이 소개 자료는 "Eastern-European Journal of Enterprise Technologies"에서 발행한 논문 "Enhancing side die resistance to thermal shock in automotive casting: a comparative study of FCD550 and SKD6 materials"을 기반으로 합니다.
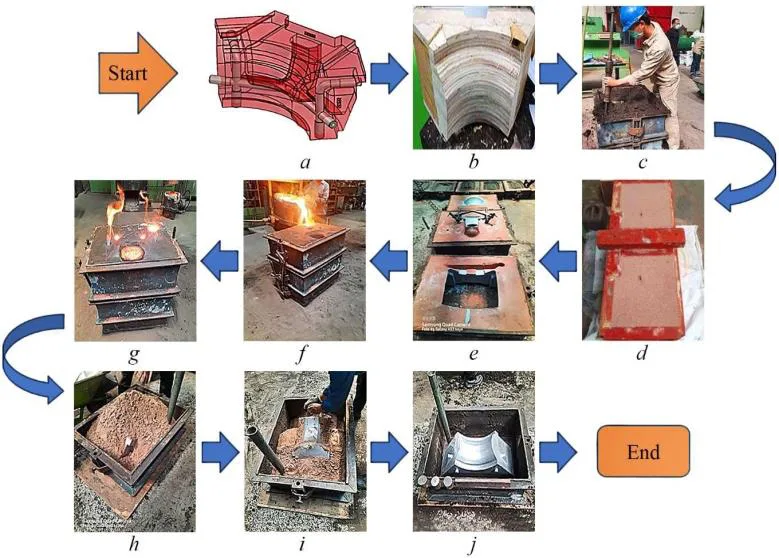
1. 개요:
- 논문 제목: Enhancing side die resistance to thermal shock in automotive casting: a comparative study of FCD550 and SKD6 materials (자동차 주조에서 열충격에 대한 사이드 다이 저항성 향상: FCD550 및 SKD6 소재 비교 연구)
- 저자: Herry Patria, Iwan Susanto, Belyamin, Dianta Mustofa Kamal
- 발행 연도: 2024
- 저널/학회명: Eastern-European Journal of Enterprise Technologies
- 키워드: thermal shock (열충격), die disc car wheel (다이 디스크 자동차 휠), manufacturing (제조), automotive parts (자동차 부품), casting productivity (주조 생산성)
2. 초록:
금형 디스크 자동차 응용 분야에서 FCD550 소재를 SKD6 소재로 대체하여 사이드 다이의 열충격 저항성을 향상시켰습니다. 주요 해결 과제는 가속화된 생산 공정으로 인한 열충격으로 사이드 다이에 균열이 발생하여 생산 중단 및 대량 고객 주문 미달로 이어지는 문제였습니다. 본 연구는 FCD550보다 열충격에 더 잘 견딜 수 있는 소재를 식별하여 사이드 다이의 내구성과 제조 공정의 전반적인 생산성을 향상시키는 것을 목표로 합니다. 연구에는 직접 생산 실험, FCD550 및 SKD6 소재 분석, 다이 특성 평가, 소재 변경 전후의 완제품 속성 평가가 포함되었습니다. 실험실 테스트 및 기계 설정 시험을 수행하여 생산 공정을 변경하고 결과를 평가했습니다. 연구 결과, SKD6이 금형 디스크 자동차 응용 분야에서 FCD550보다 열충격에 훨씬 더 강한 것으로 나타났습니다. 이 연구는 데이터 시트를 사용하여 사이드 다이 소재의 강도를 비교하고 기존 냉각 조건 하에서 설정 매개변수를 조정했습니다. 실험에는 표준 온도를 520–545 °C에서 532–538 °C로 변경하고 소킹(soaking) 시간을 최소 270–540초에서 332초로 단축하는 것이 포함되었습니다. 이로 인해 소킹 시간이 69초에서 46초로, 에이징(aging) 시간이 190초에서 180초로 단축되어 7대의 기계에서 주조 생산성이 28일당 194,870개에서 213,311개로 증가하여 사이드 다이 균열 없이 28일당 200,000개의 고객 요구 사항을 충족했습니다. TSD5605G 표준에 따른 5개 제품 샘플에 대한 내구성 테스트 결과 품질이 고객 사양을 충족하는 것으로 확인되었습니다.
