본 논문 요약은 ['CHINA FOUNDRY']에서 발행한 ['고압 다이캐스팅 공정에서 계면 열전달 계수 결정 및 응용'] 논문을 기반으로 작성되었습니다.
1. 개요:
- 제목: 고압 다이캐스팅 공정에서 계면 열전달 계수 결정 및 응용 (Determination of interfacial heat transfer coefficient and its application in high pressure die casting process)
- 저자: Cao Yongyou, Guo Zhipeng, Xiong Shoumei
- 발행 연도: 2014년
- 발행 학술지/학회: CHINA FOUNDRY
- 키워드: 고압 다이캐스팅 (high pressure die casting); 계면 열전달 계수 (interfacial heat transfer coefficient); 역 해석법 (inverse method)
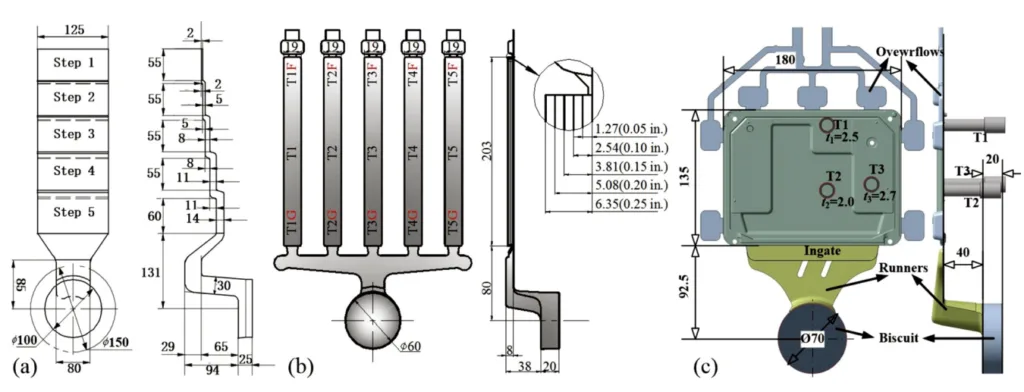
2. 초록 또는 서론
본 논문에서는 고압 다이캐스팅(HPDC)에서 계면 열전달에 대한 연구 진행 상황을 검토합니다. 계면 열전달 계수(IHTC) 결정, 주조 두께의 영향, 공정 변수 및 주조 합금이 IHTC에 미치는 영향에 대한 결과를 요약하고 논의합니다. 열 경계 조건 모델은 두 가지 상관 관계, 즉 (a) IHTC와 주조 응고 분율, (b) IHTC 피크 값과 초기 다이 표면 온도를 기반으로 개발되었습니다. 그런 다음 경계 모델을 HPDC에서 온도장 결정에 적용했으며 우수한 일치를 확인했습니다.
3. 연구 배경:
연구 주제 배경:
고압 다이캐스팅(HPDC)은 박판 부품 생산을 위한 정미 성형 공정입니다. 다이캐스팅의 우수한 특성으로 인해 다이캐스팅 제품은 자동차, 항공 우주, 의료, 전자 및 기타 산업에서 점점 더 많이 사용되고 있습니다. 금형 충전, 응고 및 다이 내부 온도 분포를 예측하는 수치 시뮬레이션 기술은 주조 기술 및 주조 제품 개발에서 매우 중요해졌습니다. 그러나 시뮬레이션의 효과는 재료 특성의 정확성과 금속-금형 경계 및 시뮬레이션 소프트웨어의 초기 조건에 따라 달라집니다. 금속-금형 계면에서의 열전달 거동을 특징짓는 계면 열전달 계수(IHTC)는 컴퓨터 시뮬레이션에서 응고 과정 중 가장 중요한 매개변수 중 하나로 여겨집니다. IHTC의 결정 및 응용은 현재 연구자들에게 중요한 문제로 부상하고 있습니다.
