1. 개요
- 제목: 고해상도 다상 시뮬레이션을 이용한 대면적 다이캐스트 부품의 복합 결함 예측 (Combined defect prediction for large-area die-cast components using high-resolution multi-phase simulation)
- 저자: J. Jakumeit, Η Behnken, R Laqua, J. Gänz, L. Becker, M. Fehlbier, O. Middelmann
- 발행년도: 2023년
- 발행 학술지/학회: IOP Conference Series: Materials Science and Engineering
- 키워드: 고압 다이캐스팅 공정 (HPDC), 다상 시뮬레이션, 주조 결함, 기공, 공기 연행, 응고, 검증
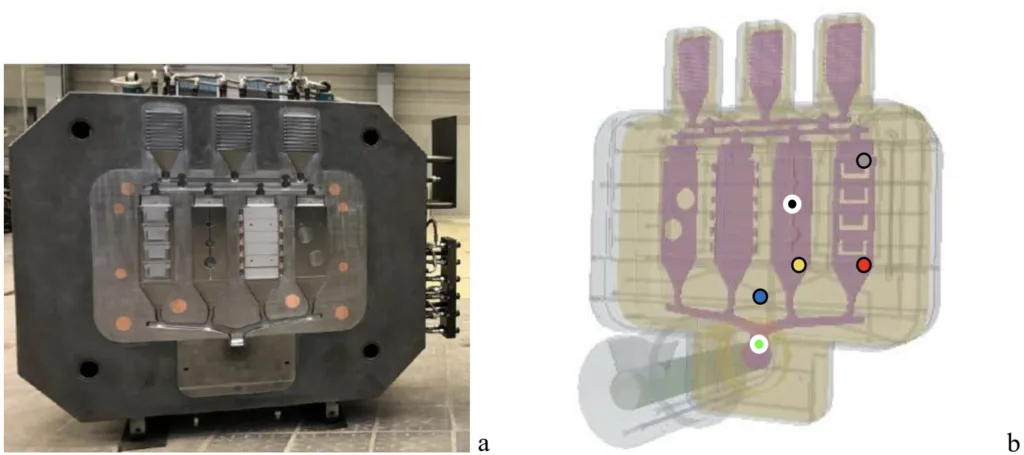
2. 연구 배경
- 연구 주제의 사회적/학문적 맥락:
- 자동차 산업에서는 비용 및 에너지 절감을 위해 기존의 용접 부품을 하나의 다이캐스트 부품으로 대체하는 대형 부품 생산 추세가 있습니다.
- 대형 HPDC 부품의 경우 금형 충전 중 초기 응고가 발생할 수 있다는 점이 중요한 문제입니다.
- 냉각 불량, 에어 포켓, 기공과 같은 주조 결함은 공간적, 시간적으로 분리될 수 없으며 서로 영향을 미칩니다.
- 기존 연구의 한계:
- 기존 다이캐스팅 시뮬레이션 모델은 계산 시간 단축을 위해 근사치를 사용하는 경우가 많습니다.
- 공기 영향 및 용융 응고 정지와 같은 현상이 모델에서 단순화되어 표현됩니다.
- 박막 영역은 메쉬 셀 수 제한으로 인해 정확하게 분석하기 어려울 수 있습니다.
- 기존 기공 모델인 Niyama 기준은 HPDC 응용 분야의 기공 예측에 적합하지 않은 것으로 밝혀졌습니다.
- 이전 모델들은 가스 및 수축 기공 사이의 상호 작용을 단순화하는 경향이 있었습니다.
- 연구의 필요성:
- 다양한 주조 결함 간의 상호 작용을 정확하게 묘사하려면 주조 공정을 보다 현실적으로 시뮬레이션해야 합니다.
- 공기를 압축성 가스로 처리하고, 응고로 인한 용융 흐름 감소를 고려하며, 체적 수축으로 인한 기공 형성을 결합적으로 처리할 수 있는 다상 접근 방식이 필요합니다.
- 이러한 다상 접근 방식을 실제 주조 실험 및 산업 응용 분야에 적용하여 검증하는 것이 실용적인 활용에 매우 중요합니다.
3. 연구 목적 및 연구 질문
- 연구 목적:
- 고해상도 다상 시뮬레이션을 사용하여 공기 연행 및 수축 기공 형성을 결합적으로 예측하는 고압 다이캐스팅 (HPDC) 응용 분야를 위한 결합 기공 모델을 개발하고 검증하는 것입니다.
