본 논문 요약은 ['고압 다이캐스팅 AlSi9Cu3(Fe) 합금의 피로 거동에 미치는 미세구조 및 주조 결함의 영향'] 논문을 ['Procedia Structural Integrity']에 발표된 내용을 기반으로 작성되었습니다.
1. 개요:
- 제목: 고압 다이캐스팅 AlSi9Cu3(Fe) 합금의 피로 거동에 미치는 미세구조 및 주조 결함의 영향 (Effects of microstructure and casting defects on the fatigue behavior of the high-pressure die-cast AlSi9Cu3(Fe) alloy)
- 저자: L. Lattanzi, A. Fabrizi, A. Fortini, M. Merlin, G. Timelli
- 발행 연도: 2017년
- 발행 학술지/학회: Procedia Structural Integrity
- 키워드: 다이캐스트 알루미늄 합금; 주조 결함; 미세구조 (die cast aluminum alloy; casting defects; microstructure)
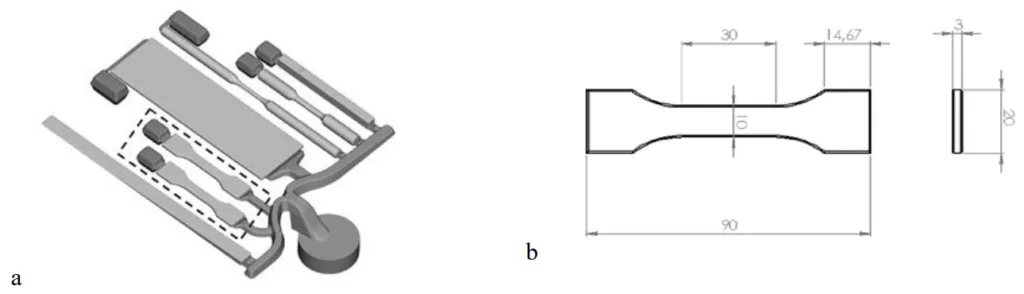
2. 연구 배경:
연구 주제 배경:
고압 다이캐스팅(HPDC) 부품은 "우수한 유연성과 높은 생산성"으로 인해 자동차 산업을 중심으로 사용이 증가하고 있습니다. 이러한 특성으로 인해 HPDC는 특히 자동차 분야에서 복잡한 형상과 우수한 표면 품질을 요구하는 대량 생산 부품 제조에 적합합니다. 그러나 HPDC 공정은 "다이의 급속 충진 및 높은 냉각 속도"로 인해 본질적으로 "기공 및 산화 피막"과 "냉간 접합"과 같은 다양한 결함 형성을 야기합니다. 이러한 결함은 "PD CEN/TR 16749:2014 표준 및 Fiorese et al. 2015에 의해 정의된 바와 같이" 주조품의 기계적 성질에 부정적인 영향을 미치며, "피로 균열의 시작점 역할을 하여 주조품의 피로 거동을 저하시킬 수 있습니다". 따라서 다이캐스트 알루미늄 합금의 피로 거동을 이해하는 것은 자동차 응용 분야의 복잡한 주조품의 성능을 평가하는 데 매우 중요합니다.
기존 연구 현황:
다이캐스트 알루미늄 합금 부품의 정적 기계적 성질에 대한 연구는 광범위하게 진행되었지만, "고압 다이캐스팅 결함이 피로 특성에 미치는 역할에 대한 연구는 매우 부족합니다". 기존 연구에 따르면 주조 결함은 정적 강도에 각기 다른 영향을 미치며, 파단 시 연신율에서 상당한 차이가 관찰됩니다. Avalle et al. 2002는 HPDC AlSi9Cu3(Fe) 시편의 정적 특성이 기공률 증가에 따라 감소한다고 보고했습니다. Avalle et al. 2002와 Mayer et al. 2003의 피로 연구에서는 HPDC AlSi9Cu3(Fe) 및 Mg 합금에서 기공과 냉간 접합이 피로 강도 감소에 미치는 역할과 기공에서의 균열 시작을 강조했습니다. Hu et al. 2014의 AlMg5Si2Mn 합금 연구에서는 영구 금형 시편이 HPDC 시편보다 짧은 피로 한계를 갖는 것으로 나타났습니다. 사형 주조, 영구 금형 주조 및 저압 다이캐스팅에 대한 연구에서도 결함이 피로 강도를 감소시키며, 결함 크기와 위치가 피로 수명에 영향을 미친다는 것을 확인했습니다. 이러한 연구들은 주로 파단면 분석과 금속 조직학적 특성 분석을 활용하여 결함이 피로 거동에 미치는 영향을 연구했습니다.
