본 논문 요약은 ['MDPI']에서 발행한 ['자동차 산업에 사용되는 차체 패널 및 구조 부재용 금속 재료의 최신 동향(Current Trends in Metallic Materials for Body Panels and Structural Members Used in the Automotive Industry)'] 논문을 기반으로 작성되었습니다.
1. 개요:
- 제목: 자동차 산업에 사용되는 차체 패널 및 구조 부재용 금속 재료의 최신 동향 (Current Trends in Metallic Materials for Body Panels and Structural Members Used in the Automotive Industry)
- 저자: 토마스 트르제피에친스키, 셰르완 모하메드 나짐
- 발행 연도: 2024년
- 발행 저널/학술 단체: Materials, MDPI
- 키워드: 알루미늄 합금; 자동차 산업; 차체 패널; 강철; 티타늄 합금
![Figure 1. Classification of steels used in the automotive industry(reproduced with permission from Reference [4]; copyright © 2024 Acta Materialia Inc. Published by Elsevier B.V. All rights reserved).](https://castman.co.kr/wp-content/uploads/image-804-1024x426.webp)
![Table 1. Selected properties of cold-rolled flat products from low-carbon steel, prepared on the basis of PN-EN 10130 [62] standard.](https://castman.co.kr/wp-content/uploads/image-805-1024x263.webp)
2. 초록 또는 서론
자동차 산업에서 차체 패널 및 하중 지지 부재용 경량 및 내구성 재료 개발은 차량 성능 저하 없이 연료 소비를 줄이려는 지속적인 노력의 결과입니다. 본 연구는 주로 대량 생산 시리즈를 특징으로 하는 자동차 산업에서 이러한 합금의 사용에 대한 조사를 다룹니다.
전체 구조에서 경량 금속의 점유율을 높이는 것은 연료 소비와 대기 중 이산화탄소 배출량을 줄이기 위한 노력의 일환입니다. 환경 지속 가능성 측면을 고려할 때 금속판은 복합 재료보다 재활용이 더 쉽습니다. 동시에 지난 10년 동안 비철금속 합금으로 만든 판재의 소성 성형과 관련된 연구가 증가했습니다.
본 논문은 자동차 산업에서 금속 재료의 기본적인 응용 분야에 대한 최신 체계적인 개요를 제공합니다. 본 논문은 강철, 알루미늄 합금, 티타늄 합금 및 마그네슘 합금의 네 가지 주요 금속 재료 그룹에 중점을 둡니다. 본 연구는 개별 재료 그룹 개발의 한계와 차체 패널 및 기타 구조 부품에 사용되는 재료의 잠재적인 개발 동향에 주목합니다.
3. 연구 배경:
연구 주제 배경:
자동차 산업은 차량 성능을 저하시키지 않으면서 연료 소비와 배출 가스를 줄여야 하는 필요성에 의해 주도됩니다. 이는 차체 패널 및 하중 지지 부재에 경량 및 내구성 재료를 개발하고 적용해야 함을 의미합니다.
자동차 산업은 대량 생산을 특징으로 하므로 재료 선택은 기술적, 재료적, 경제적 기준에 따라 매우 중요합니다. 역사적으로 강철이 주요 재료였지만, 환경 문제와 연비 향상의 필요성으로 인해 알루미늄 합금, 티타늄 합금, 마그네슘 합금과 같은 경량 대체재로의 진화가 진행 중입니다.
기존 연구 현황:
기존 연구 및 개발 노력은 울트라 라이트 스틸 오토 바디(ULSAB)와 같은 프로젝트에 의해 주도되는 첨단 고강도 강철(AHSS) 등급에 크게 집중되어 있습니다. 특히 알루미늄 합금을 포함한 비철금속 합금으로 만든 판재의 소성 성형과 관련된 연구도 지난 10년 동안 증가했습니다. 강철의 화학 조성 및 미세 구조의 지속적인 최적화와 함께 필요한 강성과 무게 감소를 달성하기 위해 금속 기반 라미네이트 및 다양한 재료를 결합한 하이브리드 구조에 대한 관심이 증가하고 있습니다.
연구의 필요성:
본 연구는 자동차 산업에서 금속 재료의 응용 분야에 대한 최신 체계적인 개요를 제공하는 데 필요합니다. 특히 강철, 알루미늄 합금, 티타늄 합금, 마그네슘 합금에 중점을 둡니다. 이러한 재료 그룹의 현재 동향, 한계 및 잠재적인 개발 동향을 이해하는 것은 특히 경량화 및 지속 가능성에 대한 요구가 증가함에 따라 자동차 부문의 미래 재료 선택 및 개발 노력을 안내하는 데 매우 중요합니다.
