본 논문 요약은 ['자동차 응용 분야를 위한 전기 모터 하우징의 고압 다이캐스팅 시뮬레이션 및 검증'] 논문을 기반으로 작성되었으며, ['토리노 공과대학교']에서 발표되었습니다.
1. 개요:
- 제목: 자동차 응용 분야를 위한 전기 모터 하우징의 고압 다이캐스팅 시뮬레이션 및 검증 (Simulation and validation of high-pressure die casting of an electric motor housing for automotive application)
- 저자: 지안루이지 란조니 (Gianluigi Lanzoni)
- 발행 연도: A.A.2020/2021
- 발행 저널/학술 단체: 토리노 공과대학교, 자동차 공학 과정 (Politecnico di Torino, Course of automotive engineering) (석사 학위 논문)
- 키워드: 고압 다이캐스팅 (High-Pressure Die Casting, HPDC), 전기 모터 하우징 (Electric Motor Housing), 자동차 응용 (Automotive Application), 공정 시뮬레이션 (Process Simulation), 검증 (Validation)
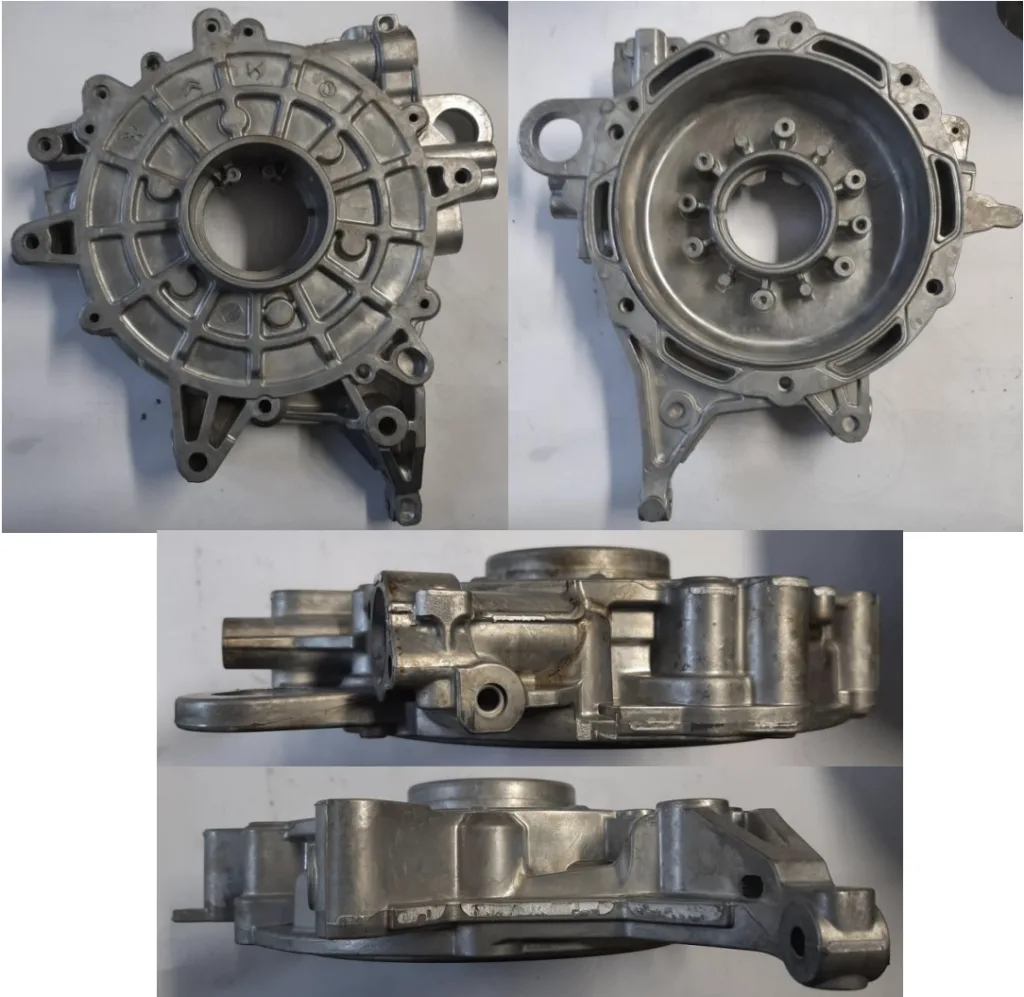
2. 연구 배경:
연구 주제 배경:
경량화 및 복잡한 자동차 부품, 특히 전기 자동차용 부품에 대한 수요가 증가함에 따라 고압 다이캐스팅 (HPDC)의 중요성이 증폭되었습니다. 본 연구는 현대 자동차 파워트레인의 핵심 부품인 전기 모터 하우징에 대한 HPDC 적용을 다룹니다. 이 연구는 HPDC 공정의 본질적인 복잡성을 강조하며, 공정 최적화 및 결함 완화를 위한 고급 시뮬레이션 기술의 필요성을 강조합니다.
기존 연구 현황:
현재 HPDC 관행은 경험에 기반을 두고 있으며, 과학 기반 접근 방식으로 진화하고 있다고 설명합니다. 주입 변수와 결과적인 주조 품질 간의 복잡한 관계를 완전히 이해하는 데 상당한 지식 격차가 존재합니다. 특히 전기 모터 하우징과 같은 새로운 부품의 생산에는 확립된 문헌과 경험적 데이터가 부족하여 체계적인 연구의 필요성을 강조합니다.
연구의 필요성:
본 연구는 HPDC를 통해 제조된 전기 모터 하우징에 대한 생산 지침을 설정하는 데 매우 중요합니다. 이러한 부품은 HPDC의 기존 제품 범위를 넘어서는 새로운 종류의 주조품을 나타냅니다. 본 연구는 공정 시뮬레이션을 활용하여 지식 격차를 해소하고 이러한 새로운 자동차 부품에 대한 강력한 제조 전략을 개발합니다. 궁극적인 목표는 시뮬레이션 결과와 실제 주조 결과를 연관시켜 산업적 구현을 위한 최적 사례를 정의하는 것입니다.
3. 연구 목적 및 연구 질문:
연구 목적:
본 논문의 주요 목적은 전기 모터 하우징 (carter) 생산에 사용되는 고압 다이캐스팅 공정을 분석하는 것입니다. 본 연구는 이 새로운 부품에 대한 HPDC 공정을 예측하고 검증하기 위해 여러 소프트웨어 플랫폼을 활용하여 공정 시뮬레이션의 효능을 평가하는 것을 목표로 합니다. 궁극적인 목표는 향후 생산 시나리오에서 유사한 전기 모터 하우징 부품의 효율적이고 고품질 제조를 위한 일련의 지침을 설정하는 것입니다.
핵심 연구:
본 연구는 다음 사항에 중점을 둡니다.
- Flow-3D Cast, Inspire Cast, PIQ2 Castle의 세 가지 개별 소프트웨어 패키지를 사용하여 HPDC 공정 시뮬레이션.
- 공정 매개변수 및 예측된 결함 형성에 초점을 맞춰 각 소프트웨어에서 얻은 시뮬레이션 결과 비교 및 대조.
- 실제 주조 부품의 실험적 몰드 샘플링 및 분석을 통한 시뮬레이션 예측 검증.
- 주조 품질에 대한 주요 공정 매개변수의 영향 조사 및 최적 매개변수 설정 식별.
