본 논문 요약은 "[주조 과학 발전을 위한 액체 알루미늄 흐름 시각화의 새로운 접근 방식]" 논문을 기반으로 작성되었으며, "[MDPI Materials]"에 발표되었습니다.
1. 개요:
- 제목: A Novel Approach to Visualize Liquid Aluminum Flow to Advance Casting Science(주조 과학 발전을 위한 액체 알루미늄 흐름 시각화의 새로운 접근 방식)
- 저자: Casey Bate, Philip King, Jay Sim, Guha Manogharan
- 발행 연도: 2023년
- 발행 저널/학술 단체: Materials (MDPI)
- 키워드: 금형 충전; 사형 주조; 석신산니트릴; 주조 유체역학; 수조 모형; 금속 유사체; 흐름 시뮬레이션
![Figure 1. Casting geometry based on prior experimental study [17], units in mm](https://castman.co.kr/wp-content/uploads/image-361-png.webp)
2. 연구 배경:
연구 주제의 사회적/학문적 맥락:
사형 주조에서 용융 금속의 난류 충전은 박막, 기공, 산화물 개재물과 같은 주조 결함의 주요 원인으로 알려져 있습니다. 이러한 결함은 기계적 성질을 저하시키고 사형 주조품의 불량률을 높입니다. 따라서 사형 금형 내 금속 흐름, 즉 주조 유체역학을 이해하고 제어하는 것은 결함 최소화에 매우 중요합니다. 수치 시뮬레이션 방법이 이 현상을 모델링하는 데 광범위하게 적용되어 왔지만, 실험적 검증은 열악한 주조 환경과 고가의 X선 장비의 한계로 인해 어려움을 겪어왔습니다.
기존 연구의 한계:
사형 금형 내 금속 흐름을 시각화하기 위한 기존의 실험적 접근 방식은 상당한 어려움에 직면해 있습니다. 불투명한 사형 금형의 특성과 열악한 주조 환경(고온, 가스 방출, 연마성 모래, 습도)은 직접적인 관찰과 데이터 획득을 제한합니다. 이전 연구에서 X선 장비를 활용한 흐름 시각화는 정성적 데이터만 제공할 수 있었고, 분석 가능한 형상, 높은 비용, 안전 문제, 그리고 와류와 같은 복잡한 3차원 흐름 현상을 포착하지 못하는 2차원 이미징의 한계로 인해 제약이 있었습니다. 수조 모형 실험이 비용 효율적인 유사체로 사용되어 왔지만, 열유체 속성이 용융 금속과 다르고 상온에서 응고되지 않는다는 점은 용융 금속 거동을 정확하게 나타내는 데 대한 우려를 제기합니다.
연구의 필요성:
주조 과학을 발전시키고 결함을 최소화하기 위해서는 사형 금형 내 액체 금속 흐름을 정확하게 시각화하고 분석할 수 있는 개선된 실험 기술이 절실히 필요합니다. 본 연구는 수조 모형보다 더 대표적인 흐름 시각화를 제공하고 덜 제한적인 조건에서 실험할 수 있는 대체 금속 유사체 재료를 사용하여 이러한 격차를 해소하고자 합니다.
3. 연구 목적 및 연구 질문:
연구 목적:
본 연구의 주요 목적은 석신산니트릴(Succinonitrile, SCN)이 사형 주조 실험에서 액체 금속 흐름, 특히 용융 알루미늄 흐름을 시각화하는 데 있어 수조 모형의 대안으로서 적합한지 평가하는 것입니다. 본 연구는 SCN이 독특한 속성을 통해 용융 금속의 흐름 거동을 효과적으로 모방할 수 있는지 확인하는 것을 목표로 합니다.
주요 연구 질문:
- 석신산니트릴(SCN)은 주조 공정에서 액체 알루미늄 흐름을 시각화하는 데 있어 수조 모형보다 더 정확한 금속 유사체 역할을 할 수 있는가?
- SCN을 사용한 정확한 금속 흐름 유사체 실험을 달성하기 위해 고려해야 할 중요한 무차원수는 무엇인가?
- SCN 흐름 거동은 유사한 주조 조건에서 수조 모형 및 용융 알루미늄 흐름과 비교하여 실험적으로나 수치 시뮬레이션을 통해 어떻게 나타나는가?
연구 가설:
본 연구는 석신산니트릴(SCN)이 용융 알루미늄과 유사한 체심 입방(Body-Centered-Cubic, BCC) 결정 구조와 수지상 응고 특성, 그리고 관리 가능한 용융 온도(~60 °C)를 가지고 있어 수조 모형보다 우수한 금속 유사체라고 가정합니다. 또한, 본 연구는 Froude 수와 벽면 거칠기가 주조 실험에서 정확한 금속 흐름 유사성을 달성하는 데 중요한 무차원 변수라고 가정합니다.