4. 연구 목적 및 연구 질문:
연구 목적:
본 논문의 목적은 자동차 산업 내 차체 패널 및 지지 부품에 사용되는 금속 재료의 응용 분야에 대한 최신 개요를 제시하는 것입니다. 주요 금속 재료 그룹인 강철, 알루미늄 합금, 티타늄 합금, 마그네슘 합금에 초점을 맞춥니다. 또한 개별 재료 그룹 개발의 한계와 차체 패널 및 기타 구조 부품에 사용되는 재료의 잠재적인 개발 동향을 강조하는 것을 목표로 합니다.
주요 연구 내용:
본 논문에서 탐구하는 주요 연구 분야는 다음과 같습니다.
- 자동차 차체 패널 및 구조 부재에 사용되는 강철, 알루미늄 합금, 티타늄 합금 및 마그네슘 합금의 현재 응용 분야.
- 각 재료 그룹 내 다양한 등급의 분류 및 특성 (예: 강철의 경우 저강도 강철, 고강도 강철, 첨단 고강도 강철).
- 이러한 금속 재료의 성형성 및 응용 분야에 영향을 미치는 가공 방법 및 요인.
- 자동차 산업에서 각 재료 그룹의 한계 및 잠재적인 개발 동향.
연구 가설:
본 논문은 검토 논문이며 명시적인 연구 가설을 제시하지 않습니다. 자동차 산업에서 금속 재료의 응용 분야에 대한 기존 지식과 동향을 체계적으로 검토하고 요약합니다.
5. 연구 방법론
연구 설계:
본 연구는 체계적 검토 설계를 채택합니다. 자동차 산업에서 금속 재료와 관련된 기존 연구 및 출판물을 수집하고 분석하는 문헌 검토입니다.
자료 수집 방법:
자료 수집 방법은 재료 과학, 자동차 공학 및 제조와 관련된 학술 단체 및 저널의 연구 논문, 산업 보고서, 표준 및 출판물을 포함한 기존 문헌에서 정보를 수집하는 것을 포함합니다. 논문 말미에 나열된 참고 문헌은 자료 수집에 사용된 출처를 나타냅니다.
분석 방법:
분석 방법은 질적 및 기술적입니다. 저자들은 다양한 출처에서 정보를 체계적으로 검토하고 종합하여 자동차 산업에서 금속 재료의 현재 동향, 응용 분야, 한계 및 미래 방향에 대한 개요를 제공했습니다. 본 논문은 재료를 그룹 및 하위 그룹으로 분류하고, 특성을 설명하고, 검토된 문헌을 기반으로 응용 분야를 논의합니다.
연구 대상 및 범위:
연구 대상은 자동차 산업, 특히 차체 패널 및 구조 부재에 사용되는 금속 재료입니다. 범위는 강철, 알루미늄 합금, 티타늄 합금 및 마그네슘 합금의 네 가지 주요 금속 재료 그룹으로 제한됩니다. 본 검토는 자동차 맥락 내에서 이러한 재료의 응용 분야, 특성, 한계 및 개발 동향에 중점을 둡니다.
6. 주요 연구 결과:
주요 연구 결과:
- 강철: 본 논문은 저탄소강에서 첨단 고강도강(AHSS)으로의 강철 사용 진화, AHSS의 다양한 세대(1세대, 2세대, 3세대)를 자세히 설명합니다. IF강, DP강, TRIP강, TWIP강, 프레스 경화강과 같은 다양한 강철 등급의 특성, 강화 메커니즘, 차체 구조, 프레임 및 보강재에서의 응용 분야를 논의합니다. 강철의 부식 방지 방법도 논의됩니다.
- 알루미늄 합금: 본 검토에서는 저밀도 및 내식성으로 인한 알루미늄 합금의 중요성 증가를 다룹니다. 알루미늄 합금을 시리즈(1xxx~9xxx)로 분류하여 합금 원소, 특성 및 응용 분야를 자세히 설명합니다. 본 논문은 5xxx 및 6xxx 시리즈가 자동차 차체 부품에 가장 관련성이 높다고 강조하고 특정 합금과 차체 패널, 구조 부품 및 클로저에서의 응용 분야를 논의합니다.
- 티타늄 합금: 티타늄 및 티타늄 합금은 고성능 응용 분야에 적합한 높은 비강도 및 내식성을 가진 재료로 제시됩니다. 본 논문은 티타늄 합금의 다양한 등급 및 분류(알파, 알파-베타, 베타), 특성, 배기 시스템, 서스펜션 스프링, 차체 부품 및 프레임에서의 응용 분야, 특히 고급 및 틈새 차량에서의 응용 분야를 논의합니다.
