본 논문 요약은 ['AU J.T.'에 의해 발행된 ['A Comparative Analysis of Grain Size and Mechanical Properties of Al-Si Alloy Components Produced by Different Casting Methods']를 기반으로 작성되었습니다.
1. 개요:
- 제목: 다양한 주조 방법으로 제작된 Al-Si 합금 부품의 결정립 크기 및 기계적 특성 비교 분석 (A Comparative Analysis of Grain Size and Mechanical Properties of Al-Si Alloy Components Produced by Different Casting Methods)
- 저자: 압둘카비르 라지 (Abdulkabir Raji)
- 발행 연도: 2010년 1월
- 발행 저널/학술 단체: AU J.T. 13(3): 158-164
- 키워드: 칠 주조 (Chill casting), 미세 조직 (microstructure), 결정립 미세화 (refinement), 사형 주조 (sand casting), 스퀴즈 주조 (squeeze casting)
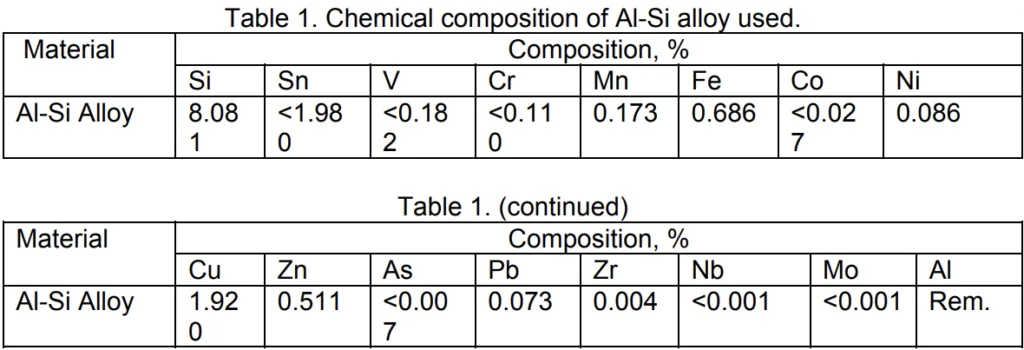
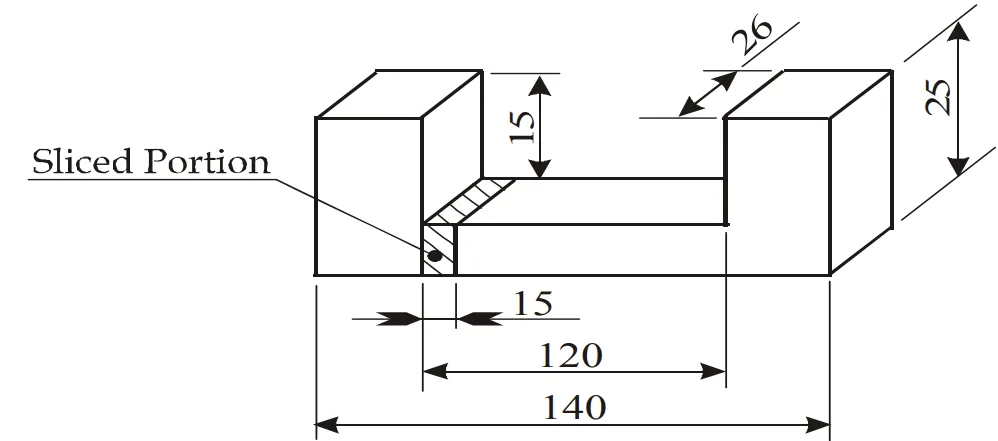
2. 초록 또는 서론
초록
본 연구는 다양한 주조 방식으로 제작된 알루미늄 실리콘 합금 부품의 주조 조직과 기계적 특성을 비교하기 위해 수행되었습니다. 이를 위해 사형 주조, 칠 주조 및 스퀴즈 주조 방법을 사용하여 Al-8%Si 합금으로 동일한 모양과 크기의 제품을 제작했습니다. 연구 결과, 주조 제품의 미세 조직의 결정립 크기는 스퀴즈 주조, 칠 주조, 사형 주조 순으로 증가하는 것으로 나타났습니다. 반대로, 주조 제품의 기계적 특성은 사형 주조, 칠 주조, 스퀴즈 주조 순으로 향상되었습니다. 따라서 스퀴즈 주조 제품은 고품질 부품을 요구하는 엔지니어링 응용 분야에서 주조 상태 그대로 사용될 수 있으며, 칠 주조 및 사형 주조 제품은 비엔지니어링 응용 분야 또는 낮은 품질 부품을 요구하는 엔지니어링 응용 분야에서 주조 상태 그대로 사용될 수 있습니다.
