본 논문은 "Euro PM2009 – Non-Ferrous Materials - Processing"에 게재된 "Development of Platinum-Base Superalloy Components via Powder Metallurgy" 논문을 기반으로 작성되었습니다.
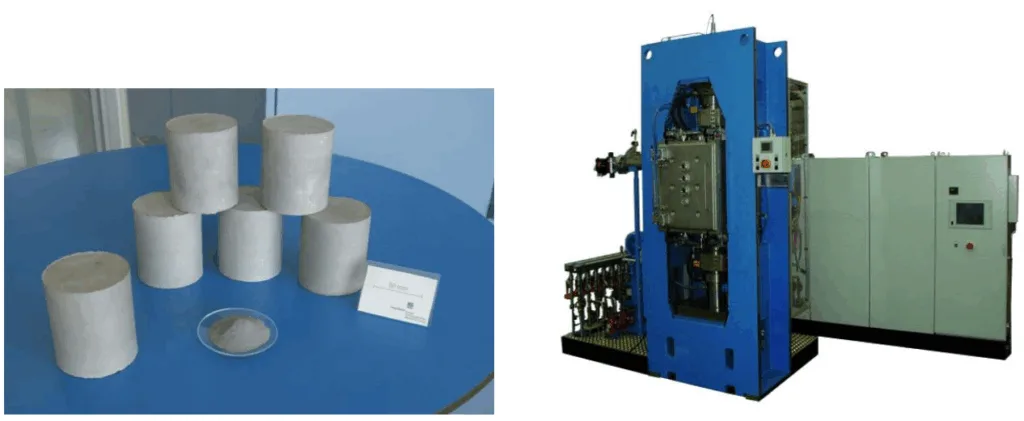
1. 개요:
- 논문 제목: Development of Platinum-Base Superalloy Components via Powder Metallurgy
- 저자: A. Mwamba, L.H. Chown and R. Süss
- 발행 연도: 2009
- 게재 학술지/학회: Euro PM2009 – Non-Ferrous Materials - Processing
- 키워드: 논문에 명시적으로 나열되지 않음.
2. 초록:
Mintek은 이전에 백금 기반 초합금을 개발했으나, 이 합금들은 주조가 어렵고 성형성이 제한적이어서 분말 야금법이 잠재적인 생산 경로로 고려되었습니다. 본 연구에서는 Pt₈₄:Al₁₁:Cr₃Ru₂ 원자 조성을 갖는 합금 백금 분말을 생산하기 위해 분말 야금법에 기반한 두 가지 방법을 사용했습니다. 첫 번째 방법에서는 알루미늄, 크롬, 루테늄 원소 분말을 백금 스펀지와 함께 용해하여 예비 합금을 형성했습니다. 그런 다음 이 예비 합금을 재용해하고 수분사하여 예비 합금 백금 분말을 생산했습니다. 두 번째 방법에서는 수분사로 생산된 순수 백금 분말을 알루미늄, 크롬, 루테늄 원소 분말과 혼합하여 기계적으로 합금했습니다. 예비 합금 분말과 기계적 합금 분말은 순수 백금 분말의 형태, 크기 분포, 밀도를 기준으로 특성화되었으며 일축 압축되었습니다. 압축체는 소결되었습니다. 광학 현미경, XRD, EDX 분석을 조합하여 소결된 시편은 분말 특성, 미세 구조, 경도에 대해 특성화되었으며 순수 백금 압축체 및 동일 조성의 주조 합금과 비교되었습니다.
3. 서론:
백금은 자동차 촉매 및 보석류 응용 분야에서의 사용으로 잘 알려져 있습니다. 그러나 특정 합금 원소 존재 시 니켈과 유사한 특성으로 인해 백금 합금이 고온 구조 재료로 사용될 가능성에 대한 관심이 높아졌습니다. 수년 동안 니켈 기반 초합금은 이러한 응용 분야에서 선택되는 재료였습니다. 항공 및 육상 터빈 블레이드에 NBSAs를 사용하는 것이 일반적인 예입니다. 그러나 더 높은 작동 온도가 요구되는 새로운 응용 분야로 인해 니켈은 기본 금속으로서 온도 한계에 도달하고 있습니다. 대체 재료가 필요하며, 이리듐(1), 로듐(2), 백금(3)과 같은 백금족 금속은 니켈과 유사한 거동을 보이면서도 더 높은 융점을 갖는 추가적인 이점으로 인해 좋은 후보로 간주되었습니다.