기존 연구 현황:
IHTC를 결정하는 기존 방법은 (1) 순수 해석적 접근법, (2) 경험적 상관 관계에 기반한 반해석적 접근법, (3) 수치적 접근법으로 분류됩니다. 순수 해석적 및 반해석적 접근법은 IHTC가 일정하다고 가정하는데, 이는 중요한 한계입니다. 수치적 접근법, 특히 역열전도 문제(IHCP)는 계면을 가로지르는 열 유속 이력을 보다 완벽하게 탐구할 수 있는 방법을 제공합니다. 이전 연구에서는 1970년대부터 HPDC에서 IHTC를 조사해 왔지만 온도 측정은 여전히 어려운 과제이며, 부적절한 열전대 설치는 불확실성을 야기할 수 있습니다.
연구의 필요성:
HPDC에서 IHTC를 정확하게 결정하는 것은 주조 공정 및 제품 개발을 최적화하는 데 필수적인 수치 시뮬레이션의 정확도를 향상시키는 데 매우 중요합니다. HPDC에서 과도 열전달의 특성과 직접 측정의 어려움으로 인해 IHTC 결정 및 공정 모델링에서의 응용에 대한 견고한 방법에 대한 추가 연구가 필요합니다.
4. 연구 목적 및 연구 질문:
연구 목적:
본 논문은 고압 다이캐스팅(HPDC)에서 계면 열전달 계수(IHTC) 결정에 대한 연구 진행 상황을 검토하고 칭화대학교 연구진의 실험적 결과를 기반으로 한 열 경계 조건 모델을 제시하는 것을 목표로 합니다.
핵심 연구 내용:
- HPDC에서 IHTC 결정을 위한 기존 방법(해석적, 반해석적, 수치적) 검토.
- 주조 두께, 공정 변수 및 주조 합금을 포함하여 IHTC에 영향을 미치는 요인 요약.
- IHTC와 주조 응고 분율 간의 상관 관계, IHTC 피크 값과 초기 다이 표면 온도를 기반으로 한 열 경계 조건 모델 개발.
- 개발된 경계 모델을 HPDC의 온도장 결정에 적용하고 실험 결과와 비교 검증.
연구 가설:
명시적으로 가설로 언급되지는 않았지만, 본 연구는 다음과 같은 전제를 기반으로 합니다.
- HPDC의 IHTC는 일정하지 않으며 응고 과정 중에 변합니다.
- 수치적 방법, 특히 IHCP는 정확한 IHTC 결정에 필수적입니다.
- IHTC는 주조 두께, 공정 변수(사출 속도, 다이 온도, 압력) 및 주조 합금에 의해 영향을 받습니다.
- IHTC 상관 관계를 기반으로 한 열 경계 조건 모델은 HPDC 시뮬레이션에서 온도장을 정확하게 예측할 수 있습니다.
5. 연구 방법론
연구 설계:
본 논문은 기존 문헌과 저자들의 자체 연구를 요약한 리뷰 논문입니다. 칭화대학교 연구진이 수행한 다이캐스팅 실험의 실험적 결과를 통합하여 열 경계 조건 모델의 개발 및 검증을 뒷받침합니다.
자료 수집 방법:
본 논문은 저자 및 다른 연구자들의 이전 연구에서 얻은 실험 데이터를 검토합니다. 칭화대학교 연구진의 실험에서는 특별히 설계된 "계단형(step-shape)", "손가락형(finger-shape)", "덮개판형(cover-plate)" 주조물(그림 1)을 활용했습니다. 온도 측정은 다이캐스팅 계면에서 1, 3, 6mm 떨어진 지점에서 특수 온도 센서 유닛(TSU)을 사용하여 수행되었습니다.
분석 방법:
본 논문에서는 IHTC 결정을 위한 다양한 해석적, 반해석적 및 수치적 방법을 논의합니다. 칭화대학교 연구진은 역 해석법을 사용하여 열전달 계수를 평가했습니다. 상관 분석 및 회귀 분석법을 사용하여 IHTC, 공정 변수, 주조 응고 분율 및 다이 표면 온도 간의 관계를 설정했습니다.
연구 대상 및 범위:
본 연구는 고압 다이캐스팅(HPDC)에서의 계면 열전달에 초점을 맞춥니다. 범위는 다음과 같습니다.
- HPDC에서 IHTC 결정 방법에 대한 문헌 검토.
- HPDC에서 알루미늄 합금(ADC12, AM50, AM60B, B390)을 사용한 실험 연구.
