본 논문 요약은 ['Solute micro-segregation profile and associated precipitation in cast Al-Mg-Si alloy'] 논문을 기반으로 작성되었으며, ['Philosophical Magazine']에 게재되었습니다.
1. 개요:
- 제목: 주조 Al-Mg-Si 합금의 용질 미세 편석 프로파일 및 관련 석출 (Solute micro-segregation profile and associated precipitation in cast Al-Mg-Si alloy)
- 저자: Artenis Bendo, Jonathan Fellowes, Matthew Smith, Masoud Moshtaghi, Zelong Jin, Kenji Matsuda, Zhongyun Fan & Xiaorong Zhou
- 발행 연도: 2024년
- 발행 저널/학회: Philosophical Magazine
- 키워드: 알루미늄 합금; 주조; 편석; 금속간 화합물; 석출; 투과 전자 현미경 (aluminium alloy; casting; segregation; intermetallic phases; precipitation; transmission electron microscopy)

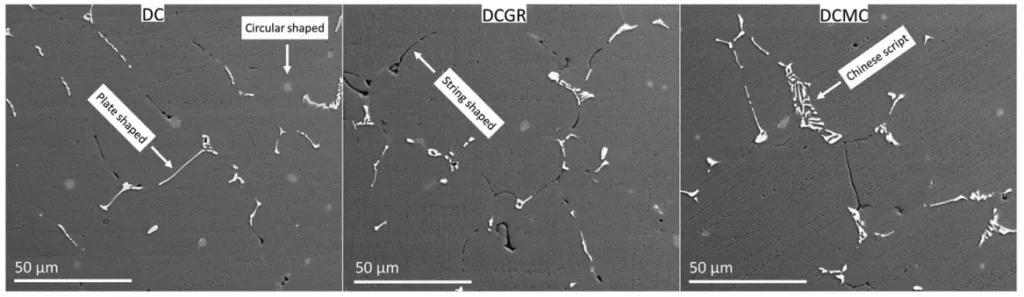
2. 연구 배경:
연구 주제 배경:
용질 편석은 알루미늄 합금의 응고 과정에서 흔히 나타나는 현상입니다. 이는 빠른 냉각 속도로 인해 발생하는 비평형 조건 때문이며 [1], 이는 많은 주조 공정의 특징입니다. 응고 중 고체/액체 계면의 진행은 용융물 내 용질의 지속적인 축적을 유발합니다 [2]. 각 원소의 분배 계수는 이 과정에서 고체 또는 액체 상 중 어느 상에 우선적으로 농축될지를 결정합니다.
기존 연구 현황:
주조 Al-Mg-Si 합금의 거시적 편석에 대한 이전 연구에서는 빌렛 중심부에서 Mg 및 Si의 고갈과 표면 근처에서의 농축을 시사했으며 [5], 이는 중심선 음극 편석이라고 알려진 현상입니다. 또한, 연구에 따르면 Al-Mg-Si 합금의 미세 편석 영역 내에서 Fe-rich 금속간 화합물과 함께 준안정상 β' 및 안정상 β가 존재하는 것으로 나타났습니다 [6–8,10,11]. 그러나 기존 문헌에서는 이러한 미세 편석 밴드 내의 상세한 농도 구배 및 원자 규모 구조에 대한 연구가 부족합니다.
연구의 필요성:
Al-Mg-Si 합금은 차량 부품 제조에 점점 더 중요하게 사용되고 있으며 [12], AA6082 알루미늄 합금은 기존의 하류 열기계적 처리 [13]를 거칠 경우 뛰어난 기계적 성능을 보여줍니다. 산업 동향은 하류 열기계적 공정과 관련된 제조 비용을 절감하기 위해 부품을 주조 상태 그대로 사용하는 방향으로 전환되고 있습니다. 단조 Al-Mg-Si 합금에서 강화상의 석출은 Mg 및 Si 용질 원소에 크게 의존하며, 이들의 농도는 미세 편석 프로파일에 의해 크게 영향을 받습니다. 따라서 이러한 편석 밴드의 구조에 대한 포괄적인 이해가 매우 중요합니다.
3. 연구 목적 및 연구 질문:
연구 목적:
본 연구는 주조 AA6082 알루미늄 합금의 미세 편석의 본질을 밝히기 위해 주요 및 부차적 미세 편석을 구별하는 것을 목표로 합니다. 주요 초점은 부차적 미세 편석 밴드의 미세 구조를 특성화하고, 특히 분포 패턴, 농도 구배 및 나노 구조를 조사하는 것입니다. 또한, 본 연구는 부차적 및 주요 미세 편석 밴드 간의 관계를 명확히 하고자 합니다.
핵심 연구 질문:
- 부차적 미세 편석 밴드 내의 미세 구조에 대한 상세한 특성화.
- 이러한 밴드 내 용질 원소의 분포 패턴 및 농도 구배 분석.
- 부차적 미세 편석 밴드에 존재하는 나노 구조 조사.
- 부차적 미세 편석 밴드와 주요 미세 편석 특징 간의 관계 규명.
연구 가설:
공식적인 가설로 명시되지는 않았지만, 본 연구는 주조 AA6082에서 미세 편석이 주요 및 부차적 유형으로 효과적으로 분류될 수 있으며, 각 유형은 뚜렷한 특징과 형성 메커니즘을 갖는다는 전제하에 진행됩니다. 중심적인 명제는 부차적 미세 편석 밴드에 대한 상세한 이해가 강화상의 석출을 제어하고 최적화하는 데 중요하며, 이는 최종 재료 특성에 영향을 미친다는 것입니다.
4. 연구 방법론
연구 설계:
본 연구는 실험적 연구 설계를 채택하여 기존의 직접 냉각 주조(DC), 결정립 미세화제 첨가 직접 냉각 주조(DCGR), 용융 상태 조절 직접 냉각 주조(DCMC)의 세 가지 주조 공정을 통해 생산된 주조 AA6082 알루미늄 합금 샘플을 활용했습니다. 이러한 비교 접근 방식을 통해 다양한 응고 조건에서 미세 편석 패턴을 조사할 수 있었습니다.
데이터 수집 방법:
다각적인 데이터 수집 접근 방식이 채택되었으며, 다음과 같은 고급 분석 기술을 사용했습니다.
- 주사 전자 현미경 (SEM): 후방 산란 전자 이미징 (BSE) 및 에너지 분산형 X선 분광법 (EDS)은 FEI Quanta 250 FEG, FEI Quanta 650 FEG 및 Tescan Mirai3LC FEG SEM을 사용하여 수행되었습니다.
- 전자 탐침 미세 분석 (EPMA): 정량적 원소 매핑은 FEG, SXES 및 EDS 검출기가 장착된 JEOL JXA-8530F를 사용하여 수행되었습니다.
- 투과 전자 현미경 (TEM) 및 주사 투과 전자 현미경 (STEM): 상세한 미세 구조 및 원자 규모 특성 분석은 FEI Tecnai TF30 FEG TEM, FEI Talos F200 X-Field Emission Gun (X-FEG) STEM 및 FEI Titan G2 80-200 수차 보정 STEM을 사용하여 달성되었습니다.
- 스파크 방출 분광법 (SES): 전체 화학 조성은 Thermo Scientific ARL iSpark 광학 스파크 방출 분광계를 사용하여 결정되었습니다.
분석 방법:
수집된 데이터는 다음과 같은 엄격한 분석을 거쳤습니다.
