본 논문 요약은 [Publisher]에 발표된 논문 A COMPARATIVE ANALYSIS ON ORGANIC AND INORGANIC CORE BINDERS FOR A GRAVITY DIECASTING AL ALLOY COMPONENT를 기반으로 작성되었습니다.
1. 개요:
- 제목: 중력 다이캐스팅 Al 합금 부품용 유기 및 무기 코어 바인더의 비교 분석 (A COMPARATIVE ANALYSIS ON ORGANIC AND INORGANIC CORE BINDERS FOR A GRAVITY DIECASTING AL ALLOY COMPONENT)
- 저자: A. Fortini, M. Merlin, G. Raminella
- 발행 연도: 2022년
- 발행 저널/학회: International Journal of Metalcasting
- 키워드: 모래 코어, 광학 측정, 중력 다이캐스팅, 수분 흡수 시험, 저장 안정성 (sand cores, optical measurement, gravity diecasting, moisture absorption tests, storage stability)
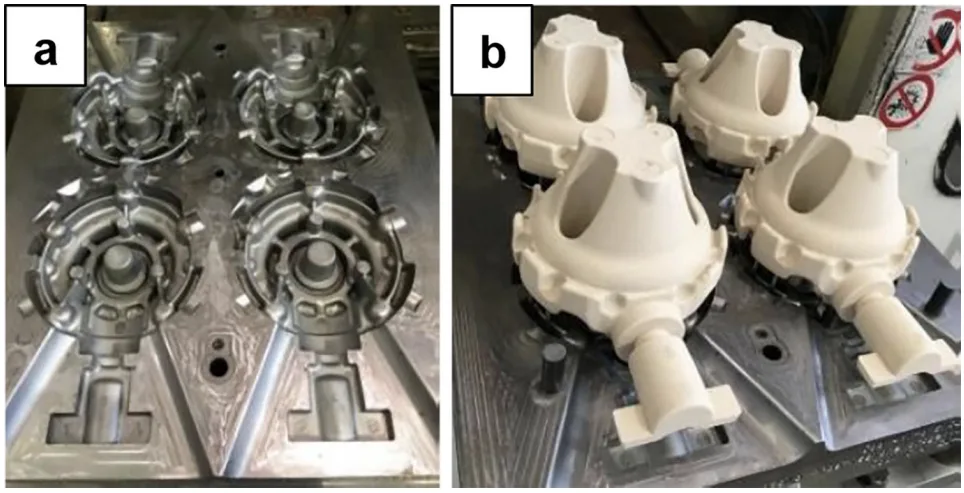
2. 연구 배경:
금속 주조 분야에서 코어 제작에 무기 바인더를 사용하는 추세가 지난 20년간 증가해 왔습니다. 무기 바인더는 기존 유기 바인더에 비해 건강 및 환경적 이점이 있지만, 상업적 용도로 널리 사용되기 위해서는 저장 안정성과 관련된 잠재적인 내재적 한계를 해결하기 위한 지속적인 기술 개선이 필요합니다. 무기 코어는 저장 안정성이 떨어질 수 있다는 점을 고려하여, 본 연구는 무기 코어 바인더가 중력 다이캐스팅 Al 합금 부품 생산에서 유기 코어를 대체할 수 있는지 확인하고자 합니다. 기존 연구는 이러한 바인더 시스템의 실제 주조 환경에서의 적용 및 성능, 특히 수분 흡수의 영향에 대한 연구가 부족했습니다. 본 연구는 이러한 격차를 해소하기 위해 실제 주조 공장 보관 조건에서 수분 민감성에 초점을 맞춰 유기 코어를 대체할 수 있는 무기 코어 바인더의 타당성을 평가합니다.
3. 연구 목적 및 연구 질문:
본 연구는 알루미늄 합금 부품의 중력 다이캐스팅 맥락에서 유기 및 무기 코어 바인더의 성능을 평가하고 비교하는 것을 목표로 합니다. 특히, 수분 흡수가 코어 안정성에 미치는 영향과 최종 주조 품질에 미치는 영향을 조사합니다.
본 논문에서 다루는 주요 연구 질문은 다음과 같습니다:
- 무기 코어 바인더는 중력 다이캐스팅 알루미늄 합금 부품 생산에서 유기 코어 바인더를 효과적으로 대체할 수 있는가?
- 주조 공장 보관 중 수분 흡수가 유기 코어와 비교하여 무기 코어의 치수 안정성 및 구조적 무결성에 어떤 영향을 미치는가?
- 유기 코어와 무기 코어를 사용하여 생산된 알루미늄 합금 주물의 기계적 특성 및 미세 구조의 차이점은 무엇인가?
- 유기 코어와 무기 코어를 사용할 때 주조 공정 중 발생하는 유해 배출물의 상대적 수준은 어떠한가?
