본 논문 요약은 Composite Structures에 발표된 논문 "중공 복합재 섹션 제조를 위한 수용성 코어 재료 (A water-soluble core material for manufacturing hollow composite sections)"를 기반으로 작성되었습니다.
1. 개요:
- 제목: 중공 복합재 섹션 제조를 위한 수용성 코어 재료
- 저자: Z. Xiao, L.T. Harper, A.R. Kennedy, N.A. Warrior
- 발행 연도: 2017년
- 발행 저널/학회: Composite Structures
- 키워드: 압축 성형, 수용성, 코어, 탄소 섬유 복합재

2. 연구 배경:
연구 주제의 사회적/학문적 맥락
코어 재료는 복합재 구조에서 단면 2차 모멘트를 증가시키고 굽힘 강성을 향상시키는 데 필수적입니다. 샌드위치 패널에는 폼 재료가 일반적으로 사용되지만, 압축 성형 또는 고압 수지 이송 성형(HP-RTM)과 같은 대량 복합재 제조 공정은 상당한 압력(30-150 bar)을 발생시킬 수 있습니다. 이러한 압력은 기존의 폐쇄 셀 폼을 매우 높은 밀도를 갖지 않는 한 찌그러뜨릴 수 있으며, 이는 무게 증가로 이어집니다. 제거 가능한 코어 재료는 대안을 제공하며, 주조 공정에서 모래 코어와 같이 중공 금속 구조 제조에 자주 사용됩니다. 그러나 기존의 제거 가능한 코어는 고압 성형 시나리오, 수지 침투, 효율적인 제거, 비용 효율성 및 환경적 고려 사항에서 종종 어려움에 직면합니다.
기존 연구의 한계
현재 제거 가능한 코어 재료는 다음과 같은 여러 가지 제한 사항을 가지고 있습니다.
- 모래 코어: 기계적 제거가 필요하며, 복잡한 형상 또는 섬세한 부품의 경우 어려울 수 있습니다.
- 추출 가능한 폴리머 및 저융점 금속: 제거 온도가 폴리머 매트릭스와 호환되지 않거나 성형 중 강성이 부족할 수 있습니다.
- 세라믹 코어용 가성 용액: 환경적 위험을 초래하고 최종 제품의 성능에 부정적인 영향을 미칠 수 있습니다.
- 수지 침투: 많은 기존 제거 가능 코어가 고압 성형 중 수지 침투에 취약하여 코어 제거를 어렵게 만듭니다.
연구의 필요성
다음과 같은 저비용, 용이하게 제거 가능한 코어 재료에 대한 분명한 필요성이 있습니다.
- 복합재 성형 중에 발생하는 고압을 견딜 수 있어야 합니다.
- 저점도 수지에 대해 불침투성이어야 합니다.
- 복합재 구조에 손상을 주지 않고 빠르고 쉽게 제거할 수 있어야 합니다.
본 연구는 중공 탄소 섬유 복합재 제조를 위해 수용성 염화나트륨(NaCl) 코어를 탐구하여 이러한 요구 사항을 해결합니다.
3. 연구 목적 및 연구 질문:
연구 목적
본 연구는 고압 성형 공정을 사용하여 중공 탄소 섬유 복합재를 제조하기 위해 수용성 트레할로스 설탕으로 결합된 수용성 염화나트륨(NaCl) 코어를 활용할 가능성을 조사합니다. 주요 목표는 다음과 같은 NaCl 코어의 가공 범위를 정의하는 것입니다.
- 적절한 기계적 물성: 고압 성형(100-150 bar)에 사용하기에 적합합니다.
- 효율적인 코어 제거: 성형 후 복합재 부품에서 효율적으로 제거합니다.
주요 연구 질문
- 개발된 NaCl 코어 재료의 압축 강도는 복합재 성형과 관련된 주변 온도 및 고온(예: 120°C)에서 얼마입니까?
- 바인더 함량, 가공 압력, 온도 및 시간과 같은 요인이 NaCl 코어의 기계적 물성(압축 및 굽힘 강도), 용해 속도 및 밀도에 어떤 영향을 미칩니까?
- NaCl 코어는 고압 성형 후 복합재 부품에서 효과적으로 제거될 수 있으며, 용해 속도는 어떻습니까?
