이 소개 자료는 "[ARCHIVES of FOUNDRY ENGINEERING]"에 게재된 논문 "[Anodization of cast aluminium alloys produced by different casting methods]"을 기반으로 합니다.
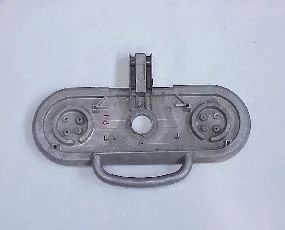
1. 개요:
- 제목: Anodization of cast aluminium alloys produced by different casting methods (다른 주조 방법으로 생산된 주조 알루미늄 합금의 아노다이징)
- 저자: K. Labisz, L.A. Dobrzański, J. Konieczny
- 발행 연도: 2008
- 게재 학술지/학회: ARCHIVES of FOUNDRY ENGINEERING (Published quarterly as the organ of the Foundry Commission of the Polish Academy of Sciences)
- 키워드: Aluminium cast alloys, Mechanical properties, Surface treatment, Alumina layer, Anodization (알루미늄 주조 합금, 기계적 성질, 표면 처리, 알루미나 층, 아노다이징)
2. 초록 (Abstract):
본 논문에서는 AlSi12 및 AlSi9Cu3 알루미늄 주조 합금의 아노다이징을 위해 사형 주조 및 고압 주조라는 두 가지 주조 방법의 유용성을 조사했습니다. 전해액 조성 및 온도, 전류 유형 및 값과 같은 정의된 아노다이징 파라미터를 사용하여 양극 산화 알루미나 표면층을 생성했습니다. 선택된 알루미늄 주조 합금의 아노다이징 후 양극 산화층의 품질, 크기 및 특성을 조사했습니다. 알루미나 층은 광학 현미경을 사용하여 관찰했으며, 기계적 특성 측정과 ABR-8251 장비를 사용한 마모 테스트도 수행했습니다. 연구에는 알루미늄 주물에 얻어진 양극 산화층의 화학적 조성, 형상 및 거칠기의 영향 분석이 포함되었습니다. 수행된 조사는 향후 연구 분야, 특히 알루미늄 주조 합금의 아노다이징 공정 최적화 방향을 보여줍니다. 예를 들어, 작업 중인 건물 구조물, 전자 제품 요소, 항공 및 자동차 산업의 건설 부품과 같은 공격적인 환경에서의 적용을 늘리기 위해 요소의 내식성을 높여 적합한 양극 표면층을 얻는 범위입니다.
3. 서론 (Introduction):
환경 조건에서 알루미늄 부품 표면은 자연적으로 얇은 알루미나 Al2O3 층으로 덮입니다. 이 층의 두께는 재료, 환경, 노출 시간에 따라 수십 나노미터 정도입니다. 적절한 아노다이징 기술을 선택하면 층의 두께를 수 마이크로미터 값까지 증가시킬 수 있습니다. 이 방법을 사용하면 표면이 염수, 산성 용액 또는 외부 기계적 영향과 같은 환경 요인에 대해 더 높은 저항성을 갖게 됩니다. 아노다이징은 알루미늄 합금 부품의 부식 방지에 일반적으로 사용되며, 따라서 양극 표면층의 특성과 품질을 결정하기 위한 ISO 7599 및 DIN 17611과 같은 국제 표준이 존재합니다. 재료 공학의 발전으로 구조용 및 공구용 금속 재료의 강도 관련 문제를 만족스럽게 해결할 수 있게 되었습니다. 지난 몇 년간 다양한 산업 분야에서 알루미늄 합금 사용이 지속적으로 증가하고 있으며, 알루미늄 및 그 합금, 알루미늄 매트릭스 복합재료 생산 기술 개발이 많은 과학 기관에서 관찰되었습니다 [6-9]. 양극 산화층은 알루미늄 전자 부품, 가정용품, 기구 부품, 정원 가구, 관광 및 스포츠 장비, 자동차 액세서리 및 알루미늄 목공 요소에 적용되어 보호 및 장식 기능을 합니다. 산화물 층은 콘덴서의 전극용 알루미늄 포일에도 생성됩니다. 경질 양극 산화층은 항공 및 자동차 산업에 적용될 수 있습니다 [10-12]. 그러나 음극 부위로 작용하는 구리의 금속간 화합물의 존재는 구리 함유 알루미늄 합금을 부식 공격에 더 취약하게 만듭니다. 높은 구리 함량은 알루미늄 합금을 아노다이징하기 가장 어려운 합금 중 하나로 만듭니다. 두꺼운 양극 산화 피막 생산은 경질 아노다이징 조건 하에서만 가능하며, 이 합금은 국부적 소손(burning)에 쉽게 영향을 받습니다. 두꺼운 다공성 산화물이 생성될 때 Al-Cu 합금의 아노다이징 공정 중 산소 발생으로 인한 피막 균열도 관찰됩니다. 이 합금의 특정 특징은 합금/피막 계면에서 상대적으로 좁은 구리 농축 영역이 형성된 후 아노다이징 중에 구리의 산화가 일어난다는 것입니다. 이는 피막 형성 중 전류 효율 감소를 초래합니다. 이 감소는 구리가 풍부한 영역 위의 산소 발생에도 기인하며, 확립된 구리 부식 억제제가 전류 효율을 개선하는 데 사용되었습니다 [13-16].
