본 논문 요약은 ['International Journal of Metalcasting']에서 발행한 ['INDUSTRY 4.0 FOUNDRY DATA MANAGEMENT AND SUPERVISED MACHINE LEARNING IN LOW-PRESSURE DIE CASTING QUALITY IMPROVEMENT'] 논문을 기반으로 작성되었습니다.
1. 개요:
- 제목: 인더스트리 4.0 주조 데이터 관리 및 저압 다이캐스팅 품질 개선을 위한 지도 학습 머신 러닝 (INDUSTRY 4.0 FOUNDRY DATA MANAGEMENT AND SUPERVISED MACHINE LEARNING IN LOW-PRESSURE DIE CASTING QUALITY IMPROVEMENT)
- 저자: Tekin Ç. Uyan, Maria Santos Silva, Pedro Vilaça, Kevin Otto, Elvan Armakan
- 발행 연도: 2023년
- 발행 저널/학회: International Journal of Metalcasting
- 키워드: 저압 다이캐스팅, 머신러닝, 알로이 휠, 인더스트리 4.0, 스마트 파운드리, 지속 가능한 금속 가공
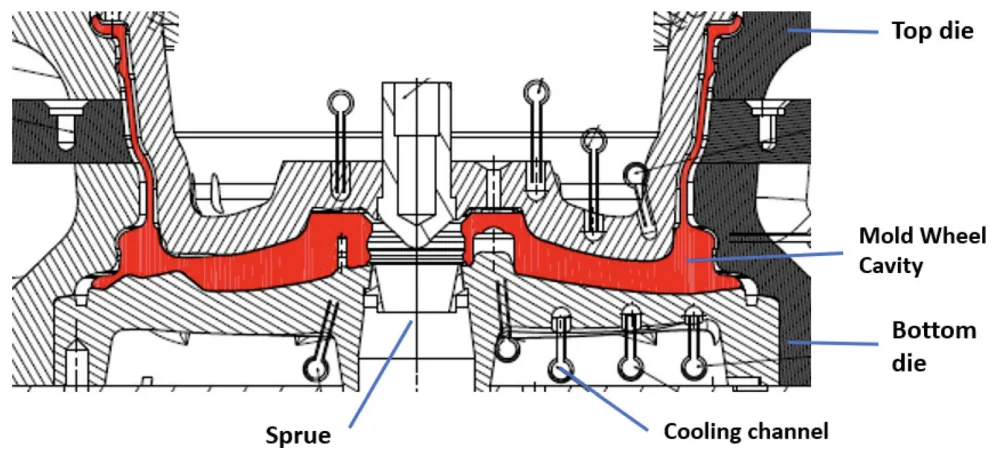
2. 초록 또는 서론
저압 다이캐스팅(LPDC)은 기공 결함이 허용되지 않는 고성능 정밀 알루미늄 합금 자동차 휠 주조품 생산에 널리 사용됩니다. LPDC 부품의 품질은 주조 공정 조건에 크게 영향을 받습니다. 가스 및 수축 기공과 같은 어려운 결함에 대한 부품 품질을 개선하기 위해 공정 변수를 최적화해야 할 필요성이 존재합니다.
이를 위해 공정 변수 측정값을 결함 발생률과 비교하여 연구해야 합니다. 본 논문에서는 인더스트리 4.0 클라우드 기반 시스템을 사용하여 데이터를 추출합니다. 이러한 데이터를 바탕으로 실제 파운드리 알루미늄 LPDC 공정에서 결함 발생을 예측하는 조건을 식별하기 위해 지도 학습 머신러닝 분류 모델을 제안합니다.
근본 원인 분석은 결함률이 낮고 잠재적인 공정 측정 변수가 많기 때문에 어렵습니다. XGBoost 분류 알고리즘 기반 모델을 사용하여 공정 조건과 결함이 있는 휠 림 생성 간의 복잡한 관계를 매핑했습니다. 데이터는 특정 LPDC 기계 및 다이 몰드에서 3교대로 6일 연속 수집했습니다.
기공 결함 발생률은 상당히 작은 샘플(결함이 있는 62개 휠을 포함한 1077개 휠)에서 수집한 13개의 공정 변수에서 추출한 36개의 특징을 사용하여 예측할 수 있었으며, 양호 부품에 대해 87%, 기공 결함이 있는 부품에 대해 74%의 정확도를 보였습니다. 본 연구는 결함률을 낮추기 위해 신제품 양산 전 생산 단계에서 공정 파라미터 튜닝을 지원하는 데 도움이 되었습니다.
3. 연구 배경:
연구 주제 배경:
저압 다이캐스팅(LPDC)은 고성능, 정밀도 및 대량 생산이 요구되는 금속 주조 부품, 특히 자동차 산업의 알루미늄 합금 휠 림 생산에 광범위하게 사용되는 공정입니다. 기공 불연속성은 LPDC 알루미늄 제품에서 가장 흔하게 발견되는 결함 중 하나이며, 부품의 무결성 및 성능을 저하시킬 수 있습니다. 따라서 기공 결함의 원인과 예방은 품질 관리에서 중요한 고려 사항이며, 부품 품질을 개선하기 위해 공정 변수를 최적화해야 할 필요성을 야기합니다.
기공 결함의 원인은 금속 조성, 수소 함량, 주조 압력, 온도, 방향성 응고 속도를 얻기 위한 다이 열 관리 등 다양한 요인에서 비롯될 수 있습니다. 이러한 주조 결함이 발생했을 때 정확한 근본 원인을 진단하고 올바른 공정 파라미터 변경을 수행하는 것은 종종 어렵습니다. 기공 결함을 유발할 수 있는 공정 설정 및 편차를 모니터링하고 분석하는 수단이 필요합니다. 인더스트리 4.0 품질 관리 시스템은 모든 공정 측정 지점에서 기록된 데이터를 검사 결과와 함께 개별 부품에 연결할 수 있습니다. 이를 통해 머신러닝 분류기 알고리즘을 활용하여 공정 결함을 유발하는 공정 설정 조합을 식별하고 공정 제어 튜닝을 지원할 수 있습니다.