3. 서론:
자동차 부품 제조에서 소재의 열충격 저항성 연구의 중요성은 매우 큽니다. 특히 차량이 더욱 발전함에 따라 혹독한 조건을 견딜 수 있는 부품에 대한 요구가 증가하고 있습니다[1]. 이러한 중요 부품 중 디스크 자동차 휠은 상당한 하중과 반복적인 응력을 견디는 중추적인 역할을 합니다[2]. 그 무결성을 보장하는 것은 차량 성능뿐만 아니라 안전 표준 준수에도 필수적입니다. 증가된 판매 주문과 생산성 향상 요구에 대응하여 제조 회사는 제품 품질을 유지하면서 생산 공정을 최적화해야 하는 과제에 직면해 있습니다. 그러나 이러한 효율성 추구는 제조 공정에서 사이드 다이 균열 발생에서 볼 수 있듯이 의도치 않게 새로운 문제를 야기할 수 있습니다. 고객 요구를 충족하기 위한 가속화된 생산 방법의 구현은 사이드 다이 영역 내에서 열충격 문제를 야기하여 균열 및 제품 품질 저하를 초래했습니다[3]. 이러한 문제를 해결하기 위해서는 열충격을 이해하는 것이 가장 중요합니다. 급격한 온도 변화는 소재에 기계적 응력을 유발하여 잠재적으로 구조적 파손으로 이어질 수 있습니다[4]. 따라서 사이드 다이와 같은 금형 소재의 열충격 저항성을 향상시키는 것은 생산 능력을 강화하고 제품 무결성을 유지하는 데 필수적입니다. 본 연구는 전통적인 FCD550 소재와 향상된 열충격 저항성을 포함한 유망한 특성을 가진 SKD6 합금을 비교하여 사이드 다이의 열충격 저항성을 향상시키는 방법을 조사하여 제조 효율성과 부품 내구성을 개선하고자 합니다.
4. 연구 요약:
연구 주제의 배경:
디스크 자동차 휠과 같은 자동차 부품은 높은 내구성과 작동 응력에 대한 저항성이 요구됩니다. 증가된 생산 요구는 가속화된 제조 공정을 필요로 하며, 이는 다이캐스팅 금형, 특히 사이드 다이 영역에서 열충격을 유발하여 균열 및 생산 중단을 초래할 수 있습니다[3]. 본 연구의 대상은 자동차 휠 디스크 제품 생산에 사용되는 사이드 다이의 열충격 저항성입니다.
기존 연구 현황:
이전 연구에서는 다이 소재의 미세 균열 및 관련 현상[5]을 확인하고 열전도율[6], 템퍼링 효과[7], 열응력 모델링[10]과 같은 측면을 탐구했습니다. 그러나 가속화된 주조 공정에서 열충격으로 인해 직접적으로 발생하는 균열 문제는 대체로 해결되지 않은 상태였습니다[9, 10]. SKD6 강재의 특성(고온 작동성, 우수한 인성, 내식성)은 알려져 있었지만[10, 11, 12], 이 특정 응용 분야에서 FCD550과 비교하여 열충격을 완화할 수 있는 잠재력은 평가가 필요했습니다.
연구 목적:
본 연구의 목적은 PSD3K 디스크 자동차 휠 타입 제품 생산 시 사이드 다이의 열충격 저항성을 향상시켜 제품 무결성과 품질을 유지하면서 제조 공정을 가속화하는 것입니다. 목표는 다음과 같습니다:
- FCD550 소재의 대체재로서 SKD6 강재의 적합성에 초점을 맞춰 우수한 열충격 저항 특성을 가진 소재를 식별하고 평가합니다.