- 현미경 이미지 분석: 미세 편석 형태 및 석출물 분포를 특성화하기 위한 SEM, TEM 및 STEM 이미지의 정성적 및 정량적 분석.
- 원소 매핑 및 라인 스캔: EPMA 및 EDS 데이터를 사용하여 원소 맵 및 농도 프로파일을 생성하여 미세 편석 밴드 내 용질 편석을 정량화했습니다.
- 전자 회절: TEM에서 얻은 선택 영역 전자 회절 (SAED) 패턴을 사용하여 상을 식별했습니다.
- 원자 규모 분해능 이미징: HAADF-STEM 이미징 및 고속 푸리에 변환 (FFT)을 사용하여 석출물의 원자 구조를 분석했습니다.
- 열역학 계산: Scheil 응고 계산을 수행하여 응고 중 상 형성 순서를 예측했습니다.
연구 대상 및 범위:
본 연구는 주조 AA6082 알루미늄 합금 샘플에 초점을 맞추었습니다. 샘플은 DC, DCGR 및 DCMC 주조 방법으로 생산된 빌렛에서 준비되었습니다. 연구 범위는 이러한 주조 상태 재료 내에서 미세 및 나노 규모의 미세 편석 현상 조사로 제한되었으며, 특히 미세 편석 밴드 및 관련 석출물의 특성 분석에 중점을 두었습니다.
5. 주요 연구 결과:
핵심 연구 결과:
본 연구 결과, 주조 AA6082 알루미늄 합금의 미세 편석은 결정립계 및 수지상 간 채널을 따라 상호 연결된 네트워크를 형성하는 것으로 나타났습니다. 미세 편석은 두 가지 뚜렷한 유형으로 분류되었습니다.
- 주요 미세 편석: 주로 결정립계에 위치하며 철 함유 금속간 화합물이 존재하는 것이 특징입니다.
- 부차적 미세 편석: 결정립계 및 수지상 간 채널 모두에서 관찰되며, 주로 Mg 및 Si 합금 원소로 구성됩니다.
원자 규모 이미징 결과, 부차적 편석 밴드는 석출물 형성 부위인 것으로 나타났습니다. 이러한 석출물은 두 가지 메커니즘을 통해 핵생성됩니다.
- 이종 핵생성: 전위 네트워크에서 발생합니다. 이러한 석출물은 석출 순서 전반에 걸쳐 형성된 상들의 혼합물로 구성됩니다.
- 동종 핵생성: 알루미늄 기지 내에서 발생합니다. 이러한 석출물은 석출 순서의 초기 단계에 나타나는 개별적인 상입니다.
데이터 해석:
주요 편석 대 부차적 편석: SEM 분석 (그림 1) 결과, 판상, 중국 문자형, 끈 모양 및 원형 모양을 포함하여 주요 편석과 관련된 거친 특징이 나타났습니다. 원소 매핑 (그림 2) 결과, 이러한 주요 편석 특징은 Si, Fe 및 Mn이 풍부한 것으로 나타났습니다. 대조적으로, EPMA (그림 3)에 의해 밝혀진 부차적 편석 밴드는 폭이 약 5-15 µm로 더 미세하며 Mg 및 Si가 풍부합니다.
부차적 편석 밴드 내 석출: EPMA 맵 (그림 3) 및 TEM/STEM 분석 (그림 4-8) 결과, 부차적 편석 밴드가 석출에 유리한 부위로 작용하는 것으로 나타났습니다. 전위선에서의 이종 핵생성은 혼합된 상을 가진 더 거친 석출물 형성을 유도합니다 (그림 6 및 7). Al 기지 내 동종 핵생성은 더 미세하고 개별적인 석출물을 생성하며, 주로 β" 및 Type-B/U2 상의 전구체입니다 (그림 8).
편석 네트워크: 부차적 편석 밴드의 상호 연결된 특성은 EPMA 맵 (그림 9)에 의해 강조되었으며, 이러한 밴드는 결정립계 및 수지상 간 채널을 따라 네트워크를 형성하여 Si 및 Mg의 고농도 영역을 연결하는 것으로 나타났습니다.
그림 목록:
- 그림 1. 주조 DC, DCGR 및 DCMC 조건에서 AA6082 Al 합금의 미세 구조의 후방 산란 전자 SEM 이미지. 판상, 중국 문자형, 끈 모양 및 원형 모양 특징의 석출이 발생했습니다.
- 그림 2. 세 가지 주조 조건의 후방 산란 전자 이미지와 해당 원소 맵. 라벨링은 표시된 상의 주요 원소 조성을 보여줍니다.
- 그림 3. 세 가지 주조 조건에서 Si 및 Mg 편석의 정성적 전자 탐침 미세 분석 (EPMA) 맵. EPMA 맵은 부차적 편석 밴드를 나타내기 위해 의도적으로 강조되었습니다. 라인 스캔은 흰색 점선으로 표시됩니다. 농도 (at.%) 대 거리 (µm) 플롯은 EPMA 맵의 해당 라인 스캔에 해당합니다.
- 그림 4. DCGR 주조에서 미세 편석 밴드에서 관찰된 형태. 육각형 모양의 알파상 철-rich 입자의 TEM 이미지, 해당 전자 회절, 원소 맵 및 큐빅 알파 철-rich 상의 (111) 존 축을 따른 노이즈 필터링된 원자 규모 HAADF-STEM 이미지.
- 그림 5. (A0) DCGR 주조에서 거친 수지상 특징 옆의 [001] 알루미늄 존 축을 따른 미세 구조의 HAADF-STEM 이미지. (A1) A0 이미지에서 흰색 점선으로 표시된 확대 영역. (A2) A1 이미지에서 흰색 점선으로 표시된 영역과 해당 원소 맵.
- 그림 6. DCGR 주조에서 미세 편석 밴드 내의 거친 금속간 화합물 옆의 [001] 알루미늄 존 축을 따른 TEM 및 STEM 이미징. (A0) 거친 금속간 화합물 옆의 미세 구조의 TEM 이미지. (A1) A0 이미지에서 검은색 점선으로 표시된 영역의 확대된 TEM 이미지. (A2) A1 이미지의 상단 부분에서 검은색 점선으로 표시된 영역의 HAADF-STEM 이미지. (1 & 2) HAADF-STEM 모드를 사용하여 전체적으로 이미징된 석출물 1과 2. 흰색 점선으로 표시된 석출물 1과 2의 단면의 필터링되지 않은 원자 규모 이미지. 녹색의 Si-rich 원자 기둥과 파란색의 Cu-rich 원자 기둥의 오버레이 및 해당 FFT. FFT에서 흰색 원은 Al 기지를 나타내고 흰색 점선 원은 Si 네트워크 반사를 나타냅니다.
- 그림 7. (a, b) [001] 알루미늄 존 축을 따른 필터링되지 않은 원자 규모 HAADF-STEM 이미지로, 이종 핵생성된 석출물의 단면을 보여줍니다. (I, II, III, IV) 다양한 석출물 단면 영역과 해당 준안정상에서 확대된 부분. 입사 빔 (z-좌표)과 평행한 원자 기둥의 원자 좌표는 무시됩니다.
- 그림 8. DCGR 주조에서 미세 편석 밴드 내의 미세 구조의 TEM 및 STEM 이미지. (A0) 그림 6 (A1)과 동일한 영역의 TEM 이미지. (A1) A0 이미지에서 검은색 점선으로 표시된 영역의 확대된 HAADF-STEM 이미지. 동종 석출이 발생했습니다. (a, b) Al 기지 내에서 동종 핵생성된 석출물과 해당 FFT의 필터링되지 않은 원자 규모 HAADF-STEM 이미지.
