본 기사에서는 [MDPI Materials]에서 발행한 논문 [Combining Structural Optimization and Process Assurance in Implicit Modelling for Casting Parts]을 소개합니다.
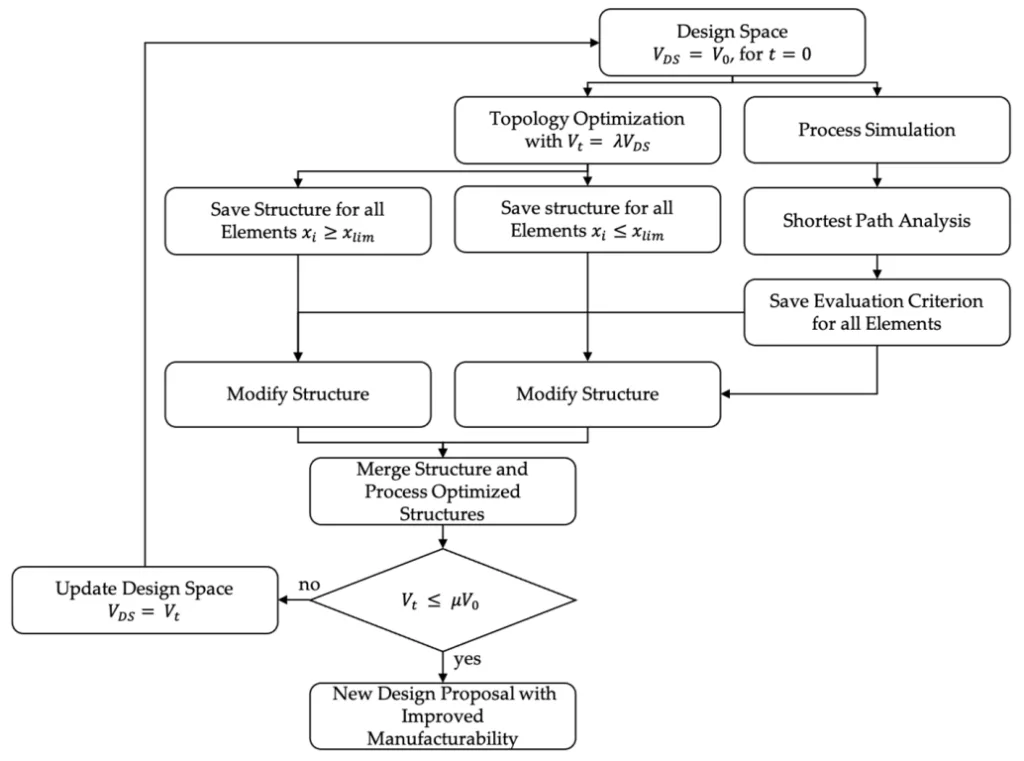
1. 개요:
- 제목: 주조 부품의 암시적 모델링에서 구조 최적화와 공정 보증 결합
- 저자: 토비아스 로스니체크, 막시밀리안 에르버, 크리스토프 하트만, 볼프람 폴크, 프랑크 리크, 스테판 트렘멜
- 출판 연도: 2021년
- 출판 저널/학회: Materials
- 키워드: 다이캐스팅; 암시적 모델링; 공정 보증; 구조 최적화; 가상 제품 개발
2. 초록 또는 서론
제조 가능한 주조 부품의 구조 최적화는 여전히 어렵고 시간이 많이 걸리는 과제입니다. 오늘날, 위상 최적화 후 설계 제안의 수동 재구성 및 설계 제안을 보증하기 위한 공정 보증 시뮬레이션이 이어집니다. 결과적으로 이 프로세스는 만족스러운 절충안에 도달할 때까지 반복적으로 반복됩니다. 본 논문에서는 암시적 형상 모델링을 사용하여 구조 및 공정 최적화된 다이캐스팅 부품을 자동으로 생성하기 위해 구조 최적화와 공정 보증 결과를 결합하는 방법을 제시합니다. 따라서 현재 설계 제안을 평가하고 두 반복 간의 제조 가능성 개선을 정량적으로 측정하기 위한 평가 기준이 개발되었습니다. 제안된 방법론을 테스트하기 위해 캔틸레버 빔을 증명 예시로 사용합니다. 결합된 반복 방법은 수동 설계 부품 및 직접 최적화 접근 방식과 비교하여 기계적 성능 및 제조 가능성에 대해 평가되었습니다. 위상 최적화(TO)와 공정 보증(PA) 결과의 조합은 자동화되어 설계 제안의 수동 재구성에 상당한 향상을 보여줍니다. 또한 제조 가능성의 개선은 기존 연구와 동등하거나 더 나은 반면, 더 적은 계산 노력을 사용하여 더 짧은 반복 시간을 가능하게 하는 적절한 메타 모델의 필요성을 강조합니다.
