본 논문 요약은 "Phase-Field Modelling of Bimodal Dendritic Solidification During Al Alloy Die Casting"을 기반으로 작성되었으며, Metals 저널에 게재되었습니다.
1. 개요:
제목: 알루미늄 합금 다이캐스팅 중 이봉형 수지상 응고의 Phase-Field 모델링 (Phase-Field Modelling of Bimodal Dendritic Solidification During Al Alloy Die Casting)
저자: 마리암 토르페(Maryam Torfeh), 지차오 니우(Zhichao Niu), 하미드 아싸디(Hamid Assadi)
발행 연도: 2025년
발행 저널: Metals
키워드: Phase-Field 모델링(phase-field modelling); HPDC; 계면 거동(interface behaviour)
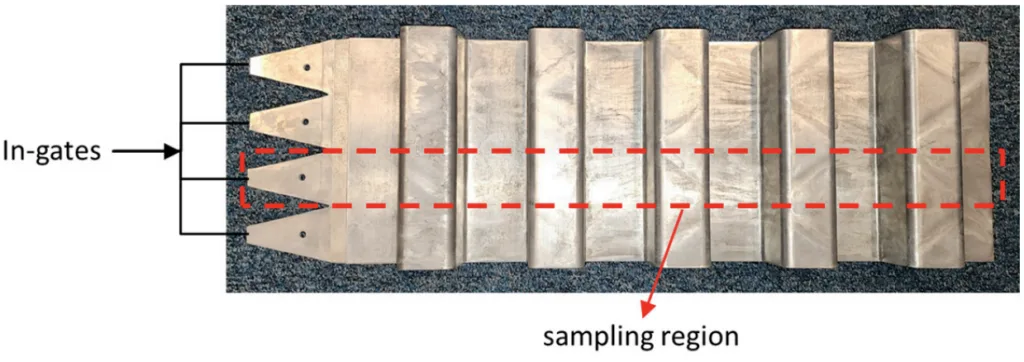
2. 연구 배경:
고압 다이캐스팅(HPDC)은 경량 알루미늄 합금으로 정밀 형상 부품을 경제적으로 제조하는 방법입니다. HPDC 제품의 최종 품질은 여러 공정 요인에 의해 근본적으로 영향을 받을 수 있습니다. 특히 긴 유동 경로로 인해 균일한 미세 구조를 유지하기 어려운 대형 HPDC 부품에서 원하는 기계적 특성을 얻기 위해서는 미세 구조를 이해하고 제어하는 것이 가장 중요합니다.
그러나 HPDC에서 응고 역학을 추적하는 것은 빠른 응고 속도, 변화하는 열 조건 및 심한 난류로 인해 본질적으로 복잡합니다. 수치 시뮬레이션이 주조 설계 및 공정 매개변수를 최적화하는 데 유용한 도구가 되었지만, 기존 연구의 대부분은 주로 유한 요소법(FEM)을 사용하여 유체 역학 및 열 전달에 초점을 맞추고 있습니다. 미세 구조 진화를 예측하는 것은 보다 최근의 초점이며, 일반적으로 FEM과 셀룰러 오토마타(CA)를 결합합니다. 응고 모델링에 강력한 기술인 상-장 방법은 HPDC 맥락에서 충분히 활용되지 못했습니다. 따라서 급속 응고 조건에서 복잡한 미세 구조 형성에 대한 더 깊은 통찰력을 얻기 위해 상-장 방법과 같은 고급 모델링 기술을 사용하여 HPDC에서 수지상 구조 진화를 조사할 필요성이 분명히 있습니다.
3. 연구 목적 및 연구 질문:
연구 목적:
본 연구는 상-장 모델링을 사용하여 고압 다이캐스팅(HPDC) 중 수지상 구조의 진화를 분석하는 것을 목표로 합니다. 주요 목표는 HPDC의 급속 응고 조건이 이봉형 수지상 미세 구조 형성에 어떻게 기여하는지 이해하는 것입니다.
