본 입문 논문은 International Journal of Metalcasting에 게재된 "저임계 원료 사용 및 자동차 응용 분야를 위한 높은 주조 가공성을 갖춘 새로운 알루미늄 합금 설계 전략" 논문의 연구 내용입니다.
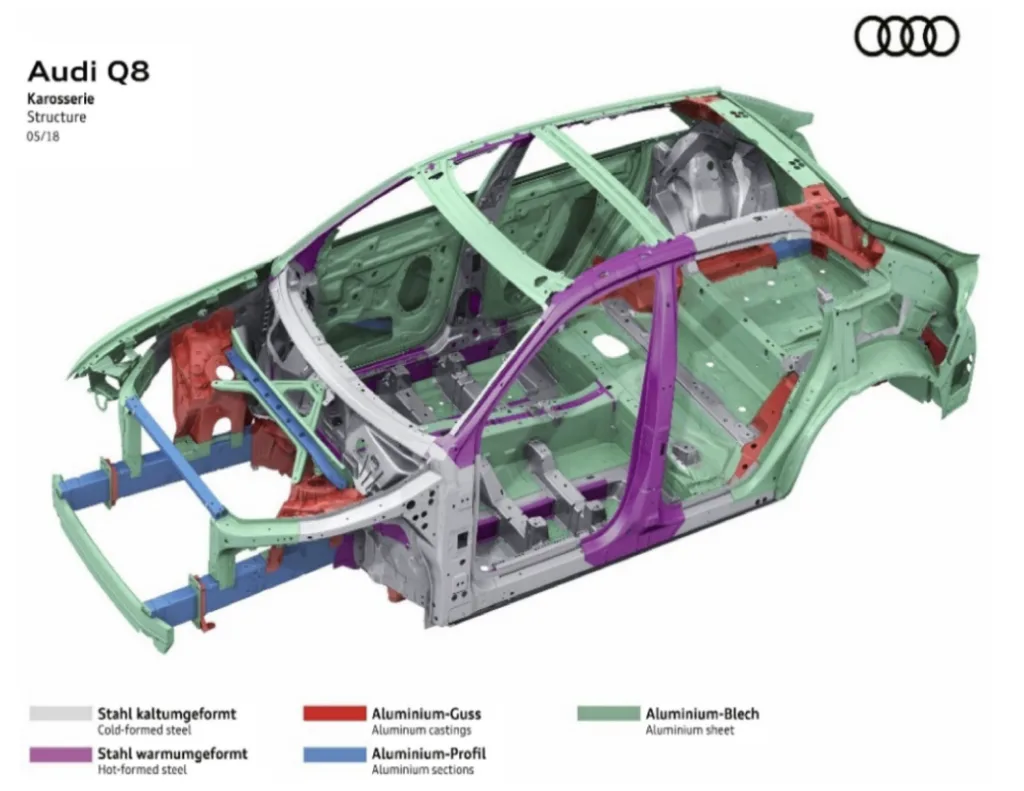
1. 개요:
- 제목: 저임계 원료 사용 및 자동차 응용 분야를 위한 높은 주조 가공성을 갖춘 새로운 알루미늄 합금 설계 전략 (A NOVEL ALUMINIUM ALLOYS DESIGN STRATEGY FOR LOW USAGE OF CRITICAL RAW MATERIALS AND HIGH CASTING PROCESSIBILITY FOR AUTOMOTIVE APPLICATIONS)
- 저자: Osama Asghar, Mattia Franceschi, Paolo Ferro and Franco Bonollo
- 출판 연도: 2025
- 게재 저널/학회: International Journal of Metalcasting
- 키워드: 알루미늄 합금, 임계 원자재, 고압 다이캐스팅, 합금 설계 (aluminium alloys, critical raw materials, high pressure die casting, alloy design)
2. 초록
2023년 유럽연합 집행위원회(EC)에서 발표한 다섯 번째 임계 원자재(CRM) 목록은 운송 산업에서 경량 소재 사용에 새로운 제약을 가합니다. 이 발표에 따르면 알루미늄(항공우주 및 자동차 산업에서 가장 널리 사용되는 경량 금속 중 하나)은 CRM으로 선언되었으며 주요 합금 원소(예: 규소 및 마그네슘)에서 임계성이 증가하는 추세가 관찰되었습니다. 따라서 자동차 산업의 다양한 부품을 위한 새로운 알루미늄 합금 및 그 가공을 개발하는 데 있어 임계성 개념을 구현하기 위한 새로운 접근 방식이 필요합니다. 본 연구는 향상된 고압 다이캐스팅(HPDC) 가공성과 함께 알루미늄 합금에서 CRM 사용을 줄이기 위한 전략을 설명하는 것을 목표로 합니다. 임계성 및 주조성 평가를 통합함으로써, 세계적인 자원 문제를 해결하면서 현대 제조의 요구를 충족시키는 지속 가능하고 고강도 알루미늄 합금 개발에 기여하는 바를 제시합니다. 이 연구는 또한 재료 연구 개발에서 CRM 개념의 구현을 지원할 것입니다.