- 주요 연구 질문:
- 공기를 압축성 가스로, 용융 응고를 다공성 매체 접근 방식으로 처리하는 다상 시뮬레이션 접근 방식이 대면적 다이캐스트 부품의 주조 결함을 정확하게 예측할 수 있을까요?
- HPDC 시뮬레이션 모델에서 공기 연행과 수축 기공 형성을 어떻게 결합하여 상호 작용을 고려할 수 있을까요?
- 용융 공급이 응고에 의해 제한되는 영역에서 압력 계산 및 용융 압축성을 기반으로 하는 결합 기공 모델이 기공 형성을 예측할 수 있을까요?
- 개발된 다상 접근 방식 및 결합 기공 모델은 실험적 주조 시험 및 산업 응용 분야와 얼마나 잘 일치할까요?
- 연구 가설:
- 압축성 공기, 응고 효과, 결합 기공 모델을 통합한 다상 시뮬레이션 접근 방식은 단순화된 모델에 비해 HPDC 주조 결함을 보다 현실적으로 예측할 수 있을 것입니다.
- 응고로 인한 압력 변화 및 가스 증발을 고려하는 결합 기공 모델은 용융 공급이 제한된 영역에서 수축 기공 형성을 정확하게 예측할 것입니다.
- 개발된 모델을 사용한 시뮬레이션 결과는 실험적 주조 시험 및 산업 사례 연구와 잘 부합하여 HPDC 응용 분야에 대한 모델의 타당성을 입증할 것입니다.
4. 연구 방법론
- 연구 설계:
- 유동 해석 소프트웨어 STAR-CCM+를 사용한 HPDC 공정의 다상 시뮬레이션 접근 방식 개발.
- 공기 연행 및 수축 기공을 고려하는 결합 기공 모델 구현.
- 특수 설계된 테스트 형상을 사용한 주조 실험을 통한 시뮬레이션 접근 방식 검증.
- 검증된 모델을 산업 주조 부품에 적용.
- 데이터 수집 방법:
- GTK 냉챔버 다이캐스팅 기계 (Bühler Carat 1400 t) 와 AlSi9Cu3 합금을 사용하여 실험적 주조 시험을 수행했습니다.
- 주조 사이클 동안 테스트 형상에 배치된 6개의 열전대를 사용하여 온도 측정을 수집했습니다.
- 산업 응용 분야 검증을 위해 주조품의 기공률을 CT 스캔을 사용하여 분석했습니다.
- 분석 방법:
- 시뮬레이션에서 계산된 온도 곡선과 측정된 온도 데이터를 비교하여 열 설정의 유효성을 검증했습니다.
- 예측된 기공 위치와 실험 주조 및 산업 부품에서 관찰된 기공 위치를 질적으로 비교했습니다.
- 결함 형성 메커니즘을 이해하기 위해 시뮬레이션 결과에서 속도, 공기 분포, 압력, 고상 분율 및 기공 가스 분포를 분석했습니다.
- 연구 대상 및 범위:
- 미충진, 냉각 불량, 공기 연행 및 기공을 조사하기 위한 4가지 테스트 케이스 (2홀, 계단, 3캠, U자형 프로파일) 를 갖는 특수 설계된 HPDC 테스트 형상.
- 상세한 기공 시뮬레이션을 위해 테스트 형상에서 추출한 단순화된 3캠 형상.
- 산업 응용 분야 검증을 위한 KSM Castings Group GmbH의 산업 구조 부품.
- 알루미늄 HPDC 응용 분야에 초점을 맞추고 AlSi9Cu3 합금을 사용하여 검증.
5. 주요 연구 결과
- 주요 연구 결과:
- HPDC 용 다상 시뮬레이션 접근 방식을 개발했습니다. 이 접근 방식은 공기와 용융 금속을 압축성 유체로 처리하고, VoF (Volume of Fluid) 방법과 HRIC (High-Resolution-Interface-Capturing) 기법을 사용하여 STAR-CCM+에서 날카로운 계면을 포착합니다.
- 공기 연행과 수축 기공을 모두 예측하기 위해 압력 축적, 응고 및 가스 증발을 고려하는 결합 기공 모델을 구현했습니다.
- 시뮬레이션 접근 방식은 계산된 온도 곡선과 주조 시험에서 얻은 측정 데이터를 비교하여 검증했으며, 좋은 일치를 보였습니다. "그림 2a는 열전대 위치에서 계산된 온도 곡선과 측정 결과를 비교합니다."