본 연구의 기본 가설은 무기 코어가 환경적 이점을 제공하지만, 수분 민감성이 실제 주조 공장 적용에 어려움을 초래할 수 있다는 것입니다. 본 연구는 이러한 어려움을 정량화하고 유기 코어를 대체할 수 있는 지속 가능한 대안으로서 무기 코어의 전반적인 실행 가능성을 평가하고자 합니다.
4. 연구 방법론
본 연구는 유기 및 무기 코어 바인더를 평가하기 위해 비교 실험 연구 설계를 채택했습니다. 연구 방법론은 다음과 같은 주요 단계를 포함합니다:
- 연구 설계: 페놀 우레탄 콜드 박스 공정을 사용하여 생산된 유기 코어와 상업용 소듐 실리케이트 기반 Cordis 바인더 시스템으로 제작된 무기 코어를 대조하는 비교 분석을 수행했습니다.
- 데이터 수집 방법:
- 수분 흡수 시험: 모래 샘플과 완성된 코어를 다양한 습도 조건에 노출시켰습니다. 점화 손실에 따른 중량 감소 및 제어된 습도 환경(40°C 및 상대 습도 100%의 항온항습 챔버, 주조 공장 창고 조건)에서의 중량 증가를 측정하여 수분 민감도를 평가했습니다.
- 3D 광학 측정: 수분 흡수로 인한 무기 코어의 치수 변화를 GOM Atos ScanBox 4105 광학 3D 측정 장비를 사용하여 CAD 모델과 비교하여 정밀하게 측정했습니다.
- 주조 시험: A356 알루미늄 합금과 유기 및 무기 코어를 모두 사용하여 구동계 오토바이 부품을 생산하는 중력 다이캐스팅 시험을 수행했습니다.
- 기계적 시험: 주물의 인장 특성(항복 강도 Rp0.2, 인장 강도 Rm, 연신율 A%)을 Galdabini Quasar 50 시험기를 사용하여 평가했습니다.
- 미세 구조 분석: 이차 덴드라이트 암 간격(SDAS) 및 기공률을 ZEISS Axioscope 7 광학 현미경 및 Zen Core 2.7 이미지 분석 소프트웨어를 사용하여 분석했습니다.
- 배출물 분석: 주조 중 발생하는 기체 유기 화합물 배출물을 수집하고 UNI CEN/TS 13649 표준에 따라 가스 크로마토그래피 기술을 사용하여 분석했습니다. 주조 사이클 후 금형 캐비티 조건에 대한 육안 검사도 수행했습니다.
- 분석 방법: 중량 측정, 치수 편차, 인장 특성, SDAS, 기공률 및 배출 농도에 대한 정량적 데이터 분석을 수행했습니다. 모래, 코어 외관 및 금형 조건에 대한 육안 검사를 기반으로 질적 평가를 수행했습니다.
- 연구 대상 및 범위: 본 연구는 자동차 부품용 A356 알루미늄 합금 부품의 중력 다이캐스팅에 사용되는 모래 코어 생산을 위해 특정 유기 바인더 시스템(페놀 우레탄 콜드 박스)과 무기 바인더 시스템(소듐 실리케이트 기반 Cordis)을 비교하는 데 중점을 두었습니다. 범위는 주조 작업과 관련된 다양한 보관 습도 조건에서 코어 성능을 평가하는 것을 포함했습니다.
5. 주요 연구 결과:
실험 결과는 유기 및 무기 코어 바인더 성능에 대한 포괄적인 비교를 제공했습니다. 주요 결과는 다음과 같습니다:
- 수분 흡수:
- 중량 손실 (WL): 표 2는 코어 유형별 점화 손실에 따른 중량 손실을 보여줍니다. 유기 코어는 1.068-1.187%의 WL 값을 나타낸 반면, 무기 코어는 0.184-0.332%의 WL 값을 나타냈습니다. 유기 코어의 경우 WL 값에는 바인더 증발로 인한 약 1.06%가 포함되어 있습니다.
- 항온항습 챔버 내 수분 흡수 (MA): 그림 3은 무기 코어가 유기 코어에 비해 항온항습 챔버(40°C 및 상대 습도 100%)에서 수분 흡수 경향이 더 큰 것을 보여주며, 이는 더 높은 MA 백분율로 반영됩니다.
- 주조 공장 창고 내 수분 흡수: 그림 5b는 주조 공장 창고(18°C 및 상대 습도 32%)에서 보관하는 동안 무기 코어의 수분 흡수 증가가 14일 동안 무시할 수 있을 정도로 작았으며, MA가 0.191%에서 0.245%로 증가했음을 보여줍니다.
- 치수 안정성:
- 3D 광학 측정 결과, 무기 코어는 항온항습 챔버의 고습도 조건에서 치수 변화를 겪었으며(그림 7a, b), 과폭 편차가 0.3mm를 초과했습니다.