3. 연구 배경:
연구 주제 배경:
지속 가능성은 산업 혁신의 주요 동력입니다. 자동차 산업은 에너지 효율성을 최적화하고 CO2 배출량을 줄이는 데 중점을 두고 있습니다. 재료 선택 및 설계는 환경적 지속 가능성을 달성하는 데 핵심입니다.
이전 연구 현황:
경량 금속, 특히 알루미늄 합금은 차량 중량을 줄이고 연비를 개선하는 데 중요합니다. 그러나 유럽연합 집행위원회는 공급 위험과 경제적 중요성 때문에 알루미늄과 주요 합금 원소(Si, Mg)를 임계 원자재(CRM)로 지정했습니다. 이전 연구는 경량화에 초점을 맞추었지만 합금 설계에서 CRM 사용을 최소화하는 데 명시적으로 초점을 맞추지는 않았습니다.
연구 필요성:
자동차 산업의 핵심 제조 공정인 고압 다이캐스팅(HPDC)에 특히 적합한, 가공성을 유지하거나 개선하면서 CRM 사용을 최소화하는 알루미늄 합금을 설계하기 위한 새로운 접근 방식이 필요합니다.
4. 연구 목적 및 연구 질문:
연구 목적:
경량 재료, 특히 알루미늄 합금에서 CRM을 줄이는 동시에 높은 HPDC 가공성을 보장하는 방법론을 제안합니다.
핵심 연구:
새로운 알루미늄 합금 설계를 위해 임계성 평가(CRM 함량 최소화)와 주조성 평가(HPDC 가공성 최적화)를 통합하는 전략을 개발합니다.
5. 연구 방법
이 연구 방법론은 Ashby et al.44의 재료 선택 방법론과 전산 도구, 주로 CALPHAD(CALculation of PHAse Diagram) 접근 방식을 결합합니다. 설계 프로세스는 다음을 포함합니다.
- 재료 라이브러리 생성: 시작 알루미늄 합금을 선택하고 CRM(Si, Mg)을 비 CRM 원소로 대체하여 합금 라이브러리를 만듭니다.
- 기계적 성능 추정: 수정된 조성으로 달성 가능한 기계적 특성을 평가합니다.
- 주조성 평가: CALPHAD 및 새로 개발된 모델을 사용하여 주요 주조성 특성(유동성, 응고 수축, 슬래그/드로스 형성, 다이 솔더링, 고온 균열)을 평가합니다.
- 임계성 평가: Ferro et al.22,59,60의 작업을 기반으로 각 합금 조성에 대한 임계성 지수를 계산합니다.
- 최적화: 가공 특성, 기계적 성능 및 낮은 임계성 간의 최상의 절충안을 제공하는 합금 시스템을 선택합니다.
- 실험적 검증: 최적의 솔루션을 검증하기 위한 향후 실험 캠페인.
6. 주요 연구 결과:
주요 연구 결과 및 제시된 데이터 분석:
이 논문은 특정 합금 조성이나 실험 데이터가 아닌 합금 설계 프레임워크를 제시합니다. 주요 결과는 다음과 같습니다.
- 임계성 개념과 알루미늄 합금과의 관련성에 대한 자세한 설명.
- HPDC의 주요 주조성 특성 식별: 유동성, 응고 수축, 슬래그/드로스 형성, 다이 솔더링 및 고온 균열.
- CALPHAD 및 기타 모델을 사용하여 이러한 특성을 평가하는 방법 설명.
- 개별 원자재에 대한 임계성 지수(CICRM) 및 전체 합금 임계성 지수(CIA) 계산 방정식 제시.