- 마그네슘 합금: 마그네슘 합금은 매우 낮은 밀도와 높은 감쇠 용량으로 강조됩니다. 본 검토에서는 낮은 가소성으로 인한 마그네슘 합금 성형의 어려움을 논의하지만 구동 시스템, 차량 림, 브래킷, 프로파일 및 내부 도어 부품에서 사용이 증가하고 있음을 지적합니다. 자동차 구조에서 특정 마그네슘 합금 및 응용 분야가 나열되어 있습니다.
제시된 데이터 분석:
본 논문은 주로 기술적인 형식으로 데이터를 제시하며, 다른 출판물에서 직접 참조한 표와 그림으로 뒷받침됩니다. 표에는 다양한 자동차 부품 및 출처 자료에 대한 참조와 함께 특정 등급의 강철, 알루미늄, 티타늄 및 마그네슘 합금이 나열되어 있습니다. 그림은 재료 분류(강철, 티타늄 합금), 가공 방법(QP강 열 사이클, TWIP강 제조) 및 재료 응용 분야의 예(Audi AL2 차체 구조, Bugatti 티타늄 부품)를 보여줍니다. 다양한 강철 등급에 대한 인장 강도 및 연신율 데이터가 그래프로 표시되고(그림 1), 다양한 스테인리스강 계열의 인장 곡선이 비교됩니다(그림 6).
그림 목록:
![Figure 2. The influence of bake hardening on stress (reproduced with permission from Reference [78]; copyright © 2024 Elsevier Ltd. All rights reserved).](https://castman.co.kr/wp-content/uploads/image-806-png.webp)
![Figure 3. Typical microstructure of (a) HSLA and (b) DP steel (reproduced with permission from Reference [31]; copyright © 2024 Woodhead Publishing Limited. All rights reserved).](https://castman.co.kr/wp-content/uploads/image-807-1024x435.webp)
![Figure 4. Fabrication procedure of the cold-rolled LC/TWIP/LC and IF/TWIP/IF sheets (reproduced with permission from Reference [102]; copyright © 2024 Elsevier B.V. All rights reserved).](https://castman.co.kr/wp-content/uploads/image-808-1024x428.webp)
![Figure 5. Thermal cycle for the quenching and partitioning process (Ac3—transformation temperature, RT—room temperature), prepared with permission from Reference [132] (copyright © 2024 Acta Materialia Inc. Published by Elsevier Ltd. All rights reserved).](https://castman.co.kr/wp-content/uploads/image-809-png.webp)
![Figure 6. Comparison of tensile curves of selected corrosion-resistant steel families (reproduced with permission from Reference [139] (copyright © 2024 Elsevier Ltd. All rights reserved).](https://castman.co.kr/wp-content/uploads/image-810-png.webp)
![Figure 7. Aluminium alloy-specific Chinese automotive demand estimates. Top to bottom, the three rows show No-LT (a–c), Middle-LT (d–f), and High-LT (g–i). Three columns show Low-PN, Middle-PN, and High-PN situations from left to right. Where LT = light-weighting-trend and PN = penetration scenario (reproduced with permission from Reference [218]; copyright © 2024 The Author(s). Published by Elsevier B.V.).](https://castman.co.kr/wp-content/uploads/image-811-1024x846.webp)
![Figure 8. Audi AL2 aluminium body structure (reproduced with permission from Reference [251]; copyright © 2024 Elsevier Science S.A. All rights reserved).](https://castman.co.kr/wp-content/uploads/image-812-png.webp)
![Figure 9. Baseline part and demonstration part geometry (reproduced with permission from Reference [279]; copyright © 2024, The Minerals, Metals & Materials Society).](https://castman.co.kr/wp-content/uploads/image-803-png.webp)