4. 연구 방법론
연구 설계:
본 연구는 액체 흐름 거동을 분석하기 위해 실험적 조사와 수치 시뮬레이션을 결합한 혼합 방법론적 접근 방식을 채택했습니다.
자료 수집 방법:
실험은 이전 연구 [17] (그림 1)의 벤치마크 사형 주조 형상을 재현한 투명 아크릴 금형에서 작동 유체로 물과 SCN을 모두 사용하여 수행되었습니다. 흐름 시각화는 300fps의 고속 비디오 녹화를 통해 달성되었으며, SCN의 가시성을 높이기 위해 녹색 식용 색소를 첨가했습니다. 수치 시뮬레이션은 Flow3D Cast 소프트웨어를 사용하여 유사한 조건에서 알루미늄, 물, SCN의 흐름을 모델링하기 위해 수행되었습니다.
분석 방법:
본 연구는 흐름 패턴의 시각적 분석을 통한 정성적 비교와 금형 충전 시간 및 스프루와 러너에서의 평균 속도 측정을 통한 정량적 비교를 통해 물, SCN, 시뮬레이션된 알루미늄의 흐름 프로파일을 비교했습니다. 무차원수, 특히 Froude 수, Reynolds 수, Weber 수를 계산하고 분석하여 서로 다른 유체 간의 흐름 유사성에 미치는 영향을 확인했습니다. 실험 결과는 수치 시뮬레이션 결과 및 알루미늄 흐름의 벤치마크 X선 실험 데이터 [17]와도 비교되었습니다.
연구 대상 및 범위:
본 연구는 벤치마크 알루미늄 판재(10 mm × 200 mm × 100 mm) [17] 주조를 위해 설계된 단순화된 하부 게이트 사형 주조 형상에서의 액체 흐름 거동에 초점을 맞췄습니다. 본 연구는 물과 SCN을 유사 유체로 사용하고 용융 알루미늄 흐름을 비교 기준으로 삼았습니다. 범위는 금형 충전 단계로 제한되었으며, 응고 측면은 주로 SCN을 유사체 재료로 선택하는 맥락에서 고려되었습니다.
5. 주요 연구 결과:
주요 연구 결과:
실험 결과 SCN 흐름 실험이 수조 모형 실험에 비해 용융 알루미늄의 흐름 프로파일을 더 정확하게 재현하는 것으로 나타났습니다. 특히, "실험 결과 SCN 흐름 실험이 용융 알루미늄의 흐름 프로파일을 더 정확하게 재현하여 금속 흐름 연구를 위한 금속 유사체로서의 유용성을 입증했습니다." 본 연구는 Froude 수와 벽면 거칠기가 정확한 금속 흐름 유사체 실험을 달성하는 데 중요한 무차원 변수임을 확인했습니다.
통계적/정성적 분석 결과:
흐름 패턴의 정성적 비교 (그림 7, 그림 8, 그림 9, 그림 11, 그림 12, 그림 13, 그림 14)는 SCN 흐름이 수조 모형 흐름보다 이전 X선 연구 [17]의 알루미늄 흐름과 시각적으로 더 유사함을 보여주었습니다. 정량적 분석 (표 9, 표 10, 표 11)은 수조 모형에서 Reynolds 수를 일치시키면 유사한 충전 시간이 나타나지만, 흐름 거동은 여전히 SCN에 비해 알루미늄을 덜 대표하는 것으로 나타났습니다. 더 높은 Froude 수 실험은 더 높은 속도와 더 짧은 충전 시간을 나타냈습니다 (표 9).
데이터 해석:
연구 결과는 수조 모형에서 Reynolds 수 유사성이 충전 시간의 유사성을 어느 정도 제공할 수 있지만, 용융 금속 흐름 패턴의 정확한 표현을 보장하지는 않는다는 것을 시사합니다. Froude 수 유사성이 전체 흐름 역학을 포착하는 데 더 중요한 것으로 보입니다. SCN은 Reynolds 수가 더 낮음에도 불구하고 (SCN의 경우 6800, 알루미늄의 경우 28,000), 수조 모형보다 용융 알루미늄과 질적으로 더 유사한 흐름 패턴을 나타내어 무차원수 일치 외에도 재료 속성의 중요성을 시사합니다. 본 연구는 Moody 선도 분석 (그림 15)에서 나타난 바와 같이 벽면 거칠기와 압력 강하가 흐름 유사성에 미치는 잠재적 영향도 강조했습니다.
그림 목록:
- 그림 1. 이전 실험 연구 [17]를 기반으로 한 주조 형상, 단위 mm.