연구의 필요성:
주조 결함과 피로에 대한 기존 연구에도 불구하고, HPDC AlSi9Cu3(Fe) 합금에서 미세구조가 피로 균열 시작 및 전파에 미치는 영향에 대한 더 자세한 이해가 필요합니다. 본 연구는 미세구조 특성 분석 및 피로 시험을 통해 균열 시작 위치와 피로 파괴에 미치는 결함의 역할을 규명하여 HPDC로 제조된 특정 합금에서 미세구조가 피로 거동에 미치는 영향을 설명하는 것을 목표로 합니다.
3. 연구 목적 및 연구 질문:
연구 목적:
본 연구의 주요 목적은 고압 다이캐스팅 AlSi9Cu3(Fe) 알루미늄 합금에서 "미세구조가 피로 균열 시작 및 전파에 미치는 영향을 설명하는 것"입니다. 이는 예비 미세구조 특성 분석 및 피로 시험, 그리고 상세한 파단면 분석을 통해 달성됩니다.
핵심 연구 질문:
핵심 연구 질문은 다음과 같습니다:
- HPDC AlSi9Cu3(Fe) 합금 시편의 미세구조는 어떻게 특징지어지는가?
- 하중 제어 조건 하에서 단축 피로 시험을 통해 피로 거동은 어떻게 평가되는가?
- 파단면 및 단면 분석을 통해 균열 시작 위치는 어떻게 식별되는가?
- 주조 결함, 특히 미세구조는 피로 균열 시작 및 전파, 그리고 전체적인 피로 파괴에 어떤 영향을 미치는가?
연구 가설:
명시적으로 가설로 제시되지는 않았지만, 연구는 다음과 같은 내용을 암묵적으로 조사합니다:
- HPDC 공정에서 발생하는 주조 결함은 AlSi9Cu3(Fe) 합금에서 피로 균열의 주요 시작점 역할을 할 것이다.
- HPDC 공정 변수에 의해 영향을 받는 미세구조적 특징은 합금의 피로 거동에 상당한 영향을 미칠 것이다.
- 주조 결함의 위치 및 유형 (예: 기공, 산화 피막, 냉간 접합, 금속간 화합물, 편석 밴드)은 피로 균열 시작 및 전파 메커니즘과 직접적인 상관 관계가 있을 것이다.
4. 연구 방법
연구 설계:
본 연구는 재료 제조, 미세구조 특성 분석, 기계적 시험 및 파면 분석을 포함하는 실험적 설계를 채택했습니다. 특정 다이를 사용하여 다이캐스트 AlSi9Cu3(Fe) 시편을 제작하고 미세구조를 분석했습니다. 단축 피로 시험을 수행한 후, 파단면을 분석하여 미세구조 및 결함과 피로 거동 간의 상관 관계를 조사했습니다.
자료 수집 방법:
- 재료 제작: 다이캐스트 AlSi9Cu3(Fe) 시편은 특정 매개변수(체결력 2.9 MN, 다이 온도 ~230 °C, 충진율 0.28, 플런저 속도 0.2 m·s⁻¹ 및 2.7 m·s⁻¹, 증압 40 MPa)를 사용하여 냉챔버 다이캐스팅 기계로 제작되었습니다. 합금의 화학 조성은 "표 1"에 제시되어 있습니다.