- NaCl 코어는 복잡한 형상 제작을 위해 가공 가능하며 대량 생산 응용 분야에 비용 효율적입니까?
연구 가설
본 연구는 최적화된 NaCl 및 트레할로스 바인더 혼합물이 다음과 같은 코어 재료를 만들 수 있다고 가정합니다.
- 충분한 압축 강도: 고압 성형을 견딜 수 있습니다.
- 수지 불침투성: 수지 침투를 방지합니다.
- 쉬운 물 제거: 성형 후 효율적인 코어 제거를 위해.
또한 코어의 기계적 물성과 용해 속도는 바인더 함량, 가공 압력, 온도 및 시간을 제어하여 조정할 수 있다고 가정합니다.
4. 연구 방법론
연구 설계
본 연구에서는 다음과 같은 실험적 접근 방식을 사용했습니다.
- 다구치 연구법: 가공 매개변수를 최적화합니다.
- 완전 요인 설계법: 사용 중 온도 변화의 영향을 평가합니다.
데이터 수집 방법
개발된 코어 재료(NT 코어) 및 벤치마크 재료를 특성화하기 위해 다양한 실험 방법을 사용했습니다.
- 기계적 시험:
- 압축 강도: 압축 시험을 사용하여 측정했습니다.
- 굽힘 강도: 3점 굽힘 시험을 사용하여 측정했습니다.
- 현미경 관찰: 광학 현미경을 사용하여 코어 재료 단면을 검사했습니다.
- 열분석 시험:
- 열팽창 계수(CTE): TMA를 사용하여 측정했습니다.
- 트레할로스 바인더의 상전이: DSC를 사용하여 분석했습니다.
- 용해 속도 측정: 초음파 수조 및 전도도계를 사용하여 용해 속도를 측정했습니다.
- 가공 시험: 볼 노즈 및 평 엔드밀을 사용하여 슬롯을 가공하여 가공성을 평가했습니다.
- 코어 제거 시험: 수압 제트 제거 시험을 수행하여 제거 속도를 비교했습니다.
분석 방법
데이터 분석 방법은 다음과 같습니다.
- 다구치 방법 분석: 중요한 가공 매개변수를 식별합니다.
- 통계 분석: 평균 효과 및 변화율을 사용하여 매개변수 영향을 정량화합니다.
- 응력-변형률 곡선 분석: 재료 거동 및 파괴 모드를 이해합니다.
- DSC 곡선 분석: 트레할로스 상전이를 특성화합니다.
- 용해 속도 계산: 전도도 변화를 기반으로 유도된 공식을 사용합니다.
- 표면 거칠기 측정: 가공 후 표면 품질을 평가합니다.
- 부피 측정: 수압 제트 시험 중 제거된 코어 부피를 정량화합니다.
연구 대상 및 범위
본 연구는 염화나트륨(NaCl)과 트레할로스 바인더로 구성된 수용성 코어 재료(NT 코어) 개발 및 특성 분석에 중점을 두었습니다. 범위는 다음과 같습니다.
- 최적화: 코어 재료 조성 및 가공 매개변수.
- 평가: 주변 온도 및 고온에서 기계적 물성.
- 평가: NT 코어의 용해 속도, 밀도, CTE 및 가공성.
- 비교: 벤치마크 재료(A 코어 및 B 코어) 대비 성능.
- 시연: 중공 복합재 섹션에서 코어 제거 공정.
5. 주요 연구 결과:
주요 연구 결과
- 높은 압축 강도: NaCl 코어는 주변 온도에서 57 MPa, 120°C에서 20 MPa의 압축 강도를 달성하여 상용 벤치마크보다 뛰어난 성능을 보였습니다.
- 가공 압력의 지배력: 가공 압력이 기계적 강도에 가장 큰 영향을 미치는 요인이었습니다.
- 바인더 함량의 영향: 바인더 함량이 8 wt%까지 기계적 물성에 긍정적인 영향을 미쳤습니다.
- 온도 및 시간 효과: 가공 온도 및 시간은 트레할로스 상전이로 인해 기계적 물성을 향상시켰으며, 최적 온도는 150°C로 확인되었습니다.