주요 연구 질문:
본 연구는 다음과 같은 주요 질문에 답하고자 합니다.
- 2차원 상-장 모델은 Al-Si 합금의 HPDC에서 관찰되는 이봉형 수지상 응고 과정을 효과적으로 시뮬레이션할 수 있는가?
- 숏 슬리브에서 다이캐비티로의 전환을 반영하는 고체-액체 계면 특성의 변화는 상-장 모델에서 수지상 형태에 어떤 영향을 미치는가?
연구 가설:
명시적으로 가설로 제시되지는 않았지만, 본 연구는 상-장 모델 내에서 고체-액체 계면 특성을 체계적으로 변화시킴으로써 HPDC 중에 발생하는 미세 구조 전환, 특히 숏 슬리브에서의 느린 냉각에서 다이캐비티에서의 급속 냉각으로의 전환으로 인한 이봉형 수지상 구조 형성을 재현할 수 있다는 전제하에 진행됩니다.
4. 연구 방법론
연구 설계:
본 연구에서는 수지상 응고를 시뮬레이션하기 위해 2차원 상-장 모델을 사용했습니다. 이 모델은 상 변환열, 열 경계 조건, 액체 및 고체 상 모두에서의 용질 확산으로 인한 온도 변화를 고려하도록 열역학적으로 공식화되었습니다.
자료 수집 방법:
본 연구는 실험적 미세 구조 분석과 수치 시뮬레이션을 모두 포함했습니다.
- 미세 구조 연구: 16,000 KN 냉챔버 HPDC 기계로 생산된 아공정 Al-7% Si 합금 주조물을 미세 구조 평가에 사용했습니다. 샘플은 리브 플레이트 주조물의 서로 다른 위치에서 채취했습니다. 미세 구조는 연마, 광택, 양극 산화 등 표준 금속학적 준비 후 광학 현미경을 사용하여 관찰했습니다.
- 수치 시뮬레이션: 상-장 시뮬레이션은 HPDC의 숏 슬리브 및 다이캐비티 단계의 조건을 대표하는 조건에서 수지상 성장을 모델링하기 위해 수행되었습니다.
분석 방법:
- 미세 현미경 관찰: 광학 현미경을 사용하여 HPDC 주조물의 서로 다른 위치에서 α-Al 입자 크기 분포 및 편석 밴드 형성을 분석했습니다.
- 상-장 모델링: 상-장 모델은 숏 슬리브에서 다이캐비티 조건으로의 전환을 모방하기 위해 고체-액체 계면 특성(두께, 에너지 및 이동성)을 다양하게 변화시켜 수지상 응고를 시뮬레이션하는 데 사용되었습니다.
연구 대상 및 범위:
본 연구는 HPDC 중 아공정 Al-7% Si 합금(Al-7% Si)의 응고 거동에 초점을 맞췄습니다. 시뮬레이션 영역은 500 × 500 셀 그리드를 사용하는 2차원이었습니다. 본 연구는 HPDC의 숏 슬리브 및 다이캐비티 단계 모두에서 수지상 응고 과정을 조사했습니다.
5. 주요 연구 결과:
주요 연구 결과:
상-장 모델은 다음 능력을 성공적으로 입증했습니다.
- 숏 슬리브 냉각 조건에서 수지상 성장을 포착합니다.
- 다이캐비티의 특징인 급속 냉각 조건에서 새로운 수지상 가지의 핵 생성 및 발달을 시뮬레이션합니다.
- 숏 슬리브에서 다이캐비티로의 전환을 반영하기 위해 고체-액체 계면 특성을 조정하여 관찰된 이봉형 미세 구조를 재현합니다.