- 미세구조 특성 분석: 예비 미세구조 조사는 "광학 현미경(OM) 및 주사 전자 현미경(SEM)"을 사용하여 수행되었습니다. 상 식별은 "X선 회절(XRD) 기법"을 사용하여 수행되었습니다. 결정립 크기 및 집합 조직 평가는 "전자 후방 산란 회절(EBSD) 조사"를 사용하여 수행되었습니다.
- 피로 시험: 단축 피로 시험은 "50 s⁻¹"의 주파수와 "80 MPa"의 응력 진폭으로 하중 제어 조건에서 "LM10 Italsigma 시험기"에서 수행되었습니다. "R = 0.1"의 응력비가 사용되었습니다. 3개의 시편에 대한 피로 수명(파괴까지의 사이클 수)을 기록했습니다.
- 파면 분석: 피로 시험 후, 파단면 및 단면을 "광학 및 주사 전자 현미경"을 사용하여 검사하여 균열 시작 위치, 전파 영역 및 피로 파괴에 미치는 결함의 역할을 식별했습니다.
자료 분석 방법:
- 미세구조 분석: OM, SEM, XRD 및 EBSD를 사용하여 결정립 크기, 형태, 상 분포, 금속간 화합물 및 주조 결함(기공, 산화 피막, 냉간 접합, 편석 밴드)을 분석했습니다. "EDS 스펙트럼 및 원소 맵"을 사용하여 금속간 화합물을 식별했습니다.
- 피로 데이터 분석: 피로 수명 데이터(파괴까지의 사이클 수)를 기록하고 분석하여 피로 성능의 분산 정도를 평가했습니다.
- 파면 분석: SEM 파단면 사진을 분석하여 균열 시작 위치, 전파 영역(안정 및 정적 파괴) 및 관련 결함을 식별했습니다. 광학 현미경을 사용하여 파단면 단면을 검사하여 균열 경로 및 전이 영역을 특성화했습니다.
연구 대상 및 범위:
연구 대상은 "다이캐스트 AlSi9Cu3(Fe) (EN AC-46000) 합금"으로 제작된 시편입니다. 연구 범위는 다음으로 제한됩니다:
- 응력비 R=0.1 및 단일 응력 진폭 수준 80 MPa의 단축 하중 조건에서의 피로 거동.
- 피로 시험된 시편의 미세구조 및 파면 분석.
- 특정 HPDC 알루미늄 합금에서 미세구조 및 주조 결함이 피로 균열 시작 및 전파에 미치는 영향 조사.
5. 주요 연구 결과:
핵심 연구 결과:
- 미세구조: 합금의 미세구조는 구상 결정립 구조의 전형적인 "장미꽃 모양의 α-Al 덴드라이트"를 나타냈습니다. 결정립 크기 및 2차 덴드라이트 암 간격(SDAS)은 코어 영역에서 유사했습니다. "표 2"는 평균 결정립 크기("17 ± 8 µm") 및 SDAS("12 ± 2 µm") 값을 보여줍니다. d/SDAS 비는 1.6 미만으로 구형 또는 구상 결정립 형태를 나타냅니다. "그림 3b"는 우선 결정립 방향이 없음을 보여줍니다. 식별된 금속간 화합물은 "β-Al5FeSi", "θ-Al2Cu" 및 블록형 "α-Al(Fe,Mn, Cr)Si (슬러지)" 상을 포함합니다. "그림 4b"는 슬러지 상을 보여줍니다. "공정 편석 밴드"가 관찰되었으며, 이는 "양의 거시적 편석" 및 국부적인 Al-Si 공정 과농축을 나타냅니다. "그림 6a"는 공정 편석 영역을 보여줍니다. "그림 6b"는 편석 밴드 영역의 기공 집중을 보여줍니다.
- 피로 수명: 다이캐스트 시편의 피로 수명은 80 MPa 응력 수준에서 "4×10⁴ 사이클"을 초과했으며, "8.7×10⁴ 사이클, 4.4×10⁴ 사이클 및 10×10⁴ 사이클"에서 파괴되었습니다. 데이터 분산은 피로 수명이 다이캐스트 결함에 의존함을 시사합니다.
