본 소개 자료는 "[7th. Int. Conf. on Thermal, Mechanical and Multiphysics Simulation and Experiments in Micro-Electronics and Micro-Systems, EuroSimE 2006]"에 게재된 "[Thermal Management of Bright LEDs for Automotive Applications]" 논문을 기반으로 작성되었습니다.
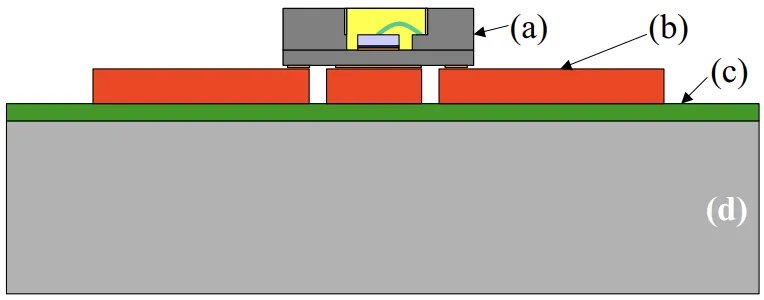
1. 개요:
- 제목: Thermal Management of Bright LEDs for Automotive Applications (자동차용 고휘도 LED의 열 관리)
- 저자: Yan Lai, Nicolás Cordero
- 발표 연도: 2006년
- 학술지/학회: 7th. Int. Conf. on Thermal, Mechanical and Multiphysics Simulation and Experiments in Micro-Electronics and Micro-Systems, EuroSimE 2006
- 키워드: 논문에 명시되지 않음.
2. 초록:
고휘도 백색 발광 다이오드(LED)는 실외 조명, 작업 및 장식 조명뿐만 아니라 항공기 및 자동차 조명(자동차 헤드라이트 포함)과 같은 많은 조명 응용 분야에서 매우 유망한 것으로 나타났습니다. 본 논문의 목적은 자동차 응용 분야에서 이러한 LED의 냉각 솔루션을 조사하는 것입니다. 본 연구에서는 소자에서 보드, 시스템 수준까지의 열 설계를 수행했으며, 최적의 열 성능을 찾기 위한 최적화 작업이 이루어졌습니다. 자연 대류와 강제 대류가 모두 탐구되었으며, 이 특정 응용 분야의 각 경우에 대한 결론이 도출되었습니다.
3. 서론:
GaN 기반 재료 기술의 발전과 함께 고휘도 백색 LED 기술은 지난 몇 년 동안 번성해 왔습니다. 작은 패키지 크기, 스타일링 유연성 및 백열 광원에 비해 우수한 성능으로 인해 LED는 오늘날 브레이크 등, 방향 지시등 및 미등과 같은 많은 자동차 외장에 널리 사용되며 일부 컨셉 차량에서는 전방 조명으로 등장했습니다. 그러나 현재 헤드라이트 응용 분야에 맞춤화된 LED는 없습니다.
현재 LED는 생산 차량에 사용하기에는 루멘 출력이 부족한 고비용 솔루션을 제공합니다. 법적 요구 사항에 따르면 헤드램프에는 램프당 750lm이 필요합니다. 그러나 현재 평균 고휘도 LED 출력이 40lm/W에 불과하므로 표준을 충족하려면 더 많은 LED와 더 높은 구동 전력이 필요합니다.
광 출력 요구량이 증가함에 따라 LED의 구동 전력은 지속적으로 증가합니다. LED 패키징의 열 관리는 이러한 장치의 효율성, 성능 및 신뢰성에 큰 영향을 미치므로 점점 더 중요해지고 있습니다.
다이오드 접합 온도가 증가하면 LED 효율이 감소하고 방출 파장이 변동합니다. 따라서 높은 효율과 상대적으로 고정된 파장을 달성하기 위해서는 LED를 최대 작동 온도(예: < 125°C)보다 훨씬 낮게 유지하는 열 솔루션이 필요합니다. 이를 달성하기 위해 열 솔루션은 포괄적이어야 하며 소자, 패키지, 보드 및 시스템 수준의 모든 수준에서 열 문제를 해결해야 합니다. 이 응용 분야에서는 상업적으로 이용 가능한 베어 다이(bare die) 고휘도 LED가 사용됩니다. 적절한 열 관리 솔루션을 찾기 위해 모든 수준에서 전산 유체 역학(CFD)을 사용한 열 시뮬레이션이 수행되었습니다.
