본 논문 요약은 ['주조 결함의 영향. 1부: A356-T6 알루미늄 주조 합금의 피로 거동'] 논문을 기반으로 작성되었으며, ['Journal of Light Metals']에 게재되었습니다.
1. 개요:
- 제목: 주조 결함의 영향. 1부: A356-T6 알루미늄 주조 합금의 피로 거동 (Fatigue behavior of A356-T6 aluminum cast alloys. Part I. Effect of casting defects)
- 저자: Q.G. Wang, D. Apelian, D.A. Lados
- 출판 연도: 2001년
- 출판 저널/학회: Journal of Light Metals
- 키워드: 알루미늄 주조, 피로 수명, 주조 결함, 파괴 역학, 와이블 통계 (Aluminum castings; Fatigue life; Casting defects; Fracture mechanics; Weibull statistics)
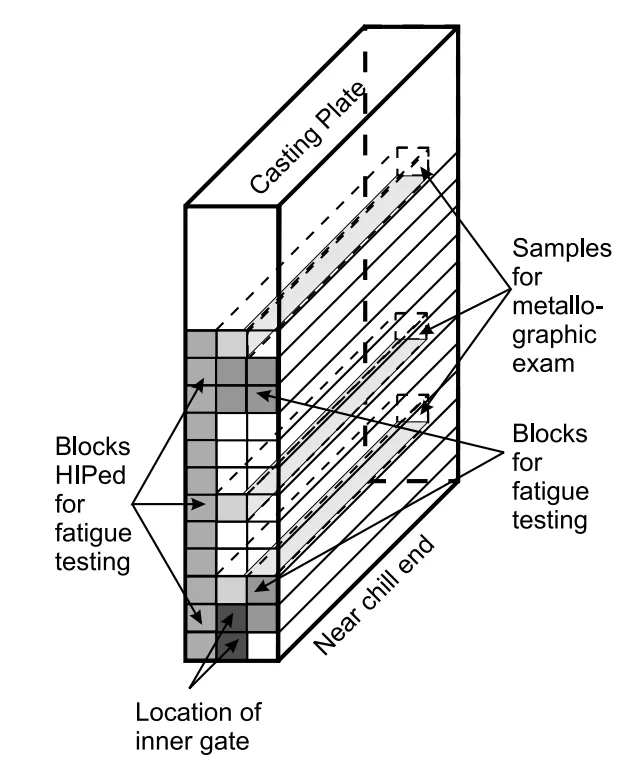
2. 연구 배경:
연구 주제 배경:
주조 알루미늄 합금은 뛰어난 주조성, 내식성, 특히 높은 강도 대 중량비로 인해 자동차 산업에서 사용이 증가하고 있습니다. 반복적인 사이클 하중 하에서 높은 신뢰성이 요구되는 형상 주조 알루미늄 부품의 사용 증가는 주조 Al-Si 합금의 피로 특성에 대한 상당한 관심을 집중시켰습니다. 주조 알루미늄 부품의 피로 특성은 주조 결함 및 미세 조직 특성에 크게 좌우됩니다.
기존 연구 현황:
일부 연구에서는 인장 연성과 마찬가지로 피로 저항성이 덴드라이트 암 간격 및 공정 실리콘 입자의 크기를 미세화함으로써 향상된다는 견해를 뒷받침하지만 [1,2], 주조 결함의 유해한 영향 또한 인식되고 있습니다 [3]. 액체 알루미늄은 수소 흡수 및 산화에 취약하여 알루미늄 주조물에서 가스 기공 및 산화물 개재물이 불가피하게 발견됩니다. 또한, 주조가 적절하게 공급되지 않으면 수축 기공이 발생하며, 이는 피로 특성에 유해합니다. 피로 수명과 결함 크기 사이의 관계를 예측하는 정량적 방법이 최근에 개발되었지만 [4–8], 기공 형상 및 결함 유형이 피로 수명에 미치는 영향에 대해 실험 데이터를 기반으로 포괄적으로 이해하는 것은 여전히 어렵습니다.
