1. 개요:
- 제목: 자동차 OEM용 마그네슘 합금 부품의 개발 및 응용: 리뷰 (Development and application of magnesium alloy parts for automotive OEMs: A review)
- 저자: Bo Liu, Jian Yang, Xiaoyu Zhang, Qin Yang, Jinsheng Zhang, Xiaoqing Li
- 발행 연도: 2023년
- 발행 저널/학회: Journal of Magnesium and Alloys
- 키워드: 마그네슘 합금; 순정 부품 제조업체; 자동차 응용; 개발 프로세스 (Magnesium alloy; Original equipment manufacturer; Automotive application; Development process)
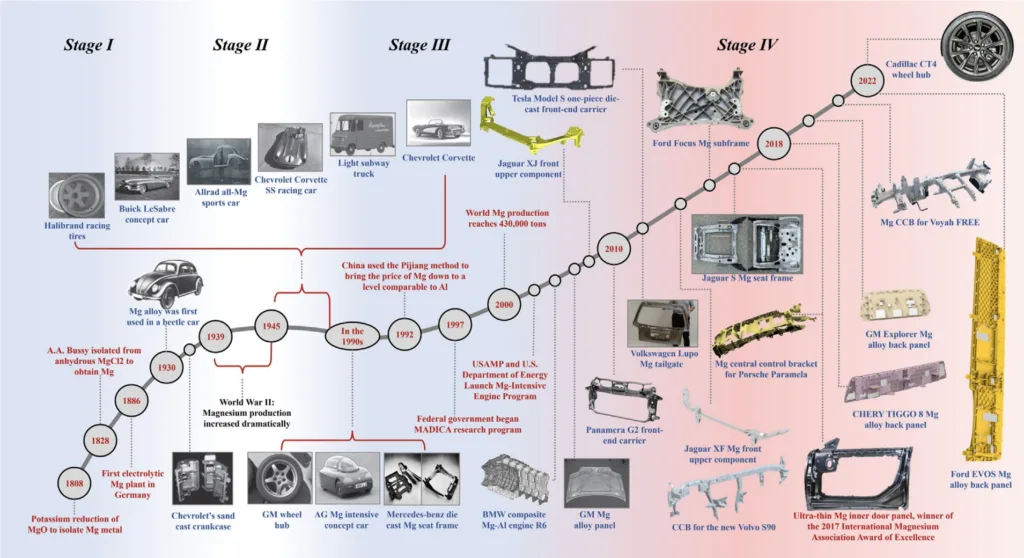
2. 연구 배경:
- 연구 주제의 사회적/학문적 맥락:
중국은 현재 "에너지 절약 및 배출 감소"와 "탄소 중립" 전략을 적극적으로 추진하고 있습니다. 중국에서 자원이 가장 풍부한 경금속 재료인 마그네슘(Mg) 합금은 자동차, 철도 운송, 항공 우주, 의료 및 전자 제품 분야로 응용 분야를 점차 확대하고 있습니다. 충칭 대학교, 상하이 자오퉁 대학교, 호주 국립 대학교 등에서는 Mg 합금의 제조, 특성 및 공정에 대한 광범위한 연구를 수행해 왔습니다. 지난 20년 동안 자동차 산업에서 Mg 합금의 비중은 점차 확대되었지만, 현재 자동차용 Mg 합금 부품의 설계 및 개발에 대한 보고는 드뭅니다. - 기존 연구의 한계:
Mg 합금의 사용 증대에도 불구하고, 특히 자동차용 Mg 합금 부품의 설계 및 개발에 대한 상세한 보고는 부족합니다. 이러한 부품의 전체 개발 과정과 성능 요구 사항에 대한 정보가 제한적입니다. - 연구의 필요성:
본 리뷰는 자동차의 4대 주요 시스템(차체, 섀시, 파워트레인, 내외장 시스템)을 중심으로 Mg 합금의 응용 모델과 대표적인 부품 사례를 요약할 필요성을 제기합니다. 또한 순정 부품 제조업체(OEM)를 위한 신뢰성 있는 다이캐스팅 Mg 합금 부품의 개발 논리를 소개하고자 합니다. 궁극적으로 자동차 분야에서 Mg 합금 부품을 개발하는 자동차 OEM의 방법, 프로세스 및 주요 고려 사항을 공유하여 자동차 분야에서 Mg 합금 응용에 대한 자신감과 동기를 부여하는 것을 목표로 합니다. 마지막으로, Mg 합금 재료가 직면한 여러 과제와 잠재적인 해결책을 식별하고 논의하는 것을 목표로 합니다.
3. 연구 목적 및 연구 질문:
- 연구 목적:
본 리뷰의 주요 목적은 자동차 부품용 다양한 Mg 합금 시리즈 개발의 역사적 발전과 최근의 진보를 요약하는 것입니다. 기존 문헌에 대한 비판적 분석을 제공합니다. 가장 중요한 것은 실제 생산 사례를 통해 다이캐스팅 Mg 합금의 전체 공정 개발 기술 경로를 설명하는 것입니다. 이는 OEM이 새로운 Mg 부품 개발에 대한 자신감을 높이기 위한 것이며, 자동차 경량화 연구에 참여하는 기업 및 제조업체에 유익한 정보가 될 것입니다. 또한, 본 리뷰는 국가 정책, 환경 보호, 에너지 절약 및 소비자 요구와 관련하여 Mg 합금 재료가 직면한 과제를 논의하고 미래 전망을 제시합니다. - 주요 연구 질문:
본 연구는 다음과 같은 질문을 암묵적으로 다룹니다.- 4대 주요 자동차 시스템 내에서 Mg 합금 부품의 일반적인 응용 분야와 모델은 무엇입니까?
- 자동차 OEM용 신뢰성 있는 다이캐스팅 Mg 합금 부품을 만들기 위한 단계별 개발 프로세스는 무엇입니까?
- 자동차 분야에서 Mg 합금의 광범위한 응용을 방해하는 주요 장애물은 무엇입니까?
- 연구 가설:
기본 가설은 Mg 합금 응용에 대한 포괄적인 리뷰와 성공적인 개발 프로세스를 보여주는 상세한 OEM 사례 연구를 제공함으로써 OEM의 자신감을 크게 높이고 자동차 제조에서 Mg 합금의 더 큰 채택을 유도할 수 있다는 것입니다.
4. 연구 방법론:
- 연구 설계:
본 연구는 기존 문헌과 자동차 OEM의 실제 사례 연구에서 정보를 종합하는 리뷰 기반 연구 설계를 채택합니다. - 자료 수집 방법:
본 연구는 자동차 응용 분야의 마그네슘 합금과 관련된 학술 출판물 및 산업 보고서에 대한 포괄적인 문헌 검토에 의존합니다. 또한 실제 OEM 응용 사례 연구를 통합하여 개발 프로세스를 설명합니다. - 분석 방법:
분석은 기존 문헌을 요약하고 비판적으로 분석하는 것을 포함합니다. 사례 연구 분석은 자동차 제조에서 Mg 합금 부품의 실제 응용 및 개발 프로세스를 이해하는 데 사용됩니다. - 연구 대상 및 범위:
본 리뷰의 범위는 자동차 부품에 다양한 Mg 합금 시리즈의 응용을 포함합니다. 차체, 섀시, 파워트레인, 내외장 트림의 4대 주요 차량 시스템을 중심으로 구성됩니다. 본 연구는 다이캐스팅을 주요 제조 공정으로 특정하여 개발 기술 경로를 상세히 설명하기 위해 OEM 사례 연구를 검토합니다.