Mintek은 NBSAs와 유사한 미세 구조를 갖는 백금 기반 초합금(PBSAs)을 개발했습니다(4-6). 백금 초합금의 미세 구조는 Pt-Al 시스템을 기반으로 합니다. 이 시스템은 Pt 기반 γ 매트릭스에 γ' Pt₃Al 입자가 포함된 미세 구조로 구성됩니다. 이 Pt-Al 기반 시스템에 Ni와 Cr(7) 또는 Ru와 Cr(8)을 합금함으로써 Pt₃Al의 L1₂ 구조를 성공적으로 안정화시켰습니다. Pt₈₄:Al₁₁:Ru₂:Cr₃ 조성을 갖는 4원계 합금이 개발되어 최상의 구조를 보이는 것으로 최적화되었습니다(7). 백금 기반 초합금의 고온 부식 거동에 대한 연구는 NBSAs를 능가하는 좋은 결과를 보여주었습니다(9). 백금 기반 초합금의 크리프 특성에 대한 조사에서도 특정 백금 기반 합금이 높은 고온 응력-파단 강도와 연성을 가져 잠재적인 고온 합금임을 보여주었습니다(10). 그러나 PBSAs의 열악한 주조성과 성형성으로 인해 전통적인 주조 및 성형 방법으로는 이러한 합금을 제조하기 어려워 분말 야금 경로를 탐색할 필요성이 제기되었습니다(4).
4. 연구 요약:
연구 주제의 배경:
백금 기반 초합금(PBSAs)은 니켈과 유사한 합금 특성을 보이면서도 더 높은 융점을 제공하기 때문에 고온 구조용 니켈 기반 초합금(NBSAs)의 대안으로 연구되고 있습니다. [서론]
이전 연구 현황:
Mintek은 이전에 Pt-Al 시스템을 기반으로 한 PBSAs를 개발했으며, 이는 Pt 기반 γ 매트릭스에 γ' Pt₃Al 석출물을 특징으로 하며, Ni, Cr, Ru와 같은 합금 원소로 안정성이 향상되었습니다. [서론] 이러한 PBSAs는 우수한 고온 부식 저항성과 크리프 특성을 보였지만, 열악한 주조성과 성형성으로 인해 어려움을 겪었습니다. [서론]
연구 목적:
본 연구는 이러한 첨단 합금의 주조 및 성형과 관련된 어려움을 극복하기 위해 특정 Pt₈₄:Al₁₁:Cr₃Ru₂ 조성을 목표로 하여 PBSAs의 실행 가능한 생산 경로로서 분말 야금법을 조사하는 것을 목표로 했습니다. [초록, 서론]
핵심 연구:
본 연구는 두 가지 별개의 분말 야금 기술에 초점을 맞추었습니다: 첫째, 예비 형성된 합금의 수분사, 둘째, 원소 분말과 수분사된 순수 백금의 기계적 합금. [초록] 이러한 방법으로 생산된 분말의 특성과 소결체의 특성을 철저히 평가하고 비교했습니다. [초록]
5. 연구 방법론
연구 설계:
본 연구는 두 가지 분말 야금 경로를 통해 목표 조성 Pt₈₄:Al₁₁:Cr₃Ru₂를 갖는 합금 백금 분말을 생산하도록 설계되었습니다: (i) 예비 합금 후 수분사, (ii) 순수 Pt 분말과 원소 첨가물의 기계적 합금. [실험 절차] 이후 분말을 압축하고 소결했으며, 생성된 재료를 특성화하여 각 경로의 효능을 평가했습니다. [실험 절차]