- 임계성 및 주조성 지수를 결합하여 합금 조성의 순위를 매기는 다목적 전략 제안.
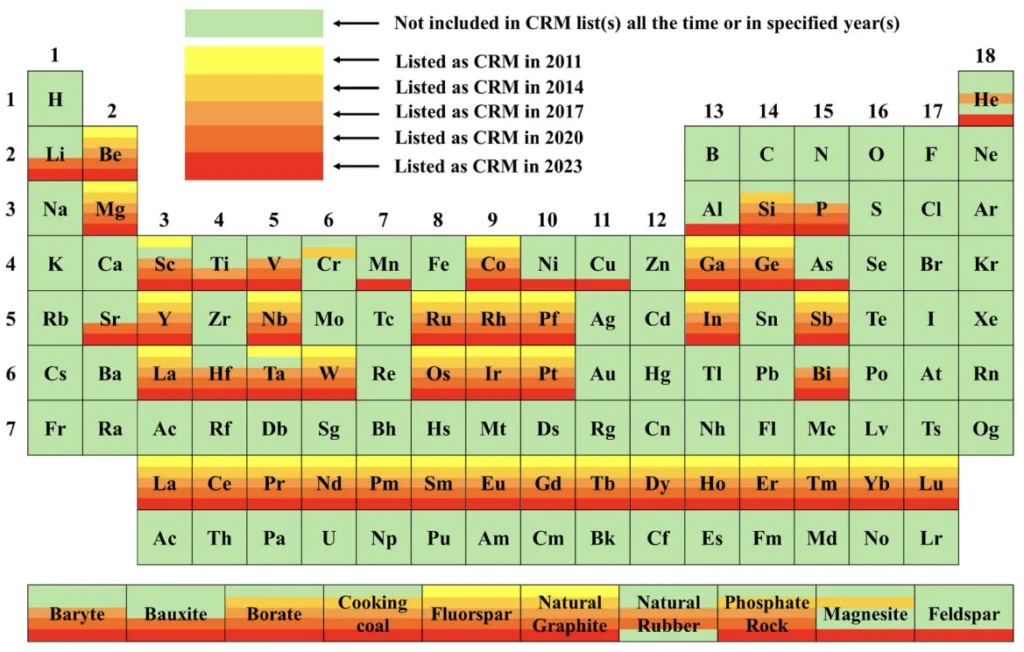
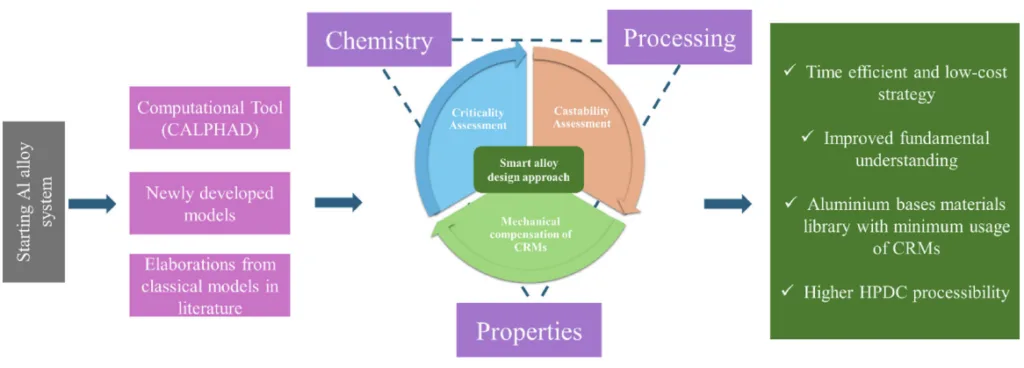
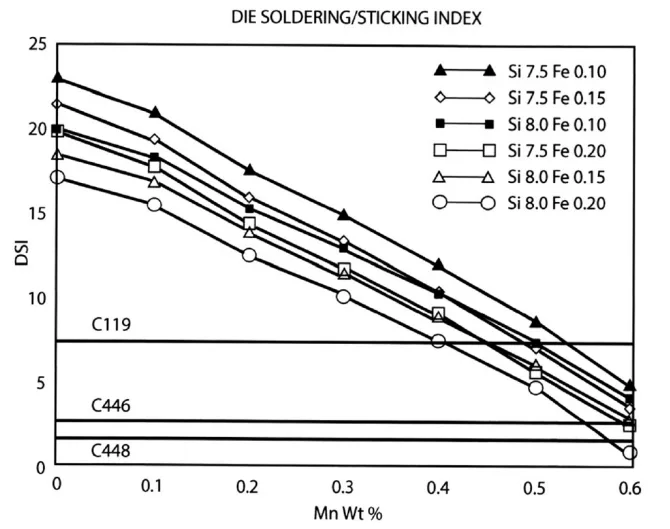
그림 이름 목록:
- 그림 1. 2011년부터 2023년까지의 유럽 CRM 평가.
