본 논문 요약은 [일본 다이캐스팅 학회 (Japan Die Casting Congress)]에서 발표된 [Added Value of Process Modelling in Development of Automotive Die Casting Parts] 논문을 기반으로 작성되었습니다.
1. 개요:
- 제목: 자동차 다이캐스팅 부품 개발에 있어서의 공정 모델링의 부가가치 (Added Value of Process Modelling in Development of Automotive Die Casting Parts)
- 저자: Andre Le-Nezet, Nicolas De Reviere, Loic Calba, Badarinath Kalkunte
- 발표 연도: 2018년
- 발표 학술대회/학회: 일본 다이캐스팅 학회 (Japan Die Casting Congress)
- 키워드: 다이캐스팅 (Die Casting), HPDC (고압 다이캐스팅), 부품 설계 (part design), 금형 설계 (die design), 주조 개발 루프 (casting development loop), 디지털 튜닝 (digital tuning), 금형 사이클링 (die cycling), 시뮬레이션 (simulation), 기공 (Porosity), 워크플로우 (Workflow), 매크로 (Macros), 자동화 (Automatization), 르노 (Renault), ESI

2. 연구 배경:
자동차 시장은 고성능 및 우수한 기계적 물성과 구조적 건전성을 갖춘 주조품에 대한 요구가 증가하고 있습니다. 일반적으로 중력 및 저압 다이캐스팅이 이러한 요구 사항을 충족하는 데 사용되지만, 고압 다이캐스팅(HPDC)은 짧은 샷 시간과 비용 효율성으로 대량 생산에 유리합니다. 그러나 HPDC 공정 자체의 한계로 인해 증가하는 요구 사항을 충족하는 데 어려움이 있습니다. 이러한 어려움을 극복하고 경쟁력을 유지하기 위해 HPDC 공정 관련 혁신과 기술 개발이 지속적으로 이루어지고 있습니다.
과거에는 공정 시뮬레이션 소프트웨어의 활용이 제한적이었습니다. 사용자 그래픽 인터페이스(GUI)가 사용자 친화적이지 못하고 공정 중심적이지 않아 활용도가 낮았습니다. 따라서 시뮬레이션은 문제 발생 후 해결(치료적 조치)하는 용도로 주로 사용되었으며, 설계 단계에서 문제를 예방하는 용도로는 활용되지 못했습니다.
그러나 컴퓨터 하드웨어의 발전, 사용자 친화적이고 주조 공정 중심적인 GUI 설계 기술의 발전, 경량 주조품 개발을 위한 제품 설계 및 재료의 복잡성 증가로 인해 공정 시뮬레이션의 중요성이 더욱 커지고 있습니다. 제품 개발 초기 단계부터 시뮬레이션을 통합하는 것은 리드 타임 단축, 비용 최적화 및 고품질 주조품 생산에 필수적입니다.
3. 연구 목적 및 연구 질문:
본 연구는 자동차 다이캐스팅 부품 개발에 있어서 공정 모델링의 부가가치를 입증하는 것을 목표로 합니다. 특히, 르노의 사례를 통해 최첨단 시뮬레이션 방법론을 적용하여 부품 및 금형 설계의 디지털 튜닝을 달성하는 방법을 조사합니다.
본 연구에서 다루는 핵심 연구 질문은 다음과 같습니다. 최신 시뮬레이션 방법론은 자동차 다이캐스팅 부품 개발 프로세스를 어떻게 개선하여 물리적 시행착오 방식에서 예측 가능하고 효율적인 디지털 접근 방식으로 전환할 수 있는가?
본 연구의 기본 가설은 공정 모델링이 설계 초기 단계에 통합될 때, 주조 엔지니어가 결함을 예측하고, 공정 변수를 최적화하며, 궁극적으로 HPDC 부품의 설계와 최종 품질을 향상시킬 수 있다는 것입니다.
4. 연구 방법론:
본 논문은 르노에서 개발한 2011년 AlSi9Cu3 기어박스 하우징을 사례 연구로 제시합니다. 연구는 ESI ProCAST 2018.0 소프트웨어를 사용하여 4단계 디지털 연구 방법론을 적용합니다. 이 방법론은 다음과 같이 구성됩니다.