기존 연구 현황:
LPDC 생산은 역사적으로 높은 불량률을 보여왔으며, 일반적으로 모든 생산 부품은 기공 결함에 대해 X선 검사를 거칩니다. 본 연구는 기공 결함 예측에 도움이 될 수 있지만, 검사를 위한 X선 기계를 대체할 수는 없습니다. 그러나 기공 결함의 원인을 정량화하는 데는 유용합니다. 일반적인 파운드리는 수백 가지의 모델과 매년 수십 가지의 새로운 제품 모델을 보유하고 있습니다.
따라서 양산 전 생산 단계에서 공정 설정을 신속하게 튜닝하는 것이 중요합니다. 현재 파운드리 공정 제어는 일반적으로 검사 기반 합격 절차에 의존합니다. 투입 자재, 주조 결과 품질 관리 및 공정 제어는 지정된 한도 내에서 준수하는지 검사하거나 모니터링합니다. 부품 결함은 X선 이미지의 기공 존재 여부에 대한 육안 검사로 정의됩니다. 작업 문제는 투입물이 허용 오차를 벗어날 때 정의됩니다. 이러한 현재 상태는 결함 제어를 어렵게 만듭니다. 첫째, 육안 검사 및 수동 제어는 상당한 반복성 및 재현성 측정 오류를 가질 수 있습니다.
또한, 이러한 접근 방식은 허용 오차 범위 내의 투입물의 조합이 기공 결함을 유발할 수 있다는 것을 인지하지 못하게 할 수 있습니다. 공정의 가상 모델, 즉 소위 "디지털 트윈"이 머신러닝 방법으로 구축되어 합격 및 불합격 부품을 예측하는 데 제안되었습니다. 이 디지털 트윈은 광범위한 품질 데이터 획득을 통해 파운드리 작업을 통해 주조 부품의 마킹 및 추적에 의존합니다.
이러한 인더스트리 4.0 디지털 트윈 모델은 오늘날 널리 보급되어 있지 않습니다. Prucha[6, 7]가 도입한 바와 같이, 고품질 결과를 위해 파운드리 공정의 인공 지능 및 데이터 기반 공정 제어를 구축하기 위해 단계별 지식 기반 접근 방식이 취해질 것입니다.
연구의 필요성:
결함 부품의 발병을 예측하기 위해 공장 데이터를 사용하여 머신러닝 모델을 구축하는 것은 여러 가지 이유로 어렵습니다. 잠재적인 인과 요인의 수가 방대합니다. 이러한 모든 공정 데이터를 수집하기 위해 계측하는 것이 어려울 수 있습니다. 또한 시계열 데이터의 특징을 식별해야 합니다. 여기에는 높고 낮은 변화, 또는 너무 높은 변동성, 또는 시간 경과에 따른 데이터의 급격한 변화가 포함될 수 있습니다. 특징은 결함의 원인과 관련될 수 있는 것으로 검토됩니다.
또한 수집된 공정 데이터는 생산되는 실제 부품과 연결되어야 합니다. 그래야 이러한 공정 조건이 부품의 합격 또는 불합격 지표와 연결될 수 있습니다. 공정 데이터를 수집하는 것만으로는 충분하지 않으며, 공정 데이터는 부품에 태그되어야 합니다. 이는 어떤 공정 데이터를 어떤 부품과 연결해야 하는지 알기 위해 파운드리를 통해 부품을 추적해야 함을 의미합니다. 이것이 스마트 파운드리의 중요한 인더스트리 4.0 과제 중 하나입니다.
파운드리는 열악한 조건에서 작동하며, 투입 자재 흐름의 시작부터 최종 주조 부품까지 각 부품을 추적하고 표시하기가 어렵습니다[1-3]. 두 번째 과제는 머신러닝 통계 분석을 위해 시계열 데이터를 특징으로 전처리하는 것입니다. 전체 데이터 세트보다는 공정 엔지니어가 이해하는 엔지니어링 통계량을 고려하는 것이 유용합니다[4, 5]. 예를 들어, 시계열 압력, 온도 및 냉각 데이터는 위상으로 분리하고 각 위상 내에서 통계량을 계산할 수 있습니다.
여기에는 데이터를 채우기 및 응고와 같은 위상으로 분리하고 위상 내에서 평균 및 분산과 같은 특징을 계산하는 것이 포함될 수 있습니다. 공정 엔지니어는 평균 변화와 다양한 위상에서 더 높고 낮은 변동성이 수율에 미치는 영향을 이해하고자 합니다. 마지막으로, 특징이 주어지면 이러한 특징을 결함률과 연결하는 데 사용할 수 있는 여러 가지 대안적인 분류 방법이 있습니다.
전반적으로 결함의 원인과 근본 원인을 더 잘 이해하기 위해 머신러닝을 탐구할 연구 기회가 존재합니다. 현재 상태의 파운드리 공정 제어는 일반적으로 검사 기반 합격 절차입니다. 투입 자재, 주조 결과 품질 관리 및 공정 제어는 지정된 한도 내에서 준수하는지 검사하거나 모니터링합니다. 부품 결함은 X선 이미지의 기공 존재 여부에 대한 육안 검사로 정의됩니다. 작업 문제는 투입물이 허용 오차를 벗어날 때 정의됩니다.
4. 연구 목적 및 연구 질문:
연구 목적:
본 연구의 목적은 LPDC 파운드리 공정 데이터를 수집하고 머신러닝 모델을 사용하여 공정 파라미터 및 공차와 사용 불가능한 주조 부품을 유발하는 중요한 결함 발생 간의 상관 관계를 분석하는 방법을 제시하는 것입니다. 이 방법은 머신 공정 데이터 수집, 부품 추적 및 결함 데이터 품질 검사를 포함합니다. 본 연구는 소규모 데이터 세트에 대한 머신러닝 응용 프로그램을 통해 공정 설정을 확립하는 데 도움이 되는 산업 파운드리의 대표적인 사례로 차별화됩니다. LPDC 기계 및 금속 관련 특징을 활용하여 고성능 자동차 휠의 알루미늄 합금 LPDC 공정의 기공 결함을 예측했습니다.