3. 연구 배경:
연구 주제의 배경:
오늘날의 제품 개발은 짧은 시장 출시 시간과 오류를 최소화한 제품 설계를 요구합니다. 따라서 최적화된 공정 설계는 제조 비용과 불량률을 줄이므로 부품은 구조적으로 최적화되고 공정 최적화되어야 합니다. 그러나 이러한 최적화 작업은 시간이 많이 걸리고 높은 수준의 전문 지식이 필요하며 여러 수동 작업 단계를 통해 결과를 결합합니다. 결과적으로 주조 부품의 구조 최적화와 공정 보증을 결합하는 디지털 엔지니어링에는 막대한 잠재력이 있습니다.
기존 연구 현황:
기본적으로 구조 및 공정 최적화는 두 개의 전문 부서 간에 공유되며, 각 부서는 부품을 반복적으로 서로 전달합니다. 각 부서는 해당 공정에 대해 얻은 파일을 준비해야 하며, 그 후 최적화 결과를 기반으로 수동으로 새로운 부품을 재설계해야 합니다. 이 프로세스는 만족스러운 절충안에 도달할 때까지 반복됩니다. 주조 부품의 구조 최적화에 대한 기존 연구에는 최소 형상 크기, 대칭 및 압출과 같은 제조 제약 조건이 있는 위상 최적화(TO)가 포함됩니다. 공정 시뮬레이션은 알려진 형상의 금형 또는 인게이트 시스템을 최적화하는 데 사용됩니다. 공정 지식은 제조 제한을 통해 상용 TO에 통합되지만, 공정 지식을 TO에 더 깊이 통합하는 것은 제한적입니다. 전체 규모의 주조 공정 시뮬레이션을 TO에 통합하는 기존 연구는 높은 반복 시간으로 인해 계산 비용이 많이 듭니다.
연구의 필요성:
문헌에는 HPDC(고압 다이캐스팅) 및 LPDC(저압 다이캐스팅)에 대한 형상 연동 평가 기준에 대한 격차가 있으며, 이는 TO 중에 공정 시뮬레이션의 필요성을 잠재적으로 줄이면서도 여전히 충분한 제조 가능성 정보를 보여줄 수 있습니다. 설계 형상을 수정하기 위한 평가 기준을 조사하고 전체 프로세스를 완전히 자율적으로 자동화하기 위한 추가 연구가 필요합니다. 본 논문에서는 인게이트 시스템 수정은 제외하고 부품 형상 수정에만 초점을 맞춥니다.
4. 연구 목적 및 연구 질문:
연구 목적:
본 연구의 목적은 TO 및 PA 결과를 자동으로 결합하여 구조 및 공정 최적화된 설계 제안을 생성하는 새로운 워크플로를 제시하는 것입니다. 주조 공정 기반 기준에 따라 구조적으로 최적화된 형상은 암시적 모델링을 통해 수정되어 제조 가능성을 향상시킵니다. 장기적인 목표는 개발된 기준을 평가하기 위해 주조 공정 시뮬레이션을 메타 모델로 대체하는 것입니다.
핵심 연구:
핵심 연구는 주조 공정에 대한 형상 연동 평가 기준의 기능성을 개발하고 입증하는 데 중점을 둡니다. 워크플로는 공정 지식을 주조 부품의 TO에 통합하고 암시적 모델링을 사용하여 TO 및 PA 결과를 결합합니다. PA의 경우 CFD 기반 공정 시뮬레이션 후 최단 경로 분석 및 평가 기준 계산이 사용됩니다.
연구 가설:
제안된 워크플로는 표준 TO 부품에 비해 제조 가능성이 향상된 새로운 설계 제안을 생성할 것입니다. TO와 PA의 조합은 구조 및 공정 최적화된 부품으로 이어질 것입니다.
5. 연구 방법론
연구 설계:
본 연구에서는 TO와 PA를 병렬로 수행한 다음 암시적 모델링 기술을 사용하여 각 방법의 최상의 요소를 결합하는 워크플로를 사용합니다. 단일 단계 최적화와 반복 최적화 접근 방식을 구별합니다. 워크플로는 HPDC 및 LPDC 공정 모두에 대해 테스트됩니다.
데이터 수집 방법:
TO의 경우 nTopology 소프트웨어(버전 3.0.4)와 SIMP를 사용한 밀도 기반 TO 방법이 사용됩니다. 공정 시뮬레이션은 FVM(유한 체적법) 및 VOF(유한 유한 요소법) 방법을 사용하여 Flow-3D(v5.0 업데이트 4) 소프트웨어를 사용하여 수행됩니다. 캔틸레버 빔이 벤치마크 예제로 사용됩니다.
분석 방법:
제조 가능성은 공정 시뮬레이션 결과에서 파생된 형상 연동 평가 기준을 사용하여 평가됩니다. HPDC의 경우 최초 유체 도달 시간(tffa)과 이론적 최단 경로 시간(tsp)의 수정된 몫(QuotHPDC)이 사용됩니다. LPDC의 경우 응고 시간(tsol)과 인게이트 레벨까지의 거리(h)의 로그 몫(QuotLPDC)이 사용됩니다. 구조적 성능은 유한 요소 해석에서 얻은 상대 체적 관련 강성(SVR)으로 평가됩니다. 평가 기준의 중앙값과 제조 가능한 요소의 수가 분석됩니다.