- 그림 2. [17] 연구의 충전 이미지.
- 그림 3. 금형 부품의 CAD 설계.
- 그림 4. 조립된 아크릴 금형의 예 (초기 실험에서).
- 그림 5. (a) 0.7초 (b) 0.9초 (c) 1초 (d) 1.2초에서 SCN, 알루미늄, 물의 시뮬레이션 결과.
- 그림 6. 예상되는 알루미늄 흐름 조건.
- 그림 7. Fr 불일치 (왼쪽) vs. Fr 일치 (오른쪽)에 대한 수조 모형 실험 결과 (a) 플러그 제거 후 0.5초, (b) 0.74초 (c) 1초, (d) 1.24초.
- 그림 8. Re 불일치 (왼쪽) vs. Re 일치 (오른쪽)에 대한 수조 모형 실험 결과 (a) 플러그 제거 후 0.5초, (b) 0.74초 (c) 1초, (d) 1.24초.
- 그림 9. 석신산니트릴 실험 결과 (a) 플러그 제거 후 0.5초, (b) 0.74초 (c) 1초, (d) 1.24초.
- 그림 10. SLA 프린팅 채널의 물 (왼쪽)과 SCN (오른쪽).
- 그림 11. 사형 금형의 알루미늄 (왼쪽 [17]), 사형 금형 시뮬레이션의 알루미늄 (중간), 일치된 SCN 시각화 (오른쪽).
- 그림 12. 사형 금형의 알루미늄 (왼쪽), 사형 금형 시뮬레이션의 물 (왼쪽 중간), Fr 불일치 아크릴의 물 (오른쪽 중간), Fr 일치 아크릴의 물 (오른쪽).
- 그림 13. 사형 금형의 알루미늄 (왼쪽), 사형 금형 시뮬레이션의 물 (왼쪽 중간), Re 불일치 아크릴의 물 (오른쪽 중간), Re 일치 아크릴의 물 (오른쪽).