- 그림 2. Audi Q8 BIW 구조에 사용된 알루미늄 성형 공정 분류; Ref 30에서 발췌.
- 그림 3. 혁신적인 알루미늄 합금을 위한 새로운 합금 설계 및 개발 전략.
- 그림 4. 알루미늄-4 wt pct 철-X 시스템의 고상선 온도.74
- 그림 5. 여러 다이캐스팅 합금의 다이 솔더링 지수.75
7. 결론:
주요 결과 요약:
자동차 산업을 위해 CRM 함량이 낮고 가공성이 우수하며 기계적 성능이 우수한 경량 알루미늄 합금을 설계하기 위한 새로운 이론적이고 체계적인 접근 방식이 개발되었습니다. 개발된 절차는 임계 원자재의 함량과 주조 공정으로 생산된 합금의 가공성에 영향을 미치는 주요 매개변수를 고려하는 지수를 정의하는 것으로 구성됩니다.
이 연구는 임계 원자재에 대한 의존도를 최소화하여 지속 가능한 알루미늄 합금을 설계하기 위한 프레임워크를 제공합니다. 이는 학문적 의의(합금 설계에 임계성 통합)와 실제적 의미(자동차 HPDC 응용 분야에 적합한 합금 개발)를 모두 갖습니다. 다목적 접근 방식을 통해 성능, 가공성 및 자원 지속 가능성을 균형 있게 고려할 수 있습니다.
8. 참고 문헌:
- [1] C. Fetting, The European green deal. ESDN Rep. 53, 24 (2020)
- [2] P.K. Mallick, Materials, design and manufacturing for lightweight vehicles. (2020) pp. 25–32, https://doi.org/10.1016/C2018-0-04153-5
- [3] A. Morita, Aluminum alloys for automobile applications. In Proceedings of the Proc. 6th (ICAA 1998), pp. 25-32
- [4] M. Franceschi, R. Bertolini, A. Fabrizi, M. Dabalà, L. Pezzato, Effect of ausforming temperature on bainite morphology in a 3.2% Si carbide-free bainitic steel. Mater. Sci. Eng. A (2023). https://doi.org/10.1016/j.msea.2022.14455
- [5] M. Franceschi, C. Soffritti, A. Fortini, L. Pezzato, G.L. Garagnani, M. Dabalà, Evaluation of wear resistance of a novel carbide- free bainitic steel. Tribol. Int. (2023). https://doi.org/10.1016/j.triboint.2022.108071
- [6] B. Ravishankar, S.K. Nayak, M.A. Kader, Hybrid composites for automotive applications—a review. J. Reinf. Plast. Compos. 38, 835–845 (2019). https://doi.org/10.1177/0731684419849708
- [7] A.A. Luo, Recent advances in light metals and manufacturing for automotive applications. CIM J. 12, 79–87 (2021). https://doi.org/10.1080/19236026.2021.1947088
- [8] S. Ray, R.P. Cooney, Thermal degradation of polymer and polymer composites. In Handbook of Environmental Degradation of Materials 3rd Edn. (2018; pp. 185-2026)
- [9] A.L. Robinson, A.I. Taub, G.A. Keoleian, Fuel efficiency drives the auto industry to reduce vehicle weight. MRS Bull. 44, 920–922 (2019). https://doi.org/10.1557/mrs.2019.298
- [10] W.S. Miller, L. Zhuang, J. Bottema, A.J. Wittebrood, P. De Smet, A. Haszler, A. Vieregge, Recent development in aluminium alloys for the automotive industry. Mater. Sci. Eng. A 280, 37–49 (2000). https://doi.org/10.1016/S0921-5093(99)00653-X
- [11] E. Georgantzia, M. Gkantou, G.S. Kamaris, aluminium alloys as structural material: a review of research. Eng. Struct. (2021). https://doi.org/10.1016/j.engstruct.2020.111372
- [12] T. Dursun, C. Soutis, Recent developments in advanced aircraft aluminium alloys. Mater. Des. 56, 862–871 (2014). https://doi.org/10.1016/j.matdes.2013.12.002
- [13] N. Prasad Rambabu, V.V.K. Eswara Prasad, R.J.H. Wanhill, Aerospace materials and material technologies volume 1: aerospace material technologies. Aerosp. Mater. Mater. Technol. (2017). https://doi.org/10.1007/978-981-10-2134-3