연구 대상 및 범위:
본 연구는 다이캐스팅 부품, 특히 HPDC 및 LPDC 공정을 사용하는 데 중점을 둡니다. 캔틸레버 빔 형상이 테스트 케이스로 사용됩니다. 본 연구에서는 단일 단계 및 반복 최적화 접근 방식을 조사하고 이를 단독 TO 및 수동 재설계 부품과 비교합니다.
6. 주요 연구 결과:
주요 연구 결과:
- 제안된 워크플로는 HPDC 및 LPDC 공정 모두에 대해 TO와 PA를 성공적으로 결합합니다.
- 암시적 모델링을 사용한 자동화된 후처리 워크플로는 공정 보증 기준에 따라 TO 형상을 효과적으로 수정합니다.
- HPDC의 경우 단일 단계 최적화(HPDC-OS)는 초기 설계 공간에 비해 159%의 제조 가능성 증가를 달성했으며, 반복 최적화(HPDC-IT)는 68%의 증가를 보였습니다.
- LPDC의 경우 단일 단계(LPDC-OS) 및 반복 최적화(LPDC-IT) 접근 방식 모두 단독 TO 설계에 비해 지향성 응고 경로와 향상된 제조 가능성을 갖는 설계 제안을 생성했습니다.
- HPDC-OS 설계 제안은 수동 설계된 HPDC-50과 제조 가능성이 비슷하고 구조적 성능에서 단독 위상 최적화 구성보다 뛰어났습니다.