연구의 필요성:
실제 응용 분야에서는 특정 수준의 기공이 주조물에서 허용되며, 이는 특정 응용 분야에 따라 다릅니다. 결함 및 기타 미세 조직 매개변수가 피로 수명에 미치는 구체적인 역할을 식별하는 것이 중요합니다. 더욱이, 결함의 역할에 대한 정량적인 이해는 설계 사양 및 품질 관리 [9] 모두에 대한 결함 허용 기준을 설정하는 데 필수적입니다.
3. 연구 목적 및 연구 질문:
연구 목적:
본 연구의 목적은 다양한 응력 조건에서 A356 알루미늄 주조 합금의 피로 성능에 미치는 주조 결함 (기공 및 산화물 필름) 및 2차 덴드라이트 암 간격 (SDAS)의 영향을 실험적으로 조사하는 것입니다. 또한 피로 균열 시작에 대한 임계 결함 (기공/산화물) 크기의 존재를 조사하고자 합니다.
핵심 연구 질문:
- 주조 결함, 특히 기공 및 산화물 필름이 A356-T6 알루미늄 합금의 피로 수명에 미치는 유해한 영향을 정량화하는 것.
- 주조 결함 크기와 피로 수명 간의 관계를 결정하는 것.
- 주조 결함과 함께 피로 성능에 미치는 2차 덴드라이트 암 간격 (SDAS)의 역할을 조사하는 것.
- 결함이 있는 주조물의 피로 수명을 예측하는 데 파괴 역학 및 와이블 통계의 적용 가능성을 탐구하는 것.
- A356-T6 합금에서 피로 균열을 시작하는 결함 유형을 식별하고 특성화하는 것.
연구 가설:
- 주조 결함은 A356-T6 알루미늄 합금의 피로 수명을 현저히 감소시킬 것이다.
- 피로 수명은 주조 결함 크기가 증가함에 따라 감소할 것이다.
- 피로 균열 시작에 대한 임계 결함 크기가 존재하며, 이 크기 미만에서는 다른 미세 조직 특징이 주요 시작점이 될 것이다.
- 파괴 역학 원리를 사용하여 결함 크기를 기반으로 주조물의 피로 수명을 정량적으로 예측할 수 있을 것이다.
- 와이블 통계는 결함이 있는 알루미늄 주조물의 피로 파괴 거동을 효과적으로 설명할 수 있을 것이다.
4. 연구 방법론
연구 설계:
A356 알루미늄 주조 합금을 사용하여 실험적 연구를 수행했습니다. 수소 수준 및 금형 충전을 제어하여 다양한 수준의 기공 및 산화물 필름으로 제작된 시험 주조물에서 원통형 시편을 준비했습니다. 일부 시편은 기공이 없는 조건을 만들기 위해 HIP-ed 및 Densal™ 처리를 거쳐 비교했습니다. 피로 시험은 다양한 응력 진폭 및 응력비 (R = 0.1, 0.2, -1)에서 수행되었습니다.
데이터 수집 방법:
피로 시험은 55Hz에서 풀-풀 및 풀-푸시 정현파 하중 제어 하에 서보 유압 Instron 기계를 사용하여 수행되었습니다. 원통형 시편은 실온에서 시험되었습니다. 각 시편에 대한 파괴까지의 사이클 수 (Nf)를 기록했습니다. 파단면은 주사 전자 현미경 (SEM)을 사용하여 피로 균열 시작점을 식별하고 결함 크기를 측정하기 위해 검사했습니다. 정량적 금속 조직 분석을 수행하여 SDAS를 측정했습니다.
분석 방법:
- 피로 균열 성장 분석: 파리-에르도간 방정식 (Paris-Erdogon equation)을 사용하여 주조 결함으로부터의 피로 균열 성장을 모델링했습니다. 균열 닫힘 효과를 통합하여 유효 응력 강도 계수 범위 (ΔKeff)를 고려했습니다.
- 와이블 통계 분석: 2-매개변수 와이블 분포 (Weibull distribution)를 사용하여 피로 수명 데이터를 통계적으로 분석하고 피로 성능의 분산을 특성화했습니다. 선형 회귀를 적용하여 와이블 계수 (b) 및 특성 피로 수명 (N₀)을 추정했습니다.