4. 연구 요약:
연구 주제의 배경:
LED의 광 출력을 높이려는 요구는 더 높은 구동 전력을 필요로 하며, 이는 LED의 효율성, 성능 및 신뢰성을 위해 효과적인 열 관리를 필수적으로 만듭니다. LED 접합 온도의 증가는 효율 감소 및 방출 파장 변화를 초래합니다. 자동차 응용 분야, 특히 헤드라이트의 경우 최적의 안정적인 성능을 보장하기 위해 LED 접합 온도를 최대 작동 한계(예: < 125°C)보다 훨씬 낮게 유지하는 것이 중요합니다.
이전 연구 현황:
본 논문은 LED가 자동차 외부 조명에 일반적으로 사용되지만 헤드라이트 응용 분야에 맞춤화된 LED는 아직 표준이 아니라고 지적합니다. 현재 LED는 비용이 많이 들고 생산 차량에 충분한 루멘 출력을 제공하지 못하며, 헤드램프에는 램프당 750lm이 필요합니다. 현재 고휘도 LED가 약 40lm/W를 출력한다는 점을 감안할 때, 필요한 조명을 달성하려면 더 많은 수의 LED를 더 높은 전력 수준에서 작동시켜야 하므로 고급 열 관리 전략의 중요한 필요성이 강조됩니다.
연구 목적:
본 논문의 주요 목적은 자동차 응용 분야, 특히 헤드라이트에 사용되는 고휘도 LED를 위한 최적의 냉각 솔루션을 조사하고 식별하는 것입니다. 이 연구에는 소자 수준에서 보드 및 시스템 수준에 이르는 포괄적인 열 설계 프로세스와 최상의 열 성능을 달성하기 위한 최적화 작업이 포함됩니다. 이 연구는 자연 대류 및 강제 대류 냉각 방법을 모두 탐구합니다.
핵심 연구:
연구의 핵심은 15개의 Cree XBright900 LED로 구성된 시스템의 열 설계 및 최적화였습니다. 각각 최대 2.5W의 열을 발생시킬 수 있는 이 LED는 5개의 보드에 각 보드당 3개의 LED로 구성되었습니다. 연구의 주요 측면은 다음과 같습니다.
- LED 패키징: LED에서 패키지 바닥까지 낮은 열 저항 경로(2°C/W 미만으로 계산됨)를 보장하기 위해 AlN(k=200W/mK)을 사용한 LED 개별 패키징.
- 절연 금속 기판(IMS) 최적화: AlN 패키지는 IMS에 장착되었습니다. IMS 구조는 다양한 재료와 층 두께를 평가하여 최적화되었습니다. 최종 설계는 70µm 구리 회로층, 75µm 유전체층(k=2.2W/mK의 세라믹/폴리머로 제작) 및 1mm 알루미늄 코어 보드로 구성되었습니다(Table 1에 자세히 설명됨).
- 히트 싱크 최적화: 알루미늄 히트 싱크는 자연 대류 냉각을 위해 설계 및 최적화되었습니다. 여기에는 CFD 소프트웨어(FloTherm)를 사용한 반복적인 프로세스가 포함되어 표면적, 핀 수, 핀 두께, 핀 높이 및 베이스 두께와 같은 최적의 매개변수를 결정하고 제조 및 응용 제약 조건을 고려했습니다.
- 냉각 방법 평가:
- 자연 대류: 최적화된 IMS 및 히트 싱크를 사용하여 개방된 공기 중과 밀폐된 헤드라이트 인클로저 내에서 성능을 시뮬레이션했습니다.