- 일반적인 다이캐스팅 결함의 형성 메커니즘 분석 및 이러한 결함 예측에 대한 시뮬레이션 정확도 평가.
연구 가설:
명시적으로 공식적인 가설로 진술되지는 않았지만, 연구는 다음과 같은 암묵적인 가정 하에 진행됩니다.
- 공정 시뮬레이션은 복잡한 전기 모터 하우징에 대한 HPDC 공정을 합리적으로 정확하게 나타낼 수 있습니다.
- 시뮬레이션 연구에서 파생된 최적화된 공정 매개변수는 주조 품질의 실질적인 개선, 결함률 감소 및 생산 효율성 향상으로 이어질 것입니다.
- 시뮬레이션 예측과 실제 주조 결과 간의 상관 관계를 설정하여 전기 모터 하우징의 HPDC에서 시뮬레이션을 예측 도구로 사용하는 것을 검증할 수 있습니다.
4. 연구 방법론
연구 설계:
본 연구는 PSA 전방 전기 모터 하우징이라는 특정 자동차 부품에 대한 HPDC 공정의 시뮬레이션 및 검증을 중심으로 사례 연구 접근 방식을 채택합니다. 방법론은 포괄적인 분석을 제공하기 위해 전산 시뮬레이션과 실험적 검증을 통합합니다.
자료 수집 방법:
데이터 수집은 다면적이며 다음을 포함합니다.
- 시뮬레이션 데이터: Flow-3D Cast, Inspire Cast, PIQ2 Castle 소프트웨어를 사용하여 수행된 공정 시뮬레이션에서 생성된 수치 데이터. 여기에는 온도 분포, 공기 포획, 다이 침식, 응고 시간 및 PQ2 다이어그램에 대한 데이터가 포함됩니다.
- 실험 데이터: 실제 몰드 샘플링 및 부품 분석에서 수집된 경험적 데이터, 다음을 포함합니다.
- 열화상: 주조 사이클 동안 다이 온도 변화를 캡처하는 열화상 이미징 데이터.
- X선 분석: 주조 부품 내의 내부 기공 및 결함을 식별하는 비파괴 평가 데이터.
- 치수 측정: 설계 사양에 대한 주조 부품의 치수 정확도를 검증하는 데이터.
분석 방법:
본 연구는 비교 및 검증 중심의 분석 접근 방식을 사용합니다.
- 소프트웨어 비교: HPDC 공정 현상을 예측하는 데 있어 각 소프트웨어 플랫폼의 기능과 한계를 평가하기 위해 세 가지 소프트웨어 플랫폼 간의 시뮬레이션 결과에 대한 비교 분석.
- 메쉬 민감도 연구: 다양한 메쉬 크기 (7.5 mm, 3.7 mm, 2.5 mm, 2 mm) 에 걸쳐 결과를 분석하여 메쉬 밀도 함수로서의 시뮬레이션 정확도 평가.
- 시뮬레이션-실험 검증: 시뮬레이션 모델의 정확성과 신뢰성을 검증하기 위해 열화상 및 X선 분석의 실험 데이터와 시뮬레이션 예측의 상관 관계 분석.
- 공정 매개변수 분석: 주조 품질 및 결함 형성에 대한 충전 시간, 유량 및 게이트 두께와 같은 주요 공정 매개변수의 영향 조사.
- PQ2 다이어그램 분석: HPDC 기계와 몰드 간의 상호 작용을 분석하고 공정 작동 창을 평가하기 위한 PQ2 다이어그램 활용.
연구 대상 및 범위:
본 연구는 다음 HPDC 공정에 특화되어 있습니다.
- 부품: PSA 전방 전기 모터 하우징 (Figure 26: PSA 전방 하우징 모델, Figure 27: PSA 전방 하우징 다이 모델)
- 재료: 알루미늄 43400 합금 (Figure 28: 합금 조성)
- 공정: Fondalpress S.p.a (Figure 1: Fondalpress S.p.a 공장) 에서 사용하는 수평 냉간 챔버 HPDC 공정.
- 소프트웨어: 공정 시뮬레이션을 위한 Flow-3D Cast, Inspire Cast, PIQ2 Castle.
- 검증 방법: 실험적 검증을 위한 몰드 샘플링, 열화상, X선 분석.
5. 주요 연구 결과:
핵심 연구 결과:
본 연구는 다양한 메쉬 크기 및 소프트웨어 플랫폼에서 포괄적인 시뮬레이션 결과를 얻었습니다. 주요 결과는 다음과 같습니다.
- 메쉬 크기 영향: 7.5 mm 메쉬를 사용한 시뮬레이션은 신뢰할 수 없는 것으로 간주되었습니다. 2.5 mm 메쉬는 정확성과 계산 효율성 간의 최적 균형을 제공하는 것으로 확인되었으며, 이는 부품의 평균 두께의 약 1/3인 메쉬 크기를 제안하는 산업 지침과 일치합니다. (Figure 29: 형상 근사 평면도, Figure 30: 복잡한 형상 근사)
- 온도 분포: 온도 시뮬레이션은 주입 실린더 출구와 게이트 근처에서 더 높은 온도를 나타내는 다양한 메쉬 밀도에서 일관된 패턴을 보여주었습니다. 더 미세한 메쉬는 더 미묘한 온도 구배를 제공했습니다. (Figure 31: 다양한 메쉬 크기 파트 1의 온도 결과, Figure 32: 다양한 메쉬 크기 파트 2의 온도 결과)
- 공기 포획 예측: 시뮬레이션은 잠재적인 공기 포획 영역, 특히 주조 상단 영역에서 강조했습니다. 더 미세한 메쉬는 공기 주머니 형성에 대한 더 세련된 표현을 나타냈습니다. (Figure 33: 다양한 메쉬 크기 파트 1에서 포획된 공기, Figure 34: 다양한 메쉬 크기 파트 2에서 포획된 공기)
- 다이 침식 분석: 다이 침식 시뮬레이션은 게이트 및 러너-몰드 캐비티 인터페이스에서 더 높은 침식 가능성을 나타내었으며, 이는 높은 합금 속도 영역과 상관 관계가 있습니다. (Figure 35: 다양한 메쉬 크기에서 다이 침식)
- 응고 시간 예측: 응고 시뮬레이션은 수축 공급에 중요한 비스킷이 마지막으로 응고되는 영역임을 일관되게 식별했습니다. (Figure 36: 다양한 메쉬 크기에서 응고 시간)
- 소프트웨어 비교: Flow-3D Cast는 다이 사이클링 및 상세한 산화물 추적과 같은 고급 기능을 제공하는 가장 포괄적이고 정확한 소프트웨어로 인식되었습니다. Inspire Cast는 사용자 친화적인 것으로, PIQ2 Castle은 사용 편의성과 기계별 매개변수 통합의 균형을 제공하는 것으로 나타났습니다. (Figure 37: Inspire Cast 및 Castle 모델링 인터페이스, Figure 38: Flow-3D Cast 열 다이 사이클링, Figure 39: 열 다이 사이클링 길이 (Flow-3D Cast), Figure 40: 세 가지 소프트웨어로 충전 설정)
- 실험적 검증: 다이 온도에 대한 열화상 측정은 시뮬레이션 예측과 질적으로 일치했지만, 실험 조건으로 인해 절대 온도 값은 달랐습니다. 주조품의 X선 분석은 시뮬레이션된 기공 위험 영역과 일반적으로 일치하는 기공 분포를 나타냈습니다. (Figure 79: 열화상 고정측 다이 열림, Figure 80: 열화상 및 시뮬레이션 결과 파트 1, Figure 81: 열화상 및 시뮬레이션 결과 파트 2, Figure 82: 기공이 있는 X선, Figure 83: 기공 위험 및 X선 결과 파트 1, Figure 84: 기공 위험 및 X선 결과 파트 2, Figure 85: 기공 위험 및 X선 결과 파트 3)
- PQ2 다이어그램 분석: PQ2 다이어그램 분석은 실제 주조 공정이 최적 영역 외부에서 작동하여 주조 품질 및 효율성을 향상시키기 위해 공정 최적화 가능성을 시사했습니다. (Figure 86: Pq^2 다이어그램 예시, Figure 87: Pq^2 다이어그램 실제 조건, Figure 88: Pq^2 다이어그램 최적 기계)
데이터 해석:
시뮬레이션 결과는 잠재적인 결함 위치 및 공정 병목 현상을 효과적으로 예측했습니다. 실험적 검증은 절대 값에서 약간의 불일치를 보였지만, 특히 기공 발생 가능성이 높은 영역을 식별하는 데 있어 일반적으로 시뮬레이션 결과를 뒷받침했습니다. PQ2 다이어그램 분석은 주조 품질 및 효율성을 향상시키기 위한 공정 최적화 기회를 강조했습니다. 본 연구는 정확한 시뮬레이션 결과를 위한 메쉬 개선의 중요성과 포괄적인 HPDC 공정 분석을 위한 다양한 시뮬레이션 소프트웨어의 상호 보완적인 강점을 강조합니다.