5. 주요 연구 결과:
- 주요 연구 결과:
본 리뷰는 4대 주요 차량 시스템에 걸쳐 Mg 합금의 응용 모델과 대표적인 부품 사례를 성공적으로 요약했습니다. 신뢰성 있는 다이캐스팅 Mg 합금 부품의 개발 논리를 설명하기 위해 두 가지 OEM 사례 연구가 제시되었습니다. 또한, 현재 자동차 산업에서 Mg 합금의 광범위한 채택을 방해하는 여러 과제를 식별하고 분류했으며 잠재적인 해결책을 논의했습니다. - 통계적/질적 분석 결과:
본 논문은 표와 그림 형태로 다음과 같은 정량적 데이터를 제시합니다.- 표 1: "Mg 합금의 기계적 특성 비교". 이 표는 Mg, AZ91, AM50, AS41, AE42 및 AISI8Cu3 합금의 밀도, 비열, 열전도율, 용융 온도, 인장 강도, 항복 강도, 연신율, 탄성 계수 및 브리넬 경도를 제공합니다.
- 표 2: "차체 내 Mg 합금 시리즈의 응용 분야". 이 표는 Mg 합금 시리즈(AZ, AM, AS, AE, AXE 및 AJ), 성능 장점, 특정 분류(예: AZ91D, AM60B), 응용 분야(예: 중앙 제어 브래킷, 시트 프레임) 및 다이캐스팅 공정을 나열합니다.
- 표 3: "일부 모델의 Mg 프런트 엔드 캐리어 및 프런트 상부 부품의 예". 이 표는 차량 유형, 기간, 무게/kg을 상세히 설명하고 Jaguar XJ, Jaguar XF, Benz AMG GT, Lincoln MKT, Tesla Model S, NIO ES8, Range Rover, Porsche Panamera G2 및 Changan ENDO EV460에 대한 부품 및 차량 유형 이미지를 제공합니다.
- 표 4: "자동차 응용 분야에서 일반적인 Mg CCB의 일부 사례". 이 표는 Rongwei 550, Ford Explorer, Dodge Caliber, LandRover LWB 5.0, LandRover LR3, ARCFOX-1(C11CB), Mercedes-Benz M-Class, Mini Cooper, Mercedes-Benz E-Class 및 Voyah FREE에 대한 차량 유형, 무게/kg, CCB 사진 및 차량 유형 사진을 나열합니다.
- 표 5: "강도 및 모달 분석 결과". 이 표는 다양한 프런트 커버 잠금 강성, 하중 한계, 극한 인장 강도, 강도, 라디에이터 시스템 모듈 장착 지점 강성, 헤드라이트 브래킷 강성, 모달 분석 및 가속 충격 테스트에 대한 결과를 제시하고 결과가 적격인지 여부를 나타냅니다.
- 표 6: "금형 흐름 분석 매개변수 설정". 이 표는 3라운드의 금형 흐름 분석에 대한 재료 온도, 금형 온도, 압력 챔버 길이, 재료 케이크 두께, 충전 속도, 임계 속도 및 고속을 보여줍니다.
- Aston Martin DB9 측면 도어 부품의 경우 "43% 감소", Chrysler Pacifica 테일게이트의 경우 "50%" 중량 감소 등 특정 부품의 중량 감소율이 언급됩니다.
- 자료 해석:
리뷰 전체에서 제시되고 분석된 데이터는 Mg 합금이 자동차 응용 분야에서 상당한 경량화 잠재력을 제공한다는 것을 일관되게 나타냅니다. OEM 사례 연구는 다이캐스팅 Mg 합금 부품 사용의 타당성과 이점을 입증합니다. 그러나 비용, 부식 및 기술 성숙도와 관련된 과제는 더 광범위한 채택을 위해 극복해야 할 중요한 장애물로 남아 있습니다. - 그림 목록:
- 그림 1. 자동차 부품 개발 역사 과정에서 Mg 합금.
- 그림 2. 자동차 도어의 Mg 합금 개발 및 응용.
- 그림 3. 프런트 엔드 캐리어 및 프런트 상부 부품의 Mg 합금 개발 및 응용.
- 그림 4. 루프, 후드 및 트렁크 리드의 Mg 합금 개발 및 응용.
- 그림 5. 휠의 Mg 합금 개발 및 응용.
- 그림 6. 스티어링 휠의 Mg 합금 개발 및 응용.
- 그림 7. 서브프레임의 Mg 합금 개발 및 응용.
- 그림 8. 파워트레인 응용 분야의 Mg 합금.
- 그림 9. 오일 팬의 Mg 합금 개발 및 응용.
- 그림 10. 시트 프레임의 Mg 합금 응용.
- 그림 11. Mg 합금 CCB의 여러 응용 분야.
- 그림 12. Mg 합금 중앙 브래킷의 여러 응용 분야.
- 그림 13. 자동차용 기타 Mg 합금 부품.
- 그림 14. MASF 전체 공정 분석 프로세스 및 결과.
- 그림 15. MAFC 전체 공정 분석 프로세스 및 결과.
- 그림 16. MASF 상세 개발 프로세스.
- 그림 17. MAFC 상세 개발 프로세스.
- 그림 18. Mg 합금 부식 방지 솔루션.
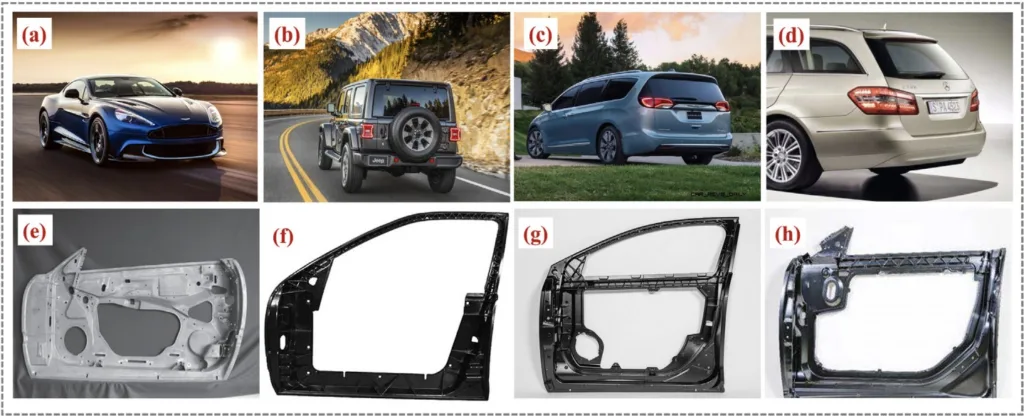
Mercedes-Benz E-Class T-Model featuring the hybrid Mg-Al hatch back; (e) Inner door frame of the Daimler-Chrysler SL Roadster; (f) Ford’s concept die-cast Mg door inner with an open architecture; (g) Integrated Mg die-cast door inner designed as part of a DOE sponsored project led by GMC; (h) Ultra-thin and ultra-light Mg alloy door inner.