데이터 수집 및 분석 방법:
분말 생산에는 Pt 스펀지와 원소 성분을 용해하여 예비 합금 분말을 만든 후 수분사(수압 200bar, 과열 100°C)하고 <150µm로 체질하는 과정이 포함되었습니다. [실험 절차] 기계적 합금 분말은 수분사된 순수 Pt 분말(<500µm)을 원소 Al, Cr, Ru와 함께 밀링하여 준비했습니다. [실험 절차]
분말 특성화에는 Arnold 측정기를 사용한 겉보기 밀도 결정, Malvern Mastersizer 2000, 광학 현미경, SEM, XRD, EDX를 사용한 입자 형상, 크기 및 분포 평가가 포함되었습니다. [실험 절차]
예비 합금 분말의 분말 압축은 MPIF 표준 41에 따라 80톤 일축 프레스를 사용하여 수행되었으며, 기계적 합금 분말은 17.50mm 다이에서 10~35MPa 범위의 중간 압력(표 1에 자세히 설명됨)으로 압축되었습니다. [실험 절차, 표 1]
소결 및 열처리는 아르곤 분위기에서 수행되었으며, 시편은 분당 8°C의 속도로 1450°C까지 가열되어 5시간 동안 유지되었습니다. [실험 절차] 소결 후 열처리에는 일부 예비 합금 및 기계적 합금 압축체를 1450°C에서 100시간 동안 재가열하고, 기계적 합금 압축체를 1250°C에서 100시간 동안 재가열하는 과정이 포함되었습니다. [실험 절차]
압축체 특성화에는 순수 벌크 백금 밀도에 대한 상대적인 생밀도 평가가 포함되었습니다. 소결 압축체는 소결 밀도, 미세 구조(광학 현미경 및 EDX 사용), 경도에 대해 분석되었으며, 동일 조성의 주조 합금과 비교되었습니다. [실험 절차]
연구 주제 및 범위:
본 연구는 분말 야금법을 통한 Pt 기반 초합금 부품(Pt₈₄:Al₁₁:Cr₃Ru₂) 개발에 초점을 맞추었으며, 예비 합금 대 기계적 합금 분말 생산 경로를 비교했습니다. [초록, 서론] 범위에는 분말 특성 평가와 소결 압축체의 미세 구조 및 기계적 특성 평가가 포함되었습니다. [초록, 서론]
6. 주요 결과:
주요 결과:
분말 특성: 예비 합금 분말은 단일 모드 입자 크기 분포를 보였으며, 입자의 50%가 43.8µm보다 컸습니다 (그림 1 및 표 2 참조). 반대로, 기계적 합금 분말은 더 미세하여 입자의 50%가 6.7µm보다 작았으며, 입자 크기 분포는 단일 모드와 이중 모드 사이였습니다 (그림 1, 표 2). 두 분말 유형 모두 둥근 불규칙한 형태를 보였습니다 (그림 2). EDX 분석 결과 두 분말 모두 성공적으로 합금되었음을 확인했습니다 (표 3). 그러나 예비 합금 분말에서는 산소가 검출되어 수분사 중 산화가 발생했음을 나타내는 반면, 밀링된 분말은 산소가 없었습니다. [분말 화학 조성, 표 3] 두 분말의 XRD 패턴은 왜곡된 백금 격자를 나타냈으며, Pt₃Al 피크도 확인되었습니다 (그림 3). [상 식별]