- 파면 분석: 피로 균열은 단면의 날카로운 모서리에서 시작되었으며, 종종 단일 위치에서 시작되었습니다. "그림 7a"는 균열 시작 영역을 보여줍니다. 파단면은 "제한된 밝은 영역"(안정적인 균열 전파)과 "불규칙한 표면 영역"(정적 파괴)을 보여주었습니다. 시작 위치는 "그림 7b"에서 볼 수 있듯이 단면 모서리의 "산화 피막 및 냉간 접합"과 관련이 있었습니다. "슬러지 입자 및 기공"은 불규칙한 영역에서 관찰되었습니다("그림 8a 및 그림 8b"). 파단면 단면은 안정적인 전파에 해당하는 매끄러운 영역과 정적 파괴에 해당하는 거친 영역을 보여주었습니다("그림 9").
데이터 해석:
- 구상 결정립 구조와 우선 집합 조직의 부재는 균일한 응고를 시사하지만, HPDC 공정으로 인해 유도된 편석 밴드 및 기공의 존재는 동적 기계적 성질에 상당한 영향을 미칩니다.
- 피로 수명의 분산은 주조 결함이 균열 전파를 제어하고 따라서 피로 거동을 제어하는 데 지배적인 역할을 한다는 것을 나타냅니다. 그러나 균열 시작은 기하학적 특성(날카로운 모서리)에 의해 영향을 받는 것으로 보입니다.
- 날카로운 모서리의 산화 피막 및 냉간 접합은 주요 균열 시작점 역할을 합니다. 이러한 결함은 재료 불연속성을 생성하여 피로 균열 시작을 용이하게 합니다.
- 슬러지 입자 및 기공은 불규칙한 정적 파괴 영역에 기여하며, 이는 균열 전파 후 최종 파괴 과정에서의 역할을 나타냅니다.
- 균열 경로는 전파 중 덴드라이트 간 공정 영역과 덴드라이트를 모두 가로지르는 반면, 정적 파괴는 덴드라이트 구조 프로파일을 따르며, 이는 덴드라이트 간 구성 요소의 파괴가 균열 전파를 촉진함을 시사합니다.
그림 목록:
- 그림 1. (a) 다이캐스팅 형상, 조사된 시편은 점선 사각형으로 표시됨; (b) 인장 시편의 기술 도면.
- 그림 2. 시편의 일반적인 OM 현미경 사진: (a) 표면 근처; (b) 중심부.
- 그림 3. (a) α-Al 결정립 크기 분포; (b) 시편 중앙 단면에서 얻은 EBSD 집합 조직 맵.
- 그림 4. 2차상 분석: (a) XRD 스펙트럼; (b) 블록형 슬러지 상의 SEM 현미경 사진.
- 그림 5. 시편 단면의 SEM 이미지.
- 그림 6. (a) 시편 단면의 공정 편석 영역; (b) 인장 시편 단면의 기공.
- 그림 7. 8.7×10⁴ 사이클에서 파괴된 시편의 SEM 이미지: (a) 균열 시작 영역. 빨간색 화살표는 균열 시작 위치를 나타내고 점선은 전이 영역을 강조 표시함; (b) 균열 시작점의 상세.
- 그림 8. 표면 특징의 SEM 이미지: (a) 기공; (b) 파괴된 슬러지 입자.
- 그림 9. 8.7×10⁴ 사이클에서 파괴된 시편의 파단면 단면. (a) 빨간색 화살표는 균열 시작점을 나타내고 점선은 전이 영역을 나타냄; (b) 고배율의 균열 전파 영역; (c) 고배율의 정적 파괴 영역.