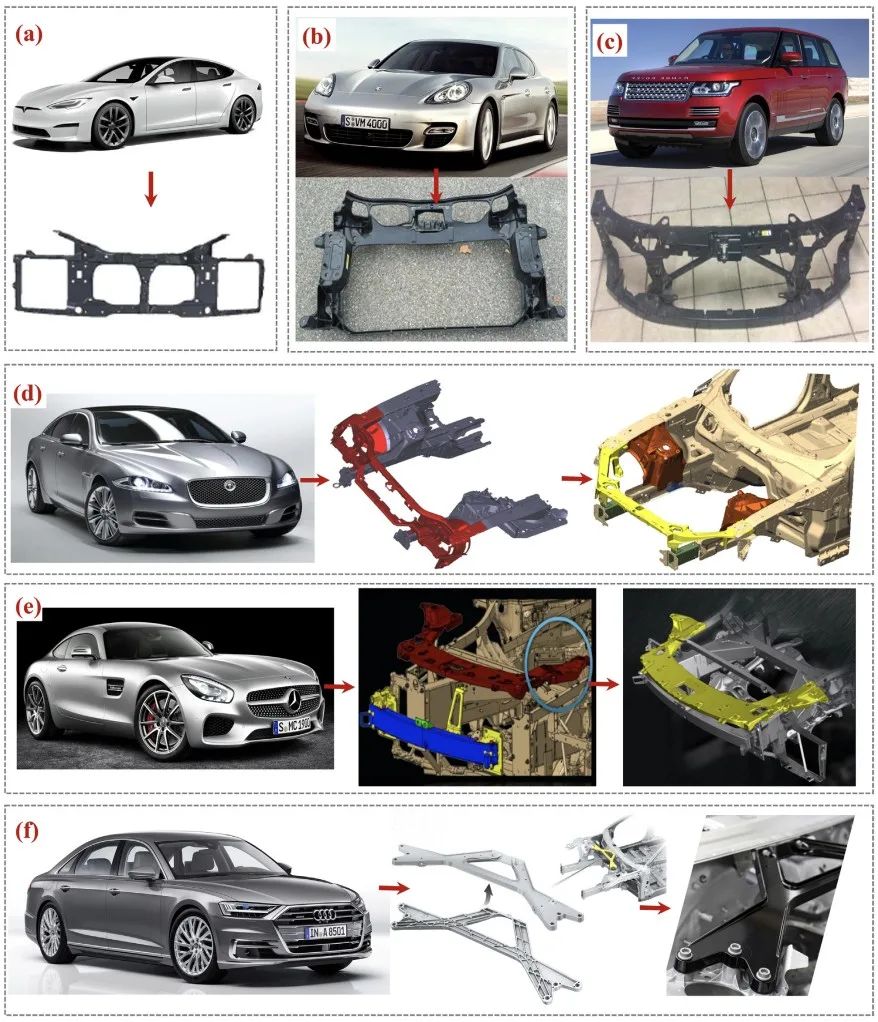
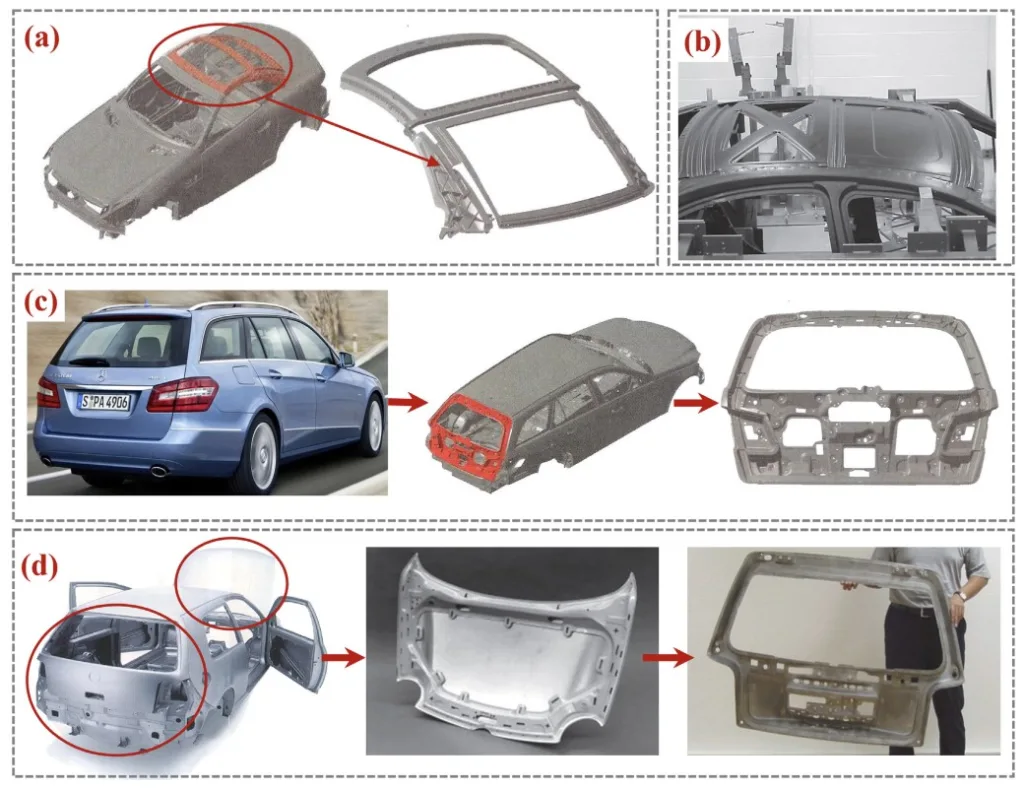
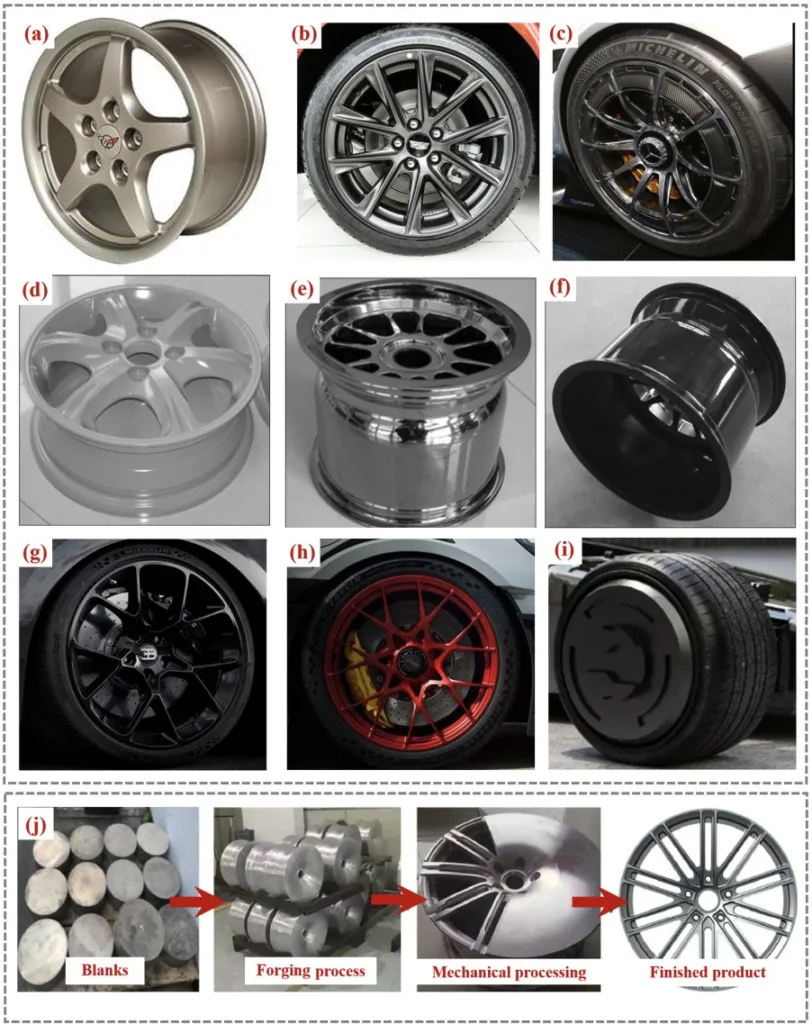
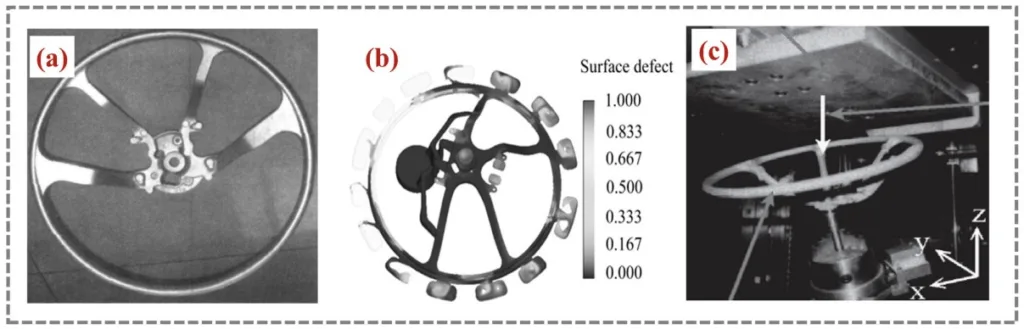
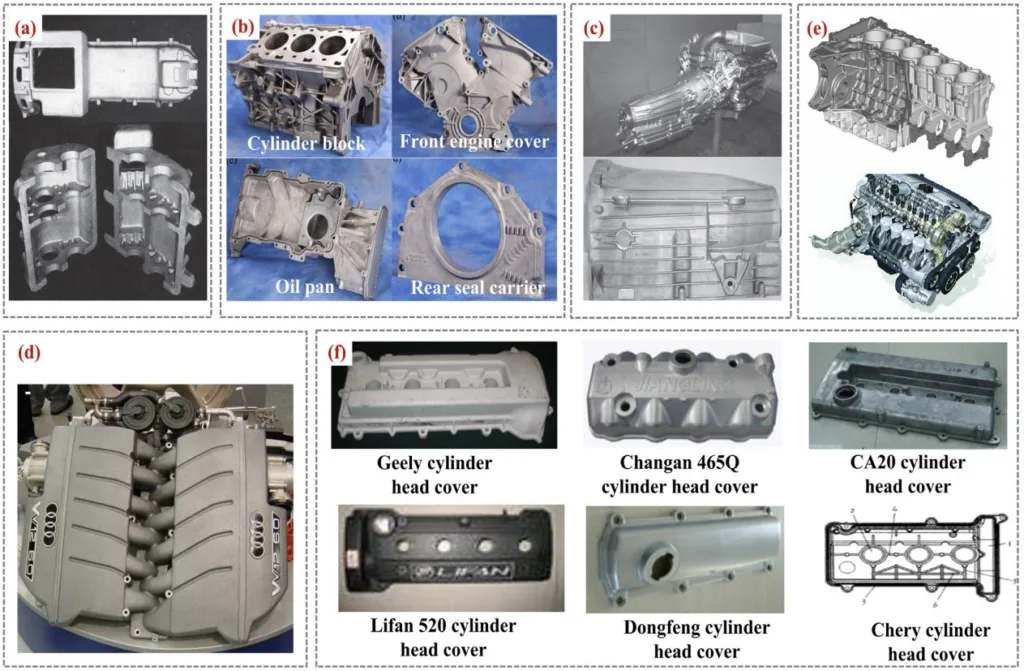
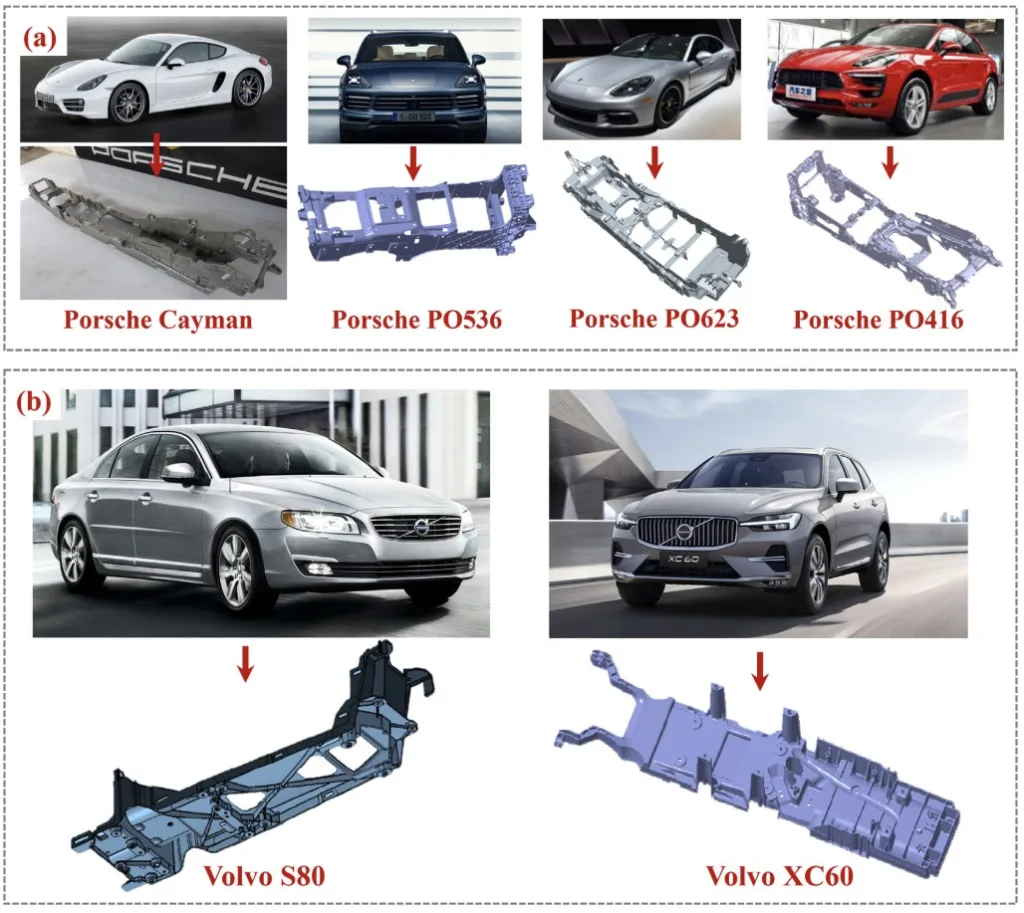
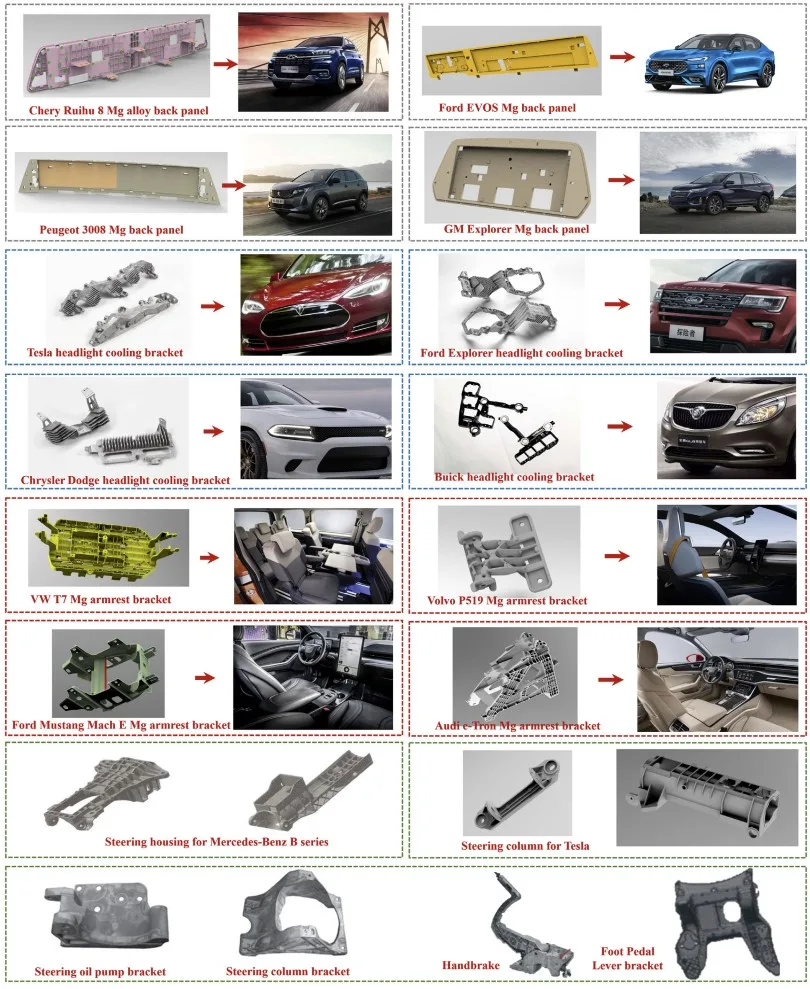
6. 결론 및 논의:
- 주요 결과 요약:
본 리뷰는 마그네슘 합금이 유리한 특성으로 인해 자동차 산업에서 가치 있는 엔지니어링 재료로 자리매김했다고 결론 내립니다. 본 논문은 OEM 생산 사례를 통해 다이캐스팅 Mg 합금의 개발 기술 경로를 강조했습니다. 또한 자동차에서 Mg 합금의 광범위한 응용 분야를 보여주어 OEM이 이러한 재료를 새로운 부품 설계에 채택하는 데 대한 자신감을 높이는 것을 목표로 합니다. Mg 합금의 응용은 "적재적소에 적합한 재료"라는 원칙을 준수하여 가벼운 밀도와 우수한 유동성과 같은 장점을 활용하면서 낮은 강도 및 부식 민감성과 같은 단점을 완화합니다. 리뷰에서는 AM50/60 및 AZ91D 시리즈 Mg 합금이 주류 재료이며 다이캐스팅이 가장 일반적인 성형 공정임을 확인했습니다. Mg 합금은 일반적으로 높은 하중을 견디는 빔 구조 부품보다는 스켈레톤 또는 브래킷 형태로 사용되며 갈바닉 부식에 덜 취약한 환경에 적용됩니다. 구조 설계 및 최적화는 비용 절감에 매우 중요합니다. - 연구의 학문적 의의:
본 리뷰는 자동차 분야에서 Mg 합금 응용에 대한 포괄적이고 최신 개요를 제공합니다. 현재 연구 개발 상태에 대한 귀중한 학문적 통찰력을 제공하며, 향후 연구를 위한 참고 자료이자 해당 분야 연구자들을 위한 통합된 자료 역할을 합니다. - 실용적 의미:
본 리뷰는 자동차 OEM에 중요한 실용적 의미를 갖습니다. 성공적인 OEM 사례 연구를 소개하고 개발 프로세스를 상세히 설명함으로써 새로운 부품 개발에 Mg 합금을 채택하는 OEM의 자신감을 높이는 것을 목표로 합니다. Mg 합금 부품 개발에 대한 실용적인 참고 자료를 제공하고 자동차 경량화의 미래 혁신을 위한 주요 과제와 기회를 강조합니다. - 연구의 한계:
본 리뷰의 범위는 주로 다이캐스팅 공정 및 OEM 사례 연구에 초점을 맞추고 있습니다. 자동차의 모든 가능한 Mg 합금 응용 분야를 포괄적으로 다루지 않거나 다른 제조 기술을 자세히 탐구하지 않을 수 있습니다.
7. 향후 후속 연구:
- 후속 연구 방향:
본 논문은 향후 연구에서 다음과 같은 분야를 탐구해야 한다고 제안합니다.- Mg 합금 적층 제조 기술.
- Mg 합금의 수소 저장 응용.
- 포괄적인 Mg 합금 재료 데이터베이스 및 성능 평가 시스템 개발.
- Mg 합금 제조의 공정 및 비용 최적화 문제 해결.
- 기술 혁신 격차 및 산업 구조 모순 극복.
- 추가 탐구가 필요한 영역:
향후 연구는 다음 사항에 초점을 맞춰야 합니다.- 차량의 추가 중량 감소를 달성하기 위한 새로운 Mg 합금 구조 및 기술 개발.