- LPDC의 경우 두 최적화 접근 방식 모두 TO 구성과 유사한 상대 체적 관련 강성을 달성했습니다.
제시된 데이터 분석:
- 그림 17은 HPDC 설계에 대한 QuotHPDC의 중앙값을 보여주며, HPDC-OS가 가장 낮은 중앙값을 달성하여 HPDC-IT 및 참조 설계에 비해 제조 가능성이 더 우수함을 시사합니다.
- 그림 18은 HPDC 설계의 제조 가능성을 평가하여 HPDC-OS가 초기 설계 공간에 비해 제조 가능한 요소의 비율 증가가 가장 높음을 보여줍니다.
- 그림 21은 LPDC 설계에 대한 QuotLPDC의 중앙값을 나타내며, 반복 및 단일 단계 접근 방식에 대해 유사한 중앙값 값을 보여주지만 TO 설계에 대해서는 더 낮은 값을 보여줍니다.
- 그림 22는 LPDC 설계의 제조 가능성을 평가하여 TO 구성이 제안된 접근 방식에 비해 제조 가능한 요소의 수가 현저히 적음을 나타냅니다.
- 그림 23은 HPDC 설계에 대한 체적 관련 강성을 보여주며, TO 설계가 단일 단계 및 반복 접근 방식보다 성능이 우수하지만 HPDC-OS는 수동 설계된 HPDC-50과 비슷함을 보여줍니다.