서론
주조 또는 금속 주조는 기원전 2000년까지 거슬러 올라가는 가장 오래된 금속 성형 방법 중 하나이며, 당시 사용된 공정 원리는 오늘날 사용되는 공정과 크게 다르지 않습니다 (Amstead et al. 1979). Wright (1990)와 Rao (1992)는 금속 주조가 훨씬 더 일찍 시작되었다고 주장합니다. Rao (1992)는 기원전 3500년으로 추정하는 반면, Wright (1990)는 주조가 거의 6000년 전으로 거슬러 올라간다고 보았습니다. 그는 또한 주조 분야의 많은 발전이 동양에서 비롯되었으며, 기원전 1000년 이전에 중국인들이 철 주조 방법을 개발했고, 도가니 강 주조법은 나중에 인도에서 발명되었다고 언급했습니다. 동양의 주조 기술 발전은 중동과 유럽으로 수출되었으며, 최초의 주철 대포는 서기 1500년경 영국에서 생산되었습니다. 미국에서 만들어진 최초의 주철 주물은 1642년에 만들어진 주철 조리 냄비였습니다 (Jain 1992). 이 미약한 시작에서 현대 주조 산업은 성장했습니다. 오늘날에는 수많은 주조 공정이 있으며, 이는 수년에 걸쳐 발전해 왔습니다. 이러한 주조 공정은 일반적으로 사형 주조와 특수 주조의 두 가지 광범위한 범주로 분류될 수 있습니다. 특수 주조에는 다이캐스팅, 중력 주조, 인베스트먼트 주조, 원심 주조, 압력 주조 등이 포함되며, 각각 고유한 장단점을 가지고 있습니다. 사형 주조는 전체 주조 생산량의 약 80%를 차지합니다 (Mikhailov 1989). 1979년에는 영국에서 생산된 주물의 80%가 생사형 주형 (Williams 1979)으로 만들어졌으며, 서독에서는 1986년 주조 생산량의 67%가 생사형 주형으로 만들어진 것으로 추정되었습니다 (Weiss and Kleinheyer 1987). 엔지니어링 제품과 소비재는 사형 주조 및 다이캐스팅을 포함한 다양한 기술로 생산됩니다. 각 대체 기술은 고유한 기능과 관련 비용을 특징으로 하며, 이는 특정 응용 분야를 결정합니다. 양호한 비교를 위해 스퀴즈 주조, 압력 다이캐스팅, 칠 주조 및 사형 주조에 의한 제품 생산을 검토합니다. 사형 주조와 스퀴즈 주조를 비교하면서 Lynch et al. (1975)은 사형 주조 부품이 거친 표면 조도를 특징으로 하지만, 사형 주조는 언더컷과 채널을 부품에 주조할 수 있고, 동시에 동일한 주형에서 많은 소형 부품을 주조하여 생산성을 높일 수 있는 저렴한 제조 수단을 제공한다고 관찰했습니다. 반면에 스퀴즈 주조는 수축 또는 미세기공이 없고, 사형 주조보다 더 매끄러운 표면 조도와 더 정밀한 공차를 가진 완전 밀도 부품을 제공할 수 있습니다. 또한 생산 속도가 빠르고 금속 이용 효율이 높아 비용 효율적인 제조 공정입니다. 스퀴즈 주조로 얻을 수 있는 최대 중량은 알루미늄 합금의 경우 19kg입니다 (Clegg 1991; Yue and Chadwick 1996). 그러나 칠 주조로 얻을 수 있는 최대 중량은 알루미늄 합금, 마그네슘 합금, 주철 및 구리 합금에 대해 각각 70kg, 25kg, 13.6kg 및 9kg입니다 (West and Gruback 1989; Clegg 1991). Clegg (1991)는 또한 표면 조도, 치수 정확도, 최소 단면 두께 및 생산량 영역에서 스퀴즈 주조와 기타 유사한 기술을 비교했습니다. 