- 지속 가능하고 재활용 가능한 Mg 생산을 위한 친환경 전해 Mg 기술 촉진.
- Mg 합금 개발 및 응용 분야의 글로벌 과제를 해결하기 위해 대학, 정부 및 연구 기관 간의 협력 강화.
8. 참고 문헌:
- [1] C. Moosbrugger, L. Marquard, Engineering Properties of Magnesium Alloys, ASM International, 2017.
- [2] F. Tong, X. Chen, S. Wei, et al., J. Magn. Alloys 9 (6) (2021) 1967-1976.
- [3] R. Li, Q. Liu, R. Zhang, et al., Energy Storage Mater. (2022).
- [4] S.H. Kang, D.W. Han, H.K. Kim, J. Magn. Alloys 8 (1) (2020) 241-251.
- [5] G. Ma, H. Xiao, J. Ye, et al., Mater. Sci. Technol. 36 (6) (2020) 645-653.
- [6] M.K. Kulekci, Int. J. Adv. Manuf. Technol. 39 (2008) 851-865.
- [7] G.L. Song, A. Atrens, Adv. Eng. Mater. 1 (1999) 11-33.
- [8] M. Grassel, M. Koch, South Dakota Med. 75 (5) (2022).
- [9] O. Myagmarjav, M. Zamengo, J. Ryu, et al., Appl. Therm. Eng. 91 (2015) 377-386.
- [10] Y. Yang, J. Zhang, B. Li, Ekoloji, 28 (107) (2019) 4827-4833.
- [11] J.S. Hoksbergen, M. Ramulu, P. Reinhall, et al., Appl. Compos. Mater. 16 (5) (2009) 263-283.
- [12] J.S. Binoj, N. Manikandan, P. Thejasree, et al., in: Investigations on Wire Electrical Discharge Machining of Magnesium Alloy AZ31B by Taguchi's Approach. Recent Advances in Materials and Modern Manufacturing, Springer, Singapore, 2022, pp. 923-931.
- [13] G. Sasaki, in: Material Mechanical Properties and Microstructure of Magnesium Alloy Matrix Composites Fabricated by Casting Process, 426, Materials Science Forum. Trans Tech Publications Ltd., Zurich-Uetikon, Switzerland, 2003, pp. 2015-2019.