4. 연구 요약 (Summary of the study):
연구 주제 배경 (Background of the research topic):
아노다이징은 알루미늄 합금의 중요한 표면 처리 기술로, 내식성 및 내마모성을 향상시킵니다. 생성된 양극 산화층의 특성은 합금 조성, 제조 공정(주조 방법), 아노다이징 파라미터에 따라 달라집니다. 합금 내 구리 함량은 아노다이징 공정을 복잡하게 만들 수 있습니다.
기존 연구 현황 (Status of previous research):
아노다이징은 기존 국제 표준과 알려진 응용 분야를 갖춘 잘 확립된 공정입니다. 이전 연구들에서는 합금 종류, 아노다이징 파라미터(전해액, 전류, 온도)의 영향 및 특정 합금 조성(예: 높은 구리 함량)과 관련된 문제점들이 결과적인 양극 산화층의 특성 및 형성 메커니즘에 미치는 영향에 대해 조사해왔습니다 [1-16].
연구 목적 (Purpose of the study):
AlSi12 및 AlSi9Cu3 알루미늄 주조 합금의 아노다이징을 위해 사형 주조와 고압 다이캐스팅이라는 두 가지 다른 주조 방법의 유용성을 조사하는 것입니다. 본 연구는 형성된 알루미나 층의 구조와 두께를 검사하고, 주조 방법이 결과적인 양극 산화층에 미치는 영향을 비교하는 것을 목표로 했습니다.
핵심 연구 (Core study):
두 가지 알루미늄 합금, EN AC-AlSi12(b) 및 EN AC-AlSi9Cu3(Fe)를 고압 주조와 사형 주조 방법을 사용하여 생산했습니다. 이 주조 샘플들을 특정하게 정의된 파라미터(H2SO4 전해액, 제어된 온도 및 펄스 전류) 하에서 아노다이징 공정에 적용했습니다. 결과적인 양극 산화 알루미나 층은 광학 현미경을 사용하여 구조와 균일성을 평가하고 두께를 측정했습니다. 마모 저항성은 표준화된 테스트(ISO 8251)를 사용하여 질량 손실을 측정함으로써 평가되었으며, 아노다이징된 샘플을 아노다이징되지 않은 샘플과 비교했습니다.
5. 연구 방법론 (Research Methodology)
연구 설계 (Research Design):
비교 실험 연구를 수행했습니다. 두 가지 일반적인 주조 알루미늄 합금(AlSi12, AlSi9Cu3)을 두 가지 다른 주조 방법(사형 주조, 고압 주조)을 사용하여 준비했습니다. 각 그룹의 샘플을 동일하고 제어된 조건에서 아노다이징했습니다. 결과적인 표면층은 미세 구조, 두께 및 마모 저항성을 기준으로 분석하고 비교했습니다. 아노다이징되지 않은 샘플은 마모 비교의 기준선으로 사용되었습니다.
데이터 수집 및 분석 방법 (Data Collection and Analysis Methods):
- 재료 준비: 표준 금속 조직학적 절차를 사용하여 샘플 절단, 마운팅, 연삭 및 연마.
- 아노다이징: H2SO4 전해액, 특정 온도 범위(-4 ~ 2°C) 및 정의된 펄스 전류 체제(표 2)를 사용하여 수행.
- 미세 구조 조사: 광학 현미경(Olympus BX60M)을 사용하여 500-1000배 배율로 양극 산화층 구조 및 기본 합금 미세 구조 관찰.
- 층 두께 측정: 현미경 사진으로부터 평가 (결과는 그림 6에 제시됨).
- 마모 테스트: ISO 8251 표준에 따라 ABR-8251 테스터를 사용하여 수행. 4.9N 하중 하에서 400 스텝 후 질량 손실 [mg] 측정 (표 3). 제어된 조건 하에서 5회 반복 테스트 (표 4).
- 초기 표면 형상: MicroProf 레이저 게이지를 사용한 분석이 언급되었으나 결과 토론에서는 자세히 다루지 않음.