스퀴즈 주조의 표면 조도는 압력 다이캐스팅으로 얻은 표면 조도와 유사하며, 0.4 ~ 3.2µm 범위 내에 있으며, 칠 주조로 얻은 표면 조도 (3.2 ~ 6.3µm 범위)보다 우수합니다. 단일 다이 반쪽에서 칠 주조로 만든 주물의 치수 공차 또는 정확도는 ±0.25mm 이내입니다. 중요한 치수가 25mm 미만인 압력 다이캐스팅의 경우, 공차는 아연 합금의 경우 ±0.08mm, 알루미늄 합금의 경우 ±0.10mm, 구리 합금의 경우 ±0.18mm가 될 수 있습니다. 25 ~ 300mm 범위 내의 치수의 경우, 앞서 언급한 세 가지 합금 등급에 대해 각각 ±0.025mm, ±0.038mm 및 ±0.051mm의 25mm 증가당 추가 허용 오차가 적용되어야 합니다. 반면에 스퀴즈 주조로 만든 알루미늄 합금 주물의 치수 공차는 0.2mm/100mm입니다 (Clegg 1991). 칠 주조의 합리적인 최소 단면 두께는 5mm인 반면, 아연 합금에서는 0.5mm, 알루미늄 합금에서는 0.8mm, 구리 합금에서는 1.5mm만큼 작은 단면을 압력 다이캐스팅으로 만들 수 있습니다. 스퀴즈 주조는 단면이 6mm 이상인 주물에 더 적합하지만, 0.3mm의 얇은 단면도 스퀴즈 주조로 만들어졌습니다 (Clegg 1991). 스퀴즈 주조는 다른 제조 공정에 비해 비교적 새로운 주조 방법으로, 주조물의 미세 조직을 공정 제어를 통해 쉽게 조작하여 필요한 최적의 특성을 얻을 수 있다는 장점이 있습니다. 또한 핵제 (nucleating agents)를 사용할 수도 있지만, 일반적으로는 필요하지 않습니다 (Yue and Chadwick 1996). Lynch et al. (1975)은 스퀴즈 주조물이 미세한 결정립, 좁은 덴드라이트 암 간격 및 작은 구성 입자로 미세 조직을 미세화한다고 관찰했습니다. 고압과 금속 주형 (다이)의 결합 효과는 높은 열전달 계수로 이어져, 핵 생성 속도와 후속 핵 성장 속도가 높아져 미세 조직의 변화를 초래합니다. 이러한 주장은 Yong and Clegg (2004)에 의해 뒷받침되었습니다. 주조 공정 개선을 위해 많은 연구가 수행되었음에도 불구하고, 공정에 대한 더 나은 이해를 위해서는 더 많은 연구가 여전히 필요합니다. 본 연구는 사형 주조, 칠 주조 및 스퀴즈 주조 방법으로 주조된 알루미늄 실리콘 합금 부품의 결정립 크기와 기계적 특성을 비교하기 위해 수행되었습니다.
3. 연구 배경:
연구 주제 배경:
금속 주조, 즉 주조 공정은 가장 오래된 금속 성형 기술 중 하나입니다. 기원전 2000년경에 시작된 주조의 기본 원리는 수천 년 동안 변함없이 유지되어 왔습니다. 현대 주조 기술은 사형 주조와 특수 주조로 광범위하게 분류되는 다양한 주조 공정으로 발전했습니다. 특수 주조 방법에는 다이캐스팅, 중력 주조, 인베스트먼트 주조, 원심 주조 및 압력 주조가 포함되며, 각 방법은 고유한 장점과 단점을 가지고 있습니다. 사형 주조는 여전히 널리 사용되는 방법으로, 전체 주조 생산량의 약 80%를 차지합니다.
