본 소개 논문은 "Jönköping University, School of Engineering, Dissertation Series No. 084"에서 발행한 "The Effect of Microstructural Features, Defects and Surface Quality on the Fatigue Performance in Al-Si-Mg Cast Alloys" 논문을 기반으로 합니다.
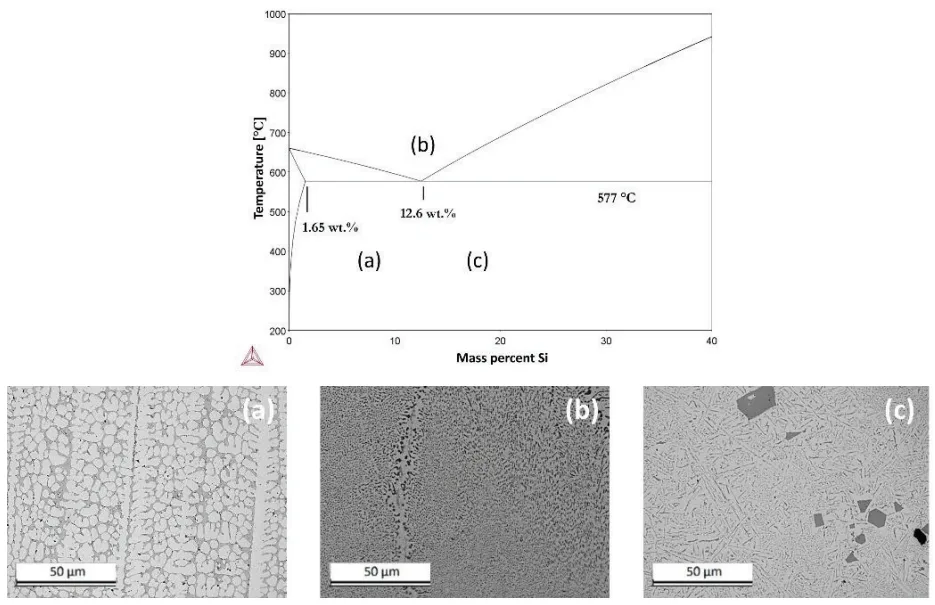
1. 개요:
- 제목: 미세조직 특징, 결함 및 표면 품질이 Al-Si-Mg 주조 합금의 피로 성능에 미치는 영향 (The Effect of Microstructural Features, Defects and Surface Quality on the Fatigue Performance in Al-Si-Mg Cast Alloys)
- 저자: Toni Bogdanoff
- 발행 연도: 2023
- 출판 저널/학회: Jönköping University, School of Engineering, Dissertation Series No. 084
- 키워드: Al-Si-Mg 주조 합금, 피로 성능, 미세조직 특징, 결함, 표면 품질, 용탕 품질, 구리 첨가, 산화 개재물(bifilms), HIP, 열처리, 주조 알루미늄.
2. 초록:
지구 온난화로 인해 산업계는 이산화탄소(CO2) 배출을 줄이기 위해 더 가벼운 부품을 제조해야 하는 상황에 직면해 있습니다. 이를 달성하기 위한 유망한 후보로는 알루미늄-실리콘(Al-Si) 주조 합금이 있으며, 이는 높은 중량 대비 강도 비율, 우수한 내식성 및 양호한 주조성을 제공합니다. 그러나 이러한 합금의 기계적 특성 변화를 이해하는 것은 중요한 응용 분야를 위한 고성능 부품 생산에 필수적입니다. 결함과 산화물은 피로 응용 분야에서 주조 부품이 거부되는 주된 이유이며, 기계적 특성에 부정적인 영향을 미칩니다.
Al-Si 주조에서 α-알루미늄 기지, Al-Si 공정, 표면 거칠기, 기공, 수소 함량, 산화물 및 금속간 화합물과 같은 파라미터와 피로 성능 간의 상관관계에 대한 포괄적인 이해는 아직 이루어지지 않았습니다.
본 학위 논문에서 제시된 연구는 최첨단 실험 기법을 사용하여 주기적 하중 하에서 Al-Si-Mg 주조 합금의 기계적 특성 및 균열 개시 및 전파 거동을 조사했습니다. 주사전자현미경(SEM)과 전자후방산란회절(EBSD), 디지털 이미지 상관법(DIC), 집속 이온빔(FIB) 밀링을 결합한 실시간(In-situ) 주기 시험을 수행했습니다. 이러한 기법을 통해 수소 함량, 표면 거칠기, 산화물 및 금속간 화합물 상을 포함하여 피로 성능에 영향을 미치는 파라미터에 대한 포괄적인 연구가 가능했습니다. 구체적으로 용탕 품질, 구리(Cu) 함량, 산화 개재물(oxide bifilms), 표면 품질 및 기공도의 영향을 조사했습니다.
열처리된 Al-Si 합금에서 증가된 Cu 농도는 금속간 화합물 상의 양을 증가시켜 균열 거동에 영향을 미쳤습니다. 또한, 높은 변형 영역에서 멀리 떨어진 영역에서도 균열 개시 지점에서 산화 개재물이 발견되었습니다. Si 및 철(Fe)이 풍부한 금속간 화합물이 이러한 개재물 위에 석출된 것으로 관찰되었습니다. 매우 작은 크기 때문에 이러한 산화물은 일반적으로 비파괴 검사로는 감지되지 않지만, 상대적으로 낮은 인장 응력에서 열리는 것으로 나타나 기계적 특성에 영향을 미칩니다. 마지막으로, Al-Si 합금 주조 표면(casting skins)은 피로 성능 향상 측면에서 흥미로운 효과를 보여, 이러한 합금에 대한 표면 연마의 부정적인 효과를 강조했습니다.
3. 서론:
온실가스, 특히 CO2 배출 감소는 전 세계적인 주요 관심사이며, 자동차와 같은 산업에서 알루미늄과 같은 경량 소재의 사용을 촉진하고 있습니다 [1]. 알루미늄-실리콘(Al-Si) 주조 합금은 높은 강도 대 중량비, 비용 효율성, 내식성 및 주조성 덕분에 주요 후보입니다 [2, 3]. 재활용 알루미늄 사용이 증가하고 있으며, 이는 1차 생산에 비해 상당한 에너지 절약을 제공합니다 [4-6]. 순수 알루미늄은 강도가 제한적이지만, 특히 Si, Cu, Mg와의 합금은 고용 강화 및 석출 강화를 통해 기계적 특성을 향상시킵니다 [7-12]. 그러나 주조 알루미늄 부품의 고주기 피로(HCF) 성능은 여전히 과제이며, 피로는 모든 고장의 약 90%에 기여합니다 [13]. 산화막(bifilms) 및 기공과 같은 결함은 피로 수명을 크게 감소시킵니다 [14-17]. 종종 부품 잠재적 피로 수명의 1%에 불과하게 제한합니다 [17]. 기공과 같은 일부 결함은 감지할 수 있지만 [19], 개재물과 같은 다른 결함은 고장 발생 시까지 감지되지 않는 경우가 많습니다 [20, 21]. 거칠기를 포함한 표면 상태 또한 피로 개시에 결정적인 영향을 미칩니다 [16]. 기계 가공된 시편에 대한 표준 실험실 피로 시험은 주조 표면(casting skins)을 가진 실제 부품의 거동을 완전히 나타내지 못할 수 있습니다 [22]. 따라서 미세조직 특징, 결함 및 표면 품질이 주조 Al-Si 합금의 기계적 성능, 특히 피로에 미치는 영향에 대한 더 나은 이해는 까다로운 응용 분야를 위한 부품 최적화에 중요합니다.