- 그림 14. 사형 금형의 알루미늄 (왼쪽), 사형 금형 시뮬레이션의 석신산니트릴 (중간), 아크릴의 석신산니트릴 (오른쪽).
- 그림 15. Moody 선도 61 아크릴에서 물 Re ≈ >28,000 (2) 아크릴에서 SCN Re ≈ 6800 (3) Re ≈ 28,000에서 물질의 상대적 거칠기는 SCN으로 인해 발생하는 압력 강하와 관련이 있습니다.
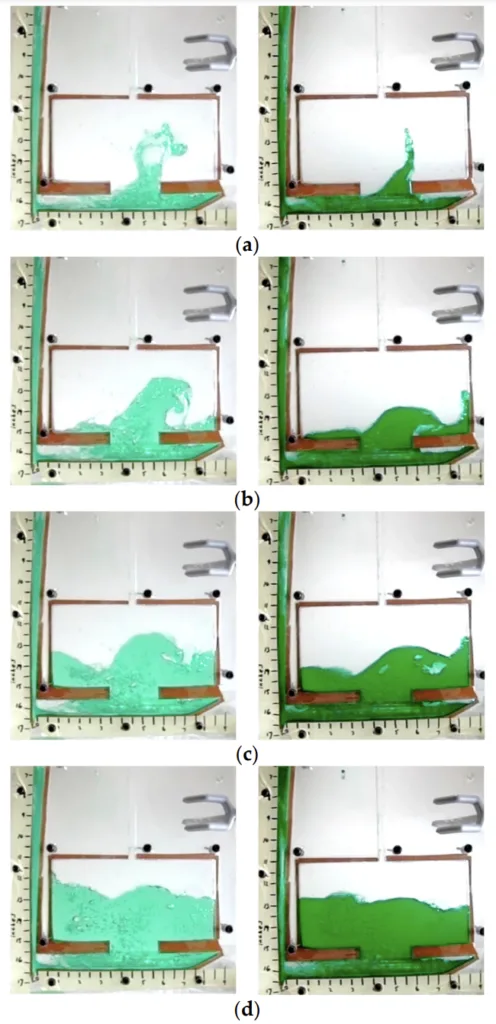
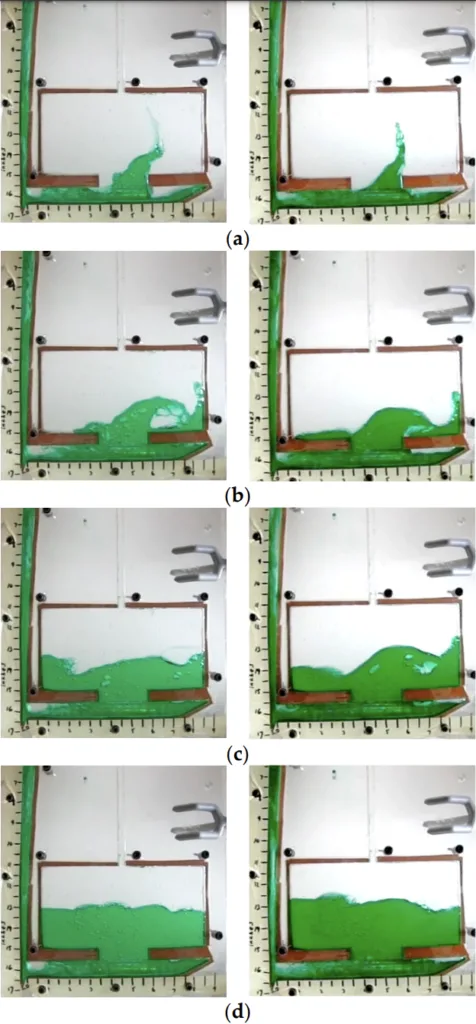
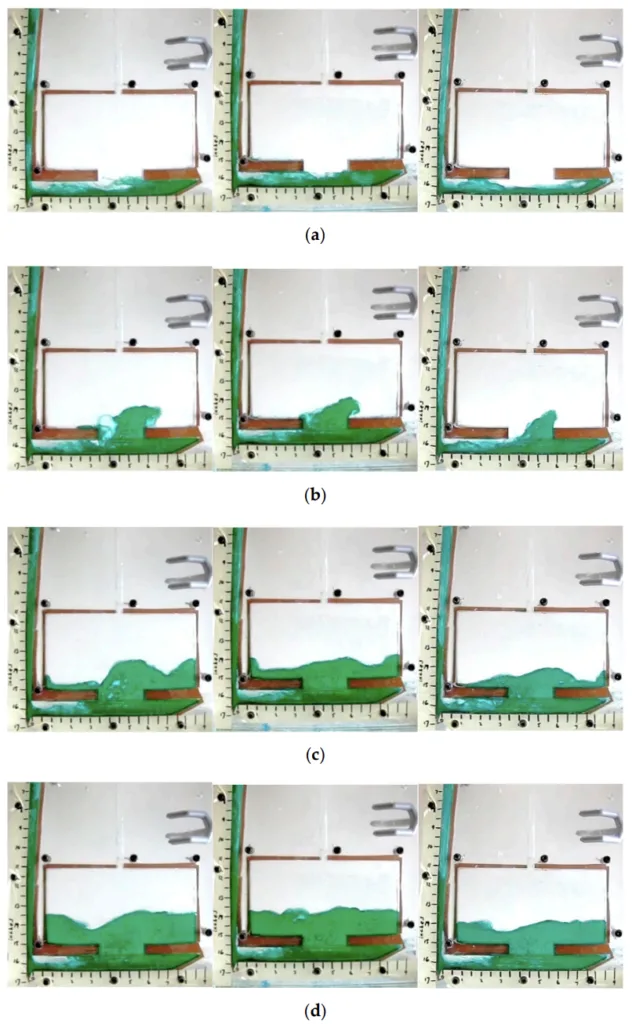
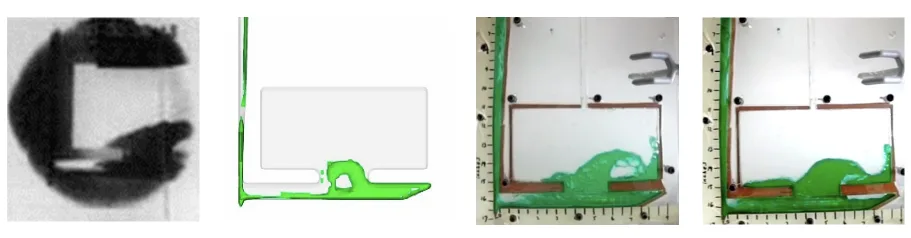
6. 결론 및 논의:
주요 결과 요약:
본 연구는 석신산니트릴(SCN)이 사형 주조 실험에서 액체 알루미늄 흐름을 시각화하는 데 있어 수조 모형보다 더 효과적인 금속 유사체라는 결론을 내립니다. 특히, "실험 결과 SCN 흐름 실험이 용융 알루미늄의 흐름 프로파일을 더 정확하게 재현하여 금속 흐름 연구를 위한 금속 유사체로서의 유용성을 입증했습니다." 수조 모형이 단순화된 표현을 제공할 수 있지만, SCN은 용융 금속과 더 유사한 재료 속성을 통해 흐름 거동에 대한 더 정확한 정성적 및 잠재적으로 정량적 표현을 제공합니다. 본 연구는 유사체 실험에서 Froude 수 유사성의 중요성을 강조하고 벽면 거칠기와 압력 강하가 흐름 유사성에 영향을 미치는 중요한 요인이며, 엄격한 Reynolds 수 일치보다 더 중요할 수 있음을 시사합니다.