그림 목록:
- Figure 1: Fondalpress S.p.a 공장 (Figure 1: Fondalpress S.p.a plant)
- Figure 2: 합금 표준 잉곳 (Figure 2: alloy standard ingots)
- Figure 3: 합금 용융 경로 (Figure 3: alloy melting path)
- Figure 4: 용융로 (Figure 4: melting furnace)
- Figure 5: 알루미늄의 수소 용해 (Figure 5: hydrogen solubilization in the aluminum)
- Figure 6: 버킷으로 피킹 (Figure 6: picking with the bucket)
- Figure 7: 탈기 스테이션 (Figure 7: degassing station)
- Figure 8: 홀더 퍼니스 (Figure 8: holder furnaces)
- Figure 9: 고압 다이캐스팅 기계 (Figure 9: high-pressure die casting machine)
- Figure 10: 다이 고정측 (Figure 10: die fixed side)
- Figure 11: 다이 이동측 (Figure 11: die moving side)
- Figure 12: 알루미늄과 윤활제 간의 상호 작용 (Figure 12: interaction between aluminum and lubricant)
- Figure 13: 다이 윤활 (Figure 13: Die lubrication)
- Figure 14: 윤활제 방울과 뜨거운 몰드 간의 상호 작용 (Figure 14: interaction between lubricant drop and the hot mold)
- Figure 15: 다이 습윤성에 대한 다양한 분무 효과 (Figure 15: effects of different pulverizations on die wettability)
- Figure 16: 3단계 주입 (Figure 16: three injection phases)
- Figure 17: 주조품을 트리밍 기계로 운반하는 로봇 (Figure 17: robot transporting the cast to the trimming machine)
- Figure 18: 트리밍 기계 (Figure 18: trimming machine)
- Figure 19: 포획된 공기 결함 (Figure 19: trapped air defects)
- Figure 20: 수소 개재물 결함 (Figure 20: hydrogen inclusions defects)
- Figure 21: 수축 결함 (Figure 21: shrinkage defects)
- Figure 22: 열간 균열 (Figure 22: hot cracks)
- Figure 23: 냉간 접합 (Figure 23: cold joints)
- Figure 24: 산화 (Figure 24: oxidations)