기존 연구 현황:
엔지니어링 제품과 소비재는 사형 주조 및 다이캐스팅을 포함한 다양한 기술을 사용하여 제조됩니다. 각 기술은 고유한 기능과 비용 구조를 가지며, 이는 특정 응용 분야를 결정합니다. 이전 연구에서는 사형 주조와 스퀴즈 주조를 비교했습니다. Lynch et al. (1975)은 사형 주조가 거친 표면 조도를 특징으로 하지만, 복잡한 형상에 적합한 비용 효율적인 제조 방법을 제공한다고 관찰했습니다. 반대로 스퀴즈 주조는 향상된 표면 조도와 치수 공차를 가진 완전 밀도 부품을 생산합니다. Clegg (1991)와 Yue and Chadwick (1996)는 알루미늄 합금에 대한 스퀴즈 주조로 얻을 수 있는 최대 중량을 19kg으로 강조했습니다.
연구의 필요성:
주조 공정 개선을 목표로 한 광범위한 연구에도 불구하고, 보다 포괄적인 이해를 위해서는 추가적인 연구가 필요합니다. 특히, 다양한 주조 방법 간의 결정립 크기 및 기계적 특성에 초점을 맞춘 비교 연구가 필요합니다. 본 연구는 사형 주조, 칠 주조 및 스퀴즈 주조가 알루미늄 실리콘 합금 부품의 미세 조직 및 기계적 특성에 미치는 영향을 비교하기 위해 설계되었습니다.
4. 연구 목적 및 연구 질문:
연구 목적:
주요 연구 목적은 사형 주조, 칠 주조 및 스퀴즈 주조 방법을 사용하여 생산된 알루미늄 실리콘 합금 부품의 미세 조직의 결정립 크기와 기계적 특성을 비교 분석하는 것입니다.
핵심 연구 질문:
핵심 연구는 다음 사항을 평가하고 비교하는 데 중점을 둡니다.
- 사형 주조, 칠 주조 및 스퀴즈 주조로 인한 Al-Si 합금 미세 조직의 결정립 크기 변화.
- 세 가지 주조 방법 각각으로 생산된 Al-Si 합금 부품의 기계적 특성, 특히 경도, 극한 인장 강도 (UTS), 항복 강도 및 연신율.
연구 가설:
본 연구는 다음과 같은 가설을 암묵적으로 설정합니다.
- 스퀴즈 주조는 Al-Si 합금 부품의 미세 조직에서 가장 미세한 결정립 크기를 나타내고, 그 다음으로 칠 주조, 그리고 가장 조대한 결정립 크기를 나타내는 사형 주조 순서가 될 것입니다.
- 경도, UTS, 항복 강도 및 연신율을 포함한 기계적 특성은 스퀴즈 주조 부품에서 가장 우수하고, 그 다음으로 칠 주조 부품, 그리고 사형 주조 부품이 가장 낮은 기계적 특성을 나타낼 것입니다.
5. 연구 방법론
연구 설계:
본 연구에서는 비교 실험 설계를 채택했습니다. 알루미늄-실리콘 합금 부품은 사형 주조, 칠 주조 및 스퀴즈 주조의 세 가지 다른 주조 방법을 사용하여 제작되었습니다. 그런 다음 주조된 부품의 결과 미세 조직과 기계적 특성을 비교했습니다.
데이터 수집 방법:
- 재료 준비: Al-Si 합금 스크랩을 사용하고, 에너지 분산형 X선 형광 분석법 (EDXRF) 및 고전적인 습식 분석법을 사용하여 조성을 확인했습니다.
- 주조 공정: 사형 주조, 칠 주조 및 스퀴즈 주조는 지정된 주입 온도와 스퀴즈 주조의 경우 다양한 스퀴즈 압력 (75MPa, 100MPa, 125MPa, 150MPa)을 사용하여 수행되었습니다. Raji와 Khan (2005; 2006)이 설명한 방법을 따라 주조 매개 변수를 제어했습니다.
- 금속 조직 검사: 시편은 절단, 연삭, 연마 및 0.24% 불산 (HF)으로 에칭하여 준비했습니다. 미세 조직은 Pol Jenalab 광학 현미경을 사용하여 x125 배율로 관찰하고 사진 촬영했습니다.