연구의 학문적 의의:
본 연구는 주조 유체역학 실험을 통해 SCN을 적용하여 주조 연구를 위한 용융 흐름을 정확하게 시각화한 최초의 보고입니다. 이는 금속 흐름 시각화 기술에 대한 기본적인 이해에 기여하고 SCN을 주조 연구를 위한 귀중한 도구로 사용하는 것을 입증합니다. 연구 결과는 수조 모형과 Reynolds 수 유사성에 대한 과도한 의존성에 도전하고 정확한 유사체 실험을 위해서는 다른 무차원수와 재료 속성을 고려해야 할 필요성을 강조합니다.
실용적 의미:
SCN의 금속 유사체로서의 성공적인 적용은 고가의 복잡한 주조 실험 또는 X선 시설에 대한 의존도를 줄여 실험실 환경에서 주조 유체역학에 대한 실험적 조사를 위한 새로운 길을 열어줍니다. "본 연구의 결과는 러너, 인게이트, 통합 충전-피딩-응고 연구와 같은 향후 금속 흐름 분석에 활용될 수 있습니다." 이러한 접근 방식은 특히 적층 제조로 구현되는 복잡한 형상에 대한 혁신적인 게이팅 시스템의 설계 및 검증을 용이하게 하고 통합 흐름-응고 시뮬레이션을 위한 보다 정확한 수치 모델 개발에 기여할 수 있습니다. 본 논문에 상세히 기술된 방법론은 또한 "혁신적인 게이팅 형상의 검증을 위한 로드맵"을 제공합니다.
연구의 한계:
본 연구는 사형 금형과 다른 열적 특성 및 표면 거칠기를 갖는 아크릴 금형의 사용을 포함한 한계를 인정합니다. "아크릴 금형의 제한된 열용량은 SCN을 더 높은 온도에서 주입하는 것을 금지하여 금형의 심각한 균열을 초래할 수 있으며 아크릴에 대한 대체 재료가 향후 연구의 초점이 될 것입니다." 또한, 본 연구는 주로 흐름 시각화에 초점을 맞추고 흐름 조건과 결과적인 응고 거동의 복합적인 영향은 완전히 탐구하지 않았습니다.
7. 향후 후속 연구:
후속 연구 방향:
향후 연구에서는 사형 금형 조건을 더 잘 모방하기 위해 개선된 열용량과 제어 가능한 표면 거칠기를 가진 대체 투명 금형 재료를 탐구해야 합니다. SCN을 금속 유사체로서 최대한 활용하기 위해 SCN을 사용한 흐름과 응고의 복합적인 영향에 대한 추가 연구가 필요합니다. "또한, 향후 연구에서는 용융 흐름에서 흔히 발생하는 산화물 박막을 더 정확하게 모방하기 위해 표면에 산화물을 형성하는 액체 금속과 유사한 물질을 탐구해야 합니다."
추가 탐구가 필요한 영역:
추가 탐구가 필요한 영역은 다음과 같습니다.
- 맞춤형 열적 및 표면 속성을 가진 고급 투명 재료 조사.
- 주조 조건에서 SCN의 응고 거동과 금속 응고와의 상관 관계 연구.
- 용융 금속 거동을 더 잘 나타내기 위해 SCN 실험에서 표면 산화물 형성을 통합하는 방법 개발.
- 금형 내에서 정량적 실시간 속도 측정을 위해 정전 용량 센서 또는 기타 센서를 SCN 기반 실험에 통합. "마지막으로, 정전 용량 센서를 금형에 통합하면 기존 사형 금형에서 금속 흐름의 상세 속도에 대한 참조를 제공할 수 있습니다 [62]."
8. 참고 문헌:
- EPA Metal Casting 2016. Available online: https://archive.epa.gov/sectors/web/html/casting.html (accessed on 7 December 2022).
- Shinde, V.D.; Mhamane, D.A. Evaluation of Sand Quality in Thermal Sand Reclamation System. Therm. Sci. Eng. 2018, 2, 538.
[CrossRef] - Campbell, J. Entrainment Defects. Mater. Sci. Technol. 2006, 22, 127–145. [CrossRef]
- Cross, M.; McBride, D.; Croft, T.N.; Williams, A.J.; Pericleous, K.; Lawrence, J.A. Computational Modeling of Mold Filling and
Related Free-Surface Flows in Shape Casting: An Overview of the Challenges Involved. Metall. Mater. Trans. B 2006, 37, 879–885.