![Figure 10. Forming trial results on 7xxx alloy at various forming temperatures (reproduced with permission from Reference [279]; copyright © 2024, The Minerals, Metals & Materials Society).](https://castman.co.kr/wp-content/uploads/image-813-1024x206.webp)
![Figure 11. The strength of Al–Si alloys, prepared on the basis of data from [209,287–290].](https://castman.co.kr/wp-content/uploads/image-814-1024x608.webp)
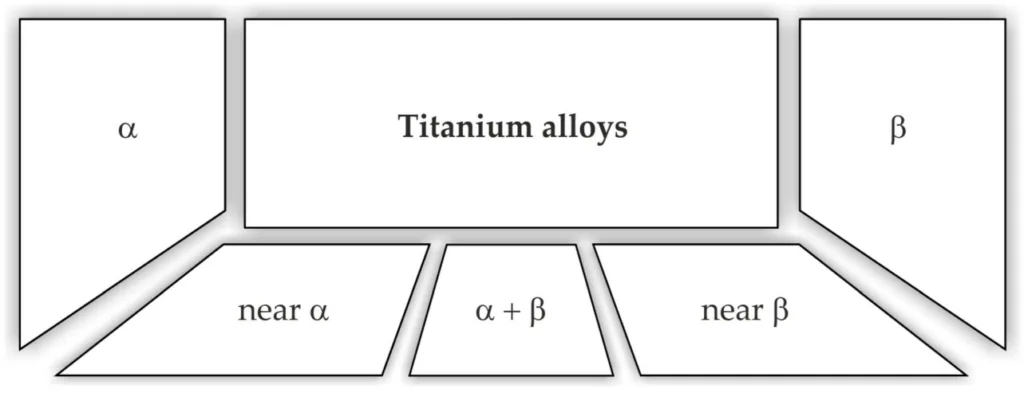
![Figure 13. The main applications of titanium and titanium alloys (reproduced with permission from Reference [314]; copyright © 2024, Springer Nature Switzerland AG).](https://castman.co.kr/wp-content/uploads/image-816-1024x670.webp)
![Figure 14. Bugatti titanium components: (a) eight-piston monobloc brake calliper, (b) active
spoiler bracket, and (c) tailpipe trim covers (reproduced with permission from Reference [319];
copyright © 2024 The Authors. Published by Elsevier B.V.).](https://castman.co.kr/wp-content/uploads/image-817-png.webp)
![Figure 15. Large titanium engine component by Precision Castparts Corporation (reproduced with
permission from Reference [320]; copyright © 2024 Published by Elsevier B.V.).](https://castman.co.kr/wp-content/uploads/image-818-png.webp)
![Figure 16. Development chronologically of titanium parts (reproduced with permission from Reference [331]; copyright © 2024 Elsevier Inc. All rights reserved).](https://castman.co.kr/wp-content/uploads/image-819-1024x633.webp)
- 그림 1. 자동차 산업에 사용되는 강철의 분류 (참고 문헌 [4]에서 허가를 받아 재현; 저작권 © 2024 Acta Materialia Inc. Elsevier B.V.에서 발행. 모든 권리 보유).
- 그림 2. 베이크 경화가 응력에 미치는 영향 (참고 문헌 [78]에서 허가를 받아 재현; 저작권 © 2024 Elsevier Ltd. 모든 권리 보유).
- 그림 3. (a) HSLA강 및 (b) DP강의 일반적인 미세 구조 (참고 문헌 [31]에서 허가를 받아 재현; 저작권 © 2024 Woodhead Publishing Limited. 모든 권리 보유).
- 그림 4. 냉간 압연 LC/TWIP/LC 및 IF/TWIP/IF 판재의 제조 절차 (참고 문헌 [102]에서 허가를 받아 재현; 저작권 © 2024 Elsevier B.V. 모든 권리 보유).
- 그림 5. 담금질 및 분할 공정의 열 사이클 (Ac3-변태 온도, RT-상온), 참고 문헌 [132]에서 허가를 받아 준비 (저작권 © 2024 Acta Materialia Inc. Elsevier Ltd. 모든 권리 보유).
- 그림 6. 선택된 내식성 강철 계열의 인장 곡선 비교 (참고 문헌 [139]에서 허가를 받아 재현; 저작권 © 2024 Elsevier Ltd. 모든 권리 보유).
- 그림 7. 알루미늄 합금별 중국 자동차 수요 추정치. 위에서 아래로 세 행은 No-LT (a−c), Middle-LT (d-f) 및 High-LT (g-i)를 보여줍니다. 세 열은 왼쪽에서 오른쪽으로 Low-PN, Middle-PN 및 High-PN 상황을 보여줍니다. 여기서 LT = 경량화 추세 및 PN = 침투 시나리오 (참고 문헌 [218]에서 허가를 받아 재현; 저작권 © 2024 The Author(s). Elsevier B.V.에서 발행).
- 그림 8. Audi AL2 알루미늄 차체 구조 (참고 문헌 [251]에서 허가를 받아 재현; 저작권 © 2024 Elsevier Science S.A. 모든 권리 보유).
- 그림 9. 기준 부품 및 시연 부품 형상 (참고 문헌 [279]에서 허가를 받아 재현; 저작권 © 2024, The Minerals, Metals & Materials Society).
- 그림 10. 다양한 성형 온도에서 7xxx 합금에 대한 성형 시험 결과 (참고 문헌 [279]에서 허가를 받아 재현; 저작권 © 2024, The Minerals, Metals & Materials Society).
- 그림 11. Al–Si 합금의 강도, [209,287-290]의 데이터를 기반으로 준비.
- 그림 12. 티타늄 합금의 분류.
- 그림 13. 티타늄 및 티타늄 합금의 주요 응용 분야 (참고 문헌 [314]에서 허가를 받아 재현; 저작권 © 2024, Springer Nature Switzerland AG).