- 주조 두께, 공정 변수(사출 속도, 다이 온도, 압력) 및 주조 합금이 IHTC에 미치는 영향 조사.
- HPDC 시뮬레이션을 위한 열 경계 조건 모델 개발 및 적용.
6. 주요 연구 결과:
핵심 연구 결과:
- IHTC 결정 방법: 순수 해석적, 반해석적 및 수치적(역 해석법) 접근법을 포함한 IHTC 결정 방법 검토. 수치적 방법, 특히 IHCP가 과도 열전달을 포착하는 데 더 효과적임을 강조합니다.
- IHTC에 영향을 미치는 요인: 주조 두께, 공정 변수(사출 속도, 초기 다이 온도, 압력) 및 주조 합금(ADC12, AM50, AM60B, B390)이 IHTC에 미치는 영향 요약. 빠른 사출 속도와 초기 다이 온도가 뚜렷한 영향을 미치는 것으로 나타났습니다. 압력의 영향은 논란의 여지가 있으며 주조 두께에 따라 달라집니다.
- IHTC 진화 단계: HPDC 중 IHTC 진화의 4단계, 즉 초기 증가 단계, 높은 값 유지 단계, 빠른 감소 단계 및 낮은 값 유지 단계를 확인했습니다.
- 열 경계 조건 모델: (a) IHTC와 주조 응고 분율, (b) IHTC 피크 값과 초기 다이 표면 온도 간의 두 가지 상관 관계를 기반으로 열 경계 조건 모델을 개발했습니다. 모델은 4가지 IHTC 진화 단계 각각에 대한 방정식으로 설명됩니다(그림 6).
- (i) h = hmax: 초기 증가 단계 이전 및 단계 중
- (ii) h = hmax - fs / fsF ×(hmax - ho): 높은 값 유지 단계
- (iii) h = ho+khf ×(1-fs)ε: 빠른 감소 단계
- (iv) h = ho: 낮은 값 유지 단계
- 모델 검증: 개발된 경계 조건 모델을 덮개판형 주조물의 온도장 및 열 평형 시뮬레이션에 적용하여 실험 결과와 우수한 일치를 보였습니다(그림 7 및 8).
제시된 데이터 분석:
- IHTC 프로파일 (그림 2): IHTC는 사출 후 빠르게 증가하고, 최대값에 도달하고, 높은 수준을 유지한 다음 급격히 감소합니다. ADC12 합금이 AM50보다 높은 IHTC를 나타냅니다. 얇은 단계에서 더 슬림한 IHTC 프로파일을 보여줍니다.
- 초기 다이 온도 영향 (그림 3, 4, 5): IHTC 피크 값(hmax)은 일반적으로 초기 다이 표면 온도(ODI)가 증가함에 따라 감소합니다. 상관 분석 결과 ln(hmax/ODI²)와 ln(ODI) 사이의 관계가 밝혀졌습니다(방정식 4 및 5).
- 모델 적용 (그림 7, 8): 개발된 열 경계 조건 모델을 사용한 시뮬레이션은 주조 주기 동안 주조물 및 다이 표면 온도 변화를 정확하게 예측하여 HPDC에서 과도 열전달 거동을 포착하는 모델의 능력을 입증했습니다.