- 열응력을 완화하기 위한 고급 냉각 시스템을 통합한 새로운 사이드 다이를 설계합니다.
- 다이캐스팅 기계 설정(예: 사출 속도, 금형 온도, 냉각 속도)을 수정하여 공정을 최적화합니다.
핵심 연구:
본 연구는 디스크 자동차 휠 주조용 사이드 다이 적용을 위해 FCD550과 SKD6 소재를 비교 분석했습니다. 소재 선택은 열충격 저항성과 관련된 특성(경도, 조성, 특히 바나듐 함량)에 초점을 맞춰 표준 데이터 시트(표 1-4)를 비교하여 이루어졌습니다. SKD6이 선택되었습니다. SKD6으로 사이드 다이를 제작(그림 1, 그림 2)하고 화학 조성을 검증했습니다(표 5). 냉각 시스템 개념을 시각화했습니다(그림 3). 다이캐스팅 기계를 사용하여 실험 시험을 수행하여 FCD550 및 SKD6 사이드 다이의 성능을 비교했습니다. 초기 시험은 기존 설정을 사용했으며, 이후 SKD6 다이에 대한 매개변수(온도, 소킹/에이징 시간)를 최적화했습니다(표 6, 그림 8). 성능은 다이 및 제품의 육안 검사, 경도 테스트(그림 6), 미세 구조 분석(그림 5), 기공 시뮬레이션(그림 7), 사이클 타임 측정 및 TSD5605G 표준에 따른 최종 제품 품질 테스트를 통해 평가되었습니다.
5. 연구 방법론
연구 설계:
본 연구는 비교 실험 설계를 사용했습니다. 다음을 포함합니다:
- 문헌 및 데이터 시트 비교를 통한 소재 선택 (FCD550 vs. SKD6).
- 선택된 소재(SKD6)로 사이드 다이 제작.
- 사이드 다이용 냉각 시스템 개념 설계 및 구현.
- 다이캐스팅 기계에서 직접 생산 실험을 수행하여 FCD550 및 SKD6 사이드 다이 성능 비교.
- SKD6 소재에 대한 기계 설정 매개변수 최적화.
- 소재 테스트, 공정 모니터링 및 제품 품질 평가를 통한 결과 검증.
데이터 수집 및 분석 방법:
- 소재 특성: 표준 데이터 시트(JIS G 5502, JIS G4404)를 사용한 비교.
- 제작된 다이 검증: 화학 조성 분석 (ARL 3460 OES), 경도 테스트 (ZHU250CL), 미세 구조 분석 (GX53 현미경, ESTM 155 표준).
- 공정 성능: 다이캐스팅 기계 매개변수(온도, 시간) 기록, 사이클 타임 측정, 균열에 대한 다이 육안 검사, 생산량 계수.
- 시뮬레이션: 기공 시각화 (그림 7에서 MAGMA 소프트웨어 사용 암시).
- 제품 품질: 치수 검사 (CMM Crystal Apex C7106), 내구성 테스트 (충격 테스트 13° 및 90°, 모멘트 수명 테스트 (CFT), 드럼 테스트 (RFT)) - Toyota 엔지니어링 표준 TSD5605G 기준.
연구 주제 및 범위:
본 연구는 자동차 디스크 휠(PSD3K 타입)의 고압 다이캐스팅에 사용되는 사이드 다이의 열충격 저항성 향상에 구체적으로 초점을 맞췄습니다. 범위는 다음을 포함합니다:
- FCD550 및 SKD6 소재 비교 평가.
- 수정된 냉각 시스템 설계 영향 평가.
- 다이캐스팅 기계 설정(온도, 소킹 시간, 에이징 시간) 최적화.
이 연구는 이 특정 응용 분야와 FCD550 및 SKD6 간의 비교에 국한되었습니다. 조사된 주요 변수는 사이드 다이 소재 대체였습니다.