- [14] D. Zhou, Z. Kang, X. Su, Study on squeeze casting process of the integrated aluminum alloy subframe. Int. J. Met. 18, 1085–1106 (2024). https://doi.org/10.1007/s40962-023-01087-6
- [15] Q. Wang, A. Bobel, M. Walker, D. Hess, H. Doty, D. Gerard, Evaluation of two new cast aluminum alloys for high performance cylinder heads. Int. J. Met. (2024). https://doi.org/10.1007/s40962-024-01341-5
- [16] Duckerfrontier Aluminium content in European passenger cars. Eur. Alum. 1–23 (2019)
- [17] COMMISSION OF THE EUROPEAN COMMUNITIES The raw materials initiative—meeting our critical needs for growth and jobs in Europe. (2008), 14
- [18] COMMISSION OF THE EUROPEAN COMMUNITIES Tackling the challenges in commodity markets and on raw materials. (2011)
- [19] COMMISSION OF THE EUROPEAN COMMUNITIES On the review of the list of critical raw materials for the EU and the implementation of the raw materials initiative. Eur. Comm. Brussels, Belgium COM no. 297 (2014)
- [20] COMMISSION OF THE EUROPEAN COMMUNITIES Comunication from the Commission to EU Parliament on the 2017 List of Critical Raw Materilas for EU 490 (2017)
- [21] COMMISSION OF THE EUROPEAN COMMUNITIES Study on the Review of the List of Critical Raw Materials - Critical Raw Materials Factsheets (2020)
- [22] M. Grohol, C. Veeh, OMMUNITIES, C.O.T.E. Study on the Critical Raw Material for the EU; Publication Office of the European Union (2023)
- [23] V. Kumar, H. Mehdi, A. Kumar, Effect of silicon and lead contents on the mechanical properties of aluminum alloy. Int. J. Mech. Eng. Technol. 2, 1326–1330 (2015)
- [24] S. Ji, D. Watson, Z. Fan, M. White, Development of a super ductile diecast Al-Mg-Si alloy. Mater. Sci. Eng. A 556, 824–833 (2012). https://doi.org/10.1016/j.msea.2012.07.074
- [25] M. Król, T. Tański, P. Snopiński, B. Tomiczek, Structure and properties of aluminium-magnesium casting alloys after heat treatment. J. Therm. Anal. Calorim. 127, 299–308 (2017). https://doi.org/10.1007/s10973-016-5845-4
- [26] M. Hofmann, H. Hofmann, C. Hagelüken, A. Hool, Critical raw materials: a perspective from the materials science community. Sustain. Mater. Technol. 17, e00074 (2018). https://doi.org/10.1016/j.susmat.2018.e00074
- [27] M. Tanwir Alam, A. Husain Ansari, Review on aluminium and its alloys for automotive applications Maulana Mukhtar Ahmad Nadvi Technical Campus Malegaon. pp. 278–294 (2017)
- [28] N. Parson, J. Fourmann, J.F. Beland, aluminum extrusions for automotive crash applications. SAE Tech. Pap. (2017). https://doi.org/10.4271/2017-01-1272
- [29] J. Mendiguren, E.S. De Argandona, L. Galdos, Hot Stamping of AA7075 Aluminum Sheets. IOP Conference Series Material Science English 159, (2016). https://doi.org/10.1088/1757-899X/159/1/012026.