- 1단계: 제조 가능성 검토 (베어 캐스팅): 초기 단계에서는 단순화된 금형 표현으로 충전 공정을 시뮬레이션하여 부품의 제조 가능성을 평가합니다. 목표는 제품 설계 초기 단계에서 공기 혼입 및 핫 스팟과 같은 잠재적인 문제를 신속하게 식별하는 것입니다.
- 2단계: 사출 시스템 설계 (비스킷/러너/게이트/오버플로우): 이 단계에서는 러너, 게이트 및 오버플로우를 포함한 사출 시스템의 설계 및 검증에 중점을 둡니다. 이 단계의 시뮬레이션은 충전 패턴과 사출 시스템 설계와 관련된 공기 혼입 및 수축 위험 가능성을 평가합니다.
- 3단계: 금형 설계 (냉각 라인 제외): 여기서는 냉각 시스템을 제외하고 완전한 금형 형상을 설계합니다. 열 사이클링 시뮬레이션을 수행하여 금형 온도 분포를 파악하고 냉각이 필요한 핫 스팟을 식별합니다.
- 4단계: 금형 설계 및 공정 검증 (전체 금형 설계): 마지막 단계에서는 냉각 시스템을 금형 설계에 통합합니다. 열 사이클링, 충전 및 응고를 포함한 전체 금형 설계 및 공정 변수를 검증하기 위해 포괄적인 시뮬레이션을 수행하여 부품 품질을 예측합니다.
데이터 수집 방법: 본 연구는 방법론의 각 단계에서 ESI ProCAST 2018.0에서 생성된 시뮬레이션 데이터를 사용합니다.
분석 방법: 분석은 주로 질적 분석이며, 충전 시간, 수축 기공 및 온도 분포 플롯을 통해 시뮬레이션 결과를 해석하는 데 중점을 둡니다. 각 설계 반복의 효과는 이러한 시뮬레이션 출력 결과를 기반으로 평가됩니다. 시뮬레이션 결과의 유효성을 검증하기 위해 시뮬레이션된 수축 기공과 실제 부품 절단면을 시각적으로 비교합니다.
연구 대상 및 범위: 본 연구는 르노 공정 엔지니어링 내 자동차 HPDC 부품 개발 프로세스에 초점을 맞추고 특정 기어박스 하우징을 사례 연구로 사용합니다. 범위는 ESI ProCAST를 사용한 설명된 4단계 디지털 시뮬레이션 방법론의 적용으로 제한됩니다.
5. 주요 연구 결과:
4단계 시뮬레이션 방법론은 다이캐스팅 부품 개발 프로세스의 각 단계에서 귀중한 통찰력을 제공했습니다.
- 1단계: 제조 가능성 검토 (베어 캐스팅): 캐비티 충전 시간 시뮬레이션(그림 1a)은 마지막으로 채워지는 영역을 식별하여 공기 제거를 용이하게 하는 오버플로우의 적절한 위치를 제시했습니다. 수축 기공 분석(그림 1b)은 주조품에서 상당한 핫 스팟을 강조하여 잠재적인 기공 위험을 나타냈습니다. "그림 1a는 마지막으로 채워지는 영역을 보여줍니다." "그림 1b는 기공을 유발할 수 있는 주조품의 주요 핫 스팟을 강조합니다."
- 2단계: 사출 시스템 설계 (비스킷/러너/게이트/오버플로우): 점진적 충전 시뮬레이션(그림 2a)은 초기 오버플로우 위치 설정을 검증했습니다. 충전 시간 분석(그림 2b 왼쪽)은 오버플로우 위치의 효과를 확인했습니다. 수축 기공 예측(그림 2b 오른쪽)은 1단계와 유사한 위험 영역을 보여주었으며, 비스킷과 러너를 시뮬레이션에 포함하여 열 기울기 및 충전 프로파일 변경으로 인해 잠재적으로 추가적인 기공 영역이 발생했습니다. "그림 2a의 점진적 충전은 초기 오버플로우의 적절한 위치 설정을 확인합니다…" "그림 2b(오른쪽)의 수축 기공 플롯은 1단계에서 관찰된 것과 거의 유사한 위험을 보여줍니다."