핵심 연구:
- LPDC 파운드리를 위한 인더스트리 4.0 데이터 수집 시스템 개발을 통해 부품과 관련 데이터를 디지털 방식으로 타임스탬프를 찍고 추적합니다.
- 지도 머신러닝 분류 모델, 특히 XGBoost를 적용하여 기공 결함을 예측하는 공정 조건을 식별합니다.
- 시계열 공정 데이터를 머신러닝 분석에 적합한 관련 통계적 특징으로 특징 엔지니어링합니다.
- 소규모의 불균형 산업 데이터 세트를 사용하여 기공 결함 예측에 대한 모델 성능을 평가합니다.
- Shapley 값을 사용하여 특징 중요도를 해석하여 기공 결함에 영향을 미치는 주요 공정 파라미터를 식별합니다.
연구 가설:
- 인더스트리 4.0 데이터 수집 시스템과 머신러닝을 결합하면 일상적으로 수집되는 생산 데이터를 사용하여 LPDC 공정의 기공 결함을 효과적으로 예측할 수 있습니다.
- XGBoost 알고리즘은 불균형 데이터 세트를 처리하는 데 적합하며 제한된 데이터 세트로 LPDC에서 기공 결함을 예측하는 데 허용 가능한 정확도를 달성할 수 있습니다.
- 시계열 공정 데이터에서 추출한 통계적 특징은 공정 변동을 효과적으로 나타내고 기공 결함 발생과 상관 관계를 가질 수 있습니다.
- 특징 중요도 분석을 통해 주요 공정 파라미터를 식별하면 LPDC에서 공정 최적화 및 결함 감소를 위한 실행 가능한 통찰력을 얻을 수 있습니다.
5. 연구 방법론
연구 설계:
본 연구는 산업 LPDC 파운드리의 과거 생산 데이터를 활용한 데이터 기반 접근 방식을 채택했습니다. 연구는 알루미늄 합금 휠 주조품을 생산하는 특정 LPDC 기계 및 다이 몰드에 초점을 맞췄습니다. 데이터 수집은 3교대로 6일 연속으로 이루어졌습니다. 연구 설계는 다음을 포함합니다.
- 데이터 수집 시스템 구현: 인더스트리 4.0 클라우드 기반 시스템을 활용하여 다양한 소스(LPDC 기계 센서, 자재 배치 데이터, X선 검사 데이터)에서 공정 데이터를 추출하고 통합합니다.
- 부품 추적: 공정 데이터를 품질 검사 결과에 연결하여 파운드리 공정 전반에 걸쳐 개별 부품을 추적하는 시스템을 구현합니다.
- 특징 엔지니어링: 시계열 공정 데이터를 전처리하여 기공 결함 형성과 관련된 통계적 특징(평균, 표준 편차, 지속 시간)을 추출합니다.
- 머신러닝 모델 개발: 추출된 특징을 기반으로 기공 결함을 예측하기 위해 XGBoost 분류 모델을 훈련하고 평가합니다.
- 모델 검증: 데이터 세트의 계층화된 분할을 훈련 및 테스트 세트로 사용하여 모델 성능을 평가하고 10겹 교차 검증을 사용합니다.
- 특징 중요도 분석: Shapley 값을 활용하여 XGBoost 모델을 해석하고 기공 결함에 영향을 미치는 주요 공정 파라미터를 식별합니다.
데이터 수집 방법:
데이터는 터키 이즈미르에 있는 Cevher Wheels Casting Plant에서 수집되었습니다. 데이터 수집 프로세스는 다음을 포함합니다.
- LPDC 기계 데이터: 성형 압력, 온도, 공기 및 물 채널 냉각을 모니터링하는 센서의 시계열 데이터로, 1~2초 간격으로 기록됩니다.
- 자재 배치 데이터: 용광로에서 채취한 샘플의 실험실 화학 분석에서 얻은 밀도 지수(DI) 및 실리콘 함량(Si)을 포함한 알루미늄 합금 금속 배치 속성입니다.
- X선 검사 데이터: DIN EN ISO 19232-1 및 DIN EN ISO 19232-5 표준에 따라 100% 휠 림의 X선 스캔으로 결정된 기공 결함에 대한 합격/불합격 결과입니다.
- 부품 추적 데이터: 데이터 세트를 연결하기 위해 공정의 각 단계(LPDC 기계, X선 검사)에서 타임스탬프 및 부품 식별자입니다.
분석 방법:
사용된 분석 방법은 다음과 같습니다.
- 통계적 특징 추출: 시계열 데이터를 위상(예: 채우기, 응고)으로 분할하고 압력 및 온도와 같은 변수에 대해 각 위상에 대한 통계적 특징(평균, 표준 편차)을 계산했습니다.
- XGBoost 분류: XGBoost 알고리즘을 이진 분류(양호/불량 부품)에 사용했습니다. Hyperopt 라이브러리의 Bayesian Optimization을 사용하여 하이퍼파라미터 튜닝을 수행했습니다.
- 성능 지표: 정확도, 정밀도, 재현율 및 F1 점수를 사용하여 모델 성능을 평가했습니다. AUC(Area Under the Curve)를 하이퍼파라미터 최적화를 위한 목적 함수로 사용했습니다.
- Shapley 값 분석: Shapley 값을 계산하여 각 입력 특징이 모델 예측에 기여하는 정도를 결정하고 특징 중요도에 대한 통찰력을 제공했습니다.