- 그러나 주조 공장 창고(18°C 및 상대 습도 32%)에서 14일 동안 보관한 후 무기 코어의 치수 편차는 최소화되어(그림 7c, d), 일반적인 주조 공장 보관 조건에서 치수 안정성을 나타냈습니다.
- 더 극단적인 모의 보관 조건(온도 범위 -8°C ~ 2°C, 상대 습도 80%)에서도 치수 변화는 제한적이었고 구조적으로 최대 48시간 동안 안정적이었습니다(그림 8).
- 주물의 기계적 특성:
- 인장 시험(그림 9) 결과, 유기 코어와 무기 코어로 생산된 주물 모두 항복 강도(Rp0.2) 및 인장 강도(Rm) 값이 유사했습니다.
- 무기 코어로 제작된 주물의 연신율(A%) 값은 유기 코어로 제작된 주물에 비해 평균적으로 약간 더 높고 분산이 적었습니다.
- 주물의 미세 구조:
- 미세 구조 분석(그림 10b) 결과, 무기 코어로 생산된 주물이 유기 코어(30-33 µm)에 비해 이차 덴드라이트 암 간격(SDAS) 값이 약간 더 낮아(22-27 µm) 더 미세한 미세 구조를 나타내는 것으로 나타났습니다.
- 기공률(표 3)은 두 코어 유형으로 생산된 주물 모두 유사하고 낮았습니다(0.08% 미만).
- 배출물 및 금형 상태:
- 배출물 분석(표 4) 결과, 무기 코어를 사용한 주조 시 유해 유기 화합물 배출 농도가 유기 코어에 비해 현저히 낮은 것으로 나타났습니다.
- 육안 검사(그림 11) 결과, 무기 코어를 사용한 금형 캐비티는 200 사이클 후에도 깨끗하게 유지되었으며, 유기 코어를 사용한 금형에서 관찰된 어두운 수지 코팅에 비해 잔류물이 최소화되었습니다.
그림 목록:
- 그림 1. 콜드 박스 공정에 의한 유기 코어 생산: (a) 하프 코어 박스, (b) 유기 코어.
- 그림 2. 수분 흡수 시험 중 모래 외관 이미지. 유기 코어: (a) 초기 조건, (b) 2시간 점화 손실 후, (c) 3시간 점화 손실 후, (d) 4시간 점화 손실 후. 무기 코어: (e) 초기 조건, (f) 1시간 점화 손실 후, (g) 2시간 점화 손실 후, (h) 3시간 점화 손실 후.
- 그림 3. 항온항습 챔버 내 보관 시간에 따른 유기 및 무기 코어의 MA(%) 막대 그래프.
- 그림 4. 항온항습 챔버 내 수분 흡수 시험 후 코어 이미지: (a) 60분 컨디셔닝 후 유기 코어, (b) 60분 컨디셔닝 후 무기 코어, (c) 및 (d) (b)의 무기 코어 파손.
- 그림 5. 주조 공장 창고 내 무기 코어의 수분 흡수 시험: (a) 코어 보관 조건 이미지, (b) 보관 시간에 따른 MA(%) 막대 그래프.
- 그림 6. 초기 조건에서 무기 코어의 3D 디지털 컬러 플롯: (a) 정면 및 (b) 후면 등각 뷰.
- 그림 7. 수분 흡수 후 무기 코어의 3D 디지털 컬러 플롯: (a) 정면 및 (b) 후면 등각 뷰 (항온항습 챔버에서 40°C 및 상대 습도 100%로 60분 보관 후), (c) 정면 및 (d) 후면 등각 뷰 (주조 공장 창고에서 18°C 및 상대 습도 32%로 14일 보관 후).
- 그림 8. 수분 흡수 후 무기 코어의 3D 디지털 컬러 플롯: (a) 정면 및 (b) 후면 등각 뷰 (주조 공장 포티코 아래에서 24시간 보관 후), (c) 정면 및 (d) 후면 등각 뷰 (주조 공장 포티코 아래에서 48시간 보관 후).
- 그림 9. 인장 특성에 대한 코어 바인더 시스템의 영향: (a) 인장 시편 위치, (b) 유기 코어를 사용한 주조 시험의 인장 특성, (c) 무기 코어를 사용한 주조 시험의 인장 특성.
- 그림 10. SDAS 값에 대한 코어 바인더 시스템의 영향: (a) 시편 위치, (b) 유기 및 무기 코어 위치별 SDAS 막대 그래프.
- 그림 11. 200 사이클 후 상부 금형 절반 이미지: (a) 유기 코어, (b) 무기 코어.