4. 연구 요약:
연구 주제 배경:
CO2 배출 감소를 위한 경량 부품의 필요성은 다양한 산업, 특히 자동차 산업에서 Al-Si 주조 합금의 사용을 촉진합니다 [1, 2]. 이 합금들은 높은 강도 대 중량비와 우수한 주조성과 같은 유리한 특성을 제공합니다 [3]. 그러나 특히 피로에 민감한 부품에서의 적용은 고유한 미세조직 특징과 결함으로 인해 종종 제한됩니다.
기존 연구 현황:
피로 파괴는 주조 Al 부품의 주요 관심사입니다 [13]. 기공 및 산화 개재물과 같은 결함, 그리고 표면 거칠기는 피로 성능을 현저히 저하시키는 것으로 알려져 있습니다 [14-17, 22]. 많은 연구가 존재하지만, α-알루미늄 기지, Al-Si 공정, 다양한 결함(기공, 산화물), 금속간 화합물 상, 수소 함량 및 표면 거칠기 간의 복잡한 상호 작용이 피로 수명에 미치는 영향에 대한 포괄적인 이해는 여전히 부족합니다 [24]. 특히 표면 거칠기와 용탕 상태에서 비롯된 결함의 역할에 관해서는 문헌에 상충되는 결과와 공백이 존재합니다 [24].
연구 목적:
본 연구의 주요 목적은 다양한 미세조직 특징, 결함(산화물/개재물, 기공 포함), 용탕 품질 파라미터(수소 함량), 합금 첨가물(특히 구리), 표면 품질(거칠기, 주조 표면)이 Al-Si-Mg 기반 주조 합금의 기계적 특성, 특히 피로 성능(균열 개시 및 전파)에 미치는 영향을 조사하고 이해하는 것이었습니다 [25, 28]. 목표는 고성능 응용 분야를 위해 이러한 합금을 최적화하고 생산 과정에서의 에너지 소비를 잠재적으로 줄일 수 있는 지식을 제공하는 것이었습니다.
핵심 연구:
본 연구는 Al-Si-Mg 및 Al-Si-Mg-Cu 주조 합금의 피로 성능에 영향을 미치는 몇 가지 주요 측면에 초점을 맞췄습니다:
- 용탕 품질: 주조 공장에서의 용탕 처리 및 취급(예: 회전식 탈가스)이 최종 기계적 특성에 미치는 영향을 평가하고, RPT 및 인장 시험과 같은 기술을 사용하여 가시적(기공) 및 숨겨진(개재물) 손상을 밝힙니다 (보충 자료 I, II).
- 구리의 역할: 다양한 Cu 함량(0 ~ 3 wt.%)이 주조 상태 및 열처리 상태에서 피로 균열 개시 및 전파 메커니즘에 미치는 영향을 조사하고, 이를 미세조직(금속간 화합물 상 예: Q-상, θ-상) 및 기지 특성의 변화와 연관시킵니다 (보충 자료 IV, V).
- 숨겨진 손상 (산화 개재물): 용탕 상태에서 발생하는 고유한 산화 개재물('숨겨진 손상')의 특성과 이것이 국부적 변형 집중 및 파괴 거동에 미치는 영향을 DIC, SEM, FIB-단층 촬영 및 STEM-EDS를 사용하여 특성화합니다. HIP가 이러한 결함을 완화하는 역할을 조사합니다 (보충 자료 III, VI, VII).
- 표면 품질 및 결함 크기: 표면 상태(주조 표면 대 기계 가공/연마 표면)와 내부 결함 특성(수소 함량에 영향을 받는 기공 크기 분포)의 복합적인 영향이 Al-Si-Cu-Mg 주물의 피로 수명에 미치는 영향을 평가합니다 (보충 자료 VIII).
5. 연구 방법론
연구 설계:
본 연구는 실증주의적 관점과 연역적 추론에 기반한 실험적 접근 방식을 사용했습니다 [132, 133]. 실험은 통제된 조건 하의 실험실 규모와 실제 산업 주조 환경(HPDC 및 사형 주조) 모두에서 수행되었습니다. 적용 가능한 경우 표준화된 시험 절차(ISO, ASTM)를 따랐으며, 필요한 경우 수정 사항을 기록했습니다 [25]. 설계는 독립 변수(예: Cu 함량, 표면 상태, 수소 수준, 공정 단계)가 종속 변수(기계적 특성, 피로 수명, 균열 거동)에 미치는 영향을 분리하여 연구하는 것을 목표로 했습니다 [26, 27].
데이터 수집 및 분석 방법:
다양한 기술이 활용되었습니다:
- 재료 준비: HPDC, 사형 주조(코팅/비코팅 주형), 방향성 응고(Bridgman 로)를 통한 주조 [29-33]. 주조 후 처리에는 열간 등방압 가압(HIP) 및 다양한 T6 유사 열처리 사이클(용체화 처리, 담금질, 시효 처리)이 포함되었습니다 [38, 50].
- 용탕 품질 평가: 감압 응고 시험(RPT), HYCAL 수소 분석, 화학 조성을 위한 광학 방출 분광법(OES), 나선형 유동성 시험, 밀도 측정(아르키메데스 원리) [35, 45-49].
- 미세조직 특성화: 광학 현미경(OM), 에너지 분산형 분광법(EDS)을 갖춘 주사 전자 현미경(SEM), 파장 분산형 분광법(WDS), 결정립 크기/방향을 위한 전자 후방 산란 회절(EBSD), 단면 관찰, 3D 단층 촬영 및 주사 투과 전자 현미경(STEM) 시편 준비를 위한 집속 이온빔(FIB) 밀링 [39-41]. 정량 분석에는 SDAS, 결정립 크기, 입자 크기/분포(예: 3NN 거리), 상 분율 및 결함 특성화가 포함되었습니다.
- 기계적 시험: ISO 6892-1에 따른 인장 시험(ST, σY, eF), 계단식 방법(ISO 12107) 및 S-N 곡선 생성을 위한 축 방향 피로 시험(R=-1, 50 Hz) [43].
- 균열 개시/전파 연구: SEM 내에서 소형 컴팩트 인장 시편을 사용한 실시간(In-situ) 주기 피로 시험, MatchID 소프트웨어를 사용한 디지털 이미지 상관법(DIC) (미시 규모용 2D, 거시 규모용 3D 스테레오 DIC)을 통한 변형률 필드(Von Mises 변형률) 매핑 [41, 43-44, 53-56].
- 결함 분석: 컴퓨터 단층 촬영(CT) 스캐닝, SEM을 사용한 파단면 분석(파면 해석) [62, 71].
- 통계 분석: 연신율(eF), 품질 지수(QT), 피로 수명(Nf)에 대한 Weibull 분포 분석, 기공 크기(deq)에 대한 로그 정규 분포 분석, Basquin 법칙 파라미터 추정, Anderson-Darling 적합도 검정, 선형 회귀 [59, 64, 91, 97, 102, 104, 106].
연구 주제 및 범위:
본 연구는 네 가지 주요 질문(RQ1-RQ4)을 다루었습니다:
- RQ1: 주조 Al-Si 부품의 기계적 특성, 특히 재활용 합금 사용 시 생산 공정(잉곳에서 최종 부품까지, 용탕 처리 및 탈가스 포함)의 영향. HPDC에서 EN-AC 46000 연구.
- RQ2: 주조 상태 및 열처리된 Al-Si-Mg 합금에서 Cu 첨가(0-3 wt.%)가 피로 균열 개시 및 전파에 미치는 영향. Bridgman 로를 통해 주조된 수정된 Al7SiMg 연구.
- RQ3: 용탕 상태에서 비롯된 숨겨진 손상(산화 개재물)의 식별, 특성화 및 기계적 특성에 대한 영향. EN-AB 42000(사형 주조), EN-AC 46000(HPDC), C355(Bridgman) 연구. HIP 효과 조사.