- Figure 25: 주조품의 평균 결함 빈도 (Figure 25: mean frequency of defects in the cast)
- Figure 26: PSA 전방 하우징 모델 (Figure 26: PSA front housing model)
- Figure 27: PSA 전방 하우징 다이 모델 (Figure 27: PSA front housing die model)
- Figure 28: 합금 조성 (Figure 28: alloy composition)
- Figure 29: 형상 근사 평면도 (Figure 29: geometry approximation plan view)
- Figure 30: 복잡한 형상 근사 (Figure 30: intricate geometry approximation)
- Figure 31: 다양한 메쉬 크기 파트 1의 온도 결과 (Figure 31: temperature results with various mesh dimension part 1)
- Figure 32: 다양한 메쉬 크기 파트 2의 온도 결과 (Figure 32: temperature results with various mesh dimension part 2)
- Figure 33: 다양한 메쉬 크기 파트 1에서 포획된 공기 (Figure 33: air trapped with various mesh dimensions part 1)
- Figure 34: 다양한 메쉬 크기 파트 2에서 포획된 공기 (Figure 34: air trapped with various mesh dimensions part 2)
- Figure 35: 다양한 메쉬 크기에서 다이 침식 (Figure 35: die erosion with various mesh dimensions)
- Figure 36: 다양한 메쉬 크기에서 응고 시간 (Figure 36: solidification times with various mesh dimensions)
- Figure 37: Inspire Cast 및 Castle 모델링 인터페이스 (Figure 37: Inspire Cast and Castle modeling interface)
- Figure 38: Flow-3D Cast 열 다이 사이클링 (Figure 38: Flow-3D Cast thermal die cycling)
- Figure 39: 열 다이 사이클링 길이 (Flow-3D Cast) (Figure 39: Thermal die cycling length (Flow-3D Cast))
- Figure 40: 세 가지 소프트웨어로 충전 설정 (Figure 40: Filling setup with the three software)
- Figure 41: 최적 기계 매개변수의 신속한 평가 (Figure 41: Rapid evaluation of the best machine parameters)