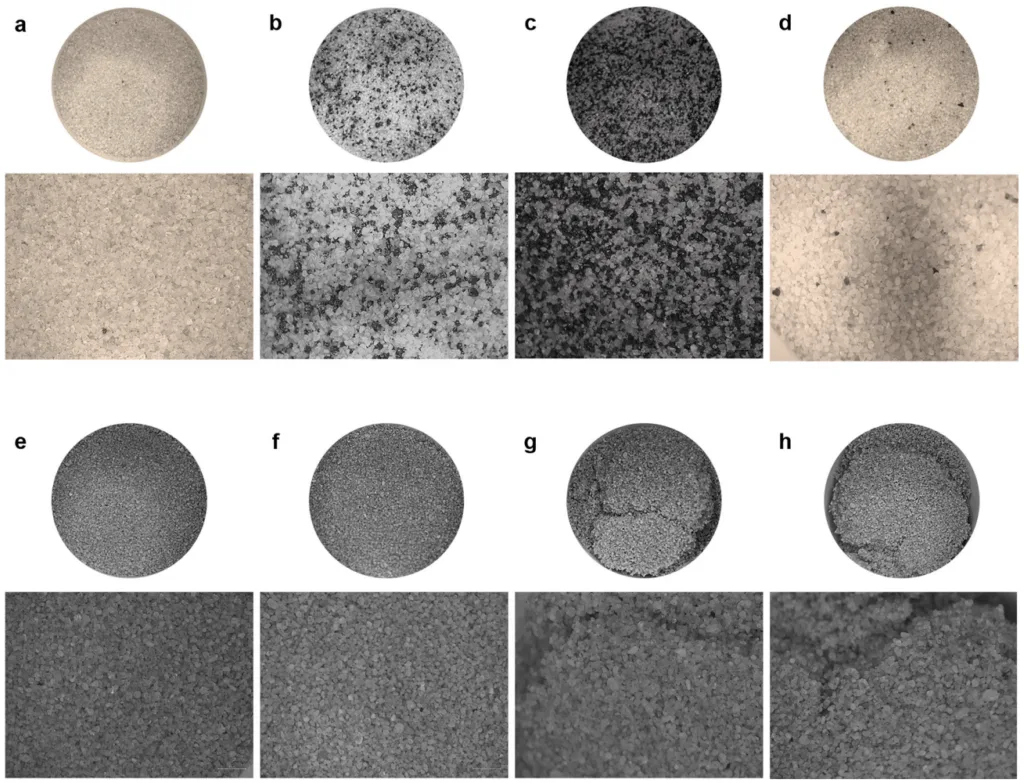
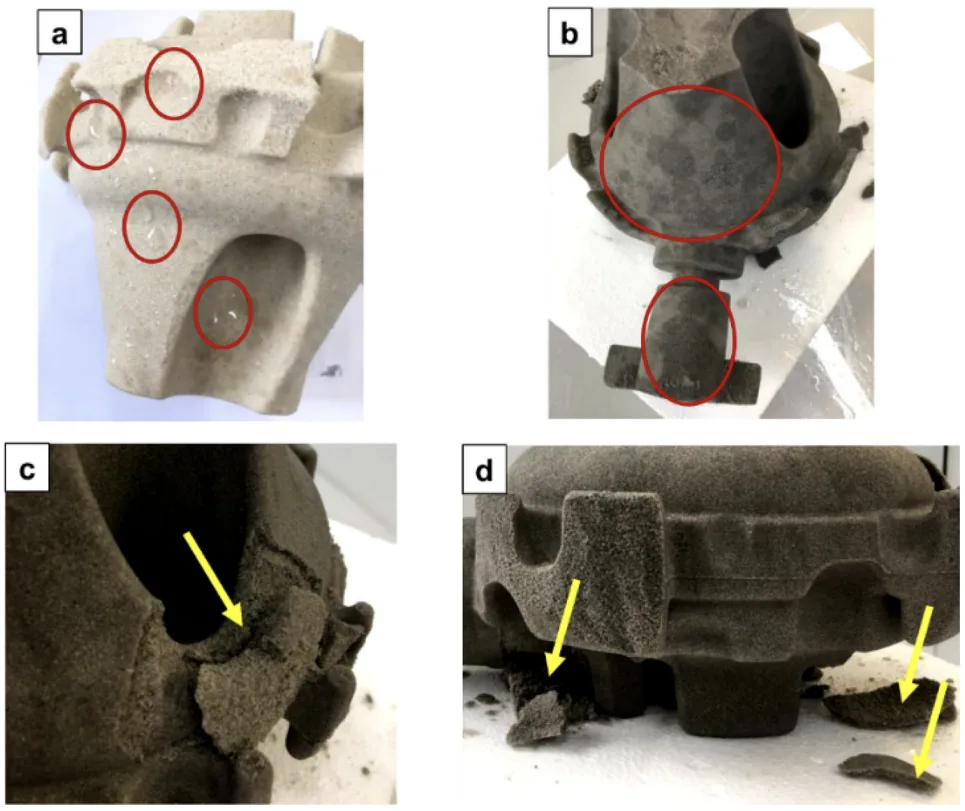
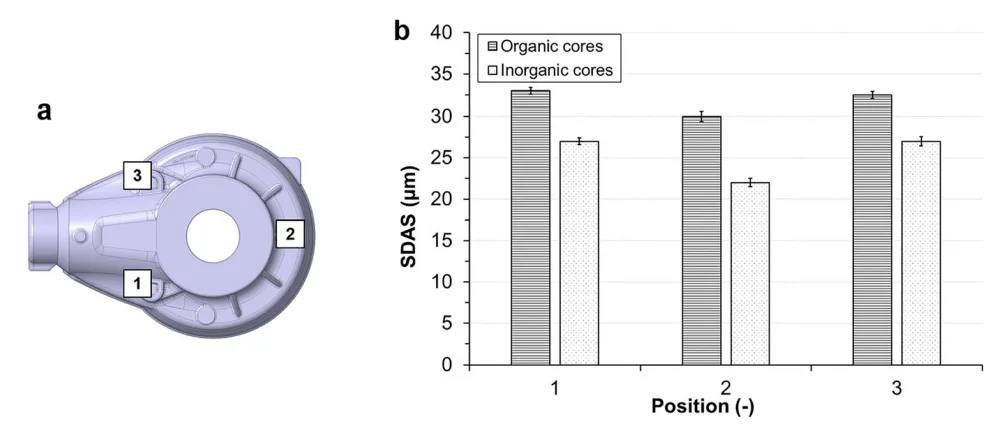
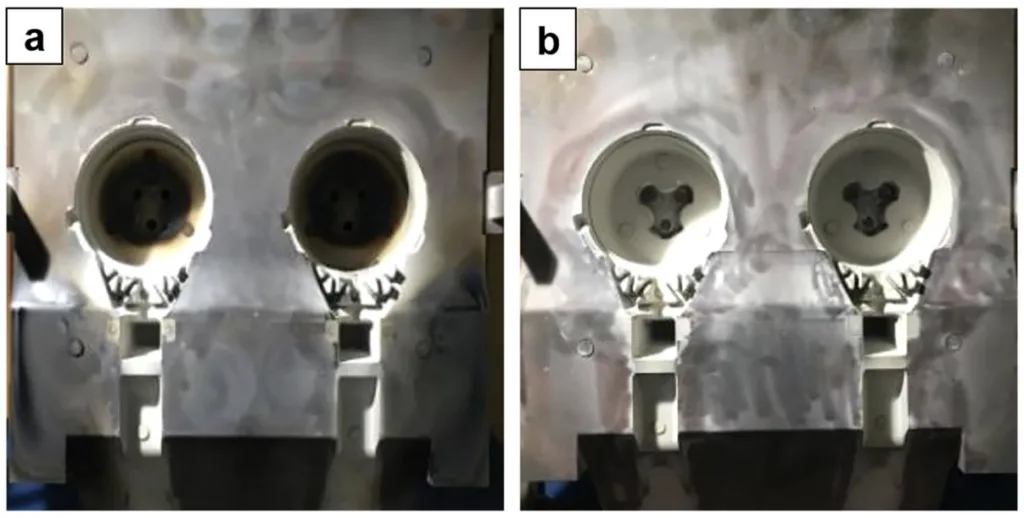
6. 결론 및 논의:
주요 결과 요약: 본 연구는 무기 코어 바인더, 특히 소듐 실리케이트 기반 시스템이 알루미늄 합금의 중력 다이캐스팅을 위한 기존 유기 바인더의 실행 가능한 대안임을 결론 내립니다. 무기 코어는 극심한 습도 조건에서 수분 흡수율이 더 높지만, 일반적인 주조 공장 창고 보관 조건(최대 14일)에서 충분한 안정성과 치수 무결성을 나타냅니다. 무기 코어로 생산된 주물은 유기 코어로 제작된 주물에 비해 기계적 특성이 유사하거나 약간 개선되었으며 미세 구조가 더 미세합니다. 결정적으로, 무기 코어는 주조 중 유해 가스 배출을 획기적으로 줄이고 확장된 주조 사이클 동안 금형 상태를 더 깨끗하게 유지함으로써 상당한 환경적 이점을 제공합니다.
연구의 학문적 의의: 본 연구는 금속 주조 분야의 무기 바인더에 대한 지식 기반을 확장하는 데 귀중한 경험적 데이터를 제공합니다. 수분 민감도에 대한 우려를 직접적으로 해결하고 중력 다이캐스팅에서 성공적인 주조 공장 적용에 대한 증거를 제공합니다. 본 연구는 무기 코어 시스템의 성능을 평가할 때 실제 주조 공장 보관 조건을 고려하는 것의 중요성을 강조합니다.