통계적/정성적 분석 결과:
- 미세 구조 관찰: 주조 미세 구조 분석 결과, 잉게이트에서 플레이트 끝단으로 이동함에 따라 평균 α-Al 입자 크기가 점진적으로 감소하는 것으로 나타났습니다. 특히 평균 크기는 잉게이트 근처(샘플 1)에서 약 21 µm에서 먼 끝단(샘플 7)에서 약 3 µm로 감소했습니다. 그림 3은 플레이트 중간 부분과 그 이후 부분에서 α-Al 입자의 약 70%가 0–10 µm 크기 범위에 속하여 잉게이트 영역에 비해 더 미세하고 균일한 입자 분포를 나타내는 것을 보여줍니다.
- 편석 밴드: 편석 밴드는 주조물 끝단으로 갈수록 더욱 두드러지게 나타났으며, 이는 주조 길이 방향으로 용질 분포의 변화를 나타냅니다.
데이터 해석:
HPDC 주조물에서 관찰된 이봉형 미세 구조는 숏 슬리브에서 외부 응고 결정(ESC)이 형성된 후, 급속 냉각 조건의 다이캐비티에 진입할 때 이러한 파편화된 ESC에서 새로운 미세 수지상 가지가 핵 생성 및 성장한 것에 기인합니다. 상-장 모델은 계면 특성을 조정하여 이러한 전환을 효과적으로 포착하여 모델이 응고 조건 변화에 민감함을 입증했습니다.
그림 목록:
- 그림 1. HPDC로 제조된 플레이트의 샘플링 영역.
- 그림 2. 플레이트를 따라 7개 샘플링 위치(S1-S7)에서의 미세 구조 진화, (a) 붉은색 화살표로 표시된 플레이트 마지막 1/3 지점에서 편석 밴드 출현, (b) α-Al 입자 비교.
- 그림 3. 플레이트를 따른 α-Al 입자의 크기 분포.
- 그림 4. 플레이트를 따른 α-Al 입자 비교, (a) 및 (b) 잉게이트 근처, (c) 플레이트 끝단 (화살표는 파편화된 수지상 가지에서 핵 생성된 새로운 가지를 나타냄).
- 그림 5. (a) 잉게이트에서 외부 응고 결정, (b,c) 2ms 후 숏 슬리브에서 수지상 가지의 상-장 및 Si 농도, (d,e) 15ms 후.
- 그림 6. 2ms 동안 숏 슬리브에서 성장하고 다이캐비티로 옮겨진 수지상 가지에서 2차 핵 생성 비교 (상태 1-3은 700-500nm의 계면 두께를 나타냄).
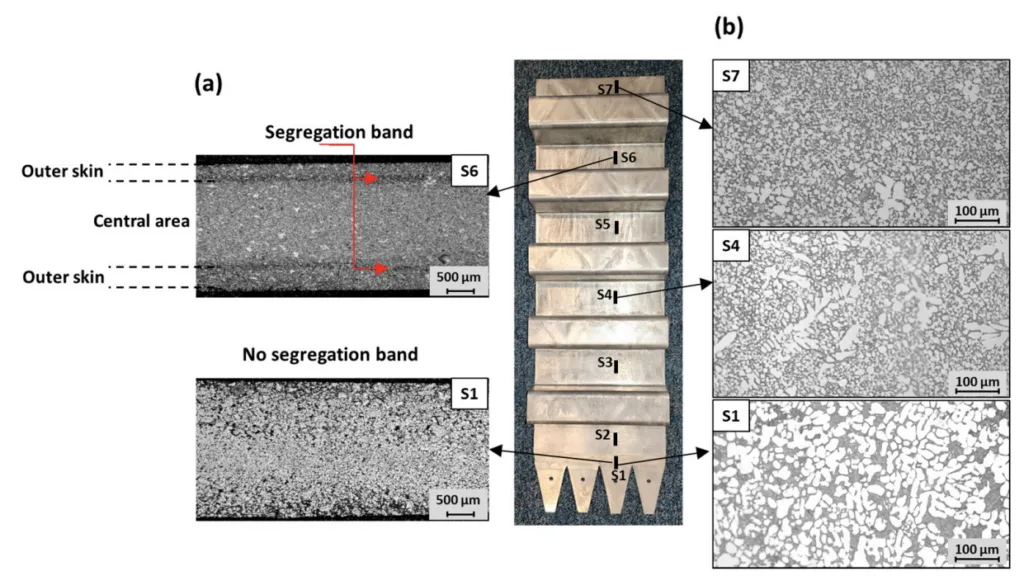
segregation band at last one-third of the plate shown by red arrows, (b) comparison of α-Al particles.