- 3단계: 금형 설계 (냉각 라인 제외): 열 금형 사이클링 시뮬레이션(그림 3a)은 가장 뜨거운 금형/주조 인터페이스에서 온도 프로파일을 제공하여 사이클 전반에 걸쳐 금형 온도 안정화를 나타냅니다. 핫 스팟 분석(그림 3b)은 2011년 금형 설계의 기존 냉각 회로 위치뿐만 아니라 이동 및 고정 금형 모두에서 핫 스팟 위치를 보여주었습니다. "그림 3a는 가장 뜨거운 금형/주조 인터페이스에서 촬영한 샷을 통한 온도 프로파일을 보여줍니다." "그림 3b는 이동 및 고정 금형 모두에서 핫 스팟을 보여줍니다…"
- 4단계: 금형 설계 및 공정 검증 (전체 금형 설계): 냉각 회로를 사용한 열 사이클링 시뮬레이션(그림 4b 왼쪽)은 금형 열 정상 상태가 냉각 시스템이 없는 시뮬레이션과 거의 동일하게 달성됨을 보여주었습니다. 그러나 내부 금형 냉각은 핫 스팟 영역에서 금형 표면에서 약 70°C의 상당한 온도 감소를 가져왔습니다. 점진적 충전 시뮬레이션(그림 4c)은 난류가 최소화된 부드러운 슬리브 충전을 보여주었습니다. 공기 혼입 분석(그림 4d)은 코어 핀 및 오버플로우 근처의 잠재적인 공기 혼입 위치를 나타냈습니다. 부품 충전 시간 플롯(그림 4e 왼쪽)은 시뮬레이션 단계에서 일관된 충전 동작을 보여주었습니다.
- 실제와의 비교: 세 가지 주요 영역(보스)에 대한 시뮬레이션된 수축 기공과 실제 부품 절단면의 비교(그림 5b)는 시뮬레이션 방법론의 예측 능력을 검증하면서 양호한 일치를 보였습니다. "그림 5b는 시뮬레이션 루프의 여러 단계에서 세 보스 모두에 대한 수축 기공 비교 대 실제 절단면을 요약하고 실제와 양호한 일치를 확인합니다."
그림 목록:
- 그림 1a: 캐비티 충전 시간 (Cavity Filling Time)