- [30] Centre, A.M. Audi Q8 Body Available online: https://www.audi-mediacenter.com/en/the-audi-q8-the-new-top-model-of-the-q-family-10412/body-10419
- [31] M. Jinta, Y. Sakai, M. Oyagi, S. Yoshizawa, K. Matsui, K. Noda, Press Forming analysis of aluminum auto body panel: wrinkle behavior in 5000 and 6000 series aluminum alloy sheet forming. JSAE Rev. 21, 407–409 (2000). https://doi.org/10.1016/S0389-4304(00)00039-4
- [32] F. Bonollo, N. Gramegna, G. Timelli, High-pressure die-casting: contradictions and challenges. Jom 67, 901–908 (2015). https://doi.org/10.1007/s11837-015-1333-8
- [33] X. Dong, H. Yang, X. Zhu, S. Ji, High strength and ductility aluminium alloy processed by high pressure die casting. J. Alloys Compd. 773, 86–96 (2019). https://doi.org/10.1016/j.jallcom.2018.09.260
- [34] X. Dong, X. Huang, L. Liu, L. He, P. Li, A liquid aluminum alloy electromagnetic transport process for high pressure die casting. J. Mater. Process. Technol. 234, 217–227 (2016). https://doi.org/10.1016/j.jmatprotec.2016.03.028
- [35] H. Blala, C. Pengzhi, Z. Shenglun, C. Gang, R. Shangwen, M. Zhang, Innovative hybrid high-pressure die-casting process for load-bearing body-in-white structural components. Int. J. Met. (2024). https://doi.org/10.1007/s40962-024-01280-1
- [36] N. Gramegna, F. Bonollo, Smart control and cognitive system applied to the HPDC foundry 4.0: a robust and competitive methodology developed under EU-FP7 music project. (2016)
- [37] A. Rai, S. Shrimant Sawant, P. Winber, M. Burgess, T. Spencer, P. Kornmayer, G. Pattinson, P.D. Edwards, C. Rinaldi, A. Reikher et al., Integrated absorbing castings (2023)
- [38] C. Bharambe, M.D. Jaybhaye, A. Dalmiya, C. Daund, D. Shinde, Analyzing casting defects in high-pressure die casting industrial case study. Mater. Today Proc. 72, 1079–1083 (2023). https://doi.org/10.1016/j.matpr.2022.09.166
- [39] E. Fiorese, F. Bonollo, G. Timelli, L. Arnberg, E. Gariboldi, New classification of defects and imperfections for aluminum alloy castings. Int. J. Met. 9, 55–66 (2015). https://doi.org/10.1007/BF03355602
- [40] G. Timelli, A. Fabrizi, The effects of microstructure heterogeneities and casting defects on the mechanical properties of high-pressure die-cast AlSi9Cu3(Fe) alloys. Metall. Mater. Trans. A Phys. Metall. Mater. Sci. 45, 5486–5498 (2014). https://doi.org/10.1007/s11661-014-2515-7
- [41] Driving Sustainable Aluminium (SALEMA) Available online: https://salemaproject.eu/
- [42] R.K. Helling, D. Russell, A investigation of the trade-off between lightweight and battery cost for an aluminium-intensive. Green Chem. 11, 380 (2009)
- [43] F. Bonollo, N. Gramegna, The MUSIC Guide to Key-Parameters in High Pressure Die Casting (2015)
- [44] M.F. Ashby, Y.J.M. Bréchet, D. Cebon, L. Salvo, Selection strategies for materials and processes. Mater. Des. 25, 51–67 (2004). https://doi.org/10.1016/S0261-3069(03)00159-6
- [45] Z. Lu, L. Zhang, Thermodynamic description of the quaternary Al-Si-Mg-Sc system and its application to the design of novel Sc-additional A356 alloys. Mater. Des. 116, 427–437 (2017). https://doi.org/10.1016/j.matdes.2016.12.034
- [46] U.R. Kattner, The calphad method and its role in material and process development. Tecnol. em Metal. Mater. e Mineração 13, 3–15 (2016). https://doi.org/10.4322/2176-1523.1059
- [47] D. Raabe, J.R. Mianroodi, J. Neugebauer, Accelerating the design of compositionally complex materials via physics-informed artificial intelligence. Nat. Comput. Sci. 3, 198–209 (2023). https://doi.org/10.1038/s43588-023-00412-7