- [14] Z.Q. Huang, H.Y. Lai, H.B. Zhou, et al., J. Min. Metall. B: Metall. 58 (1) (2022) 1-10.
- [15] N.P. Papenberg, S. Gneiger, I. Weissensteiner, et al., Materials (Basel) 13 (4) (2020) 985.
- [16] Z Zeng, M Salehi, A Kopp, et al., J. Magn. Alloys 10 (6) (2022) 1511-1541.
- [17] A.A Luo, J. Magn. Alloys 1 (1) (2013) 2-22.
- [18] T. Xu, Y. Yang, X. Peng, et al., J. Magn. Alloys 7 (3) (2019) 536-544.
- [19] J.A. Santamaría, J. Sertucha, A. Redondo, et al., Metals (Basel) 12 (4) (2022) 656.
- [20] F. D'Errico, D. Casari, La Metall. Ital. 36 (2022).
- [21] S.R. Golroudbary, I. Makarava, E. Repo, et al., Proc. CIRP 105 (2022) 589-594.
- [22] A.A Luo, Fundam. Magn. Alloy Metall. 266 (2013) 316.
- [23] S Prithivirajan, G M Naik, S Narendranath, et al., Int. J. Lightw. Mater. Manuf. 6 (1) (2023) 82-107.
- [24] A. Dziubińska, A. Gontarz, M. Dziubiński, et al., Adv. Sci. Technol. Res. J. 10 (31) (2016).
- [25] G.G. Wang, J.P Weiler, J. Magn. Alloys (2022).
- [26] Y. Yang, X. Xiong, J. Chen, et al., J. Magn. Alloys 9 (3) (2021) 705-747.
- [27] A.G Morachevskii, Russ. J. Appl. Chem. 92 (10) (2019) 1325-1335.
- [28] M.O. Pekguleryuz, A.A Kaya, Adv. Eng. Mater. 5 (12) (2003) 866-878.
- [29] J. Tan, S. Ramakrishna, Appl. Sci. 11 (15) (2021) 6861.
- [30] Alias J., Bakar N.F.A., Romzi M.A.F., et al. Development of Mg-Graphene composites and effect on microstructure and mechanical properties-a review. Enabling industry 4.0 through advances in manufacturing and materials, 2022: 139-149.
- [31] G.R Chapman, Min. Process. Extract. Metall. 111 (2) (2002) 49-52.