- 그림 1b: 주요 핫 스팟을 강조하는 수축 기공 플롯 (Shrinkage Porosity plot highlighting the main hot spots in the casting)
- 그림 2a: 캐비티 내 점진적 충전 (Progressive filling in the cavity)
- 그림 2b: 오버플로우 위치가 마지막으로 채워졌음을 확인하는 충전 시간 플롯 (왼쪽) 및 핫 스팟을 강조하는 수축 기공 (오른쪽) (Filling time plot (left), confirming the overflow locations to have filled the last and Shrinkage Porosity (right) highlighting the hot spots in the casting)
- 그림 3a: 가장 뜨거운 금형/주조 인터페이스에서 촬영한 금형 온도 프로파일 (Die temperature profile taken at hottest mold/casting interface)
- 그림 3b: 8 사이클(샷) 종료 시 이동 금형(상단) 및 고정 금형(하단)의 금형 온도 프로파일. 밝은 파란색 원과 막대는 2011년 금형의 냉각 회로를 나타냅니다. (Die temperature profile of Mobile Die (Top) and Fixed Die (Bottom) at the end of 8 cycles (shots). Light blue circles and bars indicate the cooling circuits of the 2011 die)
- 그림 4a: 금형 냉각 회로 (Die cooling circuits)
- 그림 4b: 가장 뜨거운 금형/주조 인터페이스에서 촬영한 금형 온도 프로파일 (왼쪽), 금형이 열리기 직전에 냉각수의 영향을 보여주는 금형 단면 (오른쪽) (Die temperature profile taken at hottest mold/casting interface, (left): cross section of the die showing the influence water coolants just before the mold is opened, (right))
- 그림 4c: 슬리브 충전 및 슬리브에서 캐비티 충전으로의 플런저 이동부터 시작하는 점진적 충전 (Progressive filling starting from the sleeve filling and plunger movement in the sleeve to cavity filling)
- 그림 4d: 공기 혼입 (Air Entrainment)
- 그림 4e: 충전 시간 플롯 (왼쪽) 및 수축 기공 (오른쪽) (Filling time plot (left), and Shrinkage Porosity (right))
- 그림 5a: 기공이 없어야 하는 부품으로 간주되는 3개의 주요 영역(보스)을 보여줍니다. (Shows the 3 main zones (boss) which are mandatory for this part to be considered porosity free)
- 그림 5b: 모든 3개 주요 영역에 대한 시뮬레이션과 실제 절단면의 수축 기공 비교를 보여줍니다. (Shows the shrinkage porosity comparison of simulation vs real cut sections for all the 3 main zones)
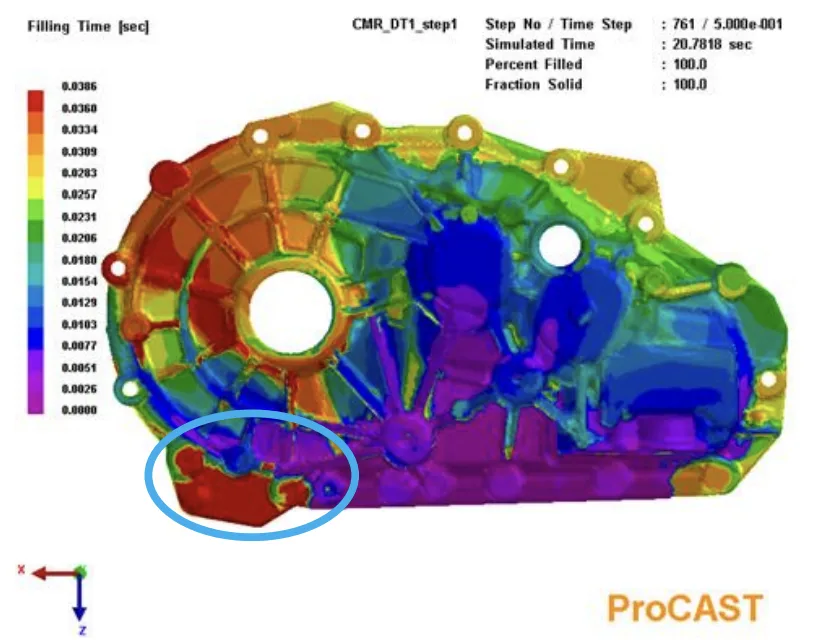
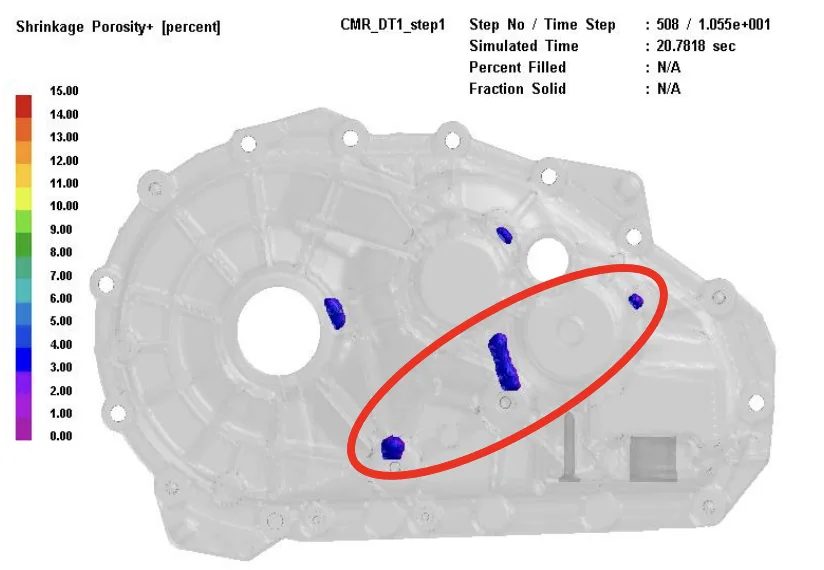
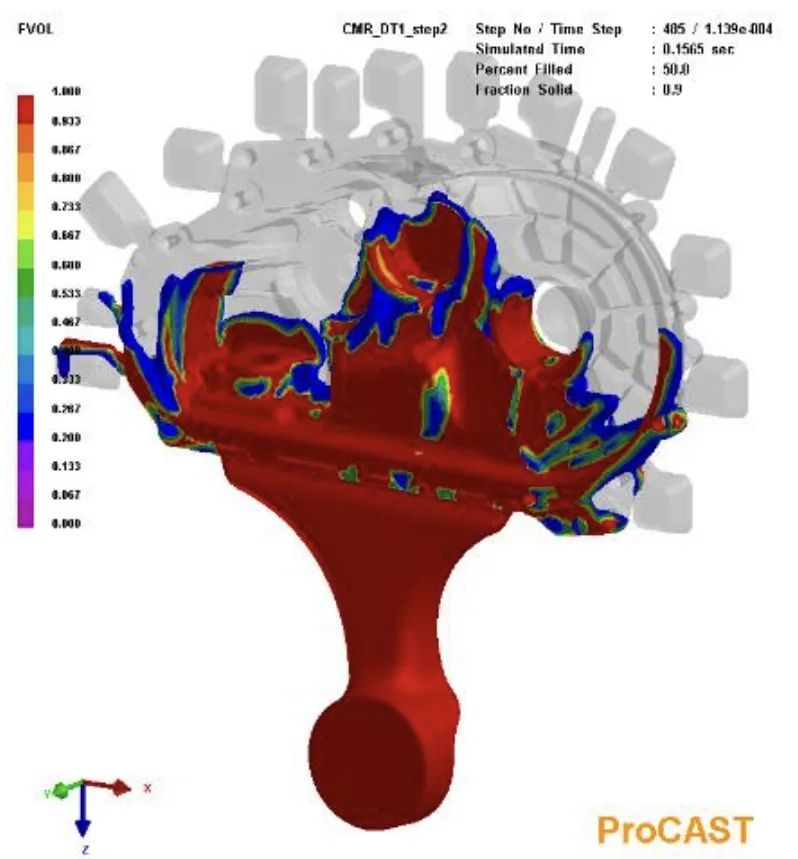