연구 대상 및 범위:
연구 대상은 Cevher Wheels Casting Plant의 특정 LPDC 기계 및 다이 몰드에서 생산된 알루미늄 합금 휠 주조품입니다. 데이터 세트는 1077개의 휠 림으로 구성되었으며, 그중 62개는 기공으로 인한 결함으로 식별되었습니다. 범위는 기공 결함으로 제한되었으며 다른 유형의 주조 결함은 포함하지 않았습니다. 분석은 LPDC 기계 작동 및 재료 속성과 관련된 13개의 공정 변수에서 파생된 36개의 특징에 초점을 맞췄습니다.
6. 주요 연구 결과:
핵심 연구 결과:
- XGBoost 분류 모델은 테스트 데이터 세트에서 양호 부품 예측에서 87%의 정확도를 달성했으며, 기공 결함이 있는 부품 예측에서는 74%의 정확도를 달성했습니다.
- Shapley 값을 사용한 특징 중요도 분석 결과, 공기 채널 유량, 특히 중앙 허브 근처 채널의 공기 유량 표준 편차 및 용융 실리콘 함량이 기공 결함의 가장 중요한 예측 변수로 확인되었습니다.
- 모델은 소규모의 불균형 산업 데이터 세트를 사용하여 기공 결함을 예측하는 능력을 입증하여 LPDC의 품질 개선을 위한 머신러닝의 잠재력을 강조했습니다.
- 정밀도와 재현율 간의 상충 관계가 관찰되어 특정 파운드리 요구 사항에 따라 오탐 또는 미탐을 최소화하는 데 우선순위를 두도록 모델 파라미터를 조정할 수 있었습니다.
제시된 데이터 분석:
- 혼동 행렬 (그림 6): 모델의 분류 성능을 보여주며, TN=440, FN=65, FP=8, TP=23입니다. 이는 불량 부품(74% 재현율)에 비해 양호 부품(87% 재현율)에 대한 정확도가 더 높다는 것을 나타냅니다.
- 통계 요약 보고서 (표 2): 양호 및 불량 부품 모두에 대한 정밀도, 재현율 및 F1 점수를 제공하여 모델 성능을 더욱 정량화합니다.
- 이진 의사 결정 트리 추정기 예시 (그림 7): XGBoost 모델의 단순화된 의사 결정 트리를 보여주며, 특정 특징 값(예: 공기 채널 2 표준 편차, 밀도 지수)이 실패 확률에 미치는 영향을 보여줍니다.
- 특징 중요도 순서 (그림 8): Shapley 지수를 기준으로 입력 특징의 순위를 매겨 기공 결함 예측에 가장 영향력 있는 변수를 강조합니다. 상위 특징은 다양한 냉각 채널의 공기 유량 표준 편차 및 용융 실리콘 함량과 관련이 있습니다.