- Figure 42: 충전 중 온도 (Figure 42: temperature during filling)
- Figure 43: 윤활 전 다이 온도 (Figure 43: die temperature before lubrication)
- Figure 44: 윤활 후 다이 온도 (Figure 44: die temperature after lubrication)
- Figure 45: 충전 종료 시 포획된 공기 및 고체 분율 (Figure 45: air trapped at the end of filling and solid fraction)
- Figure 46: 순 결함 부피 (Figure 46: defect net volume)
- Figure 47: 충전 종료 시 온도 분포 (Figure 47: temperature distribution at the end of filling)
- Figure 48: 기본 시뮬레이션의 다양한 결과 (Figure 48: various results of base simulation)
- Figure 49: 충전 및 응고 중 몰드 온도 (Figure 49: mould temperature during filling and solidification)
- Figure 50: 포획된 공기 (Figure 50: air trapped)
- Figure 51: 충전 후 온도 분포 (Figure 51: temperature distribution after filling)
- Figure 52: 포획된 공기 시뮬레이션 (Figure 52: air trapped simulation)
- Figure 53: 충전 시간 (Figure 53: filling time)
- Figure 54: 충전 및 응고 중 몰드 온도 (Figure 54: mould temperature during filling and solidification)
- Figure 55: 냉각 시스템 레이아웃 (Figure 55: cooling system layout)
- Figure 56: 냉각 시스템 레이아웃, 측면도 (Figure 56: cooling system layout, lateral views)
- Figure 57: 충전 중 온도 분포 (Figure 57: temperature distribution during filling)
- Figure 58: 포획된 공기 (Figure 58: air trapped)
- Figure 59: 충전 및 응고 중 몰드 온도 (Figure 59: mould temperature during filling and solidification)
- Figure 60: 부품 추출 및 다이 재폐쇄 전 충전 종료 시 다이 온도 (Figure 60: die temperature at filling end, before part extraction and die reclosing)