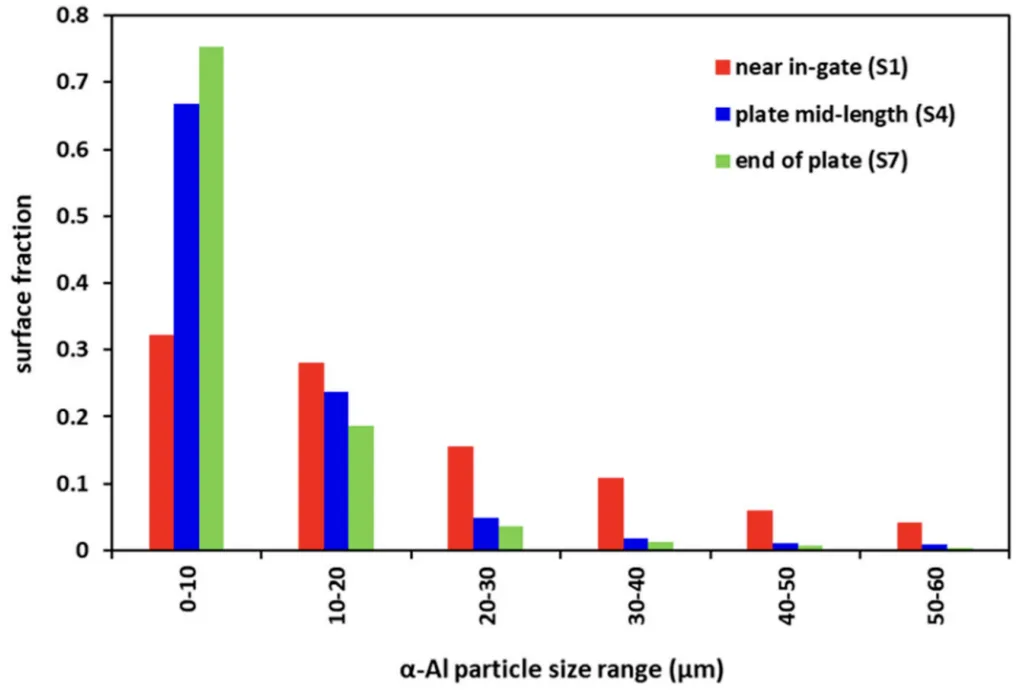
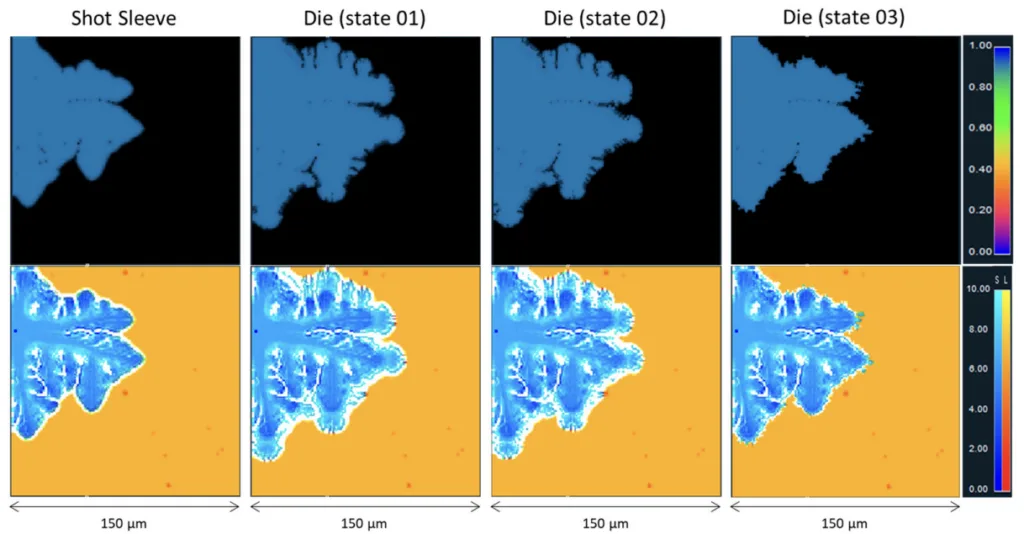
6. 결론 및 논의:
주요 결과 요약:
본 연구는 상-장 모델링을 성공적으로 사용하여 Al-Si 합금의 HPDC 중 이봉형 수지상 응고를 시뮬레이션했습니다. 이 모델은 숏 슬리브에서 다이캐비티로의 변화하는 조건을 나타내기 위해 고체-액체 계면 특성을 체계적으로 변화시켜 난류 유도 파편화 및 후속적인 새로운 수지상 가지의 핵 생성을 효과적으로 포착했습니다.