분말 압축 및 소결: 예비 합금 분말(<150µm)은 순수 Pt 분말(<500µm)이 약 17.5g/cm³에 도달한 것에 비해 약 15.0g/cm³의 생밀도를 달성하여 열악한 압축 거동을 보였습니다. [분말 압축 및 소결 반응] 기계적 합금 분말은 낮은 겉보기 밀도(약 3.5g/cm³)를 가졌고 결과적으로 낮은 생밀도(약 10.0g/cm³)를 보였습니다 (표 5 참조). [분말 압축 및 소결 반응, 표 5] 소결은 예비 합금 압축체의 경우 약 7%, 순수 Pt 압축체의 경우 약 5%의 밀도 증가를 가져왔습니다. [분말 압축 및 소결 반응] 10-20MPa에서 압축된 기계적 합금 압축체의 경우 소결 후 30-35%의 더 상당한 밀도 증가가 관찰되었습니다. [소결 후…]
소결 압축체의 미세 구조: 소결된 예비 합금 백금 압축체는 약 500nm 크기의 입방형 Pt₃Al 석출물과 약 10-50nm의 매우 미세한 석출물을 포함하는 백금 고용체 매트릭스를 특징으로 했습니다 (그림 4 (a) 및 (b)). [소결 압축체의 미세 구조] 기계적 합금 압축체 시편을 1450°C에서 100시간 동안 시효 처리했을 때 액체가 형성된 것은 흥미로운 관찰이었습니다. [소결 압축체의 미세 구조] 소결된 상태의 기계적 합금 압축체(그림 4 (c))와 이후 1250°C에서 100시간 동안 열처리된 압축체(그림 4 (d))는 무작위로 분포된 큰 석출물을 가진 회색빛 매트릭스를 보였습니다. 1250°C 열처리 후에는 100nm 미만의 석출물이 관찰되었습니다. [소결 압축체의 미세 구조]
소결 문제: 입자 탈락 및 크레이터(그림 5)와 같은 불량한 소결의 증거가 관찰되었습니다. 이는 분말 입자 표면에 존재하는 산화알루미늄 층 때문으로, 입자 간 결합을 방해했습니다. [소결 압축체의 미세 구조]
경도: 예비 합금 소결 압축체의 미세 경도 값(소결 상태 343±50 HV₀.₅, 시효 처리 369±37 HV₀.₅, 표 8)은 동일 조성의 주조 합금에 대해 보고된 일반적인 범위(300-400 HV₁₀) 내에 있었습니다. [소결 압축체의 경도] 유사하게, 이러한 예비 합금 압축체의 매크로 경도(소결 상태 336±11 HV₁₀, 시효 처리 365±23 HV₁₀, 표 9)도 주조 합금 값과 일치했습니다. [소결 압축체의 경도] 기계적 합금 압축체는 더 낮은 매크로 경도(소결 상태 139±16 HV₁₀, 시효 처리 199±15 HV₁₀, 표 9)를 보였지만, 시효 처리를 통해 상당한 증가를 보였습니다. [소결 압축체의 경도] 반대로, 기계적 합금 압축체의 미세 경도는 시효 처리 후 감소했는데(316±25에서 240±22 HV₀.₅로, 표 8), 이는 아마도 응력 완화 및 입자 이완 때문일 것입니다. [소결 압축체의 경도]