- 결합 기공 모델을 사용한 3캠 형상의 고해상도 시뮬레이션은 실험 결과와 일치하게 캠 중앙에서 기공 형성을 예측했습니다. "그림 7은 4단계 후 최종 기공 분포를 보여줍니다. 순수 열 기공 모델은 캠 중앙 근처에서 기공을 제공합니다…" 및 "기공 가스 분포와 함께 그림 7은 실제 주조에서 발견된 기공을 보여줍니다. 결합 기공 모델에 의한 기공 예측은 실험 결과와 잘 일치합니다…"
- 산업 주조 부품에 적용한 결과, 시뮬레이션은 CT 스캔으로 확인된 위치에서 수축 기공을 예측할 수 있었지만, 일부 불일치가 관찰되었습니다. "수축 기공은 CT 스캔 (그림 9c 및 9d) 에 의해 밝혀진 주조의 두 위치 (C5, B2, 그림 9a 및 9b 참조) 에서 확인되었습니다. 시뮬레이션은 지금까지 이러한 기공 위치를 예측할 수 없었습니다." 그리고 나중에 "수축 기공은 실제로 4단계 말에 순수 열 기공 모델에 의해 두 위치 C5 및 B2 (그림 9e 및 9f) 에서 표시되었습니다."
- 시뮬레이션 결과는 잘 설계된 게이팅 시스템에서 수축 기공이 공기 연행으로 인한 기공보다 우세하다는 것을 나타냅니다. "테스트 케이스 및 산업 응용 분야에 대한 기공 예측을 살펴보면 수축 기공이 공기 연행으로 인한 기공보다 우세합니다."
- 통계적/질적 분석 결과:
- 시뮬레이션 및 측정된 온도 곡선 간의 질적 일치가 관찰되었습니다 (그림 2a).
- 3캠 형상에서 예측된 기공 위치와 실험적으로 관찰된 기공 간의 질적 일치 (그림 7 및 그림 9).
- 산업 주조에서 CT 스캔과 시뮬레이션 결과 간의 기공 위치에 대한 질적 비교 (그림 9).
- 데이터 해석:
- 검증된 다상 시뮬레이션 접근 방식 및 결합 기공 모델은 HPDC 공정에서 온도 분포 및 기공 형성을 효과적으로 예측할 수 있습니다.
- 결합 기공 모델은 공기 연행과 수축 기공 사이의 복잡한 상호 작용을 포착하여 기존 모델에 비해 결함 예측 능력을 향상시킵니다.
- 고해상도 다상 시뮬레이션 방법론은 특히 크고 복잡한 부품의 HPDC 공정을 이해하고 최적화하는 데 유용한 도구를 제공합니다.
- 모델이 실험과 잘 일치하지만, 산업 응용 분야에서 기공 예측의 정확성을 개선하기 위해 추가적인 개선이 필요할 수 있으며, 특히 모델의 과민성 및 현재 기공 모델에서 다루지 않는 요인과 관련하여 개선이 필요합니다.
- 그림 목록:
- 그림 1: 이동 금형의 내부 (a) 와 2홀, 계단, 3캠 및 U자형 프로파일 (b) 의 4가지 테스트 케이스를 갖는 형상 및 a) 에 표시된 것
- 그림 2: 6개 측정 지점 (a) (그림 1b 참조) 에서 측정 및 계산된 온도 곡선 비교 및 보정된 온도 의존 HTC (b)
- 그림 3: 간단한 입구 및 출구 (a) 와 2.4 Mio 셀, 부품 영역에 1.8 Mio 셀을 갖는 고해상도 메쉬를 갖는 3캠 테스트 형상. 용융물/금형 계면에서 높은 속도 및 온도 구배 해상도를 위해 3개의 프리즘 레이어가 사용되었습니다.
- 그림 4: 충전 단계가 끝날 때 0.055초 후 속도 (a) 및 연행 공기 (b) 분포.
- 그림 5: 증압 단계가 끝날 때 0.1초 후 속도 (a) 및 연행 공기 (b) 분포.
- 그림 6: 결합 흐름 및 응고 단계가 끝날 때 1.1초 후 고상 분율 (a), 속도 (b), 압력 (c) 및 기공률 (d) 분포.
- 그림 7: 결합 기공 모델과 실험 결과에 의한 기공 예측 비교.
- 그림 8: 형상 a), 다면체 메쉬 b), 0.75초 후 충전 중 온도 및 용융물 분포 c) 및 완전 충전 및 증압 후 공기 연행 d).