- 그림 14. Bugatti 티타늄 부품: (a) 8피스톤 모노블록 브레이크 캘리퍼, (b) 액티브 스포일러 브래킷, (c) 테일파이프 트림 커버 (참고 문헌 [319]에서 허가를 받아 재현; 저작권 © 2024 The Authors. Elsevier B.V.에서 발행).
- 그림 15. Precision Castparts Corporation의 대형 티타늄 엔진 부품 (참고 문헌 [320]에서 허가를 받아 재현; 저작권 © 2024 Published by Elsevier B.V.).
- 그림 16. 티타늄 부품의 연대순 개발 (참고 문헌 [331]에서 허가를 받아 재현; 저작권 © 2024 Elsevier Inc. All rights reserved).
7. 결론:
주요 연구 결과 요약:
본 검토에서는 강철이 여전히 널리 사용되고 비용 효율적인 재료이며, 특히 AHSS는 특성과 재활용성의 균형으로 인해 자동차 제조에 적합하다고 결론 내립니다. 알루미늄 합금은 경량화로 인해 점점 더 중요해지고 있으며, 5xxx 및 6xxx 시리즈가 주류를 이루고 있습니다. 티타늄 합금은 뛰어난 비강도와 내식성을 제공하지만 비용 및 성형 문제로 인해 틈새 응용 분야로 제한됩니다. 마그네슘 합금은 알루미늄 합금보다 차량 무게를 줄일 수 있는 잠재력이 더 크지만 성형성 제한과 대량 생산의 어려움에 직면해 있습니다.
연구의 학문적 의의:
본 연구는 자동차 산업에 사용되는 금속 재료에 대한 포괄적이고 최신 체계적인 개요를 제공합니다. 재료 동향, 분류, 특성 및 응용 분야에 대한 현재 지식을 통합하여 연구자 및 전문가에게 귀중한 자료 역할을 합니다. 본 검토는 자동차 재료 과학의 연구 격차와 잠재적인 미래 방향을 강조합니다.
실용적 의미:
본 검토의 실용적인 의미는 자동차 엔지니어와 재료 과학자에게 중요합니다. 성능 요구 사항, 비용 고려 사항 및 지속 가능성 목표에 따라 재료 선택에 대한 지침을 제공합니다. 한계 및 개발 동향에 대한 개요는 재료 특성 개선, 비용 절감 및 대량 생산 차량에서 경량 금속의 응용 분야 확대를 목표로 하는 미래 연구 개발 노력을 알리는 데 도움이 될 수 있습니다.
연구의 한계 및 향후 연구 분야:
본 연구는 기존 문헌 검토에 국한되며 독창적인 실험 연구는 포함하지 않습니다. 확인된 향후 연구 분야는 다음과 같습니다.
- 코팅된 재료 및 원하는 이방성 특성을 가진 재료의 딥 드로잉 기술 개발.
- 향상된 강도 및 성형성을 가진 AHSS의 추가 개발, 새로운 냉간 스탬핑 기술 포함.
- 대량 생산에서 더 넓은 채택을 가능하게 하기 위해 경량화를 위한 기존 재료에 대한 비용 효율적인 대안 탐색.
- 지속 가능성 문제를 해결하기 위한 복합 재료의 대량 재활용 기술 개발.
- 더 넓은 구조적 응용 분야를 위한 마그네슘 합금의 성형성 한계 극복.
8. 참고 문헌:
- [1] Samek, L.; Krizan, D. Steel—Material of choice for automotive lightweight applications. In Proceedings of the International Conference Metal'2012, Brno, Czech Republic, 23–25 May 2012; pp. 1–6.
- [2] Ultra Light Steel Auto Body; Final Report; American Iron and Steel Institute: Washington, DC, USA, 1998; Available online: https://www.yumpu.com/en/document/view/5349987/ultralight-steel-auto-body-final-report-american-iron-steel- (accessed on 17 November 2023).
- [3] Perka, A.K.; John, M.; Kuruveri, U.B.; Menezes, P.L. Advanced high-strength steels for automotive applications: Arc and laser welding process, properties, and challenges. Metals 2022, 12, 1051. [CrossRef]
- [4] Kumar, A.; Singh, A. Mechanical properties of nanostructured bainitic steels. Materialia 2021, 15, 101034. [CrossRef]
- [5] All-New 2021 Jeep®Grand Cherokee Breaks New Ground in the Full-Size SUV Segment. Available online: https://www.media.stellantis.com/uk-en/jeep/press/all-new-2021-jeep-grand-cherokee-breaks-new-ground-in-the-full-size-suv-segment-uk (accessed on 17 November 2023).