6. 주요 결과:
주요 결과:
- 소재 선택: 데이터 시트 분석 결과, 조성(0.3-0.5% 바나듐 포함) 및 기계적 특성(더 높은 경도 잠재력)을 기반으로 SKD6이 FCD550보다 우수한 열충격 저항성 잠재력을 나타내어 선택되었습니다(표 1-4). 제작된 SKD6 다이는 요구되는 화학 조성 표준을 충족했습니다(표 5).
- 성능 비교: 실험 시험 결과, SKD6 다이가 FCD550 다이보다 열충격 균열에 훨씬 더 강한 것으로 나타났습니다. 유사한 초기 조건에서 1400 생산 사이클 후, FCD550 다이는 12%의 균열을 보인 반면, SKD6 다이는 0.5%의 헤어 크랙만 보였습니다(그림 7). SKD6 다이는 더 높은 온도(최대 450°C, FCD550은 362°C)에서 작동했지만 시뮬레이션 결과 제품의 미세 기공률은 더 낮았습니다(그림 7). 경도 테스트 결과 SKD6은 경화 후 47.50 HRC를 달성했습니다(그림 6).
- 공정 최적화: SKD6 다이에 대한 기계 설정이 성공적으로 최적화되었습니다. 주요 변경 사항에는 온도 조정(RZ1: 520-545°C에서 532-538°C) 및 시간 단축(소킹: 최소 270s에서 332s; 홀딩: 69s에서 46s; 에이징: 190s에서 180s)이 포함되었습니다. 이로 인해 총 사이클 타임이 517초에서 369초로 단축되었습니다(표 6, 그림 8).
- 생산성 및 품질: SKD6 다이를 사용한 최적화된 공정은 주조 생산성을 12% 증가시켜 7대의 기계에서 28일당 194,870개에서 213,311개로 증가시켰으며, 사이드 다이 균열 문제 없이 28일당 200,000개의 고객 요구 사항을 충족했습니다. 최종 제품 품질은 TSD5605G 표준에 따른 테스트를 통해 확인되었으며, 테스트된 샘플에서는 균열이 발견되지 않았습니다.
그림 목록:
- Fig. 1. Stages of side core mold manufacturing process: a – project design; b - Pola/Patten; c - die manufacture; d - core manufacture; e - furnace preparation; f- casting; g - solidification; h – sand mold disassembly; i – visual check; j – finishing side core
- Fig. 2. Stages of machining and ceramic coating process: a - side core; b - proses machining; c - proses ceramic coating; d - proses spray finishing
- Fig. 3. Visualization of main die and side die pieces
- Fig. 4. Results of material disposition: a - side die before coating; b - side die after coating
- Fig. 5. Structure micro: a - FCD550; b – SKD6
- Fig. 6. Hardness test results on SKD6 148 hours cooling on FCD550 material after cooling with water temperature 40 °C obtained test value 47.50 HRC
- Fig. 7. Micro photo visualization of: a - porosity temperature conditions FCD550; b – porosity temperature conditions SKD6; c - micro photo of porosity of FCD550; d - micro photo of porosity of SKD6
- Fig. 8. Graph of trial result evaluation data change setting parameters
7. 결론:
- 본 연구는 자동차 및 오토바이 디스크 휠에 사용되는 다이캐스팅 금형에 매우 적합한 소재로 SKD6 강재를 성공적으로 식별했습니다. FCD550과 비교하여 SKD6은 우수한 열충격 저항성을 보여 균열 형성을 12% 감소시키고 내구성을 0.5% 증가시켰습니다. 이 소재의 향상된 내열성, 인성 및 내식성은 열충격으로 인한 균열이라는 중요한 문제를 해결하여 금형 제조에서 더 높은 정밀도와 내구성을 보장합니다. 이는 신뢰할 수 있는 고품질 자동차 부품 생산에 높은 엔지니어링 표준의 중요성을 강조합니다.