그림 목록:
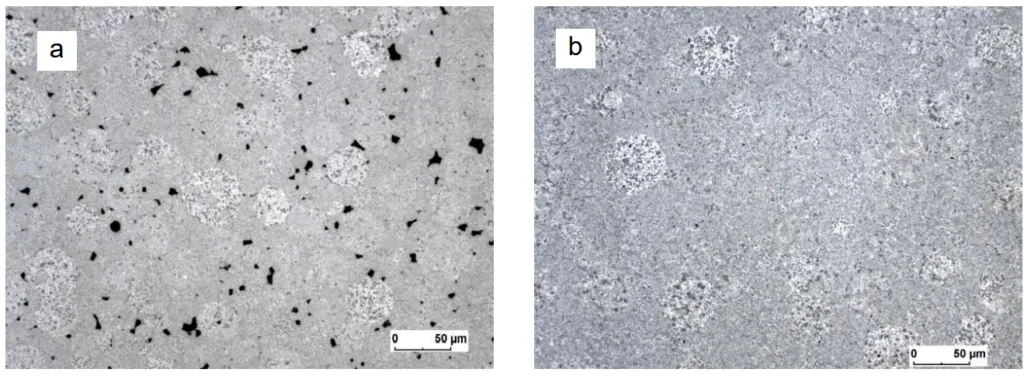
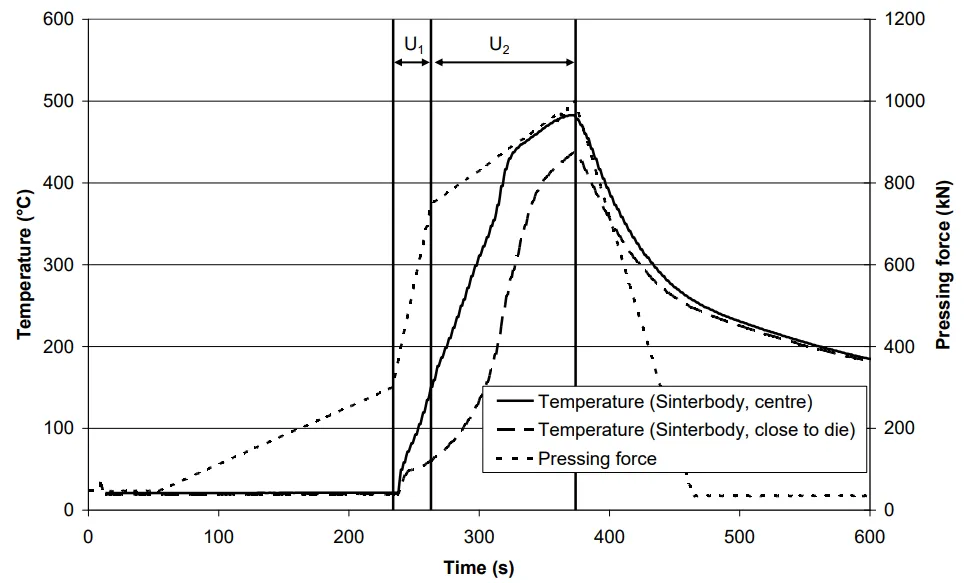
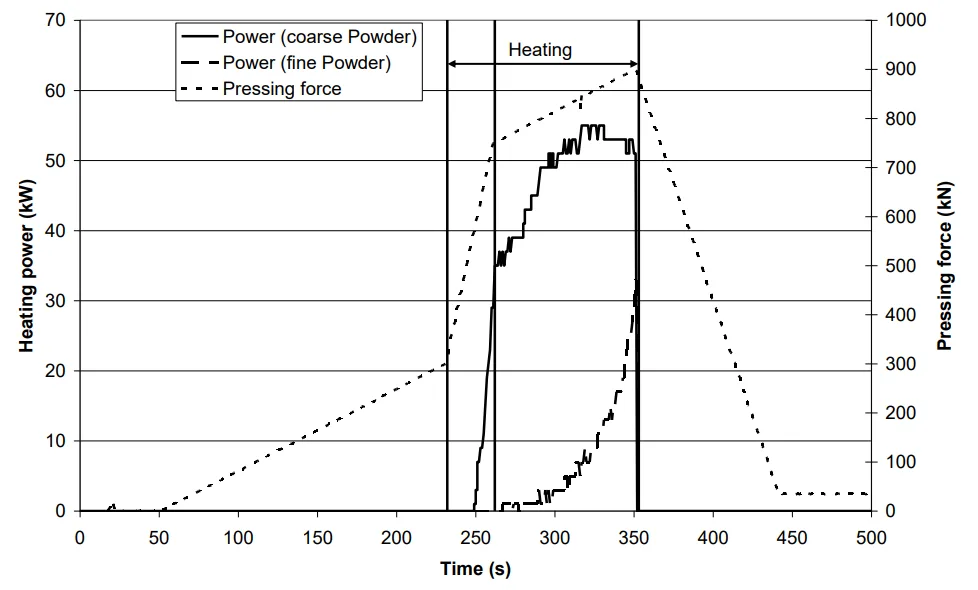
![Fig. 4. Microstructures of a consolidated MA sample (left) and a gas-atomized sample (right) with composition Mo–9Si–8B [10]. The Mo matrix is the brightest appearing phase, and the grey and dark grey appearing phases are Mo3Si and Mo5SiB2, respectively.](https://castman.co.kr/wp-content/uploads/image-2459-1024x378.webp)
![Fig. 6: Double-logarithmic plot of strain rate vs. applied stress for various Mo-9Si-8B alloys. Data for a single-crystalline Nickelbase superalloy CMSX-4 are shown for comparison [14].](https://castman.co.kr/wp-content/uploads/image-2454.webp)
- 그림 1. 두 분말의 입도 분포.
- 그림 2: 다른 분말의 입자 형상.
- 그림 3. 예비 합금 백금 분말의 XRD 패턴으로 (a) 약간 이동된 Pt 피크; (b) 약간 이동된 Pt₃Al 피크를 보여줌.
- 그림 4: 소결된 예비 합금 백금 압축체의 일반적인 미세 구조.
- 그림 5: 불량한 소결 영역의 일반적인 특징.
7. 결론:
- 예비 합금 분말의 입자 크기 및 크기 분포는 상대적으로 작은 평균 크기로 좁았습니다. 예비 합금 분말은 공기 및/또는 물의 산소와 반응한 용융물 내 알루미늄의 결과인 불연속적인 산화알루미늄 층으로 둘러싸여 있었습니다. 예비 합금 분말로 얻은 압축체는 소결 중 결합을 방해하는 산화알루미늄 층의 존재로 인해 결합되지 않은 입자와 다공성이 많아 소결 품질이 좋지 않았습니다. 소결 압축체의 미세 구조는 Pt₃Al 석출물을 가진 백금 고용체 매트릭스로 구성된 주조 합금의 미세 구조와 유사했습니다. 소결 압축체의 경도는 동일 조성의 주조 합금에서 발견되는 경도 범위(300-400 HV₁₀) 내에 있었습니다. 예비 합금 합금 압축체를 소결 온도에서 100시간 동안 재가열하고 유지해도 소결 품질이나 미세 구조는 변하지 않았으며 경도가 약간 증가하는 데 그쳤습니다.