- 그림 9. DCGR 주조에서 편석 패턴의 EPMA 맵. (a) Si 편석 맵 및 그 개략도. (b) Mg 편석 맵 및 그 개략도. (c) Mn 편석 맵 및 그 개략도. Mn 편석 맵은 Fe 편석 맵과 동일합니다. 부록을 확인하십시오. (d) 부차적 편석 밴드의 미세 구조 그림. (e) 알루미늄 수지상 경계로 돌출되기 전의 두 개의 알루미늄 수지상.
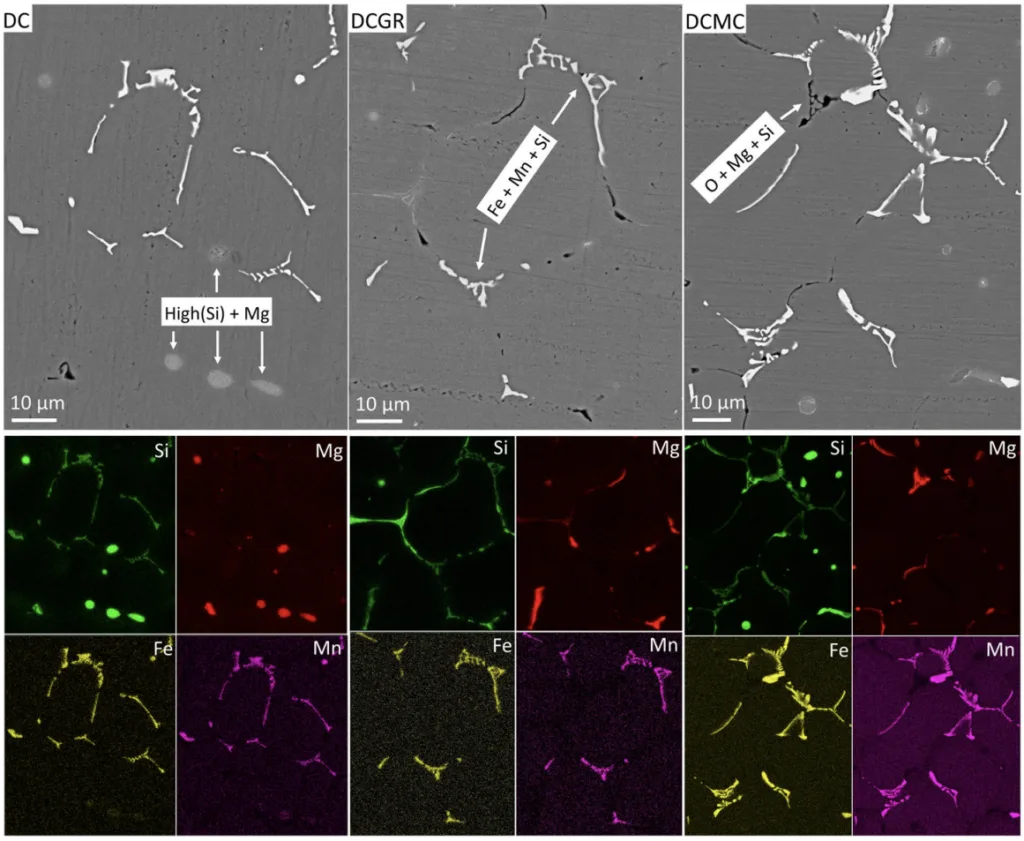
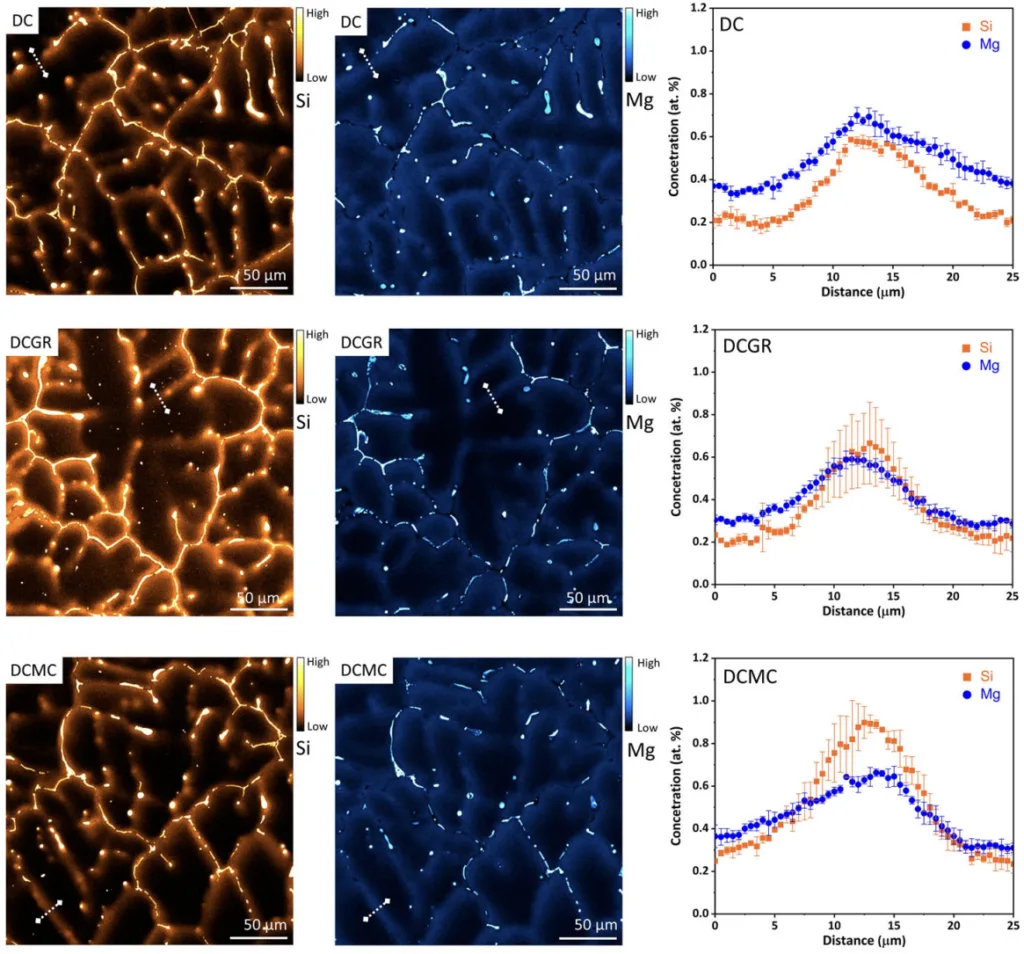
6. Conclusion:
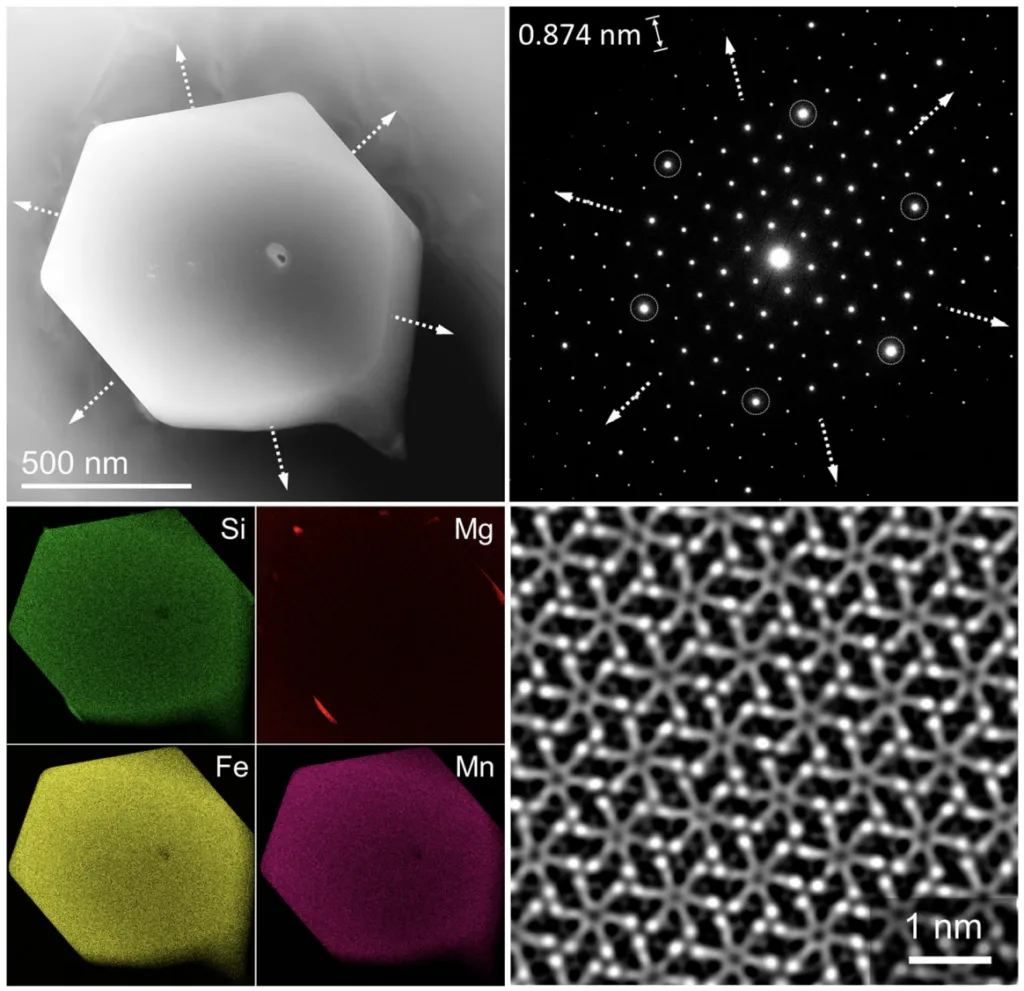
![Figure 5. (A0) The HAADF-STEM image of the microstructure along the [001] aluminium zone axis, next to a coarse dendritic feature in the DCGR cast. (A1) The enlarged area marked with dashed white lines in the AO image. (A2) The area marked with white dashed lines in the A1 image and the corresponding elemental maps.](https://castman.co.kr/wp-content/uploads/image-563-1024x719.webp)
![Figure 7. (a, b) The unfiltered atomic-scale HAADF-STEM images along the [001] aluminium zone axis, revealing the precipitate cross-sections of the heterogeneously nucleated precipitates. (I, II, III, IV) The enlarged parts from the different precipitate