- 고급 냉각 시스템이 효과적으로 설계되어 금형 내 균일한 온도 분포를 보장하고 열응력을 완화했습니다. 이 설계는 열 구배를 23% 감소시키고 제품 치수 정확도를 100% 개선했습니다. 연구 결과, 냉각 시스템 설계의 세심한 계획과 계산이 금형 균열 문제를 선제적으로 해결하여 제품이 설계 사양에 따라 정확하게 형성되고 무결성을 유지하도록 보장할 수 있음을 입증했습니다.
- 본 연구는 사출 속도, 금형 온도 및 냉각 속도를 포함한 최적화된 다이캐스팅 기계 매개변수를 달성하여 생산을 15% 가속화하고 불량률을 100% 감소시켰습니다. 엄격한 실험 데이터를 기반으로 한 이러한 최적화는 생산성 향상이 제품 품질을 저하시키지 않도록 보장했습니다. 이 전략적 접근 방식은 기계 설정을 제품 표준 및 고객 기대치에 맞춰 최종적으로 생산물의 품질과 양을 모두 향상시킵니다.
8. 참고문헌:
- [References] - (참고문헌 목록은 원본 영어 버전과 동일하게 유지됩니다.)
- [1] Wankhede, V. A., Vinodh, S. (2022). State of the art review on Industry 4.0 in manufacturing with the focus on automotive sector. International Journal of Lean Six Sigma, 13 (3), 692–732. Available at: https://www.x-mol.net/paper/article/1451642237902290944
- [2] Zhao, X., Gao, P., Zhang, Z., Wang, Q., Yan, F. (2020). Fatigue characteristics of the extruded AZ80 automotive wheel. International Journal of Fatigue, 132, 105393. https://doi.org/10.1016/j.ijfatigue.2019.105393
- [3] Klobčar, D., Kosec, L., Kosec, B., Tušek, J. (2012). Thermo fatigue cracking of die casting dies. Engineering Failure Analysis, 20, 43–53. https://doi.org/10.1016/j.engfailanal.2011.10.005
- [4] Schwam, D., Wallace, J., Birceanu, S. (2002). Die Materials for Critical Applications and Increased Production Rates. Office of Scientific and Technical Information (OSTI). https://doi.org/10.2172/806823
- [5] Su, Y., Fu, G., Liu, C., Liu, C., Long, X. (2021). Fatigue crack evolution and effect analysis of Ag sintering die-attachment in SiC power devices under power cycling based on phase-field simulation. Microelectronics Reliability, 126, 114244. https://doi.org/10.1016/j.microrel.2021.114244
- [6] Cai, H., Wang, Z., Liu, L., Li, Y., Xing, F., Guo, F. (2022). Crack source and propagation of AZ91-0.9Gd alloy. Journal of Materials Research and Technology, 16, 1571–1577. https://doi.org/10.1016/j.jmrt.2021.12.065
- [7] Schumacher, O., Marvel, C. J., Kelly, M. N., Cantwell, P. R., Vinci, R. P., Rickman, J. M. et al. (2016). Complexion time-temperature-transformation (TTT) diagrams: Opportunities and challenges. Current Opinion in Solid State and Materials Science, 20 (5), 316–323. https://doi.org/10.1016/j.cossms.2016.05.004
- [8] Lordan, E., Zhang, Y., Dou, K., Jacot, A., Tzileroglou, C., Wang, S. et al. (2022). High-Pressure Die Casting: A Review of Progress from the EPSRC Future LIME Hub. Metals, 12 (10), 1575. https://doi.org/10.3390/met12101575
- [9] Luthfiyah, S., Faridh, A., Soegijono, B. (2019). The Effect of Vacuum Quenching on Corrosion and Hardness of the Surface of SKD61 Steel. IOP Conference Series: Materials Science and Engineering, 694 (1), 012033. https://doi.org/10.1088/1757-899x/694/1/012033
- [10] Sudjadi, U., Sinaga, R. V. (2020). Study of the hardness and microstructure profiles of SKD61 steel plunger tip (local material) after plasma nitriding. IOP Conference Series: Materials Science and Engineering, 839 (1), 012019. https://doi.org/10.1088/1757-899x/839/1/012019