- 백금, 알루미늄, 크롬, 루테늄 원소 분말을 백금 기반 초합금 조성으로 기계적으로 합금하는 것이 가능합니다. 기계적 합금으로 생산된 분말은 박편 모양이었고, 평균 크기가 5µm 미만인 미세 입자가 많았으며, 응집 수준이 높았고, 단일 모드와 이중 모드 분포 사이에 있는 입자 크기 분포를 가졌습니다. 겉보기 밀도는 매우 낮았습니다. 기계적 합금 분말은 압축에 대한 반응은 좋지 않았지만 소결에 대한 반응은 좋았습니다. 압축체의 미세 구조는 다양한 크기와 형태의 Pt₃Al 석출물이 분포된 백금 고용체 매트릭스로 구성되었습니다. 압축체의 경도는 주조 합금보다 낮았는데, 그 이유는 분말을 고화하는 데 사용된 낮은 압축 압력 때문이었습니다. 시효 처리 중 미세 구조에 상당한 변화가 일어나 100nm 미만 크기의 Pt₃Al 석출물이 형성되었습니다. 시효 처리 후 미세 구조 변화로 인해 경도가 상당히 증가했습니다.
8. 참고문헌:
- [논문에 인용된 대로 참고문헌을 정확하게 기재합니다 - 원본 논문 참조]
- . YAMABE-MITARAI, Y., KOIZUMI, Y., MURAKAMI, R, Y., MARUKO, T., and HARADA, H., Scripta Materialia, Vol. 35, No. 2, 1996, pp. 211-215.
- . YAMABE-MITARAI, Y., KOIZUMI, Y., MURAKAMI, Ro, Y., MARUKO, T., and HARADA, H., Scripta Materialia, Vol. 36, No. 4, 1997, pp. 393-398.
- . WOLFF, I.M., and HILL, P.J., Plat. Metals Rev., 44(4) (2000) 158-166.
- . CORNISH, L.A., SÜSS, R., CHOWN, L.H., DOUGLAS, A., and GLANER, L., Plat. Metals Rev. (2009), 53, pp 2-10.
- . WENDEROTH, M., CORNISH, L.A., SÜSS, R., VORBERG, S., FISCHER, B., GLATZEL, U., and VÖLK, R., Metal. And Mat. Transactions A, Vol. 36 A, pp 567-575.
- . DOUGLAS, A., HILL, P.J., MURAKUMO, T., CORNISH, L.A. and SÜSS, R., Plat. Metals Rev.2009, 53, pp 69-77.
- . VÖLK, R., WENDEROTH, M., PREUSSNER, J., VORBERG, S., FISCHER, B., YAMABE-MITARI, Y., HARADA, H., and GLATZEL, U., Mater. Sci. Eng. A 510, (2009), pp 328-331.
- . HILL, P.J., CORNISH, L.A., ELLIS, P., WITCOMB, M.J., J. Alloys Comp. 322 (2001) 166-17.
- . MALEDI, N.B., POTGIETER, J.H., SEPHTON, M., CORNISH, L.A., CHOWN, L.H., and SÜSS, R., Int. Plat. Conf., The SAIMM 2006, pp 81-90.
- . SÜSS, R, FREUND, D., VÖLK, R., FISCHER, B., HILL, P.J., ELLIS, P., and WOLFF, I.M., Mat.Sc. Eng. A 338, 2002, pp 133-141.
- . SURYANARAYANA, C., Marcel Dekker, NY, USA (2004), ISBN 0-8247-4103-X, pp 269-315.
- . SHERIF EL-ESKANDARANY, M.,William Andrew Publishing, Norwich, NY, USA, (2001) ISBN 0-8155-1462-X.
- . MÖLLER, H.J., WELSCH, G., J. Am. Ceramic Society, Vol. 68-6, pp 320-325.
- . SERCOMBE, T.B., Mat. Science & Eng A 341, pp 163-168.