- [6] Galán, J.; Samek, L.; Verleysen, P.; Verbeken, K.; Houbaert, Y. Advanced high strength steels for automotive industry. Rev. Metal. 2012, 48, 118-131. [CrossRef]
- [7] Kuziak, R.; Kawalla, R.; Waengler, S. Advanced high strength steels for automotive industry. Arch. Civ. Mech. Eng. 2008, 8, 103-117. [CrossRef]
- [8] Siczek, K.; Siczek, K. Lekkie rozwiązania w przemyśle samochodowym. Autobusy 2017, 14, 1311–1314.
- [9] According to the Automotive and Transportation Market Research Report. Available online: https://mobilityforesights.com/product/automotive-ahss-market/ (accessed on 15 December 2023).
- [10] Schneider, R.; Heine, B.; Grant, R.J. Mechanical Behaviour of Commercial Aluminium Wrought Alloys at Low Temperatures, Light Metal Alloys Applications; Waldemar, A.M., Ed.; InTech: Houston, TX, USA, 2014; Available online: https://www.intechopen.com/chapters/46602 (accessed on 16 November 2023).
- [11] Bielefeldt, K.; Papacz, W.; Walkowiak, J. Environmentally friendly car plastics in automotive engineering. Arch. Motoryz. 2011, 2, 5-19.
- [12] This Aluminum-Bodied 1953 Porsche 356 1500 Pre-A Cabriolet Is Shrouded in Mystery. Available online: https://www.hagerty.com/media/automotive-history/this-aluminum-bodied-1953-porsche-356-1500-pre-a-cabriolet-is-shrouded-in-mystery/ (accessed on 16 November 2023).
- [13] Choi, C.H.; Park, S.S.; Hwang, T.W. Development of composite body panels for a lightweight vehicle. SAE Trans. 2001, 110, 143-149.
- [14] Fantuzzi, N.; Bacciocchi, M.; Benedetti, D.; Agnelli, J. The use of sustainable composites for the manufacturing of electric cars. Compos. Part C Open Access 2021, 4, 100096. [CrossRef]
- [15] Cieniek, Ł. Anizotropia i Tekstura Krystalograficzna. Starzenie po Odkształceniu. Available online: https://docplayer.pl/56885357-Cwiczenie-nr-4-anizotropia-i-tekstura-krystalograficzna-starzenie-po-odksztalceniu.html (accessed on 15 November 2023).
- [16] Sherman, A.M.; Allison, J.E. Potential for Automotive Applications of Titanium Alloys; SAE Technical Paper 860608; SAE International: Warrendale, PA, USA, 1986. [CrossRef]
- [17] Titanium for Automotive Applications. Available online: https://www.azom.com/article.aspx?ArticleID=553 (accessed on 16 November 2023).
- [18] Schauerte, O. Titanium in automotive production. Adv. Eng. Mater. 2003, 5, 411-418. [CrossRef]
- [19] Blicharski, M. Inżynieria Materiałowa, Stal.; WNT: Warszawa, Poland, 2004.
- [20] Evaluation Technologies on High Strength Steel Sheet for Automobiles. Available online: https://www.kobelcokaken.co.jp/en/example/c/index.html (accessed on 16 November 2023).
- [21] Senkara, J. Współczesne stale karoseryjne dla przemysłu motoryzacyjnego i wytyczne technologiczne ich zgrzewania. Prz. Spaw. 2009, 11, 3-7.
- [22] Best Surfaces for Cat Body Panels. Available online: https://www.thyssenkrupp-steel.com/en/industries/automotivetrucks/surfaces-for-car-body-panels/best-surfaces.html (accessed on 16 December 2023).
- [23] Kubińska-Jabcoń, E.; Niekurzak, M. Wykorzystanie nowoczesnych materiałów stosowanych w motoryzacji w celu poprawy jakości i bezpieczeństwa użytkowania pojazdów mechanicznych. Autobusy 2019, 10–11, 47–52.
- [24] Close, D.; Lallement, R.; Feuser, P.; Bold, J. Challenges in Corrosion Protection for Press-Hardened Steels. In Tagungsband Zum 9. Erlanger Workshop Warmblechumformung; Meisenbach Verlag: Erlangen, Germany, 2014; pp. 31–52.
- [25] Abotani, K.; Hirohata, K.; Kiyasu, T. Hot-Dip Galvanized Sheet Steel with Excellent Press Formability and Surface Quality for the Automotive Panels. Kawasaki Steel Tech. Rep. 2003, 48, 17-22.
- [26] EN ISO 1461:2009; Hot Dip Galvanized Coatings On Fabricated Iron And Steel Articles. Specifications and Test Methods. Comite Europeen de Normalisation: Brussels, Belgium, 1994.
- [27] Close, D. Alternative Protective Coatings for Hot Stamped Automotive Body Parts. Ph.D. Thesis, Universite de Lorraine, Lorraine, France, 22 March 2018.