cross-section areas and the respective metastable phases. The atomic coordinates of the atomic columns parallel with the incident beam (z-coordinates) are neglected.](https://castman.co.kr/wp-content/uploads/image-564-1024x991.webp)
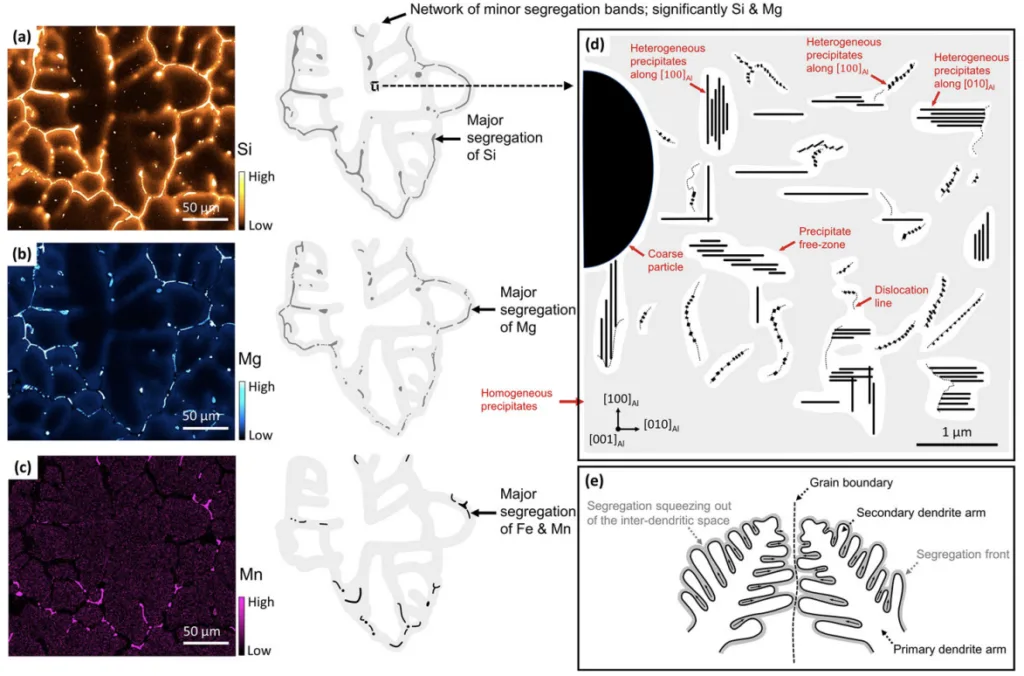
6. 결론:
주요 결과 요약:
본 연구는 결정립 미세화제 및 용융 상태 조절 유무에 따른 직접 냉각 주조로 생산된 주조 AA6082 알루미늄 합금의 미세 편석 패턴에 대한 포괄적인 조사를 제공합니다. 본 연구에서는 주요 및 부차적 미세 편석 밴드를 성공적으로 구별했습니다. Fe, Mn 및 Si가 풍부한 주요 밴드는 주로 결정립계에 위치하는 반면, Si 및 Mg가 풍부한 부차적 밴드는 수지상 간 채널 및 결정립계를 따릅니다. 알파-Al15(FeMn)3Si2 금속간 화합물상은 주요 편석 밴드의 주요 구성 성분으로 확인되었습니다. 일반적인 폭이 5-15 µm이고 Mg/Si 농도가 0.6-0.8 at.%에서 최고조에 달하는 부차적 편석 밴드는 석출에 유리한 부위 역할을 합니다. 주조 상태 미세 구조 내의 전위 네트워크는 불규칙하고 이종적으로 분포되어 이종 석출에 영향을 미칩니다. 전위에서의 이종 석출과 알루미늄 기지 내 동종 석출 모두 부차적 편석 밴드 내에서 관찰되었습니다.
연구의 학문적 의의:
본 연구는 주조 알루미늄 합금의 미세 편석에 대한 기본적인 이해에 크게 기여합니다. 거시적 편석 패턴에서 원자 규모 석출물 구조에 이르기까지 상세한 다중 규모 특성 분석을 제공합니다. 주요 및 부차적 미세 편석의 구별과 이들의 뚜렷한 특징 및 형성 메커니즘에 대한 설명은 Al-Mg-Si 합금의 응고 현상에 대한 귀중한 통찰력을 제공합니다.