연구의 학문적 의의:
본 연구는 복잡한 HPDC 공정 내에서 수지상 응고에 대한 난류의 역할에 대한 귀중한 학문적 통찰력을 제공합니다. 다이캐스팅에서 관찰되는 복잡한 미세 구조 현상을 재현하는 데 상-장 모델링 접근 방식의 유용성을 입증합니다.
실용적 의미:
본 연구 결과는 HPDC의 공정별 조건을 정확하게 나타내기 위해 상-장 모델에서 계면 특성을 조정하는 것이 매우 중요하다는 점을 강조합니다. 이는 HPDC 공정의 추가 최적화와 Al-Si 합금 주조물의 미세 구조 제어 개선을 위한 경로를 제공하여 잠재적으로 기계적 특성 및 부품 성능 향상으로 이어질 수 있습니다.
연구의 한계:
상-장 모델은 수지상 응고의 주요 측면을 효과적으로 포착했지만, 주로 응고 현상에 초점을 맞췄습니다. 난류의 영향은 고체-액체 계면 두께 조정을 통해 간접적으로 추론되었습니다. 난류 효과를 모델에 보다 직접적으로 통합하면 정확성과 예측 능력을 더욱 향상시킬 수 있습니다.
7. 향후 후속 연구:
후속 연구 방향:
향후 연구는 다음 사항에 초점을 맞춰야 합니다.
- 시뮬레이션 정확도를 높이기 위해 상-장 모델 내에 난류 효과를 보다 직접적으로 표현하는 것을 통합합니다.
- 주입 속도, 다이 온도, 가압력과 같은 더 넓은 범위의 HPDC 공정 매개변수를 탐색하기 위해 모델을 확장합니다.
- 개발된 상-장 모델링 접근 방식을 사용하여 다양한 Al-Si 합금 조성의 응고 거동을 조사합니다.
추가 탐구가 필요한 영역:
HPDC의 복잡한 조건, 특히 난류 및 급속 냉각이 계면 특성 및 미세 구조 형성에 미치는 영향 하에서 수지상 진화를 지배하는 운동론적 및 열역학적 요인 간의 상호 작용에 대한 이해를 심화하기 위한 추가 탐구가 필요합니다.
8. 참고 문헌:
- [1] Han, Q.; Zhang, J. Fluidity of Alloys Under High-Pressure Die Casting Conditions: Flow-Choking Mechanisms. Metall. Mater. Trans. B 2020, 51, 1795-1804.
- [2] Mednanský, M.; Bruna, M.; Matejka, M. Electromotor Housing Microstructure Dependence on HPDC Process Parameters. Transp. Res. Procedia 2023, 74, 680-687.