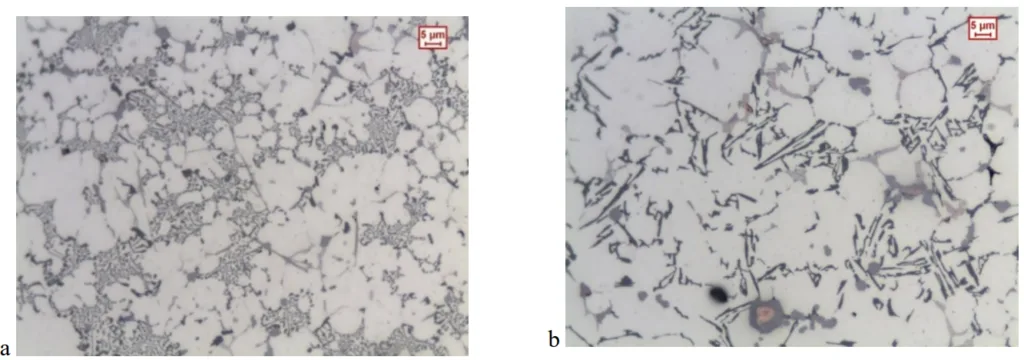
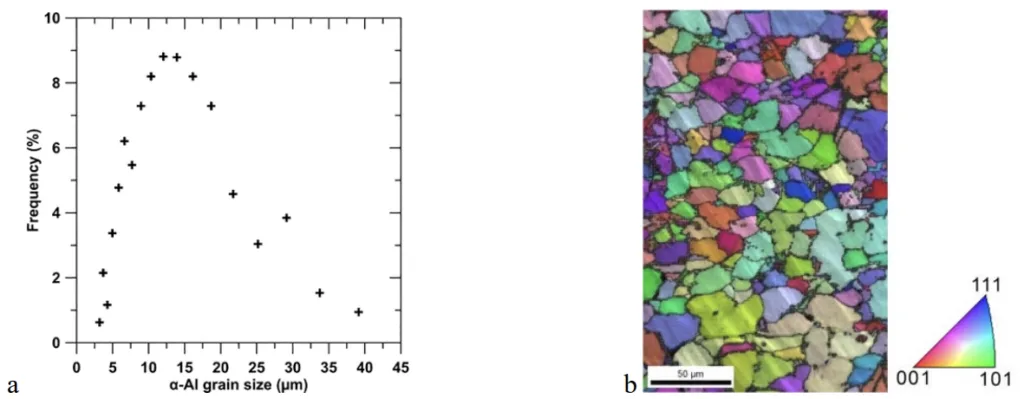
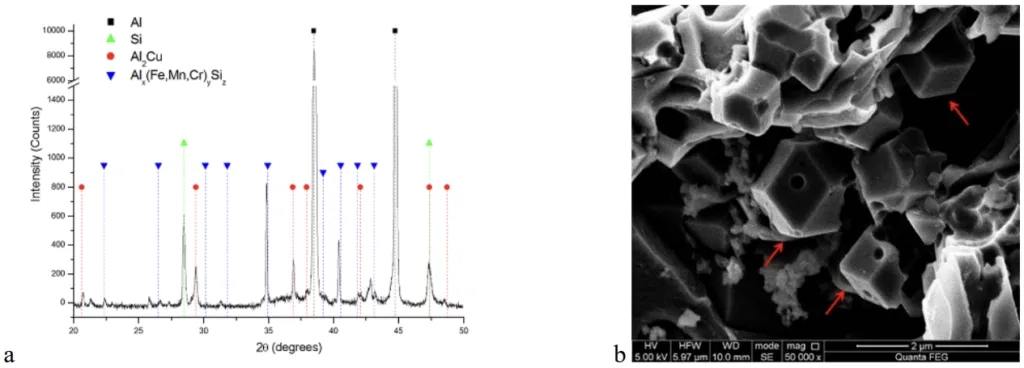

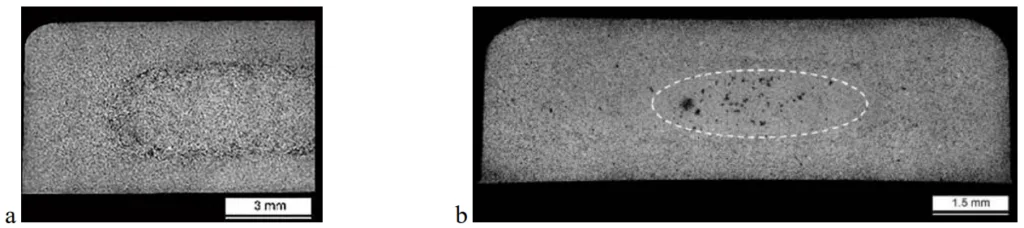
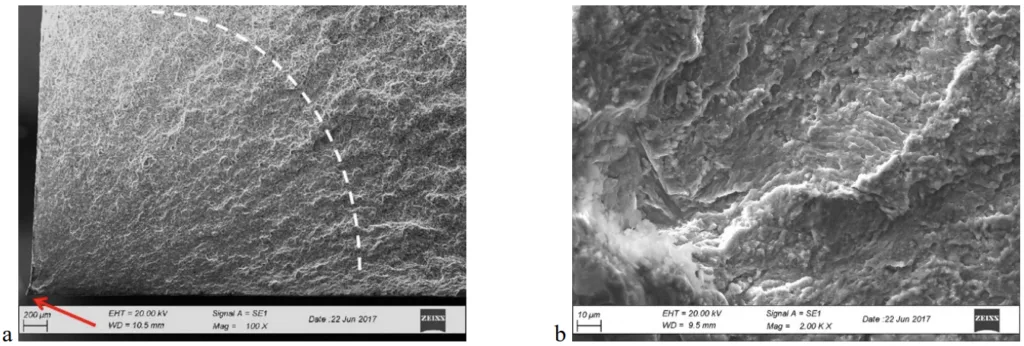