- Figure 61: 주조 추출 시 고체 분율 및 온도 (Figure 61: solid fraction and temperature at cast extraction)
- Figure 62: 기공 위험 (Figure 62: porosities risk)
- Figure 63: 충전 온도 파트 1 (Figure 63: filling temperature part 1)
- Figure 64: 충전 온도 파트 2 (Figure 64: filling temperature part 2)
- Figure 65: 포획된 공기 (Figure 65: air trapped)
- Figure 66: 충전 온도, 충전 시간 및 총 부피 제한 (Figure 66: filling temperature, filling time and total volume restriction)
- Figure 67: 충전 온도 (Figure 67: filling temperature)
- Figure 68: 충전 중 포획된 공기 (Figure 68: trapped air during filling)
- Figure 69: 순 결함 부피 및 충전 중 2상 (Figure 69: net defect volume and dual phase during filling)
- Figure 70: 다이 침식 (Figure 70: die erosion)
- Figure 71: 속도 궤적 (Figure 71: velocity trajectories)
- Figure 72: 채널 두께 (Figure 72: channels thickness)
- Figure 73: 밀봉벽 두께 (Figure 73: sealing wall thickness)
- Figure 74: 열 엔진 변속기 파트 1 시뮬레이션 예시 (Figure 74: example of simulation of thermal engine transmission part 1)
- Figure 75: 열 엔진 변속기 파트 2 시뮬레이션 예시 (Figure 75: example of simulation of thermal engine transmission part 2)
- Figure 76: 벽 두께 (Figure 76: wall thickness)
- Figure 77: 샘플링 전 다이 (Figure 77: die before sampling)
- Figure 78: 설치 전 트리밍 기계 몰드 (Figure 78: trimming machine mould before installation)
- Figure 79: 열화상 고정측 다이 열림 (Figure 79: thermograph fixed side die open)
- Figure 80: 열화상 및 시뮬레이션 결과 파트 1 (Figure 80: thermograph and simulation results part 1)
- Figure 81: 열화상 및 시뮬레이션 결과 파트 2 (Figure 81: thermograph and simulation results part 2)