- [32] J. Li, B. Li, H. Shao, et al., Catalysts 8 (2) (2018) 89.
- [33] X. Tang, L. Guo, Q. Liu, et al., Cryst. Res. Technol. 50 (3) (2015) 203-209.
- [34] I. Kabdaşlı, A. Demirbilek, T. Ölmez, Fresenius Environ. Bull. 13 (10) (2004) 951-955.
- [35] MLQLH Guo, XQ B G F Ye, Z. Wu, Progr. Chem. 21 (11) (2009) 2358.
- [36] G. Long, P. Ma, M. Chu, in: Ammoniation Technology For Dehydration of Hydrated Magnesium Chloride in China, 488, Materials Science Forum. Trans Tech Publications Ltd, 2005, pp. 95-98.
- [37] F. Wang, J.J. Wang, Q.S. Li, et al., Adv. Mater. Sci. Eng. 2022 (2022).
- [38] D.B Zhao, in: The FEA Comparison of the Front Sub Frame in a Car between JDM2 Magnesium and steel. Applied Mechanics and Materials, 538, Trans Tech Publications Ltd, 2014, pp. 87-90.
- [39] R. Lu, K. Jiao, Y. Zhao, et al., Materials (Basel) 13 (20) (2020) 4654.
- [40] R. Senthilkumar, P. Ponnusamy, M. Prakash, SAE Int. J. Adv. Curr. Pract. Mob. 3 (2020) 831-835 (2020-28-0425).
- [41] Y.Z. Li, D.W. Fan, J.M Chen, Adv. Mat. Res. 211 (2011) 705-709.
- [42] J. Lyu, A. Lider, V. Kudiiarov, Metals (Basel) 9 (7) (2019) 768.
- [43] D.T. Nguyen, S.W. Song, J. Power Sources 368 (2017) 11-17.
- [44] J. Chen, L. Tan, X. Yu, et al., J. Mech. Behav. Biomed. Mater. 87 (2018) 68-79.
- [45] SAE J 465-1983, Magnesium Casting Alloys.
- [46] Pantelakis S.G., Alexopoulos N.D., Chamos A.N. Mechanical performance evaluation of cast magnesium alloys for automotive and aeronautical applications. 2007.
- [47] B.R. Powell, A.A. Luo, P.E Krajewski, Woodhead Publishing, 2012, pp. 150-209.
- [48] S. Ando, N. Harada, M. Tsushida, et al., Key Eng. Mater. 345 (2007) 101-104.
- [49] T. Li, J. Rao, J. Zheng, et al., J. Magn. Alloys 10 (6) (2022) 1581-1597.
- [50] D. Wenbo, Q. Yaling, Y. Zhenjie, et al., Rare Met. Mater. Eng. 38 (10) (2009) 1870-1875.
- [51] R.B. Figueiredo, M.T.P. Aguilar, P.R. Cetlin, et al., Processing magnesium alloys by severe plastic deformation. IOP conference series: materials science and engineering, 63, IOP Publishing, 2014.
- [52] S.S. Wu, J.W. Zhao, L. Wan, et al., in: Numerical Simulation of Mould Filling in Rheo-Diecasting Process of Semi-Solid Magnesium alloys. Solid State Phenomena, 116, Trans Tech Publications Ltd, 2006, pp. 554-557.
- [53] H. Yan, T. Wang, M.F Fu, Mater. Sci. Forum 575 (2008) 32-36.
- [54] F. Czerwinski, in: Selected Aspects of Semisolid Forming Magnesium alloys. Materials science Forum, 539, Trans Tech Publications Ltd, 2007, pp. 1644-1649.
- [55] F. Czerwinski, Materials (Basel) 14 (21) (2021) 6631.
- [56] Y. Zhang, Q. Zhu, C. Su, et al., Front. Chem. 10 (2022).
- [57] R. Kong, F. Xue, J. Wang, et al., Res. Policy 52 (2017) 19-28.
- [58] Y. Yu, Auto Manuf. Eng. 3 (11) (2020).
- [59] B.R. Powell, P.E. Krajewski, A.A Luo, Magnesium Alloys for Lightweight Powertrains and Automotive Structures, in: Materials, Design and Manufacturing for Lightweight Vehicles, Elsevier, Amsterdam, The Netherlands, 2021, pp. 125-186.
- [60] M.A Shand, The Chemistry and Technology of Magnesia, John Wiley & Sons, 2006.
- [61] D.A Kramer, Magnesium, its Alloys and Compounds, in: Magnesium, its Alloys and Compounds, 1, US Geological Survey Open-File Report, 2001, p. 341.
- [62] J. Durlach, in: Overview of Magnesium research: History and Current trends. New Perspectives in Magnesium Research, Springer, London, 2007, pp. 3-10.
- [63] B.J.C. Luthringer, F. Feyerabend, R. Willumeit-Römer, Magn. Res. 27 (4) (2014) 142-154.
- [64] B.B Clow, in: History of Primary Magnesium Since World War II. Essential Readings in Magnesium Technology, Springer, Cham, 2016, pp. 85-87.
- [65] USAMP teamMagnesium Vision 2020: A North American Automotive Strategic Vision For Magnesium, USCAR, 2006.
- [66] C. Blawert, N. Hort, K.U Kainer, Trans. Indian Inst. Met 57 (4) (2004) 397-408.
- [67] T.K. Aune, H. Westengen, T. Ruden, SAE Trans. (1994) 553-557.
- [68] Hawke D., Gaw K. Effects of chemical surface treatments on the performance of an automotive paint system on die cast magnesium. SAE Technical Paper, 1992.
- [69] G.D. Tong, H.F. Liu, Y.H Liu, Trans. Nonferrous Met. Soc. China 20 (2010) s336-s340.
- [70] R. Seetharaman, B. Lavanya, N. Niharika, et al., Mater. Today: Proc. 4 (6) (2017) 6743-6749.
- [71] Y.G. Liu, Z.H. Huang, H. Ding, et al., Key Eng. Mater. 353 (2007) 1614-1616.
- [72] Jacques R.P., DasGupta R., Shearouse J.D. Hot chamber diecasting of magnesium alloy AM50A for automotive interior structural components. SAE Technical Paper, 1996.
- [73] Grebetz J.C. A comparison of the impact characteristics of several magnesium die casting alloys. SAE Technical Paper, 1993.
- [74] J. Jekl, J. Auld, C. Sweet, et al., Development of a Thin-Wall Magnesium Side Door Inner Panel for Automobiles, General Motors LLC, Detroit, MI (United States), 2015.
- [75] Murray R.W., Hillis J.E. Magnesium finishing: chemical treatment and coating practices. 1990.
- [76] S. Annamalai, S. Periyakgoundar, K. Paramasivam, et al., Adv. Mater. Sci. Eng. 2020 (2020).
- [77] Durairaj S.R.N., Ganesan T., Rao P.C. Vibration analysis on magnesium alloy housing and analysis of resonant frequency on the housing between magnesium and aluminium alloy. SAE Technical Paper, 2017.
- [78] Luo A.A., Forsmark J., Sun X., et al. Mechanical and thermophysical properties of magnesium alloy extrusions. SAE Technical Paper, 2010.
- [79] Verma R., Carter J.T. Quick plastic forming of a decklid inner panel with commercial AZ31 magnesium sheet. SAE Technical Paper, 2006.
- [80] Kim S.W., Lee Y.S. Warm forming of 3t Mg alloy sheet for an automotive electronic compressor case. SAE Technical Paper, 2014.
- [81] Aune T.K., Westengen H., Ruden T. Mechanical properties of energy absorbing magnesium alloys. SAE Technical Paper, 1993.
- [82] S.V. Galatanu, M. Scano, D. Pietras, et al., Proc. Struct. Integr. 26 (2020) 269-276.