- 모델 상충 관계 곡선 (그림 9): 합격 및 불합격 정확도 간의 상충 관계를 보여주며, 불량 부품 예측 정확도를 높이면 양호 부품 예측 정확도가 감소하고 그 반대의 경우도 마찬가지임을 보여줍니다.
그림 목록:
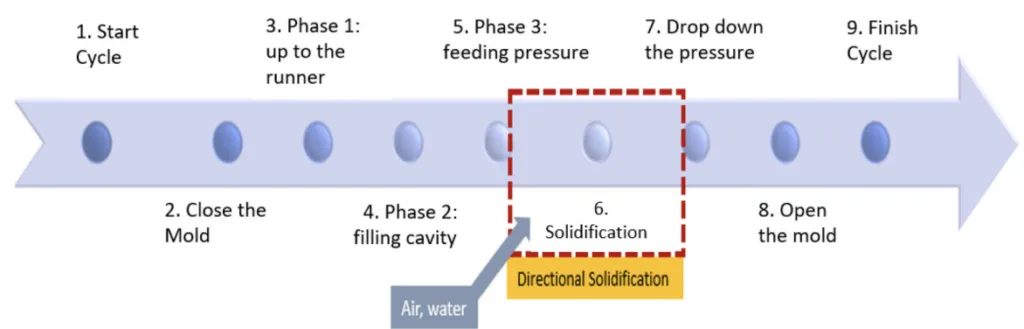


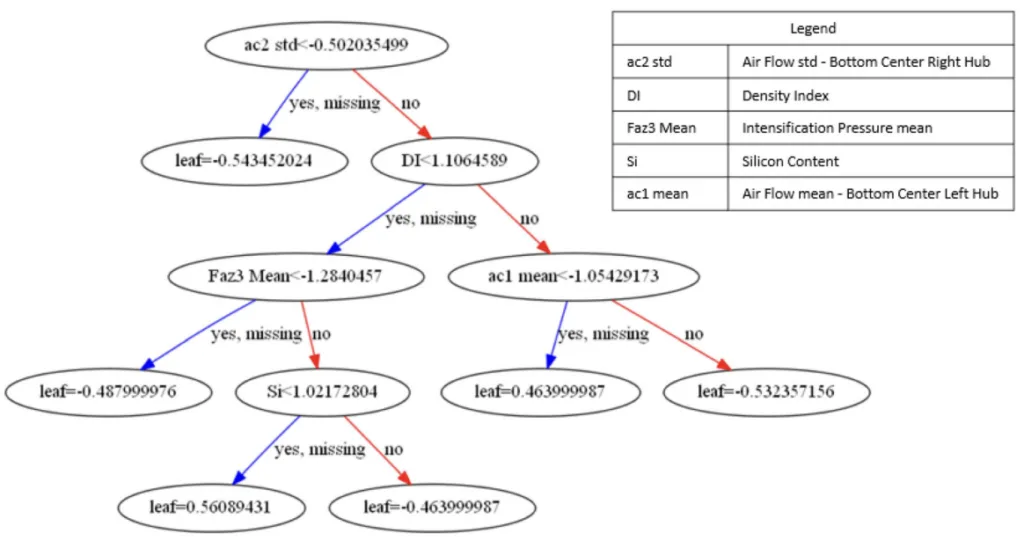
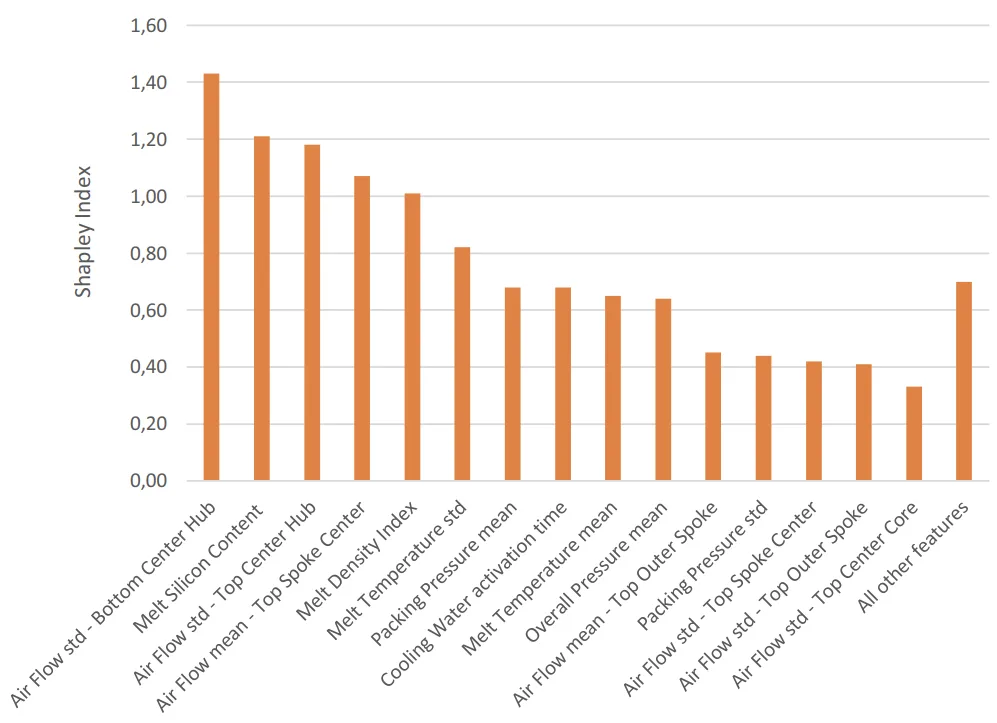
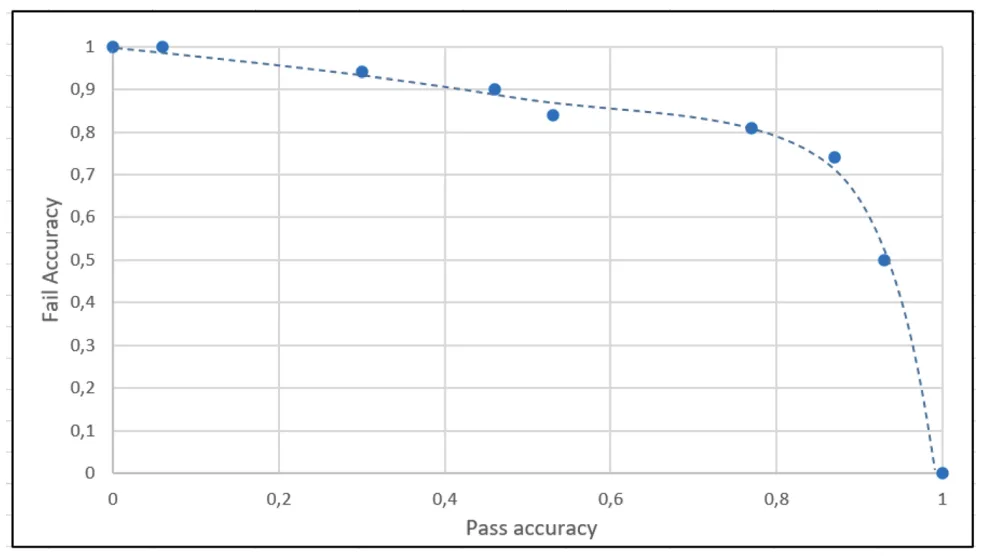
- 그림 1. LPDC 기계의 다이 몰드 단면도.
- 그림 2. 저압 다이캐스팅 공정 사이클.
- 그림 3. LPDC 기계의 시계열 압력 측정.
- 그림 4. 스포크에 기공 결함이 있는 다이캐스트 휠 림의 X선 스캔.
- 그림 5. 높은 변동성을 가진 증압 사이클의 예.
- 그림 6. 부품 품질에 대한 XGBoost 모델의 혼동 행렬.
- 그림 7. 이진 의사 결정 트리 추정기 예시.
- 그림 8. 특징 중요도 순서.
- 그림 9. 합격 및 불합격 정확도 간의 모델 상충 관계.
7. 결론:
주요 결과 요약:
본 연구는 인더스트리 4.0 데이터 관리 및 지도 머신러닝을 LPDC의 품질 개선에 성공적으로 적용한 사례를 제시합니다. XGBoost 모델은 소규모의 불균형 산업 데이터 세트를 사용하여 기공 결함을 합리적인 정확도로 효과적으로 예측했습니다. 기공 결함의 주요 예측 변수는 공기 냉각 채널 유량의 변동 및 용융 실리콘 함량으로 확인되었습니다. 본 연구는 파운드리가 생산 데이터를 활용하여 공정 최적화 및 결함 감소를 달성할 수 있는 방법론을 제공합니다.
연구의 학문적 의의:
본 연구는 머신러닝을 제조, 특히 금속 주조에 적용하는 분야의 문헌을 확장하는 데 기여합니다. 또한, 산업 현장에서 쉽게 구할 수 있는 데이터와 XGBoost 및 Shapley 값과 같은 고급 머신러닝 기술을 활용하여 LPDC의 복잡한 품질 관리 문제를 해결할 수 있음을 입증합니다. 본 연구는 산업 환경에서 효과적인 머신러닝 모델 개발을 위해 특징 엔지니어링 및 데이터 전처리의 중요성을 강조합니다.