- Figure 82: 기공이 있는 X선 (Figure 82: X-ray with porosities)
- Figure 83: 기공 위험 및 X선 결과 파트 1 (Figure 83: porosity risk and X-ray results part 1)
- Figure 84: 기공 위험 및 X선 결과 파트 2 (Figure 84: porosity risk and X-ray results part 2)
- Figure 85: 기공 위험 및 X선 결과 파트 3 (Figure 85: porosity risk and X-ray results part 3)
- Figure 86: Pq^2 다이어그램 예시 (Figure 86: example of Pq^2 diagram)
- Figure 87: Pq^2 다이어그램 실제 조건 (Figure 87: Pq^2 diagram actual condition)
- Figure 88: Pq^2 다이어그램 최적 기계 (Figure 88: Pq^2 diagram on optimal machine)
- Figure 89: 다이 추출 시 실제 부품 (Figure 89: real component at die extraction)
- Figure 90: 트리밍 후 실제 부품 (Figure 90: real component after trimming)
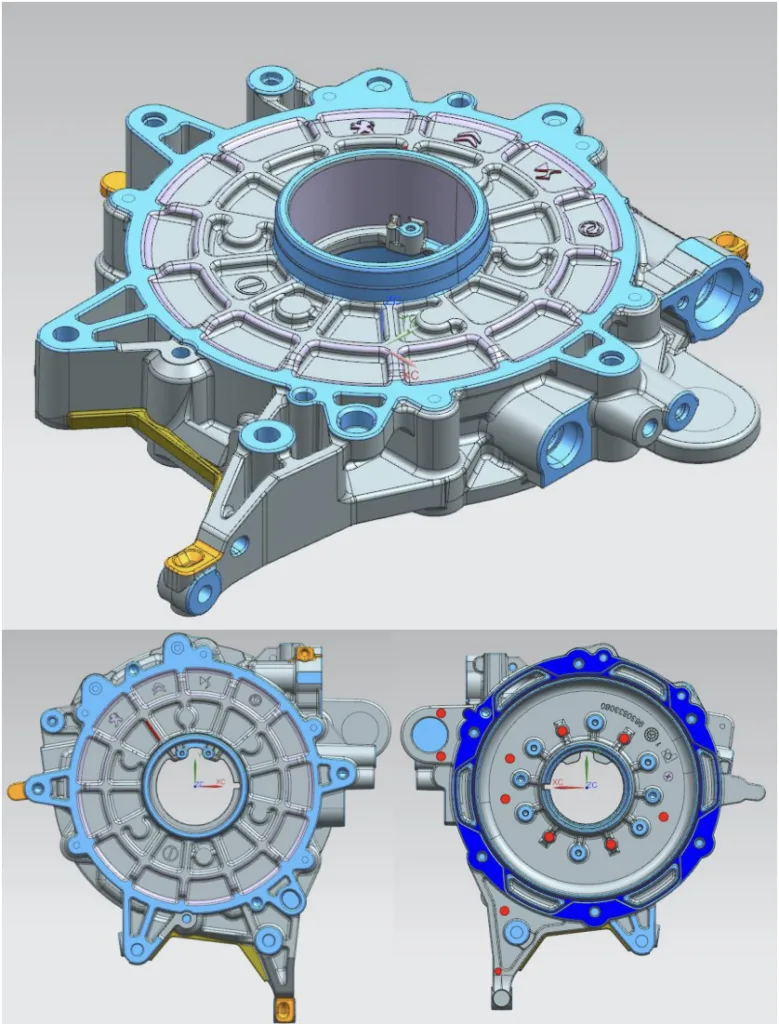
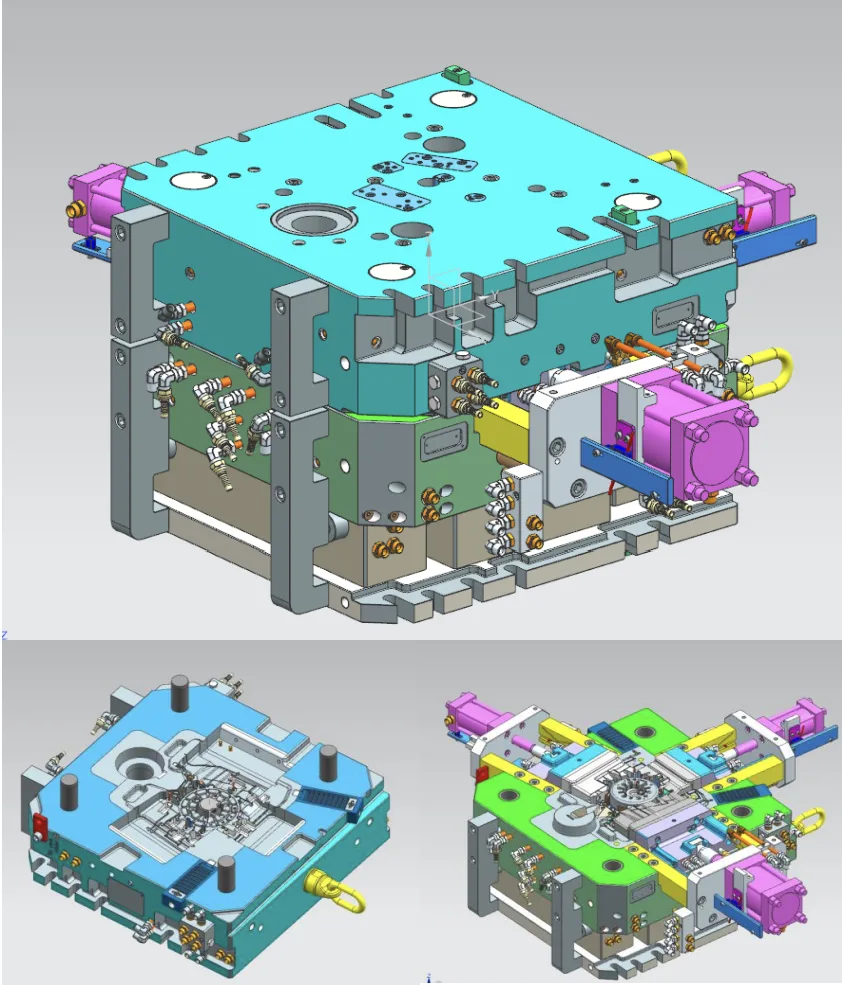
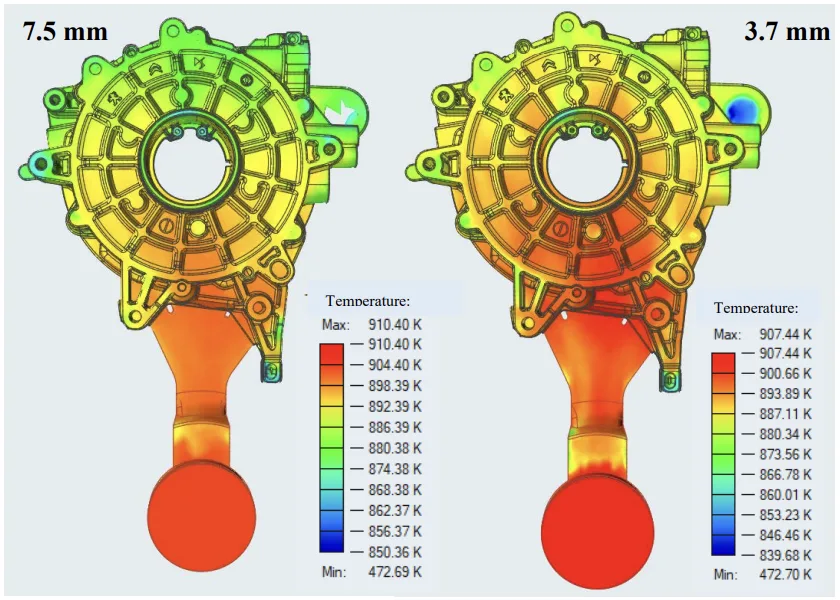
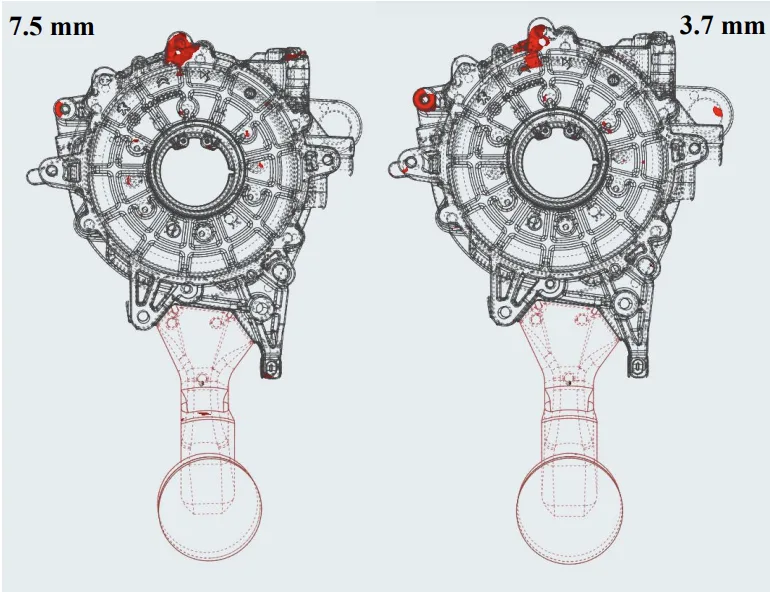
6. Conclusion:
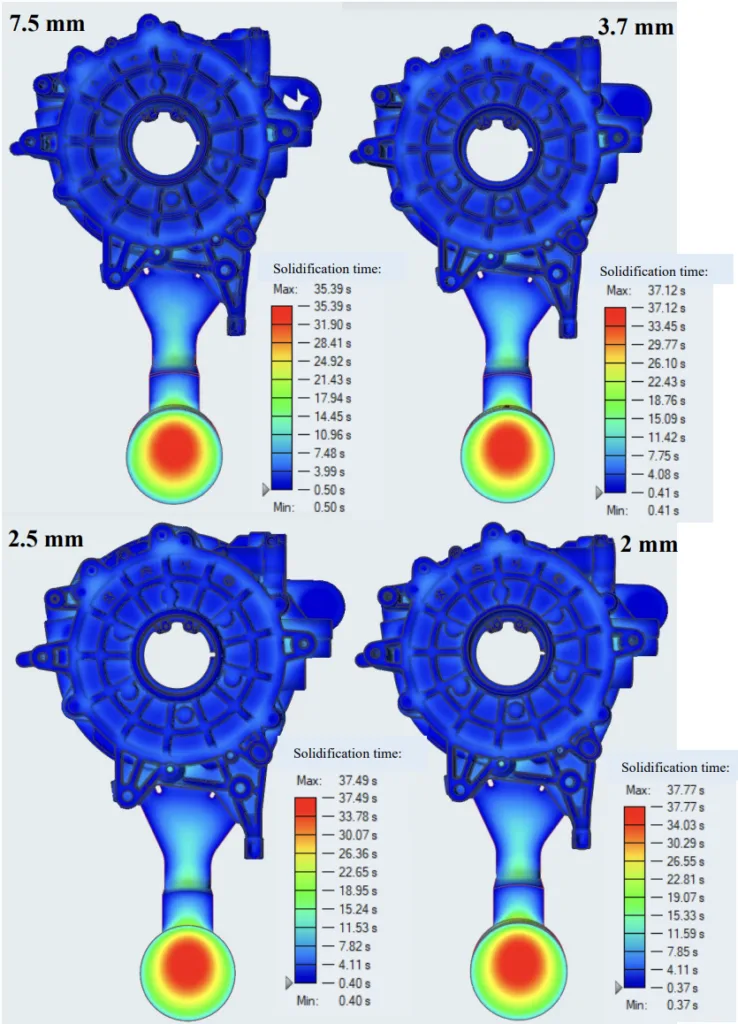
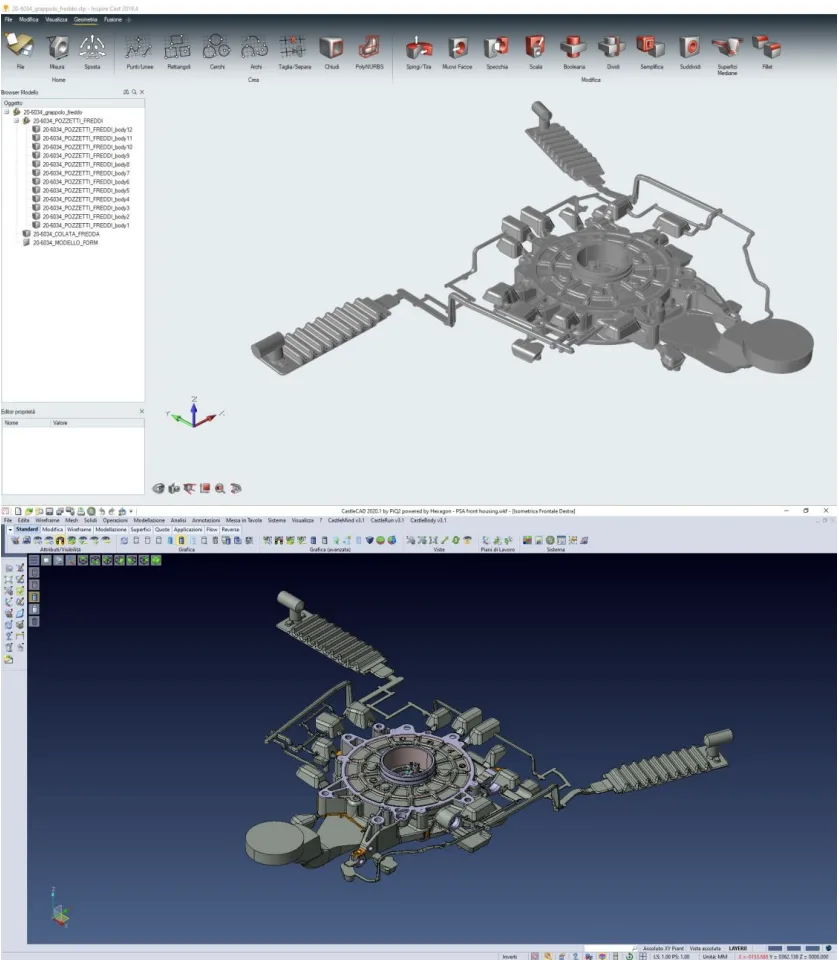
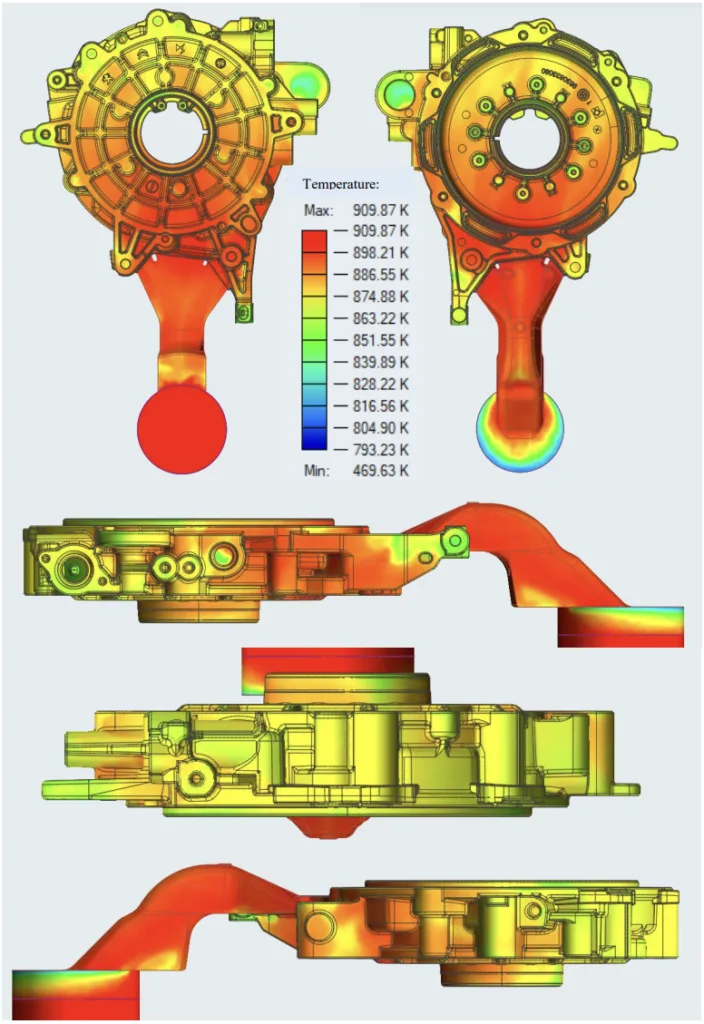
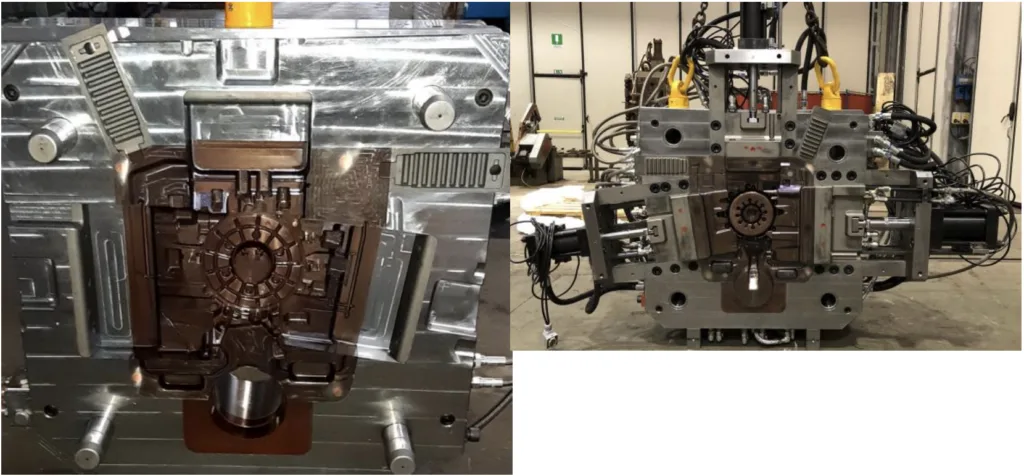
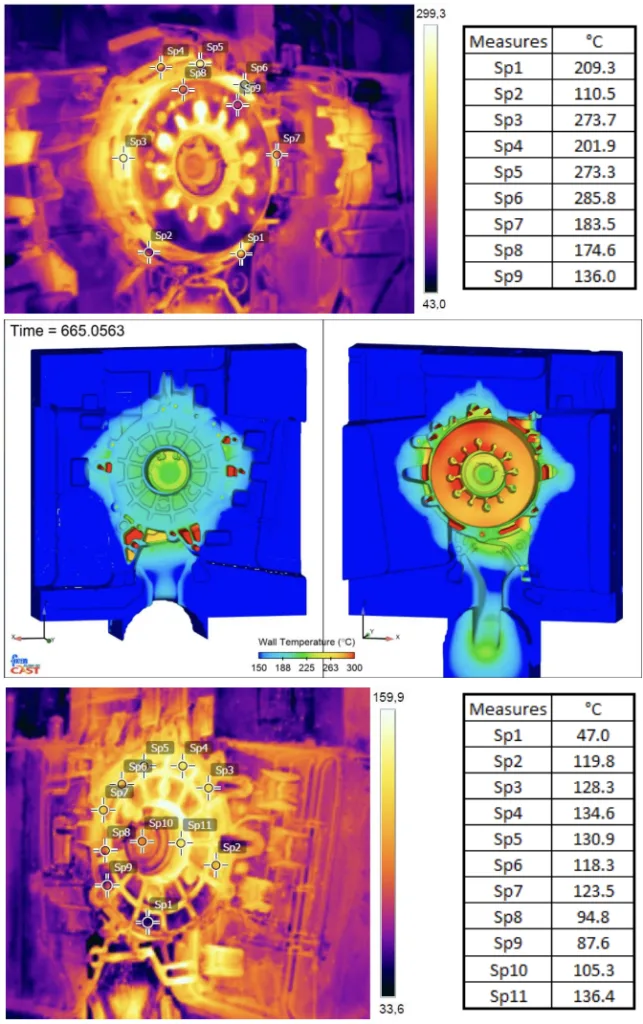
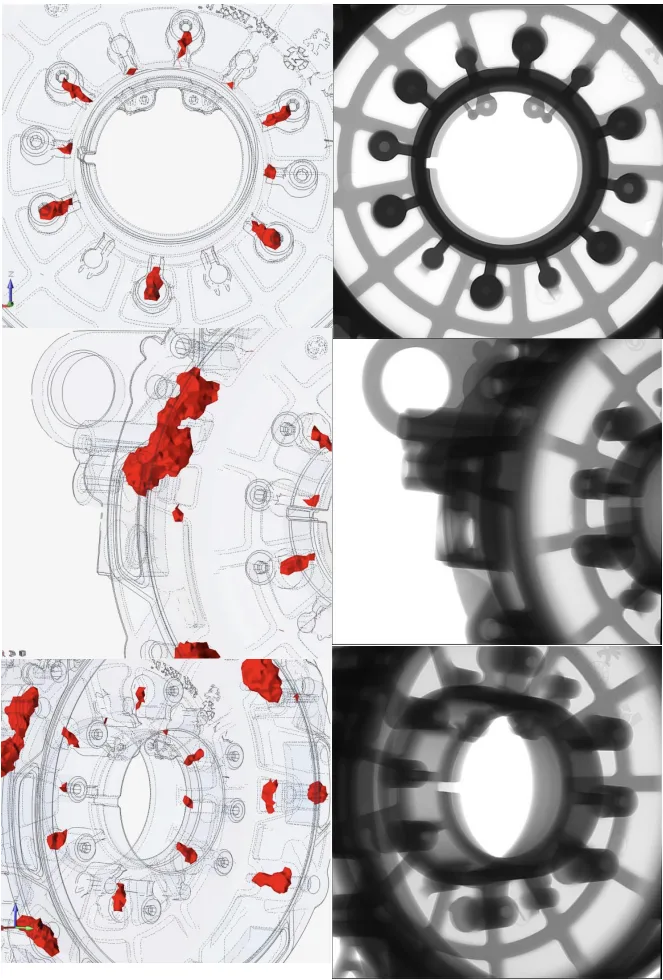
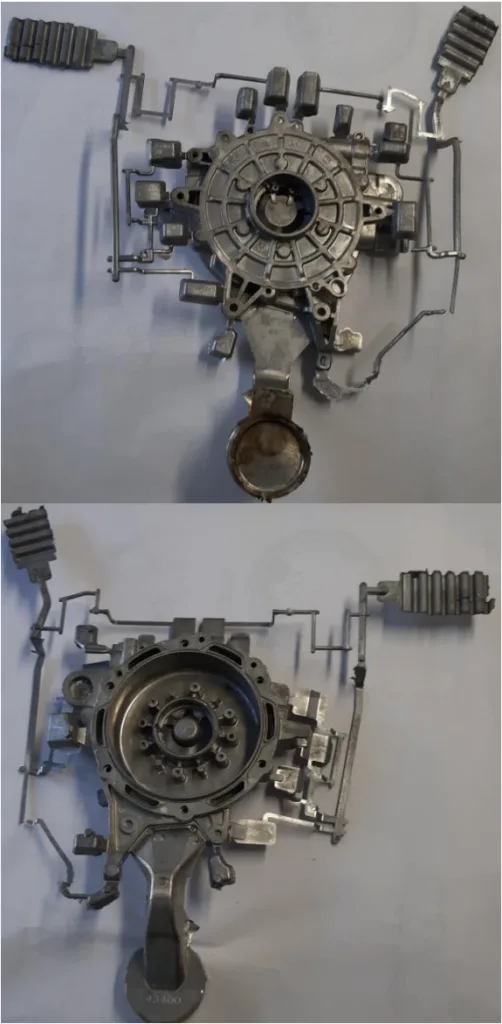
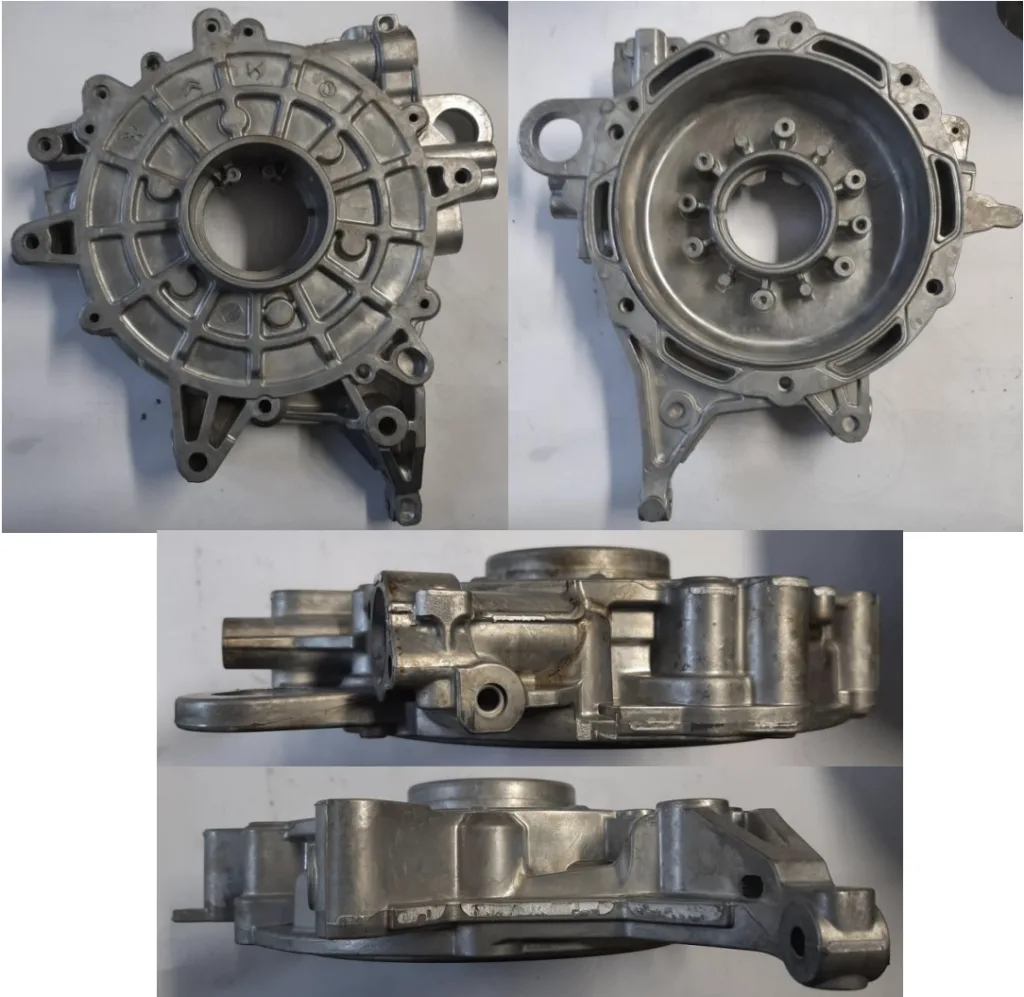
6. 결론:
주요 결과 요약:
본 연구는 여러 소프트웨어 플랫폼을 사용하여 전기 모터 하우징에 대한 HPDC 공정을 성공적으로 시뮬레이션하고 검증했습니다. 이 연구는 최적의 메쉬 설정을 식별하고, 소프트웨어 기능을 비교하고, 실험 데이터를 통해 시뮬레이션 예측을 검증했습니다. 주요 결과에는 잠재적인 결함 영역 식별, 다이 열적 거동 고려의 중요성 및 공정 최적화를 위한 PQ2 다이어그램의 유용성이 포함됩니다. 본 연구는 새로운 자동차 부품에 대한 HPDC를 최적화하는 데 있어 시뮬레이션 도구의 가치를 입증합니다.