실용적 의미:
본 연구 결과는 알루미늄 주조 산업에 직접적인 실용적 의미를 갖습니다. 미세 편석 밴드 및 관련 석출물의 형성과 특징을 이해하는 것은 주조 공정 및 후속 열처리를 최적화하는 데 매우 중요합니다. 미세 편석을 제어함으로써 강화상의 석출을 맞춤화하여 궁극적으로 자동차 부문 및 그 이상의 까다로운 응용 분야에 특히 적합한 Al-Mg-Si 합금 부품의 기계적 특성을 향상시킬 수 있습니다.
연구의 한계점
본 연구는 미세 편석 패턴의 고유한 변동성과 사용된 비교적 작은 샘플링 부피로 인해 발생하는 한계를 인정합니다. 이러한 요인으로 인해 세 가지 주조 방법 간의 미세 편석 특성에 미치는 영향 측면에서 통계적으로 유의미한 차이를 구별할 수 없었습니다. 더 큰 샘플 크기와 더 광범위한 통계 분석을 통한 향후 연구가 이러한 한계를 극복하는 데 필요할 수 있습니다.
7. 향후 후속 연구:
- 후속 연구 방향:
- 관찰된 불규칙한 전위 네트워크의 형성 메커니즘과 이종 석출을 유도하는 정확한 역할에 대한 추가 조사.
- 상 진화에 대한 보다 자세한 이해를 확립하기 위해 주요 및 부차적 편석 밴드 내에 존재하는 다양한 석출상에 대한 정량적 분석.
- 냉각 속도 및 용융 온도와 같은 특정 주조 매개변수가 결과 미세 편석 패턴 및 석출물 특성에 미치는 영향 탐구.
- 추가 탐구가 필요한 영역:
- 응고의 최종 단계에서 용질이 풍부한 용융물이 결정립계 및 수지상 간 채널로 짜내는 정확한 메커니즘.
- 주요 및 부차적 편석 밴드 간의 상호 작용과 전체 미세 구조 및 재료 특성에 대한 결합 효과.
- 다양한 주조 조건에서 Al-Mg-Si 합금의 미세 편석 형성 및 석출물 진화를 시뮬레이션하기 위한 예측 모델 개발.
8. 참고 문헌:
- [1] D.G. Eskin, R. Nadella, and L. Katgerman, Effect of different grain structures on center-line macrosegregation during direct-chill casting. Acta Mater. 56 (2008), pp. 1358–1365. doi:10.1016/j.actamat.2007.11.021.
- [2] Z. Yao, Y. Huo, M. Li, and J. Allison, A quantitative study of microsegregation in aluminum-copper alloys. Metall. Mater. Trans. A 53 (2022), pp. 2383–2401. doi:10.1007/s11661-022-06669-3.
- [3] R. Nadella, D.G. Eskin, Q. Du, and L. Katgerman, Macrosegregation in direct-chill casting of aluminium alloys. Prog. Mater. Sci. 53 (2008), pp. 421–480. doi:10.1016/j.pmatsci.2007.10.001.
- [4] X. Doré, H. Combeau, and M. Rappaz, Modelling of microsegregation in ternary alloys: applications to the solidification of Al-Mg-Si. Acta Mater. 48 (2000), pp. 3951–3962. doi:10.1016/S1359-6454(00)00177-4.
- [5] Q. Dong, X. Chen, J. Xia, X. Li, B. Zhang, and H. Nagaumi, Floating grain characterization and its effects on centerline segregation of direct-chill cast Al-Mg-Si alloy billets. Mater. Trans. 61(12) (2020), pp. 2386–2392. doi:10.2320/matertrans.MT-M2020229.
- [6] L. Lodgaard and N. Ryum, Precipitation of dispersoids containing Mn and/or Cr in Al–Mg-Si alloys. Mater. Sci. Eng. 283 (2000), pp. 144–152. doi:10.1016/S0921-5093(00)00734-6.
- [7] R. Hu, T. Ogura, H. Tezuka, T. Sato, and Q. Liu, Dispersoid formation and recrystallization behavior in an Al-Mg-Si-Mn alloy. J. Mater. Sci. Technol. 26(3) (2010), pp. 237–243. doi:10.1016/S1005-0302(10)60040-0.
- [8] M. Kenyon, J. Robson, J. Fellowes, and Z. Liang, Effect of dispersoids on the microstructure evolution in Al-Mg-Si alloys. Adv. Eng. Mater. 21 (2019), pp. 1800494. doi:10.1002/adem.201800494.
- [9] T. Dorin, M. Ramajayam, S. Babaniaris, and T.J. Langan, Micro-segregation and precipitates in as-solidified Al-Sc-Zr-(Mg)-(Si)-(Cu) alloys. Mater. Charact. 154 (2019), pp. 353-362. doi:10.1016/j.matchar.2019.06.021.
- [10] Y.S. Park, S.B. Lee, and N.J. Kim, Microstructure and mechanical properties of strip cast Al-Mg-Si-X alloys. Mater. Trans. 44(12) (2003), pp. 2617-2624. doi:10.2320/matertrans.44.2617.
- [11] M. Ganesan, L. Thuinet, D. Dye, and P.D. Lee, Quantification of microsegregation in cast Al-Si-Cu alloys. Metall. Mater. Trans. 38 (2007), pp. 557–566. doi:10.1007/s11663-007-9071-0.
- [12] G. Scamans, Electric vehicle spike demand for high strength aluminum extrusions. Light Met. Age 76 (2018), pp. 6-12.
- [13] C.D. Marioara, S.J. Andersen, J. Jansen, and H.W. Zandbergen, The influence of temperature and storage time at RT on nucleation of the β" phase in a 6082 Al-Mg-Si alloy. Acta Mater. 51 (2003), pp. 789–796. doi:10.1016/S1359-6454(02)00470-6.
- [14] A. Cibula, The grain refinement of aluminium alloy castings by additions of titatnium and boron. J. Inst. Met. 80 (1951), pp. 1–16.
- [15] Z. Fan, Y. Wang, Y. Zhang, T. Qin, X.R. Zhou, G.E. Thompson, T. Pennycook, and T. Hashimoto, Grain refining mechanism in the Al/Al-Ti-B system. Acta Mater. 84 (2015), pp. 292-304. doi:10.1016/j.actamat.2014.10.055.
- [16] Z. Fan, An epitaxial model for heterogenous nucleation on potent substrates. Metall. Mater. Trans. A 44 (2013), pp. 1409–1418. doi:10.1007/s11661-012-1495-8.
- [17] Z. Fan, B. Jiang, and Y. Zuo. Apparatus and method for liquid metals treatment. WO/2012/035357 and 2013 US 20130228045 A1.
- [18] G. Scamans, H.T. Li, J.L. Nebreda, J. Patel, I. Stone, Y. Wang, X. Yang, and Z. Fan, Advanced casting technologies using high shear melt conditioning. Fundam. Alum. Metall., Chapter 8 (2018), pp. 249–277. doi:10.1016/B978-0-08-102063-0.00008-4.
- [19] J.B. Patel, H.T. Li, X. Mingxu, and S. Jones, Melt conditioned direct chill casting (MC-DC) process for production of high-quality aluminum alloy billets. Mater. Sci. Forum 794-796 (2014), pp. 149–154. doi:10.4028/www.scientific.net/MSF.794-796.149.