- [11] Yi, W., Liu, G., Gao, J., Zhang, L. (2021). Boosting for concept design of casting aluminum alloys driven by combining computational thermodynamics and machine learning techniques. Journal of Materials Informatics. https://doi.org/10.20517/jmi.2021.10
- [12] Walsh, E., Maclean, N., Turner, A., Alsuleman, M., Prasad, E., Halbert, G. et al. (2022). Manufacture of tablets with structurally-controlled drug release using rapid tooling injection moulding. International Journal of Pharmaceutics, 624, 121956. https://doi.org/10.1016/j.ijpharm.2022.121956
- [13] Yang, Q., Wu, X., Qiu, X. (2023). Microstructural Characteristics of High-Pressure Die Casting with High Strength–Ductility Synergy Properties: A Review. Materials, 16 (5), 1954. https://doi.org/10.3390/ma16051954
- [14] Zhou, Y., Tian, N., Liu, W., Zeng, Y., Wang, G., Han, S. et al. (2022). Mechanism of heterogeneous distribution of Cr-containing dispersoids in DC casting 7475 aluminum alloy. Transactions of Nonferrous Metals Society of China, 32 (5), 1416–1427. https://doi.org/10.1016/s1003-6326(22)65883-7
- [15] Wei, C., Ou, J., Farhang Mehr, F., Maijer, D., Cockcroft, S., Wang, X. et al. (2021). A thermal-stress modelling methodology in ABAQUS for fundamentally describing the die/casting interface behaviour in a cyclic permanent die casting process. Journal of Materials Research and Technology, 15, 5252–5264. https://doi.org/10.1016/j.jmrt.2021.10.120
- [16] Campos Neto, N. D., Korenyi-Both, A. L., Vian, C., Midson, S. P., Kaufman, M. J. (2023). The development of coating selection criteria to minimize die failure by soldering and erosion during aluminum high pressure die casting. Journal of Materials Processing Technology, 316, 117954. https://doi.org/10.1016/j.jmatprotec.2023.117954
- [17] Ahmadein, M., Elsheikh, A. H., Alsaleh, N. A. (2022). Modeling of cooling and heat conduction in permanent mold casting process. Alexandria Engineering Journal, 61 (2), 1757–1768. https://doi.org/10.1016/j.aej.2021.06.048
- [18] Niu, Z., Liu, G., Li, T., Ji, S. (2022). Effect of high pressure die casting on the castability, defects and mechanical properties of aluminium alloys in extra-large thin-wall castings. Journal of Materials Processing Technology, 303, 117525. https://doi.org/10.1016/j.jmatprotec.2022.117525
- [19] Li, Z., Li, D., Zhou, W., Hu, B., Zhao, X., Wang, J. et al. (2022). Characterization on the formation of porosity and tensile properties prediction in die casting Mg alloys. Journal of Magnesium and Alloys, 10 (7), 1857–1867. https://doi.org/10.1016/j.jma.2020.12.006
- [20] Dudek, P., Białoń, J., Piwowońska, J., Walczak, W., Wrzała, K. (2023). The impact on the cost of making high pressure die castings with multi-cavity die and vacuum assistance. Vacuum, 210, 111859. https://doi.org/10.1016/j.vacuum.2023.111859
9. 저작권:
- 이 자료는 "Herry Patria, Iwan Susanto, Belyamin, Dianta Mustofa Kamal"의 논문입니다. "Enhancing side die resistance to thermal shock in automotive casting: a comparative study of FCD550 and SKD6 materials" 논문을 기반으로 합니다.
- 논문 출처: https://doi.org/10.15587/1729-4061.2024.306615
이 자료는 위 논문을 바탕으로 요약되었으며, 상업적 목적의 무단 사용을 금합니다.
Copyright © 2025 CASTMAN. All rights reserved.