- [3] Niu, Z.; Liu, G.; Li, T.; Ji, S. Effect of High Pressure Die Casting on the Castability, Defects, and Mechanical Properties of Aluminium Alloys in Extra-Large Thin-Wall Castings. J. Mater. Process. Technol. 2022, 303, 117525.
- [4] Zhu, X.; Dong, X.; Blake, P.; Ji, S. Improvement in As-Cast Strength of High-Pressure Die-Cast Al-Si-Cu-Mg Alloys by Synergistic Effect of Q-Al5Cu2Mg8Si6 and 0-Al2Cu Phases. Mater. Sci. Eng. A 2021, 802, 140612.
- [5] Laukli, H.I.; Gourlay, C.M.; Dahle, A.K.; Lohne, O. Effects of Si Content on Defect Band Formation in Hypoeutectic Al-Si Die Castings. Mater. Sci. Eng. A 2005, 413–414, 92-97.
- [6] Helenius, R.; Lohne, O.; Arnberg, L.; Laukli, H.I. The Heat Transfer during Filling of a High-Pressure Die-Casting Shot Sleeve. Mater. Sci. Eng. A 2005, 413, 52-55.
- [7] Ji, S.; Wang, Y.; Watson, D.; Fan, Z. Microstructural Characteristics of Diecast AlMgSiMn Alloy. Mater. Sci. Forum 2014, 783, 234-239.
- [8] Zheng, H.; Jiang, Y.; Liu, F.; Zhao, H. Synergistic Effect of Externally Solidified Crystals and Fe-Rich Intermetallic on the Fracture Behavior of HPDC Alloy. J. Mater. Res. Technol. 2023, 27, 2822-2832.
- [9] Xie, H.; Wang, J.; Li, Y.; Song, J.; Hu, H.; Qin, L.; Zhao, H.; Li, C.; Cui, Y.; Tan, Z.; et al. Fast Shot Speed Induced Microstructure and Mechanical Property Evolution of High-Pressure Die Casting Mg-Al-Zn-RE Alloys. J. Mater. Process. Technol. 2024, 331, 118523.
- [10] Li, J.; Yu, W.; Sun, Z.; Zheng, W.; Zhang, L.; Xue, Y.; Liu, W.; Xiong, S. Influence of Introducing Zr, Ti, Nb and Ce Elements on Externally Solidified Crystals and Mechanical Properties of High-Pressure Die-Casting Al–Si Alloy. Int. J. Miner. Metall. Mater. 2025, 32, 147-153.
- [11] Zhu, X.; Yang, H.; Dong, X.; Ji, S. The Effects of Varying Mg and Si Levels on the Microstructural Inhomogeneity and Eutectic Mg2Si Morphology in Die-Cast Al-Mg-Si Alloys. J. Mater. Sci. 2019, 54, 5773–5787.
- [12] Yang, Q.; Wu, X.; Qiu, X. Microstructural Characteristics of High-Pressure Die Casting with High Strength-Ductility Synergy Properties: A Review. Materials 2023, 16, 1954.
- [13] Gu, C.; Lu, Y.; Cinkilic, E.; Miao, J.; Klarner, A.; Yan, X.; Luo, A.A. Predicting Grain Structure in High-Pressure Die Casting of Aluminum Alloys: A Coupled Cellular Automaton and Process Model. Comput. Mater. Sci. 2019, 161, 64-75.
- [14] El-Mahallawy, N.A.; Taha, M.A.; Pokora, E.; Klein, F. On the influence of process variables on the thermal conditions and properties of high pressure die-cast magnesium alloys. J. Mater. Process. Technol. 1998, 73, 125-138.
- [15] Kwon, H.J.; Kwon, H.K. Computer aided engineering (CAE) simulation for the design optimization of gate system on high pressure die casting (HPDC) process. Robot. Comput.-Integr. Manuf. 2019, 55, 147-153.
- [16] Sharifi, P.; Jamali, J.; Sadayappan, K.; Wood, J.T. Grain size distribution and interfacial heat transfer coefficient during solidification of magnesium alloys using high pressure die casting process. J. Mater. Sci. Technol. 2018, 34, 324-334.