- RQ4: 표면 거칠기(주조 표면 대 기계 가공/연마 표면)와 내부 결함(수소와 관련된 기공)의 복합적인 영향이 Al-Si 주물의 피로 성능에 미치는 영향. 사형 주조된 Al7Si3CuMg 합금 연구.
6. 주요 결과:
주요 결과:
- 용탕 품질 및 탈가스: 용탕 품질 평가는 RPT 이상을 요구합니다. 인장 시험, 특히 Weibull 통계로 분석된 연신율(eF)은 용탕 처리(이송 단계)로 인한 '숨겨진' 개재물 손상을 드러냅니다 [보충 자료 I]. 연구된 산업 사례(EN-AC 46000)에서의 회전식 탈가스는 RPT 시편의 가시적 기공을 줄였지만, 효과적인 제거 없이 기존의 거친 개재물을 더 미세한 것으로 분해함으로써 최종 주물의 실제 기계적 특성(eF, QT)을 개선하지 못하거나 잠재적으로 악화시켰습니다 [보충 자료 I, II]. 탈가스는 비탈가스 시편에서 관찰된 Weibull 혼합 분포를 제거했지만, 단일 분포를 더 낮은 품질 쪽으로 이동시켰습니다 [보충 자료 II].
- 구리의 영향: Al7SiMg 합금에서 Cu 함량(0 ~ 3.2 wt.%) 증가는 주조 상태 및 열처리 상태 모두에서 항복 강도(σY) 및 인장 강도(ST)를 증가시켰지만, 특히 취성 Cu-풍부 금속간 화합물 상(Q-Al5Mg8Cu2Si6, θ-Al2Cu)으로 인해 주조 상태에서 연성(eF)을 크게 감소시켰습니다 [보충 자료 IV, V]. 열처리는 강도를 더욱 향상시켰고 주조 상태에 비해 연성 감소를 완화했습니다. 균열 개시는 주조 상태에서 슬립 밴드/Si 입자(낮은 Cu)에서 공정 영역/Cu-풍부 상(높은 Cu)으로 이동했습니다. 열처리된 합금에서는 균열 개시가 1차 수지상정(낮은 Cu)에서 발생하여 수지상정 간 영역 및 결정립계(높은 Cu)로 이동했습니다. 균열 전파 경로는 Cu 함량 및 기지 강화와 함께 더 구불구불해지고 수지상정 횡단에서 수지상정 간/결정립계 쪽으로 이동했습니다. 더 높은 Cu 함량은 특히 열처리 조건에서 피로 중 더 많은 2차 균열을 유발했습니다 [보충 자료 V, VII].
- 숨겨진 손상 (산화 개재물): 용탕 처리 및 주조 중에 형성된 산화 개재물은 중요한 '숨겨진' 결함으로 작용합니다. DIC는 기하학적 응력 집중원에서 멀리 떨어진 곳에서도 이러한 개재물과 관련된 국부적 변형 집중을 밝혔습니다 [보충 자료 VI]. FIB/STEM-EDS 분석 결과, 이러한 균열에는 알루미늄 산화물 층이 포함되어 있어 하중 하에서 열린 기존 개재물임을 확인했습니다 [보충 자료 VI, VII]. 이러한 개재물은 금속간 화합물 상(예: Al5FeSi) 및 Si 입자의 핵 생성 사이트로 작용합니다 [보충 자료 VII]. HIP는 가스 기공을 효과적으로 닫았지만 이러한 산화 개재물을 완전히 치유하거나 제거하지는 못했으며, 후속 피로 하중 중에 여전히 열릴 수 있습니다 [보충 자료 III, VII]. 주물에서 관찰된 손상은 개재물 손상(액체 상태의 개재물)과 기계적 손상(사용 하중)으로 구별해야 합니다 [보충 자료 VII].
- 표면 품질 및 기공도: 일반적인 가정과는 달리, 사형 주조된 Al-Si-Cu-Mg 합금의 경우 주조 표면(casting skin)의 존재가 기계 가공 및 연마(PS) 표면에 비해 피로 수명을 현저히 개선했습니다 [보충 자료 VIII]. 연마는 표면을 제거하여 표면 아래 결함(기공/개재물)을 표면에 직접 노출시켜 균열 개시 단계를 단축하거나 제거하여 피로 수명을 급격히 감소시켰습니다. 피로 파괴는 주조 상태 시편에서는 표면 아래 결함(표면 근처의 기공/불완전성)에서 시작되었지만, 연마된 시편에서는 표면에 노출된 결함에서 직접 시작되었습니다. 수소 함량 증가는 더 큰 기공과 더 높은 기공률을 유발하여 특히 연마된 시편의 경우 더 넓은 피로 수명 분포(낮은 Weibull 계수 M)를 초래했지만, 거친 주조 표면의 평균 피로 수명에는 영향이 적었습니다. 표면 품질과 기공 크기 분포 간의 상호 작용은 복잡합니다. 기존 피로 수명 예측 모델(예: Juvinall)은 주조 표면의 유익한 효과를 고려하기 위해 수정이 필요합니다 [보충 자료 VIII].
그림 이름 목록: (Figure Name List)
- Figure 1. Al-Si phase diagrams: a) hypoeutectic, b) eutectic, and c) hypereutectic microstructures.
- Figure 3. Entrainment of surface oxides [79].
- Figure 4. Hydrogen solubility in pure aluminium and aluminium alloys [42].
- Figure 5. a) Impurity-induced twinning [97]; b) restricted TPRE growth [98].
- Figure 6. The stress-strain curve of an as-cast Al7SiMg alloy, with emphasis placed on the essential parameters used in the research presented in this thesis.
- Figure 7. Overview of the research methodology.
- Figure 8. a) Cylindrical rods (length 150 mm and diameter 9 mm). b) schematic illustration of the Bridgman furnace; c) stair casting geometry (dimensions in mm).
- Figure 9. The geometry of the casting in the sand mould.
- Figure 10. The production process used in the HPDC plant.
- Figure 11. a) Schematic diagram of the tensile testing sample; b) a sample exposed to the HIP process and heat treatment.
- Figure 12. a) Dimensions of the compact-tension sample in mm; b) miniature stage for in-situ cyclic testing; c) FOV of the compact-tension sample.
- Figure 13. Tensile- and fatigue-testing sample geometry.
- Figure 14. The cross-sections of the RPT samples at different stages of production.
- Figure 15. The Weibull distributions of elongation in the different stages of production.
- Figure 16. Cross-sections of RPT samples taken at different stages of the production process, with and without degassing.
- Figure 17. The Weibull distributions of the structural quality of the two production routes.
- Figure 18. (a) Alloy Cu 0 in as-cast condition, b) Alloy Cu 0 in heat-condition.
- Figure 19. Three-nearest-neighbour (3NN) distances between particles: a) Si particles; b) Q-phases. The error bars represent the standard deviation.
- Figure 20. Beginning of crack initiation in as-cast condition: a) Alloy Cu 0; b) Alloy Cu 1.5.
- Figure 21. Crack propagation in all heat-treated alloys, imaged using a combination of EBSD and DIC: a–b) Alloy Cu 0; c–d) Alloy Cu 0.5; e–f) Alloy Cu 1.5; g–h) Alloy Cu 3.0. The yellow dashed lines represent grain boundaries, superimposed from EBSD, and the red arrows point to the initiation sites. The colour bar represents the von Mises equivalent strain, and is valid for all frames.
- Figure 22. Crack propagation in all as-cast alloys, imaged using a combination of EBSD and DIC: a) Alloy Cu 0; b) Alloy Cu 0.5; c) Alloy Cu 1.5; d) Alloy Cu 3.0. The yellow dashed lines represent grain boundaries, superimposed from EBSD. The final fracture, shown as a black dashed line in the picture, was manually added. The colour bar represents the von Mises equivalent strain.