그림 목록:
- Fig. 1: (a) 계단형 주조, (b) 손가락형 주조, (c) 덮개판형 주조 구성
- Fig. 2: AM50 및 ADC12 합금에 대한 1-5단계에서 계산된 열전달 계수 프로파일
- Fig. 3: AM50 및 ADC12 합금에 대한 1-5단계의 초기 다이 온도 함수로서 계산된 IHTC 피크 [24]
- Fig. 4: B390 합금에 대한 손가락형 주조의 초기 다이 온도 함수로서 계산된 IHTC 피크 [8]
- Fig. 5: AM60B 합금에 대한 덮개판형 주조의 초기 다이 온도 함수로서 계산된 IHTC 피크 [7]
- Fig. 6: 열 경계 조건 모델을 위한 열전달 계수의 4단계
- Fig. 7: 덮개판형 주조의 1주기 동안 주조 표면 온도 변화
- Fig. 8: 덮개판형 주조의 1주기 동안 다이 표면 온도 변화
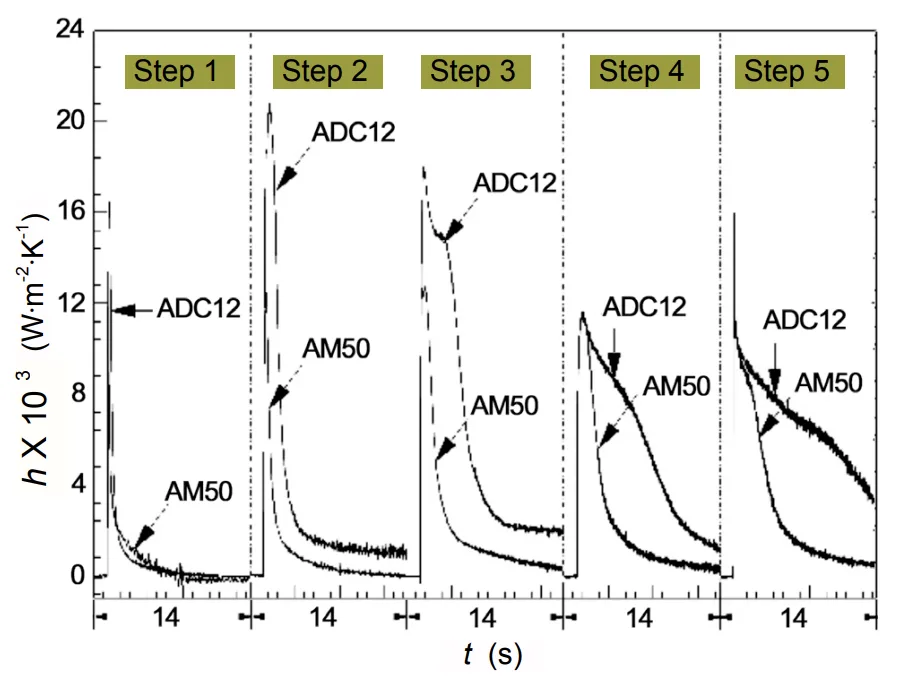
![Fig. 3: Calculated IHTC peaks as a function of initial die temperature of steps 1 to 5 for AM50 and ADC12 alloys [24]](https://castman.co.kr/wp-content/uploads/image-973-png.webp)