- 제어 가능한 용해 속도: 특정 용해 속도(SDR)는 가공 매개변수에 따라 0.14~1.23 kg/(min-m²) 범위였으며, 밀도가 높은 코어가 SDR이 낮았습니다.
- CTE 호환성: NT 코어의 CTE는 약 43 × 10⁻⁶/K로 샌드위치 패널 코어와 유사했습니다.
- 가공성 입증: NT 코어는 특히 볼 노즈 커터로 가공성이 우수함을 보였습니다.
- 성공적인 수압 제트 제거: 수압 제트 제거 시험에서 효과적인 코어 제거가 입증되었습니다.
통계적/정성적 분석 결과
- 가공 압력의 중요성: 다구치 분석 결과 가공 압력이 압축 및 굽힘 강도에 가장 큰 영향을 미치는 것으로 확인되었습니다.
- 매개변수 효과: 바인더 함량, 가공 온도 및 시간이 증가하면 일반적으로 기계적 물성이 향상되었지만 SDR은 감소했습니다.
- 트레할로스 상전이: DSC 분석 결과 가공 중 트레할로스 상전이가 확인되었으며, 이는 코어 물성에 영향을 미쳤습니다.
- 기공률 감소: 현미경 관찰 결과 고온에서 가공된 코어에서 기공률이 감소했으며, 이는 강도 향상과 관련이 있었습니다.
데이터 해석
- 기계적 맞물림: 가공 압력 증가는 염 입자의 기계적 맞물림을 향상시키고 기공률을 감소시켜 강도를 높입니다.
- 트레할로스 바인더 메커니즘: 트레할로스 바인더는 접착제 역할을 하며, 고온에서의 상전이는 공극을 채우고 더 조밀한 구조를 만들어 코어 강도를 더욱 향상시킵니다.
- 강도-용해 균형: 기계적 강도와 용해 속도 사이에 균형이 존재하며, 밀도가 높은 코어는 더 강하지만 용해 속도가 느립니다.
- NT 코어 적합성: NT 코어는 기계적 물성과 용해 속도의 균형이 잘 잡혀 있어 고압 복합재 성형에 적합합니다.
그림 목록
- 그림 1. 원형 디스크(직경 150mm, 두께 13mm)에서 시험편 절단 계획.
- 그림 2. 두 가지 유형의 절단 슬롯, 스캔 방향 및 범위 50mm (a); 유도 게이지가 위치한 6개 위치 (b), 직경 150mm의 원형 샘플 디스크.
- 그림 3. 코어 치수 (a), 복합재 쉘로 감싼 코어 (b), 수압 제트 노즐 및 감싼 코어 위치 (c)의 개략도.
- 그림 4. 서로 다른 바인더 함량 및 가공 온도(170 bar, 10분 가공)를 가진 NT 코어의 압축 (a) 및 굽힘 (b) 응력-변형률 곡선.
- 그림 5. 20°C에서 230°C까지 트레할로스의 DSC 프로필 (가열 속도 5°C/min).
- 그림 6. 20°C-150°C 범위 내에서 연속적인 두 번의 가열 공정에서 트레할로스의 DSC 프로필.
- 그림 7. 8 wt% 바인더 함량을 갖고 170 bar에서 가공된 NT 코어의 단면 광학 현미경 이미지 (a) 120°C, 10분 가공 (기공률: 16%) 및 (b) 190°C, 10분 가공 (기공률: 10%).
- 그림 8. 다구치 연구에서 NT 코어 샘플의 용해 정도 (범례: 가공 압력-바인더 함량-가공 온도-가공 시간).
- 그림 9. 서로 다른 온도 및 시간(다른 선 색상)으로 제조되고 20°C(실선) 및 120°C(점선)에서 시험된 NT 코어의 압축 강도.
- 그림 10. 서로 다른 온도 및 시간(다른 선 색상)으로 제조되고 20°C(실선), 80°C(점선) 및 120°C(점선)에서 시험된 NT 코어의 굽힘 강도.
- 그림 11. 서로 다른 시간 동안 서로 다른 온도에서 제조된 NT 코어의 다양한 색상.