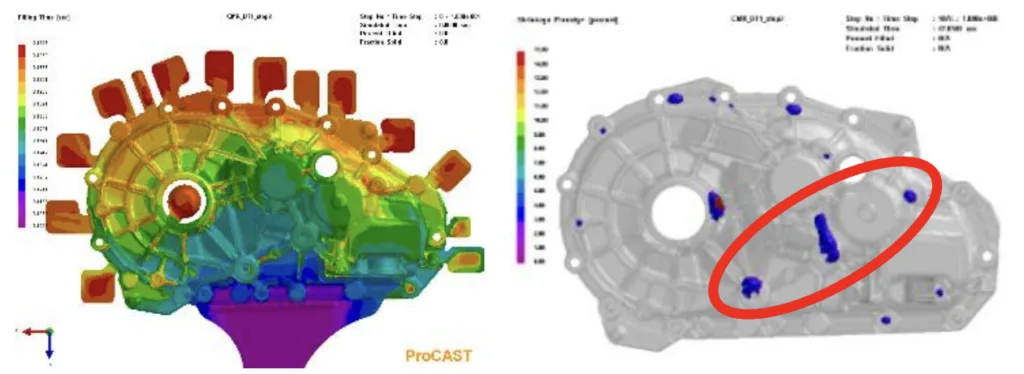
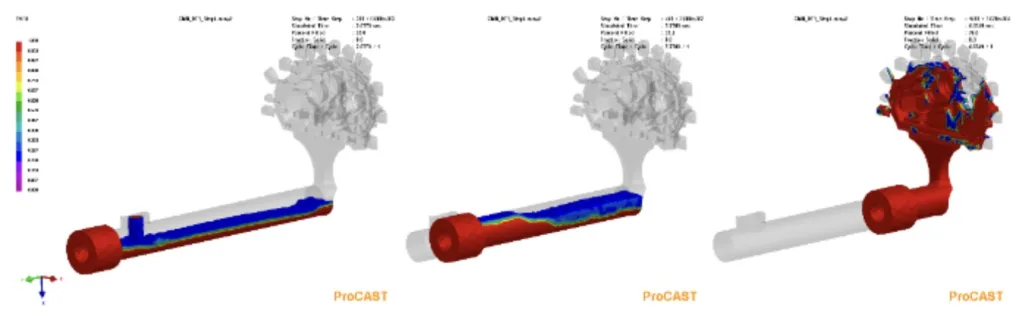
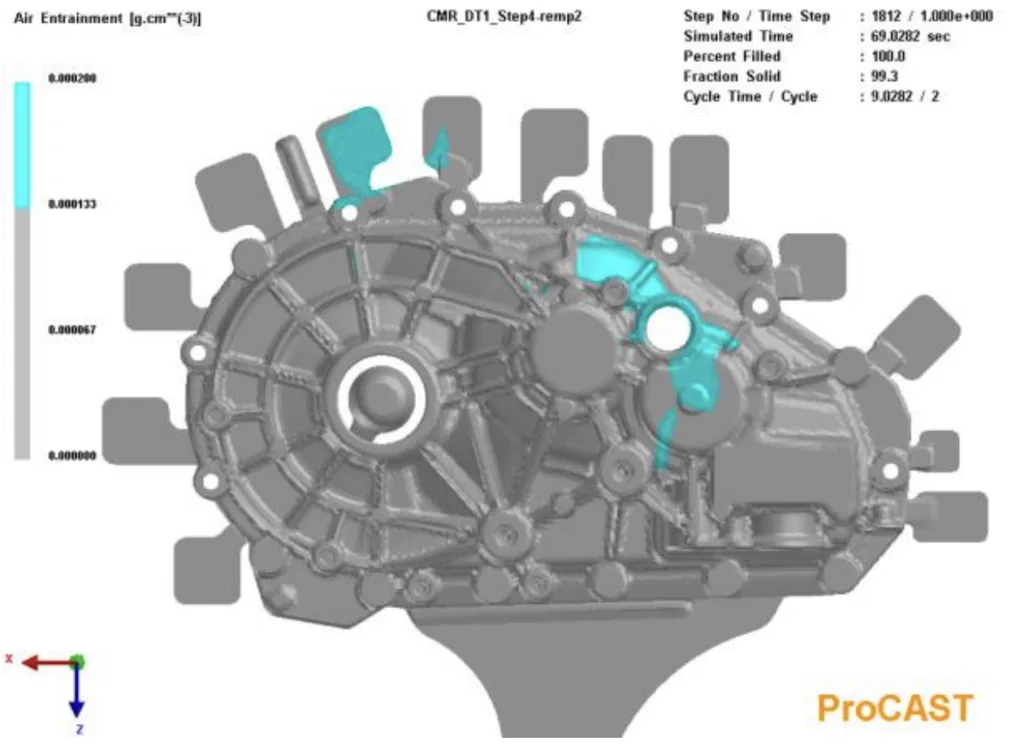
6. 결론 및 논의:
주요 결과 요약: 본 논문은 ESI ProCAST를 사용한 구조화된 4단계 시뮬레이션 방법론을 통해 자동차 HPDC 부품 개발에서 공정 모델링의 부가가치를 성공적으로 입증합니다. 제조 가능성 검토부터 전체 금형 설계 검증에 이르기까지 각 단계는 부품 및 금형 설계를 최적화하는 데 중요한 통찰력을 제공합니다. 시뮬레이션 결과는 실제 관찰과 양호한 상관관계를 보여주어 접근 방식의 정확성과 예측 능력을 강조합니다.
연구의 학문적 의의: 본 연구는 다이캐스팅 개발 초기 단계에 공정 시뮬레이션을 통합하는 것의 학문적 중요성을 강조합니다. 이는 물리적 시행착오에 대한 의존도를 줄이고 보다 효율적이고 강력한 설계 프로세스를 위한 길을 열어 디지털 튜닝 방법론의 효과를 입증합니다.
실용적 의미: 제시된 4단계 방법론은 자동차 산업의 다이캐스팅 엔지니어에게 실용적이고 가치 있는 프레임워크를 제공합니다. 이 접근 방식을 채택함으로써 제조업체는 다음을 수행할 수 있습니다.
- 부품 품질 향상: 기공 및 공기 혼입과 같은 잠재적인 결함을 사전에 식별하고 완화합니다.
- 개발 시간 단축: 물리적 반복 작업을 가상 시뮬레이션으로 대체하여 개발 주기를 단축합니다.
- 비용 최적화: 사전 시뮬레이션 기반 설계 최적화를 통해 비용이 많이 드는 금형 재작업 및 생산 지연을 최소화합니다.
초기 제조 가능성 검토(1단계)와 냉각 시스템의 전략적 설계(3단계 및 4단계)는 고품질 HPDC 부품을 달성하는 데 특히 중요한 것으로 강조됩니다.