[CrossRef] - Mi, J.; Harding, R.A.; Campbell, J. Effects of the Entrained Surface Film on the Reliability of Castings. Metall. Mater. Trans. A 2004,
35, 2893–2902. [CrossRef] - Campbell, J. Complete Casting Handbook, 1st ed.; Elsevier: Amsterdam, The Netherlands, 2015; ISBN 9780444635099.
- Dai, X.; Yang, X.; Campbell, J.; Wood, J. Effects of Runner System Design on the Mechanical Strength of Al-7Si-Mg Alloy Castings.
Mater. Sci. Eng. A 2003, 354, 315–325. [CrossRef] - Tiryakio ˘glu, M.; Campbell, J.; Alexopoulos, N.D. Quality Indices for Aluminum Alloy Castings: A Critical Review. Metall. Mater.
Trans. B 2009, 40, 802–811. [CrossRef] - Sama, S.R.; Wang, J.; Manogharan, G. Non-Conventional Mold Design for Metal Casting Using 3D Sand-Printing. J. Manuf.
Process. 2018, 34, 765–775. [CrossRef] - Sama, S.R.; Badamo, T.; Lynch, P.; Manogharan, G. Novel Sprue Designs in Metal Casting via 3D Sand-Printing. Addit. Manuf.
2019, 25, 563–578. [CrossRef] - Cleary, P.W.; Ha, J. Three-Dimensional Smoothed Particle Hydrodynamics Simulation of High Pressure Die Casting of Light
Metal Components. J. Light Met. 2002, 2, 169–183. [CrossRef] - Kermanpur, A.; Mahmoudi, S.; Hajipour, A. Numerical Simulation of Metal Flow and Solidification in the Multi-Cavity Casting
Moulds of Automotive Components. J. Mater. Process. Technol. 2008, 206, 62–68. [CrossRef] - Renukananda, K.H.; Ravi, B. Multi-Gate Systems in Casting Process: Comparative Study of Liquid Metal and Water Flow. Mater.
Manuf. Process. 2016, 31, 1091–1101. [CrossRef] - Sutaria, M.; Ravi, B. Computation of Casting Solidification Feed-Paths Using Gradient Vector Method with Various Boundary
Conditions. Int. J. Adv. Manuf. Technol. 2014, 75, 209–223. [CrossRef] - Sutaria, M.; Gada, V.H.; Sharma, A.; Ravi, B. Computation of Feed-Paths for Casting Solidification Using Level-Set-Method. J.
Mater. Process. Technol. 2012, 212, 1236–1249. [CrossRef] - Lee, P.; Chirazi, A.; See, D. Modeling Microporosity in Aluminum–Silicon Alloys: A Review. J. Light Met. 2001, 1, 15–30. [CrossRef]
- Sirrell, B.; Holliday, M.; Campbell, J. Benchmark Testing the Flow and Solidification Modeling of Al Castings. JOM 1996, 48, 20–23.
[CrossRef] - Kashiwai, S.; Ohnaka, I.; Kimatsuka, A.; Kaneyoshi, T.; Ohmichi, T.; Zhu, J. Numerical Simulation and X-Ray Direct Observation
of Mould Filling during Vacuum Suction Casting. Int. J. Cast Met. Res. 2005, 18, 144–148. [CrossRef] - Di Sabatino, M.; Syvertsen, F.; Arnberg, L.; Nordmark, A. An Improved Method for Fluidity Measurement by Gravity Casting of
Spirals in Sand Moulds. Int. J. Cast Met. Res. 2005, 18, 59–62. [CrossRef] - Sulaiman, S.; Hamouda, A.M.S. Modelling and Experimental Investigation of Solidification Process in Sand Casting. J. Mater.
Process. Technol. 2004, 155–156, 1723–1726. [CrossRef] - Johnson, W.H.; Bishop, H.F.; Pellini, W.S. Gating Factors. Foundry 1954, 102–272.
- Richins, D.S.; Wetmore, W.O. Fluid Mechanics Applied to Founding. AFS Trans. 1951, 1–24.
- Skov-Hansen, S.; Green, N.R.; Tiedje, N.S. Experimental Analysis of Flow of Ductile Cast Iron in Stream Lined Gating Systems.
Giessereiforschung. 2009, 60. - Tiedje, N. Flow through Bends in Gating Systems in Vertically Parted Moulds. AFS Trans. 1999, 581–590.
- Tiedje, N.S.; Larsen, P. Investigation of the Stability of Melt Flow in Gating Systems. Metall. Mater. Trans. B Process Metall. Mater.