연구 주제 및 범위 (Research Topics and Scope):
이 연구는 주로 주조 방법(사형 주조 대 고압 주조)이 AlSi12 및 AlSi9Cu3 주조 합금의 아노다이징 가능성 및 결과 특성(층 구조, 두께, 균일성, 내마모성)에 미치는 영향에 초점을 맞췄습니다. 범위는 상세히 기술된 특정 합금, 주조 방법 및 아노다이징 파라미터로 제한되었습니다 (표 1 & 2).
6. 주요 결과 (Key Results):
주요 결과 (Key Results):
- 고압 주조 및 사형 주조 방법으로 주조된 AlSi12 및 AlSi9Cu3 합금 모두에 양극 산화 알루미나 층이 성공적으로 생성되었습니다.
- 금속 조직 검사 결과, 모든 샘플 그룹의 양극 산화층에서 불연속성이 발견되지 않았습니다 (그림 7-12).
- 양극 산화층의 두께는 두 합금 모두에서 고압 주조 재료에 비해 사형 주조 재료에서 현저하게 더 두꺼웠습니다 (약 5배) (그림 6).
- 층 균일성은 다양했습니다: 고압 주조 부품의 경우, AlSi12가 AlSi9Cu3보다 더 균일한 (더 얇지만) 층을 생성했습니다. 사형 주조 부품의 경우, AlSi9Cu3가 더 나은 균일성 (사형 주조 AlSi12에 비해 전체적으로 더 얇음)을 보였습니다. AlSi12의 미세한 공정 구조가 더 나은 균일성을 제공하는 것으로 언급되었습니다.
- 아노다이징 처리는 아노다이징되지 않은 샘플에 비해 마모(질량 손실)를 감소시켰습니다 (표 5).
- 마모 저항성의 가장 큰 향상(질량 손실 약 50% 감소)은 사형 주조로 생산된 아노다이징된 EN AC-AlSi9Cu3(Fe) 합금에서 관찰되었습니다. 다른 아노다이징된 샘플은 30%에서 47% 사이의 질량 손실 감소를 보였습니다.
- 사형 주조 합금은 일반적으로 아노다이징 후 고압 주조 합금에 비해 낮은 질량 손실(더 높은 마모 저항성)을 나타냈습니다.
- 사형 주조된 AlSi9Cu3 합금과 고압 주조된 AlSi12 합금의 조합이 테스트된 그룹 중에서 가장 큰 마모 저항성을 보였습니다.
그림 이름 목록 (Figure Name List):
- Fig. 1. Scheme of the anodization process including the anodized part, electrolyte, power supply and the alumina surface layer.
- Fig. 2. Stages in the development of the alumina surface layer, a) barrier layer development, b) growth of small inhomogenities, c) continuously grow of pores, d) stabilization of the interpore distances (JPK Instruments AG, 2003).
- Fig. 3. Non anodized element made from the AC-AlSi12 aluminium alloy, produced by the Pressure Cast method
- Fig. 4. Anodized element made from the AC-AlSi9Cu3 aluminium alloy, produced by the Pressure Cast method
- Fig. 5. Overanodized element made from the AC-AlSi9Cu3 aluminium alloy, produced by the Pressure Cast method
- Fig. 6. Results of the anodic layer thickness measurement
- Fig. 7. Anodic alumina layer generated on the AlSi9Cu3 alloy, high pressure cast
- Fig. 8. Anodic alumina layer generated on the AlSi12 alloy, sand cast
- Fig. 9. Microstructure of the AlSi9Cu3 alloy, high pressure cast
- Fig. 10. Microstructure of the AlSi12 alloy, sand cast
- Fig. 11. Microstructure of the AlSi12 alloy, high pressure cast
- Fig. 12. Microstructure of the AlSi9Cu3 alloy, sand cast
7. 결론 (Conclusion):
본 연구는 사형 주조 및 고압 다이캐스팅 방법 모두 아노다이징에 적합한 AlSi12 및 AlSi9Cu3 합금 부품 생산에 실행 가능함을 입증했습니다. 가장 높은 마모 저항성을 나타내는 조합은 사형 주조로 생산된 AlSi9Cu3 합금이었으며, 고압 다이캐스팅으로 생산된 AlSi12 합금이 그 뒤를 이었습니다. 반대로, 사형 주조된 AlSi12 및 고압 주조된 AlSi9Cu3 부품은 더 낮은 마모 저항성을 보였습니다. 아노다이징은 아노다이징되지 않은 합금에 비해 마모로 인한 중량 손실을 현저히 감소시킵니다. 주조 방법은 아노다이징된 층의 마모 저항성에 영향을 미치며, 본 연구에서는 일반적으로 사형 주조 합금이 더 큰 저항성을 나타냈습니다.