- Figure 23. Development of slip bands during the cycling testing of alloys with different Cu contents: a) Alloy Cu 0, at the crack edge; b) Alloy Cu 0, 150 µm from the crack edge; c) Alloy Cu 1.5, at the crack edge, d) Alloy Cu 1.5, 150 µm from the crack edge.
- Figure 24. Development of secondary cracks (indicated by arrows) in heat-treated Alloy Cu 3.0 after a) 825 cycles; b) 925 cycles. c–d) magnified micrographs of the secondary cracks visible in b).
- Figure 25. FIB milling was used to investigate the material around the crack in heat-treated alloys. a) Alloy Cu 0, test stopped at 1253 cycles; b) and c) show related sections. d) Alloy Cu 3.0, test stopped at 640 cycles; e) and f) show related sections. The black arrows point to Fe-rich phases, the white arrows point to superficial cracks, and the red arrows point to the crack coming from underneath.
- Figure 26. Three-dimensional reconstruction of the FIB sections of cracks in heat-treated alloys. a) FIB section of Alloy Cu 0, test stopped at 1253 cycles, and b) three-dimensional reconstruction. c) FIB section of Alloy 3.0 Cu, test stopped at 640 cycles, and d) three-dimensional reconstruction. The red arrows show the cracks, and the blue arrows indicate the intermetallic phases.
- Figure 27. Microstructures of Al7SiMg alloy: (a) as-cast condition, 16 mm thickness, (b) as-cast condition, 32 mm thickness. The red squares highlight a magnified area. The red ovals highlight the inhomogeneous microstructure in the 32 mm-thick sample.
- Figure 28. Microstructures of the Al7SiMg alloy: (a) heat-treated condition, 16 mm thickness; (b) heat-treated condition, 32 mm thickness. The red squares highlight a magnified area.
- Figure 29. CT scan of the material in as-cast condition, showing the porosities (blue); having been HIPped (red); and having been heat-treated (green). a) 16 mm, b) 32 mm.
- Figure 30. Crack propagation in the HIPped and heat-treated conditions. a–c) the 16 mm sample, showing initiation and propagation; d–f) the 32 mm sample, showing cracks and evaluation of crack propagation.
- Figure 31. Full-field distributions of von Mises equivalent strain in a sample A under a load of (a) 11.9 kN and (b) 15.4 kN.
- Figure 32. (a) Sample A after fracture. The red circle indicates the location of the strain concentration seen in Figure 31b. (b), which is an SEM image of the oxide film found in the strain-concentration area. (c) Increased magnification of the oxide draped over the microstructure.
- Figure 33. Stress-strain curve throughout tensile testing of sample A for both the strain concentration and a symmetry reference point.
- Figure 34. (a) DIC strain field of sample B under a load of 15.9 kN just before fracture. (b) Close-up image of the upper strain concentration with an optical microscope after failure. (c) Visible crack on the sample surface after paint removal in the SEM.
- Figure 35. (a) Location of the lamella in front of the crack. (b) Extraction of the lamella. (c) STEM-EDS map of oxygen distribution in the lamella, which revealed the oxide film inside the crack.
- Figure 36. a) The FOV (300 × 300 μm) had no visible cracks after 100 cycles. b) cracks outside the FOV after 100 cycles.
- Figure 37. a) After 200 cycles, the cracks showed no continued propagation. (b) A crack was initiated at the notch after 550 cycles.
- Figure 38. a) Two cracked phases perpendicular to the loading direction. (b) BSE image of the trenching of the lamella. (c) BSE image of the 1.2 μm lamella before lifting.
- Figure 39. a) BSE, b) STEM, c) HADF, d) DF images of the lamella. The arrow points to the observed line around the open crack.
- Figure 40. a) SEM image of a crack. b) STEM-EDS image of the same crack, showing the intermetallic phases around it.
- Figure 41. a) STEM-EDS measurement of oxygen in the crack. b) EDS line scan results from points 1 to 51.
- Figure 42. Three-dimensional scans of a 900 × 900 µm area of as-cast components a) without coating (rough surface) and b) with coating (fine surface).
- Figure 43. The investigated surface conditions: a) PS, b) FS, and c) RS.
- Figure 44. Microstructure of the cast material, showing the aluminium dendrites, Si particles, and Cu- and Fe-rich phases.
- Figure 45. a) The microstructure of the sand-cast material with low hydrogen content; b) an enlarged view of the area highlighted by a red square in (a), showing oxides in the vicinity of the porosity; c) a sample with high hydrogen content, where two distinct pore sizes are evident.
- Figure 46. The probability density functions of the pore size distributions for the LH and HH conditions.
- Figure 47. Wöhler curves for a) LH and b) HH samples.
- Figure 48. Fatigue-life distributions for (a) LH and (b) HH samples with different surface conditions.
- Figure 49. a) The crack initiation point in the fracture surface of an LH sample with a casting skin. The red arrow is pointing to the casting skin. b) The crack initiation point in the fracture surface in the PS sample, at a defect located at the surface.
- Figure 50. The probability density functions of Weibull distributions for (a) samples with casting skins and (b) MS and PS samples.
7. 결론:
본 연구는 미세조직 특징, 결함 및 표면 품질이 Al-Si-Mg 주조 합금의 피로 성능에 미치는 영향을 조사했습니다. 주요 결론은 다음과 같습니다:
- 용탕 품질: 완전한 용탕 품질 평가는 숨겨진 손상을 밝히기 위해 RPT와 인장 시험 모두를 필요로 합니다. 회전식 탈가스는 초기 용탕이 손상된 경우 특성을 개선하지 못할 수 있으며, 기계적 성능 개선 없이 Weibull 혼합 분포를 제거할 수 있습니다.
- 구리의 역할: Cu 함량 증가는 강도(σY, ST)를 향상시키지만 연성(eF)을 감소시키며, 특히 주조 상태에서 그렇습니다. 이는 금속간 화합물을 증가시키고 균열 개시/전파 경로를 변경하며, 특히 열처리 후 2차 균열을 증가시킵니다.
- 숨겨진 손상: 산화 개재물은 용탕에서 비롯된 중요한 결함으로, 핵 생성 사이트로 작용하고 인장 응력 하에서 열립니다. DIC 및 STEM-EDS는 그 존재와 영향을 확인했습니다. HIP는 기공을 닫지만 개재물을 완전히 치유하지 못할 수 있습니다. 개재물 손상과 기계적 손상을 구별하는 것이 중요합니다.
- 표면 품질 및 결함 크기: 주조 표면(casting skin)은 표면 아래 결함에 대한 장벽 역할을 하고 표면에 노출된 결함으로부터의 균열 개시를 지연/방지함으로써 연마된 표면에 비해 피로 수명을 현저히 개선합니다. 연마는 피로 수명을 급격히 감소시킵니다. 기공률 증가는 주로 피로 수명 변동성에 영향을 미치며 표면 상태와 복잡하게 상호 작용합니다. 최소한의 기계 가공으로 부품을 설계하는 것이 피로 성능에 유리합니다.
8. 참고 문헌:
- [1] N. Hooftman, M. Messagie, J. Van Mierlo, T. Coosemans, A review of the European passenger car regulations–Real driving emissions vs local air quality, Renewable and Sustainable Energy Reviews 86 (2018) 1-21.
- [2] A.C. Serrenho, J.B. Norman, J.M. Allwood, The impact of reducing car weight on global emissions: the future fleet in Great Britain, Philosophical Transactions of the Royal Society A: Mathematical, Physical and Engineering Sciences 375(2095) (2017) 20160364.
- [3] A.I. Taub, A.A. Luo, Advanced lightweight materials and manufacturing processes for automotive applications, Mrs Bulletin 40(12) (2015) 1045-1054.