![Fig. 4: Calculated IHTC peaks as a function of initial die temperature of finger-shape casting for B390 alloy[8]](https://castman.co.kr/wp-content/uploads/image-974-1024x705.webp)
![Fig. 5: Calculated IHTC peaks as a function of initial die temperature of cover-plate casting for AM60B alloy [7]](https://castman.co.kr/wp-content/uploads/image-975-1024x729.webp)
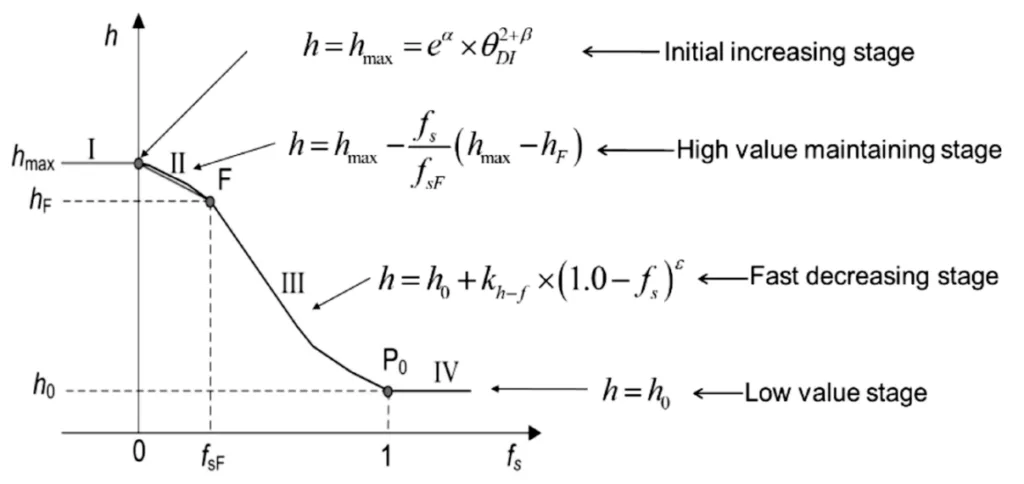
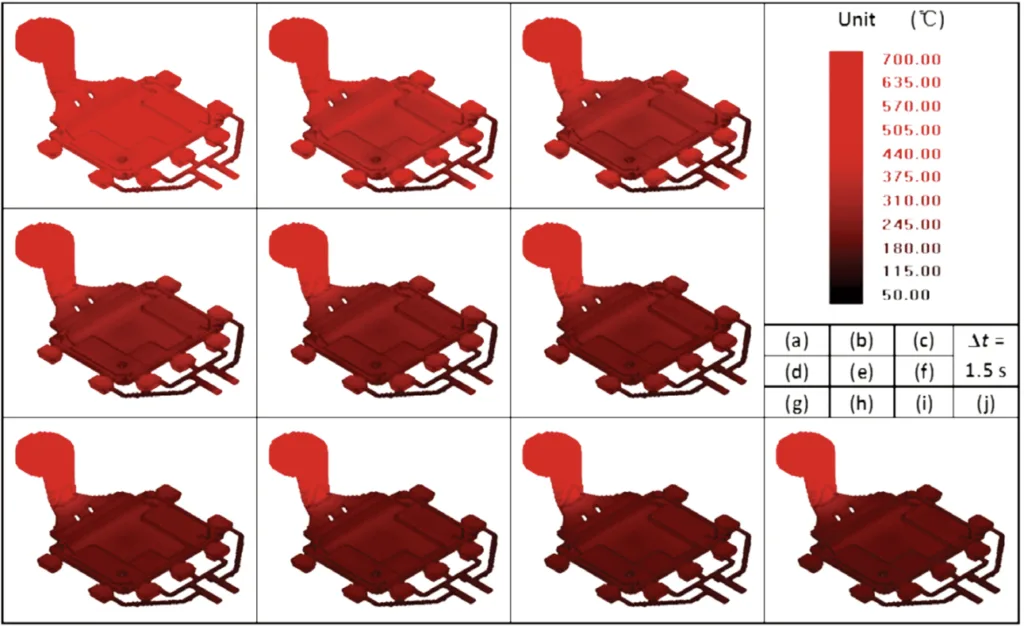
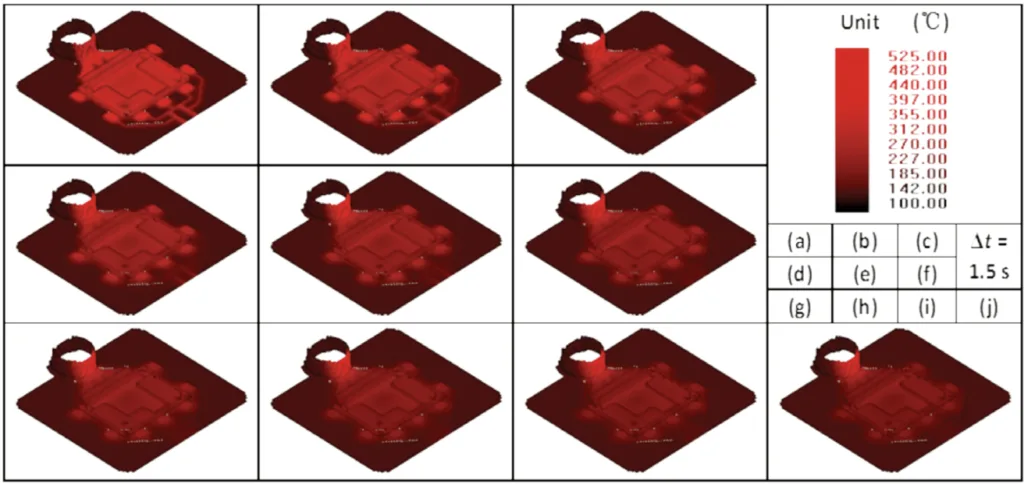
7. 결론:
주요 결과 요약:
본 논문에서는 고압 다이캐스팅(HPDC)에서 계면 열전달 계수(IHTC) 결정에 대한 연구 진행 상황을 검토했습니다. IHTC 결정을 위한 세 가지 주요 접근 방식을 요약하고 HPDC에서 정확한 온도 측정의 어려움을 강조했습니다. 칭화대학교 연구진의 연구 진행 상황을 제시하여 IHTC, 주조 응고 분율 및 초기 다이 표면 온도 간의 상관 관계를 기반으로 한 열 경계 조건 모델을 개발했습니다. 모델은 시뮬레이션을 통해 검증되었으며 실험 데이터와 우수한 일치를 보였습니다.