- 그림 24는 LPDC 설계에 대한 체적 관련 강성을 나타내며, TO 구성을 포함한 모든 접근 방식에 대해 유사한 강성을 보여줍니다.
그림 목록:
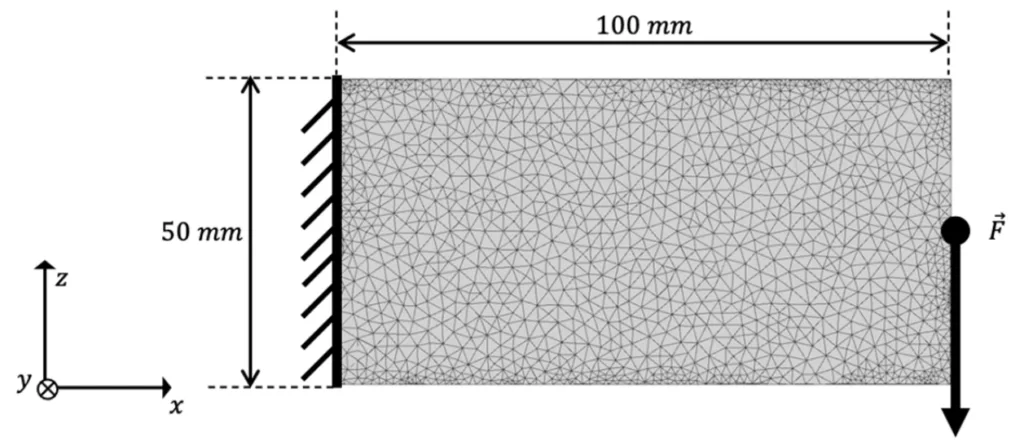
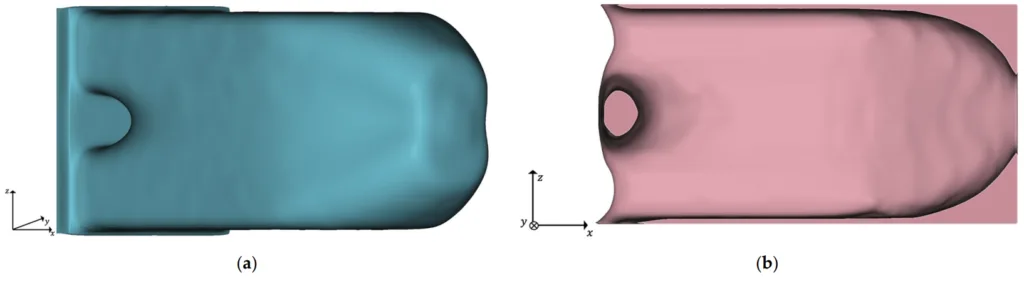
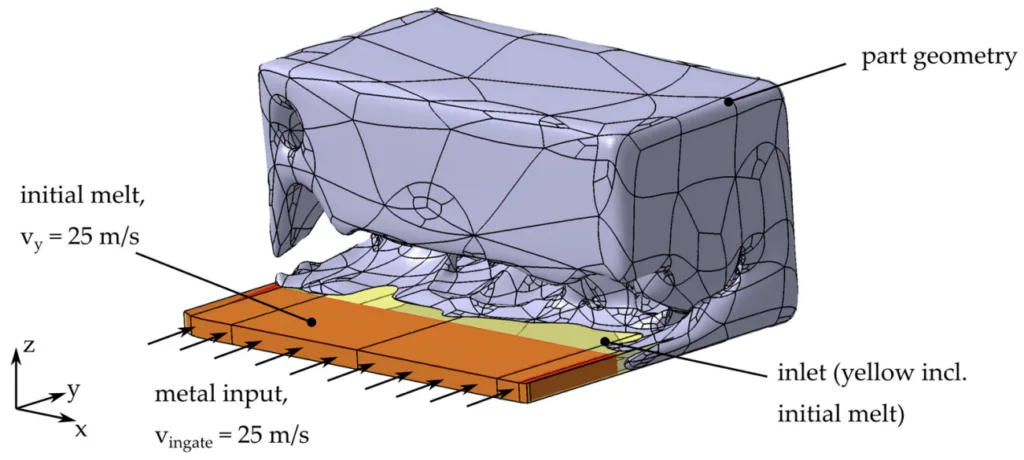
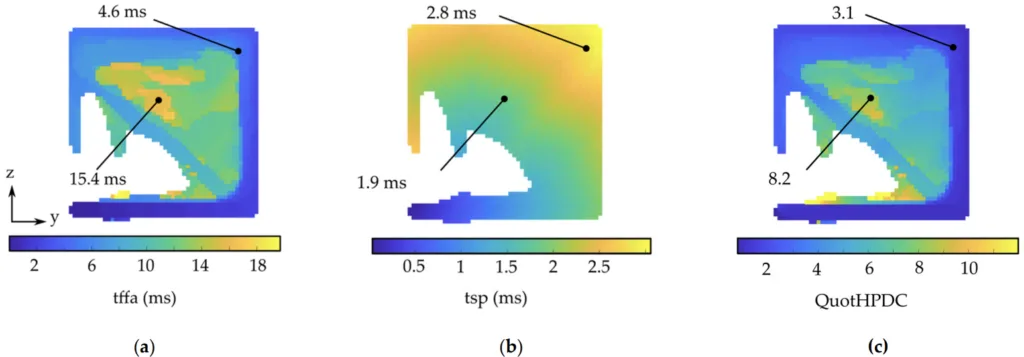
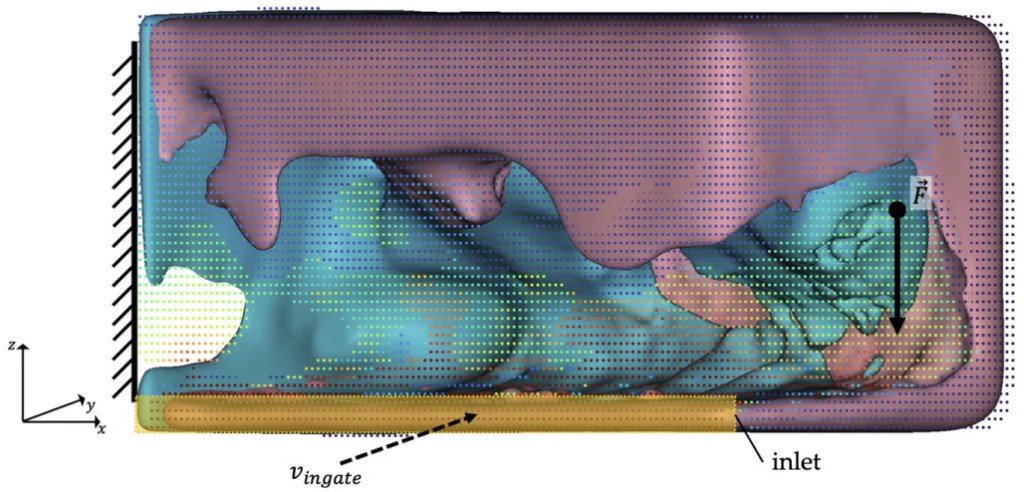
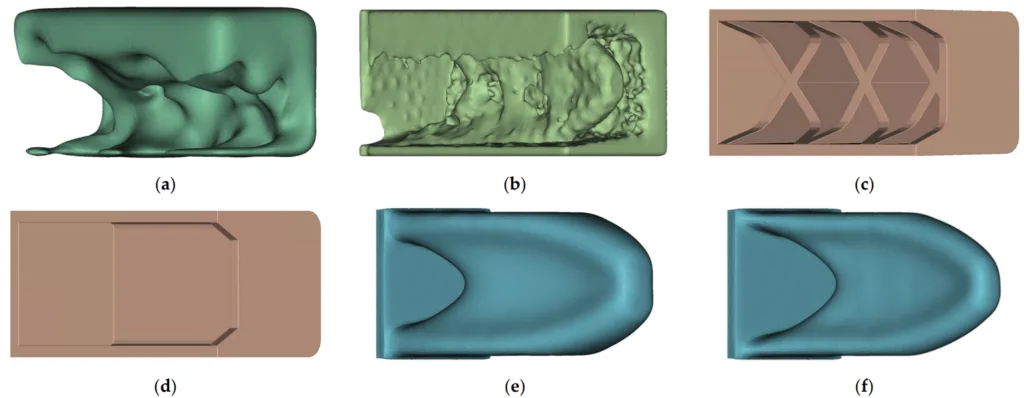
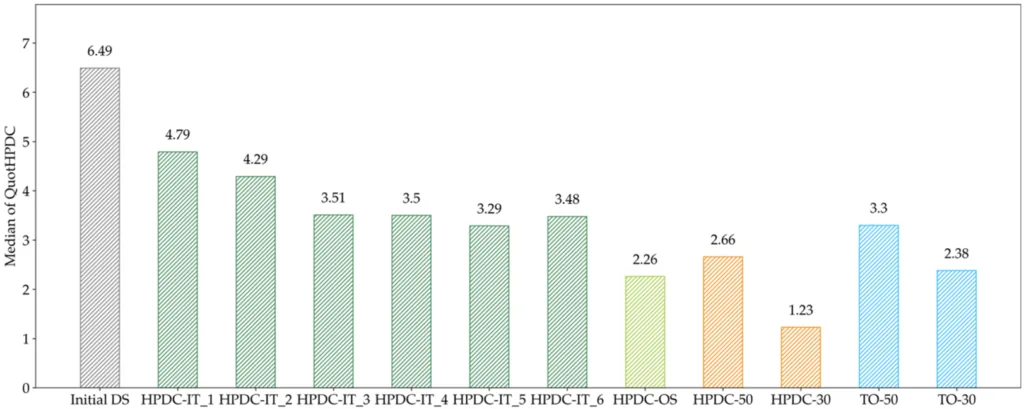
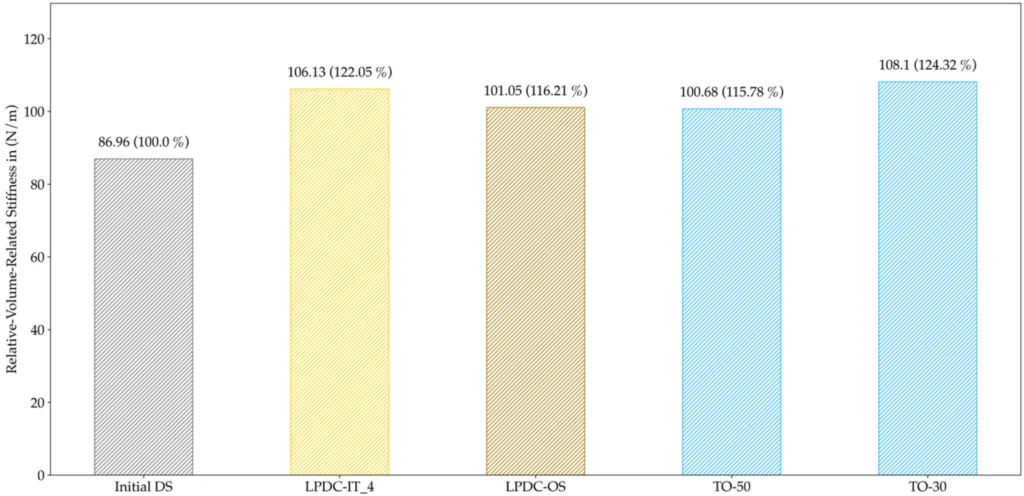
- 그림 1. 위상 최적화와 공정 보증의 조합을 위한 최적화의 제안된 워크플로.
- 그림 2. 벤치마크 예제로 사용된 캔틸레버 빔의 설정.
- 그림 3. λ = 0.2 및 xlim = 0.6인 초기 TO의 결과: (a) 최적화된 구조의 암시적 형상; (b) TO-마진의 암시적 형상의 단면.