실용적 의미:
본 연구 결과는 LPDC 파운드리에 상당한 실용적 의미를 갖습니다. 개발된 방법론은 다음을 위해 구현될 수 있습니다.
- 양산 전 생산 단계에서 기공 결함 예측: 신제품의 신속한 공정 파라미터 튜닝을 지원합니다.
- 주요 공정 파라미터 식별: 결함을 줄이기 위한 목표 공정 최적화 노력을 가능하게 합니다.
- 품질 관리 개선: 기존 검사 방법을 예측 기능으로 보완합니다.
- 스크랩률 및 생산 비용 절감: 결함 원인을 사전에 해결함으로써 가능합니다.
- 데이터 기반 의사 결정 활성화: 공정 조정 및 품질 관리에 대한 정량적 근거를 제공합니다.
연구의 한계 및 향후 연구 분야:
- 소규모 데이터 세트: 모델은 단일 LPDC 기계 및 다이 몰드의 비교적 작은 데이터 세트를 기반으로 훈련 및 검증되었습니다. 모델 일반화 및 견고성을 개선하려면 더 크고 다양한 데이터 세트가 필요합니다.
- 제한된 결함 유형: 본 연구는 기공 결함에만 초점을 맞췄습니다. 향후 연구에서는 범위를 확장하여 다른 유형의 주조 결함을 포함하고 다중 클래스 분류 모델을 개발할 수 있습니다.
- 특징 세트: 36개의 특징이 사용되었지만, 추가 공정 파라미터와 더욱 정교한 특징 엔지니어링 기술을 탐색하면 모델 성능을 더욱 향상시킬 수 있습니다.
- 자동화된 데이터 수집 및 추적: 현재 데이터 수집은 반자동화되었습니다. 향후 연구에서는 원활한 통합 및 실시간 품질 모니터링을 위해 완전 자동화된 부품 추적 및 데이터 획득 시스템을 구현하는 데 초점을 맞춰야 합니다.
- 실시간 예측 및 제어: 향후 연구에서는 개발된 모델을 사전 예방적 결함 방지를 위한 실시간 공정 제어 시스템에 통합하는 것을 탐구할 수 있습니다.
8. 참고 문헌:
- [1] T. Uyan, K. Jalava, J. Orkas, K. Otto, Sand casting implementation of two-dimensional digital code direct-part-marking using additively manufactured tags. Int. J. Metalcast. (2021). https://doi.org/10.1007/s40962-021-00680-x
- [2] J. Landry, J. Maltais, J.M. Deschênes, M. Petro, X. Godmaire, A. Fraser, Inline integration of shot-blast resistant laser marking in a die cast cell. NADCA Trans 2018, T18–T123 (2018)
- [3] A. Fraser, J. Maltais, A. Monroe, M. Hartlieb, X. Godmaire, Important considerations for laser marking an identifier on die casting parts
- [4] D. Blondheim Jr., S. Bhowmik, Time-series analysis and anomaly detection of high-pressure die casting shot profiles. NADCA Die Cast. Eng., 14–18 (2019)
- [5] D. Blondheim, Improving manufacturing applications of machine learning by understanding defect classification and the critical error threshold. Int. J. Metalcast. (2021). https://doi.org/10.1007/s40962-021-00637-0
- [6] T. Prucha, From the editor big data. Int. J. Met. 9(3), 5 (2015)
- [7] T. Prucha, From the editor—AI needs CSI: common sense input. Int. J. Met. 12(3), 425–426 (2018)
- [8] T. Chen, C. Guestrin. Xgboost: a scalable tree boosting system. In: Proceedings of the 22nd international conference on knowledge discovery and data mining, pp. 785–794 (2016)
- [9] W. Dong, Y. Huang, B. Lehane, G. Ma, XGBoost algorithm-based prediction of concrete electrical resistivity for structural health monitoring. Autom. Construct. 114, 103155 (2020)
- [10] M.S. Alajmi, A.M. Almeshal, Predicting the tool wear of a drilling process using novel machine learning XGBoost-SDA. Materials (Basel) 13(21), 1–16 (2020). https://doi.org/10.3390/ma13214952
- [11] K. Gao, H. Chen, X. Zhang, X.K. Ren, J. Chen, X. Chen, A novel material removal prediction method based on acoustic sensing and ensemble XGBoost learning algorithm for robotic belt grinding of Inconel 718. Int. J. Adv. Manuf. Technol. 105(1-4), 217-232 (2019). https://doi.org/10.1007/s00170-019-04170-7
- [12] S. Chakraborty, S. Bhattacharya, Application of XGBoost algorithm as a predictive tool in a CNC turning process. Reports Mech. Eng. 2(2), 190–201 (2021). https://doi.org/10.31181/rme2001021901b
- [13] K. Chen, H. Chen, L. Liu, S. Chen, Prediction of weld bead geometry of MAG welding based on XGBoost algorithm. Int. J. Adv. Manuf. Technol. 101(9–12), 2283–2295 (2019). https://doi.org/10.1007/s00170-018-3083-6
- [14] Z. Zhang, Y. Huang, R. Qin, W. Ren, G. Wen, XGBoost-based on-line prediction of seam tensile strength for Al-Li alloy in laser welding: experiment study and modelling. J. Manuf. Process. 64, 30-44 (2021). https://doi.org/10.1016/j.jmapro.2020.12.004
- [15] J. Deng, Y. Xu, Z. Zuo, Z. Hou, S. Chen, Bead geometry prediction for multi-layer and multi-bead wire and arc additive manufacturing based on XGBoost. Trans. Intell. Weld. Manuf. (2019). https://doi.org/10.1007/978-981-13-8668-8_7
- [16] D.K. Choi, Data-driven materials modeling with XGBoost algorithm and statistical inference analysis for prediction of fatigue strength of steels. Int. J. Precis. Eng. Manuf. 20(1), 129–138 (2019). https://doi.org/10.1007/s12541-019-00048-6
- [17] K. Song, F. Yan, T. Ding, L. Gao, S. Lu, A steel property optimization model based on the XGBoost algorithm and improved PSO. Comput. Mater. Sci. (2020). https://doi.org/10.1016/j.commatsci.2019.109472
- [18] S. Yan, D. Chen, S. Wang, S. Liu, Quality prediction method for aluminum alloy ingot based on XGBoost. In: Proceedings of the 32nd Chinese Control Decis. Conf. CCDC 2020, pp. 2542-2547, 2020. https://doi.org/10.1109/CCDC49329.2020.9164112