- 그림 9: CT 분석 (c) 및 (d) 에 의해 밝혀진 주조의 두 위치 C5 (a) 및 B2 (b) 에서 기공률을 보여주는 산업 HPDC 응용 분야 및 위치 C5 (e) 및 B2 (f) 에 대한 결합 시뮬레이션 모델에 의한 기공 예측.
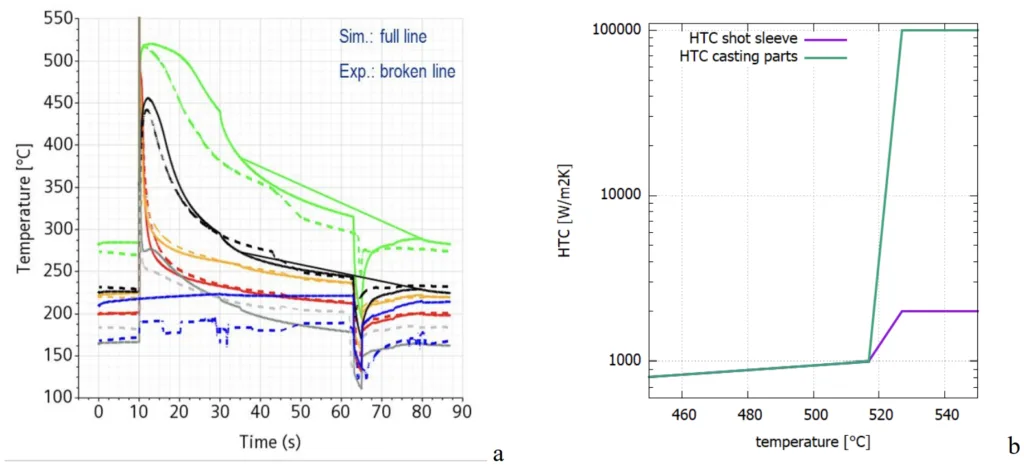
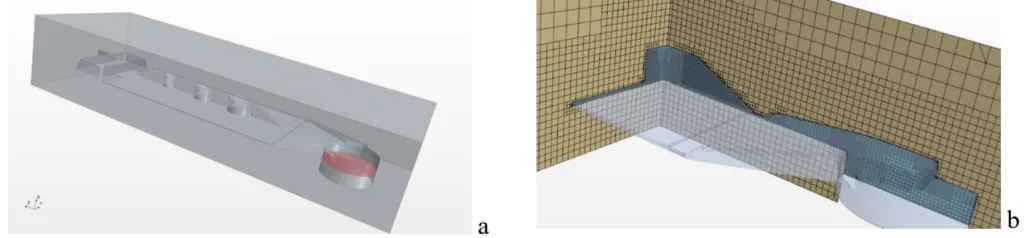
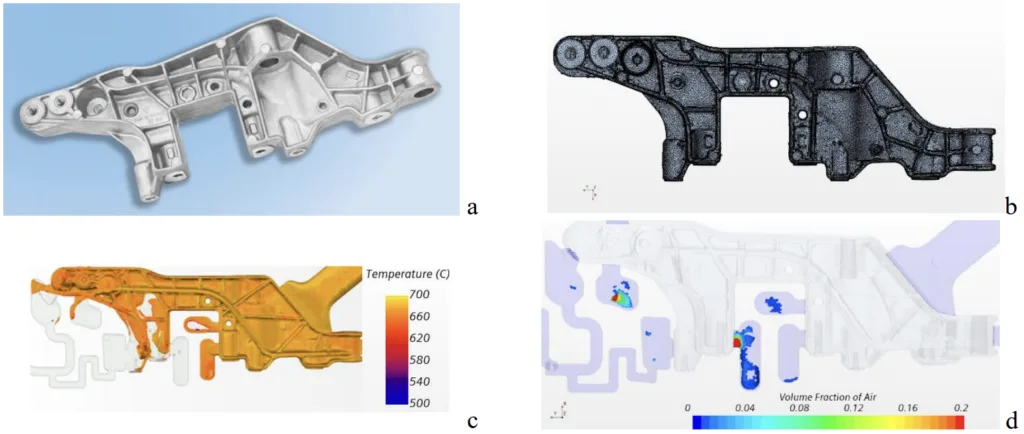
6. 결론 및 논의
- 주요 결과 요약:
- 본 연구에서는 공기 연행 및 수축 기공 예측을 위한 결합 기공 모델을 통합하여 HPDC 용 다상 유동 및 응고 시뮬레이션 접근 방식을 성공적으로 개발하고 검증했습니다.