- 그림 4. 반복 t = 2에 대해 예시적으로 표시된 HPDC의 시뮬레이션 설정.
- 그림 5. HPDC 공정의 충전 시뮬레이션 평가.
- 그림 6. 반복 t = 4에 대해 예시적으로 표시된 LPDC의 시뮬레이션 설정.
- 그림 7. 후처리 워크플로.
- 그림 8. 반복 고압 다이캐스팅 시뮬레이션에서 QuotHPDC에 대한 예시적인 점 지도, 반복 t = 2.
- 그림 9. 반복 HPDC 최적화의 예로 TO-마진의 적응형 메시 생성, 반복 t = 5.
- 그림 10. 반복 고압 주조 최적화의 예로 평활화 전 TO-마진의 암시적 체적 메시, 반복 t = 5.
- 그림 11. 반복 고압 주조 최적화의 예로 후처리 워크플로의 최종 결과, 반복 t = 5.
- 그림 12. 초기 설계 공간에 비해 체적이 50%인 HPDC-OS 최적화 결과.
- 그림 13. 초기 설계 공간에 비해 체적이 49%인 LPDC-OS 최적화 결과.
- 그림 14. λ = 0.2인 HPDC 부품의 반복 최적화의 각 반복 결과.
- 그림 15. λ = 0.2인 LPDC 부품의 반복 최적화의 각 반복 결과.
- 그림 16. 모든 HPDC 및 TO 설계 제안 비교.
- 그림 17. 모든 최적화된 형상에 대한 QuotHPDC의 중앙값 평가.
- 그림 18. HPDC 설계 제안의 제조 가능성 평가.
- 그림 19. 모든 LPDC 및 TO 설계 제안 비교: (a) LPDC-IT_4; (b) LPDC-OS; (c) TO-50; (d) TO-30.
- 그림 20. 중앙면을 따라 단면에 대한 응고 시간.
- 그림 21. LPDC 공정에서 조사된 모든 형상에 대한 QuotLPDC의 중앙값 평가.
- 그림 22. LPDC 설계 제안의 제조 가능성 평가.
- 그림 23. 모든 HPDC 구성에 대한 체적 관련 강성.
- 그림 24. 모든 LPDC 구성에 대한 체적 관련 강성.
7. 결론:
주요 연구 결과 요약:
본 연구에서는 암시적 모델링 및 형상 기반 평가 기준을 사용하여 TO와 PA를 결합하는 방법을 제시하여 새로운 설계 제안의 재구성을 자동화하고 주조 부품의 개발을 가속화했습니다. 이 접근 방식은 캔틸레버 빔에서 HPDC 및 LPDC 공정에 대해 검증되었으며, 단독 TO 설계에 비해 제조 가능성이 향상되었음을 입증했습니다. 단일 단계 최적화 접근 방식은 제조 가능성 및 구조적 성능 측면에서 HPDC에 대해 특히 유망한 결과를 보였습니다. LPDC의 경우 이 방법은 지향성 응고 경로를 용이하게 했습니다.
연구의 학문적 의의:
본 연구는 형상 연동 평가 기준에 대한 문헌의 격차를 해소하면서 공정 지식을 위상 최적화에 통합하는 새로운 워크플로를 기여합니다. TO 및 PA 결과의 자동화된 조합과 암시적 모델링의 사용은 주조를 위한 설계 최적화의 발전을 나타냅니다. 개발된 평가 기준(QuotHPDC 및 QuotLPDC)은 제조 가능성 평가를 위한 정량적 측정을 제공합니다.
실용적 의미:
자동화된 워크플로는 최적화된 주조 부품 개발에서 수동 재설계 노력과 시간을 크게 줄입니다. 이 방법을 통해 설계자는 공정 보증 준비가 완료된 구조 및 공정 최적화 설계를 생성하여 반복적인 설계 주기에서 시간을 절약할 수 있습니다. 이 접근 방식은 상용 TO 소프트웨어에 적용 가능하며 다양한 주조 공정에 적용할 수 있습니다.
연구의 한계 및 향후 연구 분야:
본 연구에서는 단계 길이와 설계 공간이 최적화 결과에 영향을 미치는 중요한 매개변수임을 확인하여 추가 조사가 필요합니다. 후처리에서의 평활화 매개변수 및 램프 설정도 향후 연구가 필요합니다. 시간 소모적인 공정 시뮬레이션을 대체할 메타 모델의 필요성은 매개변수 연구 및 전체 워크플로 성능의 효율성을 향상시키기 위한 향후 개발의 중요한 영역으로 강조됩니다. 향후 연구에서는 복잡한 LPDC 부품에 대한 원하는 응고 축을 설명하는 방법 개발과 다목적 최적화에서 제조 가능성과 구조적 성능 간의 절충점을 탐색하는 데 중점을 두어야 합니다.