- [19] S. Pan, Z. Zheng, Z. Guo, H. Luo, An optimized XGBoost method for predicting reservoir porosity using petrophysical logs. J. Pet. Sci. Eng. 208, 109520 (2022). https://doi.org/10.1016/j.petrol.2021.109520
- [20] T. Tao et al., Wind turbine blade icing diagnosis using hybrid features and Stacked-XGBoost algorithm. Renew. Energy 180, 1004–1013 (2021). https://doi.org/10.1016/j.renene.2021.09.008
- [21] V.D. Tsoukalas, S.A. Mavrommatis, N.G. Orfanou-dakis, A.K. Baldoukas. A study of porosity formation in pressure die casting using the Taguchi approach. In: Proc. Inst. Mech. Eng. Part B J. Eng. Manuf., vol. 218, no. 1, pp. 77-86, 2004. https://doi.org/10.1243/095440504772830228
- [22] Q.C. Hsu, A.T. Do, Minimum porosity formation in pressure die casting by taguchi method. Math. Probl. Eng. (2013). https://doi.org/10.1155/2013/920865
- [23] W. Ye, W. Shiping, N. Lianjie, X. Xiang, Z. Jianbing, X. Wenfeng, Optimization of low-pressure die casting process parameters for reduction of shrinkage porosity in ZL205A alloy casting using Taguchi method. Proc. Inst. Mech. Eng. 228(11), 1508–1514 (2014). https://doi.org/10.1177/0954405414521065
- [24] D.M. Maijer, W.S. Owen, R.A. Vetter, An investigation of predictive control for aluminum wheel casting via a virtual process model. J. Mater. Process. Technol. 209(4), 1965–1979 (2009). https://doi.org/10.1016/J.JMATPROTEC.2008.04.057
- [25] V.D. Tsoukalas, Optimization of porosity formation in AlSi9Cu3 pressure die castings using genetic algorithm analysis. Mater. Des. 29(10), 2027–2033 (2008). https://doi.org/10.1016/j.matdes.2008.04.016
- [26] Guo, S.M., et al., Inline inspection improvement using machine learning on broadband plasma inspector in an advanced foundry fab. In: Proceedings of the SEMI Advanced Semiconductor Manufacturing Conference (ASMC). IEEE (2019)
- [27] Park, S., et al., Prediction of the CNC tool wear using the machine learning technique.. In: Proceedings of the 2019 International Conference on Computational Science and Computational Intelligence (CSCI)
- [28] D. Wilk-Kolodziejczyk, K. Regulski, G. Gumienny, Comparative analysis of the properties of the nodular cast iron with carbides and the austempered ductile iron with use of the machine learning and the support vector machine. Int. J. Adv. Manuf. Technol. 87(1-4), 1077–1093 (2016)
- [29] R. Rodríguez-Pérez, J. Bajorath, Interpretation of machine learning models using shapley values: application to compound potency and multi-target activity predictions. J. Comput. Aided. Mol. Des. 34(10), 1013-1026 (2020). https://doi.org/10.1007/$10822-2020-00314-0
- [30] L. Zaremba, C.S. Zaremba, M. Suchenek, Modification of shapley value and its implementation in decision making. Found. Manag. 9(1), 257-272 (2017). https://doi.org/10.1515/fman-2017-0020]
- [31] D.C. Landinez-Lamadrid, D.G. Ramirez-Ríos, D. Neira Rodado, K. Parra Negrete, J.P. Combita Niño, Shapley Value: its algorithms and application to supply chains. INGE CUC 13(1), 61–69 (2017). https://doi.org/10.17981/ingecuc.13.1.2017.06
- [32] J. Ohana et al., Shapley values for LightGBM model applied to regime detection. 2021. [Online]. Available: https://hal.archives-ouvertes.fr/hal-03320300
- [33] J.K. Kittur, G.C. ManjunathPatel, M.B. Parappagoudar, Modeling of pressure die casting process: an artificial intelligence approach. Int. J. Metalcast. 10(1), 70–87 (2016). https://doi.org/10.1007/s40962-015-0001-7
- [34] J.K. Rai, A.M. Lajimi, P. Xirouchakis, An intelligent system for predicting HPDC process variables in interactive environment. J. Mater. Process. Technol. 203(1-3), 72–79 (2008). https://doi.org/10.1016/J.JMATPROTEC.2007.10.011
- [35] A. Kopper, R. Karkare, R.C. Paffenroth, D. Apelian, Model selection and evaluation for machine learning: deep learning in materials processing. Integr. Mater. Manuf. Innov. 9(3), 287-300 (2020)
- [36] A.E. Kopper, D. Apelian, Predicting quality of castings via supervised learning method. Int. J. Metalcast. (2021). https://doi.org/10.1007/s40962-021-00606-7
- [37] N. Sun, A. Kopper, R. Karkare, R.C. Paffenroth, D. Apelian, Machine learning pathway for harnessing knowledge and data in material processing. Int. J. Metalcast. 15(2), 398–410 (2021). https://doi.org/10.1007/s40962-020-00506-2
- [38] C. Reilly, J. Duan, L. Yao, D.M. Maijer, S.L. Cockcroft, Process modeling of low-pressure die casting of aluminum alloy automotive wheels. JOM 65(9), 1111-1121 (2013)
- [39] L. Zhang, R. Wang, An intelligent system for low-pressure die-cast process parameters optimization. Int. J. Adv. Manuf. Technol. 65(1-4), 517–524 (2013)