- 그림 12. Ø10 mm 볼 노즈 커터(a), Ø10 mm 평 커터(b)로 엔드 밀링 후 NT 코어.
- 그림 13. 수압 제트 시험 중 B 코어 및 NT 코어(8 wt% 바인더 함량, 150°C 및 170 bar에서 30분 압착)의 부피 변화.
- 그림 14. 개방형 일체형 보강 프리프레그 패널 (a) NT 코어 위치 및 (b) NT 코어 제거 후, 블라인드 홀 표시.
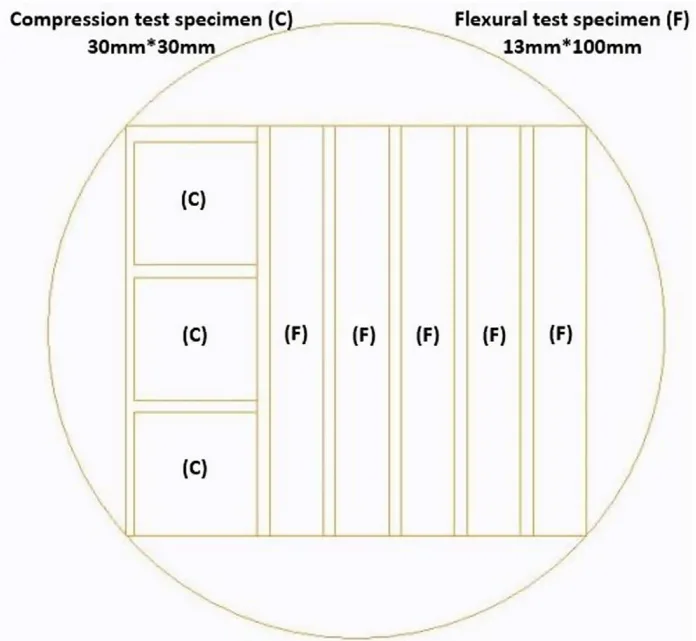
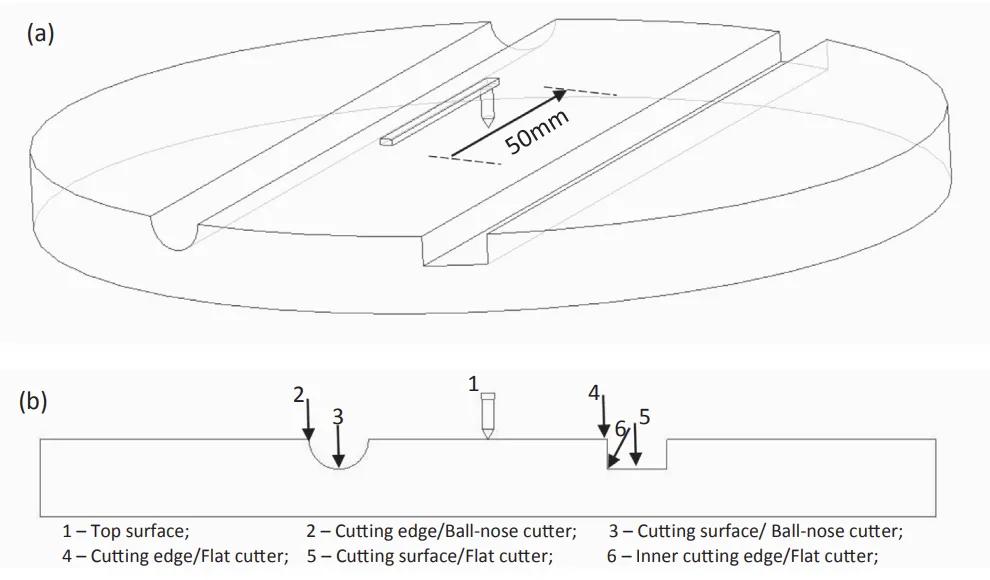
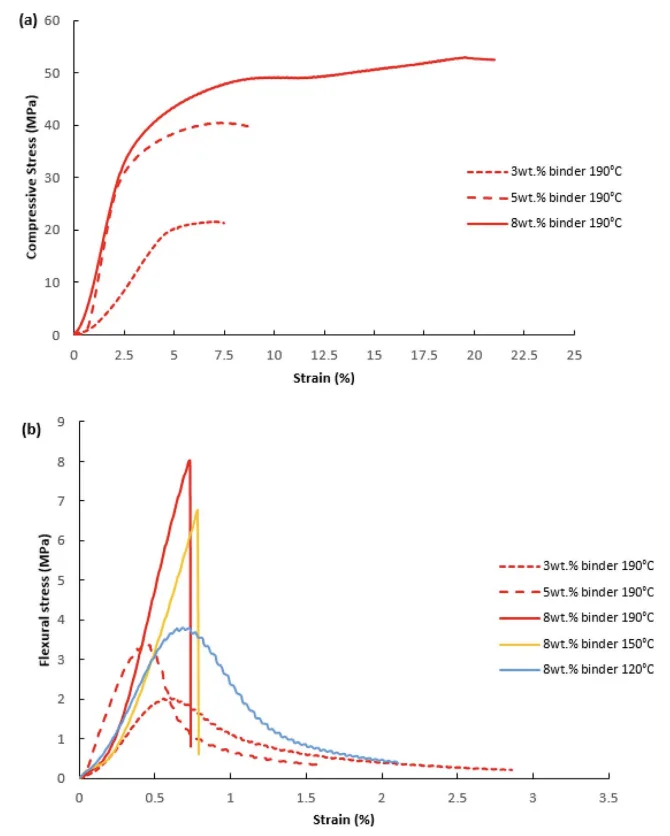
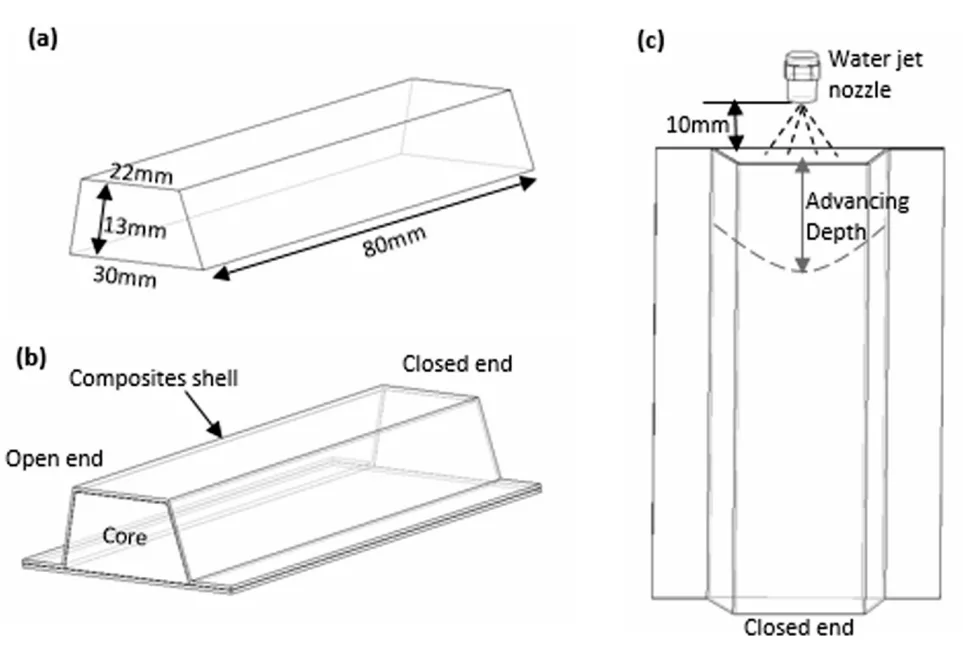
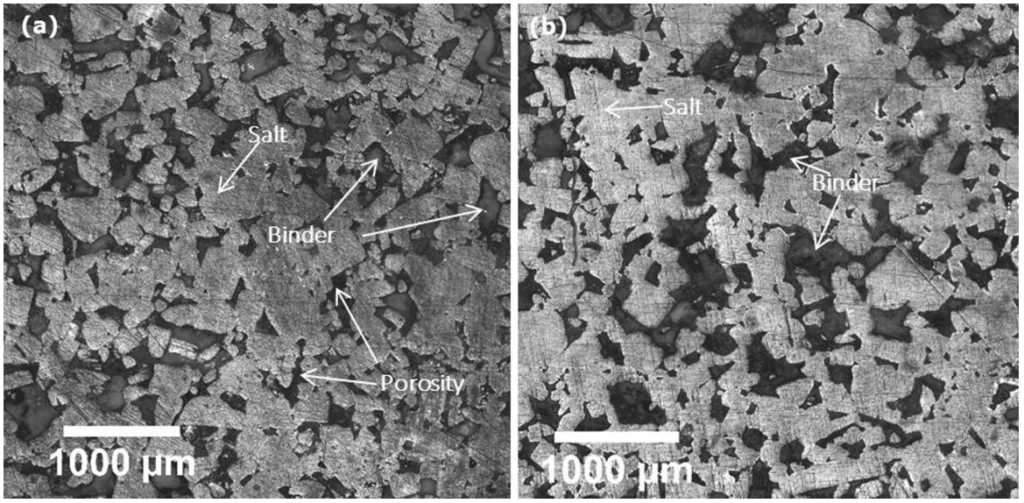