8. 참고 문헌:
- [1] Hautsch, S.; Heilmeier, F.; Rieg, F.; Volk, W. Effiziente Entwicklung von prozessoptimalen druckgussbauteilen durch kombination von topologieoptimierung und prozesssimulation. In Stuttgarter Symposium für Produktentwicklung SSP17; Binz, H., Bertsche, B., Spath, D., Roth, D., Eds.; Fraunhofer-Institut für Arbeitswirtschaft und Organisation IAO: Stuttgart, Germany, 2017.
- [2] Heilmeier, F.; Goller, D.; Opritescu, D.; Thoma, C.; Rieg, F.; Volk, W. Support for Ingate Design by Analysing the Geometry of High Pressure Die Cast Geometries Using Dijkstra's Shortest Path Algorithm. Adv. Mater. Res. 2016, 1140, 400-407. [CrossRef]
- [3] Franke, T.; Fiebig, S.; Paul, K.; Vietor, T.; Sellschopp, J. Topology optimization with integrated casting simulation and parallel manufacturing process improvement. In Advances in Structural and Multidisciplinary Optimization; Schumacher, A., Vietor, T., Fiebig, S., Bletzinger, K.-U., Maute, K., Eds.; Springer International Publishing: Basel, Switzerland, 2018; ISBN 978-3-319-67987-7.
- [4] Franke, T.; Fiebig, S.; Bartz, R.; Vietor, T.; Hage, J.; vom Hofe, A. Adaptive Topology and Shape Optimization with Integrated Casting Simulation. In EngOpt 2018, Proceedings of the 6th International Conference on Engineering Optimization, Braunschweig, Germany, 5–9 June 2017; Rodrigues, H.C., Herskovits, J., Mota Soares, C.M., Araújo, A.L., Guedes, J.M., Folgado, J.O., Moleiro, F., Madeira, J.F.A., Eds.; Springer International Publishing: Basel, Switzerland, 2019; ISBN 978-3-319-97772-0.
- [5] Glamsch, J.; Deese, K.; Rieg, F. Methods for Increased Efficiency of FEM-Based Topology Optimization. Int. J. Simul. Model. 2019, 18, 453-463. [CrossRef]
- [6] Harzheim, L. Strukturoptimierung Grundlagen und Anwendung, 3rd ed.; Europa-Lehrmittel: Haan-Gruiten, Germany, 2019.
- [7] Rosnitschek, T.; Hentschel, R.; Siegel, T.; Kleinschrodt, C.; Zimmermann, M.; Alber-Laukant, B.; Rieg, F. Optimized One-Click Development for Topology-Optimized Structures. Appl. Sci. 2021, 11, 2400. [CrossRef]
- [8] Harzheim, L.; Graf, G. A Review of Optimization of Cast Parts Using Topology Optimization: I—Topology Optimization without Manufacturing Constraints. Struct. Multidisc. Optim. 2005, 30, 491-497. [CrossRef]
- [9] Harzheim, L.; Graf, G. A Review of Optimization of Cast Parts Using Topology Optimization: II—Topology Optimization with Manufacturing Constraints. Struct. Multidisc. Optim. 2006, 31, 388-399. [CrossRef]
- [10] Vatanabe, S.L.; Lippi, T.N.; de Lima, C.R.; Paulino, G.H.; Silva, E.C.N. Topology Optimization with Manufacturing Constraints: A Unified Projection-Based Approach. Adv. Eng. Softw. 2016, 100, 97-112. [CrossRef]
- [11] Gersborg, A.R.; Andreasen, C.S. An Explicit Parameterization for Casting Constraints in Gradient Driven Topology Optimization. Struct. Multidisc. Optim. 2011, 44, 875-881. [CrossRef]
- [12] Sato, Y.; Yamada, T.; Izui, K.; Nishiwaki, S. Manufacturability Evaluation for Molded Parts Using Fictitious Physical Models, and Its Application in Topology Optimization. Int. J. Adv. Manuf. Technol. 2017, 92, 1391-1409. [CrossRef]
- [13] Li, Q.; Chen, W.; Liu, S.; Fan, H. Topology Optimization Design of Cast Parts Based on Virtual Temperature Method. Comput. Aided Des. 2018, 94, 28-40. [CrossRef]
- [14] Wang, Y.; Kang, Z. Structural Shape and Topology Optimization of Cast Parts Using Level Set Method: Structural Shape and Topology Optimization of Cast Parts Using Level Set Method. Int. J. Numer. Meth. Eng. 2017, 111, 1252–1273. [CrossRef]
- [15] Xu, B.; Han, Y.S.; Zhao, L.; Xie, Y.M. Topology Optimization of Continuum Structures for Natural Frequencies Considering Casting Constraints. Eng. Optim. 2019, 51, 941-960. [CrossRef]
- [16] Nogowizin, B. Theorie und Praxis des Druckgusses; Schiele & Schön: Berlin, Germany, 2011.