- [48] M. Hu, Q. Tan, R. Knibbe, M. Xu, B. Jiang, S. Wang, X. Li, M.X. Zhang, Recent applications of machine learning in alloy design: a review. Mater. Sci. Eng. R. Rep. 155, 100746 (2023). https://doi.org/10.1016/j.mser.2023.100746
- [49] P. Krall, I. Weißensteiner, S. Pogatscher, Recycling aluminum alloys for the automotive industry: breaking the source-sink paradigm. Resour. Conserv. Recycl. (2024). https://doi.org/10.1016/j.resconrec.2023.107370
- [50] D. Raabe, D. Ponge, P.J. Uggowitzer, M. Roscher, M. Paolantonio, C. Liu, H. Antrekowitsch, E. Kozeschnik, D. Seidmann, B. Gault et al., Making sustainable aluminum by recycling scrap: the science of "Dirty" alloys. Prog. Mater. Sci. (2022). https://doi.org/10.1016/j.pmatsci.2022.100947
- [51] M. Bertram, S. Ramkumar, H. Rechberger, G. Rombach, C. Bayliss, K.J. Martchek, D.B. Müller, G. Liu, A regionally-linked, dynamic material flow modelling tool for rolled, extruded and cast aluminium products. Resour. Conserv. Recycl. 125, 48–69 (2017). https://doi.org/10.1016/j.resconrec.2017.05.014
- [52] D. Raabe, C.C. Tasan, E.A. Olivetti, Strategies for improving the sustainability of structural metals. Nature 575, 64–74 (2019). https://doi.org/10.1038/s41586-019-1702-5
- [53] L.B. Chappuis, (Vehicle P.E.-M.F.M.C. Material Specifications and Recycling for the 2015 Ford F-150 (2015)
- [54] G. Rombach, Raw material supply by aluminium recycling-efficiency evaluation and long-term availability. Acta Mater. 61, 1012–1020 (2013). https://doi.org/10.1016/j.actamat.2012.08.064
- [55] European Aluminium Circular Aluminium Action Plan. A Strategy for Achieving Aluminium's Full Potential for Circular Economy by 2030. Executive Summary.
- [56] B. Mathai, C. Mathew, Effect of silicon on microstructure and mechanical properties of Cu-Fe alloys. J. Alloys Compd. 707, 184–188 (2017). https://doi.org/10.1016/j.jallcom.2016.12.352
- [57] G.K. Sigworth, R.J. Donahue, The metallurgy of aluminum alloys for structural high-pressure die castings. Int. J. Met. 15, 1031–1046 (2021). https://doi.org/10.1007/s40962-020-00535-x
- [58] L. Zhang, J. Li, Investigating thermal and mechanical characteristics of die-casting aluminum alloys: a comprehensive investigation via thermal analysis. Int. J. Met. (2024). https://doi.org/10.1007/s40962-024-01258-z
- [59] P. Ferro, F. Bonollo, lightweight design versus raw materials criticalities. Sustain. Mater. Technol. 35, e00543 (2023). https://doi.org/10.1016/j.susmat.2022.e00543
- [60] P. Ferro, F. Bonollo, Materials selection in a critical raw materials perspective. Mater. Des. 177, 107848 (2019). https://doi.org/10.1016/j.matdes.2019.107848
- [61] M. Di Sabatino, On fluidity of aluminium alloys. Metall. Ital. 100 (2008)
- [62] J. Campbell, Complete casting Handbook: Metal Casting Processes, Metallurgy, Techniques and Design (Butterworth-Heinemann, 2015)
- [63] H.S. Bang, H.I. Kwon, S.B. Chung, D.U. Kim, M.S. Kim, Experimental investigation and numerical simulation of the fluidity of A356 aluminum alloy. Metals (Basel). 12, 1–13 (2022). https://doi.org/10.3390/met12111986
- [64] A. Heidarzadeh, M. Emamy, A. Rahimzadeh, R. Soufi, D. Sohrabi BabaHeidary, S. Nasibi, The effect of copper addition on the fluidity and viscosity of an Al-Mg-Si Alloy. J. Mater. Eng. Perform. 23, 469–476 (2014). https://doi.org/10.1007/s11665-013-0794-6