- [20] K.M.S. Manu, N.S. Barekar, J.L. Nebreda, J.B. Patel, and Z. Fan, In-situ microstructural control of A6082 alloy to modify second phase particles by melt conditioned direct chill
- [21] G. Scamans, H.T. Li, and Z. Fan, Melt conditioned casting of aluminum alloys, 13th International Conference on Aluminum Alloys (ICAA13), 2012. doi:10.1007/978-3-319-48761-8_213.
- [22] S. Kumar and K.A.Q. O'Reilly, Influence of Al grain structure on Fe bearing intermetallics during DC casting of an Al-Mg-Si alloy. Mater. Charact. 120 (2016), pp. 311–322. doi:10.1016/j.matchar.2016.09.017.
- [23] S. Kumar, P.S. Grant, and K.A.Q. O'Reilly, Evolution of Fe bearing intermetallics during DC casting and homogenization of an Al-Mg-Si Al alloy. Metall. Mater. Trans. A 47 (2016), pp. 3000–3014. doi:10.1007/s11661-016-3451-5.
- [24] S. Kumar, P.S. Grant, and K.A.Q. O'Reilly, Fe bearing intermetallic phase formation in a wrought Al-Mg-Si alloy. Trans. Indian Inst. Met. 65(6) (2012), pp. 553–557. doi:10.1007/s12666-012-0221-y.
- [25] A. Verma, S. Kumar, P.S. Grant, and K.A.Q. O'Reilly, Influence of cooling rate on the Fe intermetallic formation in an AA6063 Al alloy. J. Alloys Compd. 555 (2013), pp. 274–282. doi:10.1016/j.jallcom.2012.12.077.
- [26] T. Hashimoto, G.E. Thompson, M. Curioni, X. Zhou, and P. Skeldon, Three-dimensional imaging of light metals using serial block face scanning electron microscopy (SBFSEM). Mat. Sci. Forum 765 (2013), pp. 501–505. doi:10.4028/www.scientific.net/MSF.765.501.
- [27] J.M. Yu, T. Hashimoto, H.T. Li, N. Wanderka, Z. Zhang, C. Cai, X.L. Zhong, J. Qin, Q.P. Dong, H. Nagaumi, and X.N. Wang, Formation of intermetallic phases in unrefined and refined AA6082 Al alloys investigated by using SEM-based ultramicrotomy tomography. J. Mater. Sci. Technol. 120 (2022), pp. 118–128. doi:10.1016/j.jmst.2022.02.007.
- [28] C.M. Dinnis, J.A. Taylor, and A.K. Dahle, As-cast morphology of iron-intermetallics in Al-Si foundry alloys. Scr. Mater. 53 (2005), pp. 955–958. doi:10.1016/j.scriptamat.2005.06.028.
- [29] Z. Que and C.L. Mendis, Heterogenous nucleation and phase transformation of Fe-rich intermetallic compounds in Al-Mg-Si alloys. J. Alloys Compd. 836 (2020), pp. 155515. doi:10.1016/j.jallcom.2020.155515.
- [30] Z. Que, Y. Wang, and Z. Fan, Formation of the Fe-containing intermetallic compounds during solidification of Al-5Mg-2Si-0.7Mn-1.1Fe alloy. Metall. Mater. Trans. A 49 (2018), pp. 2173–2181. doi:10.1007/s11661-018-4591-6.
- [31] Y.L. Liu and S.B. Kang, The solidification process of Al-Mg-Si alloys. J. Mater. Sci. 32 (1997), pp. 1443–1447. doi:10.1023/A:1018545732009.
- [32] Y.L. Liu, S.B. Kang, and H.W. Kim, The complex microstructures in an as-cast Al-Mg-Si alloy. Mater. Lett. 41 (1999), pp. 267–272. doi:10.1016/S0167-577X(99)00141-X.
- [33] Z. Fan, M. Xia, H. Zhang, G. Liu, J.B. Patel, Z. Bian, I. Bayandorian, Y. Wang, H.T. Li, and G.M. Scamans, Melt conditioning by advanced shear technology (MCAST) for refining solidification microstructure. Int. J. Cast Met. Res. 22(1-4) (2009), pp. 103–107. doi:10.1179/136404609X367443.
- [34] Z. Fan, Y. Wang, Z.F. Zhang, M. Xia, H.T. Li, J. Xu, L. Granas, and G.M. Scamans, Shear enhanced heterogenous nucleation in some Mg-and Al-alloys. Int. J. Cast Met. Res. 22(1-4) (2009), pp. 318–322. doi:10.1179/136404609X367452.
- [35] D. Luo, I. Chang, J.B. Patel, K. Al-Helal, Y. Huang, G.M. Scamans, and Z. Fan, Microstructure and mechanical properties of recycled AA6111 alloy processed by melt conditioned direct chill (MC-DC) casting. M&Ns-19 (17-19 July 2019), pp. 81–85.
- [36] S.H. Oh, Y. Kauffmann, C. Scheu, W.D. Kaplan, and M. Rühle, Ordered liquid aluminum at the interface with sapphire. Science 310(5748) (2005), pp. 661-663. doi:10.1126/science.1118611.
- [37] H.T. Li, Y. Wang, and Z. Fan, Enhanced heterogeneous nucleation on oxides in Al alloys by intensive shearing. IOP Conf. Ser.: Mater. Sci. Eng. 27 (2012), pp. 012047. doi:10.1088/1757-899X/27/1/012047.
- [38] J.L. Nebreda, J.B. Patel, I. Stone, and G.M. Scamans, De-ironing of aluminium alloy scrap by high shear melt conditioning technology, Proceedings of the 6th Decennial International Conference on Solidification Processing, Old Windsor, July 2017. doi:10.3390/met12101579.
- [39] Z.P. Que, Y.P. Zhou, Y. Wang, and Z. Fan, Effect of MgO on phase selection in Al-Mg-Si-Fe-Mn alloys. Trans. Indian Inst. Met. 68(6) (2015), pp. 1167–1172. doi:10.1007/s12666-015-0664-z.
- [40] H.T. Li, S. Ji, Y. Wang, M. Xia, and Z. Fan, Effect of intensive melt shearing on the formation of Fe-containing intermetallics in LM24 Al-alloy. IOP Conf. Ser.: Mater. Sci. Eng. 27 (2012), pp. 012075. doi:10.1088/1757-899X/27/1/012075.
- [41] H.T. Li, M. Xia, P. Jarry, G.M. Scamans, and Z. Fan, Grain refinement in a AlZnMgCuTi alloy by intensive melt shearing: A multi-step nucleation mechanism. J. Cryst. Growth 314 (2011), pp. 285–292. doi:10.1016/j.jcrysgro.2010.10.168.
- [42] M. Cooper, The crystal structure of the ternary alloy a(AlFeSi). Acta Cryst. 23 (1967), pp. 1106-1107. doi:10.1107/S0365110X67004372.
- [43] K. Matsuda, T. Kawabata, Y. Uetani, T. Sato, and S. Ikeno, Hexagonal tabular β-phase in Al-Mg-Si-Cu alloy. Scr. Mater. 47 (2002), pp. 467-471. doi:10.1016/S1359-6462(02)00173-2.