- [17] Cuesta, R.; Delgado, A.; Maroto, A.; Mozo, D. Numerically modeling oxide entrainment in the filling of castings: The effect of the webber number. J. Oper. Manag. 2006, 58, 62–65. [CrossRef]
- [18] Kwon, H.-J.; Kwon, H.-K. Computer Aided Engineering (CAE) Simulation for the Design Optimization of Gate System on High Pressure Die Casting (HPDC) Process. Robot. Comput. Integr. Manuf. 2019, 55, 147-153. [CrossRef]
- [19] Dou, K.; Lordan, E.; Zhang, Y.J.; Jacot, A.; Fan, Z.Y. A Complete Computer Aided Engineering (CAE) Modelling and Optimization of High Pressure Die Casting (HPDC) Process. J. Manuf. Process. 2020, 60, 435-446. [CrossRef]
- [20] Mehtedi, M.E.; Mancia, T.; Buonadonna, P.; Guzzini, L.; Santini, E.; Forcellese, A. Design Optimization of Gate System on High Pressure Die Casting of AlSi13Fe Alloy by Means of Finite Element Simulations. Procedia CIRP 2020, 88, 509-514. [CrossRef]
- [21] Shahane, S.; Aluru, N.; Ferreira, P.; Kapoor, S.G.; Vanka, S.P. Finite Volume Simulation Framework for Die Casting with Uncertainty Quantification. Appl. Math. Model. 2019, 74, 132-150. [CrossRef]
- [22] Hirt, C.W.; Nichols, B.D. Volume of fluid (VOF) method for the dynamics of free boundaries. J. Comput. Phys. 1981, 39, 201-225. [CrossRef]
- [23] Cleary, P.; Ha, J.; Alguine, V.; Nguyen, T. Flow modelling in casting processes. Appl. Math. Model. 2002, 26, 171-190. [CrossRef]
- [24] Dabade, U.A.; Bhedasgaonkar, R.C. Casting Defect Analysis using Design of Experiments (DoE) and Computer Aided Casting Simulation Technique. Procedia CIRP 2013, 7, 616-621. [CrossRef]
- [25] Hahn, I.; Sturm, J. Von der Simulation zur gießtechnischen Optimierung. Giesserei 2015, 102, 86–100.
- [26] Hahn, I.; Sturm, J. Autonomous optimization of casting processes and designs. In Proceedings of the World Foundry Congress, Hangzhou, China, 16–20 October 2010; pp. 16-20.
- [27] Jadhav, A.R.; Hujare, D.P.; Hujare, P.P. Design and Optimization of Gating System, Modification of Cooling System Position and Flow Simulation for Cold Chamber High Pressure Die Casting Machine. Mater. Today Proc. 2021, S2214785320389598. [CrossRef]
- [28] Pinto, H.A.; Silva, F.J.G.; Martinho, R.P.; Campilho, R.D.S.G.; Pinto, A.G. Improvement and Validation of Zamak Die Casting Moulds. Procedia Manuf. 2019, 38, 1547–1557. [CrossRef]
- [29] Shahane, S.; Aluru, N.; Ferreira, P.; Kapoor, S.G.; Vanka, S.P. Optimization of Solidification in Die Casting Using Numerical Simulations and Machine Learning. J. Manuf. Process. 2020, 51, 130-141. [CrossRef]
- [30] Liu, J.; Ma, Y. A Survey of Manufacturing Oriented Topology Optimization Methods. Adv. Eng. Softw. 2016, 100, 161–175. [CrossRef]
- [31] Dijkstra, E.W. A note on two problems in connexion with graphs. Numer. Math. 1959, 1, 269-271. [CrossRef]
- [32] OPTIMAT: Entwicklung und Validierung von Softwaretools zur Simulation des Betriebsverhaltens von Werkstoffen in thermisch und Mechanisch Hoch Belasteten Komponenten, Arbeitsanteil NEMAK Wernigerode GmbH: Abschlussbericht, Berichtszeitraum: 1 May 2007–31 October 2010. Werkstoffinnovation für Industrie und Gesellschaft—WING: 2010. Available online: https://www.tib.eu/de/suchen?tx_tibsearch_search%5Baction%5D=download&tx_tibsearch_search%5Bcontroller%5D=Download&tx_tibsearch_search%5Bdocid%5D=TIBKAT%3A717891933&cHash=74e07aebe8553baac3ac1f2580585d68#download-mark (accessed on 1 July 2021).
- [33] Majernik, J.; Gaspar, S.; Kmec, J.; Karkova, M.; Mascenik, J. Possibility of Utilization of Gate Geometry to Modify the Mechanical and Structural Properties of Castings on the Al-Si Basis. Materials 2020, 13, 3539. [CrossRef]
- [34] nTopology's Implicit Modeling Technology. Available online: https://ntopology.com/resources/whitepaper-implicit-modeling-technology/ (accessed on 25 April 2021).
9. 저작권:
- 이 자료는 "[Copyright: 2021 by the authors.]"의 논문: "[주조 부품의 암시적 모델링에서 구조 최적화와 공정 보증 결합]"을 기반으로 합니다.
- 논문 출처: https://doi.org/10.3390/ma14133715
본 자료는 위 논문을 소개하기 위해 제작되었으며, 상업적 목적으로 무단 사용하는 것을 금지합니다.
Copyright © 2025 CASTMAN. All rights reserved.