- [4] E. Balomenos, D. Panias, I.J.M.P. Paspaliaris, E.M. Review, Energy and exergy analysis of the primary aluminum production processes: a review on current and future sustainability, 32(2) (2011) 69-89.
- [5] I. Polmear, D. StJohn, J.-F. Nie, M. Qian, Light alloys: metallurgy of the light metals, Butterworth-Heinemann2017.
- [6] C. Jirang, H.J.J.T.o.N.M.S.o.C. Roven, Recycling of automotive aluminum, 20(11) (2010) 2057-2063.
- [7] S. Seifeddine, E. Sjölander, T. Bogdanoff, On the role of copper and cooling rates on the microstructure, defect formations and mechanical properties of Al-Si-Mg alloys, (2013).
- [8] C. Caceres, C. Davidson, J. Griffiths, Q. Wang, The effect of Mg on the microstructure and mechanical behavior of Al-Si-Mg casting alloys, Metallurgical and materials transactions A 30(10) (1999) 2611-2618.
- [9] S. Shabestari, H. Moemeni, Effect of copper and solidification conditions on the microstructure and mechanical properties of Al–Si–Mg alloys, Journal of Materials Processing Technology 153 (2004) 193-198.
- [10] M.T. Di Giovanni, E.A. Mørtsell, T. Saito, S. Akhtar, M. Di Sabatino, Y. Li, E. Cerri, Influence of Cu addition on the heat treatment response of A356 foundry alloy, Materials Today Communications 19 (2019) 342-348.
- [11] Y. Zheng, W. Xiao, S. Ge, W. Zhao, S. Hanada, C. Ma, Effects of Cu content and Cu/Mg ratio on the microstructure and mechanical properties of Al–Si–Cu–Mg alloys, Journal of Alloys and Compounds 649 (2015) 291-296.
- [12] S. Morin, E. Elgallad, H. Doty, S. Valtierra, F.J.A.i.M.S. Samuel, Engineering, Effect of Mg content and heat treatment on the mechanical properties of low pressure Die-Cast 380 alloy, 2016 (2016).
- [13] U. Krupp, Fatigue crack propagation in metals and alloys: microstructural aspects and modelling concepts, John Wiley & Sons2007.
- [14] I. Serrano-Munoz, J.-Y. Buffiere, R. Mokso, C. Verdu, Y. Nadot, Location, location & size: defects close to surfaces dominate fatigue crack initiation, Scientific reports 7(1) (2017) 45239.
- [15] I. Serrano-Munoz, J.-Y. Buffiere, C. Verdu, Y. Gaillard, P. Mu, Y. Nadot, Influence of surface and internal casting defects on the fatigue behaviour of A357-T6 cast aluminium alloy, International Journal of Fatigue 82 (2016) 361-370.
- [16] H. Jiang, P. Bowen, J.J.J.o.m.s. Knott, Fatigue performance of a cast aluminium alloy Al-7Si-Mg with surface defects, 34(4) (1999) 719-725.
- [17] C. Nyahumwa, Ν.R. Green, J. Campbell, The concept of the fatigue potential of cast alloys, Journal of the Mechanical Behavior of Materials 9(4) (1998) 227-236.
- [19] O. Lashkari, L. Yao, S. Cockcroft, D. Maijer, X-ray microtomographic characterization of porosity in aluminum alloy A356, Metallurgical and Materials Transactions A 40 (2009) 991-999.
- [20] Z. Ma, A. Samuel, F. Samuel, H. Doty, S. Valtierra, A study of tensile properties in Al–Si–Cu and Al–Si–Mg alloys: Effect of β-iron intermetallics and porosity, Materials Science and Engineering: A 490(1-2) (2008) 36-51.
- [21] J. Campbell, M. Tiryakioğlu, Fatigue Failure in Engineered Components and How It Can Be Eliminated: Case Studies on the Influence of Bifilms, Metals 12(8) (2022) 1320.
- [22] M.R. Bayoumi, A. Abdellatif, Effect of surface finish on fatigue strength, Engineering Fracture Mechanics 51(5) (1995) 861-870.
- [24] A.E. Jarfors, A comparison between semisolid casting methods for aluminium alloys, Metals 10(10) (2020) 1368.
- [25] J. Olofsson, I.L. Svensson, Incorporating predicted local mechanical behaviour of cast components into finite element simulations, Materials & Design 34 (2012) 494-500.
- [26] M. Tiryakioglu, D. Askeland, C. Ramsay, Relationship between metal fluidity and optimum pouring time: a literature review, TRANSACTIONS AMERICAN FOUNDRYMENS SOCIETY (1993) 685-685.
- [27] J. Olofsson, I.L. Svensson, P. Lava, D. Debruyne, Characterisation and investigation of local variations in mechanical behaviour in cast aluminium using gradient solidification, Digital Image Correlation and finite element simulation, Materials & Design 56 (2014) 755-762.
- [28] D. Dwivedi, R. Sharma, A. Kumar, Influence of silicon content and heat treatment parameters on mechanical properties of cast Al–Si–Mg alloys, International Journal of Cast Metals Research 19(5) (2006) 275-282.
- [29] S. Roy, L.F. Allard, A. Rodriguez, W.D. Porter, A. Shyam, Comparative evaluation of cast aluminum alloys for automotive cylinder heads: Part II—mechanical and thermal properties, Metallurgical and Materials Transactions A 48(5) (2017) 2543-2562.
- [30] N. Tenekedjiev, J. Gruzleski, Hypereutectic aluminium-silicon casting alloys—a review, Cast Metals 3(2) (1990) 96-105.
- [31] O. Atasoy, F. Yilmaz, R. Elliott, Growth structures in aluminium-silicon alloys I. The coupled zone, Journal of crystal growth 66(1) (1984) 137-146.
- [32] A. Dahle, K. Nogita, S. McDonald, J. Zindel, L. Hogan, Eutectic nucleation and growth in hypoeutectic Al-Si alloys at different strontium levels, Metallurgical and Materials Transactions A 32(4) (2001) 949-960.
- [33] A. Samuel, F. Samuel, Effect of alloying elements and dendrite arm spacing on the microstructure and hardness of an Al-Si-Cu-Mg-Fe-Mn (380) aluminium die-casting alloy, Journal of Materials Science 30(7) (1995) 1698-1708.
- [35] E. Sjölander, S. Seifeddine, The heat treatment of Al–Si–Cu–Mg casting alloys, Journal of Materials Processing Technology 210(10) (2010) 1249-1259.
- [38] S.J.M.S. Shabestari, E. A, The effect of iron and manganese on the formation of intermetallic compounds in aluminum–silicon alloys, 383(2) (2004) 289-298.
- [39] C.M. Dinnis, J.A. Taylor, A.K.J.S.m. Dahle, As-cast morphology of iron-intermetallics in Al–Si foundry alloys, 53(8) (2005) 955-958.
- [40] A. Dahle, K. Nogita, S. McDonald, C. Dinnis, L. Lu, Eutectic modification and microstructure development in Al–Si Alloys, Materials Science and Engineering: A 413 (2005) 243-248.
- [41] A. Greer, Overview: Application of heterogeneous nucleation in grain-refining of metals, The Journal of Chemical Physics 145(21) (2016) 211704.
- [42] J. Campbell, Castings, Butterworth-Heinemann2003.
- [43] J. Campbell, Entrainment defects, Materials science and technology 22(2) (2006) 127-145.
- [45] M. Divandari, J. Campbell, Mechanisms of bubble trail formation in castings, Trans. AFS 109 (2001) 433-442.
- [46] G. Gyarmati, G. Fegyverneki, M. Tokár, T. Mende, The effects of rotary degassing treatments on the melt quality of an Al–Si casting alloy, International Journal of Metalcasting 15(1) (2021) 141-151.