- [28] Ulbrich, D.; Kowalczyk, J.; Stachowiak, A.; Sawczuk, W.; Selech, J. The Influence of Surface Preparation of the Steel during the Renovation of the Car Body on Its Corrosion Resistance. Coatings 2021, 11, 384. [CrossRef]
- [29] Santos, D.; Raminhos, H.; Costa, M.R.; Diamantino, T.; Goodwin, F. Performance of finish coated galvanized steel sheets for automotive bodies. Prog. Org. Coat. 2008, 62, 265-273. [CrossRef]
- [30] Wyrobek, K. Modelowanie procesu tłoczenia części nadwozia samochodu ze stali superwysoko wytrzymałej. Inż. Masz. 2017, 22, 76-84.
- [31] Horvath, C.D. Advanced steels for lightweight automotive structures. In Materials, Design and Manufacturing for Lightweight Vehicles; Mallick, P.K., Ed.; Woodhead Publishing: Sawston, UK, 2010; pp. 35–78.
- [32] Grosman, F.; Piela, A. Zastosowanie nowej metody badań do wstępnej oceny właściwości użytkowych blach dla motoryzacji. Inż. Mater. 1991, 12, 84-87.
- [33] Trzepieciński, T.; Najm, S.M. Application of artificial neural networks to the analysis of friction behaviour in a drawbead profile in sheet metal forming. Materials 2022, 15, 9022. [CrossRef] [PubMed]
- [34] Trzepieciński, T.; Szwajka, K.; Szewczyk, M. Pressure-assisted lubrication of DC01 steel sheets to reduce friction in sheet-metal-forming processes. Lubricants 2023, 11, 169. [CrossRef]
- [35] Kajal, G.; Tyagi, M.R.; Kumar, G. A review on the effect of residual stresses in incremental sheet metal forming used in automotive and medical sectors. Mater. Today Proc. 2023, 78, 524-534. [CrossRef]
- [36] Ma, L.; Wang, Z. The effects of through-thickness shear stress on the formability of sheet metal—A review. J. Manuf. Proc. 2021, 71, 269-289. [CrossRef]
- [37] Trzepieciński, T.; Lemu, H.G. Improving prediction of springback in sheet metal forming using multilayer perceptron-based genetic algorithm. Materials 2020, 13, 3129. [CrossRef] [PubMed]
- [38] Szewczyk, M.; Szwajka, K. Assessment of the tribological performance of bio-based lubricants using analysis of variance. Adv. Mech. Mater. Eng. 2023, 40, 31-38. [CrossRef]
- [39] Trzepieciński, T.; Najm, S.M.; Sbayti, M.; Belhadjsalah, H.; Szpunar, M.; Lemu, H.G. New advances and future possibilities in forming technology of hybrid metal-polymer composites used in aerospace applications. J. Compos. Sci. 2021, 5, 217. [CrossRef]
- [40] Trzepieciński, T.; Najm, S.M.; Oleksik, V.; Vasilca, D.; Paniti, I.; Szpunar, M. Recent developments and future challenges in incremental sheet forming of aluminium and aluminium alloy sheets. Metals 2022, 12, 124. [CrossRef]
- [41] Żaba, K.; Puchlerska, S.; Kuczek, Ł.; Trzepieciński, T.; Maj, P. Effect of step size on the formability of Al/Cu bimetallic sheets in single point incremental sheet forming. Materials 2023, 16, 367. [CrossRef] [PubMed]
- [42] Rajarajan, C.; Sivaraj, P.; Sonar, T.; Raja, S.; Mathiazhagan, N. Resistance spot welding of advanced high strength steel for fabrication of thin-walled automotive structural frames. Forces Mech. 2022, 7, 100084. [CrossRef]
- [43] Ahmed, M.M.Z.; El-Sayed Selaman, M.M.; Fydrych, D.; Cam, G. Review on friction stir welding of dissimilar magnesium and aluminum alloys: Scientometric analysis and strategies for achieving high-quality joints. J. Magnes. Alloys 2023, 11, 4082-4127. [CrossRef]
- [44] Tomków, J.; Fydrych, D.; Rogalski, G. Dissimilar underwater wet welding of HSLA steels. Int. J. Adv. Manuf. Technol. 2020, 109, 717-725. [CrossRef]
- [45] André, V.; Costas, M.; Langseth, M.; Morin, D. Behavior and Large-Scale Modeling of Multi-Sheet Aluminum Connections With Self-Piercing Rivets. J. Manuf. Sci. Eng. 2023, 145, 101010. [CrossRef]
- [46] Çavuşoğlu, O.; Bakırcı, A.; Dinkçi, H.; Yılmazoğlu, A.G. Triple joining of different sheets with self-pierce riveting method. Sci. Technol. Weld. Join. 2022, 27, 579-585. [CrossRef]
- [47] Zhou, Z.-J.; Huang, Z.-C.; Jiang, Y.-Q.; Tang, N.-L. Joining Properties of SPFC440/AA5052 Multi-Material Self-Piercing Riveting Joints. Materials 2022, 15, 2962. [CrossRef]
- [48] Cmorej, D.; Kaščák, L'. Numerical simulation of mechanical joining of three DP600 and DC06 steel sheets. Adv. Mech. Mater. Eng. 2023, 40, 23-29. [CrossRef]
- [49] Huang, Z.C.; Huang, G.H.; Shan, F.W.; Jiang, Y.Q.; Zou, Y.Q.; Nie, X.Y. Forming quality and microstructure evolution of AA6061-T6 aluminum alloy joint during flow drill screwing process. Adv. Eng. Mater. 2023, 25, 2300054. [CrossRef]
- [50] Kinsley, B.L. 7—Tailor welded blanks for the automotive industry. In Tailor Welded Blanks for Advanced Manufacturing; Kinsley, B.L., Wu, X., Eds.; Woodhead Publishing: Sawston, UK, 2011; pp. 164-180.