- [83] Effect of Section Thicknesses On Tensile Behavior and Microstructure of High Pressure Die Cast Magnesium Alloy AM50. Pacific Rim International Conference On Advanced Materials and Processing (PRICM 5) pt.1. Dept. of Mechanical, Automotive & Materials Engineering University of Windsor Windsor, Ontario, Canada, 2005 N9B 3P4; Manufacturing System Department, Ford Research Laboratory, Ford Motor Company, Dearborn, MI, USA 48121; Dept. of Mechanical, Automotive & Material.
- [84] H. Alves, U. Koster, E. Aghion, et al., Mater. Technol. 16 (2) (2001) 110-126.
- [85] Sadayappan K., Vassos M. Evaluation of a thixomolded magnesium alloy component for automotive application. SAE Technical Paper, 2010.
- [86] Hubbert T., Chen X., Li N., et al. 2005 Ford GT magnesium I/P structure. SAE Technical Paper, 2004.
- [87] S. Kim, H. Yoo, Y. Kim, Magn. Technol. (2002).
- [88] Y.Q. Ma, R. Chen, E.H Han, Mater. Sci. Forum 488 (2005) 265-268.
- [89] Gerken R.T., Ghaffari B., Sachdev A.K., et al. Low-cost magnesium alloy sheet component development and demonstration project. SAE Technical Paper, 2022.
- [90] M.O. Pekguleryuz, E. Baril, in: Development of Creep Resistant Mg-Al-Sr alloys. Essential readings in Magnesium Technology, Springer, Cham, 2016, pp. 283-289.
- [91] H. Westengen, P. Bakke, Mater. Sci. Forum. 419 (2003) 35-42.
- [92] M.A. Easton, S. Zhu, T.B. Abbott, et al., Adv. Eng. Mater. 18 (6) (2016) 953-962.
- [93] S. Gavras, S. Zhu, M.A. Easton, et al., Front. Mater. 6 (2019) 262.
- [94] Y. Xue, M.F. Horstemeyer, D.L. McDowell, et al., Int. J. Fatigue 29 (4) (2007) 666-676.
- [95] D. Argo, M. Lefebvre, Melt protection for the AJ 52 magnesium strontium alloy, in: Magnesium Technology 2003 as held at the 2003 TMS Annual Meeting, 2003, pp. 15-21.
- [96] Burns J., Han L., Hu H., et al. Effects of section thicknesses on tensile properties of permanent mould cast magnesium alloy AJ 62. Minerals, metals and materials society/AIME, 420 Commonwealth Dr., P. O. Box 430 Warrendale PA 15086 USA. [np]. 14-18 Feb, 2010.
- [97] Blanchard P.J., Bretz G.T., Subramanian S., et al. The application of magnesium die casting to vehicle closures. SAE Technical Paper, 2005.
- [98] L. Riopelle, Magnesium Applications, in: International Magnesium Association (IMA) Annual Magnesium in Automotive Seminar, April 20, 2004 Livonia, MI.
- [99] Eng L. An assessment of mass reduction opportunities for a 2017-2020 model year vehicle program. 2010.
- [100] Aston Martin global website, 2018.
- [101] Daimler Global Media, media.daimler.com, 2017.
- [102] FCA North America media, media.fcanorthamerica.com, 2017.
- [103] S. Gibbs, Metal Casting Design and Purchasing (July/August 2010) 29e33.
- [104] IMA, Magn. Showcase 12 (2010) 2.
- [105] J.P Weiler, Next generation magnesium liftgate-utilizing advanced technologies to maximum ass reduction in a high volume vehicle application. International magnesium association's 73rd annual world magnesium conference, 2016.
- [106] Blawert C., Heitmann V., Hche D., et al. Design of hybrid Mg/Al components for the automotive body-Preventing general and galvanic corrosion. ibekor com, 2011.
- [107] J.P Weiler, J. Magn. Alloys 7 (2) (2019) 297-304.
- [108] Balzer J.S., Dellock P.K., Maj M.H., et al. Structural magnesium front end support assembly. SAE Technical Paper, 2003.
- [109] A.A. Luo, R.C. McCune, Magnesium Front End Projects, V.S. Department of Energy, Automotive Lightweighting Materials, FY, 2008 2006 Progress Report, TMS 2008.
- [110] C. Blawert, N. Hort, K.U Kainer, Trans.- Indian Inst. Met. 57 (4) (2004) 397-408.
- [111] S. Logan, A. Kizyma, C. Patterson, et al., SAE Trans. (2006) 469-486.
- [112] F. Moll, M. Mekkaoui, S. Schumann, et al., Application of Mg sheets in car body structures, in: Magnesium: Proceedings of the 6th International Conference Magnesium Alloys and Their Applications, Wiley-VCH Verlag GmbH & Co. KGaA, Weinheim, FRG, 2003, pp. 936-942.
- [113] J.T. Carter, P.E. Krajewski, R. Verma, JOM 60 (11) (2008) 77-81.
- [114] Reuters, G.M. Tests magnesium sheet metal to make cars lighter, Oct. 2012.
- [115] A.A. Luo, A.K. Sachdev, B.R Powell, China Foundry 7 (4) (2010) 463-469.
- [116] A.K. Rodriguez, G. Ayoub, G. Kridli, et al., Phys. Proc. 55 (2014) 46-52.
- [117] W.H. Zhu, Z.X. Zheng, J.Z. Feng, et al., Adv. Mater. Res. 118 (2010) 930-934.
- [118] M. Gobbi, G. MASTINU, F. Ballo, et al., SAE Int. J. Passeng. Cars-Mech. Syst. 8 (1) (2015) 119-127.
- [119] M. Graf, M. Ullmann, R. Kawalla, Proc. Eng. 81 (2014) 546-551.
- [120] Wang J., Chen H. A preparation method for wheel hub production by positive and negative extrusion: CN102581053A. 2012.
- [121] P.H. Fu, L.M. Peng, W.J. Ding, Chin. J. Eng. Sci. 20 (1) (2018) 84-89.
- [122] Y.H. Peng, D.Y. Li, Y.C. Wang, et al., Mater. Sci. Forum. 488 (2005) 393-396.
- [123] R. Shang, W. Altenhof, H. Hu, et al., SAE Int. J. Mater. Manuf. 1 (1) (2009) 9-15.
- [124] G.F. Quan, S.D Liu, Ordnance Mater. Sci. Eng. 35 (04) (2012) 26-31.
- [125] W. Qiang, Z. Zhang, X. Zhang, et al., Trans. Nonferrous Met. Soc. China 20 (2010) s599-s603.
- [126] W. Qiang, Z.M. Zhang, X. Zhang, et al., Trans. Nonferrous Met. Soc. China 18 (2008) s205-s208.
- [127] Nayak S., Garg A.K., Chaturvedi M., et al. Performance evaluation of PU over-molded thermoplastic steering wheel. SAE Technical Paper, 2010.
- [128] Garg A., Surisetty G., Chaturvedi M., et al. High performance thermoplastic steering wheel. SAE Technical Paper, 2009.
- [129] W. Ames, W. Altenhof, SAE Trans. (2000) 390-399.
- [130] P.L. Mao, L.I.U. Zheng, C.Y. Wang, et al., Trans. Nonferrous Met. Soc. China 18 (2008) s218-s222.
- [131] D.Y Kwak, A study on performance evaluation and improvement of steering wheel with Mg die casting core, in: Transactions of Korean Society of Automotive Engineers Annual Autumn Conference, 2003, pp. 1185-1190.
- [132] W.J. Altenhof, W. Ames, P.R. Frise, et al., Int. J. Crashworth. 8 (3) (2003) 237-246.
- [133] J. Liao, Adv. Mat. Res. 328 (2011) 213-219.
- [134] K.J. Kim, H.J. Kim, C.Y Jeong, Mater. Res. Innov. 18 (sup2) (2014) S2-666-S2-672.
- [135] Wickberg A., Ericsson R. Magnesium in the Volvo LCP 2000. SAE Technical Paper, 1985.