Process. Sci. 2011, 42, 189–201. [CrossRef] - Cao, H.; Shen, C.; Wang, C.; Xu, H.; Zhu, J. Direct Observation of Filling Process and Porosity Prediction in High Pressure Die
Casting. Materials 2019, 12, 1099. [CrossRef] [PubMed] - Thomas, B.G.; Mika, L.J.; Najjar, F.M. Simulation of Fluid Flow inside a Continuous Slab-Casting Machine. Metall. Trans. B 1990,
21, 387–400. [CrossRef] - Thomas, B.G.; Najjar, F.M. Finite Element Modelling of Turbulent Fluid Flow and Heat Transfer in Continuous Casting. Appl.
Math. Model. 1991, 15, 226–243. [CrossRef] - Sahai, Y.; Emi, T. Criteria for Water Modeling of Melt Flow and Inclusion Removal in Continuous Casting Tundishes. ISIJ Int.
1996, 36, 1166–1173. [CrossRef] - Kuyucak, S. Sponsored Research: Clean Steel Casting Production—Water Modeling Studies of Bottom-Pouring Ladle Operations.
Trans. Am. Foundry Soc. 2006, 114, 811–818. - Beckermann, C. Water Modeling of Steel Flow, Air Entrainment and Filtration. In Proceedings of the 46th SFSA Technical and
Operating Conference, Chicago, IL, USA, 4–7 November 1992; pp. 1–18. - Derollez, P.; Lefebvre, J.; Descamps, M.; Press, W.; Fontaine, H. Structure of Succinonitrile in Its Plastic Phase. J. Phys. Condens.
Matter 1990, 2, 6893–6903. [CrossRef] - Glicksman, M.E.; Schaefer, R.J.; Ayres, J.D. Dendritic Growth—A Test of Theory. Metall. Trans. A 1976, 7, 1747–1759. [CrossRef]
- Janz, G.J.; Fitzgerald, W.E. Infrared Spectrum and Molecular Structure of Succinonitrile. J. Chem. Phys. 1955, 23, 1973–1974.
[CrossRef] - Fitzgerald, W.E.; Janz, G.J. Vibrational Spectra and Molecular Structure of 1,2-Dicyanoethane. J. Mol. Spectrosc. 1957, 1, 49–60.
[CrossRef] - Weinberg, F.; Chalmers, B. Dendritic Growth in Lead. Can. J. Phys. 1951, 29, 382. [CrossRef]
- Weinberg, F.; Chalmers, B. Further Observations on Dendritic Growth in Metals. Can. J. Phys. 1952, 30, 488. [CrossRef]
- Chalmers, B. The Preparation of Single Crystals and Bicrystals by the Controlled Solidification of Molten Metals. Can. J. Phys.
1953, 31, 132. [CrossRef] - Huang, S.C.; Glicksman, M.E. Overview 12: Fundamentals of Dendritic Solidification-I. Steady-State Tip Growth. Acta Metall.
1981, 29, 701–715. [CrossRef] - Teng, J.; Liu, S. Re-Determination of Succinonitrile (SCN)–Camphor Phase Diagram. J. Cryst. Growth 2006, 290, 248–257. [CrossRef]
- Shang, S.; Han, Z.; Luo, A.A. Study on the Response of Dendritic Growth to Periodic Increase–Decrease Pressure in Solidification
via in Situ Observation Using Succinonitrile. J. Cryst. Growth 2018, 498, 85–92. [CrossRef] - Losert, W.; Shi, B.Q.; Cummins, H.Z. Evolution of Dendritic Patterns during Alloy Solidification: From the Initial Instability to the
Steady State. Proc. Natl. Acad. Sci. USA 1998, 95, 439–442. [CrossRef] - Karma, A.; Lee, Y.H.; Plapp, M. Three-Dimensional Dendrite-Tip Morphology at Low Undercooling. Phys. Rev. E 2000, 61,
3996–4006. [CrossRef] - Jeong, J.-H.; Dantzig, J.A.; Goldenfeld, N. Dendritic Growth with Fluid Flow in Pure Materials. Metall. Mater. Trans. A 2003, 34,
459–466. [CrossRef] - Trivedi, R.; Shen, Y.; Liu, S. Cellular-to-Dendritic Transition during the Directional Solidification of Binary Alloys. Metall. Mater.
Trans. A 2003, 34, 395–401. [CrossRef] - Chopra, M.A.; Glicksman, M.E.; Singh, N.B. Dendritic Solidification in Binary Alloys. Metall. Trans. A Phys. Metall. Mater. Sci.