- [51] Keeler, S.; Kimchi, M. Advanced High-Strength Steels. Application Guidelines Version 5.0, World Auto Steel. 2014. Available online: https://www.worldautosteel.org/projects/advanced-high-strength-steel-application-guidelines/ (accessed on 16 November 2023).
- [52] ULSAB-AVC. Available online: https://www.worldautosteel.org/projects/ulsab-avc-2/ (accessed on 16 November 2022).
- [53] ULSAC. Available online: https://www.worldautosteel.org/projects/ulsac-2/ (accessed on 16 November 2022).
- [54] ULSAS-UltraLight Steel Auto Suspensions Report. Available online: https://www.worldautosteel.org/ulsas-ultralight-steel-auto-suspensions-report/ (accessed on 16 November 2022).
- [55] FutureSteel Vehicle. Available online: https://www.worldautosteel.org/projects/future-steel-vehicle/ (accessed on 16 November 2022).
- [56] Richter, J.; Kuhtz, M.; Hornig, A.; Harhash, M.; Palkowski, H.; Gude, M. A mixed numerical-experimental method to characterize metal-polymer interfaces for crash applications. Metals 2021, 11, 818. [CrossRef]
- [57] Structure-Borne-Damping Composite Material with Customized Properties. Available online: https://www.thyssenkrupp-steel.com/en/products/composite-material/overview-composite-material.html (accessed on 16 November 2023).
- [58] Kustroń, P.; Korzeniowski, M.; Piwowarczyk, T.; Sokołowski, P. Development of resistance spot welding processes of metal-plastic composites. Materials 2021, 14, 3233. [CrossRef] [PubMed]
- [59] HybrixTM = ∑[214Lightweight, Formable, Strong, Eco-Friendly]. Available online: https://www.lamera.se/ (accessed on 16 November 2023).
- [60] Hammarberg, S.; Kajberg, J.; Larsson, S.; Moshfegh, R.; Jonsén, P. Novel methodology for experimental characterization of micro-sandwich materials. Materials 2021, 14, 4396. [CrossRef] [PubMed]
- [61] Sokolova, O.A.; Kühn, M.; Palkowski, H. Deep drawing properties of lightweight steel/polymer/steel sandwich composites. Arch. Civ. Mech. Eng. 2012, 12, 105-112. [CrossRef]
- [62] EN 10130; Cold Rolled Low Carbon Steel Flat Products for Cold Forming—Technical Delivery Conditions. European Committee for Standardization: Brussels, Belgium, 2009.
- [63] Trzepieciński, T.; Szwajka, K.; Szewczyk, M. An investigation into the friction of cold-rolled low-carbon DC06 steel sheets in sheet metal forming using radial basis function neural networks. Appl. Sci. 2023, 13, 9572. [CrossRef]
- [64] Sudo, M.; Hashimoto, S.I.; Kambe, S. Niobium bearing ferrite-bainite high strength hot-rolled sheet steel with improved formability. Trans. Iron Steel Inst. Jpn. 1983, 23, 303-311. [CrossRef]
- [65] Complex Phase Steels. Available online: https://automotive.arcelormittal.com/products/flat/first_gen_AHSS/CP (accessed on 16 November 2023).
9. 저작권:
- 본 자료는 "토마스 트르제피에친스키 및 셰르완 모하메드 나짐"의 논문: "자동차 산업에 사용되는 차체 패널 및 구조 부재용 금속 재료의 최신 동향"을 기반으로 합니다.
- 논문 출처: https://doi.org/10.3390/ma17030590
본 자료는 위 논문을 기반으로 요약되었으며, 상업적 목적으로 무단 사용하는 것을 금지합니다.
Copyright © 2025 CASTMAN. All rights reserved.