- . BONDYKE, K.J., and DUDAS, J.H. United States Patent 3,796,566, June 1972.
9. 저작권:
- 본 자료는 "A. Mwamba, L.H. Chown and R. Süss"의 논문입니다. "Development of Platinum-Base Superalloy Components via Powder Metallurgy"를 기반으로 합니다.
- 논문 출처: 논문에 DOI가 제공되지 않음.
본 자료는 위 논문을 바탕으로 요약되었으며, 상업적 목적의 무단 사용을 금합니다.
Copyright © 2025 CASTMAN. All rights reserved.
논문 요약:
연구에 대한 주요 질문과 답변:
본 연구는 주조성이 낮은 백금 기반 초합금(Pt₈₄:Al₁₁:Cr₃Ru₂)을 분말 야금법을 이용하여 개발하고자 하였으며, 예비 합금 수분사 분말과 기계적 합금 분말을 비교하였습니다. 연구 결과, 두 방법 모두 합금 분말을 생산할 수 있었으나, 예비 합금 경로는 산화물 오염으로 인해 소결성이 좋지 않았던 반면, 기계적 합금 경로는 낮은 생밀도에도 불구하고 더 나은 소결 반응을 보였습니다. Pt₃Al 석출물을 포함하는 미세 구조가 얻어졌으며, 예비 합금 압축체의 경도 값은 주조 합금과 유사했으나, 기계적 합금 압축체는 경도가 낮았지만 시효 처리를 통해 크게 향상되었습니다.
Q1. Pt₈₄:Al₁₁:Cr₃Ru₂ 합금 분말 생산을 위해 조사된 두 가지 분말 야금 방법은 무엇이었습니까?
A1. 두 가지 방법은 다음과 같습니다: 1) 백금 스펀지와 원소 분말을 용해하여 예비 합금을 만든 후 수분사하는 방법, 2) 수분사된 순수 백금 분말과 알루미늄, 크롬, 루테늄 원소 분말을 기계적으로 합금하는 방법. [초록; 실험 절차]
Q2. 예비 합금 백금 분말의 소결 품질에 영향을 미치는 주요 문제는 무엇이었습니까?
A2. 주요 문제는 예비 합금 분말 입자 표면에 존재하는 불연속적인 산화알루미늄 층으로, 이는 용융물 내 알루미늄이 공기 및/또는 물의 산소와 반응하여 분사 중에 형성된 것이며, 소결 중 양호한 결합을 방해했습니다. [결론 1; 소결 압축체의 미세 구조]
Q3. 기계적 합금 분말은 예비 합금 분말과 비교하여 압축 및 소결에 어떻게 반응했습니까?
A3. 기계적 합금 분말은 낮은 겉보기 밀도와 가공 경화로 인해 압축에 대한 반응은 좋지 않았지만(낮은 생밀도), 밀도가 크게 증가하는 등 소결에 대한 반응은 좋았습니다. [분말 압축 및 소결 반응; 결론 2]
Q4. 두 분말 경로에서 얻은 소결 압축체에서 관찰된 일반적인 미세 구조는 무엇이었습니까?
A4. 두 경로에서 얻은 소결 압축체는 일반적으로 다양한 크기와 형태의 Pt₃Al 석출물을 가진 백금 고용체 매트릭스로 구성되었습니다. [소결 압축체의 미세 구조; 결론 1, 2]
Q5. 소결된 분말 야금 압축체의 경도는 동일 조성의 주조 합금과 비교하여 어떠했습니까?
A5. 소결된 예비 합금 압축체의 경도는 주조 합금 범위(300-400 HV₁₀) 내에 있었던 반면, 기계적 합금 압축체의 경도는 주로 사용된 낮은 압축 압력으로 인해 더 낮았지만, 시효 처리를 통해 상당히 증가했습니다. [소결 압축체의 경도; 결론 1, 2]
Q6. 기계적 합금 압축체 시편을 1450°C에서 100시간 동안 시효 처리했을 때 어떤 흥미로운 현상이 관찰되었습니까?
A6. 기계적 합금 압축체 시편을 1450°C에서 100시간 동안 시효 처리한 결과 액체가 형성되었으며, 이는 순수 백금의 융점보다 낮은 온도에서 액상 소결이 가능할 수 있음을 나타냅니다. [소결 압축체의 미세 구조]