- 이 모델은 액체 용융물과 가스를 압축성 유체로 처리하고, 온도 의존성 점도 및 다공성 매체 접근 방식을 사용하여 용융 흐름에 대한 응고 효과를 고려하며, 압력 변화 및 가스 증발을 기반으로 기공 형성을 시뮬레이션합니다.
- 실험적 주조 시험 및 산업 응용 분야에 대한 검증은 HPDC 부품에서 온도 분포 및 기공 형성을 예측하는 모델의 능력을 입증했습니다.
- 연구의 학문적 의의:
- 본 연구는 주조 결함을 보다 현실적이고 포괄적으로 예측하는 접근 방식을 제공함으로써 다이캐스팅 시뮬레이션 기술 발전에 기여합니다.
- 결합 기공 모델은 공기 연행과 수축 기공 사이의 복잡한 상호 작용을 다루어 기존 모델에 비해 결함 예측 정확도를 향상시킵니다.
- 고해상도 다상 시뮬레이션 방법론은 특히 크고 복잡한 부품의 HPDC 공정을 이해하고 최적화하는 데 유용한 도구를 제공합니다.
- 연구의 실제적 의미:
- 검증된 시뮬레이션 접근 방식은 다이캐스팅 엔지니어가 공정 매개변수, 금형 설계 및 게이팅 시스템을 최적화하여 주조 결함을 최소화하고 부품 품질을 향상시키는 데 사용할 수 있습니다.
- 기공 및 기타 결함을 정확하게 예측함으로써 모델은 스크랩률을 줄이고, 공정 개발 시간을 단축하며, HPDC 제조의 전반적인 효율성을 향상시키는 데 도움이 될 수 있습니다.
- 산업 응용 분야는 실제 주조 문제를 해결하고 고품질 다이캐스트 부품 생산을 개선하는 모델의 잠재력을 입증합니다.
- 연구의 한계:
- 모델이 실험 데이터와 잘 일치하지만, 산업 응용 분야에서 기공 예측에 여전히 불일치가 있어 추가 개선의 여지가 있음을 시사합니다.
- 모델이 특정 매개변수에 과민하여 일부 경우에서 기공을 과도하게 예측할 수 있습니다.
- Beckermann [13] 이 언급한 바와 같이 현재 기공 모델에서 명시적으로 다루지 않은 요인들이 시뮬레이션 예측과 실제 주조 결과 간의 차이에 기여할 수 있습니다.
7. 향후 후속 연구
- 후속 연구 방향:
- 산업 응용 분야에 대한 정확성과 견고성을 개선하기 위해 결합 기공 모델을 추가로 개선합니다.
- 모델의 과민성 및 잠재적인 보정 또는 모델 매개변수 조정을 조사합니다.
- Beckermann [13] 등이 확인한 HPDC 기공 형성에 영향을 미치는 추가 요인을 모델에 통합합니다.
- 더 넓은 범위의 주조 형상, 합금 및 공정 조건으로 모델을 추가로 검증합니다.
- 고해상도 다상 시뮬레이션의 산업 현장에서 더 넓은 채택을 가능하게 하기 위해 시뮬레이션 시간을 단축하는 보다 효율적인 계산 방법을 개발합니다.
- 추가 탐구가 필요한 영역:
- 가스 증발에 대한 임계 압력 수준과 재료 특성 및 공정 조건에 대한 의존성에 대한 상세한 조사.
- 용융물에 용해된 수소 또는 공기가 기공 형성 및 가스 증발에 미치는 영향 연구.
- HPDC 에서 다상 유동 시뮬레이션의 정확도를 더욱 향상시키기 위한 고급 난류 모델 및 계면 포착 기술 탐색.
- 다이캐스팅 엔지니어가 결합 기공 모델을 쉽게 적용할 수 있도록 사용자 친화적인 시뮬레이션 도구 및 지침 개발.
8. 참고 문헌
- [1] Duan H Z, Shen J N, & Li Y P (2012). Comparative analysis of HPDC process of an auto part with ProCAST and FLOW-3D. In Applied Mechanics and Materials (Vol. 184, pp. 90-94). Trans Tech Publications Ltd.
- [2] Bodhayana M R and Ramesha N 2014 Int. J. Research in Engineering and Technology 03 (11) 1163
- [3] Aghion E, Moscovitch N and Arnon A (2007). The correlation between wall thickness and properties of HPDC Magnesium alloys. Materials Science and Engineering: A, 447(1-2), 341-346.