연구의 한계: 본 연구는 단일 사례 연구(기어박스 하우징)를 기반으로 하므로 연구 결과의 일반화 가능성이 제한될 수 있습니다. 또한 방법론은 르노의 공정 및 ESI ProCAST 소프트웨어 사용에 특화되어 있습니다. 다양한 부품 형상과 다양한 시뮬레이션 도구를 사용한 추가 연구가 유익할 것입니다.
7. 향후 후속 연구:
본 논문은 향후 연구를 위한 여러 방향을 제시합니다.
- 공정 변동 관리: 합금 온도 변동과 같은 제조 공정 변동이 부품 품질에 미치는 영향을 조사하고 이러한 변동에 덜 민감한 강력한 설계를 개발합니다.
- 최적화 도구: ProCAST 내에 통합된 ESI PAM-OPT와 같은 최적화 도구를 활용하여 공정 제어 및 부품 품질 향상을 위한 제조 변수를 체계적으로 정의하고 최적화하는 방법을 모색합니다.
- 인더스트리 4.0 통합: 시뮬레이션 및 최적화 도구의 통합을 지속적으로 발전시켜 다이캐스팅 공정을 인더스트리 4.0 표준으로 전환하고 보다 자동화되고 데이터 기반 제조를 가능하게 합니다.
강력한 설계 방법론, 시뮬레이션과 최적화 알고리즘의 원활한 통합, 다이캐스팅 분야 내 인더스트리 4.0 원칙의 광범위한 구현에 대한 추가 연구가 필요합니다.
8. 참고 문헌:
[1] Ch. Pequet, M. Gremaud, and M. Rappaz, "Modelling of microporosity, macroporosity, and pipe-phrinkage formation during the solidification of alloys using a mushy-zone refinement method: applications to aluminium alloys", Met. Mater. Trans., 33A (2002) 2095.
[2] Imad Khan, M & Frayman, Yakov & Nahavandi, Saeid. (2012). Modelling of porosity defects in high pressure die casting with a neural network.
[3] G. Couturier, and M. Rappaz, "Effect of volatile elements on porosity formation in solidifying alloys", Mod. Sim. Mater. Sc. Engng., (2005)
[4] Wang, LH & Nguyen, T & Savage, G & Davidson, C. (2003). Thermal and flow modelling of ladling and injection in high pressure die casting process. International Journal of Cast Metals Research. 16. 409-417. 10.1179/136404603225007863.
[5] Karban, Robert. (2000). The effects of intensification pressure, gate velocity, and intermediate shot velocity on the internal quality of aluminum die castings. ETD Collection for Purdue University.
[6] G. Couturier, J.-L. Desbiolles, and M. Rappaz, "A Porosity Model for Multi-Gas Systems in Multi-Component Alloys", MCWASP, Edited by TMS Publ., Warrendale, USA, 2006)
[7] Tsoukalas, Vasilios. (2003). The Effect of Die Casting Machine Parameters on Porosity of Aluminum Die Castings. International Journal of Cast Metals Research. 15. 581-588. 10.1080/13640461.2003.11819544.
[8] S. Dargusch, Matthew & Dour, Gilles & Schauer, N & M. Dinnis, C & M. Savage, George. (2006). The influence of pressure during solidification of high pressure die cast aluminium telecommunications components. Journal of Materials Processing Technology. 180. 10.1016/j.jmatprotec.2006.05.001.
[9] N. Obiekea, Kenneth & Y. Aku, Shekarau & S. Yawas, Danjuma. (2014). Effects of Pressure on the Mechanical Properties and Microstructure of Die Cast Aluminum A380 Alloy. Journal of Minerals and Materials Characterization and Engineering. 02. 248-258. 10.4236/jmmce.2014.23029.
[10] G. Couturier and M. Rappaz, “Modelling of porosity formation in multicomponent alloys in the presence of several dissolved gases and volatile solute elements", Symposium on Simulation of Aluminum Shape Casting
[11] ESI ProCAST 2018.0 User Manual 2006
9. 저작권:
- This material is Andre Le-Nezet, Nicolas De Reviere, Loic Calba, Badarinath Kalkunte's paper: Based on Added Value of Process Modelling in Development of Automotive Die Casting Parts.
- Paper Source: Japan Die Casting Congresse paper]
- Copyright © 2025 CASTMAN. All rights reserved.
본 자료는 상기 논문을 기반으로 요약되었으며, 상업적 목적으로 무단 사용하는 것을 금지합니다.