- [65] A.T. Dinsdale, P.N. Quested, The viscosity of aluminum and its alloys - a review of data and models. J. Mater. Sci. 39, 7221–7228 (2004). https://doi.org/10.1023/B:JMSC.0000048735.50256.96
- [66] E.A. Moelwyn-Hughes, Physical Chemistry (Cambridge University Press, 2015)
- [67] A.K. Dahle, D.H. StJohn, Rheological behaviour of the mushy zone and its effect on the formation of casting defects during solidification. Acta Mater. 47, 31–41 (1998). https://doi.org/10.1016/S1359-6454(98)00342-5
- [68] S. Bozorgi, K. Haberl, C. Kneissl, T. Pabel, P. Schumacher, Effect of alloying elements (magnesium and copper) on hot cracking susceptibility of AlSiMgCu-alloys. TMS Annu. Meet. (2011). https://doi.org/10.1002/9781118062050.ch14
- [69] J.F. Wallace, A guide to correcting soldering. Die Cast. Eng. 50, 44–47 (2006)
- [70] B. Dewhirst, S. Li, P. Hogan, D. Apelian, Castability measures for diecasting alloys: fluidity, hot tearing, and die soldering. Metall. Ital. 101 (2009)
- [71] M. Kohlhepp, P.J. Uggowitzer, M. Hummel, H.W. Höppel, Formation of die soldering and the influence of alloying elements on the intermetallic interface. Materials (Basel) (2021). https://doi.org/10.3390/ma14071580
- [72] S. Belmares-Perales, M. Castro-Román, M. Herrera-Trejo, L.E. Ramirez-Vidaurri, Effect of cooling rate and Fe/Mn weight ratio on volume fractions of a-AlFeSi and ẞ-AlFeSi Phases in Al-7.3Si-3.5Cu Alloy. Met. Mater. Int. 14, 307–314 (2008). https://doi.org/10.3365/met.mat.2008.06.307
- [73] S. Seifeddine, S. Johansson, I.L. Svensson, the influence of cooling rate and manganese content on the ẞ-Al5FeSi phase formation and mechanical properties of Al-Si-based alloys. Mater. Sci. Eng. A 490, 385–390 (2008). https://doi.org/10.1016/j.msea.2008.01.056
- [74] Q. Han, S. Viswanathan, Analysis of the mechanism of die soldering in aluminum die casting. Metall. Mater. Trans. A Phys. Metall. Mater. Sci. 34, 139–146 (2003). https://doi.org/10.1007/s11661-003-0215-9
- [75] J.C. Lin, Q.T. Fang, C.E. Garesche, H. Haddenhorst, Al-Si-Mg-Mn casting alloy and method 11 (2004)
- [76] R.D. Peterson, A historical perspective on dross processing. Mater. Sci. Forum 693, 13–23 (2011). https://doi.org/10.4028/www.scientific.net/MSF.693.13
- [77] E. Tillová, M. Chalupová, L. Kuchariková, I. Švecová, J. Belan, Sludge phases as cause of higher wear of cutting tools during machining of secondary AlSi12Cu₁ castings. Manuf. Technol. 19, 874–879 (2019). https://doi.org/10.21062/ujep/387.2019/a/1213-2489/mt/19/5/874
- [78] S. Ferraro, G. Timelli, Influence of sludge particles on the tensile properties of die-cast secondary aluminum alloys. Metall. Mater. Trans. B Process Metall. Mater. Process. Sci. 46, 1022–1034 (2015). https://doi.org/10.1007/s11663-014-0260-3
- [79] A. Fabrizi, G. Timelli, The influence of cooling rate and Fe/Cr content on the evolution of Fe-rich compounds in a secondary Al–Si–Cu diecasting alloy. IOP Conf. Ser. Mater. Sci. Eng. (2016). https://doi.org/10.1088/1757-899X/117/1/012017
- [80] S.G. Shabestari, The effect of iron and manganese on the formation of intermetallic compounds in aluminum-silicon alloys. Mater. Sci. Eng. A 383, 289–298 (2004). https://doi.org/10.1016/j.msea.2004.06.022
9. 저작권:
- 본 자료는 "Osama Asghar, Mattia Franceschi, Paolo Ferro and Franco Bonollo"의 "저임계 원료 사용 및 자동차 응용 분야를 위한 높은 주조 가공성을 갖춘 새로운 알루미늄 합금 설계 전략" 논문을 기반으로 합니다.
- 논문 출처: https://doi.org/10.1007/s40962-024-01502-6
본 자료는 위 논문을 소개하기 위해 작성되었으며, 상업적 목적으로 무단 사용하는 것을 금합니다. Copyright © 2025 CASTMAN. All rights reserved.