- [4] Wang T, Huang J, Fu H, Yu K and Yao S (2022). Influence of Process Parameters on Filling and Feeding Capacity during High-Pressure Die-Casting Process. Applied Sciences, 12(9), 4757.
- [5] Simcenter STAR-CCM+: https://www.plm.automation.siemens.com/global/de/products/simcenter/STAR-CCM.html
- [6] Jana S, Kättlitz O, Hediger F, Jakumeit J and Aguilar J (2012). MCWASP XIII, IOP Publishing, IOP Conf. Series: Materials Science and Engineering.
- [7] Stefanescu, D. M. (2005). Computer simulation of shrinkage related defects in metal castings-a review. International Journal of Cast Metals Research, 18(3), 129-143.
- [8] Beech J, Barkhudarov M, Changands K, Chin B (1998) in ‘Modelling of casting, welding and advanced solidificationprocesses VIII', (ed. B. G. Thomas and C. Beckerman), 1071; Warrendale, PA, TMS.
- [9] Jakumeit J, Behnken H, Laqua R, Mbewou S, Fehlbier M, Gänz J, & Becker, L. (2021). Coupled Modeling of Misrun, Cold Shut, Air Entrainment, and Porosity for High-Pressure Die Casting Applications. In Light Metals 2021 (pp. 865-870). Springer, Cham.
- [10] Niyama T, Uchida M, Morika W A, Saito S (1982) Int. cast metals journal 7:52-63
- [11] Carlson K D and Beckermann C (2009). Metallurgical and Materials Transactions A, 40(1), 163-175.
- [12] Jakumeit, J., Jana, S., Böttger, B., Laqua, R., Jouani, M. Y., & Bührig-Polaczek, A. (2012, January). In IOP Conference Series: Materials Science and Engineering (27, No. 1, p. 012066). IOP Publishing.
- [13] Beckermann C and Monroe A 2009 Porosity simulation for high pressure die castings Die Casting Engineer (The North American Die Casting Association) ISSN 0012-25JX
- [14] Carlson K D, Lin Z and Beckermann C (2007). Modeling the effect of finite-rate hydrogen diffusion on porosity formation in aluminum alloys. Metallurgical and Materials Transactions B, 38(4), 541-555.
- [15] Khalajzadeh V, Goettsch, D D and Beckermann C (2016). In Shape Casting: 6th International Symposium (pp. 35-42). Springer, Cham
- [16] Khalajzadeh V and Beckermann C (2020). Simulation of shrinkage porosity formation during alloy solidification. Metallurgical and Materials Transactions A, 51(5), 2239-2254.
- [17] Ferziger J H and Peric M (ed) 2002 Computational Methods for Fluid Dynamics (McGraw-Hill) ISBN 2-540-42074-6
- [18] Teskeredzic A, Demirdzic I and Muzaferija S 2002 Num. Heat Trans. B 42 43
- [19] Demirdzic I and Muzaferija S 1995 Computer Methods in Appl. Mech. and Eng. 125 235-255.
- [20] Muzaferija S and Peric M 1999 Computation of free surface flows using interface-tracking and interface-capturing methods. Nonlinear Water Wave Interaction, ed O Mahrenholtz and M. Markiewicz, (Southampton: WIP Press) 59-100
- [21] Sabau S and Viswanath S 2002 Met. Mat. Trans. B 33B 131
- [22] Poirier D R (1987). Permeability for flow of interdendritic liquid in columnar-dendritic alloys. Metallurgical Transactions B, 18(1), 245-255.Poirier D R, Yeum K and Mapples A L 1987 Metall. Mater. Trans. A 18 1979
- [23] Jakumeit, J., Subasic, E., & Bünck, M. (2016). Prediction of misruns in thin wall castings using computational simulation. In Shape Casting: 5th International Symposium 2014 (pp. 253-260). Springer International Publishing.
9. 저작권
- 본 자료는 J. Jakumeit, Η Behnken, R Laqua, J. Gänz, L. Becker, M. Fehlbier, O. Middelmann의 논문: 고해상도 다상 시뮬레이션을 이용한 대면적 다이캐스트 부품의 복합 결함 예측 (Combined defect prediction for large-area die-cast components using high-resolution multi-phase simulation) 을 기반으로 작성되었습니다.
- 논문 출처: http://dx.doi.org/10.1088/1757-899X/1281/1/012027
본 자료는 위 논문을 기반으로 요약되었으며, 상업적 목적의 무단 사용을 금지합니다.
Copyright © 2025 CASTMAN. All rights reserved.