- 파괴 역학적 접근: 파단면에서 주조 결함의 크기를 측정하고 파괴 역학 모델에서 초기 균열 크기 (aᵢ)로 사용하여 피로 수명을 예측했습니다.
- 미세 파면 분석: SEM 및 EDS를 사용하여 피로 균열 시작점 (기공, 산화물 필름)을 식별하고 파괴 특징을 특성화했습니다.
연구 대상 및 범위:
본 연구는 Sr 개질된 A356-T6 알루미늄 주조 합금에 초점을 맞추었습니다. 시편은 다양한 2차 덴드라이트 암 간격 (SDAS) 및 주조 결함 (기공 및 산화물 필름) 수준으로 준비되었습니다. 본 연구에서는 결함 크기 (최대 400-500 µm) 및 응력비 (R = 0.1, -1)가 실온 피로 성능에 미치는 영향을 조사했습니다. HIP-ed 및 Densal™ 처리된 시편을 포함하여 결함이 없는 조건을 나타냈습니다.
5. 주요 연구 결과:
핵심 연구 결과:
- 주조 결함은 결함이 없는 (HIP-ed) 시편에 비해 피로 수명을 최소 한 자릿수 이상 현저히 감소시켰습니다.
- 피로 수명은 주조 결함 크기가 증가함에 따라 감소했습니다.
- HIP-ed 시편은 비 HIP-ed 시편보다 현저히 긴 피로 수명을 나타냈습니다.
- 피로 균열 시작에 대한 임계 결함 크기가 존재하는 것으로 보이며, 이 크기 미만에서는 피로 균열이 공정 입자 및 슬립 밴드와 같은 다른 원천에서 시작되었습니다.
- 피로 균열은 주로 시편 표면 또는 표면 근처에 위치한 기공 및 산화물 필름에서 시작되었습니다.
- 기공은 산화물 필름보다 피로 수명에 더 유해한 것으로 밝혀졌습니다.
- 피로 수명 데이터는 2-매개변수 와이블 분포에 의해 잘 설명되었습니다.
- 결함이 있는 주조물의 피로 수명은 결함 크기를 기반으로 파괴 역학을 사용하여 정량적으로 예측할 수 있었습니다.
데이터 해석:
- 주조 결함, 특히 기공 및 산화물 필름의 존재는 A356-T6 합금의 피로 수명을 제어하는 주요 요인입니다.
- 더 큰 결함은 응력 집중 증가 및 가속화된 균열 전파로 인해 더 빠른 피로 파괴를 유발합니다.
- HIP과 같은 공정을 통해 주조 결함을 제거하거나 줄이면 피로 성능이 크게 향상됩니다.
- 와이블 분포는 결함 특성의 가변성을 고려하여 주조 알루미늄 합금의 피로 파괴의 통계적 특성을 효과적으로 포착합니다.
- 파괴 역학은 결함 크기를 기반으로 피로 수명을 예측하는 데 실행 가능한 접근 방식을 제공하며, 이는 결함으로부터의 균열 전파가 이러한 재료에서 피로 파괴의 지배적인 단계임을 시사합니다.
- 기공 및 산화물 필름에서 시작된 균열에 대한 와이블 계수 및 특성 피로 수명의 차이는 서로 다른 결함 유형과 관련된 뚜렷한 피로 거동을 나타냅니다.
그림 목록:
- Fig. 5. 다양한 결함 크기를 가진 Sr 개질된 A356 합금의 S-N 데이터, 두 가지 다른 응력비 (a) R = 0.1 및 (b) R = -1에서 시험. "→"는 런아웃 – 시편이 최대 10⁷ 사이클까지 파괴되지 않았음을 나타냅니다.
- Fig. 6. Sr 개질된 A356 주조물에서 피로 균열을 시작하는 다양한 결함을 보여주는 SEM 현미경 사진: (a) 기공; (b) 산화물 필름.
- Fig. 7. 다양한 결함을 포함하는 Sr 개질된 A356 주조 합금의 피로 수명 데이터에 대한 2-매개변수 와이블 플롯.