- [48] M.B. Đurđević, Z. Odanović, J. Pavlović-Krstić, Melt quality control at aluminum casting plants, Metalurgija 16(1) (2010) 63-76.
- [49] M. Riestra, A. Bjurenstedt, T. Bogdanoff, E. Ghassemali, S. Seifeddine, Complexities in the Assessment of Melt Quality, International Journal of Metalcasting 12(3) (2018) 441-448.
- [50] M. Uludağ, R. Çetin, D. Dispinar, M.J.M. Tiryakioğlu, Characterization of the effect of melt treatments on melt quality in Al-7wt% Si-Mg alloys, 7(5) (2017) 157.
- [52] G. Eisaabadi, M. Tiryakioğlu, P. Davami, S.-K. Kim, Y.O. Yoon, G.-Y. Yeom, N.-S. Kim, The effect of remelting on the melt and casting quality in Al–7% Si–Mg castings, Materials Science and Engineering: A 605 (2014) 203-209.
- [59] G. Timelli, F. Bonollo, Fluidity of aluminium die castings alloy, International Journal of Cast Metals Research 20(6) (2007) 304-311.
- [60] M. Di Sabatino, L. Arnberg, A review on the fluidity of Al based alloys, Metallurgical Science and Tecnology 22(1) (2004).
- [61] A. Dahle, P. Tøndel, C. Paradies, L. Arnberg, Effect of grain refinement on the fluidity of two commercial Al-Si foundry alloys, Metallurgical and Materials Transactions A 27(8) (1996) 2305-2313.
- [62] A. Rotella, Y. Nadot, M. Piellard, R. Augustin, M. Fleuriot, Fatigue limit of a cast Al-Si-Mg alloy (A357-T6) with natural casting shrinkages using ASTM standard X-Ray inspection, International Journal of Fatigue (2018).
- [64] K. Fisher, W. Kurz, Fundamentals of solidification, Trans Tech Publications (1986).
- [65] Y. Cho, H.-C. Lee, K. Oh, A. Dahle, Effect of strontium and phosphorus on eutectic Al-Si nucleation and formation of β-Al 5 FeSi in hypoeutectic Al-Si foundry alloys, Metallurgical and Materials Transactions A 39(10) (2008) 2435-2448.
- [66] E.A. Mørtsell, F. Qian, C.D. Marioara, Y. Li, Precipitation in an A356 foundry alloy with Cu additions-A transmission electron microscopy study, Journal of Alloys and Compounds 785 (2019) 1106-1114.
- [67] T. Saito, E.A. Mørtsell, S. Wenner, C.D. Marioara, S.J. Andersen, J. Friis, K. Matsuda, R. Holmestad, Atomic structures of precipitates in Al–Mg–Si alloys with small additions of other elements, Adv. Eng. Mater. 20(7) (2018) 1800125.
- [68] S. Roy, L.F. Allard, A. Rodriguez, T.R. Watkins, A. Shyam, Comparative Evaluation of Cast Aluminum Alloys for Automotive Cylinder Heads: Part I—Microstructure Evolution, Metallurgical and Materials Transactions A (2017) 1-14.
- [69] R. Taghiabadi, A. Fayegh, A. Pakbin, M. Nazari, M. Ghoncheh, Quality index and hot tearing susceptibility of Al–7Si–0.35 Mg–xCu alloys, Transactions of Nonferrous Metals Society of China 28(7) (2018) 1275-1286.
- [70] M. Avalle, G. Belingardi, M.P. Cavatorta, R. Doglione, Casting defects and fatigue strength of a die cast aluminium alloy: a comparison between standard specimens and production components, International journal of Fatigue 24(1) (2002) 1-9.
- [71] F. Guerra, A. Bedolla-Jacuinde, H. Valdes-Vera, J. Quintero-Ortiz, A. Zarate-Rangel, J. Pacheco-Cedeño, Measurement of Air Entrainment and its Effect on the Microstructure and Mechanical Properties of a A356 Aluminum Alloy, International Journal of Metalcasting (2022) 1-19.
- [73] M. Tiryakioğlu, P. Yousefian, P.D.J.M. Eason, M.T. A, Quantification of entrainment damage in A356 aluminum alloy castings, 49(11) (2018) 5815-5822.
- [74] D. Dispinar, J. Campbell, Porosity, hydrogen and bifilm content in Al alloy castings, Materials Science and Engineering: A 528(10) (2011) 3860-3865.
- [76] X. Cao, J.J.M. Campbell, M.T. A, The nucleation of Fe-rich phases on oxide films in Al-11.5 Si-0.4 Mg cast alloys, 34(7) (2003) 1409-1420.
- [79] J. Campbell, Perspective chapter: A personal overview of casting processes, Casting Processes and Modelling of Metallic Materials (2020) 1-17.
- [80] M. Tiryakioğlu, The Effect of Hydrogen on Pore Formation in Aluminum Alloy Castings: Myth Versus Reality, Metals 10(3) (2020) 368.
- [82] V.-D. Le, N. Saintier, F. Morel, D. Bellett, P. Osmond, Investigation of the effect of porosity on the high cycle fatigue behaviour of cast Al-Si alloy by X-ray micro-tomography, International Journal of Fatigue 106 (2018) 24-37.
- [86] C. Caceres, M. Djurdjevic, T. Stockwell, J. Sokolowski, The effect of Cu content on the level of microporosity in Al-Si-Cu-Mg casting alloys, Scripta Materialia 40(5) (1999) 631-637.
- [97] S.-Z. Lu, A. Hellawell, Growth mechanisms of silicon in Al-Si alloys, Journal of Crystal growth 73(2) (1985) 316-328.
- [98] D. Jenkinson, L. Hogan, The modification of aluminium-silicon alloys with strontium, Journal of Crystal Growth 28(2) (1975) 171-187.
- [99] M. Timpel, N. Wanderka, R. Schlesiger, T. Yamamoto, N. Lazarev, D. Isheim, G. Schmitz, S. Matsumura, J. Banhart, The role of strontium in modifying aluminium–silicon alloys, Acta Materialia 60(9) (2012) 3920-3928.
- [100] A. Knuutinen, K. Nogita, S. McDonald, A. Dahle, Modification of Al–Si alloys with Ba, Ca, Y and Yb, Journal of Light Metals 1(4) (2001) 229-240.
- [101] S.J. Mashl, H. Bodycote, Hot Isostatic Pressing of Castings, Casting, 2008.
- [102] A. Eklund, M. Ahlfors, Heat treatment of PM parts by Hot Isostatic Pressing, Metal Powder Report 73(3) (2018) 163-169.
- [103] H. Atkinson, S. Davies, Fundamental aspects of hot isostatic pressing: an overview, Metallurgical and Materials Transactions A 31(12) (2000) 2981-3000.
- [104] M.H. Lee, J.J. Kim, K.H. Kim, N.J. Kim, S. Lee, E.W. Lee, Effects of HIPping on high-cycle fatigue properties of investment cast A356 aluminum alloys, Materials Science and Engineering: A 340(1-2) (2003) 123-129.
- [105] C. Lei, W. Frazier, E. Lee, The effect of hot isostatic pressing on cast aluminum, Jom 49(11) (1997) 38-39.
- [106] G. Ran, J. Zhou, Q. Wang, The effect of hot isostatic pressing on the microstructure and tensile properties of an unmodified A356-T6 cast aluminum alloy, Journal of alloys and compounds 421(1-2) (2006) 80-86.
- [107] L. Ceschini, A. Morri, G. Sambogna, The effect of hot isostatic pressing on the fatigue behaviour of sand-cast A356-T6 and A204-T6 aluminum alloys, Journal of materials processing technology 204(1-3) (2008) 231-238.
