 것을 금지합니다.
Copyright © 2025 CASTMAN. All rights reserved.