- [44] C. Li, Y.Y. Wu, H. Li, and X.F. Liu, Morphological evolution and growth mechanism of primary Mg2Si phase in Al-Mg2Si alloys. Acta Mater. 59 (2011), pp. 1058–1067. doi:10.1016/j.actamat.2010.10.036.
- [45] E. Cinkilic, M. Moodispaw, J. Zhang, J. Miao, and A.A. Luo, A new recycled Al-Si-Mg alloy for sustainable structural die casting applications. Metall. Mater. Trans. A 53 (2022), pp. 2861–2873. doi:10.1007/s11661-022-06711-4.
- [46] C.J. Simensen, P. Fartum, and A. Andersen, Analysis of intermetallic particles in aluminium by dissolution of the sample in butanol. Fresenius Z. Anal. Chem. 319 (1984), pp. 286-292. doi:10.1007/BF00487273.
- [47] J. Gjønnes, V. Hansen, S.J. Andersen, C.D. Marioara, and X.Z. Li, Electron crystallography of aluminum alloy phases. Z. Kristallogr. 218 (2003), pp. 293–307. doi:10.1524/zkri.218.4.293.20745.
- [48] N.C.W. Kuijpers, F.J. Vermolen, C. Vuik, P.T.G. Koenis, K.E. Nilsen, and S. van der Zwaag, The dependence of the β-AlFeSi to a-Al(FeMn)Si transformation kinetics in Al-Mg-Si alloys on the alloying elements. Mat. Sci. Eng. A 394 (2005), pp. 9–19. doi:10.1016/j.msea.2004.09.073.
- [49] K. Al-Helal, J.L. Nebreda, J.B. Patel, and G.M. Scamans, High-shear de-gassing and de-ironing of an aluminum casting alloy made directly from aluminum end-of-life vehicle scrap. Recycling 6 (2021), pp. 66. doi:10.3390/recycling6040066.
- [50] N.C.W. Kuijpers, W.H. Kool, P.T.G. Koenis, K.E. Nilsen, I. Todd, and S. van der Zwaag, Assessment of different techniques for quantification of a-Al(FeMn)Si and β-AlFeSi intermetallics in AA6xxx alloys. Mater. Charact. 49 (2002), pp. 409–420. doi:10.1016/S1044-5803(03)00036-6.
- [51] N.C.W. Kuijpers, F.J. Vermolen, K. Vuik, and S. van der Zwaag, A model of the β-AlFeSi to a-Al(FeMn)Si transformation in Al-Mg-Si alloys. Mater. Trans. 44(7) (2003), pp. 1448–1456. doi:10.2320/matertrans.44.1448.
- [52] H. Tanihata, T. Sugawara, K. Matsuda, and S. Ikeno, Effect of casting and homogenizing treatment conditions on the formation of Al-Fe-Si intermetallic compounds in 6063 Al-Mg-Si alloys. J. Mater. Sci. 34 (1999), pp. 1205–1210. doi:10.1023/A:1004504805781.
- [53] D.T.L. Alexander and A.L. Greer, Solid-state intermetallic phase tranformations in 3XXX aluminium alloys. Acta Mater. 50 (2002), pp. 2571–2583. doi:10.1016/S1359-6454(02)00085-X.
- [54] V.S. Zolotorevsky, N.A. Belov, and M.V. Glazoff, Casting Aluminum Alloys, Chapter 2, Elsevier Science Ltd., Amsterdam, 2007.
- [55] S.J. Andersen, C.D. Marioara, J. Friis, R. Bjørge, Q. Du, I.G. Ringdalen, S. Wenner, E.A. Mørtsell, R. Holmestad, T. Saito, J. Røyset, and O. Reiso, Directionality and column arrangement principles of precipiatetes in Al-Mg-Si-(Cu) and Al-Mg-Cu linked to line defect in Al. Mater. Sci. Forum 877 (2016), pp. 461–470. doi:10.4028/www.scientific.net/MSF.877.461.
- [56] T. Saito, E.A. Mørtsell, S. Wenner, C.D. Marioara, S.J. Andersen, J. Friis, K. Matsuda, and R. Holmestad, Atomic structures of precipitates in Al-Mg-Si alloys with small additions of other elements. Adv. Eng. Mater. 20 (2018), pp. 180015. doi:10.1002/adem.201800125.
- [57] S. Pogatscher, H. Antrekowitsch, M. Werinos, F. Moszner, S.S.A. Gerstl, M.F. Francis, W.A. Curtin, J.F. Löffler, and P.J. Uggowitzer, Diffusion on demand to control precipitation aging: application to Al-Mg-Si alloys. Phys. Rev. Lett. 112 (2014), pp. 225701. doi:10.1103/PhysRevLett.112.225701.
- [58] S. Pogatscher, H. Antrekowitsch, H. Leitner, D. Pöschmann, Z.L. Zhang, and P.J. Uggowitzer, Influence of interrupted quenching on artificial aging of Al-Mg-Si alloys. Acta Mater. 60 (2012), pp. 4496–4505. doi:10.1016/j.actamat.2012.04.026.
- [59] S. Pogatscher, H. Antrekowitsch, H. Leitner, T. Ebner, and P.J. Uggowitzer, Mechanisms controlling the artificial aging of Al-Mg-Si alloys. Acta Mater. 59 (2011), pp. 3352-3363. doi:10.1016/j.actamat.2011.02.010.
- [60] S. Qin, A. Bendo, T. Tsuchiya, S. Lee, and K. Matsuda, Effect of cooling rate on precipitation during homogenization cooling in excess Si type Al-Mg-Si alloy. Mater. Lett. 278 (2020), pp. 128363. doi:10.1016/j.matlet.2020.128363.
- [61] S. Qin, A. Bendo, T. Tsuchiya, S. Lee, Y. Zou, and K. Matsuda, Effect of cooling rate on precipitation during homogenization cooling in balanced Al-Mg2Si alloy. Mater. Trans. 61(11) (2020), pp. 2115–2120. doi:10.2320/matertrans.MT-M2020189.
- [62] M.R. Gazizov, A.V. Dubina, D.A. Zhemchuzhnikova, and R.O. Kaibyshev, Effect of equal channel angular pressing and aging on the microstructure and mechanical properties of an Al-Cu-Mg-Si alloy. Phys. Met. Metallogr. 116(7) (2015), pp. 718–729. doi:10.1134/S0031918X15070066.
- [63] M. Gazizov, C.D. Marioara, J. Friis, S. Wenner, R. Holmestad, and R. Kaibyshev, Precipitation behavior in an Al-Cu-Mg-Si alloy during ageing. Mater. Sci. Eng. A 767 (2019), pp. 138369. doi:10.1016/j.msea.2019.138369.
- [64] Y.X. Lai, W. Fan, M.J. Yin, C.L. Wu, and J.H. Chen, Structures and formation mechanisms of dislocation-induced precipitates in relation to the age-hardening responses of Al-Mg-Si alloys. J. Mater. Sci. Technol. 41 (2020), pp. 127–138. doi:10.1016/j.jmst.2019.11.001.
- [65] K. Matsuda, S. Shimizu, H. Gamada, Y. Uetani, F. Shinagawa, and S. Ikeno, Effect of deformation on the precipitates in Al-Mg2Si alloys containing silicon in excess. Mater. Des. Eng. 48(1) (1999), pp. 10–15. doi:10.2472/jsms.48.10.