연구의 학문적 의의:
본 논문은 HPDC, 특히 전기 모터 하우징과 같은 새로운 자동차 부품의 맥락에서 학문적 이해에 기여합니다. 전통적인 경험 기반 HPDC 관행과 현대적인 시뮬레이션 기반 접근 방식 간의 격차를 해소합니다. 비교 소프트웨어 분석은 다이캐스팅 응용 분야에 적합한 시뮬레이션 도구를 선택하는 데 있어 연구원과 실무자에게 귀중한 통찰력을 제공합니다.
실용적 의미:
본 연구 결과는 HPDC를 통한 전기 변속기 부품의 지속 가능한 생산을 위한 실용적인 지침을 제공합니다. 본 연구는 공정 매개변수를 최적화하고, 결함을 최소화하고, 생산 리드 타임과 비용을 절감하는 데 있어 시뮬레이션의 효과를 입증합니다. 시뮬레이션과 실험적 검증을 결합한 확립된 워크플로는 새롭고 복잡한 부품을 다이캐스팅하는 산업적 구현을 위한 귀중한 템플릿 역할을 합니다.
연구의 한계
본 연구는 다음과 같은 여러 가지 한계를 인정합니다.
- 시뮬레이션 정확도: 시뮬레이션은 본질적으로 실제 공정의 근사치이며 HPDC의 모든 복잡성을 포착하지 못할 수 있습니다.
- 계산 비용: 특히 미세한 메쉬와 복잡한 모델을 사용한 고충실도 시뮬레이션은 상당한 계산 자원과 시간을 요구합니다.
- 소프트웨어 제한 사항: 각 소프트웨어 플랫폼에는 PIQ2 Castle의 단순화된 열 다이 사이클링 모델 및 Inspire Cast의 제한된 메쉬 제어와 같은 고유한 제한 사항이 있습니다.
- 단순화된 몰드 모델: 시뮬레이션된 몰드는 실제 다이의 단순화된 표현으로, 열 시뮬레이션의 정확도에 영향을 미칠 수 있습니다.
- 실험적 불일치: 실험 조건 및 측정 한계로 인해 시뮬레이션된 다이 온도와 측정된 다이 온도 간에 차이가 관찰되었습니다.
7. 향후 후속 연구:
- 후속 연구 방향
향후 연구 방향은 다음과 같습니다. - 고급 오버플로 최적화: 시뮬레이션 통찰력을 기반으로 오버플로 설계를 더욱 개선하여 공기 배출을 개선하고 기공을 최소화합니다.
- 냉각 시스템 최적화: 열 관리를 개선하고 응고 시간을 단축하기 위해 다양한 냉각 채널 구성 및 냉각 전략을 조사하고 최적화합니다.
- 다이 침식 완화: 다이 침식 메커니즘에 대한 보다 자세한 분석을 수행하고 다이 마모를 최소화하고 다이 수명을 연장하기 위한 전략을 모색합니다.
- 응력 분석 통합: 냉각 중 잔류 응력 및 잠재적인 부품 변형을 예측하기 위해 응력 분석 시뮬레이션을 통합합니다.
- 소프트웨어 개선: 현재 제한 사항을 해결하기 위해 시뮬레이션 소프트웨어를 더욱 개발합니다. 예를 들어 개선된 열 다이 사이클링 모델 및 보다 사용자 친화적인 메쉬 생성 도구 등이 있습니다.
- 추가 탐구가 필요한 영역
추가 탐구가 필요한 영역은 다음과 같습니다. - 향상된 다이 열 시뮬레이션: 보다 상세한 몰드 형상 및 열 전달 모델을 통합하여 다이 열 시뮬레이션의 정확도를 향상시킵니다.
- 개선된 메쉬 생성 기술: 복잡한 다이캐스팅 형상을 처리하고 메쉬 품질을 개선하기 위해 보다 자동화되고 강력한 메쉬 생성 기술을 개발합니다.
- 강력한 시뮬레이션 워크플로: 산업 환경에서 HPDC 공정 설계 및 최적화를 위한 표준화되고 검증된 시뮬레이션 워크플로를 구축합니다.
- 다중 물리 시뮬레이션: 유체 흐름, 열 전달 및 응고를 응력 및 변형과 같은 기타 관련 현상과 결합하기 위해 다중 물리 시뮬레이션을 통합합니다.
8. 참고 문헌:
- Luigi Andreoni, “Quaderni della colata a pressione delle leghe d’alluminio”, EDIMET, 1993
- Buhler, “Ottimizzazione di processo”
- Andrea Manente, “Igiene delle leghe di alluminio”
- Altair University, “Learn Casting and Solidification with Altair Inspire Cast”
- Top 18 Die-Casting Defects and How to Fix Them, Five-Star Tooling, https://www.fstooling.com/what-cause-die-casting-defects-and-how-to-fix-them/
- EN AC-46000 (46000-F, AISi9Cu3(Fe)) Cast Aluminum, https://www.makeitfrom.com/material-properties/EN-AC-46000-46000-F-AISi9Cu3Fe-Cast-Aluminum/
- Flow 3D-cast, XC engineering, https://www.xceng.com/it/servizi/software-commerciali/flow-3d-cast/
- PIQ2, Castle, https://piq2.com/
- Fondalpress S.p.a, https://fondalpress.it/
9. 저작권:
- 본 자료는 "[지안루이지 란조니]"의 논문: "[자동차 응용 분야를 위한 전기 모터 하우징의 고압 다이캐스팅 시뮬레이션 및 검증]"을 기반으로 합니다.
- 논문 출처: [DOI URL]
본 자료는 상기 논문을 기반으로 요약되었으며, 상업적 목적으로 무단 사용하는 것을 금지합니다.
Copyright © 2025 CASTMAN. All rights reserved.