실용적 의미: 본 연구 결과는 주조 공장이 지속 가능성을 높이고 작업장 환경을 개선하기 위해 주조 품질 저하 없이 중력 다이캐스팅에 무기 코어 바인더를 자신 있게 채택할 수 있음을 강력히 시사합니다. 무기 코어와 관련된 배출 감소 및 금형 청결도는 환경 및 건강상의 이점뿐만 아니라 유지 보수 및 청소 감소를 통한 잠재적인 비용 절감으로 이어집니다. 본 연구는 무기 코어의 수분 관련 저장 불안정성에 대한 우려가 일반적인 주조 공장 관행, 특히 창고 조건에서 최대 14일의 보관 기간 내에서 관리 가능하다는 것을 시사합니다.
연구의 한계: 본 연구는 사용된 유기 및 무기 바인더 시스템의 정확한 조성에 대한 기밀성과 관련된 한계를 인정합니다. 또한, 주조 공장 창고 조건에서 14일 이상 무기 코어의 장기 저장 안정성은 광범위하게 조사되지 않았습니다.
7. 향후 후속 연구:
후속 연구 방향: 향후 연구는 무기 바인더의 조성을 더욱 최적화하여 고유한 내습성을 향상시키는 데 초점을 맞춰야 하며, 특정 첨가제 통합을 통해 잠재적으로 가능합니다.
추가 탐구가 필요한 영역: 더 넓은 범위의 주조 조건에서 무기 코어의 장기 보관 거동을 조사하고 중력 다이캐스팅 외에 다른 알루미늄 합금 및 주조 공정에서 성능을 평가하는 추가 탐구가 권장됩니다. 무기 코어와 관련된 금형 유지 보수 및 청소 감소의 경제적 이점을 조사하는 것도 향후 연구를 위한 가치 있는 영역이 될 것입니다.
8. 참고 문헌:
[1] F. Czerwinski, M. Mir, W. Kasprzak, Application of cores and binders in metalcasting. Int. J. Cast Met. Res. 28, 129-139 (2015). https://doi.org/10.1179/1743133614Y.0000000140
[2] A. Kmita, C. Fischer, K. Hodor, M. Holtzer, A. Roczniak, Thermal decomposition of foundry resins: a determination of organic products by thermogravimetry-gas chromatography-mass spectrometry (TG–GC-MS). Arab. J. Chem. 11, 380–387 (2018). https://doi.org/10.1016/j.arabjc.2016.11.003
[3] S.M. Glowacki, C.R. Crandell, G.R. Cannon, F.S. Clobes, J.K. Voigt, R.C. Furness, J.C. McComb, B.A. Knight, Emissions studies at a test foundry using an advanced oxidation-clear water system. AFS Trans. 111, 579-598 (2003)
[4] Y. Wang, F.S. Cannon, M. Salama, J. Goudzwaard, J.C. Furness, Characterization of hydrocarbon emissions from green sand foundry core binders by analytical pyrolysis. Environ. Sci. Technol. 41, 7922–7927 (2007). https://doi.org/10.1021/es0716570
[5] S.M. Dobosz, K. Major-Gabryś, A. Grabarczyk, New materials in the production of moulding and core sands. Arch. Foundry Eng. 15, 25–28 (2015). https://doi.org/10.1515/afe-2015-0073
[6] R. Ramakrishnan, B. Griebel, W. Volk, D. Günther, J. Günther, 3D printing of inorganic sand moulds for casting applications. Adv. Mater. Res. 1018, 441-449 (2014)
[7] H. Polzin, Inorganic Binders: For Mould and Core Production in the Foundry (Schiele & Schön, Berlin, 2014).