- [66] E. Thronsen, C.D. Marioara, J.K. Sunde, K. Minakuchi, T. Katsumi, I. Erga, S.J. Andersen, J. Friis, K. Marthinsen, K. Matsuda, and R. Holmestad, The effect of
- [67] E. Thronsen, H. Morkeseth, C.D. Marioara, K. Minakuchi, T. Katsumi, K. Marthinsen, K. Matsuda, and R. Holmestad, The effect of small additions of Fe and heavy deformation on the precipitation in an Al-1.1Mg-0.5Cu-0.3Si at.% alloy. Metall. Mater. Trans. 53 (2022), pp. 3296–3310. doi:10.1007/s11661-022-06744-9.
- [68] K. Matsuda, S. Tada, S. Ikeno, T. Sato, and A. Kamio, Crystal system of rod-shaped precipitates in an Al-1.0mass%Mg2Si-0.4mass%Si alloy. Scr. Metall. Mater. 32(8) (1995), pp. 1175-1180. doi:10.1016/0956-716X(95)00121-B.
- [69] K. Matsuda, S. Ikeno, T. Sato, and A. Kamio, A metastable phase having the orthorhombic crystal lattice in an Al-1.0mass% Mg2Si-0.4mass% Si alloy. Scr. Mater. 34(11) (1996), pp. 1797–1802. doi:10.1016/1359-6462(96)00057-7.
- [70] K. Matsuda, S. Ikeno, T. Sato, and A. Kamio, Classification of metastable phases in Al-Mg2Si alloys by HRTEM. Mater. Sci. Forum 217-222 (1996), pp. 707–712. doi:10.4028/www.scientific.net/MSF.217-222.707.
- [71] S.J. Andersen, C.D. Marioara, R. Vissers, A. Frøseth, and H.W. Zandbergen, The structural relation between precipitates in Al-Mg-Si alloys, the Al-matrix and diamond silicon, with emphasis on the trigonal phase U1-MgAl2Si2. Mater. Sci. Eng. A 444 (2007), pp. 157–169. doi:10.1016/j.msea.2006.08.084.
- [72] S.J. Andersen, C.D. Marioara, A. Frøseth, R. Vissers, and H.W. Zandbergen, Crystal structure of the orthorhombic U2-Al4Mg4Si4 precipitate in the Al-Mg-Si alloy system and its relation to the β' and β” phases. Mater. Sci. Eng. A 390 (2005), pp. 127–138. doi:10.1016/j.msea.2004.09.019.
- [73] S.J. Andersen, C.D. Marioara, A. Frøseth, R. Vissers, and H.W. Zandbergen, Crystal structures of the trigonal U1-MgAl2Si2 and orthorhombic U2-Mg4Al4Si4 precipitates in the Al-Mg-Si alloy system. I. Phys. Conf. Ser. 179 (2003), pp. 225.
- [74] K. Matsuda, Y. Uetani, T. Sato, and S. Ikeno, Metastable phases in an Al-Mg-Si alloy containing copper. Metall. Mater. Trans. A 32 (2001), pp. 1293–1299. doi:10.1007/s11661-001-0219-2.
- [75] K. Matsuda, D. Teguri, Y. Uetani, T. Sato, and S. Ikeno, Cu-seggregation at the Q'/α-Al interface in Al-Mg-Si-Cu alloy. Scr. Mater. 47 (2002), pp. 833–837. doi:10.1016/S1359-6462(02)00325-1.
- [76] S. Wenner, C.D. Marioara, S.J. Andersen, and R. Holmestad, Effect of room temperature storage time on precipitation in Al-Mg-Si(-Cu) alloys with different Mg/Si ratios. Int. J. Mater. Res. 103 (2012), pp. 948–954. doi:10.3139/146.110795.
- [77] H.S. Hasting, J.C. Walmsley, A.T.J. Van Helvoort, C.D. Marioara, S.J. Andersen, and R. Holmestad, Z-contrast imaging of the arrangement of Cu in precipitates in 6XXX-series aluminium alloys. Philos. Mag. Lett. 86(9) (2006), pp. 589–597. doi:10.1080/09500830600938340.
- [78] C.D. Marioara, S.J. Andersen, T.N. Stene, H. Hasting, J. Walmsley, A.T.J. Van Helvoort, and R. Holmestad, The effect of Cu on precipitation in Al-Mg-Si alloys. Philos. Mag. 87(23) (2007), pp. 3385–3413. doi:10.1080/14786430701287377.
- [79] L. Arnberg and B. Aurivillius, The crystal structure of AlxCu2Mg12-xSi7 (h-AlCuMgSi). Acta Chem. Scand. 34a (1980), pp. 1–5.
- [80] M. Torsaeter, R. Vissers, C.D. Marioara, S.J. Andersen, and R. Holmestad, Crystal structure determination of the Q' and C-type plate precipitates in Al-Mg-Si-Cu (6xxx) alloys, in Jürgen Hirsch, Birgit Skrotzki, Günter Gottstein (Eds.), Aluminium Alloys: Their Physical and Mechanical Properties, vol. 2, Wiley-VHC, Aachen, 2008.
- [81] M. Fiawoo, X. Gao, L. Bourgeois, N. Parson, X.Q. Zhang, M. Couper, and J.F. Nie, Formation of multiple orientation relationships of Q precipitates in Al-Mg-Si-Cu alloys. Scr. Mater. 88 (2014), pp. 53–56. doi:10.1016/j.scriptamat.2014.05.013.
- [82] M. Torsaeter, W. Lefebvre, C.D. Marioara, S.J. Andersen, J.C. Walmsley, and R. Holmestad, Study of intergrown L and Q' precipitates in Al-Mg-Si-Cu alloys. Scr. Mater. 64 (2011), pp. 817–820. doi:10.1016/j.scriptamat.2011.01.008.
- [83] G.M. Scamans, N.J.H. Holroyd, and C.D.S. Tuck, The role of magnesium segregation in the intergranular stress corrosion cracking of aluminium alloy. Corros. Sci. 27(4) (1987), pp. 329–347. doi:10.1016/0010-938X(87)90076-Χ.
- [84] X. Sauvage, N. Enikeev, R. Valiev, Y. Nasedkina, and M. Murashkin, Atomic-scale analysis of the segregation and precipitation mechanisms in a severely deformed Al-Mg alloy. Acta Mater. 72 (2014), pp. 125–136. doi:10.1016/j.actamat.2014.03.033.
- [85] M. de Hass and J.T.M. De Hosson, Grain boundary segregation and precipitation in aluminium alloys. Scripta Mater. 44 (2001), pp. 281-286. doi:10.1016/S1359-6462(00)00577-7.
- [86] K. Teichmann, C.D. Marioara, S.J. Andersen, and K. Marthinsen, The effect of preaging deformation on the precipitation behavior of an Al-Mg-Si alloy. Metall. Mater. Trans. A 43 (2012), pp. 4006–4014. doi:10.1007/s11661-012-1235-0.
9. 저작권:
- 본 자료는 "Artenis Bendo, Jonathan Fellowes, Matthew Smith, Masoud Moshtaghi, Zelong Jin, Kenji Matsuda, Zhongyun Fan & Xiaorong Zhou"의 논문: "Solute micro-segregation profile and associated precipitation in cast Al-Mg-Si alloy"를 기반으로 합니다.
- 논문 출처: https://doi.org/10.1080/14786435.2024.2336012
본 자료는 상기 논문을 기반으로 요약되었으며, 상업적 목적으로 무단 사용하는 것을 금지합니다.
Copyright © 2025 CASTMAN. All rights reserved.