1988, 19, 3087–3096. [CrossRef] - Shen, H.F.; Beckermann, C. An Experimental Study of Deformation of a Columnar Dendritic Mushy Zone Using a Transparent
Succinonitrile-Acetone Alloy. Metall. Mater. Trans. B Process Metall. Mater. Process. Sci. 2002, 33, 69–78. [CrossRef] - Esaka, H.; Wakabayashi, T.; Shinozuka, K.; Tamura, M. Origin of Equiaxed Grains and Their Motion in the Liquid Phase. ISIJ Int.
2003, 43, 1415–1420. [CrossRef] - Khalifa, W.; Tsunekawa, Y.; Okumiya, M. Ultrasonic Grain Refining Effects in A356 Al-Si Cast Alloy. AFS Trans. 2010, 91–98.
- Bryne, O. Performance Comparison of C-Si, Mc-Si and a-Si Thin Film PV by PVsyst Simulation. J. Optoelectron. Adv. Mater. 2013,
15, 326–334. [CrossRef] - Tin, P.; de Groh, H.C., III. Surface Tension and Viscosity of Succinonitrile—Acetone Alloys Using Surface Light Scattering
Spectrometer. Int. J. Thermophys. 2004, 25, 1143–1153. [CrossRef] - Ceynar, D.L.; Beckermann, C. Measurement of the Density of Succinonitrile—Acetone Alloys. J. Cryst. Growth 2001, 222, 380–391.
[CrossRef] - Petrakis, L.; Rao, A. Rotational Transition and Self-Diffusion in Polycrystalline Succinonitrile. J. Chem. Phys. 1963, 39, 1633–1635.
[CrossRef] - Sigma-Aldrich. Material Safety Data Sheet. 2018, pp. 1–8. Available online: https://www.sigmaaldrich.com/US/en/sds/
aldrich/160962 (accessed on 7 December 2022). - Hockaday, L.A. Rapid 3D Printing of Anatomically Accurate and Mechanically Heterogeneous Aortic Valve Hydrogel Scaffolds.
Int. Soc. Biofabr. 2012, 4, 035005. [CrossRef] [PubMed] - Morgan, A.J.L.; Hidalgo, L.; Jose, S.; Jamieson, W.D.; Wymant, M.; Song, B.; Stephens, P.; Barrow, D.A.; Castell, O.K. Simple and
Versatile 3D Printed Microfluidics Using Fused Filament Fabrication. PLoS ONE 2016, 11, e0152023. [CrossRef] [PubMed] - Cooper, D.E.; Stanford, M.; Kibble, K.A.; Gibbons, G.J. Additive Manufacturing for Product Improvement at Red Bull Technology.
J. Mater. 2012, 41, 226–230. [CrossRef] - Amili, O.; Schiavazzi, D.; Moen, S.; Jagadeesan, B. Hemodynamics in a Giant Intracranial Aneurysm Characterized by in Vitro 4D
Flow MRI. PLoS ONE 2018, 13, e0188323. [CrossRef] - Kinstlinger, I.S.; Miller, J.S.; Miller, J.S.; Miller, J.S. 3D-Printed Fluidic Networks as Vasculature for Engineered Tissue. Lab Chip
2016, 16, 2025–2043. [CrossRef] - Klein, J.; Stern, M.; Franchin, G.; Kayser, M.; Inamura, C.; Dave, S.; Weaver, J.C.; Houk, P.; Colombo, P.; Yang, M.; et al. Additive
Manufacturing of Optically Transparent Glass. 3D Print. Addit. Manuf. 2015, 2, 92–105. [CrossRef] - Munson, B.R.; Young, F.D.; Okiishi, T.H. Fundamentals of Fluid Mechanics; John Wiley & Sons: Hoboken, NJ, USA, 2006; ISBN
978-0-471-67582-2. - Sama, S.R.; MacDonald, E.; Voigt, R.; Manogharan, G. Manogharan Measurement of Metal Velocity in Sand Casting during Mold
Filling. Metals 2019, 9, 1079. [CrossRef]
Disclaimer/Publisher’s Note: The statements, opinions and data contained in all publications are solely those of the individual
author(s) and contributor(s) and not of MDPI and/or the editor(s). MDPI and/or the editor(s) disclaim responsibility for any injury to
people or property resulting from any ideas, methods, instructions or products referred to in the content.
9. 저작권:
본 자료는 "[Casey Bate, Philip King, Jay Sim and Guha Manogharan]"의 논문: "[주조 과학 발전을 위한 액체 알루미늄 흐름 시각화의 새로운 접근 방식]"을 기반으로 합니다.
논문 출처: https://doi.org/10.3390/ma16020756
본 자료는 위 논문을 기반으로 요약되었으며, 상업적 목적으로 무단 사용하는 것을 금지합니다.
Copyright © 2025 CASTMAN. All rights reserved.