- 기계적 시험: 인장 시험은 만능 시험기를 사용하여 수행했으며, 경도는 Raji와 Khan (2006)이 설명한 절차에 따라 Rockwell 경도 시험기를 사용하여 측정했습니다.
분석 방법:
- 정량적 결정립 크기 분석: 결정립 크기는 특정 배율에서 결정립 수를 기반으로 계산된 미국 재료 시험 협회 (ASTM) 결정립 크기 번호 (n)를 사용하여 정량적으로 평가했습니다.
- 기계적 특성 비교 분석: 경도, UTS, 항복 강도 및 연신율에 대해 얻은 데이터를 표로 작성하고 다양한 주조 방법 및 공정 매개 변수 (주입 온도, 스퀴즈 압력)에 걸쳐 비교했습니다. 통계 분석은 추세와 차이를 보여주기 위해 표에 데이터를 제시하는 방식으로 암묵적으로 사용되었습니다.
연구 대상 및 범위:
- 재료: 알루미늄-실리콘 (Al-Si) 합금, 특히 Al-8%Si 합금.
- 주조 방법: 사형 주조, 칠 주조 및 스퀴즈 주조.
- 공정 매개 변수: 주입 온도 (사형 주조의 경우 650°C, 700°C, 750°C, 800°C, 칠 및 스퀴즈 주조의 경우 650°C, 700°C, 750°C), 스퀴즈 압력 (스퀴즈 주조의 경우 75MPa, 100MPa, 125MPa, 150MPa).
- 범위: 본 연구는 지정된 Al-Si 합금에 대한 이러한 세 가지 주조 방법의 비교와 결정립 크기 및 선택된 기계적 특성 평가로 제한됩니다.
6. 주요 연구 결과:
주요 연구 결과:
- 결정립 크기: 미세 조직 분석 결과, 결정립 크기는 스퀴즈 주조 < 칠 주조 < 사형 주조 순으로 증가하는 것으로 나타났습니다. 스퀴즈 주조물이 가장 미세한 결정립을 나타냈고, 사형 주조물이 가장 조대한 결정립을 나타냈습니다. 스퀴즈 주조에서 스퀴즈 압력을 증가시키면 결정립 크기가 더 미세해졌습니다.
- 경도: 스퀴즈 주조 부품은 칠 주조보다 43-47% 증가한 최대 HRF58.0의 가장 높은 경도 값을 나타냈습니다. 칠 주조는 사형 주조보다 경도가 높았습니다. 사형 주조는 HRF33.0에서 HRF35.5 범위의 가장 낮은 경도를 나타냈습니다.
- 극한 인장 강도 (UTS): 스퀴즈 주조는 온도와 압력에 따라 146에서 232 MPa 범위의 가장 높은 UTS를 나타냈습니다. 칠 주조는 약 115 MPa의 UTS를 가졌습니다. 사형 주조는 65에서 102 MPa 범위의 가장 낮은 UTS를 가졌습니다.
- 항복 강도: 항복 강도의 추세는 UTS의 추세를 반영하여 스퀴즈 주조가 가장 높은 값을 나타내고, 그 다음으로 칠 주조, 사형 주조 순이었습니다.
- 연신율: 스퀴즈 주조는 가장 높은 연신율 (3.4-3.8%)을 나타냈고, 그 다음으로 칠 주조 (2.4-2.7%), 사형 주조 (2.0-2.3%) 순이었습니다.
제시된 데이터 분석:
표 2는 다양한 주조 방법으로 생산된 알루미늄-실리콘 합금의 특성을 보여줍니다. 사형 주조에서 칠 주조, 스퀴즈 주조로 주조 방법이 변경됨에 따라 ASTM 결정립 크기 번호 (n*)가 증가하여 결정립 크기가 더 미세해지는 명확한 추세를 보여줍니다. 반대로 UTS, 항복 강도 및 경도 값은 동일한 순서로 증가하여 스퀴즈 주조를 통해 얻은 더 미세한 결정립 구조로 기계적 특성이 향상됨을 보여줍니다. 연신율 또한 덜 뚜렷하지만 유사한 추세를 따릅니다.