연구의 학문적 의의:
본 리뷰는 HPDC에서 IHTC 연구에 대한 포괄적인 개요를 제공하며, 결정 방법 및 영향 요인에 대한 지식을 통합합니다. 개발된 열 경계 조건 모델은 HPDC 시뮬레이션에서 금속-금형 계면에서의 열전달을 보다 정확하게 나타내는 데 기여하여 주조 공정 모델링 분야를 발전시킵니다.
실용적 의미:
검증된 열 경계 조건 모델은 HPDC 공정 시뮬레이션에 실제로 적용하여 온도장 및 응고 거동 예측을 개선할 수 있습니다. 이는 다이 설계, 공정 변수 및 궁극적으로 산업용 HPDC 응용 분야에서 주조 품질 및 효율성을 최적화하는 데 도움이 될 수 있습니다.
연구의 한계 및 향후 연구 분야:
본 논문은 주로 알루미늄 합금과 특정 주조 형상에 초점을 맞추고 있습니다. 향후 연구에서는 다음이 필요합니다.
- 더 넓은 범위의 주조 합금 및 복잡한 형상에 대한 열 경계 조건 모델 검증.
- IHTC에 대한 기타 공정 변수 및 다이 코팅 조건의 영향 조사.
- 갭 형성 및 표면 거칠기 효과와 같은 금속-금형 계면에서 더 복잡한 현상을 설명하기 위해 모델 개선.
- HPDC에서 실험적 IHTC 결정의 정확도를 향상시키기 위한 고급 온도 측정 기술 탐구.
8. 참고 문헌:
- [1] Nelson C W. Nature of heat transfer at the die face. In: Proceedings of 6th SDCE International Die Casting Congrass; Cleveland, OH, 1970: 1-8.
- [2] Garcia A and Prates M. Mathematical model for the unidirectional solidification of metals: I. Cooled molds. Metallurgical Transaction B, 1978, 9(3): 449-457.
- [3] Garcia A, Clyne T, and Prates M. Mathematical model for the unidirectional solidification of metals: II. Massive molds. Metallurgical Transactions B, 1979, 10(1): 85-92.
- [4] Prates M and Biloni H. Variables affecting the nature of the chill zone. Metallurgical Transactions, 1972, 3(6): 1501-1510.
- [5] Beck J V. Nonlinear estimation applied to the nonlinear inverse heat conduction problem. International Journal of Heat and Mass Transfer, 1970, 13(4): 703-716.
- [6] Beck J V, Blackwell B, and Clair C R. Inverse Heat Conduction: III-posed problems, 1985.
- [7] Cao Y, Guo Z, and Xiong S. A Study on Heat Transfer at Metal/ Die Interface during High Pressure Die Casting of AM60B Alloy. In: Proceedings of the 8th Pacific Rim International Congress on Advanced Materials and Processing (Pricm 8). Waikoloa, Hawaii, US, TMS (The Minerals, Metals & Materials Society), 2013: 3041-3049.
- [8] Cao Y, Guo Z, and Xiong S. Determination of the metal/die interfacial heat transfer coefficient of high pressure die cast B390 alloy. IOP Conference Series, Materials Science and Engineering, 2012, 33(1): 012010.
- [9] Guo Z P, Xiong S M, Liu B C, et al. Effect of Process Parameters, Casting Thickness, and Alloys on the Interfacial Heat Transfer coefficient in the High-Pressure Die-Casting Process. Metallurgical and Materials Transactions A: Physical Metallurgy and Materials Science, 2008, 39A(12): 2896-2905.