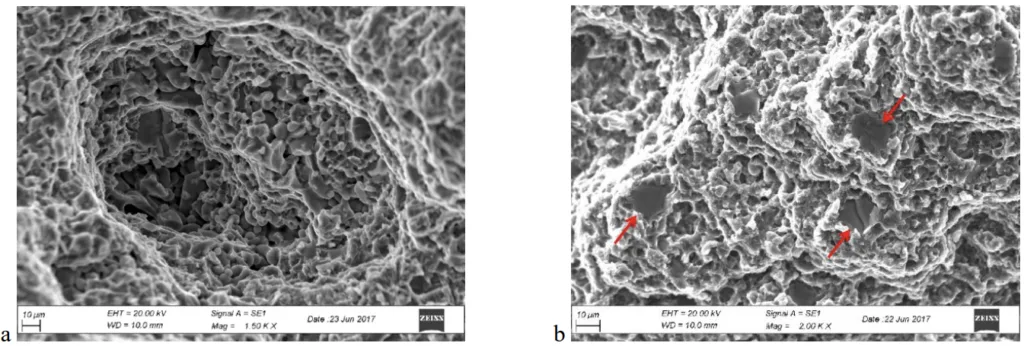
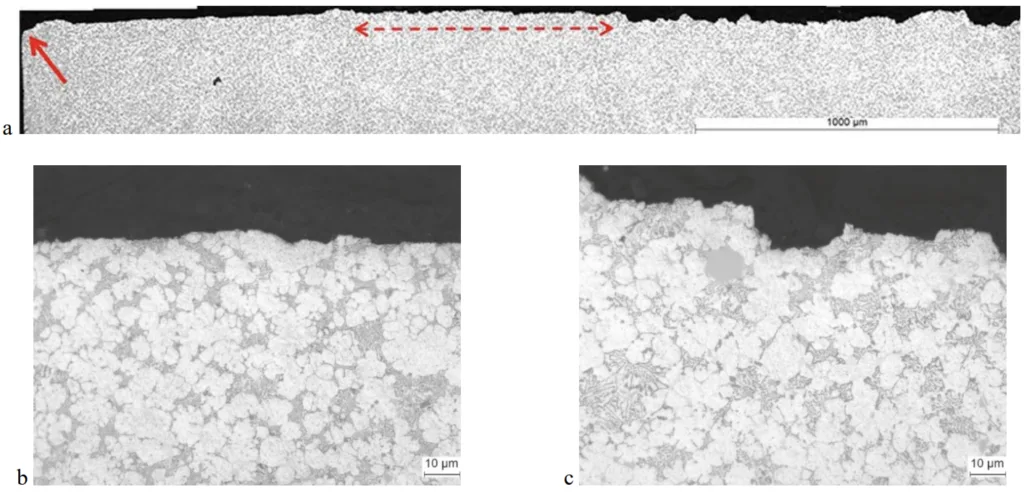
6. 결론:
주요 결과 요약:
본 연구에서는 HPDC EN AC 46000 합금의 피로 거동에 미치는 미세구조 및 주조 결함의 영향을 조사했습니다. 단축 피로 시험 및 미세구조/파면 분석 결과 다음과 같은 사실이 밝혀졌습니다:
- HPDC 공정으로 인해 편석 밴드 및 기공이 존재합니다.