- 강제 대류(공기): 이는 간략하게 탐구되었지만 공간, 신뢰성, 비용 및 고유량 팬의 필요성과 관련된 제약으로 인해 실현 불가능한 것으로 기각되었습니다.
- 액체 냉각: 수동 및 능동 액체 냉각 솔루션이 대안으로 조사되었습니다. 수동 액체 냉각은 응용 분야의 기하학적 제약으로 인해 부적합한 것으로 밝혀졌습니다. 원격 열교환기에 연결된 수냉식 콜드 플레이트를 사용하는 능동 액체 냉각을 시뮬레이션하고 분석했습니다.
5. 연구 방법론
연구 설계:
본 연구는 LED 다이(소자 수준)에서 패키지, 절연 금속 기판(IMS 보드), 그리고 히트 싱크와 작동 환경(예: 헤드라이트 인클로저)을 포함하는 시스템 수준까지 열 관리 문제를 해결하는 다단계 열 설계 전략을 채택했습니다. 반복적인 최적화 방법론은 특히 히트 싱크에 대한 설계 프로세스의 핵심이었으며, 상충되는 설계 매개변수(예: 열 성능 대 무게, 크기 및 제조 가능성)의 균형을 맞추는 것을 목표로 했습니다. 이 연구는 Cree XBright900 LED를 사용하는 시스템에 중점을 두었으며, 5개의 보드에 15개의 LED가 분산된 구성(보드당 3개의 LED)을 사용했습니다.
데이터 수집 및 분석 방법:
열 성능은 상용 전산 유체 역학(CFD) 소프트웨어인 FloTherm [3]을 사용하여 분석 및 최적화되었습니다. 방법론에는 다음이 포함되었습니다.
- LED 패키지의 열 저항 계산.
- 열 저항을 최소화하기 위해 다양한 재료와 층 두께를 비교하여 IMS 최적화를 위한 매개변수 연구 수행.
- 자연 대류 하에서 LED 접합 온도를 최소화하는 것을 목표로 핀 수, 핀 두께, 핀 높이 및 베이스 플레이트 치수를 포함한 히트 싱크 설계 매개변수를 최적화하기 위한 반복 시뮬레이션 수행.
- 다양한 냉각 전략(개방 공기 및 인클로저 내 자연 대류, 능동 액체 냉각)의 열 성능 시뮬레이션 및 비교.
연구 주제 및 범위:
본 연구는 자동차 헤드라이트 응용 분야를 위한 고휘도 백색 LED, 특히 Cree XBright900 모델의 열 관리에 집중했습니다. 연구 범위는 다음과 같습니다.
- 효율적인 방열을 위한 질화 알루미늄(AlN)을 사용한 개별 LED 패키지 설계.
- LED 패키지 장착을 위한 절연 금속 기판(IMS) 보드 설계 및 최적화.
- 자연 대류 냉각에 적합한 알루미늄 히트 싱크 설계 및 최적화.
- 다양한 환경(개방 공기 대 헤드라이트 인클로저 내부 배치)에서의 시스템 열 성능 평가.
- 강제 공기 대류에 대한 간략한 고려와 수동 액체 냉각 및 능동 액체 냉각 시스템에 대한 보다 상세한 분석을 포함한 대체 냉각 솔루션 조사.
- 테스트 대상 시스템은 15개의 LED로 구성되었으며, 각 LED는 최대 2.5W의 열을 발생시킬 수 있었고, 주요 열 관리 목표는 LED 접합 온도를 125°C 미만으로 유지하는 것이었습니다.
6. 주요 결과:
주요 결과:
- IMS 최적화: 70µm 구리 회로층, 열전도율(k) 2.2W/mK의 75µm 세라믹/폴리머 유전체층, 1mm 두께의 알루미늄 기판으로 구성된 최적화된 절연 금속 기판(IMS) 보드 구조가 결정되었습니다. Table 1에 자세히 설명된 이 구성은 열 확산을 향상시키고 전체 열 저항을 줄이도록 설계되었습니다.