[8] P. Lechner, G. Fuchs, C. Hartmann, F. Steinlehner, F. Ettemeyer, W. Volk, Acoustical and optical determination of mechanical properties of inorganically-bound foundry core materials. Materials (Basel) 13, 2531 (2020). https://doi.org/10.3390/ma13112531
[9] B.J. Stauder, H. Kerber, P. Schumacher, Foundry sand core property assessment by 3-point bending test evaluation. J. Mater. Process. Technol. 237, 188-196 (2016). https://doi.org/10.1016/j.jmatprotec.2016.06.010
[10] B. Grabowska, S. Żymankowska-Kumon, S. Cukrowicz, K. Kaczmarska, A. Bobrowski, B. Tyliszczak, Thermoanalytical tests (TG-DTG-DSC, Py-GC/MS) of foundry binders on the example of polymer composition of poly(acrylic acid)-sodium carboxymethylcellulose. J. Therm. Anal. Calorim. 138, 4427-4436 (2019). https://doi.org/10.1007/s10973-019-08883-5
[11] B.J. Stauder, D. Gruber, P. Schumacher, Specific fracture energy and de-agglomeration rate of silicate-bonded foundry sand cores. Prod. Eng. 12, 807-816 (2018). https://doi.org/10.1007/s11740-018-0854-8
[12] H. Bargaoui, F. Azzouz, D. Thibault, G. Cailletaud, Thermomechanical behavior of resin bonded foundry sand cores during casting. J. Mater. Process. Technol. 246, 30-41 (2017). https://doi.org/10.1016/j.jmatprotec.2017.03.002
[13] C. Menet, P. Reynaud, G. Fantozzi, D. Thibault, A. Laforêt, Thermomechanical properties and fracture of resin-bonded-sand cores – experimental study and application in aluminium foundry. EPJ Web Conf. 140, 08006 (2017). https://doi.org/10.1051/epjconf/201714008006
[14] P. Lechner, J. Stahl, F. Ettemeyer, B. Himmel, B. Tananau-Blumenschein, W. Volk, Fracture statistics for inorganically-bound core materials. Materials (Basel) 11, 2306 (2018). https://doi.org/10.3390/ma11112306
[15] J.T. Fox, F.S. Cannon, N.R. Brown, H. Huang, J.C. Furness, Comparison of a new, green foundry binder with conventional foundry binders. Int. J. Adhes. Adhes. 34, 38–45 (2012). https://doi.org/10.1016/j.ijadhadh.2011.11.011
[16] A. Bobrowski, S. Żymankowska-Kumon, K. Kaczmarska, D. Drożyński, B. Grabowska, Studies on the gases emission of moulding and core sands with an inorganic binder containing a relaxation additive. Arch. Foundry Eng. (2020). https://doi.org/10.24425/afe.2020.131296
[17] K. Major-Gabryś, Environmentally friendly foundry molding and core sands. J. Mater. Eng. Perform. 28, 3905–3911 (2019). https://doi.org/10.1007/s11665-019-03947-x
[18] M. Holtzer, R. Dańko, A. Kmita, D. Drożyński, M. Kubecki, M. Skrzyński, A. Roczniak, Environmental impact of the reclaimed sand addition to molding sand with furan and phenol-formaldehyde resin—a comparison. Materials (Basel) 13, 4395 (2020). https://doi.org/10.3390/ma13194395
[19] Y.S. Zhang, L. Xia, J. Huang, Study on a new inorganic binder for fabricating casting mold and core. Adv. Mater. Res. 287–290, 1603–1606 (2011)
[20] W. Liu, T. Wang, Y. Li, Y. Ren, W. Huo, Preparation of a new animal glue binder for foundry use. China Foundry. 13, 238–242 (2016). https://doi.org/10.1007/s41230-016-6029-3
[21] K. Major-Gabrys, A. Grabarczyk, M. Dobosz, Modification of foundry binders by biodegradable material. Arch. Foundry Eng. 18, 31-34 (2018). https://doi.org/10.24425/122498
[22] I. Vasková, L. Varga, I. Prass, V. Dargai, M. Conev, M. Hrubovčáková, M. Bartošová, B. Bul'ko, P. Demeter, Examination of behavior from selected foundry sands with alkali silicate-based inorganic binders. Metals (Basel) 10, 235 (2020). https://doi.org/10.3390/met10020235
[23] L. Song, W. Liu, F. Xin, Y. Li, Effect of silica fume on humidity resistance of sodium silicate binder for core-making process. Int. J. Met. 14, 977–986 (2020). https://doi.org/10.1007/s40962-019-00405-1
[24] L. Zaretskiy, Modified silicate binders new developments and applications. Int. J. Met. 10, 88–99 (2016). https://doi.org/10.1007/s40962-015-0005-3
[25] J. Weise, J. Hilbers, F. Handels, D. Lehmhus, M. Busse, M. Heuser, New core technology for light metal casting. Adv. Eng. Mater. 21, 1800608 (2019). https://doi.org/10.1002/adem.201800608
[26] L. Zaretskiy, Hydrous solid silicates in new foundry binders. Int. J. Met. 12, 275–291 (2018). https://doi.org/10.1007/s40962-017-0155-6