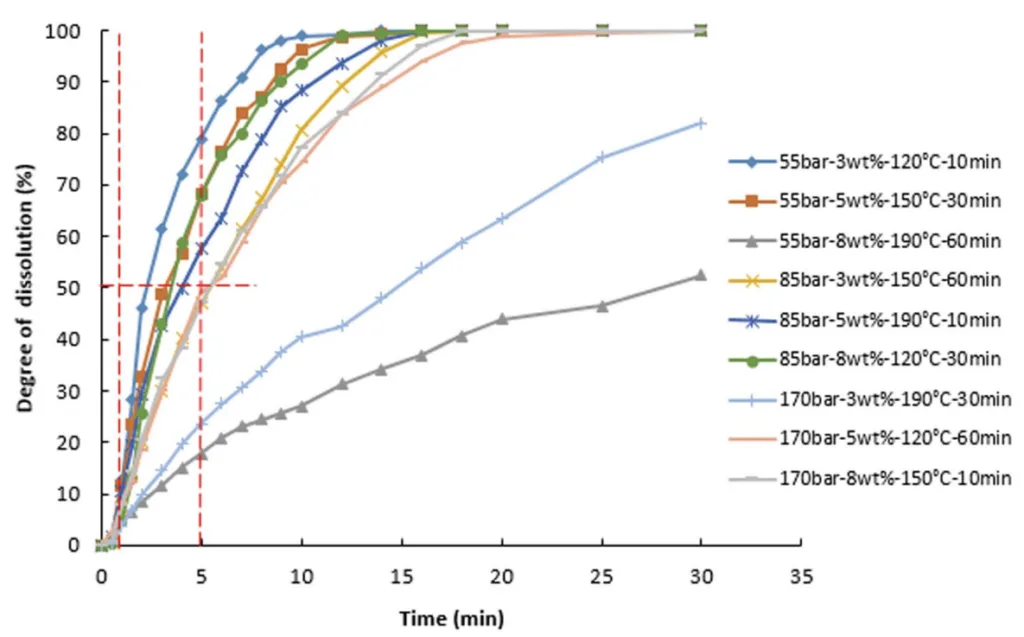
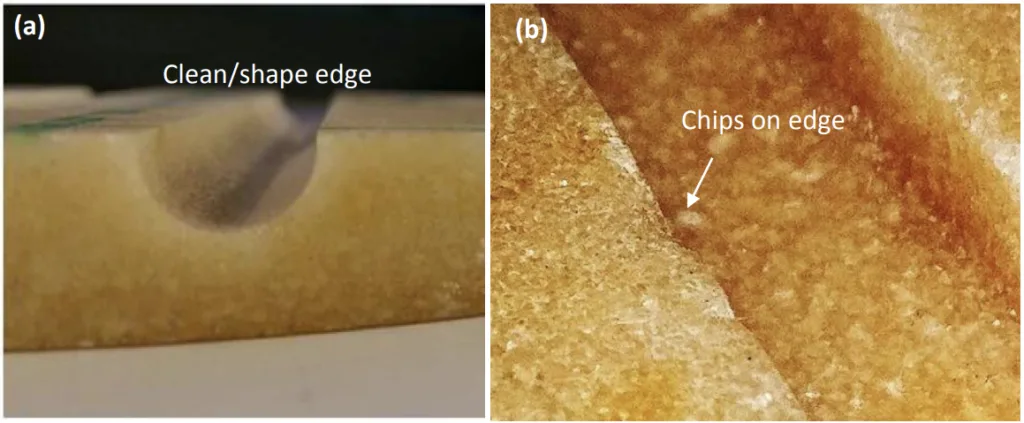

6. 결론 및 논의:
주요 결과 요약
본 연구에서는 고압 복합재 성형에 적합한 트레할로스 바인더를 사용한 수용성 NaCl 기반 코어(NT 코어)를 성공적으로 개발했습니다. NT 코어는 다음을 입증했습니다.