- 피로 수명은 분산을 나타내며, 이는 결함 제어 균열 전파를 나타냅니다.
- 균열 시작은 날카로운 모서리에 위치한 산화 피막 및 냉간 접합에서 발생합니다.
- 파단면은 안정적인 전파 및 정적 파괴 영역으로 구성되며, 후자에는 슬러지 입자 및 기공이 존재합니다.
- 파단면 단면은 균열 경로의 매끄러운 부분(전파)과 거친 부분(정적 파괴)을 구별합니다.
연구의 학문적 의의:
본 연구는 미세구조 및 주조 결함을 피로 균열 시작 및 전파 메커니즘과 직접적으로 연결함으로써 HPDC 알루미늄 합금의 피로 거동에 대한 기본적인 이해에 기여합니다. 결함 유형 및 위치에 대한 상세한 특성 분석을 제공하여 HPDC 공정 유도 결함이 피로 성능에 미치는 영향에 대한 통찰력을 제공합니다. 또한 다이캐스트 부품의 피로 설계에서 기하학적 특징과 재료 결함을 모두 고려하는 것의 중요성을 강조합니다.
연구의 실제적 의미:
본 연구 결과는 특히 자동차 응용 분야에서 다이캐스팅 산업에 실질적인 의미를 갖습니다. 산화 피막, 냉간 접합, 편석 밴드 및 기공이 피로 파괴에 미치는 역할을 이해하면 결함 형성을 최소화하고 부품 신뢰성을 향상시키기 위한 공정 최적화를 안내할 수 있습니다. 특히, 편석 및 기공을 줄이기 위한 다이 충진 및 냉각 속도 제어, 그리고 날카로운 모서리와 같은 중요한 위치에서 냉간 접합 형성을 최소화하기 위한 다이 설계 최적화는 HPDC AlSi9Cu3(Fe) 합금 부품의 피로 성능을 향상시킬 수 있습니다.
연구의 한계점
본 연구는 "예비 연구"이며 다음과 같은 한계점을 포함합니다:
- 피로 시험은 단일 응력 진폭 수준 및 응력비에서 수행되었으므로, 더 넓은 범위의 하중 조건에 대한 피로 수명 데이터의 일반화 가능성이 제한됩니다.
- 시험된 피로 시편 수(3개)가 적어 피로 수명 분산 및 결함 특성과 피로 수명 간의 정량적 상관 관계의 통계적 유의성이 제한됩니다.
- 본 연구는 특정 합금 및 HPDC 공정 매개변수에 초점을 맞추었으며, 결과가 다른 합금 또는 주조 조건에 직접적으로 적용되지 않을 수 있습니다.
7. 향후 후속 연구:
- 후속 연구 방향
향후 연구는 "미세구조 구성 요소의 역할을 보다 포괄적으로 조사하기 위해 심화되어야 합니다". "또한, 결함이 사이클 수에 미치는 영향에 대한 통계적 평가를 가능하게 하기 위해 더 많은 수의 피로 시험이 수행될 것입니다." 여기에는 다음이 포함됩니다:- S-N 곡선을 생성하고 피로 강도를 평가하기 위해 다중 응력 수준에서 피로 시험을 수행합니다.