- [109] T. Rich, J. Orbison, R. Duncan, P. Olivero, R. Peterec, The effect of hot isostatic pressing on crack initiation, fatigue, and mechanical properties of two cast aluminum alloys, Journal of materials engineering and performance 8(3) (1999) 315-324.
- [113] A. Mohamed, F. Samuel, Influence of Mg and solution heat treatment on the occurrence of incipient melting in Al–Si–Cu–Mg cast alloys, Materials Science and Engineering: A 543 (2012) 22-34.
- [116] N.E. Dowling, Mechanical behavior of materials: engineering methods for deformation, fracture, and fatigue, Pearson2012.
- [117] E. Ghassemali, M. Riestra, T. Bogdanoff, B.S. Kumar, S. Seifeddine, Hall-Petch equation in a hypoeutectic Al-Si cast alloy: grain size vs. secondary dendrite arm spacing, Procedia Engineering 207 (2017) 19-24.
- [118] T. Bogdanoff, S. Seifeddine, A.K. Dahle, The effect of SI content on microstructure and mechanical properties of Al-Si alloy, La Metallurgia Italiana 108(6) (2016).
- [119] C. Caceres, I.L. Svensson, J. Taylor, Strength-ductility behaviour of Al-Si-Cu-Mg casting alloys in T6 temper, International Journal of Cast Metals Research 15(5) (2003) 531-543.
- [122] S. Suresh, Fatigue of materials, Cambridge university press1998.
- [124] M. Leitner, C. Garb, H. Remes, M. Stoschka, Microporosity and statistical size effect on the fatigue strength of cast aluminium alloys EN AC 45500 and 46200, Materials Science and Engineering: A 707 (2017) 567-575.
- [126] J.T. Staley Jr, M. Tiryakioğlu, J. Campbell, The effect of hot isostatic pressing (HIP) on the fatigue life of A206-T71 aluminum castings, Materials Science and Engineering: A 465(1-2) (2007) 136-145.
- [127] D.A. Lados, D. Apelian, Fatigue crack growth characteristics in cast Al–Si–Mg alloys: Part I. Effect of processing conditions and microstructure, Materials Science and Engineering: A 385(1-2) (2004) 200-211.
- [128] D.A. Lados, D. Apelian, J.F. Major, Fatigue crack growth mechanisms at the microstructure scale in Al-Si-Mg cast alloys: Mechanisms in regions II and III, Metallurgical and Materials Transactions A 37(8) (2006) 2405-2418.
- [131] Q. Wang, D. Apelian, D. Lados, Fatigue behavior of A356/357 aluminum cast alloys. Part II–Effect of microstructural constituents, Journal of light metals 1(1) (2001) 85-97.
- [132] K. Williamson, Research methods for students, academics and professionals: Information management and systems, Elsevier2002.
- [133] P. Johannesson, E. Perjons, An introduction to design science, Springer2014.
- [134] K.A. Kasvayee, E. Ghassemali, K. Salomonsson, S. Sujakhu, S. Castagne, A.E. Jarfors, Microstructural strain mapping during in-situ cyclic testing of ductile iron, Materials Characterization 140 (2018) 333-339.
- [135] K.A. Kasvayee, K. Salomonsson, E. Ghassemali, A.E. Jarfors, Microstructural strain distribution in ductile iron; comparison between finite element simulation and digital image correlation measurements, Materials Science and Engineering: A 655 (2016) 27-35.
- [136] E. Erzi, M. Tiryakioğlu, A simple procedure to determine incoming quality of aluminum alloy ingots and its application to A356 alloy ingots, International Journal of Metalcasting 14(4) (2020) 999-1004.
- [137] D. Dispinar, J. Campbell, A comparison of methods used to assess aluminium melt quality, 136th TMS Annual Meeting, Shape Casting: 2nd International Symposium, Orlando, Florida, USA,(February 2007), 2007, pp. 11-18.
- [138] D. Dispinar, S. Akhtar, A. Nordmark, M. Di Sabatino, L. Arnberg, Degassing, hydrogen and porosity phenomena in A356, Materials Science and Engineering: A 527(16-17) (2010) 3719-3725.
- [139] W. Weibull, A statistical theory of strength of materials, IVB-Handl. (1939).
- [140] W. Weibull, A statistical distribution function of wide applicability, Journal of applied mechanics (1951).
- [141] M. Tiryakioğlu, D. Hudak, On estimating Weibull modulus by the linear regression method, Journal of materials science 42(24) (2007) 10173-10179.
- [142] M. Tiryakioğlu, D. Hudak, Guidelines for two-parameter Weibull analysis for flaw-containing materials, Metallurgical and Materials Transactions B 42(6) (2011) 1130-1135.
- [143] M. Tiryakioğlu, D. Hudak, G. Ökten, On evaluating Weibull fits to mechanical testing data, Materials Science and Engineering: A 527(1-2) (2009) 397-399.
- [144] D. Dispinar, J. Campbell, Metal quality studies in secondary remelting of aluminium, Foundry Trade Journal 178(3612) (2004) 78-81.
- [145] R. Kimura, Molten Metal Quality of Aluminium Alloy Die Castings, J.JFS 87 (2015) 412-416.
- [146] M. Tiryakioğlu, J. Campbell, N.D. Alexopoulos, On the ductility of cast Al-7 pct Si-Mg alloys, Metallurgical and Materials Transactions A 40(4) (2009) 1000-1007.
- [147] M. Tiryakioğlu, J. Campbell, N.D. Alexopoulos, On the ductility potential of cast Al–Cu–Mg (206) alloys, Materials Science and Engineering: A 506(1-2) (2009) 23-26.
- [148] M. Tiryakioğlu, J. Campbell, N.D. Alexopoulos, Quality indices for aluminum alloy castings: A critical review, Metallurgical and Materials Transactions B 40(6) (2009) 802-811.
- [149] M. Tiryakioğlu, J. Campbell, Quality index for aluminum alloy castings, International Journal of Metalcasting 8(3) (2014) 39-42.
- [150] M. Tiryakioğlu, J. Campbell, Weibull analysis of mechanical data for castings: A guide to the interpretation of probability plots, Metallurgical and Materials Transactions A 41 (2010) 3121-3129.
- [151] T. Lu, J. Wu, Y. Pan, S. Tao, Y. Chen, Optimizing the tensile properties of Al–11Si–0.3 Mg alloys: Role of Cu addition, Journal of Alloys and Compounds 631 (2015) 276-282.
- [152] E. Sjölander, S. Seifeddine, Optimisation of solution treatment of cast Al–Si–Cu alloys, Materials & design 31 (2010) S44-S49.
- [153] J.H. Sokolowski, X. Sun, G. Byczynski, D. Northwood, D. Penrod, R. Thomas, A. Esseltine, The removal of copper-phase segregation and the subsequent improvement in mechanical properties of cast 319 aluminium alloys by a two-stage solution heat treatment, Journal of Materials Processing Technology 53(1-2) (1995) 385-392.
- [154] G. Wang, Q. Sun, L. Feng, L. Hui, C. Jing, Influence of Cu content on ageing behavior of AlSiMgCu cast alloys, Materials & design 28(3) (2007) 1001-1005.
- [155] S. Toschi, Optimization of A354 Al-Si-Cu-Mg Alloy Heat Treatment: Effect on Microstructure, Hardness, and Tensile Properties of Peak Aged and Overaged Alloy, Metals 8(11) (2018) 961.
- [156] J.J. Friel, Practical guide to image analysis, ASM international2000.
- [157] J.-M. Song, C.-F. Huang, H.-Y. Chuang, Microstructural characteristics and vibration fracture properties of Sn-Ag-Cu-TM (TM= Co, Ni, and Zn) alloys, Journal of electronic materials 35(12) (2006) 2154-2163.