데이터는 사형 주조 (0 MPa 스퀴즈 압력)의 경우 주입 온도를 650°C에서 800°C로 높이면 결정립 미세화 (더 낮은 n*)가 감소하고 UTS, 항복 강도 및 경도가 감소하는 것으로 나타났습니다.
스퀴즈 주조의 경우 스퀴즈 압력을 높이면 일반적으로 결정립 크기가 더 미세해지고 (더 높은 n*) 기계적 특성이 향상됩니다. 그러나 주입 온도의 영향은 테스트된 범위 (650°C ~ 750°C) 내에서 스퀴즈 압력의 상당한 영향에 비해 일관성이 떨어집니다.
그림 2-5는 결정립 크기 차이를 시각적으로 확인시켜줍니다. 그림 2 (사형 주조), 그림 3 (칠 주조), 그림 4 및 5 (스퀴즈 주조)는 x125 배율의 현미경 사진을 보여줍니다. 현미경 사진은 사형 주조가 더 조대한 결정립 (그림 2)을 가지고 있고, 칠 주조는 더 미세한 결정립 (그림 3)을 가지고 있으며, 스퀴즈 주조는 가장 미세한 결정립 구조 (그림 4 및 5)를 나타내는 것을 보여줍니다. 흰색 패치는 알루미늄 (α)의 1차 알파 고용체를 나타내고, 검은색 패치는 공정 공정 (α+Si)을 나타냅니다.
그림 목록:
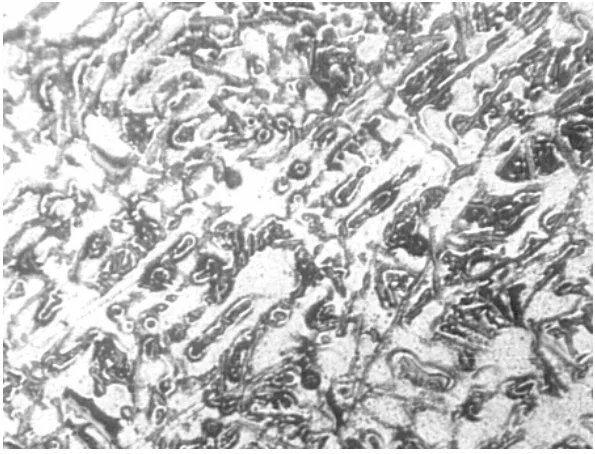
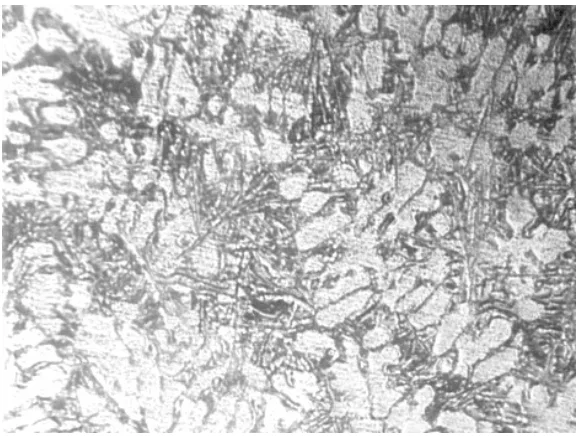
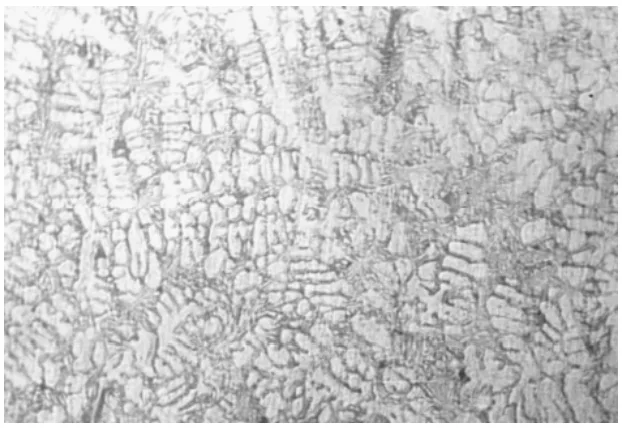
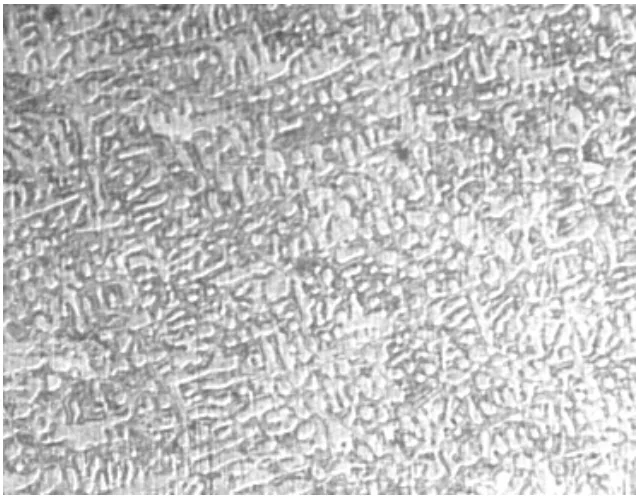
- 그림 1. 금속 조직 시험을 위한 주조물의 절단 부분; 치수는 mm 단위입니다.