- 결함 특성(크기, 유형, 위치)과 피로 수명 간의 관계를 정량화하기 위해 더 큰 데이터 세트로 통계 분석을 수행합니다.
- 미세구조, 결함 형성 및 피로 거동에 대한 다양한 HPDC 공정 매개변수의 영향을 조사합니다.
- HPDC 부품의 결함 특성 분석 및 품질 관리를 위한 고급 비파괴 검사 방법을 탐색합니다.
- 추가 탐구가 필요한 영역
추가 탐구가 필요한 영역은 다음과 같습니다:- 산화 피막 및 냉간 접합에서의 피로 균열 시작의 정확한 메커니즘.
- 피로 균열 전파에서 다양한 유형의 금속간 화합물의 역할.
- 편석 밴드, 기공 및 피로 성능 간의 상호 작용.
- HPDC 부품의 미세구조 및 결함 특성을 기반으로 한 피로 수명 예측 모델 개발.
8. 참고 문헌:
- Ammar H.R., Samuel A.M., Samuel F.H., 2008. Porosity and the fatigue behavior of hypoeutectic and hypereutectic aluminum-silicon casting alloys. International Journal of Fatigue 30, 1024-1035.
- Avalle M., Belingardi G., Cavatorta M.P., Doglione R., 2002. Casting defects and fatigue strength of a die cast aluminium alloy: a comparison between standard specimens and production components. International Journal of Fatigue 24, 1-9.
- Fabrizi A., Ferraro S., Timelli G., 2013. The influence of Sr, Mg and Cu addition on the microstructural properties of a secondary AlSiCu3(Fe) die casting alloy. Materials Characterization 85, 13-25.
- Fiorese E., Bonollo F., Timelli G., Arnberg L., Gariboldi E., 2015. New classificationof defects and imperfections for aluminum alloy castings. International Journal of Metalcasting 9, 55-66.
- Hu Z., Wan L., Lu S., Zhu P., Wu S., 2014. Research on the microstructure, fatigue and corrosion behavior of permanent mold and die cast aluminum alloy. Materials and Design 55, 353-360.
- Mayer H., Papakyriacou M., Zettl B., Stanzl-Tschegg S.E., 2003. Influence of porosity on the fatigue limit of die cast magnesium and aluminium alloys. International Journal of Fatigue 25, 245-256.
- Meneghetti G., Susmel L., Tovo R., 2007. High-cycle fatigue crack paths in specimens having different stress concentration features. Engineering Failure Analysis 14, 656-672.
- Mu P., Nadot Y., Nadot-Martin C., Chabod A., Serrano-Munoz I., Verdu C., 2014. Influence of casting defects on the fatigue behavior of cast aluminum AS7G06-T6. International Journal of Fatigue 63, 97-109.
- Serrano-Munoz I., Buffiere J.-Y., Verdu C., Gaillard Y., Mu P., Nadot Y., 2016. Influence of surface and internal casting defects on the fatigue behaviour of A357-T6 cast aluminium alloy. International Journal of Fatigue 82, 361-370.
- Timelli G., Ferraro S., Grosselle F., Bonollo F., Voltazza F., Capra L., 2011. Caratterizzazione meccanica e microstrutturale di leghe di alluminio pressocolate. La Metallurgia Italiana 1, 5-17.
- Wang Q.G., Apelian D., Lados D.A., 2001. Fatigue behavior of A356-T6 aluminum cast alloys. Part I. Effect of casting defects. Journal of Light Metals 1, 73-84.
9. 저작권:
- 본 자료는 "The Authors"의 논문: "고압 다이캐스팅 AlSi9Cu3(Fe) 합금의 피로 거동에 미치는 미세구조 및 주조 결함의 영향"을 기반으로 작성되었습니다.
- 논문 출처: 10.1016/j.prostr.2017.11.119
본 자료는 상기 논문을 기반으로 요약되었으며, 상업적 목적으로 무단 사용하는 것을 금지합니다.
Copyright © 2025 CASTMAN. All rights reserved.