- Fig. 8. 기공 크기의 함수로서 Sr 개질된 A356-T6 합금의 피로 수명; (a) SDAS: 20-25 µm, (b) SDAS: 70-75 µm.
- Fig. 9. 다양한 SDAS 값에 대한 산화물 필름 크기의 함수로서 Sr 개질된 A356-T6 합금의 피로 수명.
- Fig. 10. (a) R = 0.1 및 (b) R = -1에서 시험에 대한 결함 크기 √A의 영향을 포함하는 수정된 피로 수명 플롯.
- Fig. 11. (a) R = 0.1 및 (b) R = -1에서 시험에 대한 실제 피로 수명 (Nf)과 계산된 균열 전파 수명 (Np)의 비교.
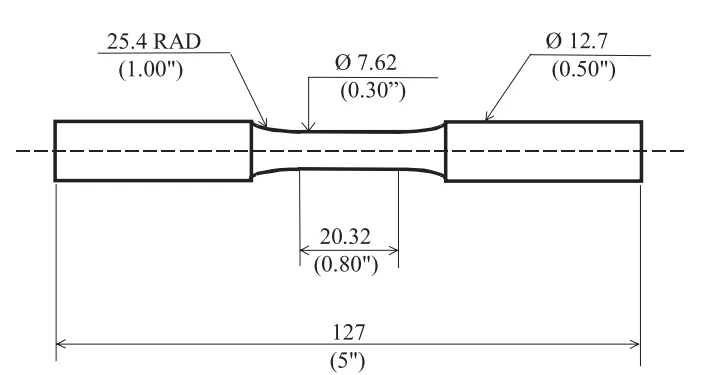
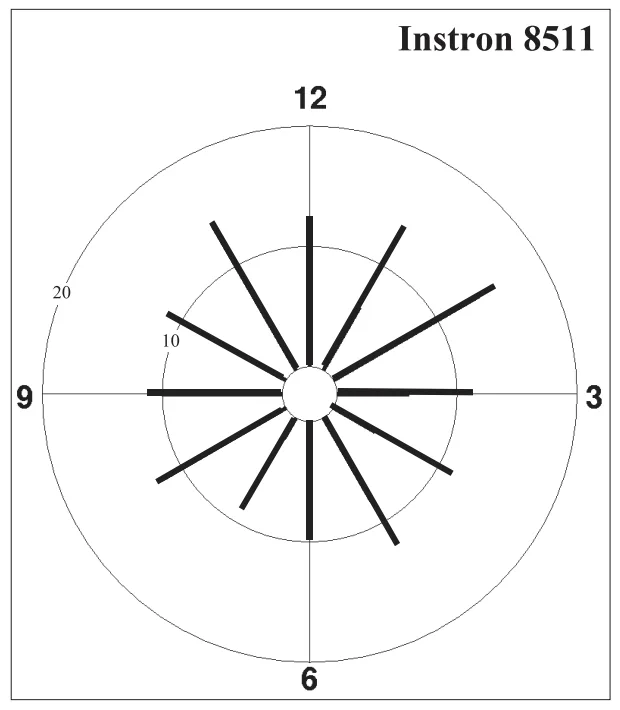
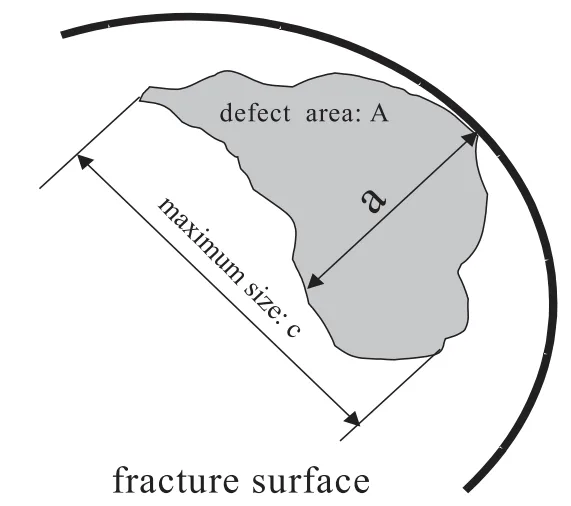
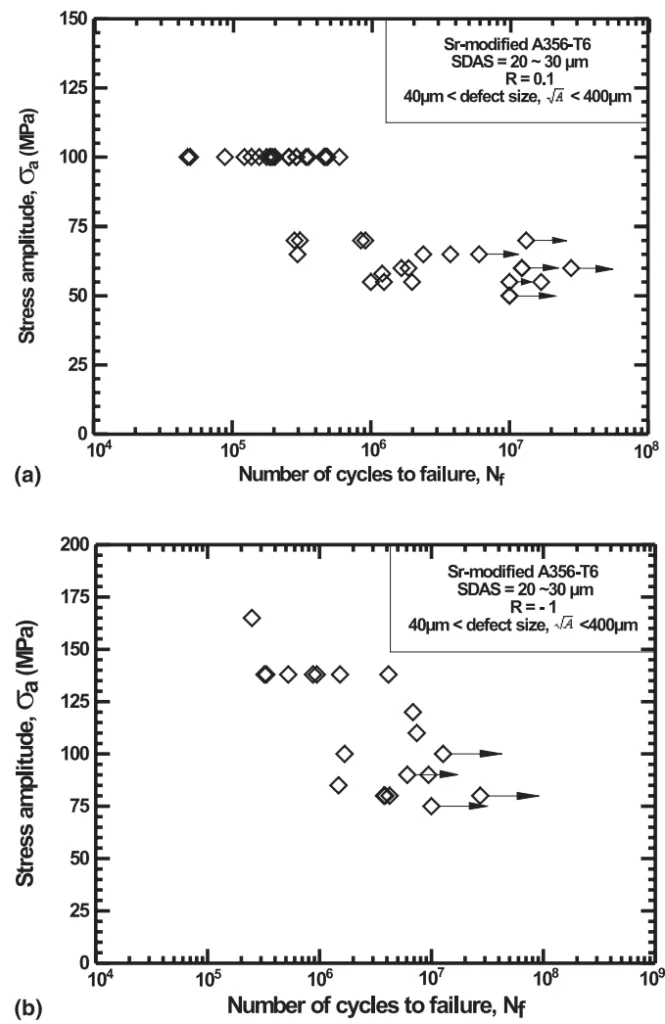
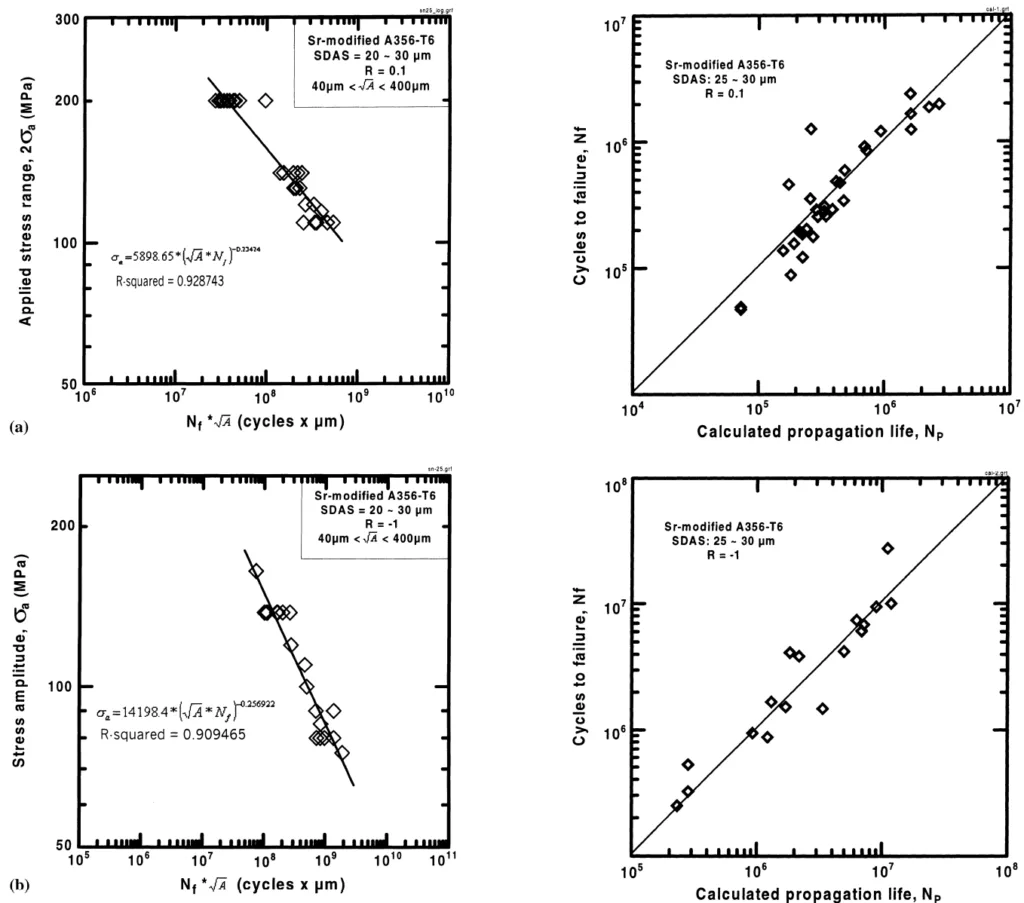
6. 결론:
주요 결과 요약:
본 연구는 주조 결함, 특히 기공 및 산화물 필름이 A356-T6 알루미늄 주조 합금의 피로 거동에 상당한 유해한 영향을 미친다는 것을 결정적으로 입증합니다. 이러한 결함은 피로 수명의 균열 전파 단계뿐만 아니라 균열 시작 단계도 단축시킵니다. 주조 결함 크기는 피로 수명 감소와 직접적인 상관 관계가 있습니다. 임계 결함 크기 미만에서는 피로 균열이 다른 미세 조직 특징에서 시작됩니다. 파괴 역학 및 와이블 통계는 이러한 재료의 피로 수명을 분석하고 예측하는 효과적인 도구입니다. 기공은 피로 성능 측면에서 산화물 필름보다 더 중요한 결함 유형으로 확인되었습니다.
연구의 학문적 의의:
본 연구는 자동차 산업에서 널리 사용되는 재료인 A356-T6 합금의 피로 성능에 미치는 주조 결함의 영향에 대한 귀중한 정량적 데이터를 제공합니다. 결함이 있는 주조 알루미늄 합금의 피로 수명 예측에 파괴 역학 및 와이블 통계의 적용 가능성을 입증합니다. 본 연구는 주조 결함의 존재 하에서 피로 균열 시작 및 전파 메커니즘에 대한 더 깊은 이해에 기여하며, 기공과 산화물 필름의 역할을 구별합니다.
실용적 의미:
본 연구 결과는 다이캐스팅 산업에 중요한 실용적 의미를 갖습니다. 결함 크기와 피로 수명 간의 확립된 상관 관계는 주조 알루미늄 부품에 대한 결함 허용 기준 및 품질 관리 표준 개발에 정보를 제공할 수 있습니다. 임계 결함 크기의 식별은 원하는 피로 성능을 달성하기 위해 결함 수준을 최소화하기 위한 목표를 제공합니다. 본 연구는 특히 주조 공정 중 기공을 줄이는 것의 중요성을 강조합니다. 예측 모델은 부품 설계 및 수명 평가에 활용되어 피로에 중요한 응용 분야에서 주조 알루미늄 부품의 신뢰성을 향상시킬 수 있습니다.
연구의 한계
본 연구는 특정 하중 조건 (정현파 하중, R=0.1, -1) 하에서 A356-T6 합금의 실온 피로 거동에 초점을 맞추었습니다. 연구 결과는 이 합금 및 이러한 시험 조건에 특이적일 수 있습니다. 본 연구에서는 주로 기공 및 산화물 필름을 주조 결함으로 고려했으며, 다른 유형의 결함 및 이들의 상호 작용에 대한 추가 연구가 필요합니다. 파괴 역학 모델의 균열 닫힘 가정 (Kopening = 0)은 단순화이며, 특히 음의 응력비에서 수명 예측에 어느 정도의 근사치를 도입할 수 있습니다.