8. 참고문헌 (References):
- [1] M.H. Robert, D. Delbin: Production of cellular A2011 alloy from semi-solid state, Journal of Achievements in Materials and Manufacturing Engineering, 17, (2006), pp. 137-140.
- [2] M. Wierzbińska, J. Sieniawski: Effect of morphology of eutectic silicon crystals on mechanical properties and cleavage fracture toughness of AlSi5Cu1 alloy, Journal of Achievements in Materials and Manufacturing Engineering, 14, (2006), pp. 31-36
- [3] Ι. Tsangaraki-Kaplanoglou, S. Theohari, Th. Dimogerontakis, Y. Wang, H. Kuo, S. Kia: Effect of alloy types on the anodizing process of aluminum, Surface & Coatings Technology, 200, (2006), pp. 2634 - 2641
- [4] K. P. Han, J. L. Fang: Decorative-protective coatings on aluminium, Surface and Coathings Technology, 88 (1996) pp. 178-182
- [5] H. Konno, K. Utaka, R. Furuichi: Two step of anodizing process of aluminium as a means of improving the chemical and physical properties of oxide films, Corrosion Science, 38, (1996), pp. 2247-2256
- [6] M. Maejima, K. Saruwatari, M. Takaya: Friction behaviour of anodic oxide film on aluminum impregnated with molybdenum sulfide compounds, Surface and Coatings Technology, 132 (2000), pp. 105-110
- [7] I. Vrublevsky, V. Parkoun, V. Sokol, J. Schreckenbach: Study of chemical dissolution of the barrier oxide layer of porous alumina films formed in oxalic acid using a re-anodizing technique, Applied Surface Science 236 (2004) pp. 270-277
- [8] J. Konieczny, L.A. Dobrzański, K. Labisz, J. Duszczyk: The influence of cast method and anodizing parameters on structure and layer thickness of aluminum alloys, Journal of Materials Processing Technology, 157-158 (2004), pp. 718-723
- [9] L.E. Fratila-Apachitei, J. Duszczyk, L. Katgerman: AlSi(Cu) anodic oxide layers formed in H2SO4 at low temperature using different current waveforms, Surface and Coatings Technology, 165, (2003), pp. 232-240
- [10] S.J. Garcia-Vergara, P. Skeldon, G.E. Thompson, H. Habazaki: Pore development during anodizing of Al-3.5 at.%W alloy in phosphoric acid, Surface & Coatings Technology, 201, (2007), pp. 9506-9511
- [11] M. Shahid, A.Q. Khan: Mechanism of film growth during anodizing of Al-alloy-8090/SiC metal matrix composite in sulphuric acid electrolyte, Journal of Materials Science, 32, (1997), pp. 3775-3781
- [12] T. Haga, H. Sakaguchi, H. Inui, H. Watari, S. Kumai, Aluminum alloy semisolid strip casting using an unequal diameter twin roll caster, Journal of Achievements in Materials and Manufacturing Engineering, 14, (2006), pp. 157-162
- [13] D. Djozan, M. Amir-Zehni, Anodizing of inner surface of long and small-bore aluminum tube, Surface and Coatings Technology, 173, 2003, pp. 185-191
- [14] L.E. Fratila-Apachitei, J. Duszczyk, L. Katgerman, Voltage transients and morphology of AlSi(Cu) anodic oxide layers formed in H2SO4 at low temperature, Surface and Coatings Technology, 157 (2002) pp. 80-92
- [15] J. Zhang, X. Zhao, Y. Zuo, J. Xiong, The bonding strength and corrosion resistance of aluminum alloy by anodizing treatment in a phosphoric acid modified boric acid/sulfuric acid bath, Surface & Coatings Technology, 202, 2008, pp. 3149-3156
- [16] T. Dimogerontakis, L. Kompotiatis, I. Kaplanoglou, oxygen evolution during the formation of barrier type anodic film on 2024-T3 aluminium alloy, Corrosion Science, 39, (1998), 1939-1951
9. 저작권 (Copyright):
- 이 자료는 "[K. Labisz, L.A. Dobrzański, J. Konieczny]"의 논문입니다. "[Anodization of cast aluminium alloys produced by different casting methods]"를 기반으로 합니다.
- 논문 출처: [DOI URL이 있다면 삽입, 없다면 'DOI 정보 없음'으로 명시]
이 자료는 상기 논문을 바탕으로 요약되었으며, 상업적 목적의 무단 사용을 금합니다.
Copyright © 2025 CASTMAN. All rights reserved.