- 그림 2. 700°C 주입 온도에서 사형 주조된 Al-8%Si 합금의 현미경 사진 (x125); 흰색 패치는 1차 α이고 검은색 패치는 공정 공정, α + Si입니다.
- 그림 3. 650°C 주입 온도에서 칠 주조된 Al-8%Si 합금의 현미경 사진 (x125); 흰색 패치는 1차 α이고 검은색 패치는 공정 공정, α + Si입니다.
- 그림 4. 650°C 주입 온도 및 100MPa 스퀴즈 압력에서 스퀴즈 주조된 Al-8%Si 합금의 현미경 사진 (x125); 흰색 패치는 1차 α이고 검은색 패치는 공정 공정, α + Si입니다.
- 그림 5. 750°C 주입 온도 및 125MPa 스퀴즈 압력에서 스퀴즈 주조된 Al-8%Si 합금의 현미경 사진 (x125); 흰색 패치는 1차 α이고 검은색 패치는 공정 공정, α + Si입니다.
7. 결론:
주요 연구 결과 요약:
본 연구는 다음과 같은 결론을 내렸습니다.
- 주조물의 미세 조직은 사형 주조, 칠 주조, 스퀴즈 주조 순으로 결정립 미세화 정도가 증가합니다.
- 일반적으로 스퀴즈 주조의 기계적 특성이 칠 주조 및 사형 주조보다 높으며, 사형 주조의 기계적 특성이 가장 낮습니다.
- 스퀴즈 주조는 칠 주조 및 사형 주조에 비해 스퀴즈 주조물의 기계적 특성을 크게 향상시킵니다.
- 사형 주조는 비엔지니어링 응용 분야 및 낮은 기계적 특성 요구 사항이 있는 엔지니어링 응용 분야에서 주조 상태 그대로 사용될 수 있습니다. 칠 주조 및 스퀴즈 주조는 각각 중간 및 높은 기계적 특성을 요구하는 엔지니어링 응용 분야에서 주조 상태 그대로 활용될 수 있습니다.
연구의 학문적 의의:
본 연구는 다양한 주조 방법이 Al-Si 합금의 미세 조직 및 기계적 특성에 미치는 영향에 대한 기본적인 이해에 기여합니다. 칠 주조 및 스퀴즈 주조와 관련된 더 높은 냉각 속도가 결정립 미세화 및 향상된 기계적 특성으로 이어진다는 확립된 지식을 강화하면서 사형, 칠 및 스퀴즈 주조의 비교 성능에 대한 정량적 데이터를 제공합니다. 본 연구는 Al-Si 합금에서 우수한 재료 특성을 달성하는 데 있어 스퀴즈 주조의 효과를 입증합니다.
실용적 의미:
본 연구 결과는 Al-Si 합금 부품의 원하는 성능 특성에 따라 적절한 주조 방법을 선택하는 데 있어 엔지니어와 제조업체에 실용적인 지침을 제공합니다. 우수한 기계적 특성을 가진 고품질 부품이 필요한 응용 분야의 경우 스퀴즈 주조가 선호되는 방법입니다. 칠 주조는 사형 주조보다 향상된 특성의 균형을 제공하며 중간 성능 응용 분야에 적합할 수 있습니다. 사형 주조는 낮은 기계적 특성이 허용되는 비용에 민감한 응용 분야에 여전히 실행 가능한 옵션입니다.