[27] T. Sivarupan, M. El Mansori, N. Coniglio, M. Dargusch, Effect of process parameters on flexure strength and gas permeability of 3D printed sand molds. J. Manuf. Process. 54, 420–437 (2020). https://doi.org/10.1016/j.jmapro.2020.02.043
[28] L. Song, W. Liu, Y. Li, F. Xin, Humidity-resistant inorganic binder for sand core making in foundry practice. China Foundry 16, 267–271 (2019). https://doi.org/10.1007/s41230-019-8169-8
[29] F. Liu, Z. Fan, X. Liu, H. Wang, J. He, Research on humidity resistance of sodium silicate sand hardened by twice microwave heating process. Mater. Manuf. Process. 29, 184–187 (2014). https://doi.org/10.1080/10426914.2013.872260
[30] F. Liu, Z. Fan, X. Liu, Y. Huang, P. Jiang, Effect of surface coating strengthening on humidity resistance of sodium silicate bonded sand cured by microwave heating. Mater. Manuf. Process. 31, 1639–1642 (2016). https://doi.org/10.1080/10426914.2015.1117631
[31] Z. Chun-Xi, Recent advances in waterglass sand technologies. China Foundry 4, 13–17 (2007)
[32] J.F. Allen, F.S. Cannon, C. Nieto-Delgado, R.C. Voigt, J.T. Fox, J. Lamonski, J.D. Kirby, Full-scale air emissions monitoring and casting quality demonstration of a hybrid hydrolyzed collagen-alkali silicate core binder. Int. J. Met. 10, 172–189 (2016). https://doi.org/10.1007/s40962-016-0021-y
[33] J.T. Fox, J.F. Allen, F.S. Cannon, C.C. Cash, R.C. Voigt, J.A. DeVenne, J.C. Furness, J.S. Lamonski, P. Farver, Full-scale demonstration of a hybrid hydrolyzed collagen-alkali silicate core binder. Int. J. Met. 9, 51-61 (2015). https://doi.org/10.1007/BF03355623
[34] X.J. Li, Z.T. Fan, H.F. Wang, Strength and humidity resistance of sodium silicate sand by ester-microwave composite curing. Zhuzao/Foundry 61, 147–151 (2012)
[35] M. Stachowicz, K. Granat, Long-term effects of relative humidity on properties of microwave hardened moulding sand with sodium silicate. Arch. Foundry Eng. (2017). https://doi.org/10.1515/afe-2017-0104
[36] C. Lustig, M. Baldy, E. Müller, M.L. Reinold, S.M. Anderten, M. Schweinefuß, R. Vargovic, Method for producing a moulding material mixture and a moulded body thereof in the casting industry and kit for use in this method. US 2020/0130049 A1, (2020)
[37] T. Pabel, C. Kneißl, P. Schumacher, J. Brotzki, J. Müller, Improved properties of aluminium cast parts through the use of inorganic cores. Foundry Trade J. Int. 186, 257-261 (2012)
[38] N. Ünlü, A. Odabaş, Development and evaluation of a new eco-friendly sodium silicate-based binder system. Int. J. Met. 12, 765–771 (2018). https://doi.org/10.1007/s40962-018-0210-y
[39] K. Lochte, The inorganic binder system properties and experience. Cast. Plant Technol. Int. 21(32), 6 (2005)
[40] J. Peng, X. Tang, J. He, D. Xu, Effect of heat treatment on microstructure and tensile properties of A356 alloys. Trans. Nonferrous Met. Soc. China 21, 1950–1956 (2011). https://doi.org/10.1016/S1003-6326(11)60955-2
[41] J. Pezda, A. Jarco, Effect of T6 heat treatment parameters on technological quality of the AlSi7Mg alloy. Arch. Foundry Eng. 16, 95–100 (2016). https://doi.org/10.1515/afe-2016-0091
[42] J. Pezda, Influence of heat treatment parameters on the mechanical properties of hypoeutectic al-si-mg alloy. Metalurgija. 53, 221–224 (2014)
[43] F. Xin, W. Liu, L. Song, Y. Li, Modification of inorganic binder used for sand core-making in foundry practice. China Foundry 17, 341–346 (2020). https://doi.org/10.1007/s41230-020-0018-2
[44] P. Jelínek, H. Polzin, R. Škuta, Utilization of physical dehydradion for hardening of cores bonded with colloidal solutions of alkaline silicates. Acta Metall. Slovaca. 10, 10–23 (2004)
[45] R. Krishnaraj, Control of pollution emitted by foundries. Environ. Chem. Lett. 13, 149–156 (2015). https://doi.org/10.1007/s10311-015-0500-z
[46] D.K. Ghosh, Comparison of molding sand technology between alphaset (ApNB) and furan (FNB). Arch. Foundry Eng. (2019). https://doi.org/10.24425/afe.2019.129623
9. 저작권:
본 자료는 A. Fortini, M. Merlin, G. Raminella의 논문 A COMPARATIVE ANALYSIS ON ORGANIC AND INORGANIC CORE BINDERS FOR A GRAVITY DIECASTING AL ALLOY COMPONENT를 기반으로 합니다.
논문 출처: https://doi.org/10.1007/s40962-021-00628-1
본 자료는 상기 논문을 요약한 것으로, 상업적 목적의 무단 사용을 금지합니다.
Copyright © 2025 CASTMAN. All rights reserved.