- 높은 기계적 강도: 20°C에서 57.3 MPa, 120°C에서 19.7 MPa의 압축 강도; 20°C에서 10.2 MPa, 120°C에서 3.2 MPa의 굽힘 강도.
- 최적화된 물성: 기계적 물성은 특히 압력과 온도와 같은 가공 매개변수를 조정하여 최적화되었습니다.
- 제어 가능한 용해: 코어는 제어 가능한 용해 속도와 우수한 가공성을 나타냈습니다.
- 성공적인 제거: 수압 제트를 사용하여 복합재 부품에서 효과적인 제거가 입증되었습니다.
연구의 학문적 중요성
본 연구는 다음과 같은 학문적 기여를 합니다.
- 실용적인 저비용 수용성 코어 재료 도입: 복합재의 고압 성형을 위해.
- 상세한 이해 제공: NaCl-트레할로스 코어의 가공 매개변수, 기계적 물성 및 용해 거동 간의 관계에 대한 이해.
- 트레할로스 바인더 역할 규명: 상전이를 통해 코어 성능을 향상시키는 데 있어서의 역할 규명.
실용적 의미
NT 코어는 다음과 같은 여러 가지 실용적인 이점을 제공합니다.
- 실용적인 대안: 복잡한 중공 복합재 구조 제조를 위한 기존의 제거 가능한 코어 재료에 대한 실용적인 대안.
- 수용성: 쉽고 환경 친화적인 제거 가능.
- 가공성: 복잡한 형상 제작 가능.
- 고온에서 높은 강도: 고압 RTM 및 압축 성형에 적합합니다.
- 저비용: NaCl 및 트레할로스 사용으로 경제적으로 매력적입니다.
연구의 한계
- 120°C에서 기계적 물성 감소: 고온 성형 응용 분야에 대한 고려가 필요합니다.
- 잠재적인 수지 침투: 특정 수지 시스템 또는 가공 조건에 코팅층이 필요함을 시사합니다.
- 더 느린 수압 제트 제거 속도: 벤치마크 B 코어에 비해 최적화의 여지가 있음을 나타냅니다.
- 제한된 범위: 특정 조성 및 가공 범위에 초점을 맞추어 추가 탐구가 필요합니다.
7. 향후 후속 연구:
후속 연구 방향
- 수지 침투를 방지하기 위한 코팅 방법 연구.
- 제거 속도를 향상시키기 위한 수압 제트 제거 매개변수 최적화.
- 환경 지속 가능성을 높이기 위한 용해된 NaCl 및 트레할로스의 재활용 가능성 탐구.
- 복잡한 형상에 대한 추가 가공 시험 수행.
- 실제 복합재 부품 제조 및 구조 시험에서 성능 평가.
- NT 코어 재료의 장기 안정성 및 저장 수명 조사.
- 기계적 물성 및 용해 속도를 더욱 향상시키기 위한 대체 바인더 재료 및 조성 탐구.
추가 탐구가 필요한 영역
- 코어 성능 및 제거에 대한 다양한 수지 시스템 및 성형 사이클의 영향.
- 산업 응용 분야를 위한 NT 코어의 대량 생산.
- 특정 응용 분야에서 다른 코어 재료와 비교한 비용-편익 분석.
- NT 코어 생산, 사용 및 폐기의 환경 영향 평가.