- [136] Aragones J., Goundan K., Kolp S., et al. Development of the 2006 Corvette Z06 structural cast magnesium crossmember. SAE Technical Paper, 2005.
- [137] N. Li, R. Osborne, B. Cox, et al., SAE Trans. (2005) 79–88.
- [138] Chen X., Wagner D., Heath G., et al. Cast magnesium subframe development-bolt load retention. SAE Technical Paper, 2021.
- [139] H. Friedrich, S. Schumann, J. Mater. Process. Technol. 117 (3) (2001) 276-281.
- [140] F.H. Froes, D. Eliezer, E. Aghion, JOM 50 (9) (1998) 30-34.
- [141] B.R. Powell, Magnesium Powertrain Cast Components, U.S. Department of Energy, Washington, D.C, April 2009 Published in FY2008 Annual Progress Report for Automotive Lightweighting Materials.
- [142] B.R. Powell, L.J. Ouimet, J.E. Allison, et al., SAE Trans. (2004) 250-259.
- [143] J. Greiner, C. Doerr, H. Nauerz, et al., Comfort Fuel Econ. SAE Trans. (2004) 283-293.
- [144] Bavarian Motor Works (2007) Magnesium fosters rebirth of an automotive engine. International magnesium association: the global voice for magnesium (May):1-3.
- [145] Hoeschl M., Wagener W., Wolf J. BMW's magnesium-aluminium composite crankcase, state-of-the-art light metal casting and manufacturing. SAE Technical Paper, 2006.
- [146] H.W. Shin, Y.J Chung, Trans. Korean Soc. Autom. Eng. 17 (2) (2009) 141-149.
- [147] H.W. Shin, Int. J. Precis. Eng. Manuf. 13 (11) (2012) 2011–2016.
- [148] M. Pekguleryuz, P. Labelle, D. Argo, Magnesium die casting alloy AJ62x with superior creep resistance, ductility and die castability, SAE 2003 World Congress & Exhibition, 2001 2003-01-0190.
- [149] Hines J.A., McCune R.C., Allison J.E., et al. The USAMP magnesium powertrain cast components project. SAE Technical Paper, 2006.
- [150] S. Mantovani, G.A. Campo, A. Ferrari, Proc. Inst. Mech. Eng., Part C: J. Mech. Eng. Sci. 235 (10) (2021) 1703-1723.
- [151] Y. Kuwano, Y. Sakamoto, A. Uno, et al., Honda R D Tech. Rev. 20 (1) (2008) 46.
- [152] S.F. Wang, W.W. Hu, Z.H. Gao, et al., The application of magnesium alloy in automotive seat design, in: Applied Mechanics and Materials, 395, Trans Tech Publications Ltd, 2013, pp. 266-270.
- [153] J.M Willekens, Magnesium seat-frames: history and evaluation, in: Proceedings of the Third International Magnesium Conference, 1996, pp. 207-211.
- [154] Sikora S.P., Beeh E., Jäger A., et al. Concepts for manufacturing a seat backrest structure dominated by an extruded magnesium alloy. SAE Technical Paper, 2021.
- [155] Abate M., Willman M. Use of cast magnesium back frames in automotive seating. SAE Technical Paper, 2005.
- [156] Hector B., Heiss W. Magnesium die-castings as structural members in the integral seat of the new mercedes-benz roadster. SAE Technical Paper, 1990.
- [157] P. Koltun, A. Tharumarajah, Mater. Sci. Forum 618 (2009) 17-20.
- [158] B. Liu, Z.C. Qiu, Q. Yang, et al., Mater. Sci. Forum 877 (2017) 668-673.
- [159] W.J. Joost, P.E Krajewski, Scr. Mater. 128 (2017) 107-112.
- [160] I.J Polmear, Mater. Sci. Technol. 10 (1) (1994) 1-16.
- [161] E. Baril, P. Labelle, M. Pekguleryuz, JOM 55 (11) (2003) 34-39.
- [162] E. Aghion, B. Bronfin, F. Von Buch, et al., JOM 55 (11) (2003) 30-33.
- [163] S. Novotny, M. Geiger, J. Mater. Process. Technol. 138 (1-3) (2003) 594-599.
- [164] Liu B., Zhan Z., Zhao X., et al. A research on the body-in-white (BIW) weight reduction at the conceptual design phase. SAE Technical Paper, 2014.
- [165] B. Liu, J. Yang, Z. Zhan, et al., SAE Int. J. Mater. Manuf. 8 (3) (2015) 616-622.
- [166] B. Liu, C. Yan, H. Wang, Proc. Inst. Mech. Eng., Part B: J. Eng. Manuf. 234 (3) (2020) 621-628.
- [167] Y.K. Gao, D.W. Gao, Y.H Gao, Adv. Mat. Res. 156 (2011) 245-251.
- [168] S. Chandra, M. Maeder, J. Bienert, et al., Mech. Syst. Signal. Process. 187 (2023) 109945.
- [169] G. Dao, S. Youhong, L. Guanyu, et al., Mech. Syst. Signal. Process. 185 (2023) 109768.
- [170] G.G. Wang, J. Bos, J. Magn. Alloys 6 (2) (2018) 114-120.
- [171] M.H. Yoo, J.H. Song, J.H. Oh, et al., Robot Comput. Integr. Manuf. 55 (2019) 154-159.
- [172] B. Liu, P. Liu, Z.T Zhu, Adv. Mater. Res. 1063 (2015) 207-210.
- [173] G. Li, W. Jiang, Z. Fan, et al., Int. J. Adv. Manuf. Technol. 91 (1) (2017) 1355-1368.
- [174] B. Dybowski, R. Jarosz, A. Kiełbus, Solid State Phenom. 197 (2013) 125-130.
- [175] Y.K. Shen, J.J. Liu, C.T. Chang, et al., Int. Commun. Heat Mass Transf. 29 (1) (2002) 97-105.
- [176] L. Bichler, C. Ravindran, Mater. Sci. Forum. 638 (2010) 1591-1595.
- [177] F.W. Bach, M. Rodman, A. Rossberg, Adv. Mater. Res. 6 (2005) 665-672.
- [178] K. Strobel, M.A. Easton, V. Tyagi, et al., Int. J. Cast Met. Res. 23 (2) (2010) 81-91.
- [179] S. Das, A. Dubreuil, L. Bushi, et al., A Life Cycle Assessment of a Magnesium Automotive Front End, Oak Ridge National Lab. (ORNL), Oak Ridge, TN (United States), 2009.
- [180] S.V.S. Prasad, S.B. Prasad, K. Verma, et al., J. Magn. Alloys (2021).
- [181] H. Haferkamp, R. Boehm, U. Holzkamp, et al., Mater. Trans. 42 (7) (2001) 1160-1166.
- [182] P.S. Sreejith, B.K.A Ngoi, J. Mater. Process. Technol. 101 (1-3) (2000) 287-291.
- [183] S. Agarwal, J. Curtin, B. Duffy, et al., Mater. Sci. Eng.: C 68 (2016) 948-963.
- [184] K.S. Tseng, G.L. Sheu, S.T Huang, Mater. Sci. Forum. 488 (2005) 49-52.
- [185] J. Song, J. She, D. Chen, et al., J. Magn. Alloys 8 (1) (2020) 1-41.
- [186] R. Shah, V. Mittal, E. Matsil, et al., Adv. Mech. Eng. 13 (3) (2021) 16878140211003398.
9. 저작권:
- 본 자료는 Bo Liu, Jian Yang, Xiaoyu Zhang, Qin Yang, Jinsheng Zhang, Xiaoqing Li의 논문: [Development and application of magnesium alloy parts for automotive OEMs: A review]을 기반으로 작성되었습니다.
- 논문 출처: https://doi.org/10.1016/j.jma.2022.12.015
본 자료는 위 논문을 요약한 것으로, 상업적 목적으로 무단 사용하는 것을 금지합니다.
Copyright © 2025 CASTMAN. All rights reserved.