- 자연 대류를 위한 히트 싱크 최적화:
- CFD 시뮬레이션을 사용한 반복적인 최적화 프로세스를 통해 알루미늄 히트 싱크에 대한 최적의 핀 수(Figure 3), 핀 두께(Figure 4), 핀 높이(Figure 5) 및 베이스 플레이트 면적(Figure 6)을 정의했습니다.
- 개방된 공기 중에서 자연 대류 하에 최적화된 히트 싱크에 장착된 3개의 LED(각각 3W 방열)가 있는 IMS 보드의 시뮬레이션은 60~100°C 범위의 온도 프로파일을 보여주었습니다(Figure 7).
- 인클로저 내 자연 대류의 한계: 최적화된 히트 싱크가 있는 LED 어셈블리를 헤드라이트 인클로저 내부에 배치했을 때, 자연 대류는 LED 접합 온도를 원하는 125°C 미만으로 유지하기에 충분하지 않았습니다. 시뮬레이션 결과, 제한된 공간 내 공기 재순환으로 인해 접합 온도가 이 한계를 초과하여 200°C까지 높아질 수 있음을 나타냈습니다(Figure 8).
- 강제 공기 대류 평가: 강제 공기 대류가 고려되었지만 헤드라이트 내 공간 제한, 팬의 신뢰성 문제, 비용 및 조립 복잡성과 관련된 실제적인 제약으로 인해 실현 가능한 솔루션이 아닌 것으로 간주되었습니다.
- 수동 액체 냉각 평가: 수동 액체 냉각은 이 특정 응용 분야에 부적합한 것으로 밝혀졌습니다. 효과적인 수동 대류를 위해 필요한 방향(히트 싱크 아래의 열원)은 LED의 광 출력을 방해합니다. 또한 물(열전도율 0.6W/mK)을 통한 전도에만 의존하는 것은 열 부하에 충분하지 않았습니다.
- 능동 액체 냉각 성능: IMS 보드 아래에 장착되고 원격 열교환기에 연결된 수냉식 콜드 플레이트를 사용하는 능동 액체 냉각(Figure 9)은 열 성능에서 상당한 개선을 보여주었습니다. 이 시스템의 계산된 LED 접합 온도는 110°C였으며(Figure 10), 이는 인클로저 내 자연 대류에 비해 90°C 개선된 것입니다.
- 확인된 절충안: 이 연구는 열적으로 최적의 솔루션을 달성하는 것과 제조 가능성, 무게 제한 및 사용 가능한 공간과 같은 실제 응용 제약 조건을 준수하는 것 사이의 고유한 절충안을 강조했습니다. 능동 액체 냉각은 우수한 열 성능을 제공했지만 펌핑 누출 위험, 펌프 신뢰성 문제, 추가 전력 소비, 액체 증발, 건조 및 막힘 가능성, 추가 유지 보수 필요성과 같은 잠재적인 단점도 도입했습니다.
그림 이름 목록:
- Figure 1. Insulated Metal Substrate assembly. (a) AlN cup with wire-bonded LED, (b) Circuit layer, (c) Dielectric layer and (d) Aluminium substrate. (절연 금속 기판 어셈블리. (a) 와이어 본딩된 LED가 있는 AlN 컵, (b) 회로층, (c) 유전체층 및 (d) 알루미늄 기판.)
- Figure 2. Simulated IMS Board with three LEDS mounted on a vertical Heat Sink. (수직 히트 싱크에 장착된 3개의 LED가 있는 시뮬레이션된 IMS 보드.)
- Figure 3. LED Junction Temperature vs. Fin Number (LED 접합 온도 대 핀 수)
- Figure 4. LED Junction Temperature vs. Fin Thickness (LED 접합 온도 대 핀 두께)
- Figure 5. LED Junction Temperature vs. Fin Height (LED 접합 온도 대 핀 높이)
- Figure 6. LED Junction Temperature vs. Base Plate Area (LED 접합 온도 대 베이스 플레이트 면적)
- Figure 7. Cross Section Temperature Profiles in Natural Convection for assembly in Figure 2. (a) Top view and (b) Side view. Temperature range shown is 60 to 100°C. (Figure 2의 어셈블리에 대한 자연 대류에서의 단면 온도 프로파일. (a) 상면도 및 (b) 측면도. 표시된 온도 범위는 60~100°C입니다.)