7. 향후 후속 연구:
- 후속 연구 방향
향후 연구에서는 기공 형상 및 형태, 그리고 서로 다른 유형의 산화물 필름 (young vs. old)이 피로 수명에 미치는 영향을 탐구해야 합니다. 가변 진폭 하중 및 고온에서 피로 거동을 조사하면 연구 결과의 적용 가능성이 확대될 것입니다. 특히 음의 응력비에서 균열 닫힘 효과를 보다 정확하게 설명하고, 보다 강력한 피로 수명 예측을 위해 결함 크기 및 유형의 통계적 분포를 통합하기 위해 파괴 역학 모델을 개선하기 위한 추가 연구가 필요합니다. - 추가 탐구가 필요한 영역
피로 균열 시작에 미치는 주조 결함과 공정 실리콘 입자 및 금속간 화합물과 같은 다른 미세 조직 특징 간의 상호 작용을 완전히 이해하기 위한 추가 탐구가 필요합니다. 크기, 형상 및 분포를 포함하여 주조 결함을 정확하게 특성화하기 위한 고급 비파괴 검사 (NDE) 기술을 개발하는 것은 산업 현장에서 결함 기반 피로 수명 예측 모델을 구현하는 데 매우 중요합니다. 피로 성능 향상에 대한 다양한 결함 감소 전략 및 주조 후 처리의 효과를 조사하는 것은 향후 연구를 위한 중요한 영역으로 남아 있습니다.
8. 참고 문헌:
- [1] A.Wickberg, G. Gustafsson, L.E. Larsson, Microstructural effects on the fatigue properties of a cast Al7SiMg alloy, SAE Technical Publication #840121, 1984.
- [2] T.L. Reinhart, ASM Handbook, vol. 19, ASM International, Materials Park, OH, 1996, pp. 813-822.
- [3] N.E. Promisel, Evaluation of non-ferrous materials, 1956 (cited by H.E. Boyer, Atlas of fatigue curves, American Society of Metals, 1986).
- [4] M.J. Couper, A.E. Neeson, J.R. Griffiths, Casting defects and the fatigue life of an aluminum casting alloy, Fatigue Fract. Eng. Mater. Struct. 13 (1990) 213-227.
- [5] B. Skallerud, T. Iveland, G. Härkegård, Fatigue life assessment of aluminum alloys with casting defects, Eng. Fracture Mech. 44 (1993) 857-874.
- [6] J.A. Odegard, K. Pedersen, Fatigue properties of an A356 (AlSi7Mg) aluminium alloy for automotive applications - fatigue life prediction, SAE technical paper SAE-940811, 1994, pp. 25-32.
- [7] Chih-Hsien Ting, A model for the long-life fatigue behaviour of small notches, Ph.D. Dissertation, University of Illinois at Urbana-Champaign, 1991.
- [8] D.L McLellan, M.M. McLellan, An approach to fatigue design for aluminum castings, AFS Trans. 104 (1996) 445-449.
- [9] J.F. Major, Porosity control and fatigue behaviour in A356T61 aluminum alloy, AFS Trans. 105 (1997) 901-906.
- [10] W. Elber, Fatigue crack closure under cyclic tension, Eng. Fracture Mech. 2 (1970) 37-45.
- [11] N.E. Dowling, ASTM STP 637 (1977) 97–121.
- [12] D. Wilhem, J. FitzGerald, J. Carter, D. Dittmer, An empirical approach to determining K for surface cracks, in: Proceedings of the Fifth International Conference on Fracture, vol. 1, Cannes, 1981, pp. 11-21.
- [13] W. Weibull, A statistical distribution function of wide applicability, J. App. Mech. 18 (1951) 293-297.
- [14] A. Khalili, K. Kromp, Statistical properties of weibull estimators, J. Mater. Sci. 26 (1991) 6741-6752.
- [15] J. Campbell, The origin of porosity in castings, in: Proceedings of the fourth Asia Foundry Congress incorporated in 32nd Annual Convention of Australian Foundry Institute, 1996, pp. 33-50.