- [158] D.A. Lados, D. Apelian, P.E. Jones, J.F. Major, Microstructural mechanisms controlling fatigue crack growth in Al–Si–Mg cast alloys, Materials Science and Engineering: A 468 (2007) 237-245.
- [159] N. Rathod, J. Manghani, Effect of modifier and grain refiner on cast Al-7Si aluminum alloy: A review, International Journal of emerging trends in engineering and development 5(2) (2012) 574-582.
- [160] M. Riestra, E. Ghassemali, T. Bogdanoff, S. Seifeddine, Interactive effects of grain refinement, eutectic modification and solidification rate on tensile properties of Al-10Si alloy, Materials Science and Engineering: A 703 (2017) 270-279.
- [161] L. Ceschini, A. Morri, S. Toschi, S. Seifeddine, Room and high temperature fatigue behaviour of the A354 and C355 (Al–Si–Cu–Mg) alloys: Role of microstructure and heat treatment, Materials Science and Engineering: A 653 (2016) 129-138.
- [162] T. Bogdanoff, L. Lattanzi, M. Merlin, E. Ghassemali, S. Seifeddine, The Influence of Copper Addition on Crack Initiation and Propagation in an Al-Si-Mg Alloy During Cyclic Testing, Materialia (2020) 100787.
- [163] T. Bogdanoff, L. Lattanzi, M. Merlin, E. Ghassemali, A.E. Jarfors, S.J.M.S. Seifeddine, E. A, The complex interaction between microstructural features and crack evolution during cyclic testing in heat-treated Al–Si–Mg–Cu cast alloys, 825 (2021) 141930.
- [164] G. Gyarmati, G. Fegyverneki, Z. Kéri, D. Molnár, M. Tokár, L. Varga, T. Mende, Controlled precipitation of intermetallic (Al, Si) 3Ti compound particles on double oxide films in liquid aluminum alloys, Materials Characterization 181 (2021) 111467.
- [165] X. Cao, J. Campbell, The solidification characteristics of Fe-rich intermetallics in Al-11.5 Si-0.4 Mg cast alloys, Metallurgical and Materials Transactions A 35(5) (2004) 1425-1436.
- [170] M. Schaffer, B. Schaffer, Q. Ramasse, Sample preparation for atomic-resolution STEM at low voltages by FIB, Ultramicroscopy 114 (2012) 62-71.
- [171] Y. Umeno, A. Kushima, T. Kitamura, P. Gumbsch, J. Li, Ab initio study of the surface properties and ideal strength of (100) silicon thin films, physical Review B 72(16) (2005) 165431.
- [172] S.-M. Dubois, G.-M. Rignanese, T. Pardoen, J.-C. Charlier, Ideal strength of silicon: An ab initio study, Physical Review B 74(23) (2006) 235203.
- [173] M. Mueller, G. Žagar, A. Mortensen, In-situ strength of individual silicon particles within an aluminium casting alloy, Acta Materialia (2017).
- [174] M. Mueller, M. Fornabaio, G. Žagar, A. Mortensen, Microscopic strength of silicon particles in an aluminium–silicon alloy, Acta Materialia 105 (2016) 165-175.
- [175] A. Noreyan, Y. Qi, V. Stoilov, Critical shear stresses at aluminum–silicon interfaces, Acta materialia 56(14) (2008) 3461-3469.
- [176] M. Tiryakioğlu, On the heterogeneous nucleation pressure for hydrogen pores in liquid aluminium, International Journal of Cast Metals Research 33(4-5) (2020) 153-156.
- [177] P. Yousefian, M. Tiryakioğlu, Pore formation during solidification of aluminum: reconciliation of experimental observations, modeling assumptions, and classical nucleation theory, Metallurgical and Materials Transactions A 49 (2018) 563-575.
- [178] S. Pomberger, M. Leitner, M.J.M.T.P. Stoschka, Evaluation of surface roughness parameters and their impact on fatigue strength of Al-Si cast material, Materials Today Preceedings 12 (2019) 225-234.
- [179] M. Tiryakioğlu, J. Campbell, C.J.M. Nyahumwa, M.T. B, Fracture surface facets and fatigue life potential of castings, 42(6) (2011) 1098-1103.
- [180] H. Dvorak, E. Schwegtier Jr, Statistical distribution of flaw sizes, International Journal of Fracture Mechanics 8(1) (1972) 110-111.
- [181] M. Tiryakioğlu, Pore size distributions in AM50 Mg alloy die castings, Materials Science and Engineering: A 465(1-2) (2007) 287-289.
- [182] M. Tiryakioğlu, On fatigue life variability in cast Al–10% Si–Mg alloys, Materials Science and Engineering: A 527(6) (2010) 1560-1564.
- [183] T.W. Anderson, D.A. Darling, A test of goodness of fit, Journal of the American statistical association 49(268) (1954) 765-769.
- [184] O. Basquin, The exponential law of endurance tests, Proc Am Soc Test Mater, 1910, pp. 625-630.
- [185] S. Sarkani, T. Mazzuchi, D. Lewandowski, D. Kihl, Runout analysis in fatigue investigation, Engineering Fracture Mechanics 74(18) (2007) 2971-2980.
- [186] R. Hidalgo Coca, J.A. Esnaola Ramos, I. Llavori Osa, M. Larrañaga Serna, N. Herrero Dorca, I. Hurtado Hurtado, A. Kortabarria Lezeta, Influence of Surface Finish and Porosity on the Fatigue behaviour of A356 Aluminium Casting Alloy, 12th International Fatigue Congress (FATIGUE 2018), France, 2018.
- [187] J. Linder, M. Axelsson, H. Nilsson, The influence of porosity on the fatigue life for sand and permanent mould cast aluminium, International Journal of Fatigue 28(12) (2006) 1752-1758.
- [188] B. Zhao, J. Song, L. Xie, Z. Hu, J. Chen, Surface roughness effect on fatigue strength of aluminum alloy using revised stress field intensity approach, Scientific reports 11(1) (2021) 19279.
- [189] B. Skallerud, T. Iveland, G. Härkegård, Fatigue life assessment of aluminum alloys with casting defects, Engineering Fracture Mechanics 44(6) (1993) 857-874.
- [191] L. Wang, N. Limodin, A. El Bartali, J.-F. Witz, R. Seghir, J.-Y. Buffiere, E. Charkaluk, Influence of pores on crack initiation in monotonic tensile and cyclic loadings in lost foam casting A319 alloy by using 3D in-situ analysis, Materials Science and Engineering: A 673 (2016) 362-372.
- [192] R.C. Juvinall, Engineering considerations of stress strain and strength, 1967, 580 P. MCGRAW-HILL BOOK CO., NEW YORK (1967).
- [193] H. Özdeş, M. Tiryakioğlu, On estimating high-cycle fatigue life of cast Al-Si-Mg-(Cu) alloys from tensile test results, Materials Science and Engineering: A 688 (2017) 9-15.
- [194] H. Özdeş, M. Tiryakioğlu, The effect of structural quality on fatigue life in 319 aluminum alloy castings, Journal of Materials Engineering and Performance 26 (2017) 736-743.
9. 저작권:
- 본 자료는 "Toni Bogdanoff"의 논문입니다. "The Effect of Microstructural Features, Defects and Surface Quality on the Fatigue Performance in Al-Si-Mg Cast Alloys"를 기반으로 합니다.
- 논문 출처: http://urn.kb.se/resolve?urn=urn:nbn:se:hj:diva-61111
본 자료는 상기 논문을 바탕으로 요약되었으며, 상업적 목적의 무단 사용을 금합니다.
Copyright © 2025 CASTMAN. All rights reserved.