- [40] B. Zhang, S.L. Cockcroft, D.M. Maijer, J.D. Zhu, A.Β. Phillion, Casting defects in low-pressure die-cast aluminum alloy wheels. JOM 57(11), 36–43 (2005). https://doi.org/10.1007/s11837-005-0025-1
- [41] ASTM E155-15, Standard reference radiographs for inspection of aluminum and magnesium castings. ASTM International, West Conshohocken, 2015, www.astm.org
- [42] ISO 19232-1:2013, Non-destructive testing-image quality of radiographs-Part 1: determination of the image quality value using wire-type image quality indicators
- [43] ISO 19232-5:2018, Non-destructive testing-image quality of radiographs-Part 5: determination of the image unsharpness and basic spatial resolution value using duplex wire-type image quality indicators
- [44] D. Dispinar, J. Campbell, Porosity, hydrogen and bifilm content in Al alloy castings. Mater. Sci. Eng. A 528(10-11), 3860–3865 (2011). https://doi.org/10.1016/j.msea.2011.01.084
- [45] S. Akhtar, L. Arnberg, M. Di Sabatino et al., A comparative study of porosity and pore morphology in a directionally solidified A356 alloy. Int. Metalcast. 3, 39-52 (2009). https://doi.org/10.1007/BF03355440
- [46] P. Fan, S.L. Cockcroft, D.M. Maijer, L. Yao, C. Reilly, A.B. Phillion, Porosity prediction in A356 wheel casting. Metall. Mater. Trans. B. Sci. 50, 2421-2425 (2019)
- [47] M. Uludağ, R. Çetin, L. Gemi et al., Change in porosity of A356 by holding time and its effect on mechanical properties. J. Mater. Eng. Perform. 27, 5141-5151 (2018). https://doi.org/10.1007/s11665-018-3534-0
- [48] S.G. Lee, A.M. Gokhale, G.R. Patel, M. Evans, Effect of process parameters on porosity distributions in high-pressure die-cast AM50 Mg-alloy. Mater. Sci. Eng. A 427(1-2), 99–111 (2006). https://doi.org/10.1016/j.msea.2006.04.082
- [49] K.N. Obiekea, S.Y. Aku, D.S. Yawas, Effects of pressure on the mechanical properties and microstructure of die cast aluminum A380 alloy. J. Miner. Mater. Charact. Eng. 02(03), 248-258 (2014). https://doi.org/10.4236/jmmce.2014.23029
- [50] H.S. Jang, H.J. Kang, J.Y. Park, Y.S. Choi, S. Shin, Effects of casting conditions for reduced pressure test on melt quality of Al-Si alloy. Metals 10(11), 1422 (2020). https://doi.org/10.3390/MET10111422
- [51] M. Di Sabatino, L. Arnberg, Castability of aluminium alloys. Trans. Indian Inst. Met. 62(4), 321–325 (2009)
- [52] B. Dybowski, L. Poloczek, A. Kiełbus, The porosity description in hypoeutectic Al-Si alloys. In Proceedings of the Key Engineering Materials (vol. 682, pp. 83-90). Trans Tech Publications Ltd (2016)
- [53] G.T. Gridli, P.A. Friedman, J.M. Boileau, Manufacturing processes for light alloys.. In Proceedings of the materials, design and manufacturing for light-weight vehicles, pp. 267-320. Woodhead Publishing (2021)
- [54] D. Sui, Z. Cui, R. Wang, S. Hao, Q. Han, Effect of cooling process on porosity in the aluminum alloy automotive wheel during low-pressure die casting. Int. J. Met. 10(1), 32–42 (2016). https://doi.org/10.1007/s40962-015-0008-0
- [55] D. Blondheim, A. Monroe, Macro porosity formation: a study in high pressure die casting. Int. J. Metalcast. 16(1), 330-341 (2022). https://doi.org/10.1007/s40962-021-00602-x
- [56] T. Prucha, From the editor—signals within signals. Int. J. Met. 9(2), 4 (2015)
- [57] D. Krstajic, L.J. Buturovic, D.E. Leahy, S. Thomas, Cross-validation pitfalls when selecting and assessing regression and classification models. J. Cheminform. 6(1), 10 (2014). https://doi.org/10.1186/1758-2946-6-10
- [58] J. Bergstra, D. Yamins, D.D. Cox, Making a science of model search: hyperparameter optimization in hundreds of dimensions for vision architectures. To appear in Proc. of the 30th International Conference on Machine Learning (ICML 2013)
- [59] G. Lemaître, F. Nogueira, C.K. Aridas, Imbalanced-learn: a python toolbox to tackle the curse of imbalanced datasets in machine learning. J. Mach. Learn. Res. 18(1), 559–563 (2017)
- [60] D.L. Wilson, Asymptotic properties of nearest neighbor rules using edited data. IEEE Trans. Syst. Man Commun. 2(3), 408–421 (1972)
- [61] L.S. Shapley, Notes on the N-person Game—I: characteristic-point solutions of the four-person game. Rand Corporation (1951)
- [62] D. Blondheim Jr., Utilizing machine learning autoencoders to detect anomalies in time-series data. NADCA Die Casting Engineer (2021)
9. 저작권:
- 본 자료는 "[The Author(s)]"의 논문: "[INDUSTRY 4.0 FOUNDRY DATA MANAGEMENT AND SUPERVISED MACHINE LEARNING IN LOW-PRESSURE DIE CASTING QUALITY IMPROVEMENT]"을 기반으로 합니다.
- 논문 출처: https://doi.org/10.1007/s40962-022-00783-z
본 자료는 상기 논문을 요약한 것으로, 상업적 목적으로 무단 사용하는 것을 금지합니다.
Copyright © 2025 CASTMAN. All rights reserved.