- Figure 8. Optimised Heat Sink inside a headlight enclosure (Tj = 200°C). Temperature range shown is 25 to 180°C. (헤드라이트 인클로저 내부의 최적화된 히트 싱크 (Tj = 200°C). 표시된 온도 범위는 25~180°C입니다.)
- Figure 9. Active Liquid Cooling. The IMS board is mounted on a liquid-cooled cold plate which is connected with hoses to a heat exchanger. (능동 액체 냉각. IMS 보드는 액체 냉각식 콜드 플레이트에 장착되며 호스를 통해 열교환기에 연결됩니다.)
- Figure 10. Temperature Profile of Active Liquid Cooling (Figure 9). Temperature range shown is 35 to 95°C. The flow velocity range is 0 to 4.5 m/s. (능동 액체 냉각의 온도 프로파일 (Figure 9). 표시된 온도 범위는 35~95°C입니다. 유속 범위는 0~4.5m/s입니다.)
7. 결론:
본 논문은 새로운 자동차 헤드라이트 응용 분야에 맞춤화된 LED를 위한 최적의 냉각 솔루션 선택 절차를 간략하게 설명합니다. 연구 결과, 자연 대류 냉각은 조사 대상 고전력 LED 시스템의 LED 접합 온도를 최대 허용 수준 이하로 유지하기에 충분하지 않았으며, 특히 밀폐된 환경에서는 더욱 그러했습니다. 공기를 이용한 강제 대류 냉각 또한 자동차 환경 내 공간 및 신뢰성 제약으로 인해 실현 불가능한 것으로 결정되었습니다. 시뮬레이션 결과, 자동차 응용 분야에서 고휘도 LED의 열 관리에서 능동 액체 냉각은 냉각 능력을 크게 향상시켜 접합 온도를 약 200°C(밀폐된 환경에서 자연 대류로 달성)에서 110°C로 낮출 수 있음을 보여주었습니다. 그러나 본 논문은 펌핑 누출 가능성, 펌프 신뢰성 문제, 추가 전력 소비, 액체 증발, 건조 및 막힘 위험, 추가 유지 보수 요구 사항과 같은 액체 냉각과 관련된 몇 가지 주요 단점도 인정합니다. 저자들은 향후 특정 광 출력에 대해 더 적은 구동 전력을 필요로 하는 훨씬 더 밝은 백색 LED가 개발됨에 따라 더 간단한 공기 냉각 솔루션이 다시 적절해질 수 있다고 제안합니다.
8. 참고문헌:
- [1] Pearson, T., Mounier, E., Eloy, J.C., Jourdan, D., "Solid-state lighting in the automobile: concept, market timing and performance," LEDs Magazine, pp. 25-27, Apr. 2005.
- [2] Stratford, J and Musters, A, “Insulated metal printed circuits – a user-friendly revolution in power design," Electronics Cooling, vol. 10, pp. 30-34, Nov. 2004.
- [3] Flomerics Ltd., FloThermTM 6.1 Instruction Manual, 2005.
- [4] Karimpourian, B. and Mahmoudi, J., “Some important considerations in heatsink design," Proc. of the 6th EuroSimE Conference, pp 406-413 (2005)
- [5] Azar, K., “Cooling technology options, part 1," Electronics Cooling, vol. 9, Aug. 2003
- [6] Azar, K., "Cooling technology options, part 2," Electronics Cooling, vol. 9, Nov. 2003
9. 저작권:
- 본 자료는 "Yan Lai, Nicolás Cordero"의 논문입니다. "[Thermal Management of Bright LEDs for Automotive Applications]"을 기반으로 합니다.
- 논문 출처: https://doi.org/10.1109/ESIME.2006.1643953
본 자료는 위 논문을 바탕으로 요약되었으며, 상업적 목적의 무단 사용을 금합니다.
Copyright © 2025 CASTMAN. All rights reserved.