- [17] Dou, K.; Lordan, E.; Zhang, Y.J.; Jacot, A.; Fan, Z.Y. A complete computer aided engineering (CAE) modelling and optimization of high pressure die casting (HPDC) process. J. Manuf. Process. 2020, 60, 435-446.
- [18] Assadi, H. A Phase-Field Model for Non-Equilibrium Solidification of Intermetallics. Acta Mater. 2007, 55, 5225-5235.
- [19] Li, B.; Xu, Q.Y.; Liu, B.C. Numerical Modeling of Microstructure Evolution and Dendrite Growth for Al-Si Alloy Casting during Low Pressure Die Casting. Mater. Sci. Forum 2007, 561–565, 1787-1792.
- [20] Belov, N.A.; Eskin, D.G.; Aksenov, A.A. Multicomponent Phase Diagrams: Applications for Commercial Aluminum Alloys; Elsevier: Amsterdam, The Netherlands, 2005; p. 48.
- [21] Dey, A.K.; Poddar, P.; Singh, K.K.; Sahoo, K.L. Mechanical and Wear Properties of Rheocast and Conventional Gravity Die Cast A356 Alloy. Mater. Sci. Eng. A 2006, 435-436, 521-529.
- [22] Zheng, H.; Jiang, Y.; Liu, F.; Zhao, H. Microstructure Heterogeneity Optimization of HPDC Al-Si-Mg-Cu Alloys by Modifying the Characteristic of Externally Solidified Crystals. J. Alloys Compd. 2024, 976, 173167.
- [23] Otarawanna, S.; Gourlay, C.M.; Laukli, H.I.; Dahle, A.K. Microstructure Formation in High Pressure Die Casting. Trans. Indian Inst. Met. 2009, 62, 499-503.
- [24] Laukli, H.I.; Gourlay, C.M.; Dahle, A.K. Migration of Crystals during the Filling of Semi-Solid Castings. Metall. Mater. Trans. A 2005, 36, 805-818.
- [25] Hao, Y.Z.; Zhao, H.D.; Shen, X.; Wang, X.L.; Zheng, H.T. Simulation of a-Al Grain Formation in High Vacuum Die-Casting Al-Si-Mg Alloys with Multi-Component Quantitative Cellular Automaton Method. China Foundry 2022, 19, 99–108.
- [26] Han, Q.; Xu, H. Fluidity of Alloys under High Pressure Die Casting Conditions. Scr. Mater. 2005, 53, 7-10.
- [27] Reyes, A.E.S.; Guerrero, G.A.; Ortiz, G.R.; Gasga, J.R.; Robledo, J.F.G.; Flores, O.L.; Costa, P.S. Microstructural, Microscratch and Nanohardness Mechanical Characterization of Secondary Commercial HPDC AlSi9Cu3-Type Alloy. J. Mater. Res. Technol. 2020, 9, 8266-8282.
- [28] Zhang, H.; Li, D.; Wang, Q.; Fan, Z.; Luo, M.; Midson, S.P.; Zhu, Q. Effect of Primary a-Al Morphology in Slurry on Segregation during 357 Semi-Solid Die Casting. Solid State Phenom. 2019, 285, 398-402.
- [29] Gourlay, C.M.; Laukli, H.I.; Dahle, A.K. Segregation Band Formation in Al-Si Die Castings. Metall. Mater. Trans. A 2004, 35, 2881-2891.
9. 저작권:
*본 자료는 마리암 토르페, 지차오 니우, 하미드 아싸디의 논문 "Phase-Field Modelling of Bimodal Dendritic Solidification During Al Alloy Die Casting"을 기반으로 합니다.
*논문 출처: https://doi.org/10.3390/met15010066
본 자료는 상기 논문을 기반으로 요약되었으며, 상업적 목적으로 무단 사용하는 것을 금지합니다.
Copyright © 2025 CASTMAN. All rights reserved.