8. 참고 문헌:
- [1] Graf M, et al. High pressure resin transfer moulding-process advancements. In: 10th ACCE 2010.
- [2] Ritter K. RTM advances facilitate mass production in the automotive market. 2012 Available from: http://www.materialstoday.com/composite-applications/features/rtm-advances-facilitate-mass-production-in-the/.
- [3] Zajonz A, Stoger W. In-mold foamed cores for lightweight design. 2015 Available from: http://www.rohacell.com/sites/lists/PP-HP/Documents/KUint_2015_10%20In-Mold%20Foamed_.pdf.
- [4] Jelinek P, Adamkova E. Lost cores for high-pressure die casting. Arch Foundry Eng 2014;14(2/2014):101-4.
- [5] Michels H, Bunck M, Buhrig-Polaczek A. Suitability of lost cores in rheocasting process. Trans Nonferrous Met Soc China 2010;20:948-53.
- [6] LaFay V. Application of no-bake sodium silicate binder systems. Int J Metalcast 2012;6(3):19-26.
- [7] Jiang W, et al. Preparation and properties of a novel water soluble core material. J Mater Sci Technol 2010;26:270-5.
- [8] Sangeeta D, Niskayuna NY. Method of dissolving or leaching ceramic cores in airfoils. US: General Electric Company; 1998.
- [9] Amaro AM, et al. Effects of alkaline and acid solutions on glass/epoxy composites. Polym Degrad Stab 2013;98:853-62.
- [10] Pierri D. Lost core: new perspectives in die casting. 2012 Available from: http://doc.assofond.it/congr2012/tecn/2BUHLER.pdf.
- [11] Yaokawa J, et al. Strength of salt core composed of alkali carbonate and alkali chloride mixtures made by casting technique. Mater Trans 2007;48(5):1034-41.
- [12] Jelinek P, et al. Development of foundry cores based on inorganic salts. Mater Technol 2013;47:689-93.
- [13] Edward BF, Paul GA. Process for making soluble cores. U.S. Patents; 1974.
- [14] Pierri D. Lost core neue Perspektiven im Druckguss. 2013 Available from: www.fhnw.ch/technik/forschung-und-entwicklung/giesserei-zentrum/giessereitag/giessereitag-2013/lost-core-neue-perspektiven-im-druckguss-dario-pierri-buhler-ag.pdf.
- [15] Taylor LS, York P. Characterization of the phase transitions of trehalose dihydrate on heating and subsequent dehydration. J Pharm Sci 1998;87(3):347-55.
- [16] Sussich F, et al. Polymorphic amorphous and crystalline forms of trehalose. J Am Chem Soc 1998;120:7893-9.
- [17] Furuki T, Kishi A, Sakurai M. De- and rehydration behavior of a, a-trehalose dihydrate under humidity-controlled atmospheres. Carbohydr Res 2005;340:429-38.
- [18] German RM. Powder metallurgy science. 105 College Rd. E, Princeton, NJ 08540, USA: Metal Powder Industries Federation; 1984. p. 279.
- [19] Rao ASM, et al. Thermophysical properties of NaCl, NaBr and NaF by y-ray attenuation technique. J Mod Phys 2013;04(02):208-14.
- [20] ROHACELL for the Automotive Industry. [cited 2016; Available from: http://www.rohacell.com/sites/lists/PP-HP/Documents/ROHACELL-Automotive-EN.pdf.
- [21] Newman S, Meyer FJ. Mica composites of improved strength. Polym Compos 1980;1(1):37-43.
- [22] Gunay M, et al. Investigation of the effect of rake angle on main cutting force. Int J Mach Tools Manuf 2004;44:953-9.
9. 저작권:
- 본 자료는 Z. Xiao, L.T. Harper, A.R. Kennedy, N.A. Warrior의 논문 "중공 복합재 섹션 제조를 위한 수용성 코어 재료 (A water-soluble core material for manufacturing hollow composite sections)"를 기반으로 합니다.
- 논문 출처: http://dx.doi.org/10.1016/j.compstruct.2017.09.058
본 자료는 상기 논문을 기반으로 요약되었으며, 상업적 목적으로 무단 사용하는 것을 금지합니다.
Copyright © 2025 CASTMAN. All rights reserved.