- [16] Q.G. Wang, Microstructure and tensile fracture behavior of Al-Si-Mg casting alloys, Ph.D. Thesis, The University of Queensland, Brisbane, Australia, 1997.
- [17] C.H. Cáceres, C.J. Davidson, J.R. Griffiths, The deformation and fracture behaviour of an Al-Si-Mg casting alloy, Mater. Sci. Eng. A A197 (1995) 171-179.
- [18] Q.G. Wang, C.H. Cáceres, The fracture mode in Al-Si-Mg casting alloys, Mater. Sci. Eng. A A241 (1998) 72-82.
- [19] Q.G. Wang, C.H. Cáceres, On the strain hardening behavior of Al-Si-Mg casting alloys, Mater. Sci. Eng. A 234-236A (1997) 106-109.
- [20] C.H. Cáceres, Q.G. Wang, J.R. Griffiths, C.J. Davidson, The effect of Mg on the microstructure and mechanical behavior of two commercial Al-Si-Mg casting alloys, Metall. Trans. A 30A (1999) 2611-2618.
- [21] Q.G. Wang, C.H. Cáceres, J.R. Griffiths, The cracking of Fe-rich and eutectic Si particles in an Al-7Si-0.7Mg casting alloy, AFS Trans. 106 (1998) 131-136.
- [22] D.S. Saunders, J.R. Griffiths, B.A. Parker, The fracture toughness of an aluminum casting alloy, J. Aust. Inst. Metals 20 (1975) 33-38.
- [23] D.A. Gerard, D.A. Koss, The dependence of crack initiation on porosity during low cycle fatigue, Mater. Sci. Eng. A 129 (1990) 77-85.
- [24] D.A. Gerard, The influence of porosity on low cycle fatigue, Ph.D. Dissertation, Michigan Technological University, Houghton, MI, 1989, pp. 1–167.
- [25] J.C. Ting, The long-life regime fatigue analysis for lost foam cast Al-Si Alloy 319, Ph.D. Dissertation, University of Illinois-Champaign, IL, 1991, pp. 1–186.
- [26] J. Campbell, C. Nyahumwa, N.R. Green, The concept of the fatigue potential of cast alloys, in: Proceedings of Materials Solution Conference '98 on Advances in Aluminum Casting Technology, 12-15 October 1998, pp. 225-233.
- [27] C. Nyahumwa, N.R. Green, J. Campbell, Effect of mold filling turbulence on fatigue properties of cast aluminum alloys, AFS Trans. 106 (1998) 215-223.
- [28] J.C. Newman Jr., A crack opening stress equation for fatigue crack growth, Int. J. Fracture 24 (1984) 131-135.
- [29] J.C. Newman Jr., A crack closure model for prediction of fatigue crack growth under aircraft spectrum loading, ASTM STP 748 (1982) 53-84.
- [30] N.E. Dowling, N.S. Iyyer, Fatigue crack growth and closure at high cyclic strains, Mater. Sci. Eng. 96 (1987) 99-107.
- [31] I. Gustavson, A. Melander, A finite element study of the early growth of fatigue cracks emanating from a spherical pore, in: Proceedings of the Fifth International Conference on Numerical Methods in Fracture Mechanics, Germany, 1990, pp. 225-236.
- [32] Y. Verremen, J.P. Ballon, J. Masounave, Fatigue short crack propagation and plasticity-induced crack closure at the toe of a fillet welded joint, in: The Behavior of Short Fatigue Cracks, EGF publication 1, 1986, pp. 387-404 (Mechanical Engineering Publication, London).
9. 저작권:
- 본 자료는 "[Q.G. Wang, D. Apelian, D.A. Lados]"의 논문: "[주조 결함의 영향. 1부: A356-T6 알루미늄 주조 합금의 피로 거동]"을 기반으로 합니다.
- 논문 출처: https://doi.org/10.1016/S1471-5317(00)00008-0
본 자료는 상기 논문을 기반으로 요약되었으며, 상업적 목적으로 무단 사용하는 것을 금지합니다.
Copyright © 2025 CASTMAN. All rights reserved.