연구의 한계 및 향후 연구 분야:
본 연구는 Al-8%Si 합금과 특정 범위의 주조 매개 변수로 제한됩니다. 향후 연구에서는 다음 사항을 탐구할 수 있습니다.
- 이러한 주조 방법의 비교 성능에 대한 더 넓은 범위의 합금 조성의 영향.
- 특정 Al-Si 합금에 대한 기계적 특성을 최대화하기 위한 스퀴즈 주조 매개 변수 (압력, 온도, 속도)의 최적화.
- 이러한 주조 방법으로 생산된 부품의 피로 강도 및 충격 인성과 같은 기타 기계적 특성 조사.
- 포괄적인 방법 선택 가이드를 제공하기 위해 생산 비용과 달성 가능한 기계적 특성을 고려한 각 주조 방법의 경제성 분석.
8. 참고 문헌:
- Amstead, B.H.; Ostwald, P.F.; and Begeman, M.L. 1979. Manufacturing processes. 7th ed., John Wiley and Sons, New York, NY, USA.
- Askeland, D.R. 1985. The science and engineering of materials. PWS Publishing Co., Boston, MA, USA.
- Clegg, A.J. 1991. Precision casting processes. Pergamon Press PLC, Oxford, UK.
- Jain, P.L. 1992. Principles of foundry technology. 3rd ed., Tata Mc Graw-Hill Publishing Co., Ltd., New Delhi, India.
- Lynch, R.F.; Olley, R.P., and Gallagher, P.C.J. 1975. Squeeze casting of brass and bronze. Paper No.75-90. AFS Trans. 83: 561-8.
- Mikhailov, A.M. 1989. Metal casting. Mir Publishers, Moscow, USSR.
- Raji, A.; and Khan, R.H. 2005. Effect of pouring temperature on the properties of Al-8%Si alloy sand cast components. Global J. Engin. Res. 4(1&2): 1-4.
- Raji, A.; and Khan, R.H. 2006. Effects of pouring temperature and squeeze pressure on the properties of Al-8%Si alloy squeeze cast components. AU J.T. 9(4): 229-37, April.
- Rao, P.N. 1992. Manufacturing technology: Foundry, forming and welding. Tata McGraw-Hill Publishing Co., Ltd., New Delhi, India.
- Weiss, R.; and Kleinheyer, U. 1987. Current trends in the use of moulding and core making processes. Casting Plant Technol. 3(4): 10-9.
- West, C.E.; and Gruback, T.E. 1989. Permanent mold casting. In: ASM. 1989. Metals handbook (Casting). vol. 15, pp. 275-85, ASM, Metal Park, OH, USA.
- Williams, R. 1997. The present status and future of green sand in the foundry industry. The British Foundryman 72(6, Special Supplement): 53-62.
- Wright, R.T. 1990. Manufacturing systems. The Goodheart-Willcox Co., Inc., Tinley Park, IL, USA.
- Yong, M.S.; and Clegg, A.J. 2004. Process optimisation for a squeeze cast magnesium alloy. J. Materials Process. Technol. 145(1): 134-41, January.
- Yue, T.M.; and Chadwick, G.A. 1996. Squeeze casting of light alloys and their composites. J. Materials Process. Technol. 58(2-3): 302-7, March.
9. 저작권:
- 본 자료는 "압둘카비르 라지 (Abdulkabir Raji)"의 논문 "다양한 주조 방법으로 제작된 Al-Si 합금 부품의 결정립 크기 및 기계적 특성 비교 분석 (A Comparative Analysis of Grain Size and Mechanical Properties of Al-Si Alloy Components Produced by Different Casting Methods)"을 기반으로 합니다.
- 논문 출처: https://www.ajol.info/index.php/ajt/article/view/54637
본 자료는 상기 논문을 요약한 것으로, 상업적 목적으로 무단 사용하는 것을 금지합니다.
Copyright © 2025 CASTMAN. All rights reserved.