- [10] Guo Z P, Xiong S M, Liu B C, et al. Determination of the heat transfer coefficient at metal-die interface in high pressure die casting process of AM50 alloy. International Journal of Heat and Mass Transfer. 2008, 51(25-26): 6032-6038.
- [11] Guo Z P, Xiong S M, Murakami M, et al. Study on interfacial heat transfer coefficient as metal/die interface during high pressure die casting process of AZ91D alloy. China Foundry, 2007, 4(1): 5-9.
- [12] Hamasaiid A, Dour G, Dargusch M et al. Heat transfer at the casting /die interface in high pressure casting - Experimental results and contribution to modeling. In: Proceedings of MCWASP XI: Modeling of Casting, Welding and Advanced Solidification Processes, Opio, France: Minerals, Metals and Materials Society (TMS), 2006, 2: 1205-1212.
- [13] Dour G, Daugusch M, Davidson C, et al. Development of a non-intrusive heat transfer coefficient gauge and its application to high pressure die casting; Effect of the process parameters. Journal of Materials Processing Technology, 2005, 169(2): 223-233.
- [14] Hallam C P and Griffiths W D. A model of the interfacial heat-transfer coefficient for the aluminum gravity die-casting process. Metallurgical and Materials Transactions B: Process Metallurgy and Materials Processing Science, 2004, 35(4): 721-733.
- [15] El-Mahallawy N A, Taha M A, Pokora E, et al. On the influence of process variables on the thermal conditions and properties of high pressure die-cast magnesium alloys. Journal of Materials Processing Technology, 1998, 73(1-3): 125-138.
- [16] Papai J and Mobley C. Die thermal fields and heat fluxes during die casting of 380 aluminum alloy in H-13 steel dies. NADCA Transactions, 1991: 377-384.
- [17] Ho K and Pehlke R D. Metal-mold interfacial heat transfer. Metallurgical Transactions B (Process Metallurgy), 1985, 16B(3): 585-594.
- [18] Sekhar J A, Abbaschian G J, and Mehrabian R. Effect of pressure on metal-die heat transfer coefficient during solidification. Materials Science and Engineering, 1979, 40(1): 105-110.
- [19] Hong S, Backman D, and Mehrabian R. Heat transfer coefficient in aluminum alloy die casting. Metallurgical Transactions B, 1979, 10(2): 299-301.
- [20] Backman D, Mehrabian R, and Flemings M. Die thermal behavior in machine casting of partially solid high temperature alloys. Metallurgical Transactions B, 1977, 8(2): 471-477.
- [21] Ho K and Pehlke R D. Transient methods for determination of metal-mold interfacial heat transfer. In: Proceedings of Transactions of the American Foundrymen's Society, Proceedings of the Eighty-seventh Annual Meeting, Rosemont, II, USA, AFS, 1983, 91: 689-698.
- [22] Dour G, Dargusch M, and Davidson C. Recommendations and guidelines for the performance of accurate heat transfer measurements in rapid forming processes. International Journal of Heat and Mass Transfer, 2006, 49(11-12): 1773-1789.
- [23] Hamasaiid A, Dour G, Dargusch M S, et al. Heat-transfer coefficient and in-cavity pressure at the casting-die interface during high-pressure die casting of the magnesium alloy AZ91D. Metallurgical and Materials Transactions A - Physical Metallurgy and Materials Science, 2008, 39A(4): 853-864.
- [24] Guo Z P, Xiong S M, Liu B C, et al. Development of thermal boundary condition model at metal/die interface of high pressure die casting process. International Journal of Cast Metals Research, 2011, 24(3-4): 151-157.
9. 저작권:
- 본 자료는 "Cao Yongyou, Guo Zhipeng, and Xiong Shoumei"의 논문: "고압 다이캐스팅 공정에서 계면 열전달 계수 결정 및 응용"을 기반으로 합니다.
- 논문 출처: [https://doi.org/](DOI URL은 논문에 없으므로, 있다면 추가해주세요)
본 자료는 상기 논문을 요약한 것으로, 상업적 목적으로 무단 사용하는 것을 금지합니다.
Copyright © 2025 CASTMAN. All rights reserved.